Tiger Hu Sun, Junyu Ge, Zhihang Jia, Nan Huang
Faculty of Civil Engineering and Mechanics, Jiangsu University, Zhenjiang, China
Correspondence to: Tiger Hu Sun, Faculty of Civil Engineering and Mechanics, Jiangsu University, Zhenjiang, China.
Email: |  |
Copyright © 2019 The Author(s). Published by Scientific & Academic Publishing.
This work is licensed under the Creative Commons Attribution International License (CC BY).
http://creativecommons.org/licenses/by/4.0/

Abstract
Magnetorheological grease (MRG) is a new type of MR material, which is mainly composed of micron sized magnetic particles, basic solution and additives. Because of its low settlement rate, simple sealing structure, easy preparation and so on, it has a huge engineering application prospect. In this study, the samples of MRG with 5%, 15%, 25%, 35%, 45% carbonyl iron (CI) powder were prepared by using commercial grease as the matrix. The shear stress and viscosity of MRG with different CI powder volume fractions and the change of zero field apparent viscosity with CI powder volume fractions were measured by using a rotating rheometer and a parallel plate measuring system. The results show that the mechanical properties of MRG can be described by Bingham viscoplastic model. With the increase of magnetic induction intensity, the shear stress of MRG increases; when the shear strain rate is less than 50s-1, the shear stress of MRG increases rapidly, but when the shear strain rate is greater than 50s-1, the shear stress of MRG tends to be gentle; the apparent viscosity of MRG increases with the increase of magnetic induction intensity, at first it rises rapidly, then it tends to be stable; zero field viscosity of MRG increases with the increase of CI powder volume fractions.
Keywords:
Magnetorheological Greases, Rheological Characteristics, Samples, Experimental, Magnetic Field
Cite this paper: Tiger Hu Sun, Junyu Ge, Zhihang Jia, Nan Huang, Preparation of Magnetorheological Greases and Study Their Rheological Characteristics Considering the Variety of Factors, International Journal of Materials Engineering , Vol. 9 No. 2, 2019, pp. 34-38. doi: 10.5923/j.ijme.20190902.03.
1. Introduction
Magnetorheological (MR) fluid is considered as one of the intelligent and smart materials because of its adjustable rheological characteristics [1–3]. It exhibits a unique change that transforms from fluid-like state to solid-like state within milliseconds under the existence of an external magnetic field and returns to their original fluid-like state with the absence of an external magnetic field. Furthermore, this change is rapid, noticeable, and reversible. Previous studies have shown that during the dynamic phase transition, the magnetic particles form chain or cluster structures that change rheological properties of MR fluids, such as shear stress, shear yield stress, apparent viscosity, storage modulus, and so on [4-6]. Therefore, MR fluids allow widespread engineering applications including active controllable shock absorber, clutch, engine mounts, damper, sealing device and others [7–9]. Even though MR fluids have lots of merits, they have a serious sedimentation drawback caused by the density mismatch, which obstruct their extensive industrial applications [10]. Due to this sedimentation problem, various methods, such as coating polymer on magnetic particles, addition of an additive into MR fluids have been studied to reduce the density mismatch [11]. Based on these arguments, changing of a suspending medium can also give another possibility to overcome the problem, and grease becomes a strong candidate in this category [12]. Note that the suspending grease medium is a non-Newtonian fluid exhibiting a yield-stress property. By comparison with typical MR fluids, the advantage of MR grease (MRG) is the excellent dispersion stability of magnetic particles in a grease medium. Since MRG adopts grease materials as a carrier medium, the sedimentation phenomenon does not occur in the system due to the characteristic of the medium, which has the capability to disperse particles in balance against gravity [13-15]. Due to the outstanding dispersion stability characteristic of the MRG, Its advantages in industrial applications are more and more obvious, such as seismic controllable dampers which are used for provision against an earthquake. Without magnetic field, the torque performance of MRG-based is constant and it is not dependent on the operating speed, but the torque output of MRF clutch is strongly dependent on the operating speed. Especially in the application of sealing device, it can eliminate the leakage problem of MRF device after multiple use, greatly reduce the cost and prolong the service life of sealing device.Sahin et al. [16] investigated the effect of temperature on the rheological properties of the MR grease materials. In their study, the authors observed a significant effect on both apparent viscosity and yield stress. In addition, Zhang et al. [17] studied MR shear-thickening fluid prepared from nano-size silica particles suspended in ethylene glycol along with micron-size CI particles and claimed that this new type of MR fluid exhibited a high MR effect without sedimentation. Rankin et al. [18] put the ferromagnetic particles in grease with different viscosity respectively, and prepared the MRG with different zero field viscosity, it is proved by calculation that the matrix of lubricating grease will not affect the magnetorheological response while avoiding particle setting.Generally, ferromagnetic and ferromagnetic materials such as carbonyl iron (CI), iron, and iron oxide are used as magnetic particles for MR materials because they possess properties that are easily magnetized and demagnetized under external magnetic fields. In this study, among various magnetic materials, the CI is selected due to its high saturation magnetization and soft magnetic characteristic. Grease was chosen as a carrier fluid, because it is expected to improve sedimentation problem [19-20]. MRG was prepared via a simple method by mixing CI particles and commercial grease in a certain ratio. Our main focus was to examine rheological properties of the as-prepared CI based MRG via both static and dynamic test by using a rotational rheometer (MCR 300, Physica, Germany) equipped, the MR equipment (Physica MRD 180, Germany) and A 20mm diameter parallel-plate measuring system at a gap of 1mm under an applied magnetic field strength. The steady shear test was measured in the shear rate ranging from 0.01 to 200s−1. All measurements were carried out at room temperature.
2. Materials of Preparation
2.1. Micron Magnetic Particles
Soft magnetic carbonyl iron (standard CM grade, BASF, Germany) microspherical particles were adopted as dispersed phase of the MRG system as shown in Fig.1(a). Its main properties are shown in Table 1. Commercial grease (Multiservice Grease E, Hankook Shell Oil Co., Ltd, Korea) was used as a suspending medium. Table 1. The main properties of CI powder  |
| |
|
We then prepared MRG with various volume fractions of CI particles by directly mixing CI particles and commercial grease. The commercial grease was stirred for 5 minutes by a mechanical stirrer, and then CI particles were added. After that, both materials were mixed for 20 minutes at room temperature by a mechanical stirrer and a homogenizer.
2.2. Base Solution
The carrier is prepared with methyl silicone oil with a viscosity of 0.1 Pa·s and PEG-400 polyethylene glycol as shown in Fig.1(b).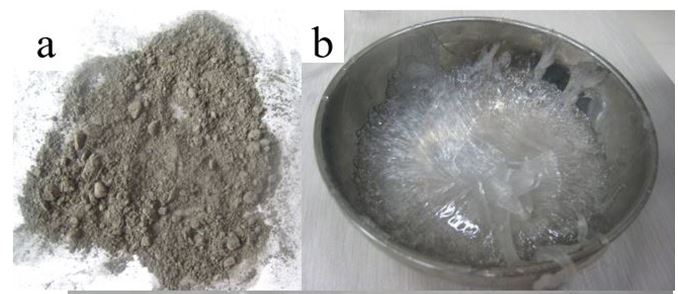 | Figure 1. (a) Carbonyl iron (CI) powder (b) Base solution PEG-400 polyethylene glycol |
2.3. Additives
The surfactants include absolute alcohol, polyethylene glycol, oleic acid, isopropionic acid, glycerol, OP emulsifier, etc; Thixotropic agents include graphite, sodium nitrite, magnesium aluminum silicate, bentonite, organic bentonite, nano calcium carbonate, nano silicon dioxide, etc.
3. Methods of Preparation
MRG, comprised of a suspension of soft magnetic CI microspherical particles dispersed in a grease medium, was prepared by a mechanical stirring method.In order to prevent particle agglomeration during the ball milling process, an appropriate amount of dispersant and solvent need to be added during ball milling.The main steps of MRG preparation:(1) Take 300g of carbonyl iron powder, 6g of oleic acid and 60g of anhydrous ethanol to mix, prepare 4 parts, and put them into 4 ball milling tanks of M-3SP2 double planet ball mill and stir for 5 minutes.(2) After ball milling for 3 hours, take out 610g of the mixture and put it in a DZF-6020 Vacuum drying box for drying and storage, After that, 122g mixture was taken out and dried at 5, 10, 15, 20, 30, 48 and 58 hours respectively.(3) Weigh other components according to the specified proportion, put them into the ball milling tank and stir them mechanically and evenly with DW-2-80W electric mixer, and then use B25 high shear emulsifier to disperse the mixture at high speed.(4) Using M-3SP2 ball mill to disperse the mixture, MRG can be obtained.According to the above methods, MRG samples were prepared as shown in Fig.2. The main components of MRG are shown in Table 2. 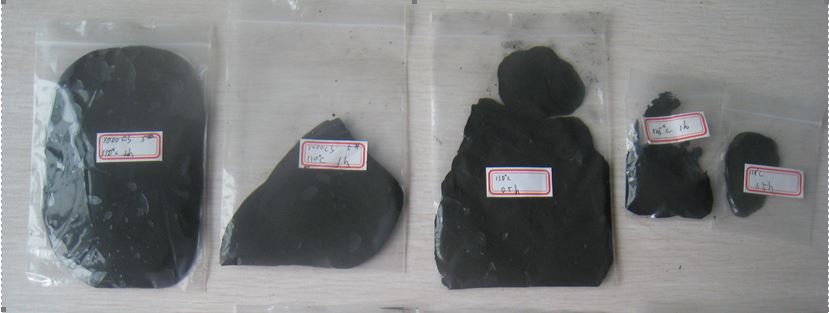 | Figure 2. Samples of prepared MRG |
Table 2. Five samples of MRG with different volume fraction of CI particles 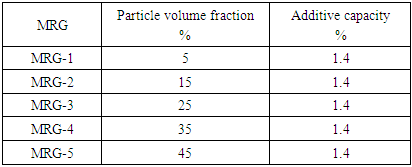 |
| |
|
4. Results
4.1. Shear Stress and Magnetic Induction Intensity
The magnetization of the magnetic particles is far from the saturation state when the external magnetic induction intensity is small, and therefore the shear stress in each of the 4 samples increases quickly with the increasing of magnetic induction intensity B and shown in Fig.3.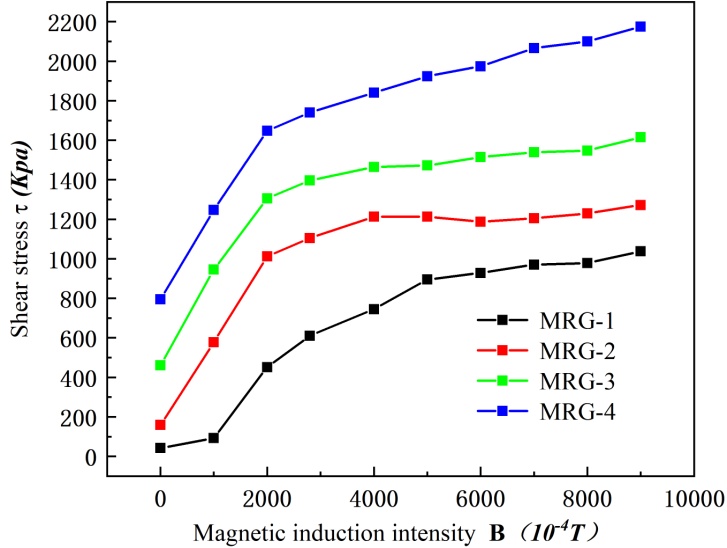 | Figure 3. Relationship between shear stress and magnetic induction intensity of MRG samples with different volume fraction of CI particles |
The shear stress increases almost linearly as B is small, but the slope decreases gradually with the increase of B. It can be attributed to the variation of the susceptibility of the particles against the magnetic induction intensity. It can be imagined that the shear stress will reach a saturated value as the magnetic induction intensity is sufficiently large when the particles are fully magnetized and the fracture and the re-formation of chain-like microstructures reaches a balance state.
4.2. Shear Stress and Shear Strain Rate
One of the most important characteristics of MRG is that they exhibit the properties of viscous fluid without applying a magnetic field, but they exhibit the property of solid-like materials within a few microseconds with applying a magnetic field. Therefore, this mechanical property of MRG is often described with the Bingham’s viscoplastic model, in which the shear stress
can be expressed as | (1) |
Where
is the shear strain rate,
is the yield shear stress corresponding to static shearing or shearing at
, and
is the viscosity of MRG. The shear stresses of the samples MRG-1 through 5 except 3 at the shear strain rate of 10s-1, 20s-1, 30s-1, 40s-1, 50s-1, 60s-1, 70s-1, 80s-1, 90s-1 and 100s-1 are tested and shown in Fig.4.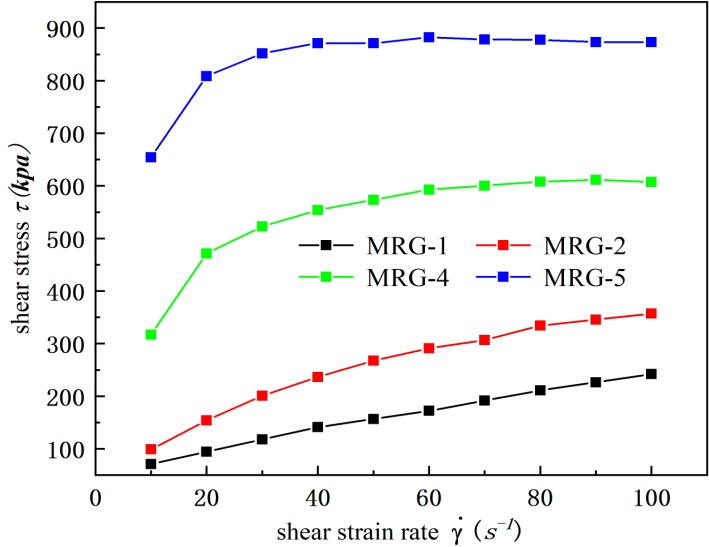 | Figure 4. Relationship between shear stress and shear strain rate of MRG samples with different volume fraction of CI particles |
It can be seen that as the shear strain rate is smaller than 50s-1, the shear stress increases with the increase of shear strain rate, and this constitutive behavior can be well described with Eq. (1). But the shear stress tends to be gentle gradually with the increase of the shear strain rate as it is larger than 50s-1. It is known that the chains of dipolar particles tend to align in the direction of the applied magnetic field, while the applied shear deformation drives the chains to incline from the direction. When an MRG is subjected to both applied static magnetic field and shear deformation, the motion of the particles, as well as the reorganization of the chains, should be determined by both the magnetic force and the applied deformation. If the deformation rate is small, there will be sufficient time for the failure chains to be re-constructed, and the number of the available chains will not be reduced. It can also be imagined that at a very large shear strain rate, there is not sufficient time for the failure chains to be re-constructed so that the number of the available chains decreases and the resistance to the overall applied shear deformation is reduced, which may slow down the growth rate of shear stress.
4.3. Viscosity and Magnetic Induction Intensity
The apparent viscosity of MRG-1~4 is the measured shear stress under certain conditions divided by shear strain rate. Obviously, the apparent viscosity is the dynamic viscosity for Newtonian fluid, which is a constant value independent of the magnetic induction intensity, but it is not so for MRG. Under the certain magnetic induction intensity, the apparent viscosity of MRG changes with the magnetic induction intensity and shown in Fig.5.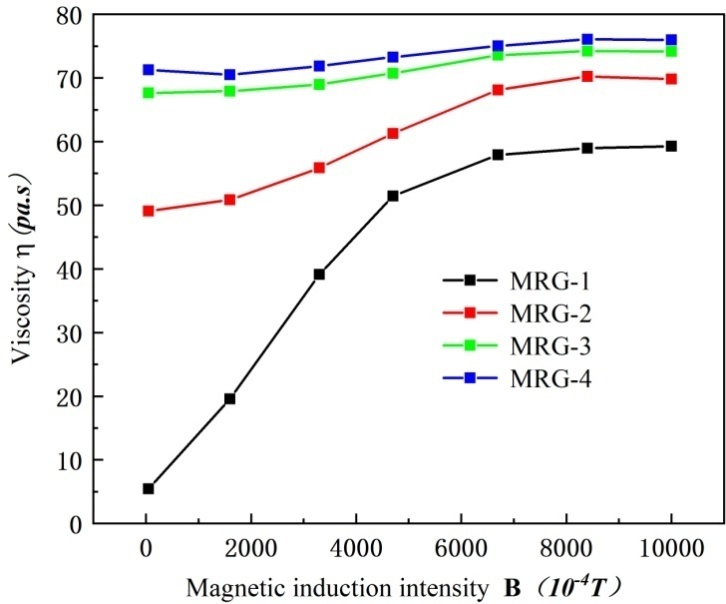 | Figure 5. Relationship between viscosity and magnetic induction intensity of MRG samples with different volume fraction of CI particles |
The apparent viscosity increases with the increase of magnetic induction intensity, at the beginning they increase quickly and then level off. It should be noted that, with the increasing of the CI volume fraction, the viscosity of MRG changes less and less obviously under the external magnetic field.
4.4. Zero-field Apparent Viscosity and Particle Volume Fraction
As one of the most important indicators to measure the performance of MRG, zero-field apparent viscosity is significant in practical applications. Generally, we require that the MRG flows well without external magnetic field. That is, the zero-field viscosity is low. The zero-field apparent viscosity of MRG-1 through 4 changes with the CI volume fraction as shown in Fig.6. 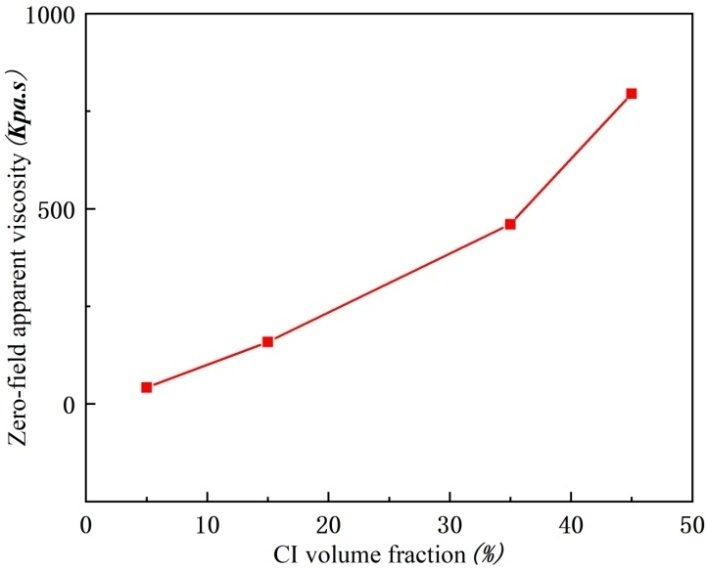 | Figure 6. Relationship between zero-field apparent viscosity and particle volume fraction of MRG samples with different volume fraction of CI particles |
As the volume fraction of magnetic particles increases, the zero field viscosity increases. This is similar to the role of the viscosity variation in the external magnetic field. In order not to affect the rheological properties of MRG, when the volume fraction of magnetic particles increases to a certain extent, the zero field apparent viscosity will also reach the maximum value.
5. Conclusions
The MRG can complete the magnetization into viscous material during a few milliseconds, which can return without external magnetic field and be both environmental protection and energy saving. The testing devices with excellent characteristics are very infrequent for MRG, so we designed a kind of testing equipment and confected 8 samples of MRG. In this research, we considered the main factors that affect the rheological properties of MRG including magnetic induction intensity, shear stress, viscosity, shear strain rate, zero-field viscosity, and etc. We also carried out relative experimental study for the MRG and proved it reliable and practical through experimental investigation. Sincerely hope our research work can provide effective help and guidance to the physical mechanism of MRG.
ACKNOWLEDGEMENTS
This work was financially supported by The National Natural Science Foundation of China (Grant No. 11702116), The National Natural Science Foundation of Jiangsu in China (Grant No. BK20160484), and the Foundation of Jiangsu University (14JDG162).
References
[1] | J. Rabinow. The Magnetic Fluid Clutch. AIEE Trans, 1948, Vol.67: 1308-1315. |
[2] | S. Mazlan, I. Ismail, H. Zamzuri, et al. Compressive and tensile stresses of magnetorheological fluids in squeeze mode. Int J App Electrom Mech, 2011(4), Vol.36: 327-337. |
[3] | A. Olabi, A. Grunwald. Design and application of magneto-rheological fluid. Material & Design, 2007(10), Vol.28: 2658-2664. |
[4] | X. Tang, X. Zhang, R. Tao, et al. Structure-enhanced yield stress of magnetorheological fluids. Journal of Applied Physics, 2000(5), Vol.87: 2634-2638. |
[5] | S. Genc, P. Phule. Rheological properties of magnetorheological fluids. Smart Material & Structures, 2002(1), Vol.11: 140-146. |
[6] | Y. Wang, Q. Luo, H. Liu, et al. Aggregated chain morphological variation analysis of magnetorheological fluid (MRF) in squeeze mode. Smart Material an Structures, 2019(10), Vol.28: 1-9. |
[7] | D. Li, D. Keogh, D. Huang, et al. Modeling the Response of Magnetorheological Fluid Dampers under Seismic Conditions. Applied Sciences-Basel, 2019(19), Vol.9: 4189. |
[8] | Y. Liang, J. Alvarado, K. Iagnemma, et al. Dynamic Sealing Using Magnetorheological Fluids. Physical Review Applied, 2018(6), Vol.10. |
[9] | Z. Tian, X. Wu, X. Xiao, et al. Influence of Temperature on Torque Transmission Stability of Magnetorheological Fluid. Journal of Magnetics, 2018(4), Vol.23: 529-535. |
[10] | H. Seugyong, K. Kwanglok, K. Kwangmin, et al. 45.5-tesla direct-current magnetic field generated with a high-temperature superconducting magnet. Nature. 2019, Vol.570: 496-499. |
[11] | X. Xu, W. Koshebae, Y. Tokunaga, et al. Transformation between meron and skyrmion topological spin textures in a chiral magnet. Nature. 2019(7743), Vol.564. |
[12] | I. Belopolski, K. Manna, D. Sanchez, et al. Discovery of topological Weyl fermion lines and drumhead surface states in a room temperature magnet. Science. 2019(6459), Vol. 365: 1278. |
[13] | T. Kurumaji, T. Nakajima, M. Hirschberger, et al. Skyrmion lattice with a giant topological Hall effect in a frustrated triangular-lattice magnet. Science. 2019(6456), Vol. 365: 914-919. |
[14] | R. Ahamed, SB. Choi, M. Ferdaus, et al. A state of art on magneto-rheological materials and their potential applications. Journal of Intelligent Material System and Structures, 2018(10), Vol.29: 2051-2095. |
[15] | H. Wang, G. Zhang, J. Wang, et al. Normal force of lithium-based magnetorheological grease under quasi-static shear with large deformation. Rsc Advances, 2019(47), Vol.9: 27167-27175. |
[16] | H. Sahin, W. Xiaoije, G. Faramarz. A New Model for Yield Stress of Magneto-Rheological Greases/Gels under Combined Effects of Magnetic Field and Temperature. Active and Passive Smart Structures and Integrated System, 2013, Vol.7288 72881E-1. |
[17] | X. Zhang, R. Wu, K. Guo, et al. Dynamic characteristics of magnetorheological fluid squeeze flow considering wall slip and inertia. Journal of Intelligent Material System and Structures, 2019, Article Number: UNSP 1045389X19888781. |
[18] | P. Rankin, A. Horvath, D. Klingenberg, et al. Magnetorheology in viscoplastic media. Rheologica Acta, 1999(5), Vol.38: 471-477. |
[19] | H. Wang, Y. Li, G. Zhang, et al. Effect of temperature on rheological properties of lithium-based magnetorheological grease. Smart Materials and Structures, 2019(3), Vol.28, Article Number: 035002. |
[20] | J. Zheng, Y. Li, J. Wang, et al. Accelerated thermal aging of grease-based magnetorheological fluids and their lifetime prediction. Materials Research Express, 2018(8), Vol.5, Article Number: 085702. |