Ndubuisi I. Mbada1, Ola Aponbiede2, Terver Ause2, Ayo Alabi2
1Nigerian Institute of Transport Technology (NITT), Zaria, Nigeria
2Department of Metallurgical & Materials Engineering, Ahmadu Bello University, Zaria, Nigeria
Correspondence to: Ndubuisi I. Mbada, Nigerian Institute of Transport Technology (NITT), Zaria, Nigeria.
Email: |  |
Copyright © 2016 Scientific & Academic Publishing. All Rights Reserved.
This work is licensed under the Creative Commons Attribution International License (CC BY).
http://creativecommons.org/licenses/by/4.0/

Abstract
Background and objective: There is a renaissance in the usage of Kenaf and other natural fibres in composite applications. This study investigated the effects of mercerization of Kenaf fibres treated with 1%w/w - 6%w/w NaOH in comparison with un-treated one. Materials and Methods: The bast fibre type of Kenaf obtained from plant stem was used in this study. Mercerization treatment for the modification of the fibre surface and removal of some waxy impurities was carried out using gravimetrically prepared NaOH concentrations of1%w/w to 6%w/w at 25°C. Kenaf fibre diameter and density was determined using optical microscope and Archimedes principle respectively. The weight of the fibre was calculated from bulk density and fibre diameter. Fourier Transform Infra Red Spectrophotometer was used for the analysis. Results: Kenaf fibre has a measured density of
. The absorption peak for the untreated Kenaf fibre at 1732.12cm-1 which corresponds to the C=O stretching of the hemicelluloses for Kenaf fibres were absent for the treated fibres. Mercerization did not produce any visible change in the absorption peak around 1509cm-1 for treated Kenaf fibre; as the lignin content of the fibres was unaffected. Mercerization led to weight reduction and, the diameters of the Kenaf fibre decreases with increasing %w/w NaOH concentrations. Pearson’s coefficient indicates an inverse relationship between concentration (mercerization level) and fibre weight (r = -0.9857). The regression equation to predict Kenaf fibre weight relationship with mercerization level yielded an R2 value of 0.971608 at 5.81 * 10-8 Standard Error. Conclusions: The measured density of Kenaf fibre was
. There is an inverse relationship between fibre weight and the mercerization level. Mercerization level used in this study with peak absorption around 1509cm-1, did not affect the lignin constituent of the Kenaf fibre. The regression model on the effect of mercerization on Kenaf fibre weight yielded 97% linear relationship. Overall, mercerization treatment on Kenaf fibre affects the fibre surface, reduces inversely the fibre diameter with higher %w/w NaOH concentrations and improves the adhesion characteristics.
Keywords:
Absorption Peak, Fibrillation, Hemicelluloses, Kenaf Fibre, Mercerization
Cite this paper: Ndubuisi I. Mbada, Ola Aponbiede, Terver Ause, Ayo Alabi, Effects of Mercerization Treatment on Kenaf Fibre (Hibiscus cannabinus L.), International Journal of Materials Engineering , Vol. 6 No. 1, 2016, pp. 8-14. doi: 10.5923/j.ijme.20160601.02.
1. Introduction
Depletion of petroleum resources and stringent environmental control measures are forcing industries to source for alternative materials that are eco-friendly, while not over relying on fossil fuel, natural fibres foots the bill in their application in composites [1, 2]. Natural fibres are gaining increase popularity among researchers in the field of science and engineering, as a result of the increased awareness of global environmental factors which includes: principles of sustainability, industrial ecology, and eco-efficiency which form the focus of next generation of materials, products and processes [2].The concept of material substitution is crucial because it is chancy to rely solely on synthetic materials, without consideration for alternatives, which are readily available in nature. Natural fibres are structurally made up of cellulose, lignin, and hemicelluloses. The cellulose is the building block of natural fibres and it dictates most of the properties [3]. The structure of natural fibres is crystalline and they also have orientation angles known as microfibrillar angle which contributes immensely to the mechanical properties of natural fibre [4]. Kenaf (Hibiscus cannabinus L.) is a natural fibre yielding plant. Kenaf is a dicotyledonous plant harvested annually or bi-annually, and can grow up to 3.5m high [5]. Kenaf apart from being a fibre producing plant can also yield edible oil, and other useful products such as paper, cords and ropes, mats, sacks and industrial solvents. In addition, sea going vessels, also have their sails made from Kenaf for centuries. Recently, there is a renaissance in the usage of Kenaf and other natural fibres in composite applications [6, 7]. There are some drawbacks in the use of natural fibre as reinforcement in composite applications which includes the- hydrophilic nature of cellulose, high polar nature, and poor resistance to moisture absorption. These inherent shortcomings affect some of the physical properties of natural fibre reinforced composites [8]. Poor adhesions between the fibre-matrix inter-phase and swelling of natural fibre have been addressed by some of the techniques for fibre surface modification. Some of these techniques include mercerization, silane treatment, and impregnation of fibres, chemical modification and physical treatment [9, 10].Natural fibre production is a two stage process of decortications which is the separation of the bark from the woody core and retting which involves the loosening of the pectin and the lignin holding the bast fibres to the bark through the action of microorganisms on the bark biomass, this can be achieved by soaking the bark for twenty-one days in a pond [3, 17] (Munder, Furll, & Hempel, 2005). The major growers of kenaf include: China, India, Myanmar, Bangladesh, USA, Philippines and Malaysia. Traditionally Kenaf has been used in textile, gunny sack, and cordage material and in paper production, recent research as shown its suitability for building material and in recycled plastics [18] (Webber III, Bhardwaj, & Bledsoe, 2002). Mercerization method involves the use of alkali at different concentrations, time and temperature to treat natural fibre [11]. Kenaf fibres have been treated with NaOH, as reported by different works [3, 11, 12]. Kenaf fibres mainly consist of crystalline cellulose surrounded and cemented together with hemicelluloses, lignin, waxy materials and other impurities. Thus the fibres can be considered as a bundle of microfribils [4]. Akil et al [3] reported that important modification which must be done by alkaline treatment is the disruption of hydrogen bonding in the network structure, thereby increasing surface roughness. This treatment removes certain hemicelluloses, lignin, wax and oils covering the external surface of the fibre cell wall; depolymerizes cellulose, and exposes the short length crystallites. Alkaline treatment leads to fibrillation of the fibre bundles into small fibres. In other words, this treatment reduces fibre diameter and thereby increases aspect ratio. This study investigated the effects of mercerization of Kenaf fibres treated with 1%w/w - 6%w/w NaOH concentrations in comparison with un-treated one.
2. Materials and Methods
2.1. Materials
Kenaf fibre, is a natural fibre, obtain from the stem of the kenaf plant. The Kenaf bast fibre was sourced from the Institute of Agricultural Research (IAR), Ahmadu Bello University (ABU) Zaria, Nigeria. The Kenaf fibre is planted and cultivated in Zaria, under the IAR fibre research programme.
2.2. Mercerization Process
Sodium Hydroxide (NaOH) was used for mercerization treatment-which is a fibre surface modification process used in this research work. Apart from modification of the fibre surface, mercerization also aids in removal of some of the waxy impurities, such as lignin and hemicelluloses, which are responsible for an easy deformation of the cellular networks of the Kenaf fibre [4]. NaOH Pellets, GRG M.W 40.00, Assay 96%, produced by Avondale Laboratories (Supplies and Services) limited Banbury, Oxon., England was used for the mercerization in this study. The fibres were treated in NaOH of concentrations of 1%w/w, 2%w/w, 3%w/w, 4%w/w, 5%w/w, and 6%w/w at 25°C. The experimental set-up was done in the Laboratory of the Department of Metallurgical and Material Engineering, ABU, Zaria. Prior to the mercerization treatment, the flasks were washed and rinsed with de-ionized water. The NaOH concentrations were prepared gravimetrically. Thereafter, the fibre strands were introduced into the alkaline solution for two hours. A stopwatch was used to time the duration of the mercerization. Following, the mercerization, the alkaline solution was drained and the Kenaf fibre was rinsed with flowing water to remove any trace of alkali. The rinsing process was done vigorously and repeatedly, so as to thoroughly remove any trace of NaOH.
2.3. Determination of Fibre Diameter
The diameter of the Kenaf fibre was determined using optical microscope. The procedure was as follows: fibres were selected at random from the bulk for observation. Each of the selected fibres was cut into three different fibres along the length; the microscopic measurement was taken as the average measurement of the three fibre diameters. The reason was that; there are variations in diameter along the length of the fibre, as reported in the literature [13]. The assumptions made are that: the fibre is cylindrical across its length, and has a uniform cross sectional area that can be expressed with the equation: | (1) |
Where A, is the uniform cross sectional Area, d is fibre diameter,
.
2.4. Bulk Density of Kenaf Fibre
The bulk density of the fibre was determined using Archimedes principle. The fibre bundle was first weighed in air; the weight was recorded as Mka, and then immersed in paraffin, the weight was recorded as Mkp. The density of paraffin
was already determined before usage. The bulk density is given by the formula [14]. 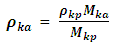 | (2) |
The specific gravity of the Paraffin
used for the experiment was 0.775.Weight of Kenaf in air
Weight of beaker + 150ml paraffin = 226.763gWeight of beaker + 150ml paraffin + Kenaf = 229.345gFrom Equation (2)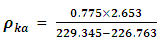

2.5. Determination of Kenaf Fibre Weight
The following assumptions were made [13]:i. the fibre geometry is considered as a perfect cylindrical tubeii. the fibre has uniform cross-sectional area across the entire lengthThe weight of the fibre was calculated from density and fibre diameter.
The fibre volume is calculated based on the assumption that the fibre geometry is cylindrical, thus the formula for calculating the volume of a cylinder is given by: 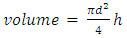 | (3) |
The length (h) of the fibre is taken to be unity, thus the mass of the fibre is calculated from: 


2.6. FTIR Analysis
The infra red spectra of each fibre category were examined using Fourier Transform Infrared (FTIR) analysis. The FTIR analysis was performed on SHIMADZU FTIR 8400s Fourier Transform Infra Red Spectrophotometer. The wave forms of the spectra were plotted with the Transmittance (T) against the wave number (1/cm). A characteristic peak gives the nature of the chemical bond and the functional groups present in the fibres.
3. Results and Discussion
3.1. FTIR Result and Analysis
The FTIR spectra of the un-treated kenaf fibre, and the 1%w/w NaOH treated kenaf fibre are shown in figures 1 and 2. It was observed from the FTIR spectra that the mercerization treatment resulted in structural modification to the fibre surface - Infrared spectroscopy detects the vibration characteristics of chemical functional groups in a sample [15]. The Alkali treatment on the fibre was seen to affect the wave number and the absorption bands for each of the fibre treated categories. The removal of hemicelluloses and other impurities leads to reduction in fibre diameter (figure 3). This is corroborated by the assumption that the fibres treated with NaOH at varying %w/w showed decrease in diameter and roughening of the fibre surface which results in improvement in mechanical interlocking of the fibre and the adhesion characteristics of the fibre as reported by Edeerozeyet al [12]. From the FTIR analysis of the un-treated and treated Kenaf fibres, it was observed that the absorption peak for the un-treated Kenaf fibre at 1732.12cm-1, (figure 1) which corresponds to the C=O stretching of the hemicelluloses was missing for Kenaf fibres that were subjected to mercerization treatment. Moreover, there were no visible change in the absorption peak around 1509cm-1 in the Kenaf fibres treated with NaOH which is as a result of aromatic skeletal ring vibration of lignin. It is implied that mercerization does not affect the lignin constituent of the Kenaf fibre at that particular concentration. Hence, from the FTIR analysis, it seems that mercerization only affects the hemicelluloses constituent of the Kenaf fibre.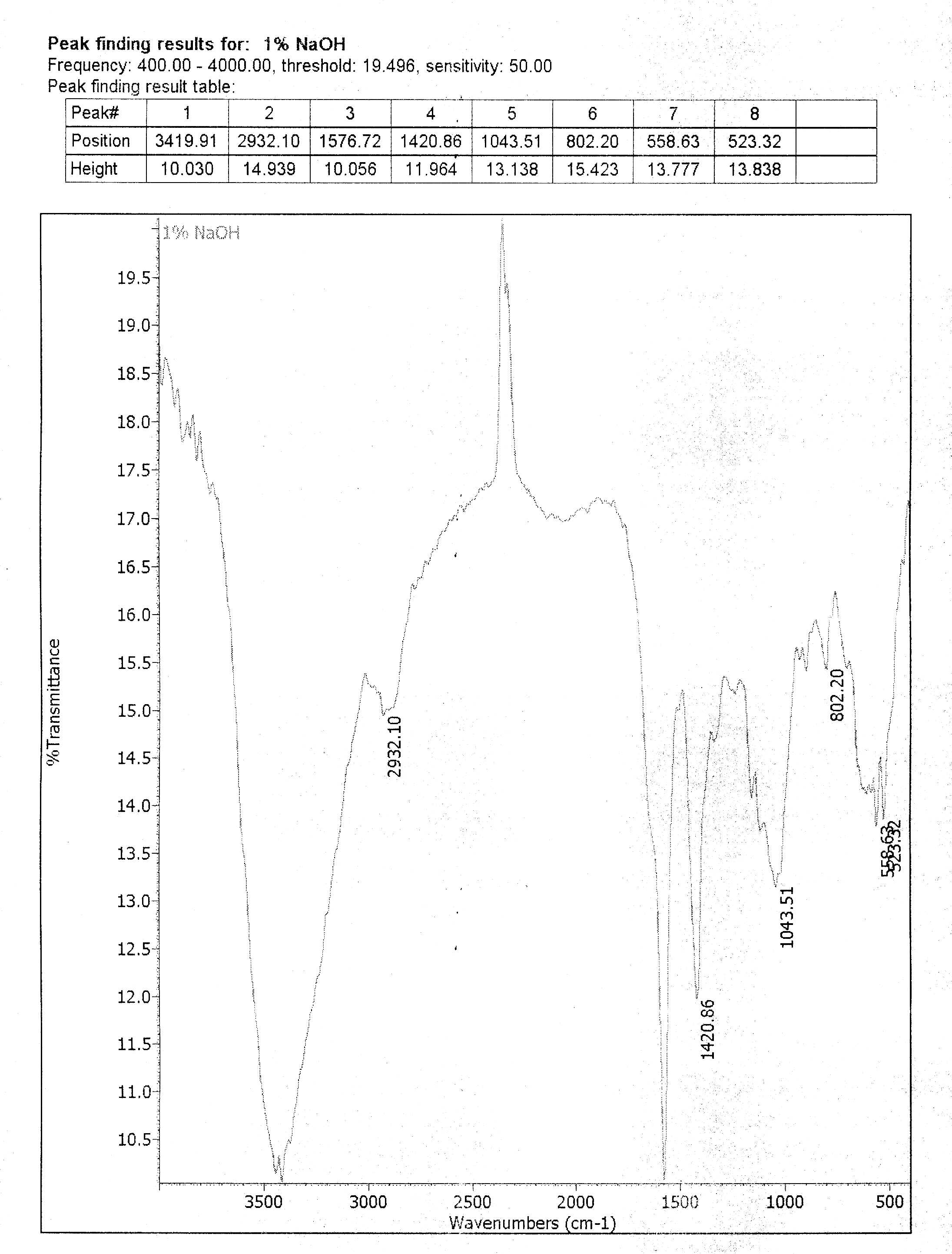 | Figure 2. FTIR Analysis of 1%w/w NaOH Treated Kenaf Fibre |
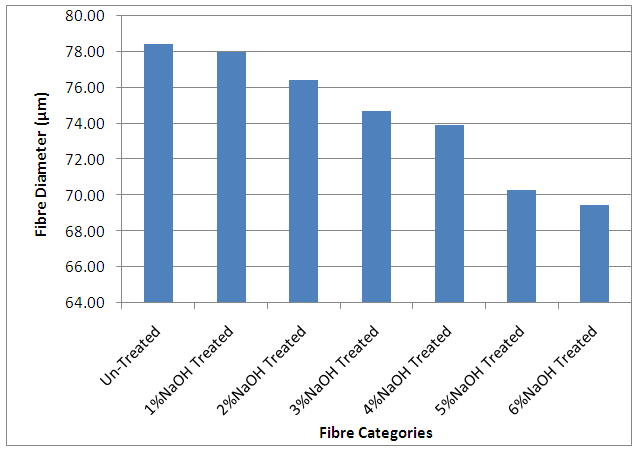 | Figure 3. Effect of Mercerization Treatment on the Kenaf Fibre Diameter |
3.2. Density/ Specific Weight
The density of the Kenaf fibre from empirical determination was:
From this result, it is adduced that the light weight of Kenaf fibre, when compared to some other type of fibres has gross positive effect on composites prepared from them [3].
3.3. Effect of Mercerization on Fibre Diameter
The results of the fibre diameter as shown in figure 3 revealed that the diameters of Kenaf fibre decreases gradually as a result of mercerization treatment on the fibres. The reduction in diameter is inversely proportional to the %w/w NaOH concentration. It was observed that the fibres treated at 6%w/w NaOH concentration had the least fibre diameter. This reduction in fibre diameter was as a result of removal of waxy impurities and change in crystallinity of hemicelluloses in addition to part removal of carbonyl and alcohol contents of the fibre. Table 1. Fibre Weight Calculation Table 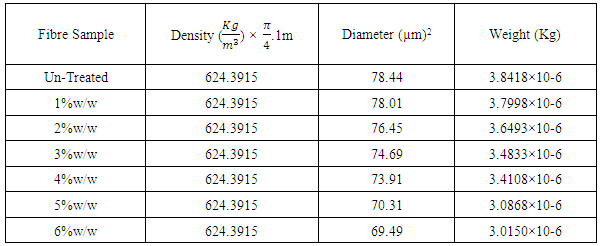 |
| |
|
3.4. Effect of Mercerization on Fibre Weight
The effect of mercerization on the fibre weight can be shown from simple regression analysis and correlation using calculated value of fibre weight for the treated and the un-treated fibres at various %w/w NaOH concentrations. The concentration is the regressor (x) while the fibre weight is the response (y), the concentration and the fibre weight were treated as variables x and y. Table 2 gives the summary of the result from excel spread sheet analysis of the data. The best line of fit showing the relationship between mercerization level and fibre weight is estimated using least square plot (figure 4). The analysis shows the relationship between the mercerization level and fibre weight.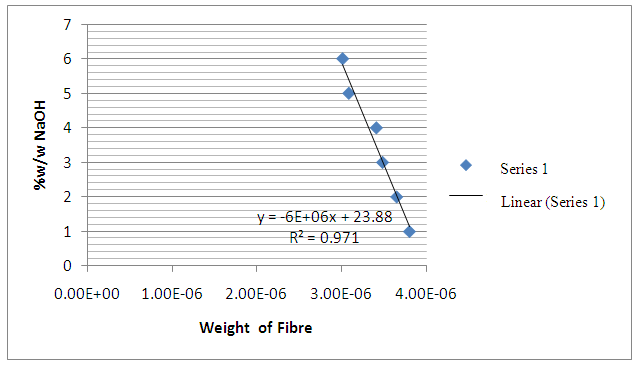 | Figure 4. Least Square Plot |
Table 2. Statistics Summary Table 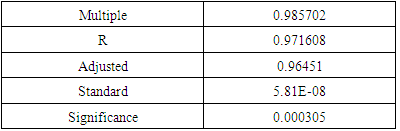 |
| |
|
The Pearson product moment correlation coefficient gives a negative correlation (r = -0.9857). The Pearson co-efficient reveals a strong relationship between concentration (mercerization level) and fibre weight. Using simple regression analysis, the result showed that the weights of the fibre at different mercerization level correlate with the concentration of NaOH used for the fibre surface treatment. The sample coefficient of determination, i.e.
(=0.9716) indicates that approximately 97% of variation in fibre weight is accounted for by a linear relationship with concentration, at 0.05 confidence interval. Also, the significance F-ratio of 0.000305 confirms that the observed linear relationship between concentration and fibre weight is not as a result of chance or random variation. This result suggests that the higher the %w/w NaOH (mercerization level), the higher the weight reduction effect on Kenaf fibre. Mercerization of Kenaf fibre lead to weight reduction and improve specific properties which conforms to the recent trend in automotive industry which includes the following: reduction in weight, improve fuel economy, and energy saving which has been the driven force for the new researches in composite development and application in this field [16].
4. Conclusions
The result from the study showed that mercerization treatment on Kenaf fibre were found to affect the fibre surface thereby improving the adhesion characteristics of the Kenaf fibre as well as reduction in the diameter; the higher the %w/w NaOH the lower the fibre diameter. The FTIR analysis showed that mercerization affects the treated Kenaf fibre due to the absence of the absorption peak found in the un-treated Kenaf fibre at 1732.12cm-1. Furthermore, it was observed that at the mercerization levels used for the experiment- up to 6%w/w NaOH does not affect the lignin content of the kenaf fibres. There is a linear relationship between fibre weight and the mercerization level. The measured density of Kenaf fibre was
. From the regression analysis the R value was 0.9716, while the significance F (= 0.000305) negates the hypothesis that the observed relationship is due to chance, or random variation. Thus, it can be inferentially stated that the higher the %w/w NaOH the lower the weight of fibre.
References
[1] | K. Oksman, M. Skrifvars, J.F Selin. Natural fibres as reinforcement in polylactic acid (PLA) composites. Science and Technology. 2003; 63(9), pp. 1317-1324. |
[2] | A. Mohanty, M. Misra, L. Drzal, S. Selke, B. Harte, G. Hinrichsen. Natural Fibre Biopolymers, and Biocomposites: An Introduction. In A. Mohanty, M. Misra, & L. Drzal, Natural Fibre Biopolymers, and Biocomposites: An Introduction (p. 1). Boca Ranton, FL: CRC Press. 2005. |
[3] | H. Akil, M. Omar, A. Mazuki, S. Safiee, Z. Ishak, A. Abu Bakar, A. Kenaf fiber reinforced composites: A review. Materials and Design-Elsevier, 2011; 4107–4121. |
[4] | Y. Cao, S. Sakamoto, K. Goda. Effect sof Heat and Akali Treatment on Mechanical Properties of Kenaf Fibre. 16th Internation Conference on Composite Materials, Kyoto, Japan. 2007; 1-4. |
[5] | M. Ishak, Z. Leman, S. Sapuan, A. Edeerozey, S. Othman. Mechanical properties of kenaf bast and core fibre reinforced unsaturated polyester composites. 9th National Symposium on Polymeric Materials. 2009; 1-6. |
[6] | A.Leao, R.Rowell, N. Tavares. Application of Natural Fibre in Automotive industry in Brazil-Thermoforming Processes. Science and Technology of Polymers and Advanced Materials 1998. P.755. |
[7] | B. Deepa, L. Pothan, R. Mavelil-Sam, S. Thomas. Structure, properties and recyclability of Natural fibre Reinforced Polymer Composites. Recent Developments in Polymer Recycling, 2011; 101-120. |
[8] | R. Malkapuram, V. Kumar, S.N. Yuvraj. Recent Development in Natural Fibre Reinforced Polypropylene Composites. Journal of Reinforced Plastics and Composites. 2008; 1169-1189. |
[9] | Y. Han, S. Han, D. Cho, H. Kim. Kenaf Polypropylene Biocomposites: Effect of Electron Beam Irradiation and Alkali Treatment on Kenaf Natural Fibres. Compos Inter. 2007; 559-78. |
[10] | S. I.Aji, S. M. Sapuan, E. S. Zainudin, K. Abdan. Kenaf fibres as reinforcement for polymeric composites: A review. International Journal of Mechanical and Materials Engineering. 2009; 4(3): 239-248. |
[11] | P. Herrera Franco, A. Valadez-Gonzalez. Fibre-Matrix Adhesion in Natural Fibre Composites. In A. Mohanty, M. Misra, & L. Drzal, Natural Fibres, Biopolymers and Biocomposites. Boca Ranton, FL: CRC Press.2005; 187-188. |
[12] | A. Edeerozey, H. Akil, A. Azar, M. Ariffin. Chemical Modification of Kenaf Fibres. Materials Letters. 2007; 61(10): 2023-2025. |
[13] | N. Ribot, Z. Ahmad, N. Mustaffa. Mechanical Properties of Kenaf Fibre Composite using Co-Cured In-Line Fibre Joint. International Journal of Engineering Science and Technology. 2011; 3526-3534. |
[14] | Hodgman C. Archimedes’ Principle And Specific Density. In CRC, Handbook of Chemistry and Physics. Clevland: Chemical Rubber Company. 1957; 1981-1990. |
[15] | H. Onggo, S. Pujiastuti. Effect of Weathering on Functional Group and Mechanical Properties of Polypropylene-Kenaf Composites. Indonesian Journal of Materia Science.2010; 123-128. |
[16] | J. Holbery, D. Houston. Natural Fibre-Reinforced Polymer composites in Automotive Applications. Journal of the Minerals, Metals and the Materials Society. 2006; 58, 80-86. |
[17] | F. Munder, C. Fürll, H. Hempel. Processing of Bast Fiber Plants for Industrial Application. In A. Mohanty, M. Misra, & L. Drzal, Natural Fibre Biopolymers, and Biocomposites (p. 109-140). Boca Ranton, FL: CRC Press. 2005. |
[18] | C.L. Webber III, H.L. Bhardwaj, V. K. Bledsoe. Kenaf Production: Fiber, Feed, and Seed. In J. Janick, & A. Whipkey, Trends in New Crops and New Uses (P.348). Alexandria, VA: ASHS Press . 2002. |