Pavana Kumara B. , Rowin D'Souza , Saakshath G. , Johnathan Bruce Fernandez , Jason Brenden D'Souza
Department of Mechanical Engineering, St Joseph Engineering College, Mangaluru, India
Correspondence to: Pavana Kumara B. , Department of Mechanical Engineering, St Joseph Engineering College, Mangaluru, India.
Email: |  |
Copyright © 2017 The Author(s). Published by Scientific & Academic Publishing.
This work is licensed under the Creative Commons Attribution International License (CC BY).
http://creativecommons.org/licenses/by/4.0/

Abstract
Many of our modern technologies require materials with unusual combination of properties that cannot be met by the conventional materials like metals, alloys, ceramics etc. For this purpose, a new class of materials known as composite materials are being used. Aluminium filled epoxy moulds have been used in indirect rapid tooling for a long time. These moulds, having a low processing cost, are very competitive when applied in the manufacturing of low volume series of plastic parts. The metallic filler is added to increase the thermal conductivity of the composite, while the glass fibres allow for the improvement of the wear resistance. The present work reports on abrasive wear behaviour of Aluminium Modified Epoxy and Glass fibre composite with 5wt% and 10wt% of Aluminium particles. Results showed that addition of Aluminium particles is beneficial for low abrasive conditions.
Keywords:
Composite Material, Wear Study, Glass Fibre, Epoxy, Aluminium
Cite this paper: Pavana Kumara B. , Rowin D'Souza , Saakshath G. , Johnathan Bruce Fernandez , Jason Brenden D'Souza , Abrasive Wear Performance of Aluminium Modified Epoxy-Glass Fibre Composites, International Journal of Materials Engineering , Vol. 7 No. 3, 2017, pp. 55-60. doi: 10.5923/j.ijme.20170703.03.
1. Introduction
The composite materials have been used by mankind for several hundred years to improve the quality of life. But it is hard to understand the fact that how man used the bricks to make sturdier houses by stacking them in line hence making strong buildings that lasted for a long time. Composite materials are extending the horizons of designers in all branches of engineering, and yet the degree to which this is happening can easily pass unperceived. The simple term composites give little indication of the vast range of individual combinations that are included in this class of materials. The loose definition of composites is materials composed of two or more distinctly identifiable constituents. In composites, materials are combined in such a way as to enable us to make better use of their virtues while minimizing to some extent the effects of their deficiencies. This process of optimization can release a designer from the constraints associated with the selection and manufacture of conventional materials. Fibers or particles embedded in matrix of another material would be the best example of modern-day composite materials, which are mostly structural. Composite materials have many characteristics that differ from those of conventional engineering materials. Although some characteristics are merely a modification of conventional behaviour, others are totally new and require new analytical and experimental procedures [1]. Composite materials are often heterogeneous and anisotropic. The fibers can be combined with most conventional resins to obtain excellent properties. Many researchers have analysed different properties of polymer composite materials. Xiang Zhang et al. [2] studied the tribological and mechanical properties of glass fibre reinforced paper-based composite friction material. It was resulted that the shear strength increased initially and then decreased, but the compressibility increased and the recovery decreased as the glass fibre content increased. The friction torque of the sample with 10wt% glass fibers was flatter during the mixed asperity contact phase of the engagement, while the friction coefficient was higher and the wear rate was lower compared with other samples. B. Suresha et al. [3] studied the role of fillers on friction and slide wear characteristics in glass-epoxy composite systems. The coefficients of frictional values show an increasing trend with subsequent increase in load/sliding velocities. It was observed that the Graphite filled G-E composite shows lower coefficient of friction than the other two composites irrespective of variation in the load/sliding velocities. SiC filled G-E composite exhibited the maximum wear resistance. N.S El-Tayeb et al. [4] studied the friction and wear properties of E-glass fibre reinforced epoxy composites under different sliding contact conditions. Friction and wear experiments were conducted in the normal direction of the fibre orientation against a cylindrical counter face using a pin on ring technique for different sliding surface conditions. Improvement in friction coefficient and wear rate were observed when sliding took place against either clean or wet counter face.Composites are finding increased use in aerospace, automotive, marine and civil infrastructure applications. In recent years, polymer, metal and hybrid composites are extensively utilized in tribological components such as cams, brakes, bearing and gears because of their self-lubrication properties, lower friction and better wear resistance [5]. More and more composites are now being used as sliding components, which were formerly composed of only metallic materials. Still, developments are underway to explore other fields of application for these materials and to tailor their properties for extreme load-bearing and environmental temperature conditions [6,7].The objective of present work is to develop and characterize a new class of composites with a polymer called epoxy as the matrix and Glass as reinforcement and aluminium as filler. Further investigation of this composite material on its abrasive wear properties and introduce a new class of functional hybrid composites suitable for tribological applications.
2. Experimental Setup
2.1. Materials
The various materials that have been used for the processing of the composite materials is given below.Pr 257 is the epoxy resin that was used for the processing of the composites in the present test. The hardener used for the Pr 257 epoxy resin was Aradur 140.Glass fibre is the reinforcement used in this study. Its main function is to influence the properties of the composites into which it is incorporated. E-Glass fibre type is used in this study. E-Glass is a low alkali glass with a typical nominal composition of SiO2 54wt%, Al2O3 14wt%, CaO+MgO 22wt%, B2O3 10wt% and Na2O+K2O less then 2wt% [4].Aluminium is used as filler material in this study. Aluminium metal is procured from HI-TECH agency. Addition of Aluminium powder in epoxy glass fiber composite increases the thermal conductivity of the composite. Thereby improving the wear resistance of composite [8].There are several techniques for the preparation of polymer matrix composites. Out of these the hand lay-up technique is the simplest and most widely used technique for the processing of the composites. [9]. The hand lay-up setup consists of 2 finely polished rectangular plates. The dimensions of plate used were 200mm×200mm×10mm. This was very essential to obtain a good surface finish in the composite materials casted.
2.2. Samples for Testing
Once the composite materials had been prepared, the next important step is to cut them into test samples of sizes according to the ASTM standards. Cutting is carried out using a 24TPI hacksaw blade. Many samples of each type were cut and prepared for each of the tests. The list of ASTM standards used is mentioned in the Table 1.Table 1. ASTM standards for density and wear measurement 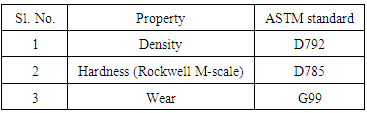 |
| |
|
2.3. Testing
Once the composite materials have been prepared and cut to the required shape using ASTM standards they are then used for testing. The test has been carried out in a Wear and Friction Monitor DUCOM TR-210C commonly known as Pin-on-disc machine as shown in Figure 1.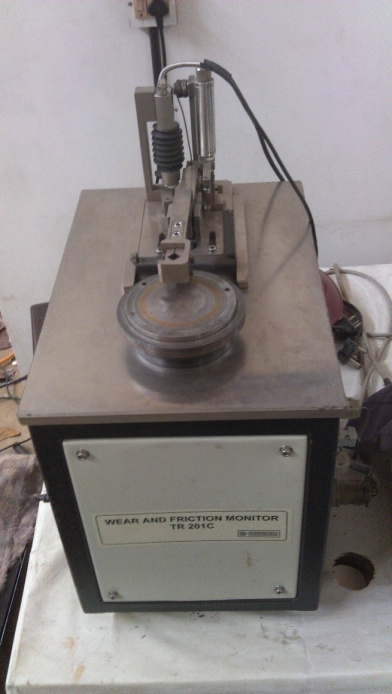 | Figure 1. Pin on disc setup |
3. Results and Discussion
3.1. Density
The densities of the composites were measured by the displacement method based on Archimedes’s principle. In this method distilled water is taken in the measuring jar having graduations in millimetres and the initial level of water is noted. Then each of the samples is weighed using an electronic balance of AY220 type. The weighed samples were then dropped into the water in the measuring jar. This resulted in the rise in water level. The final level of water is noted and the difference in initial and final reading gives the volume of samples dropped into it. The ratio of weight of sample to its volume as obtained by the above procedure yielded the density of the composites.The result of above experiment is plotted in the form of graph as shown in the Figure 2. The density of EG0 is found to be least. But the density of its composite EG5 had a 12.9% increase in its density. The density of EG10 is found to be 19.88% greater than EG0 and 6.17% greater than EG5.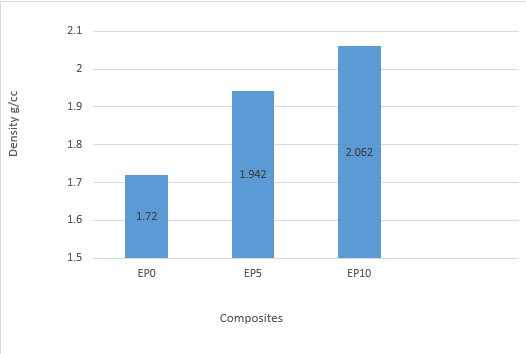 | Figure 2. Densities of different composite specimens |
3.2. Wear Properties
3.2.1. Effect of Load on Coefficient of Friction (COF)
The result of COF of various composites with respect to load at constant speed is displayed in the Figure 3. The COF increases with load for samples EG0, EG5 and EG10. But it increases initially for 5N to 10N and then decreases for 15N. Various other research on filled polymer composites reflect similar kind of result. Xiang Zhang et al. [2] studied the tribological and mechanical properties of glass fiber reinforced paper-based composite friction material. They found that the friction torque of the sample with 10wt% glass fibers was flatter during the mixed asperity contact phase of the engagement, while the friction coefficient was higher and the wear rate was lower compared with other samples.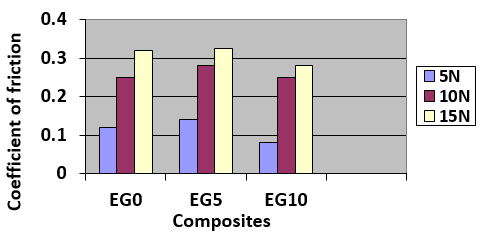 | Figure 3. Variation of COF for different loads (60m and 600 paper) |
3.2.2. Effect of Sliding Distance on Coefficient of Friction
The effect of sliding distance on COF is shown in Figure 4. It is observed that the COF decreases for sample EG0 and EG5. But for the sample EG10 there is a sudden decrease in COF and then it increases. It increases and then decreases for 20m, 40m and 60m sliding distances. | Figure 4. Variation of COF for different sliding distance (15N and 600 paper) |
3.2.3. Effect of Load on Wear Loss
Effect of load on wear loss is illustrated in the Figure 5. The wear loss increases as the load increases for each sample. It is also observed that for epoxy glass fiber composites the wear loss is maximum at highest load and goes on decreasing as the filler is added.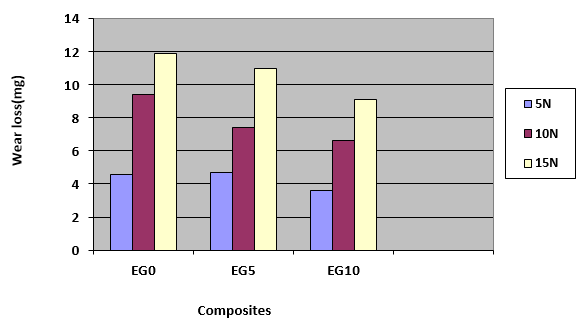 | Figure 5. Variation of wear losses for different loads (60m and 600 paper) |
3.2.4. Effect of Sliding Distance on Wear Loss
Effect of sliding distance on wear loss is shown in Figure 6. It is observed that the wear loss increases with the increase in sliding distance for the samples EG0 and EG5. It is observed that the wear loss for epoxy glass fiber composite is found to be higher than the epoxy glass fiber Aluminium composite. The wear loss for sample EG10 is maximum for 20m sliding distance and it decreases steadily with the increase in the sliding distance. The wear loss decreases for 40m and 60m for all the samples. 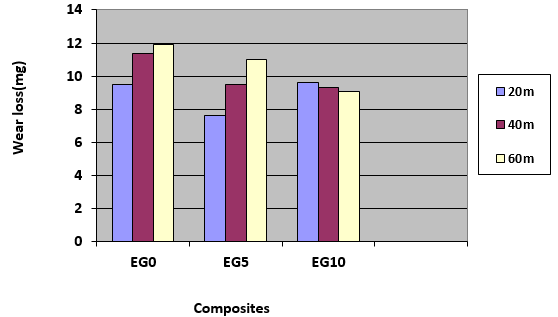 | Figure 6. Variation of Wear losses for different sliding distances (15N and 600 paper) |
3.2.5. Effect of Load on Specific Wear Rate
The result of specific wear rate of various composites with respect to load (5, 10 and 15N) at constant speed is displayed in the Figure 7. The specific wear rate reduces with the increase in load for EG5 and EG10, and it shows a varying trend for EG0. Specific wear decreases for all the sample for all three (5, 10 and 15N) loads.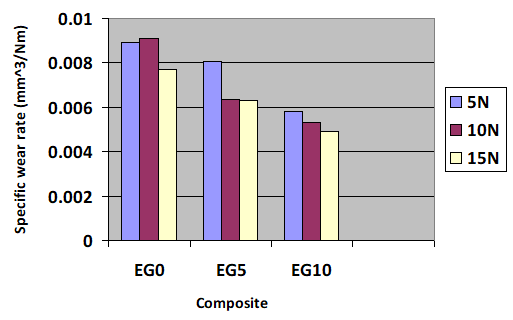 | Figure 7. Variation of wear losses for different grit size papers (60m and 15N) |
3.2.6. Effect of Sliding Distance on Specific Wear Rate
The effect of sliding distance on specific wear rate is shown in Figure 8. It is clear from the figure that the specific wear rate decreases for all the samples. It is observed that the specific wear rate decreases for sliding distances 40m and 60m for all the samples. But it shows varying trend for sliding distance 20m.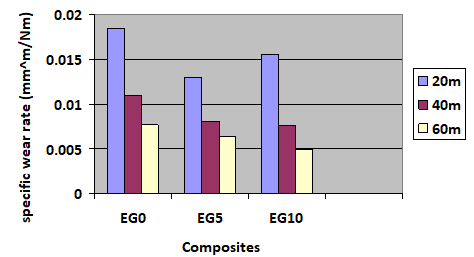 | Figure 8. Variation of wear losses for different grit size papers (60m and 15N) |
3.3. Worn Surface Morphology
The worn surfaces of specimen were examined by scanning electron microscope. The morphology of worn surface of epoxy glass fibre matrix and composites with different percentage of aluminium particles are shown in the Figures 9 to Figures 11. Worn surface of EG0 for 320 grit size is shown in Figure 9. From Figure 9(a), the arrow mark shows the direction of sliding. It is further noticed that there is ploughing marks on the surface of the sample. This is due to the coarser grain particles in the abrasive paper. From Figure 9(b), the scar marks are wide because of the coarser grain particles.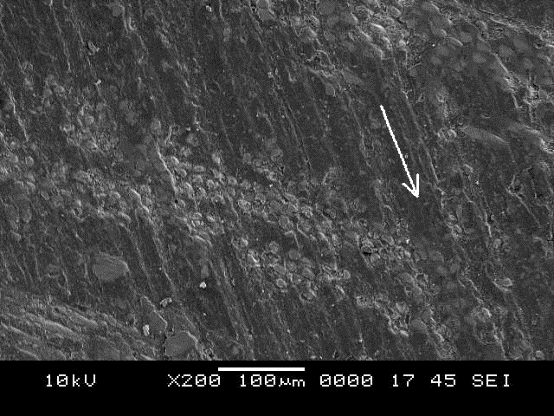 | Figure 9. (a) Variation of specific wear rate for different grit size (15Nand 60m) |
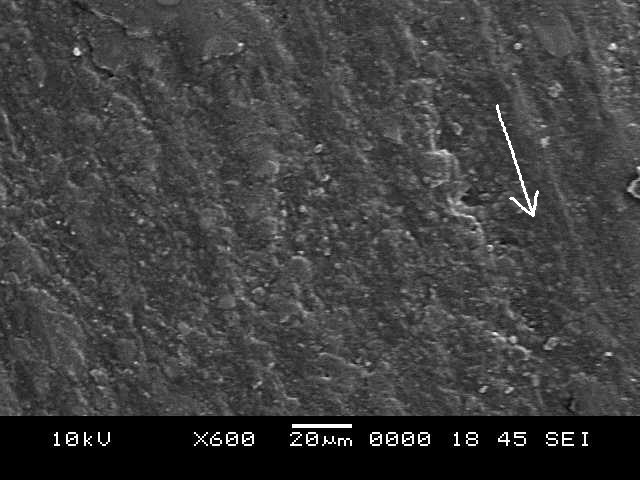 | Figure 9. (b) Variation of specific wear rate for different grit size (15N and 60m) |
 | Figure 10. (a) Variation of specific wear rate for different grit size (15N and 60m) |
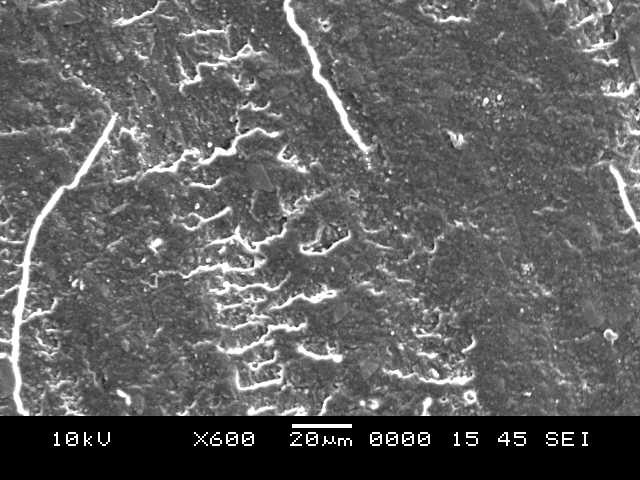 | Figure 10. (b) Variation of specific wear rate for different grit size (15N and 60m) |
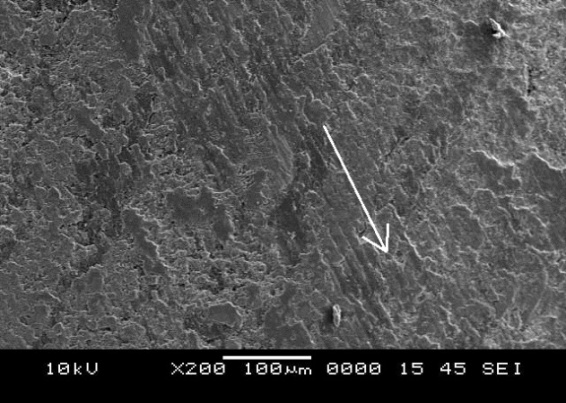 | Figure 11. (a) Variation of specific wear rate for different grit size (15N and 60m) |
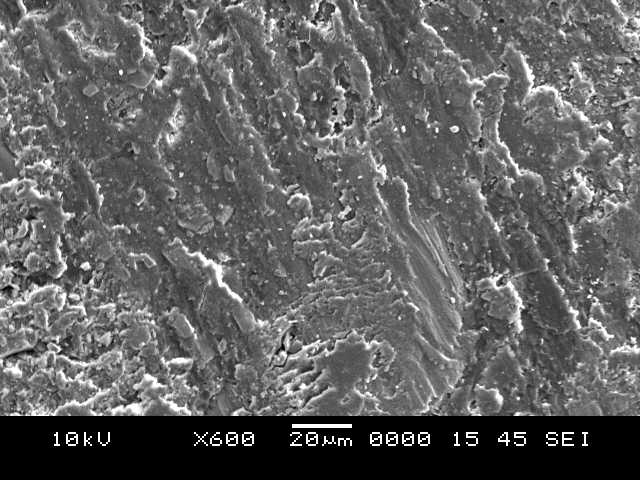 | Figure 11. (b) Variation of specific wear rate for different grit size (15N and 60m) |
4. Conclusions
The processing of epoxy glass fiber and aluminium reinforced composites is successfully performed using hand lay-up technique. The wear behaviour of epoxy glass fibre and aluminium reinforced composites is examined for different conditions like normal load and sliding distance. Based on the results of the study the following conclusions were drawn. The addition of filler to the epoxy glass fibre composite resulted in increase of density. This is an expected result as the high dense filler increase the density of the composites. Addition of Aluminium fillers into epoxy glass fibre composites resulted in the increase in hardness for EG5. For EG10 decrease in hardness is observed. The abrasive wear loss of epoxy glass fiber and aluminium reinforced composites showed a decreasing trend for all the loads (5, 10 and 15N). Abrasive wear loss shows a decreasing trend for sliding distance. Whereas sudden increase is observed for EG10. This shows that optimum percentage of Aluminium powder to be used for preparing composite lies between 5 to 10%. Specific wear rate shows similar trend to abrasive wear loss. The decrease in wear loss is due to the addition of aluminium which increases the thermal conductivity of the composite. The addition of filler content to epoxy glass fiber composite is beneficial for abrasive conditions (150, 320 and 600 grit size). But a varying trend is observed for coefficient of friction for all the test conditions employed. Thus, we can conclude that the performance of aluminium reinforced epoxy glass composite is better compared to that of epoxy glass composite for abrasive wear conditions.SEM studies of worn surface indicates cracking and ploughing wear mechanism under all experimental conditions.
References
[1] | H.J. Kim, “Enhancement of mechanical properties of aluminium/epoxy composites with silane functionalization of aluminium powder,” Composites part B, vol. 43, pp. 1743-1748, 2012. |
[2] | Xiang Zhang, Ke-Zhi Li., “Tribological and mechanical properties of glass fibre reinforced paper-based composite friction material,” Tribology international, vol. 69, pp. 156-167, 2014. |
[3] | B. Suresha, “The Role of Fillers on Friction and Slide Wear Characteristics in Glass-Epoxy Composite Systems,” Journal of Minerals & Materials Characterization & Engineering, Vol. 5, pp. 87-101, 2006. |
[4] | N.S El-Tayeb, R.M Gadelrab, “Friction and wear properties of E-glass fibre reinforced epoxy composites under different sliding contact conditions,” Wear, vol. 192, pp. 112-117, 1996. |
[5] | N.S.M El-Tayeb, B.F Yousif, “Evaluation of glass fibre reinforced polyester composite for multi-pass abrasive wear application,” Wear, vol. 262, pp. 1140-1151, 2007. |
[6] | Hasim Pihtili, Nihat Tosun, “Investigation of the wear behaviour of a glass-fibre-reinforced composite and plain polyester resin,” Composite science and technology, vol. 62, pp. 367-370, 2002. |
[7] | Hasim Pihtili, “An experimental investigation of wear of glass fibre-epoxy resin and glass fibre-polyester resin composite materials,” European polymer journal, vol. 45, pp. 149-154, 2009. |
[8] | P.V. Vasconcelos, “Impact fracture study of epoxy-based composites with aluminium particles and milled fibres, Journal of Materials Processing Technology, vol. 170, pp. 277-283, 2005. |
[9] | S. Basavarajappa, “Effect of Filler Materials on Dry Sliding Wear Behavior of Polymer Matrix Composites,” Journal of Minerals & Materials Characterization & Engineering, Vol 8, pp. 379-391, 2009. |
[10] | A. Mimaroglu, H. Unal, T.Arda, “Friction and wear performance of pure and glass fibre reinforced poly-ether-imide on polymer and steel counterface materials,” Wear, vol. 262, pp. 1407-1413, 2007. |
[11] | N. Mohan, S. Natarajan, “Abrasive wear behaviour of hard powders filled glass fabric-epoxy hybrid composites,” Materials and design, vol. 32, pp. 1704-1709, 2011. |
[12] | B. Suresha, G Chandramohan, “Mechanical and three body abrasive wear behaviour of three-dimensional glass fabric reinforced vinyl ester composite,” Materials Science and Engineering A, vol. 480, pp. 573-579, 2008. |