Júlio C. Pigozzo1, Felipe N. Arroyo2, Diego H. Almeida3, Anderson R. Vobornik Wolenski4, André L. Christoforo3, Francisco A. R. Lahr5
1Department of Civil Engineering, Technology Center, State University of Maringá (UEM), Maringá, Brazil
2Faculdades Integradas de Cacoal (UNESC), Cacoal, Brazil
3Department of Civil Engineering (DECiv), Federal University of São Carlos (UFSCar), São Carlos, Brazil
4Federal Institute of Santa Catarina - São Carlos Campus, São Carlos, Brazil
5Department of Structural Engineering (SET), São Carlos Engineering School, São Paulo University (EESC/USP), São Carlos, Brazil
Correspondence to: André L. Christoforo, Department of Civil Engineering (DECiv), Federal University of São Carlos (UFSCar), São Carlos, Brazil.
Email: |  |
Copyright © 2018 The Author(s). Published by Scientific & Academic Publishing.
This work is licensed under the Creative Commons Attribution International License (CC BY).
http://creativecommons.org/licenses/by/4.0/

Abstract
The connections with bonded-in steel bars present excellent aesthetics, trustworthy performance, high strength and stiffness, and are more economic compared to the equivalent traditional mechanical connections. Nonetheless, their use in an economic and safe way depends on the deeply knowledge about influences on the pull out behaviour and on many different connection work conditions. Among these parameters, it can be pointed out with great relevance, the diameter variation of the bars used, which influence directly on the adherence surface on the anchorage area. In this work, the experiment was conducted in order to evaluate the effects of steel bar diameter variations of bonded-in with the epoxy resin Compound, in three directions (0, 45and 90º) between the rods and the wood fibers. The wood natural variability was considered through random sample of a batch of structural Pinus oocarpa Shiedetimbers. In each observation, with a total of seven combinations of variables, six replications were presented. The steel bars used were highly stiffness ones (CA-50), with threaded surface solicited into the axial direction under monotonic loadings, with two consecutive load cycles. Thereafter statistical analysis, the results are presented and commented in a comparative way.
Keywords:
Structural resins, Glued-in rods, Anchorage strength, Epoxi resin
Cite this paper: Júlio C. Pigozzo, Felipe N. Arroyo, Diego H. Almeida, Anderson R. Vobornik Wolenski, André L. Christoforo, Francisco A. R. Lahr, Pull Out Strength Evaluation of Bonded-in Steel Bars in Pinus oocarpa Shiede Structural Members, International Journal of Materials Engineering , Vol. 8 No. 5, 2018, pp. 85-89. doi: 10.5923/j.ijme.20180805.01.
1. Introduction
The connection design is the key to ensuring the performance and safety of timber structures [1]. With the possibility of developing simple and durable connections, steel bars bonded with structural resins have been applied in different situations [2].This type of connection has received attention and recognition mainly for its excellent aesthetic appearance and performance. The connections with glued steel bars have been widely used in European countries, with the largest applications in glued laminated structures [3].Structural synthetic resins most used in timber structures are classified into three groups: phenol-resorcinol formoldehydes (PRF), polyurethanes (PUR) and epoxies (EP), which has been continuously developing and presenting better properties [4].Gardner [5] concluded that epoxy resins are clearly the most suitable adhesives for reinforcing or bonding steel elements in structural members. It is considered a new technology, with limitations of data on the behavior of these resins in long-term tests and there are many types of epoxy resins. The results obtained for one resin cannot be extrapolated, predicting the behavior of another.According to Bainbridge and Mettem [6], it is considered that the requirements for adhesives in this case are: to achieve good adhesion in wood; achieve significant shear strength (to keep the section of the adhesive layer intact); and to keep the anchoring of the bars (through the combination of chemical adhesion and mechanical adhesion), completely involving the bar rough surface. Due to the particularities of the bar surface preparation in the construction environment, the practice of using textured or filament bars has been standardized to maximize mechanical adhesion. Due to economic reasons, construction processes and the low cost of the material, it is possible to disregard the high levels of preparation of the bar surfaces to maximize the chemical adhesion, compared to the high performance of the mechanical adhesion.Several calculation models are developed to estimate the average response of the anchorage strength, with many independent variables involved, such as: natural variability of the wood mechanical properties; epoxy resin used; distance from the hole to the edge of the member; form of solicitation of the steel bar (one or two sides request); glue line thickness; bar surface roughness; predominant rupture model; anchorage length; bar diameter; moisture content of wood. Some of these variables can be controlled in the project, others are insignificant in the response and can be disregarded, leaving only a few independent and significant variables, such as: variations of moisture content of wood; variations in anchorage length; and variations of the bar diameters [7].
2. Literature Review
Considering the steel bars anchorages with the following conditions: the predominant rupture model is the rupture of the adhesion on the steel surface, where it breaks initially the chemical adhesion and after the mechanical adhesion; using an epoxy resin which exhibits glassy consistency after hardening (particularly low or medium viscosity resins); necessarily steel bars with rough surfaces; and the glue line thickness not be less than 1.0 mm, subject to the following conditions (Equation 1). | (1) |
Where: D = hole diameter; d = steel bar diameter.Buchanan and Deng [8], Deng et al. [3], Buchanan and Moss [9], Aicher et al. [4] and Gustafsson and Serrano [10], presented numerical models trying to determine the average anchorage strength, considering the main independent variables that influence these results. In long experiments using short or long loads, steel bars with rough surfaces, wood from C24 and C32 strength classes treated with CCA (Chromate Copper Arsenate) and different epoxy resins, obtained, in a common way, the following responses: - bars with deformed surface had lower anchorage strengths, compared to threaded surface bars;- rupture loads were approximately proportional to the anchorage lengths, up to the limit of twenty times the bar diameter, furthermore, the additions are insignificant; - ruptureload was approximately proportional to the steel bar diameter; - rupture force to increase with the increase of hole diameter; - there were significant differences between the types of epoxy resins. These authors considered, in the numerical models, the variable anchorage slenderness (Equation 2), thus considering, indirectly, the effects of the variations of the diameters of the anchored steel bars. They state that the anchorage strength can be estimated to good approximation via a simple equation, which includes the bar diameter and anchorage slenderness. They further state that the intensity of the effects of some parameters on the anchorage strength may vary depending on the specific behavior of the adhesive. | (2) |
Where: λ = anchorage slenderness; La = anchorage length; d = steel bar diameter.Figure 1 shows relationship between anchorage strength (RA) versus anchorage length (La) and steel bar diameter (d) [8]. 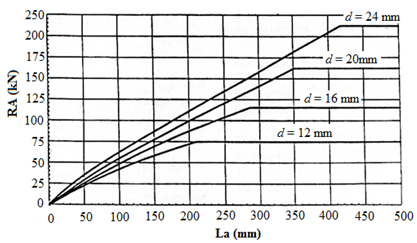 | Figure 1. Relationship between anchorage strength (RA) versus anchorage length (La) and steel bar diameter (d) [8] |
Deng et al. [3] supplemented the information presented by Buchanan and Deng [8], analyzing the stress distribution in bonded bars through an analytical model, the finite element method (MEF). They concluded that these analyzes allowed the explanations of different types of ruptures observed in experiments with short loads. Gustafsson and Serrano [10] presented comparative models to evaluate the anchorage strengths bonded steel bars. The numerical model presented was an empirical model, and the analytical models are based on: one of them in the fracture mechanics, considering linear elastic tensions and the properties of the adhesive layers and the second, in finite elements with three dimensions, that considers a non-linear fracture mechanism and the behavior of the adhesive layers.Bengtsson et al. [11] analyzed two production control methods for anchoring steel bars bonded to timber structures using Norway spruce wood specie. They used a destructive method with specimens and a non-destructive method for load tests. They presented important considerations regarding the form of solicitation of the steel bars in relation to the wood. Anchorage test pulling on both sides speciemen produced higher strengths, compared to tests on one side. For EP and PUR resins, with λ = 20, the differences were accentuated. The number of defects detected varied with the type of adhesive, the anchorage slenderness and the type of error caused. Figure 2 shows the types of axial stresses in glued bars. | Figure 2. Representation types of axial stresses in glued bars: (a) one-sided request; (b) and (c) two-sided requests [11] |
In order to correlate the anchorage strength with anchorage steel bar surface, Pigozzo [2] presented studies evaluating the average adhesion surface of CA-50 steel bars, for diameters equals to 6.3, 8.0, 10.0, and 12.5 mm of four commercial suppliers: Gerdau, Votoraço, Belgo-Mineira and Açominas. It presented a numerical model that relates the average area of the anchorage surface as a function of the nominal anchorage surface, calculated via nominal steel bar diameter.
3. Material and Methods
This experiment was carried out to evaluate the effects of the variations of the steel bar diameters on the anchorage strengths, using an epoxy resin (liquid consistency) in Pinus oocarpa Shiede wood specie (apparent density equal to 550 kg/m³). Anchorage strengths were compared with the same anchorage surface, however, varying steel bar diameters and anchorage length.Wood natural variability wood was considered by means of a random sampling, obtaining six timber beams with dimensions of 5.5x20x300 cm. From each beam a series of specimens were obtained, corresponding to the observations of desired anchorages. In this way, a total of six replications were carried out for each observation. The mechanical properties of the wood along the length of each studied beam were assumed constant.Specimens were manufactured considering the relationships between the effective anchorage surface and the nominal steel bar diameters, using the Equation 3, valid for the interval 6.3 mm ≤ d ≤ 12.5 mm [2]. | (3) |
Where: Aam= average anchorage area of the steel bar surface per unit of anchorage length (cm²/cm); d = steel bar diameter.Adopting steel bar diameter d1 = 6.3 mm, d2 = 8.0 mm and d3 = 10.0 mm and using Equation 3, the average anchorage area are equal to 2.01, 2.68 and 3.35 cm²/cm, respectively.Steel bars were glued in the 0, 45 and 90º directions in relation to the grain of wood specimen (Fig. 3 and Fig. 4).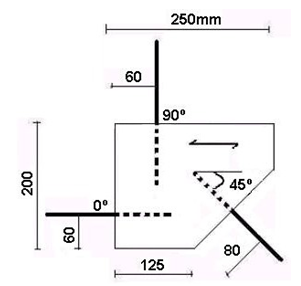 | Figure 3. Dimensions and positioning of the steel bars on the Pinus oocarpa Shiede specimen |
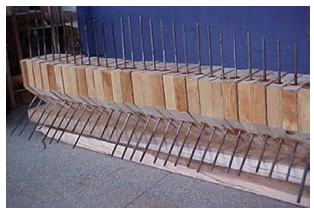 | Figure 4. Pinus oocarpa Shiede specimens with glued steel bar |
In all specimens, the steel bars received surface cleaning treatment by applying a rotating steel brush until it reached the white color at the end in contact with the resin. Subsequently, thinner (commonly used for cleaning) was applied as solvent to remove oil residues. CA-50 steel bars (fyd = 500 MPa) with a diameter of 6.3 mm, axially requested in two load cycles with monotonic loads, were used, the first cycle being with up to 70% of the ultimate strength.Statistical analyzes applied were:- analysis of multiple linear regression: a statistical model capable of explaining the variations of anchorage strengths as a function of the anchorage surface (Aa) and wood apparent density of wood (ρ12%);- test "t", which shows the significance of the variable in the model by means of the associated "p" probability;- residue analysis: they are used to confirm the fundamental hypotheses, indicating if the applied tests are adequate and possible to be used. The level of significance was α = 5%.
4. Results and Discussion
Table 1 presents average anchorage strength results, according to three steel bar diameters (d1 = 6.3 mm; d2= 8 mm and d3 = 10 mm) for each direction to the grain (0, 45 and 90º).Table 1. Results obtained from the anchorage strengths in the 0, 45 and 90° directions  |
| |
|
Table 2 shows regression models to estimate anchorage strength (RA) as function of anchorage surface (Aa) and wood apparent density (ρ12%).Table 2. Regression model to estimate RA in the 0, 45 and 90° directions 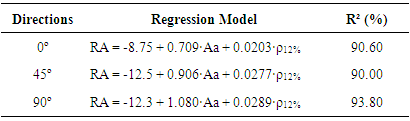 |
| |
|
By analysis of variance, it can be observed that all regression models can be considered highly significant. The studies of the residuals versus independent variables showed symmetry, indicating zero mean. The uniform dispersion of points around zero indicates no correlation between residues and variables observed.Normality tests for the residues indicate that anchorage strength present a normal distribution. Therefore, the tests used in each analysis are suitable and possible to be used.Density variations of Pinus oocarpaShiede wood air dried were not significant in all regression models studied at a significance level of 5%.The anchorage, in any direction, did not show fragile rupture. Steel bars progressively lost anchorage strength, as the anchorage length decreases with the pullout steel bar.Anchorage rupture models presented, predominantly, loss of chemical adhesion on the bar surface and subsequent loss of mechanical adhesion. As wood of low mechanical strength, in the 0 and 45° directions, wood fragments from the outer end of the anchorage were pulled together with the bar.Anchorage strength at 90° directions are larger than the corresponding ones in the 45° direction, which in turn are larger than the corresponding ones in the 0° direction.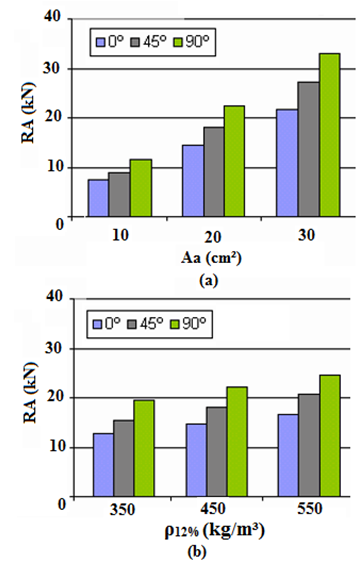 | Figure 5. Comparisons of anchorage strength for (a) anchorage surface and (b) apparent density variations in the 0, 45 and 90º directions |
5. Conclusions
The results of this study permit us to conclude:- Anchorage strength at 90° directions are larger than the corresponding ones in the 45° direction, which in turn are larger than the corresponding ones in the 0° direction.- Regression models to estimate RA as function of Aa and ρ12% presented R² values higher to 90% for all directions between steel bar and wood specimen grain.
ACKNOWLEDGEMENTS
For all the provided support, the authors thanks the Fundação de Amparo à Pesquisa do Estado de São Paulo (FAPESP) and Coordenação de Aperfeiçoamento de Pessoal de Nível Superior (CAPES).
References
[1] | Madsen, B. Timber connections with strength and reliability of steel. International Wood Conference, Toronto, Canada, p. 4-504, 4-511, 1996. |
[2] | Pigozzo, J. C. Estudo e aplicações de barras de aço coladas, comoconectores em placas mistas de madeira e concreto para tabuleiro de pontes. São Carlos, 2004. Tese (Doutorado em Engenharia de Estruturas) – Escola de Engenharia de São Carlos, Universidade de São Paulo, São Carlos, 2004. |
[3] | Deng, J. X. et al. Glued bolts in glulam: an analysis of stress distribution. Proceedings of 5th World Conference on Timber Engineering, Switzerland, 1998. |
[4] | Aicher, S.; Gustafsson, P.; Wolf, M. Load displacement and bond strength of glued-in rods in timber influenced by adhesive, wood density, rod slenderness and diameter. 1st International RILEM Symposium on Timber Engineering, Stockholm, Sweden, Sep. 13–14, p. 369–381, 1999. |
[5] | Gardner, G. Reinforced glued laminated timber system epoxy/steel timber composite material. Proceedings of Pacific Timber Engineering Conference, Australia, 1994. |
[6] | Bainbridge, R. J.; Mettem, C. J. Bonded in rods for timber structure: a versatile method for achieving structural connections. The Structural Engineering, v. 77, n. 15, p. 24-27, 1999. |
[7] | Barchelar, M. L.; Mcintosh, K. A. Structural joint in glulam. 5th World Conference Timber Engineering, Montreux, Switzerland, v. 1, p. 289-296, 1998. |
[8] | Buchanan, A.; Deng, J. Strength of epoxied steel rods in glulam timber. Proceedings of International Wood Engineering Conference, United States of America, 1996. |
[9] | Buchanan, A.; Moss, P. Design of epoxied steel rods in glulam timber. Pacific Timber Engineering Conference, Rotorua, New Zealand, March, p. 286–293, 1999. |
[10] | Gustafsson, P. J.; Serrano, E. Predicting the pull-out strength of glued-in rods. 6th World Conference on Timber Structure, Vancouver, Canada, Jul 31-Aug 3, p. 7,4,4, 2000. |
[11] | Bengtsson, C.; Kemmsies, M.; Johansson, C. J. Production control methods for glued-in rods for timber structures. 6th World Conference on Timber Structure, Vancouver, Canada, Jul 31-Aug 3, p. 7,4,1, 2000. |