João Paulo Boff Almeida1, Kênia A. de Lima Scariot1, Gustavo Henrique Nunes1, Francieli S. Delavy1, Jennifer Mayara Vilas Boas da Silva2, Anderson Renato Vobornik Wolenski3, André Luis Christoforo4, Francisco Antonio Rocco Lahr5
1Department of Civil Engineering, University of Mato Grosso State (UNEMAT), Sinop, Brazil
2Department of Architecture and Urbanism, University of Cuiabá (UNIC), Sinop, Brazil
3Federal Institute of Santa Catarina - São Carlos Campus, São Carlos, Brazil
4Department of Civil Engineering (DECiv), Federal University of São Carlos (UFSCar), São Carlos, Brazil
5Department of Structural Engineering (SET), São Carlos Engineering School, São Paulo University (EESC/USP), São Carlos, Brazil
Correspondence to: André Luis Christoforo, Department of Civil Engineering (DECiv), Federal University of São Carlos (UFSCar), São Carlos, Brazil.
Email: |  |
Copyright © 2018 The Author(s). Published by Scientific & Academic Publishing.
This work is licensed under the Creative Commons Attribution International License (CC BY).
http://creativecommons.org/licenses/by/4.0/

Abstract
The combination of hot weather typical factors, such as high temperature and low relative humidity of the air, associated with the delay in concrete application due to lack of planning in concreting, are some causes of slump loss in this material. Depending on the type of work and the adopted execution methods, this loss may make both placement and compaction more difficult. Thus, consistency correction through water addition or other plasticizer additives are common. In this context, this research aimed to analyze the variations of slump loss in concrete through time and the consequences of water addition in the mixture. Therefore, it was performed a study with trace of characteristic resistance to compression correspondent to 35 MPa, analyzing 70 test specimens in a total of seven subsequent periods, from 0 min (after preparation) and 180 min. The specimens were molded according to ABNT NBR 5738 (2015) Brazilian standard and submitted to compression test after 28 days being cured, according to ABNT NBR 5739 (2018) Brazilian standard. Results showed that after 180 min, water addition caused a 68,60% increase in water to cement ratio and a 59,20% loss of resistance to compression. In summary, water addition to slump correction was observed to be an extremely harmful practice to concrete and it should be avoided or minimized.
Keywords:
Retempering, Consistency, Slump Loss, Water To Cement Ratio
Cite this paper: João Paulo Boff Almeida, Kênia A. de Lima Scariot, Gustavo Henrique Nunes, Francieli S. Delavy, Jennifer Mayara Vilas Boas da Silva, Anderson Renato Vobornik Wolenski, André Luis Christoforo, Francisco Antonio Rocco Lahr, Influence of Water Addition to Correct the Slump in Compressive Strength of Concrete Produced in Sinop - Brazil, International Journal of Materials Engineering , Vol. 8 No. 3, 2018, pp. 35-39. doi: 10.5923/j.ijme.20180803.01.
1. Introduction
Portland cement concrete consists in the resultant material of adequate combination of cement, fine aggregate, coarse aggregate and water. Admixtures may also be employed in order to provide special properties to the product [1, 2]. Homogeneity and cohesion that provide workability and the required resistance to the material are factors directly associated to materials dosage and mixture [3, 5]. Thus, seeking for better practicality, economy and quality in constructions through rationalized processes, most concrete consumed in Brazil comes from plants with dosage centrals [5, 7].Despite the advantages offered by the machined material, concrete industries and enterprises often face problems associated to delay in material delivery or application, which cause workability loss and unviability of concrete usage [8].In this context, it is usual to practice the water addition for slump restoration and correction, in order to make concrete application possible in construction sites [9].Concrete workability in the moment of usage is of real interest. If consistency in this moment is not appropriate to provide good compacting, it is necessary to correct it in order to obtain, theoretically, total compaction, able to reduce to the maximum the presence of voids and avoid possible concreting failures [10].Concrete slump correction with water, admixtures or even a combination of both is a usual and traditional practice to solve material loss [6, 11, 12]. Hawkins [13] and Alhozaimy [14] mention, however, that water addition may generate significant resistance loss, while it increases water to cement ratio in concrete mixture.The added water complementarily restores workability and conditions concrete application. However, it influences the segregation of aggregates and performance degradation, not only in resistance but also in material durability [15].Concrete’s water to cement ratio comprehends an elementary factor to obtain the necessary resistance and durability [16, 17]. Assuming concrete total compaction, resistance to compression may be considered inversely proportional to this relation. Such consideration is known as Abrams’ law and it is presented in Figure 1, which also illustrates the decrease of resistance due to concrete partial compaction [10].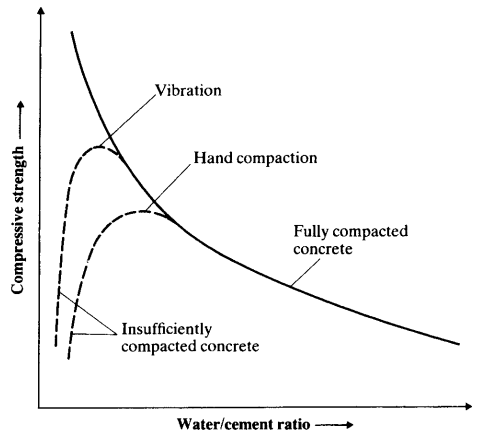 | Figure 1. Relation between resistance and water/cement ratio in function of compaction degree [10] |
For two hours, concrete behaves as a viscous liquid, making its transporting, placing and compacting possible, without many problems. Immediately after this, concrete begins to present significant solid internal structure, whose resistance tends to increase with time, making remixture operation impossible [18].In order to avoid handling of concrete after the beginning of solidification, ABNT NBR 14931 (2004) [19] suggests that the period between the use of kneading water and the end of concreting is not over 150 minutes.Studies based on computer models demonstrated the importance of spatial conditions in the influence of cement hydration [20, 21]. The delay in placement, combined with the high temperatures in Mato Grosso state, stimulate the accelerated evaporation of kneading water in concrete material. This factor is able to condition the water/cement ratio of mixture, as well as water addition to the correction of material consistency.According to Moreno & Higa [22], among the climatic classifications that describe Mato Grosso state, the one by Strahler [23] is very satisfactory. Because of its latitudinal position and territorial extension, the state presents two units: I – Continental Equatorial Climate, which comprises the north region; and II – Alternately Humid and Dry Continental Tropical Climate, comprising the center-south portion of the state. In order to demonstrate more specific features of each region, the climate was partitioned in subunits. They are: I-A, I-B, I-C e II-A, II-B, II-C, II-D and II-E [22].Considering this detailed climatic classification, the city Sinop is located in I-B subunit, presenting height from 200 to 400 m and usually reaching temperatures over 35°C, having the maximum temperature of 42°C [22].In predominantly hot climates like the one in Sinop, concreting may present some problems coming from concrete temperature elevation and fresh mixture evaporation ratio. A high temperature propitiates quick cement hydration, leading to accelerated solidification and decreased long-term resistance of hardened concrete [10].Considering such environmental factors and admitting that concrete is hardly ever placed immediately after its preparation, water addition to adjust the material consistency is a usual practice at construction sites in the studied region.It is important to highlight that ABNT NBR 12655 (2015) standard [24], responsible for establishing the conditions demanded for preparation, control and receiving of concrete destined to the execution of simple, reinforced and prestressed concrete structures, does not mention about the technique of supplementary water addition. That said, in order to study any normative or even bibliographic indefinition, this research aimed to analyze, from laboratory assays, the slump variation throughout time and the probable loss of resistance to compression in concrete due to kneading water addition to the correction of consistency.
2. Material and Methods
The concrete samples were produced and assayed at Universidade do Estado de Mato Grosso (UNEMAT) concrete laboratory, Sinop campus. The concrete mixture was prepared in a mixer with trace of characteristic resistance to compression correspondent to 35 MPa and slump equals to 12 cm. An aggregate with a maximum diameter of 19 mm and CP II Z-32 cement with a consume of 380 kg/m³ were used.After the preparation (0 min) and after 30, 60, 90, 120, 150 and 180 min, concrete samples were taken, in order to verify slump loss, through slump test, as shown in Figure 2. Slump test was performed following ABNT NBR NM 67 (1998) Brazilian standard recommendations [25].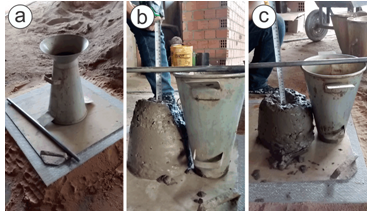 | Figure 2. a) Slump kit used to concrete slump test; b) Initial slump; c) Slump corrected through water addition |
When it was necessary, water was added to the mixture with the help of a graduated test tube (Figure 3) in order to reestablish initial slump. This procedure was performed in attempts, with repetitions being done when the measured consistency was not the desired one.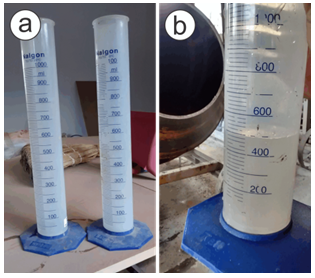 | Figure 3. a) Graduated test tube used to water addition in concrete; b) 500 ml water measurement with the help of a graduated test tube |
Throughout the time among the specified periods, the mixer kept moving working to homogenize the mixture, before slump test and after water addition.Following ABNT NBR 5738 (2015) Brazilian standard recommendations [26], 10 test specimens were molded to each studied time, totalizing 70 experimental results. The samples were identified according to the respective molding time and submitted to cure in fresh water for 28 days.The assays to determine the resistance to compression were performed according to ABNT NBR 5739 (2018) Brazilian standard prescriptions [27]. An analogic manual hydraulic press was used (Figure 4).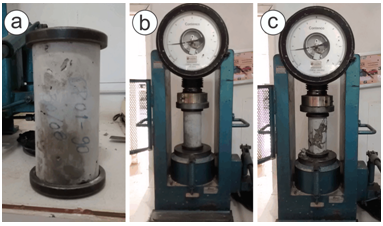 | Figure 4. a) CP capped with confined neopreme; b) Manual hydraulic press and CP before compression assay; c) Hydraulic press and CP broken after compression assay |
For statistical interpretation, a variation coefficient (Equation 1) was used to analyze dispersion of data obtained through the resistance to compression assay. In equation 1, Cv denotes the variation coefficient, Sd and
consist of standard deviation and average values of samples, respectively. | (1) |
3. Results and Discussion
Next, the results obtained from slump tests and resistance to compression, performed with samples submitted to different water additions to slump correction, will be presented and analyzed. Table 1 presents the results obtained from performed slump tests, evidencing the amount of water added to consistency correction and the water to cement ratio changed in function of this addition.Table 1. Initial slump, amount of water added, corrected slump and altered water to cement ratio 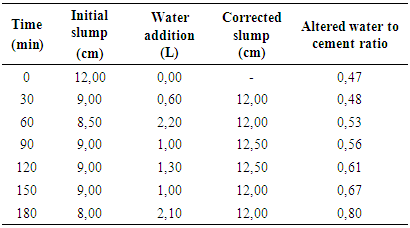 |
| |
|
Supplementary water addition to readjustment of initial slump caused an increase in water to cement ratio (0,47) of 40,45% and 68,60% to the time periods correspondent to 150 and 180 minutes respectively. Figure 5 describes the increase of water to cement ratio for every studied time period, also evidenced in Table 1.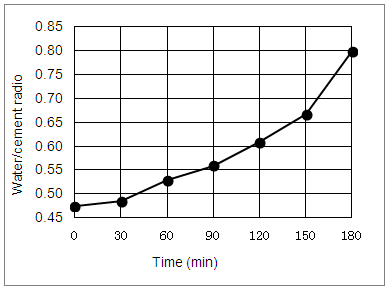 | Figure 5. Water to cement ratio variation through time |
Table 2 presents mean values (
), minimum (Min), maximum (Max) and variation coefficient (Cv), the compressive strengths measured at the end of 28 days.It is possible to verify in Table 2 that water addition in the second time period studied did not affect resistance to compression. On the other hand, it was observed a 45,18% loss in resistance to compression of samples correspondent to 150 min time period (recommended time to handling and application of concrete according to ABNT NBR 14931 (2004) Brazilian standard [19]). In the same way, it was verified a resistance loss equivalent to 59,20% to 150 min time period.Table 2. Mean of resistances to compression after 28 days, variation coefficient, minimum and maximum values 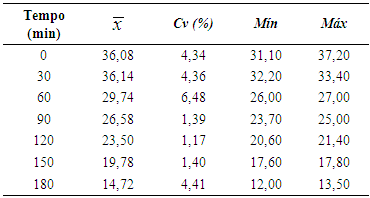 |
| |
|
Teixeira and Polisser [6], in a study performed at concrete dosage central, quantified the resistance loss when there was slump correction with water addition to the concrete, obtaining a 34% loss for a concrete with characteristic resistance to compression of 20 MPa after 150 minutes.In similar study, Erdogdu [28] observed a 40% decrease in resistance to compression related to initial resistance for concrete with cement consumption of 300 kg/m³, with slump corrected through water addition.
4. Conclusions
Through the results obtained in the present research, it was possible to conclude:- The concrete correspondent to 0 min time period obtained intended resistance (36,08 MPa), considering that the resistance trace corresponded to a 35 MPa concrete.- At 180 minutes, supplementary water addition caused a 68,60% increase in relation to initial water to cement ratio.- The resistance of concrete retempered with water to slump correction considerably decreases with mixture time. After 150 min of mixture, a 45,18% loss was observed in relation to concrete (36,08 MPa) initial resistance. After 180 min, the observed loss was 59,20%.- Water addition aiming slump correction is an extremely harmful practice in concrete resistance to compression, making the concrete application ideal after its preparation.
References
[1] | Petrucci, E. G, R. Concreto de cimento Portland. 14. ed. São Paulo: Globo, 2005. |
[2] | Mehta, P. K.; Monteiro, P. J. M. Concrete: Microestructure, properties and materials. New York: McGraww-Hill, 2006, 684p. |
[3] | Bye, G. C.; Sruble, L.; Livesey, P.; Del Strother, P. Portland Cement Composition, Production and Properties. London: ICE Publishing, 2011, 240p. |
[4] | Hewlett, P. C. Lea’s Chemistry of Cement and Concrete. London: Elsevier Science & Technology Books, 2004, 1066p. |
[5] | Barboza, L. S.; Gonçalves, E. C.; Dos Santos, T. M. S.; Sartori, A. L. Influência do Tempo Máximo de Mistura e Transporte Especificado pela ABNT NBR 7212:2012 na Resistência a Compressão de Concretos Usinados, Revista de Engenharia Civil IMED 2017, 4(2): 20-33. |
[6] | Teixeira, R. B.; Pelisser, F. Análise da Perda de Resistência à Compressão do Concreto com Adição de Água para Correção da Perda de Abatimento ao Longo do Tempo, Revista de Iniciação Científica UNESC 2007, 5(1). |
[7] | Polesello, E.; Rohden, A. B.; Dal Molin, D. C. C.; Masuero, A. B. O Limite de Tempo Especificado pela NBR 7212, para Mistura e Transporte do Concreto, pode ser Ultrapassado?, Revista Ibracon de Estruturas e Materiais 2013, 6(2): 339-359. |
[8] | Sobhani, J.; Najimi, M.; Pourkhorshidi. Effects of retempering methods on the compressive strength and water permeability of Concrete, Scientia Iranica 2012, 19(2): 211-217. |
[9] | Erdogdu, S. Arslantürk, C. and Kurbetci, S. Influence of Fly Ash and Silica Fume on the Consistency Retention and Compressive Strength of Concrete Subjected to Prolonged Agitating, Construction and Building Materials 2011, 25: 1277-1281. |
[10] | Neville, A. M.; Brooks, J. J. Concrete Technology. Porto London: Pearson, 2010. 460p. |
[11] | Ravina, D. Slump Retention of Fly Ash Concrete with and Without Chemical Admixtures, ACI Concrete International 1975, 17: 25-29. |
[12] | Baskoca, A. Ozkul, M. H.; Artirma, S. Effect of Chemical Admixtures on Workability and Strength Properties of Prolonged Agited Concrete, Cement and Concrete Research 1998, 28(5): 737-747. |
[13] | Hawkins, M. J. Concrete Retempering Studies, Journal Proceedings 1962, 59(1): 63-72. |
[14] | Alhozaimy, A. M. Effect of Retempering on the Compressive Srength of Ready Mixed Concrete in Hot-Dry Environments, Cement and Concrete Composites 2007, 29(2): 124-127. |
[15] | Kim, Y. Y; Lee, K. M.; Bang, J. W.; Kwon, S. J. Effect of W/C Rartio on Durability and Porosity in Cement Mortar with Constant Cement Amount, Advances in Materials Science and Engineering 2014, 11p. |
[16] | Bentz, D. P. Three‐Dimensional Computer Simulation of Portland Cement Hydration and Microstructure Development, Journal of the American Ceramic Society 1997, 80(1): 3-21. |
[17] | Felekoglu, B.; Türkel, S.; Baradan, B. Effect of Water/Cement on the Fresh and Hardened Properties of Self-Compacting Concrete, Building and Environment 2007, 42: 1795-1802. |
[18] | Fusco, P. B. Tecnologia do concreto estrutural: tópicos aplicados. São Paulo: Pini, 2008. 184p. |
[19] | Associação Brasileira de Normas Técnicas – ABNT. NBR 14931: Execução de estruturas de concreto – Procedimento. Rio de Janeiro, RJ, Brasil, 2004, 59p. |
[20] | Van Breugel, K. Simulation and Formation of Structure in Hardening Cement-Based Materials, PhD Thesis, Delft University of Technology 1991. |
[21] | Bentz, D. P. Three‐Dimensional Computer Simulation of Portland Cement Hydration and Microstructure Development, Journal of the American Ceramic Society 1997, 80(1): 3-21. |
[22] | Moreno, G.; Higa, T. C. S. Geografia de Mato Grosso: Território, Sociedade, Ambiente. Cuiabá: Entrelinhas, 2005. 296p. |
[23] | Strahler, A. H.; Strahler, A. N. Physical Geography: Science and Systems of the Human Environment. New York: Wiley, 2005, 794p. |
[24] | Associação Brasileira de Normas Técnicas – ABNT. NBR 12655: Concreto – Preparo, controle e recebimento. Rio de Janeiro, RJ, Brasil, 2015, 23p. |
[25] | Associação Brasileira de Normas Técnicas – ABNT. NBR NM 67: Concreto – Determinação da consistência pelo abatimento do tronco de cone. Rio de Janeiro, RJ, Brasil, 1998, 8p. |
[26] | Associação Brasileira de Normas Técnicas – ABNT. NBR 5738: Concreto – Procedimento para moldagem e cura de corpos de prova. Rio de Janeiro, RJ, Brasil, 2015, 9p. |
[27] | Associação Brasileira de Normas Técnicas – ABNT. NBR 5739: Concreto – Ensaio de compressão de corpos de prova cilíndricos. Rio de Janeiro, RJ, Brasil, 2018, 9p. |
[28] | Erdogdu, Sakir. Influence of retempering with superplasticizer admixtures on slump loss and compressive strength of concrete subjected to prolonged mixing, Cement and Concrete Research 2005, 35: 907-912. |