Thaweesak Tanaram1, Nuttee Thungsuk2, Harittapak Apirat3, Narong Mungkung4, Yoshimi Okamura5, Toshifumi Yuji5
1Faculty of Industrial Technology, Pibulsongkram Rajabhat University, Phitsanulok, Thailand
2Department of Electrical Engineering, Dhonburi Rajabhat University Samut-Prakan, Samut-Prakan, Thailand
3Faculty of Science and Technology, Dhonburi Rajabhat University, Thailand
4Department of Electrical Technology Education, King Mongkut's University of Technology Thonburi, Bangkok, Thailand
5Faculty of Education & Culture, University of Miyazaki, Miyazaki, Japan
Correspondence to: Nuttee Thungsuk, Department of Electrical Engineering, Dhonburi Rajabhat University Samut-Prakan, Samut-Prakan, Thailand.
Email: |  |
Copyright © 2016 Scientific & Academic Publishing. All Rights Reserved.
This work is licensed under the Creative Commons Attribution International License (CC BY).
http://creativecommons.org/licenses/by/4.0/

Abstract
This research paper aims to present the development of low-pressure high-frequency plasma chemical vapor deposition system for preparation of Zinc oxide (ZnO) thin film on silicon wafer, B-doped p-type Si (100) wafer, with powder deposition. The plasma system for this experimental used mixture of argon (Ar) and oxygen (O2) gas at 10 L/min. and 2 L/min., respectively. The ZnO thin film was performed by heating the ZnO powder. The Ar and O2 gas have been heating in pipe with silicone belt heater and micro gas heater. The temperature was controlled by temperature control (PID). The ZnO thin film was investigated by using contact angle meter and scanning electron microscope (SEM) to confirm the formation of ZnO thin film on the substrate. The results from the contact angle meter confirmed that the Si wafer with ZnO thin film showed an increased in hydrophobic property compared to the traditional Si wafer. In addition, the results from SEM confirmed that the formation of ZnO thin film on surface was in typical pyramid shape structure with crystal grain size about 100–120 nm.
Keywords:
Zinc Oxide, Plasma CVD, Scanning electron microscope (SEM), Thin film
Cite this paper: Thaweesak Tanaram, Nuttee Thungsuk, Harittapak Apirat, Narong Mungkung, Yoshimi Okamura, Toshifumi Yuji, Preparation of ZnO Thin Film by Development Low-Pressure High-Frequency Plasma Chemical Vapor Deposition System, International Journal of Materials Engineering , Vol. 6 No. 5, 2016, pp. 155-158. doi: 10.5923/j.ijme.20160605.03.
1. Introduction
Zinc Oxide (ZnO) has been interesting in the cluster of semiconductor because of many advantages such as high transmission and a good conductor [1]. ZnO is N-type semiconductor with a wide band gap material, 3.37 eV direct band gap at room temperature, and a high excitation binding energy of 60 meV [2]. Therefore, the ZnO was applied to use as transducers, luminescent materials, transparent conductors, photo detectors, heat mirrors, varistors, optical modulator waveguides, gas sensors and solar cells [3, 4].There are many systems from ZnO thin film such as chemical vapor deposition, Radio-frequency (RF) magnetron sputtering, spray pyrolysis, pulsed laser deposition, sol–gel-dip-coating, electro-deposition, metal–organic chemical vapor deposition (MOCVD), molecular beam epitaxy(MBE) [5, 6]. The most popularsystem for thin film formation is RF- magnetron sputtering but the disadvantage of this system is imperfection of film structural and instability of the electrical properties of the film [7]. On the other hand, plasma chemical vapor deposition (Plasma CVD) can from the thin film complety at low temperature [8].In this research, the development low-pressure high-frequency plasma chemical vapor deposition system for preparation of ZnO thin film on silicon wafer B-doped p-type Si (100) wafer was presented. The plasma equipment with suitable for ZnO thin film formation was developed. The ZnO thin film was simply investigated using contact angle meter and scanning electron microscope (SEM) for basic analysis of ZnO thin film.
2. Experimental Setup
Fig. 1 Shows the system of low-pressure high-frequency plasma chemical vapor deposition for preparation of ZnO thin film. The main component of plasma CVD system were plasma chamber, matching box, RF-power, vacuum pump, gas heater, ZnO powder, Temperature control, mass flow controller and gas supply. The vacuum chamber of plasma CVD system was composed of stain steel (SUS316), with a diameter of 430 mm and high of 180 mm. The diameter of the electrode for generating plasma process was 200 mm. The distance between upper and lower plasma electrodes was 20 mm. The showerhead and gas distribution plate had 145 fine pores arranged in the shape of grid. The distance between each pore was 12 mm. The diameter of each pore was 1.0 mm. 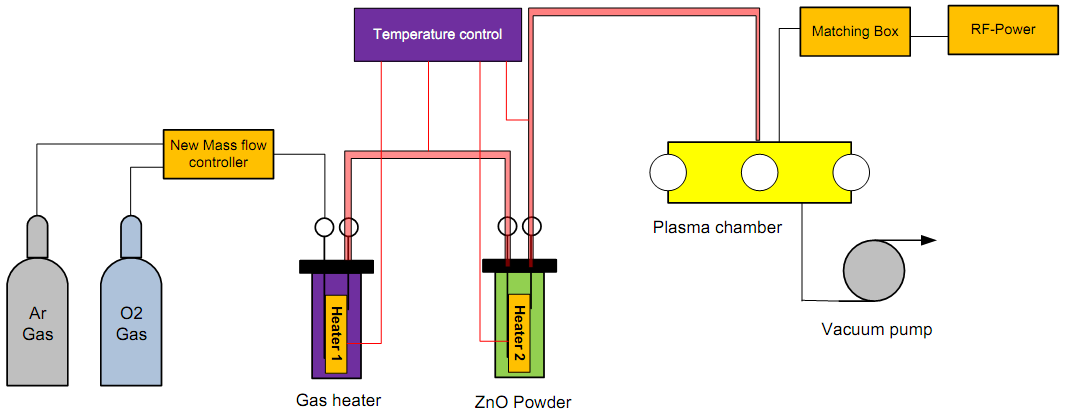 | Figure 1. The system of low-pressure high-frequency plasma CVD for preparation of ZnO thin film |
The electrode had a structure that allowed the formation of uniform thin film to be deposited after the vapor spreading to form a metallic thin film at low temperature while the lower electrode served as a ground. The substrate heater had contained the lower electrode in vacuum chamber of plasma CVD system. The port for exhaust gas, which was a fundamental structure in plasma equipment, was installed in the vacuum chamber at the side surface of the system. Inside the vacuum chamber was maintained at constant temperature during plasma deposition by flowing of cooling water onto the outer wall portion of the reactor.An argon and oxygen tanks were installed with mass flow controller for mixing the two gases. Heater and sensor for measurement of temperature were installed at 4 points, gas heater, ZnO powder source, gas pipeline between gas heater and ZnO powder source and gas pipeline between ZnO powder source and plasma chamber. The heater at a gas pipeline was 50 W. silicone belt heater with 10 mm. insulator for maintained the temperature. The 120 W. Taika-Taika Co.,Ltd model CL heater was installed at the outside of the ZnO powder source, for temperature control and forwarding powder to chamber for thin film formation in the plasma process. The 500 W. micro gas heater type MCA-500E was used to increase the temperature at low-pressure high-frequency plasma chemical vapor deposition system for ZnO thin film formation. All heaters in the system were measured by thermocouple sensors. The temperature controlled by 4 temperature control (PID), Panasonic Co., Ltd type KT4H. The temperature can be set at different temperature for each controlled point.The experiment used silicon wafer B-doped p-type Si (100) wafer for ZnO thin film formation. The effect of the gas mixture between argon and oxygen on the ZnO thin film formation was studied at the gas flow rate of 10 L/min. and 2 L/min., respectively. During the preparation of ZnO thin film, 300 W. RF-power was used for 10 min to deposit the ZnO thin film and the pressure in vacuum chamber was 3.5102 Pa. for all condition of experiments. In the experimental, the heating system at the lower electrode of silicon wafer with low-pressure high-frequency plasma chemical vapor deposition was adjusted between 100–300C during deposition. The formation of ZnO thin film was investigated using contact angle meter from Kyowa Interface Science Co.,Ltd (Type CA-D) to measure an angle of water droplet from hydrophobic properties. In addition, thin film was also investigated using a scanning electron microscope (SEM) to analyze the surface morphology of the ZnO thin films.
3. Results and Discussion
Fig. 2 shows plasma emission in vacuum chamber during ZnO deposition by low-pressure high- frequency plasma CVD method at eyehole width of 75 mm. the area between upper and lower plasma electrode of 20 mm. Fig. 2a shows plasma phenomenon from ZnO powder source during ZnO deposition at the plasma power of 300 W., vacuum level of 3.2×102 Pa., temperature of 300C and Ar gas flow rate of 10 L/min. while Fig. 2b shows plasma phenomenon at gas mixture of Ar and O2 gas at 10 L/min. and 2 L/min., respectively when plasma power, vacuum level and temperature was maintained. The plasma phenomenon in Fig. 2a and Fig. 2b were different from the observation with bare eyes. Fig. 2a and Fig. 2b showed plasma color in blue and red, respectively. It was found that when increasing ZnO powder source with the mixture of Ar and O2 gas into low-pressure high- frequency plasma CVD method resulted in plasma phenomenon was red color, in addition non ZnO powder source when surface treatment with the mixture of Ar and O2 gas only was violet color [9].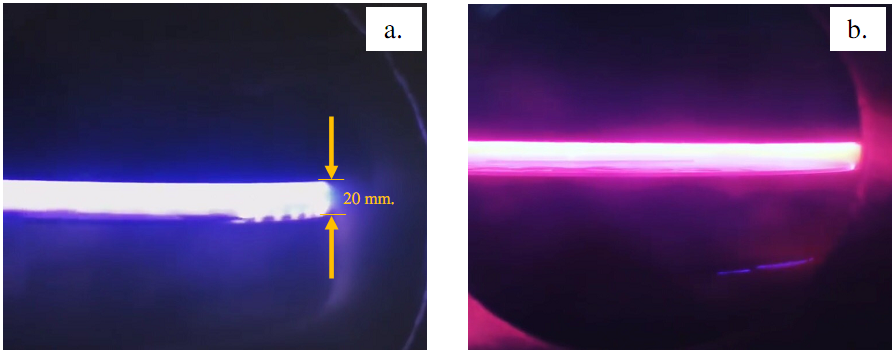 | Figure 2. Plasma phenomenon a) Ar gas flow rate b) a mixture of Ar and O2 gas |
Fig. 3 shows the action of a water droplet dropped down onto a B-doped p-type Si (100) wafer with contact angle meter using the θ/2 method with the 1 μL. pure water droplet. Fig. 3a and Fig. 3b were the change of a water droplet of the original silicon wafer surface and the surface of ZnO thin film on silicon wafer from low-pressure high-frequency plasma chemical vapor deposition system under the condition as in Fig 2b, respectively. It was found that the contact angle of original silicon wafer surface and surface of ZnO thin film from plasma deposition was 35.8 and 81.1 degree, respectively. The hydrophobic properties at the surface of ZnO thin film increased from the plasma deposition. The contact angle of the original silicon wafer surface and surface of ZnO thin film were difference about 45 degree due to surface topography and microstructure and chemical composition on substrate with ZnO thin film [10].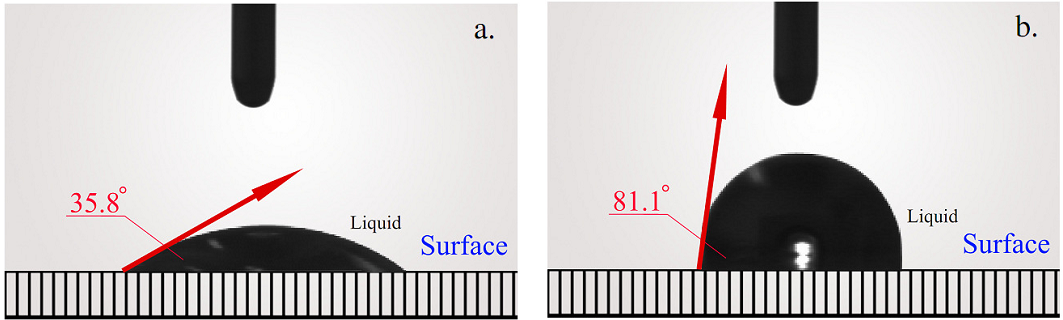 | Figure 3. The action of a water droplet on silicon wafer a) The original silicon wafer surface b) The ZnO thin film on silicon wafer surface |
Fig. 4 shows relationship between the contact angles and the temperature of substrate of the ZnO thin film from plasma deposition on silicon wafer with low-pressure high-frequency plasma chemical vapor deposition system under the condition of: 300 W. with plasma power of 3.4×102 Pa. Vacuum level and the mixture of Ar and O2 gas at 10 L/min. and 2 L/min., respectively, while the temperature of lower electrode was 100-300 C. It was found that the contact angle of the ZnO thin film from plasma deposition increased about 70, 81 and 84 degree when temperature of lower electrode was 100, 200 and 300 C, respectively. The hydrophobic properties improved from the increase of contact angle as a result of morphology structure of the surface changed due to the increase of roughness of the thin film [11].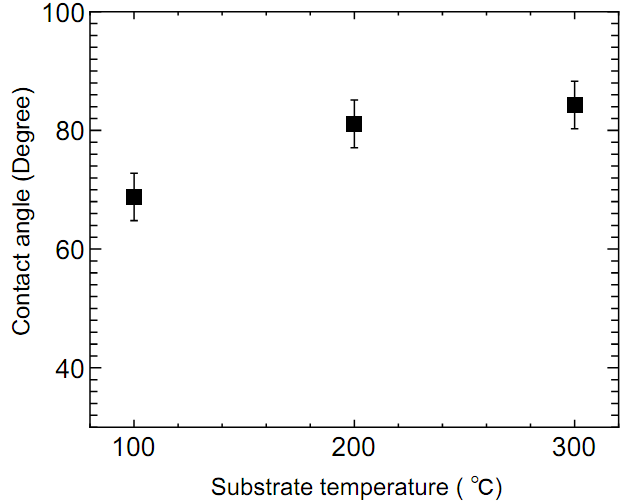 | Figure 4. The relationship between the contact angles and the temperature of substrate |
Fig. 5 shows the SEM image of the surface of ZnO thin film on silicon wafer substrate by low-pressure high-frequency plasma chemical vapor deposition system under the same experimental conditions as in Fig. 4. When Fig. 5 (a), (b) and (c) ware substrate heating at 100C, 200C and 300C, respectively. Fig. 5 (a) shows the surface morphology of the ZnO thin films at deposition temperature of 100C. It was found that the ZnO thin films had a smooth surface with crystal grain size of approximately 80–100 nm. The grain size at deposition temperature of 200C to 300C changed to the crystal grain size about 100–120 nm. When the deposition temperature increased resulting in the surface morphology of the films changed to typical pyramid shape structure [12]. It was confirmed that the grain size of ZnO thin films tended to be larger when temperature increased which results in the better crystal quality.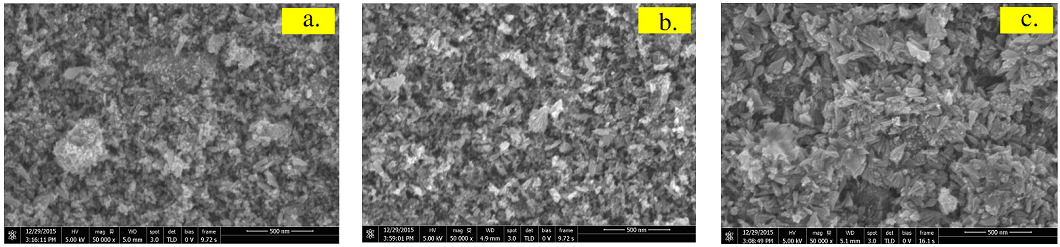 | Figure 5. The SEM image of the ZnO thin film on silicon wafer a) 100C b) 200C c) 300C |
4. Conclusions
The preparation of ZnO thin film was successfully performed by developed the low-pressure high-frequency plasma CVD system with powder deposition. The results were investigated by measuring the surface of ZnO thin film from ZnO powder deposition. The contact angle meter confirmed that the hydrophobic properties changed. The contact angle increased compared with the original silicon wafer, confirming the formation of ZnO thin film on the silicon wafer surface as a result of the crystal grain of ZnO formation on surface. In addition, when deposition temperature increased, the hydrophobic properties changed, the angle of water droplet increased due to the changed of grain size of ZnO thin film on surface. The results from scanning electron microscope (SEM) also confirmed that the morphology ZnO thin film on surface changed to typical pyramid shape structure with larger of crystal grain size.
ACKNOWLEDGMENTS
This work has been supported by Pibulsongkram Rajabhat University (PSRU) Research fund, Thailand. The authors would like to thank Plasma laboratory of University of Miyazaki for place of experiment.
References
[1] | J-I. Nomoto, Y. Nishi, T. Miyata, T. Minami. (2013). Influence of the kind and content of doped impurities on impurity-doped ZnO transparent electrode applications in thin-film solar cells. Thin Solid Films. 534, 426–431. |
[2] | J. Panigrahi, D. Behera, I. Mohanty, U. Subudhi, B.B. Nayak, B.S. Acharya. (2011). Radio frequency plasma enhanced chemical vapor based ZnO thin film deposition on glass substrate: A novel approach towards antibacterial agent. Applied Surface Science. 258, 304–311. |
[3] | A.N. Banerjee, C.K. Ghosh, K.K. Chattopadhyay, H. Minoura, A.K. Sarkar, A. Akiba, A. Kamiya, T. Endo. (2006). Low-temperature deposition of ZnO thin films on PET and glass substrates by DC-sputtering technique. Thin Solid Films. 496, 112 – 116. |
[4] | B.N. Pawar, G. Cai, D. Ham, R.S. Mane, T. Ganesh, A. Ghule, R. Sharma, K.D. Jadhava, S-H. Han. (2009). Preparation of transparent and conducting boron-doped ZnO electrode for its application in dye-sensitized solar cells. Solar Energy Materials & Solar Cells. 93, 524–527. |
[5] | J. Lee, D. Lee, D. Lim, K. Yang. (2007). Structural, electrical and optical properties of ZnO:Al films deposited on flexible organic substrates for solar cell applications. Thin Solid Films. 515, 6094–6098. |
[6] | W. Lu, Y. Dong, C. Li, Y. Xia, B. Liu, J. Xie, N. Li, Y. Zhang. (2014). Preparation of ZnO films with variable electric field-assisted atomiclayer deposition technique. Applied Surface Science. 303, 111–117. |
[7] | A. Mart’ın, J.P. Espino’s, A. Justo, J.P. Holgado, F. Yubero, A.R. Gonz’alez-Elipe. (2002). Preparation of transparent and conductive Al-doped ZnO thin films by ECR plasma enhanced CVD. Surface and Coatings Technology. 151 –152, 289–293. |
[8] | P.K. Shishodia, H.J. Kim, A. Wakahara, A. Yoshida, G. Shishodia, R.M. Mehra. (2006). Plasma enhanced chemical vapor deposition of ZnO thin films. Journal of Non-Crystalline Solids. 352, 2343–2346. |
[9] | N. Thungsuk, P. Nuchuay, D. Hirotani, Y. Okamura, K. Nakabayashi, H. Kinoshita, T. Yuji, N. Mungkung, N. Kasayapanand. (2014). Development of low-pressure high-frequency plasma chemical vapor deposition method on surface modification of silicon wafer. Vacuum. 109, 166-169. |
[10] | M. Shaban, A.M. El Sayed. (2016). Effects of lanthanum and sodium on the structural, optical and hydrophilic properties of sol–gel derived ZnO films: A comparative study. Materials Science in Semiconductor Processing. 41, 323-334. |
[11] | Y. Huang, D.K. Sarkar, X-G. Chen. (2015). Superhydrophobic nanostructured ZnO thin films on aluminum alloy substrates by electrophoretic deposition process. Applied Surface Science. 327, 327-334. |
[12] | X-L. Chen, Q. Lin, J. Ni, D-K. Zhang, J. Sun, Y. Zhao, X-H. Geng. (2011). Textured surface boron-doped ZnO transparent conductive oxides on polyethylene terephthalate substrates for Si-based thin film solar cells. Thin Solid Films. (520) Issue 4, 1263-1267. |