Abhishek Sharma1, K. C. Swami2
1Jagannath Gupta Institute of Engineering & Technology, Jaipur, India
2Malaviya National Institute of Technology, Jaipur, India
Correspondence to: Abhishek Sharma, Jagannath Gupta Institute of Engineering & Technology, Jaipur, India.
Email: |  |
Copyright © 2017 Scientific & Academic Publishing. All Rights Reserved.
This work is licensed under the Creative Commons Attribution International License (CC BY).
http://creativecommons.org/licenses/by/4.0/

Abstract
In the present investigation, pulsed dc glow discharge plasma nitriding process on the AISI 1045 steel has been carried out at three different temperatures i.e., at 450°C, 475°C and 500°C for 10 hrs duration in order to achieve good nitride results. The microstructure of the base material and the nitrided layer has been examined by X-ray diffraction. Hardness property has been investigated for both un-nitrided and plasma-nitrided materials. It is observed that the microstructure of the core material remains unaltered and Iron Nitride is formed in the hardened surface layer after plasma nitriding at all the three temperatures employed. Surface hardness increases substantially after plasma nitriding. Surface hardness increases with the increase in plasma nitriding temperature due to greater diffusivity at higher temperatures.
Keywords:
Glow discharge plasma, Nitriding process, AISI 1045 steel, Surface hardness & XRD
Cite this paper: Abhishek Sharma, K. C. Swami, Pulsed DC Glow Discharge Plasma Nitriding Process on the AISI 1045 Steel, International Journal of Materials Engineering , Vol. 7 No. 1, 2017, pp. 12-16. doi: 10.5923/j.ijme.20170701.02.
1. Introduction
The main objective of nitriding is to increase the hardness of the component surface by enriching it with nitrogen [1-6]. The most significant advantage associated with the nitriding process is that it does not require a phase change from ferrite to austenite or from austenite to martensite of the base steel component. The bulk of the material under nitriding treatment remains in the same phase during the complete procedure [1]. The bond structure in transition metal nitrides consists of a mixture of covalent, metallic and ionic components, and is responsible for high hardness, excellent wear resistance, chemical inertness, good electrical conductivity and superconducting properties. A number of processes are available by which a wide variety of alloys can be nitride. Number of reports on this process has been published [4-9].In this paper, we have taken AISI 1045 plain carbon steel. Plain carbon steel is the most frequently used steel. A typical application for carburized plain carbon steel is for parts with hard wear resistant surface, e.g., small shafts, plunges, or highly loaded gearing. In this study, plasma nitriding parameters were examined to reveal optimal nitriding conditions originating from gas mixture, temperature and process time.
2. Experimental Procedure
2.1. Materials and Sample Preparation
Plain carbon steel AISI 1045 was selected for the present study and its chemical composition are shown in the table 1. Table 1. Chemical composition of the alloy AISI 1045 (wt. %) 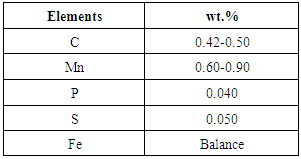 |
| |
|
The samples were in cylindrical shaped of height 5 mm (approx.). Samples were initially polished to give a mirror finish appearance. Before plasma nitriding, the prepared samples were ultrasonically cleaned with acetone and dried. All the samples were plasma nitrided in three batches using three different temperatures with the same gas composition.
2.2. Plasma Nitriding Process
This process was carried out in a 500 mm diameter and 500 mm height bell shaped stainless steel vacuum chamber. Mechanically prepared sample of AISI 1045 steel was mounted on the sample holder of the vacuum chamber. Initially, the vacuum chamber was evacuated to a base pressure of 0.05 mbar by a rotary pump [Fig. 1]. The samples were first sputter cleaned using N2–H2 gas mixture in 25%:75% ratio. The gas flow rate was controlled by the butterfly valves mounted on the vacuum chamber to maintain a pressure of 1 mbar. Plasma was generated using a D.C. pulsed power supply. 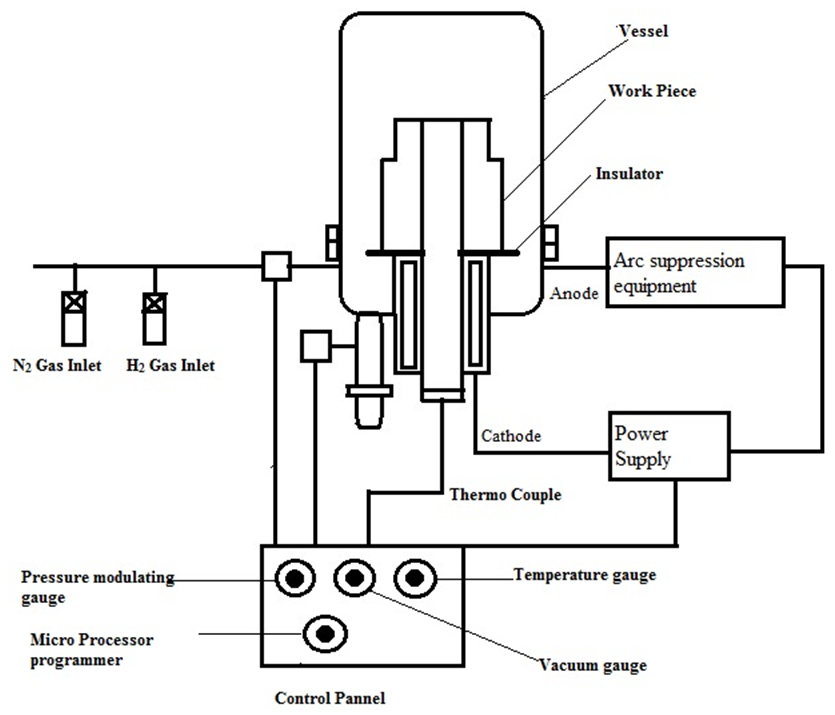 | Figure 1. Schematic of Plasma nitriding Set up |
Sputter cleaning process was performed for 1 h at 250°C to remove the native oxide layer and contamination so as to expose a fresh surface of the samples for plasma nitriding. The temperature of the samples was monitored with a Fe-Constantan-Fe thermocouple (J-type), which is attached to the sample holder through the tubularsupport. There is an error of ±5°C in the temperature readings. After completing the sputter cleaning process, the mixture of nitrogen and hydrogen gas was introduced in the reactor for plasma nitriding. Plasma nitriding was carried out using three different temperatures 450°C, 475°C and 500°C at same gas mixtures (25% N2 and 75% H2) under a pressure of 4.5 mbar for 10 hrs. After 10 hrs these nitrided samples were cooled in vacuum chamber under the flow of the gas mixture till the temperature decreased to 150°C. This is mostly done to eliminate formation of oxide layer on the surface of the samples.After plasma nitriding process, test parts were cut cross-sectional and examined using Vicker’s Hardness method throughout the cutting surface. Microhardness of samples before and after plasma nitriding process has beenmeasured. Hardness measurements were performed on nitrided surfaces with a Leitz Vickers Hardness tester using a load of 100g. X-Ray diffraction of the samples was performed on SEIFERT XRD 3000PTS X-ray diffractometer manufactured by Rich Seifert & Company, Germany, using a Cu–Kα (λ=1.5418 A˚) source in the Bragg–Brentano mode. A graphite crystal monochromator was used for the glancing incidence (GI) mode.
3. Results and Discussion
The results obtained from hardness and nitrided layer measurements are exhibited in Table 2. At same nitriding time and three different temperatures have resulted in change of hardness and case depth of nitrided layer as well. The change in thickness of nitrided layer will probably provide superior service life.Table 2. Test results of hardness and layer thickness measurements 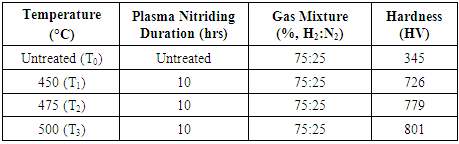 |
| |
|
This study has shown that the characteristics of nitrided layer could be modified in a wide range. These results have shown that at same Plasma Nitriding Time and Gas Mixture hardness increases as we increase the temperature. Although the hardest nitraded layer was obtained at 500°C, 75% H2+25% N2 gas mixture and 10 hours duration, for AISI 1045 steel. These results are exhibiting properties that can be applied to different service conditions providing production economy due to the amount of H2 in gas mixture where depth of nitrided layer is more desirable compared to higher hardness.The hardness profiles of nitrided cases are given in above Fig 2. The surface hardness of specimensincreases as temperature increases, while the core hardness remains unchanged. The combination of high kinetic energy of ions with the thermal activation results deeper penetration in plasma nitriding. The effect of surface cleaning of steels by glow discharge of H2 is another important feature of plasma treatment [12, 14]. As a result of both effects, it was concluded that the activation energy of ion nitriding was lower than conventional techniques, allowing higher penetration rates [16].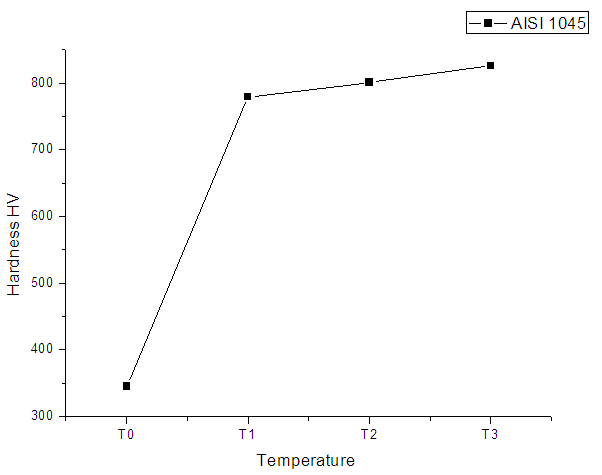 | Figure 2. Hardness curve for AISI 1045 |
The X-ray diffraction patterns measured at the surface of the specimens are given in Fig. 3. In Fig. 3 we show the glancing incidence XRD patterns of the untreated AISI 1045 compared with the modified surface taken at 2° incidence angle. While the pattern for the untreated sample (Fig. 3a) shows the α-Fe peak, the treated surface shows peaks in addition to that of α-Fe, which are assigned to hexagonal ε-Fe3N (Fig. 3b, 3c, 3d). The broad peak could be due to phase of ε-Fe3N which we confirm with higher resolution XRD studies. It is also noted that the asymmetry in the α-Fe peak is due to hexagonal ε-Fe3N. This is clearly seen in all three XRD patterns (Fig. 3b, 3c, 3d). We find no evidence of any other phase within the sensitivity of the technique, which probes <1 micron of the surface in GIXRD. 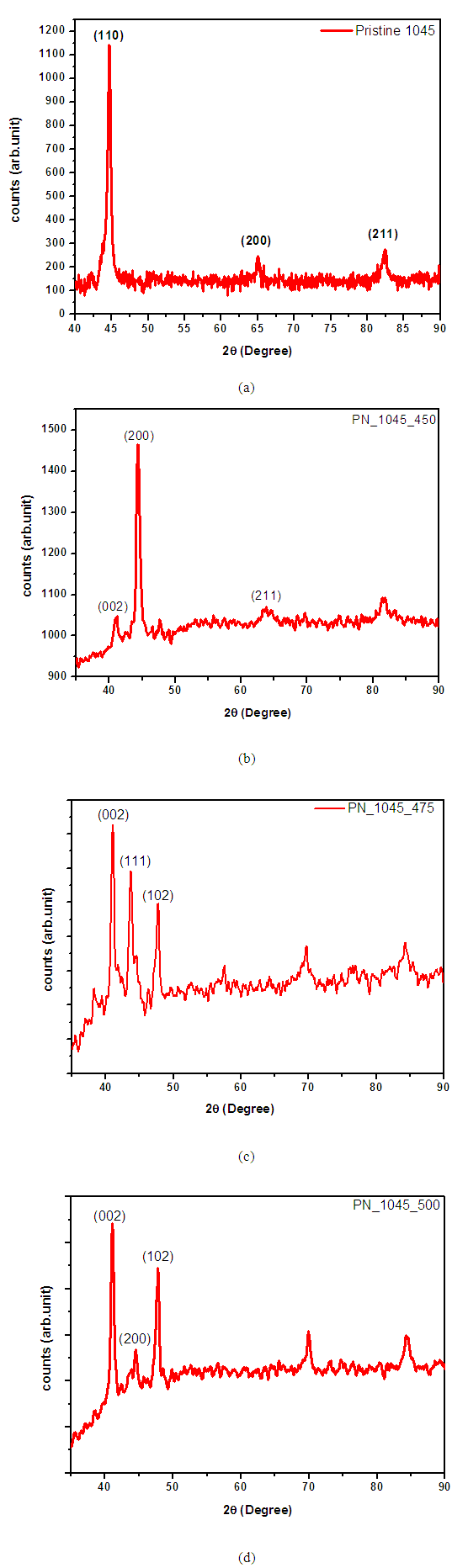 | Figure 3. Glancing-incidenceX-ray diffraction patterns ofAISI 1045, (a) untreated sample and plasma-nitrided (b) at 450°C, (c) at 475°C, (c) at 500°C |
4. Conclusions
In conclusion we have obtained plasma nitrided AISI 1045 with predominantly epsilon-Fe3N phase on the surface. The broad peak of Fe3N confirms nitride phase formation. The Hardness profiles indicate a direct relation of the increased surface micro hardness in plasma nitrided AISI 1045 to the nitride phase formation in the nitride layer.
References
[1] | Metals Handbook, Heat Treating, Vol. 4, American Society for Metals, Metals Park, 9th edn, 1981, p.191. |
[2] | B. Edenhofer, Metall. Mater. Tech. (1976) p.421. |
[3] | B. Edenhofer, Met. Prog., 109(3), (1976) (38). |
[4] | W.D. Soccorsy and W.T. Ebihara, Tech. Rep. RE 70-156, 1970 (Science and Technology Laboratory, Rock Island, IL). |
[5] | P.C. Jindal, J. Vat. Sci. Technol., 15 (1978) 313. |
[6] | R.M. Lerner, J. Iron Steel Inst., London, 210 (1972) 631. |
[7] | B. Edenhofer and T.J. Bewley, in P.M. Unterweiser (ed), Heat Treatment 76, American Society for Metals, Metals Park, OH, 1977, p.7. |
[8] | M. Hudis, J. Appl. Phys.. 44 (1973) 1489. |
[9] | V.A. Phillips and A.U. Seybolt, Trans. Metall. Sot. AIME, 242 (1968) 2415. |
[10] | S. Mandl, R. Gunzel, E. Richter, W. Moller, Surf. Coat. Technol, 100–101 (1998) 372. |
[11] | W. Liang, X. Bin, Y. Zhiwei, S. Yaqin, Surf. Coat. Technol. 130(2000) 304. |
[12] | J.G. Conybear, Ind. Heating 59 (1992) 53. |
[13] | M.F. Danke, F.J. Worzala, J. Sci. Forum 102–104 (1992) 259. |
[14] | J.S. Murday, I.L. Singer, J. Vac. Sci. Tech. 17 (1986) 327. |
[15] | Z.M. Zheng, B.Y. Tang, P.K. Chu, X.B. Tian, S.Y. Wang, X.F. Wang, J. Vac. Sci. Tech. B 17 (2) (1999) 851. |
[16] | D.C. Kothari, M.R. Nair, A.A. Rangwala, K.B. Lal, P.D. Prabhawalkar, P.M. Raole, Nucl. Instrum. Methods B 1/8 (1985) 235. |