André Luis Christoforo1, Tulio Hallak Panzera2, Lincoln Cardoso Brandão2, Victor Almeida de Araújo3, Diogo Aparecido Lopes Silva4, Francisco Antonio Rocco Lahr5
1Centre for Innovation and Technology in Composites (CITeC), Department of Civil Engineering (DECiv), Federal University of São Carlos (UFSCar), São Carlos, Brazil
2Centre for Innovation and Technology in Composites (CITeC), Department of Mechanical Engineering, Federal University of São João del-Rei, São João del-Rei, Brazil
3Research Group LIGNO of UNESP-Itapeva, Department of Forest Sciences, School of Agriculture Luiz de Queiroz of University of São Paulo (ESALQ/USP), Piracicaba, Brazil
4Department of Production Engineering, Engineering School of São Carlos (EESC/USP), São Carlos, Brazil
5Department of Structures Engineering (SET), Engineering School of São Carlos of University of São Paulo (EESC/USP), São Carlos, Brazil
Correspondence to: André Luis Christoforo, Centre for Innovation and Technology in Composites (CITeC), Department of Civil Engineering (DECiv), Federal University of São Carlos (UFSCar), São Carlos, Brazil.
Email: |  |
Copyright © 2015 Scientific & Academic Publishing. All Rights Reserved.
Abstract
This paper proposes an alternative method of calculation based on the Least Squares method to determine the longitudinal modulus of elasticity in timber beams with structural sizes. The developed equations require knowledge of three points measured in displacements along the element, allowing greater reliability on the response-variable, using the static bending test in three and in four points. The proposed methodologies were employed together, aiming to verify possible differences between the values of the modulus of elasticity. The results for Eucalyptus grandis timber showed statistical equivalence between the methods. Thus, the modulus of elasticity can be obtained by both schemes of structural tests applied.
Keywords:
Timber beams, Longitudinal modulus of elasticity, Least squares method
Cite this paper: André Luis Christoforo, Tulio Hallak Panzera, Lincoln Cardoso Brandão, Victor Almeida de Araújo, Diogo Aparecido Lopes Silva, Francisco Antonio Rocco Lahr, Comparison among the Longitudinal Modulus of Elasticity in Eucalyptus grandis Timber Beams by Alternative Methodologies, International Journal of Materials Engineering , Vol. 5 No. 4, 2015, pp. 77-81. doi: 10.5923/j.ijme.20150504.01.
1. Introduction
Among the main materials used in the manufacturing of structures, the wood is highlighted because it is a renewable material with excellent strength/density ratio, about four times if wood is compared with steel [1].The project of wooden structures – as well as in other materials – requires knowledge of some variables, as the modulus of elasticity, obtained through the experimental tests recommended by normative documents, which can be destructive or not.Insofar as the wood is an orthotropic and heterogeneous material, and seeking a greater reliability, its characterization in bending requires experimentation in elements with structural sizes. In this context, only international normative documents can be cited, since the Brazilian NBR 7190 [2] (Project of Wooden Structures), which treats of the wood characterization, it just contemplates the condition of destructive test in small-dimensions and free from defects specimens.The American standard ASTM D198 [3] (Standard test Method of Static Tests of Lumber in Structural Sizes) recommends static bending test in four points (Figure 1) in the determination of the flexural modulus of elasticity (Em), expressed by Equation 1, where F is the force applied in the proportional limit, L is the span between the supports, a is the distance between the applied forces, b is the width of the specimen, h is the thickness of the specimen and δ is the arrow obtained in the midpoint of the span.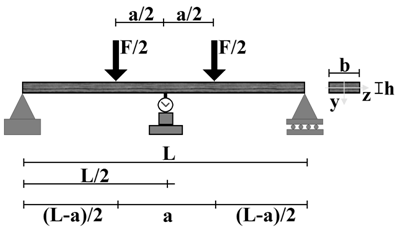 | Figure 1. Four-points bending tests according to ASTM D198 [3] |
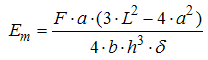 | (1) |
The American standard ASTM D3043 [4] (Standard Methods of Testing Structural Panels in Flexure) uses the structural model of static bending in four points in the determination of the properties of strength and stiffness in wooden boards, indicating the position of lower inertia of the element (flatwise), as shown in Figure 2.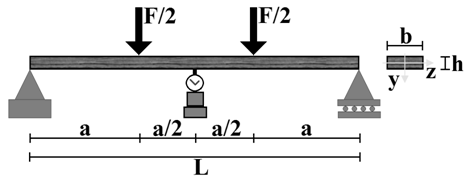 | Figure 2. Four-points bending tests according to ASTM D3043 [4] |
The modulus of elasticity calculated by the standard ASTM D3043 [4], titled apparent (Ea), and it is obtained by Equation 2.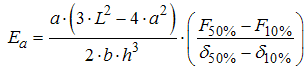 | (2) |
In the Equation 2, F50% and F10% are the forces (N) corresponding to 10% and 50% of the maximum load applied in the specimen, δ50% and δ10% are the displacements (mm) corresponding to 10% and 50% of maximum load, b and h correspond respectively to the width and height (mm) of the cross-section of the specimen, a is the distance between supports and the application point of force, and L is the span between supports.The American standard ASTM D4761 [5] (Standard Test Methods for Mechanical Properties of Lumber and Wood-base Structural Material) uses the bending test in three points to obtain the apparent modulus of elasticity (Equation 3) in upright boards (Figure 3), where Iz is the moment of inertia in relation to the “z” axis.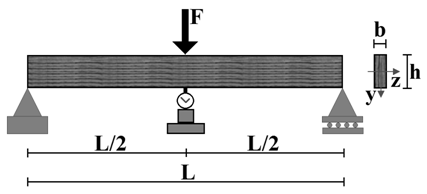 | Figure 3. Three-points bending tests according to ASTM D4761 [5] |
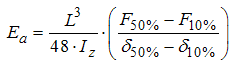 | (3) |
Two calculation methods proposed by the standards ASTM D3043 [4] and ASTM D4761 [5] can provide different values for the modulus of elasticity, justified by the intensity and scale of shearing forces, leading to apparent values for the flexural modulus of elasticity, whereas the model of beams used in the development of the equations does not include the portion of the shear strength [6].However, Bodig and Jayne [7] state that in a larger ratio of beam length (L) by the height of the cross-section (h), the contribution of shearing in the deflections calculation will be smaller. For L/h relations, “equal or superior to 21”, this contribution is negligible [8].The American standard ASTM D4761 [5], which adopts bending tests in three points, proposes that ratio “L/h” for the testing of upright boards must be among 17 and 21. In this cases, the apparent modulus of elasticity (Ea) approaches of the flexural modulus of elasticity (Em).The European standard EN 789 [9] (Determination of the Mechanical Properties of Wood-based Boards) recommends the static bending in four points, according to the curvature method, recording the vertical displacement at mid-span, but on the other point among the loading operation. In this condition, is preferable one point as far as possible of the mid-span. The interpretation of the results is made from the recording of the variation of the curvature in relation to the applied loads. In this case, the flexural modulus of elasticity (Equation 4) is based solely on the bending moment.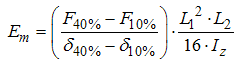 | (4) |
In Equation 4, F40% and F10% are the forces (in Kgf) corresponding to 10% and 40% of the maximum loading applied to specimen, δ40% and δ10% are the displacements (in cm) corresponding to 10% and 40% of maximum loading, L1 is the reference distance for measuring of displacement in center span (in cm), and L2 is the half of the length of the shearing zone (in cm).Wood structural composites, such as panels glued from laminas (Laminated Veneer Lumber - LVL) and the boards of laminated particles (Laminated Strand Lumber - LSL, Oriented Strand Lumber - OSL and Parallel Strand Lumber - PSL) are generally characterized in bending because of the premises of calculation of American standard ASTM D5456 [10] (Standard Specification for Evaluation of Structural Composites Lumber Products), which uses the static bending test in three points in the determination of the modulus of elasticity and the flexural strength of the laminas, being evaluated for the two possible positions: the major and minor moment of inertia, according to the composition of lamina in the element formation [11, 12].In Brazil, the researches involving the characterization of wooden elements by destructive testing follow the premises of methods and calculations contained in international normative documents, which was cited in the studies of Pigozzo [13], Fiorelli [14] and Miotto [15].Like previously mentioned, the characterization of wooden elements of structural sizes can also be performed by non-destructive tests, which aim the determination of physical-mechanical properties of a structural element without the changing of its capabilities of use [16].The advantage of the use of non-destructive tests consist in the absence of the extraction of specimens, enabling the study of the structural integrity [17, 18], commonly performed by ultrasound and transverse vibration tests.Of the foregoing, the calculation models proposed by the standard documents for the determination of the flexural modulus of elasticity in wood elements (parts) with structural sizes (by destructive tests) do not include methods of optimization.In relation to conventional non-destructive tests, it is highlighted the need to acquire special equipments to determine the modulus of elasticity.This research proposes two analytical methodologies of calculation, based on the Least Square Method and the Static Bending test in three and four points, of a non-destructive way, to determine the longitudinal modulus of elasticity in sawn wood elements of structural sizes. The utilization of analytical approaches is made for Eucalyptus grandis wood, aiming to verify the difference between both methods.
2. Material and Methods
For the determination of modulus of elasticity were used 24 pieces of Eucalyptus grandis wood with dimensions of 6 cm 16 cm 200 cm, respecting the relation
, disesteeming the influence of the shearing forces in the deflection calculation [8].The experimental test used in the determination of the modulus of elasticity are considered non-destructive, because of the largest value of displacement found is limited to the ratio L/200, where L is the span between the supports, expressed in centimeters. This is an average of small displacements defined by NBR 7190 [2], resulting in physical and geometric linearity to the wooden beams. The schemes of tests for the determination of the flexural modulus of elasticity by both methodologies of calculation are illustrated in Figures 4a and 4b respectively.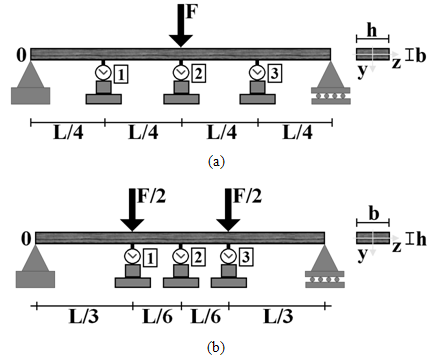 | Figure 4. Bending tests: (a) Three-points with three dial gages, (b) Four-points with three dial gages |
The use of the methodology proposed in this study requires the knowledge of the value of the analytical displacements of the element in the positions of the three dial gages (R1, R2, R3). The analytical displacement (V) coincident with the positions of the dial gages for both structural schemes of testing were obtained from the strength of the materials by the Euler-Bernoulli’s beam theory, which was written as function of the longitudinal modulus of elasticity (E).The modulus of elasticity calculated with the information from the test models (Figure 4) is related to the idea of least squares method (Equation 7), aiming to determine the value of the modulus of elasticity with the lowest possible index of residue generated between the values of the analytical (V) and experimental (δ) displacements. They are unquestionably more accurate when are compared to methods without optimization criteria, such as proposed by standardization documents.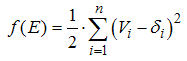 | (7) |
The equality of the first derivative of Equation 7 to zero in each case (Figures 4a and 4b) leads to values of the modulus of elasticity, which minimize the residue between the analytical and experimental displacements, expressed respectively by the Equations 8 and 9, proving that they are points of global minima by the criterion of the second derivative. | (8) |
 | (9) |
Equations 8 and 9 allow to obtain the longitudinal modulus of elasticity for the structural schemes of static bending in three (Em,3p) and four points (Em,4p), respectively. In order to verify the difference between them, a confidence interval of the difference among means was used, expressed by Equation 10, where μ is the population mean of differences,
is the arithmetic mean of the differences, n is the sample size, Sm is the standard deviation of the differences, and
is the value tabulated for Student’s distribution “t” with n-1 degrees of freedom and significance level α. | (10) |
3. Results and Discussions
The values of modulus of elasticity Em,3p and Em,4p (three and four points) obtained for the woods of Eucalyptus grandis are presented in Table 1.Table 1. Values of longitudinal modulus of elasticity Em,3p and Em,4p for Eucalyptus grandis 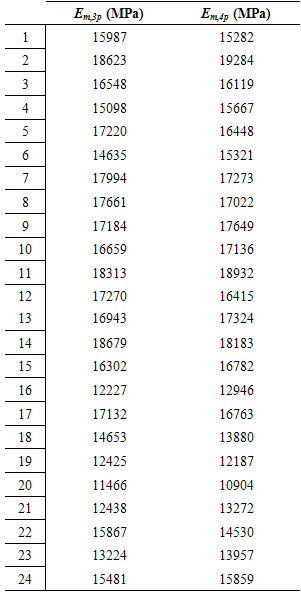 |
| |
|
The confidence interval between the values of Em,3p and Em,4p is
, and as the zero is located within the interval, it is stated that these are statistically equivalent. Graphs of linear regression and of residues between the values of the modulus of elasticity for both methods of calculation are shown by the Figure 5, whose adjustment equation and coefficient of correlation (R2) obtained are respectively
and 0.90.
4. Conclusions
Analytical methods of calculation proposed allow determining the modulus of elasticity in elements with structural sizes with a higher reliability when it is compared to other methodologies, whereas it is based on optimization concepts.Through the strong correlation obtained and the statistical equivalence found among the modulus of elasticity values of the Eucalyptus grandis woods by both calculation methodologies, it is found a small influence of shear strength coming from the static bending model in three points, because of the existence of shearing also in the load application region. This situation exclusively results by the measures of the wood elements respect the ratio between length and height of the cross section stipulated in the study of Rocco Lahr [8].It is emphasized that this methodology can also be used to specimens, and not only for sawn wood (lumber), but also for glued laminated timber beams (glulam), wood-based panels, etc, that can be aimed at other future research.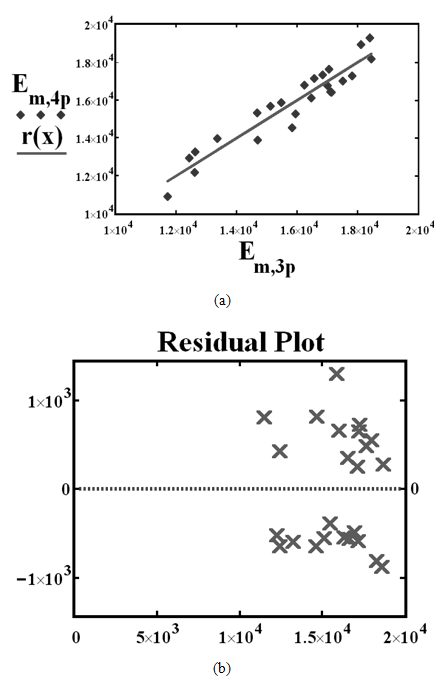 | Figure 5. Linear regression between Em,3p and Em,4p modulus of elasticity |
References
[1] | Calil Jr, C.; Lahr, F. A. R.; Dias, A. A. Dimensionamento de elementos estruturais de madeira. Editora Manole Ltda, Barueri – SP, ISBN: 85-204-1515-6, 2003. |
[2] | Associação Brasileira de Normas Técnicas (ABNT). Projeto de Estruturas de Madeira. NBR 7190, Rio de Janeiro, 1997. |
[3] | American Society for Testing and Materials (ASTM). Standard test method of static tests of lumber in structural sizes. ASTM D 198. Annual book of ASTM standards, v. 03.01. ASTM, West Conshohocken, Philadelphia, 1997. |
[4] | American Society for Testing and Materials (ASTM). Standard methods of testing structural panels in flexure. ASTM D 3043-95. Annual book of ASTM standards. ASTM, West Conshohocken, Philadelphia, 1995. |
[5] | American Society for Testing and Materials (ASTM). Standard test methods for mechanical properties of lumber and wood-base structural material. ASTM D 4761-96. Annual book of ASTM standards. ASTM, West Conshohocken, Philadelphia, 1996. |
[6] | Guitard, D. Mécanique du matériau bois et composites. Cepadues-editions. France, 1987. |
[7] | Bodig, J.; Jayne, B. A. Mechanics of wood and wood composites. Krieger Publishing Company. Malabar, Florida, 1992. |
[8] | Rocco Lahr, F. A. Sobre a determinação de propriedades de elasticidade da madeira. Tese de Doutorado. Escola de Engenharia de São Carlos, Universidade de São Paulo, São Carlos, SP, 216p, 1983. |
[9] | European Standard (EN). Estruturas de Madeira - Métodos de teste - Determinação das propriedades mecânicas de painéis derivados de madeira. EN 789, European Stardard (versão portuguesa), Bruxelas, 1995. |
[10] | American Society for Testing and Materials (ASTM). Standard specification for evaluation of structural composites lumber products. ASTM D 5456. Annual book of ASTM standards. ASTM, West Conshohocken, PA, 2006. |
[11] | Palma. H. A. L.; Ballarin, A. W.; Abilio, R. M. Propriedades mecânicas de painéis LVL de Pinus tropicais. In: XI Encontro brasileiro em madeira e estruturas de madeiras, Londrina, 2008. |
[12] | Palma. H. A. L.; Ballarin, A. W.; Rocha, C. D. Propriedades de flexão de vigas LVL de Eucalyptus grandis. In: XI Encontro brasileiro em madeira e estruturas de madeiras, Londrina, 2008. |
[13] | Pigozzo, J. C.; Pletz, E.; Lahr, F. A. R. Aspectos da classificação mecânica de peças estruturais de madeira. In: VII Encontro Brasileiro em Madeiras e em Estruturas de Madeira. São Carlos, SP, 2000. |
[14] | Fiorelli, J. Estudo teórico e experimental de vigas de madeira laminada colada reforçadas com fibra de vidro. São Carlos: USP, 2005. 108p. Tese (Doutorado em Ciência e Engenharia de Materiais) - Universidade de São Paulo, 2005. |
[15] | Miotto, J. L; Dias, A. A. Produção e avaliação de vigas de madeira laminada colada confeccionadas com lâminas de eucalipto. Revista Tecnológica, Edição Especial ENTECA, p. 35-45, 2009. |
[16] | Ross, R. J.; Brashaw, B. K.; Pellerin, R. F. Nondestructive evaluation of wood. Forest Products Journal, v. 48, n. 1, p. 14-19, 1998. |
[17] | Miná, A. J. S.; Oliveira, F. G. R.; Calil Jr, C.; Dias, A. A.; Sales, A. Avaliação não destrutiva de postes de madeira por meio de ultrassom. Scientia Forestalis, n. 65, p. 188-196, 2004. |
[18] | Oliveira, F. G. R.; Sales, A. Ultrassonic measurements in Brazilian hardwood. Materials and Research, v. 5, n. 1, p. 51-55, 2002. |