Shamsa Al Menhali , Ghanim Kashwani , Abeer Sajwani
Independent Researcher, UAE
Correspondence to: Ghanim Kashwani , Independent Researcher, UAE.
Email: |  |
Copyright © 2015 Scientific & Academic Publishing. All Rights Reserved.
Abstract
The global imbalance between supply and demand for oil and gas is growing. This trend was the turn behind studies from numerous oil organizations related to cementing. One of the important functions of cement sheaths is to provide hydraulic zonal isolation between different reservoirs in the well bore. Lost circulation or lost returns is known as the total or partial loss of drilling fluid or cement while drilling. It can be an expensive, time consuming or disastrous process as a blow out and loss life. The significant and continuing losses of mud and /or cement slurry to a formation during drilling operations affects the oil industry. These problems have negative impact on well economics, well integrity and well life cycle. It has been globally estimated that these problems cause financial loss of billions dollars per year in addition to extensive depletion of rig resources. This paper presents an analysis review for advanced safety engineering controls and materials that are used during cementing in onshore oil construction projects.
Keywords:
Construction Material, Cementing, Lost Circulation, Light weight Cement
Cite this paper: Shamsa Al Menhali , Ghanim Kashwani , Abeer Sajwani , Safety Engineering Controls of Lost Circulation during Cementing in Onshore Oil Construction Projects, International Journal of Materials Engineering , Vol. 5 No. 3, 2015, pp. 46-49. doi: 10.5923/j.ijme.20150503.02.
1. Introduction
One of the primary contributors to loss circulation is fractured Calcium Carbonate reservoirs and depleted aquifer zones. Severe loss circulation results in poor well construction which on the long run deteriorates the casing corrosion and results in communication between different zones [1, 2]. Other problems, such as wellbore instability, stuck pipe and even blowouts have been the result of lost circulation. Losses in reservoir not only change the wettability of rocks and affect permeability but also affect production time based on effort to flush out the invaded fluid. Besides the obvious benefits of maintaining circulation, preventing or curing mud losses is important to other drilling objectives such as obtaining good quality formation evaluation and achieving an effective primary cement bond on casing. The use of cement spacer technology is a viable mean of resolving most of these problems. This technology can be applied to strengthen a wellbore with high degree of losses as preventive method. In addition, it can also be used as corrective method where wellbore has been fractured due to hydrostatic pressure or Equivalent Circulation Density (ECD). Onshore oil construction projects have experienced severe losses in surface holes due to depleted aquifers combined with fractured / highly permeable limestone formation [3, 4]. Aerated Mud, currently being used in onshore oil construction projects is not a solution for curing losses but only help to reduce the hydrostatic head to minimize the losses in depleted zone. Aerated Mud has many adverse effects in operations due to the abrasive nature of air (corrosion, erosion in tubular, twist off, uncertainty of hydrostatic head and hole cleaning). Conventional Loss Circulation Material (LCM) re-enforcement and cement plugs effectiveness in curing losses was found to be limited.
2. Lost Circulation
There are numerous lost-circulation treatments available in the drilling industry. These systems can be summarized into two main categories [5, 6]. First, conventional treatments are the ones that include a combination of granular, fibrous, and flaky materials that are mixed with either the drilling fluids during the drilling phase or with the cement slurries during the drilling and the primary cementing phases. Second, specialized treatments which include systems such as specialized cements, dilatant slurries, reinforcing soft or hard plugs, cross-linked polymers, and silicate systems that are also used either during the drilling or the cementing phases.The success level for curing lost circulation is highly dependent on key factors like the durability and the temperature limitation of the treatment, the treatment placement, and the impact of the treatment on the produced formations [5, 6]. The common technique is to cure the losses before proceeding with the cementing operation; however, there are numerous cases in which losses are encountered just before or during the cementing operations. Some of the traditional treatments for these scenarios have been spotting cement plugs in the open hole during the drilling phase or cementing with a lightweight cement system that includes LCM during the cementing phase. The success level for these kinds of treatments varied from one case to the other and there was a need for a new type of treatment.Total losses may also occur, where the return of fluids is completely lost to the surface. This may fall into either the minor or severe losses categories, depending on the amount lost and the time involved in regaining circulation.Lost circulation can be classified and falls into two main categories [7]:• "Minor losses" - losses are between 6 and 50 barrels and remains within those amounts, or is ceased, within 48 hours.• "Severe losses" - losses are greater than 50 barrels or it takes greater than 48 hours to control or cease the lost circulation.Although preferred stopping lost circulation completely is not always possible. Controlled losses allow wellbore full prevention which may result in an influx of gas or fluid going into wellbore and causing a “Kick “that lead to blow out. A number of options are used in onshore oil construction projects when lost circulation occurs depending on severity. For example, minor losses can be controlled by increasing the viscosity of the fluid with bentonite and/or polymers, or with the addition of other additives [8]:• Adding LCM in Drilling Fluid, cement or in Spacer will help to form net and prevent losing more fluid.• Reducing drilling fluid density to minimize formation Damage.Severe Losses will be handled the same conventional way in minor losses and unconventional method such as pumping additives followed by cement to create flash set of cement in affected formation. Also, if severe losses occur and circulation can’t be regained, several options are available depending on operational requirement and the depth being drilled at in relation to desired production geological zone where losses occurred and continuation of drilling the well is very often followed.Continuing drilling while pumping drilling fluid is one option, though continued drilling while pumping water is less costly and more often used. Sometimes, the cuttings from continued drilling will aid in reducing leaks or stopping losses altogether. A third option is to cement the zone where the losses occurred, and to drill through the cement and continue drilling the well. This third option is very often the most cost effective if severe losses occur, as lost circulation sometimes cannot be controlled with other methods. Also, onshore oil construction projects consider several factors depending on what additives are used:• Hole size currently being drilled.• Drilling fluid in use. The additives must be compatible.• Depth of the well in regards to geological stability.• Depth of well in relation to the desired production zones. Plugging a production zone is not a desired outcome.• Other drill string mechanical equipment such as a mud motor or tools. If the additive(s) will not go through the drill string, they cannot be used.
3. Innovation of Cement Design
3.1. Thixotropic Cement for the Aquifer Formation
The mechanism of thixotropic cement consists of a composition comprising of water, hydraulic cement, titanium chelates, and crosslink able that provide enhanced cementing subterranean zones. For example, onshore oil construction projects use thixotropic cements primarily to assist in controlling lost circulation problems, in certain squeeze cementing applications and in situations where maintaining annular fill is a problem. Cements possessing thixotropic properties are desirable since they provide rapid development of static gel strength after placement. That is to say, thixotropic cements are designed so that slurry viscosities remain low while the slurry is moving, but when allowed to remain static will rapidly gell [9].The subterranean formation is typically cemented or sealed by pumping aqueous hydraulic cement slurry into the annulus between the pipe and the formation. In the soft practiced placement of cement at the annular space between the casings of an oil well, the cement slurry is commonly pumped down inside the casing and backed up the annular space surrounding the casing. Occasionally, the cement is introduced directly into the annular space at the outer side of the casing. Where the cement has been pumped down the casing initially, any cement slurry which remains in the casing is displaced into the annulus by a suitable fluid or fluids.
3.2. Fibers in Cement Slurries
Fiber Reinforced Polymer (FRP) were introduced in 1980's to increase the tensile and compressive strength of materials which leads to more efficient, safe, stable, environmental friendly and durable features. Since late 1980's, fiber composite materials such as carbon fibers have been used in many applications and caused a revolution in this construction materials field. For example, Fibers have been used extensively in the construction industry as a way of reinforcing concrete. The main purpose of these fibers is to increase concrete toughness and prevent cracks from further propagation. Moreover the FRP's are use in many engineering fields nowadays such as automobile manufacturing, aerospace industries, Infrastructure and many construction field applications and etc.In cementing, Additives are monofilament polypropylene fibers that help counter lost circulation problems during primary or remedial cementing. They can also be used in plugs to increase durability, provide resistance to abrasion and impact, and support unstable holes to reduce the possibility of stuck pipe during drillout [10]. The use of solid lost circulation materials should be limited when pumping through small orifices, including liner hangers, stage collars, and poppet-type float collars and casing shoes. The use of bottom plugs with these materials is not recommended based on Practice.Eliminating or controlling lost circulation during drilling or cement operations is a costly and time-consuming process. Traditional treatments include lost circulation materials (LCM), cement, cross-linked polymers, dilatant slurries, reinforcing plugs, and silicate systems. The general practice is to cure the losses before proceeding to the cementing operation [11, 12]. The mixed results of such treatments affect the cementing operations and sometimes precede even with partial or total losses which led to the development of a fiber cement system. Fiber forms a fibrous network across highly permeable formations, induced and natural fractures, and vugular formations to prevent and stop the losses during remedial or primary cementing operations. Unlike conventional fibers that normally are difficult to disperse in the cement slurries and tend to plug surface and downhole equipment.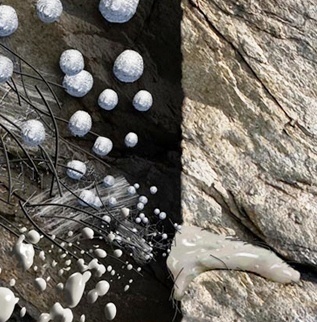 | Figure 1. Fiber mechanism in cement slurries |
Laboratory tests have shown the effectiveness of fiber in plugging different hole sizes. The efficiency of this system was enhanced in the laboratory when combined with high-performance lightweight cement slurry. Several jobs showed substantial success rates compared with traditional lost-circulation treatments. This was confirmed by cement returns to surface and cement coverage across the lost-circulation zones [13].
3.3. Light Weight Cement & Cement Spacer System
The invention relates to a light weight cement composition made from combined 2-3 particle with different sizes which are used in sealing or cementing subterranean zones penetrated by a wellbore; in addition to weak fractured formation such as cementing the annular space between an oil and/or gas well casing and the surrounding formation. Filtrates from cement slurries can damage producing formations, adversely affect production, and may require unscheduled stimulation treatments to address the problem. In addition, the increased Equivalent Circulating Density (ECD) generated by pumping cement slurries can lead to induced losses and contribute to a poor quality cement job. The cement spacer system is used to help mitigate lost circulation issues while cementing. It can minimize filtrate invasion, damage, and induced losses. Based on its ultra-low invasion fluid technology, this system forms a barrier at the wellbore wall to strengthen the wellbore. The formation can retain its integrity and permeability for optimized production because of the near 100% return permeability property of the spacer. Cement spacers reduce slurry fallback after placement, which prevents induced losses and eliminates costly remedial cement jobs. In wells with critical fracture gradients, cement spacer technology enables the use of standard slurry designs and densities where highly extended or special lightweight slurries were previously required. This also forms a seal to minimize filtrate invasion into the formation, effectively reduces cement losses and formation damage from filtrate migration, enhances hole cleaning prior to cement placement, effectively removing gelled drilling fluid by optimizing flow regime, density and chemical enhancement. It also provides wellbore strengthening, reduces incidents of induced losses, and is compatible with virtually all cement systems and drilling fluids [14, 15]. This eliminates the need to compromise on thickening times and compressive strength. Mixed at a base concentration of 15 lb/bbl, the spacer is weighted using barite. When used with an oil-based drilling fluid, proprietary cementing surfactant(s) should be added at a concentration of 0.5 to 3.0 gal/bbl.
4. Results & Conclusions
There are numerous lost-circulation treatments available in the drilling industry. These systems can be summarized into two main categories. Conventional treatments are the ones that include a combination of granular, fibrous, and flaky materials that are mixed with either the drilling fluids during the drilling phase or with the cement slurries during the drilling or the primary cementing phases. Specialized treatments include systems such as specialized cements, dilatant slurries, reinforcing soft or hard plugs, cross-linked polymers, and silicate systems that are also used either during the drilling or the cementing phases.The success level for curing lost circulation is highly dependent on key factors like the durability and the temperature limitation of the treatment, the treatment placement, and the impact of the treatment on the producing formations [16]. The common technique is to cure the losses before proceeding with the cementing operation; however, there are numerous cases in which losses are encountered just before or during the cementing operations. Some of the traditional treatments for these scenarios have been spotting cement plugs in the open hole during the drilling phase or cementing with a lightweight cement system that includes LCM during the cementing phase [17]. The success level for these kinds of treatments varied from one case to the other and there was a need for a new type of treatment and due to that the authors recommend the oil onshore construction companies to start using new materials such as fibers during the cementing process to enhance the mechanical properties of the isolation zone.
References
[1] | Liu Dawei, Kang Yili, Lei Ming, et al. Research progresses in temporary plugging technology for carbonate reservoir protection. Drilling Fluid & Completion Fluid, 2008, 25(5): 57–61. |
[2] | Otutu F. Novel wellbore strengthening enables drilling of exploration well in a highly depleted formation. SPE 148506, 2011. |
[3] | Tada H, Paris P C, Erwin N. The stress analysis handbook. Hellertown: All Research, 1973. |
[4] | Sun Jinsheng, Su Yi’nao, Luo Pingya, et al. Mechanism study on ultra-low invasion drilling fluid for improvement of formation pressure-bearing ability. Drilling Fluid & Completion Fluid, 2005, 22(5): 1–3. |
[5] | Kulkarni S, Savari S, Kumar A, et al. Novel rheological tool to determine lost circulation material (LCM) plugging performance.SPE 150726, 2012. |
[6] | Liu Xiangjun, Luo Pingya. Rock mechanism and petroleum engineering. Beijing: Petroleum Industry Press, 2004. |
[7] | Xie Heping, Chen Zhonghui. Rock mechanics. Beijing: Science Press, 2004. |
[8] | Li Daqi, Kang Yili, Liu Xiushan, et al. The lost circulation pressure of carbonate formation on the basis of leakage mechanism. Acta Petrolei Sinica, 2011, 32(5): 900–904. |
[9] | Dupriest F E. Fracture closure stress (FCS) and lost returns practices. SPE 92192, 2005. |
[10] | Salehi S, Nygaard R. Numerical modeling of induced fracture propagation: A novel approach for lost circulation materials design in borehole strengthening applications. SPE 135155,2012. |
[11] | Chen Mian, Jin Yan, Zhang Guangqing. Rock mechanics in petroleum engineering. Beijing: Science Press, 2008. |
[12] | Lü Kaihe, Qiu Zhengsong, Wei Huiming, et al. Study on techniques of auto-adapting lost circulation resistance and control for drilling fluid. Acta Petrolei Sinica, 2008, 29(5): 757–760. |
[13] | Li Jiaxue, Huang Jinjun, Luo Pingya, et al. Plugging mechanism and estimation models of rigid particles while drilling in fracture formations. Acta Petrolei Sinica, 2011, 32(3):509–513. |
[14] | Zheng Lihui, Kong Lingchen, Cao Yuan, et al. The mechanism for fuzzy-ball working fluids for controlling & killing lost circulation. Chinese Science Bulletin, 2010, 55(15): 1520–1528. |
[15] | Wang Gui, Pu Xiaolin. Plugging mechanism of drilling fluid by enhancing wellbore pressure. Acta Petrolei Sinica, 2010, 31(6): 1009–1021. |
[16] | Morita N, Fuh G. Parametric analysis of wellbore- strengthening methods from basic rock mechanics. SPE 145765, 2012. |
[17] | Yang Pei, Chen Mian, Jin Yan, et al. Crack pressure bearing capacity model and its application to plugging of fractured formation. Chinese Journal of Rock Mechanics and Engineering, 2012, 31(3): 479–487. |