A. A. Yekinni1, S. K. Bello1, L. O. Mudashiru2, L. A. Animashaun1
1Department of Mechanical Engineering, Lagos State Polytechnic, Ikorodu, Lagos
2Department of Mechanical Engineering, Ladoke Akintola University of Technology, Ogbomosho
Correspondence to: A. A. Yekinni, Department of Mechanical Engineering, Lagos State Polytechnic, Ikorodu, Lagos.
Email: |  |
Copyright © 2015 Scientific & Academic Publishing. All Rights Reserved.
Abstract
The QTS 124 agitation quench tank manufactured by L&L Special furnace Co. Inc to be used for uniform quenching of hot metals was redesigned, modified and developed for the purpose of this research. After modification the equipment can be used with different quenching media such as water, oil, light polymer and brine. Other distinguishing features introduced in the machine are electric heater and thermostat so that quenchant can be pre-heated to different temperatures to determine the effect of temperature gradient on hardness of metals and also obtain the optimum initial quenching temperature of quenchant for the desired mechanical property of any metal during heat treatment. Performance evaluation of the machine was carried out with as-cast Al 6050 alloy heated to 350C and was quenched in water and oil from 20C at 10C interval to 80C with and without agitation of the quenchant. The results showed that for both water and oil hardness decreases as quenchant temperature increases with and without agitation. Uniform and steady rate of cooling was achieved by agitation of samples in the quenching media. Also from hardness values obtained, water has greater effect on hardness of Al 6050 alloy when compared to oil for dimension of the specimen used.
Keywords:
Agitation, Hardness, Quenchent, Temperature gradient
Cite this paper: A. A. Yekinni, S. K. Bello, L. O. Mudashiru, L. A. Animashaun, Modification and Fabrication of Quenching Machine: Influence of Agitation and Temperature Gradient on Hardness of Al 6050 Alloy, International Journal of Materials Engineering , Vol. 5 No. 2, 2015, pp. 32-38. doi: 10.5923/j.ijme.20150502.03.
1. Introduction
Heat treatment of metals and alloys is one of the many wonderful processes discovered by man to mould materials to desired properties for making tools, implements, components and machines. It is a multiparameters process in which the selection of appropriate parameters predicts required behaviours of treated components. Heat treatment can be defined as an operation or set of operations in a metal involving heating for a period of time and cooling at a control rate to change the mechanical properties of the metal without changing the shape [1]. Transformation in the solid state can be obtained using heat treatment procedures, which cause changes in microstructure resulting in materials with a wide range of hardness and mechanical properties. Although an exact relationship between hardness and wear performance does not exist, hardness has traditionally been the properly used for quality control, selection of steel, and heat treatment and performance evaluation [2, 3].The QTS 124 quench tank developed by L&L Special Furnace Co Inc is used for the uniform quenching of hot steels. It may be used with water, lightweight polymer, or oil. It is not designed for use with brine. Water or polymer must have rust inhibitors (or else tank must be stainless steel). The QTS 124 features proper agitation which insures uniform quenching and disperses the bubbles of vaporized quenchant that form on the surface of the hot parts being quenched. These bubbles, if not dispersed, can cause uneven quenching times which would result in a poorly quenched part. The agitation also prevents localized overheating which, in the case of oil quench media, could cause a fire [4]. Reference [5] also designed a quench tank agitation using flow modelling and the quench speed was timed by the programmable logic controller.Quenching is a critically important process in the development of desired metallurgical properties in the heat treatment of steel and aluminium alloys. According to [6], quenching was described as a crucial step to suppress the precipitation to retain the supersaturation of solid solution, control the distortion, and minimize the residual stress in aluminium alloys. Quenching media commonly used for aluminium alloys include brine solution, air, water, oil and polymer solutions to obtain certain hardness and mechanical properties requirements [7, 8]. The ideal quenchant is one that exhibits little or no vapour stage, a rapid nucleated boiling stage, and a slow rate during convective cooling [9]. There are many factors that affect heat transfer rates during quenching and thus also affecting cooling curve shape. The most important of these factors and their effect on heat transfer rates are as summarized in table 1. The kind of quenching medium, the selection of quenching medium temperature and the selection of the medium state (unagitated, agitated) are determining factors [10]. According to [11], it is possible to determine the heat transfer coefficients during quenching using a probe.Reference [12] in their study used simulation to analyze two models of agitation system in quench process. The results showed that the cooling of material was not uniform for the case one (agitation in the bottom of the tank), because the temperature profile of one side was very different from the others, showing that in this case it is possible to occur different formation of microstructures in the same material. For the case where a lateral arrangement is used abetter uniformity was achieved. They therefore concluded that cooling uniformity is necessary to avoid the formation of different microstructures. Their analysis provides information of how computational fluid dynamics (CFD) can be used to improve control of quench process for optimal quench uniformity.Proper agitation insures uniform quenching and disperses the bubbles of vaporized quenchant that form on the surface of the hot parts being quenched. These bubbles, if not dispersed, can cause uneven quenching times which would result in a poorly quenched part [4]. The agitation also prevents localized overheating which, in the case of oil quench media, could cause a fire. Optimal quench uniformity is essential if the potential for cracking, distortion, residual stress and spotty hardness is to be minimized. This means that heat transfer during the film boiling (vapour blanket) and nucleate boiling processes during heat transfer in vaporizable liquids such as water, oil and aqueous polymers must be as uniform as possible throughout the quenching process. One of the most important factors affecting quench uniformity is the design of the quench system. Deficiencies in system design have frequently been inadequately addressed by both heat treating engineers and equipment suppliers, often with disastrous results. Reference [13] stressed further that to achieve optimal properties the cooling rate should be as uniform as possible. Therefore, magnitude and turbulence of fluid flow around a part in the quench zone is critically important relative to the uniformity of heat transfer throughout the quenching process. The impact of non-uniform flow is increased distortion and cracking. So it is critically important to optimize the uniformity of fluid flow in the quench zone to provide optimum control of distortion and to minimize cracking. Studies by [14] revealed that hardness of quenched sample is not uniform throughout the entire volume of the sample that it decreases with distance from the quenched end. There are many factors that affect heat transfer rate according to [15] during quenching. The most important of these factors are summarized in table 1.Table 1. Factors Effecting Heat Transfer Rates 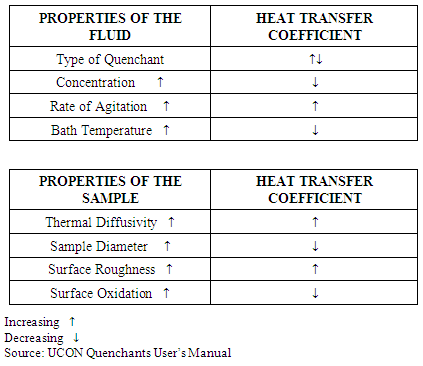 |
| |
|
According to [16], proper agitation of the quench bath is often the single parameter that dictates the success of the quenching process. That increasing agitation rates will result in a corresponding increase in heat transfer rates all three cooling phases during the quenching process. Quenching tank agitation can be provided by various methods including recirculation pumps, submerged spray, air or nitrogen sparge, impeller stirrer, ultrasonic’s, actual movement of the part itself, or a combination of two or more of these methods. Many schemes are deployed to ensure quench effectiveness: speed of drop, quenchant temperature, quench concentration and water soluble additives. However quench tank agitation has not been studied in the field as thoroughly as the other phases. The main obstacle has been the inability to see the flows and how they are related to the loads insert into the tanks. Many quench tanks are installed with designs that move volumes of quenchant with limited consideration to flow pattern and additions of work fixtures. Work fixtures or baskets can disrupt a seemingly well thought out agitation scheme in ways that completely defeat the designed agitation [5]. Therefore, the purpose of this study is to show how a seemingly “well” agitated quench tank can be studied and the process improved by introducing features that ensure its versatility.
2. Materials and Methods
2.1. Material Selection
The machine consists of the following component parts: Electric motor, electric heater, caster wheels, control switches, thermostat, specimen basket, quenching tank, tank cover, agitator (impeller), drain pipe and shaft coupling. In order to prevent corrosion, 18/8 grade steel was used to construct the frame, quenching tank, specimen basket, and cover. The shaft coupling was made of cast iron while the impeller was made of mild steel. Necessary assumptions were made on selection of type and power rating of electric motor and electric heater.The quenchant used in the study are water and Oil. Though according to [15], severe distortion and residual stresses are often encountered when aluminium is quenched in water, but when oil is used as quenching medium a drastic reduction in both residual stresses and distortion is achieved. A quenchant having similar physical properties with UCON nitrite quenchant A was selected.The quenchant with physical properties in table 2 is a non-flammable aqueous solution of a liquid organic polymer and a corrosion inhibitor produced by Mobil oil producing. When mixed with water at 1:1 it produces a clear homogenous solution at room temperature.Table 2. Physical properties of Quenchant 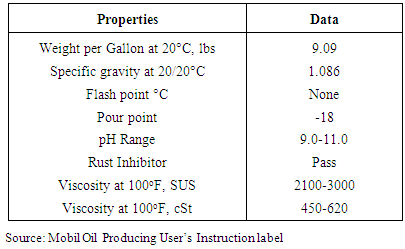 |
| |
|
2.2. Methods
2.2.1. Theoretical Frames
Design of quenching tank and specimen basketQuenching tank (0.209m3) and perforated specimen basket are made of 1mm thick stainless steel sheet.Volume of tank and basket were determined using equation (1) | (1) |
where, V = Volume of tank, D = Diameter of tank, H = Height of tank.Design of AgitatorThe nominal diameter of the impeller shaft was selected based on strength and rigidity. The agitator is a four blade angled impeller for open and close system suitable for oil, brine solution, water and polymer solution.The required power level is proportional to mixer speed by equation (2) | (2) |
Where P = power and N = impeller speed.Design of the control switchAll electrical connections were at normal for liquid tight box. An On/Off was included for the electric heater and a Start/Stop button for the agitation circuits inside the box. The control switch voltage is 240V.Design of Shaft coupling and KeywayA sleeve coupling was designed to transmit full torque by means of a key and a sleeve from electric motor to the agitator and to reduce transmission shock load during operation.The usual proportions of a cast iron sleeve coupling are as shown in equations 3a and 3b was used in the design. | (3a) |
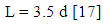 | (3b) |
Where D = outer diameter of sleeve, L = length of sleeve and d = diameter of shaft.The length of the coupling key is designed according to equation (4)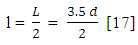 | (4) |
where l = length of coupling key.Drain pipeDrain pipe of diameter 30 mm was created near the bottom to drain the tank. The pipe is capped.
2.2.2. Fundamental Assumptions
1) Electric heater selectionAn electric heater rated 1500W was selected considering the capacity of the quenching tank to be attached to the base on one side of the machine. The power output is sufficient to pre-heat the quenchant to a specified temperature within a short period. A thermostat is provided to control the heater.The power rating was determined using equation (5) | (5) |
Where P = Power in Watt, m = mass of quenchant in Kg, ϴ = maximum expected temperature of the quenchant in C, t = time of heating in seconds, c= Specific heat capacity of quenchant in JKg-1C-12) Electric motor selectionThe electric motor used is 0.5Hp with a maximum speed of 1400rpm. Torque delivered by the motor is given by equation (6)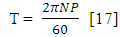 | (6) |
Where T = Torque in Nm, P = Power in Watt, N= Speed of electric motor in rpm.According to [10], input power into the oil per 1Kg Pw was calculated from torque moment and angular velocity values at device for swirling by formula in equation 7 | (7) |
WhereT = Torque momentN= rotational speedm = mass of oil in device3) Selection of Caster WheelsFour swivel caster wheels each of diameter 27mm were fixed for mobility of the machine. Two of these are stationary while the remaining two are movable for controlling and steering.
2.3. Experimental Procedure
2.3.1. Materials
The mechanical properties of cast Aluminium alloys of 6000 series are very attractive for many applications in military, automotive and aircraft industries since the silicon, as the major alloying element, can offer excellent castability, medium strength, good forming, good corrosion resistance characteristics, and machinability. Also the presence of small amount of magnesium makes the alloy heat treatable [6].Cast Al/Si, Al/SiMg-alloy (Al 6050) with the chemical composition in Table 2 is selected for the present investigation. Energy Dispersive X-ray Fluorescence Spectrometer EDX 3600B was used to conduct accurate analysis of elemental composition of the cast aluminium alloy.Chemical Composition of Al 6050 alloy (wt %) 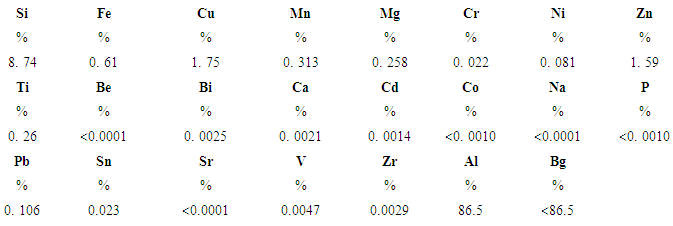 |
| |
|
2.3.2. Sample Preparation
Among the major casting processes, permanent mould casting can provide better mechanical properties, smoother cast surface, less tendency for entrapped gas, and finer dendrite arm spacing and grain structure [18]. About 25 Kg of Al 6050 knuckles were melted in a Morgan molten metal crucible furnace and cast into the pre-heated cast iron mould. The melt pouring temperature was kept constant at 800C. Aluminum alloy bars of dimension 200 x100 x 50 mm were cast in a permanent mould in the Foundry Workshop of Lagos State Polytechnic. Specimens of dimension 60 x 30 x 15 mm were fabricated from the cast bars and used in this study. The specimen was preheated to 350C in a Bamford Sherfield Carbolite heat treatment furnace and was quenched in water and oil (liquid organic polymer) from 20C at 10C interval to 80C with and without agitation of the quenchant. The tank agitation used in this study is 1400rpm.For the determination of hardness values sample surfaces were prepared using polishing machine model TegraPol-31, with silicon dioxide emery paper of grit size 4 x 10-2 μm.
2.3.3. Hardness Number Measurement Test
The Rockwell hardness test was done on Albert Gnehm Rockwell hardness tester. Twenty eight samples of Al 6050 were prepared. The Rockwell hardness values with reference scale HRB were taken for all samples and shown by graphs. Hardness before heat treatment (as cast) is 69HB.
3. Result and Discussion
3.1. Modified Agitated Quenching Machine
Figures 1-5 show the picture, geometric model, third angle projection, and exploded view of the manufactured modified QTS 124 L&L Quench machine.
3.2. Hardness Number
Figure 5 shows the hardness values of the aluminium cast after quenching in water and oil. It reveals a uniform and steady rate decrease in hardness as temperature gradient closes when quenchant was agitated. This is due to homogenous and decrease in formation of matensite in the Aluminium alloy matrix. The graphs also reveal non uniform and non-steady unagitated samples with decrease in hardness values as temperature gradient closes. The lower hardness value of the as-cast sample.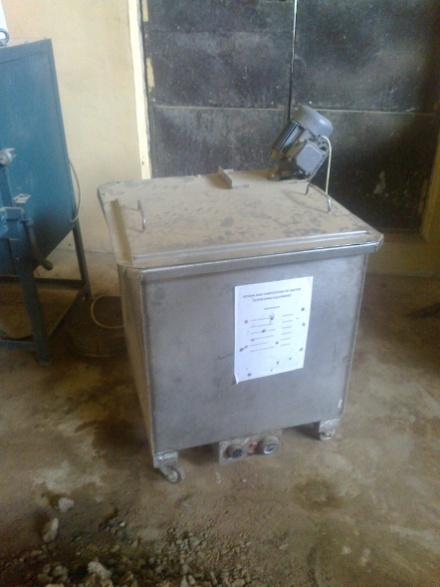 | Figure 1. Picture of the Agitated Quench machine |
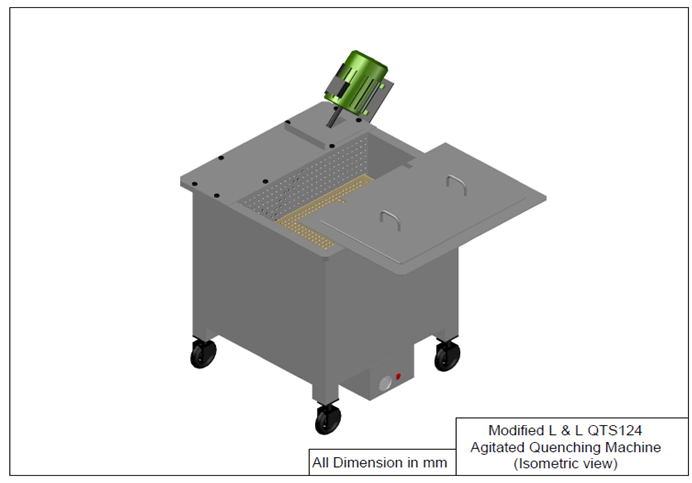 | Figure 2. The Isometric view of the Agitated Quench machine |
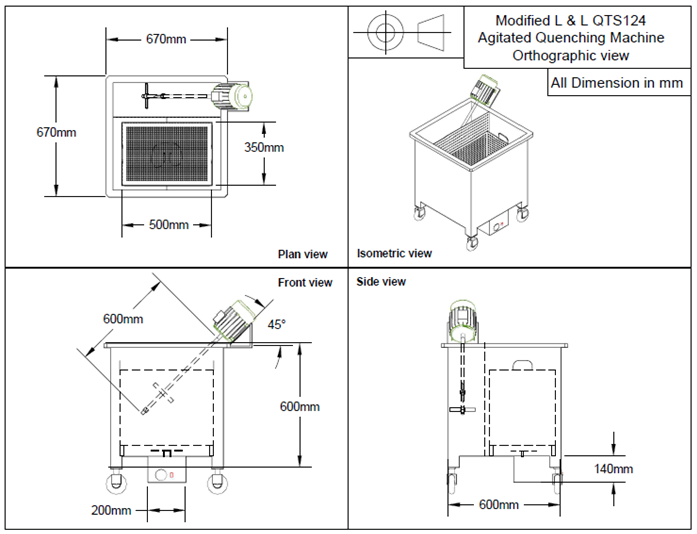 | Figure 3. The third angle projection of the Agitated Quench machine |
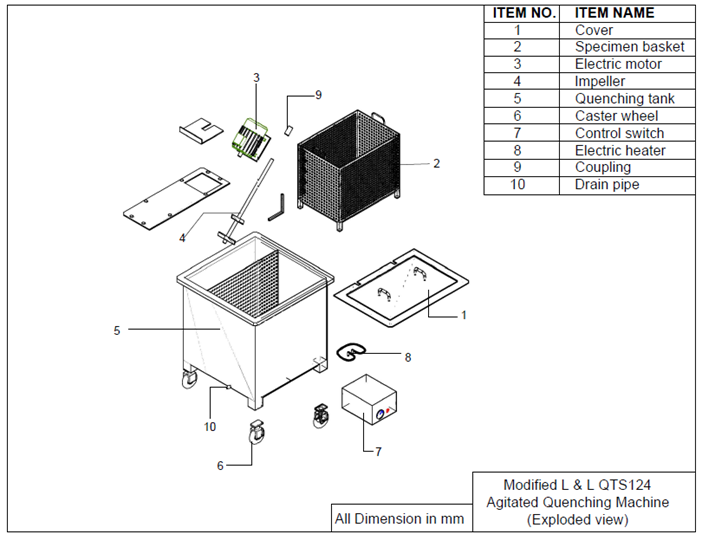 | Figure 4. The exploded view of the Agitated Quench machine |
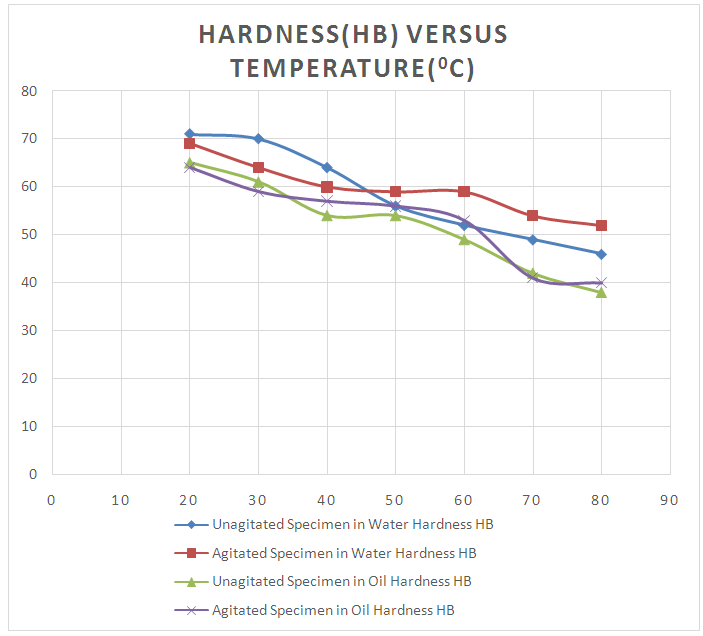 | Figure 5. Comparative hardness of Al 6050 Alloy in water and oil |
4. Summary
The following summary can be drawn from the present study:1. The Quenching Equipment was modified, fabricated and worked effectively with more versatility.2. The rate in decrease of hardness of unagitated of quenched samples is not uniform throughout the entire section of the sample due to non uniform heat transfer.3. The rate in decrease of hardness of agitated samples is uniform throughout the section due to improvement in film formation and therefore enhancing the uniformity of the heat transfer process.4. The equipment has no limitation in the use of quenchant.5. The equipment allows for variation of temperature gradient between the specimen and quenchant.6. Comparing the hardness values obtained for various sample when quenched in water and oil. It obvious that water is more suitable for thick aluminium alloys as there could be quenching distortion if water is used for thin sheet of aluminium alloys.7. Massive production and use of the equipment for heat treatment in the industries, research institutes and educational institutions will assist a developing country in ensuring its drive towards sustainable development in materials applications.
ACKNOWLEDGEMENTS
The Authors are grateful to the HOD, Mechanical Engineering of Lagos state Polytechnic, Ikorodu, Lagos, for his permission to allow the fabrication of the machine and use of equipment for test at the Mechanical Engineering Workshops.
References
[1] | Prabhudav, K.A. (1988) Handbook of Heat Treatment of Steels. Tata McGraw-Hill Publishing Company Limited, New Delhi. |
[2] | Musa R.S ‘(2008) Effect of type and character of quenching medium on Hardness of steel through heat treatment. This thesis is submitted to Faculty of Mechanical Engineering as Partial Fulfillment of Requirement for Award of the Degree of Bachelor of Mechanical Engineering (Structure & Material) Faculty of Mechanical Engineering Universiti Teknikal Malaysia Melaka. |
[3] | Totten G.E and Liang H (2004) Mechanical Tribology: Materials, Characterization and Applications, Eds, Marcel Dekker, New York, NY. |
[4] | L&L Special Furnace Co Inc. QTS 124 Small portable Agitated Quench Tank. Product Bulleting No QTS-3-00. http://www.thomasnet.com/productsearch/item/148521-8181-1028-1195/l-l- |
[5] | Bogh N (1994) Quench Tank Agitation Design Using Flow Modeling. Small portable Agitated Quench Tank. Proceeding of International Heat Treating Conference: Equipment and Processes, 18-20 Schaumburg, Illinois. |
[6] | Shuhui Ma (2006) A Methodology to Predict the Effects of Quench Rates on Mechanical Properties of Cast Aluminum Alloys. A Dissertation Submitted to the faculty of the Worcester Polytechnic Institutein partial fulfilment of the requirements for the Degree of Doctor of Philosophy in Materials Science and Engineering. |
[7] | Totten G.E (2007) Steel heat treatment handbook, second ed. Portland: CRC Press Taylor & Francis Group, 820. |
[8] | Bernardin J.D and I. Mudawar, I (1995) Validation of the Quench Factor Technique in Predicting Hardness in Heat Treatable Aluminum Alloys. International Journal for Heat Mass Transfer, 1995. 38(5) 863-873. |
[9] | Herring D.H (2010) Oil Quenching, The HERRING GROUP, Inc. Professional Support Services. http://www.heat-treat-doctor.com/... |
[10] | Taraba B, Duehring S, Spanielka J, and Hajdu S (2012), Effect of Agitation Work on Heat Transfer during Cooling in OilISORAPID 277HM. Journal of Mechanical Engineering 58, 2, 102-106 |
[11] | Hassan H.S, Peet M.J, Jalil J.M and Bhadeshia K.D.H (2009), Heat transfer and phase transformations in steels. PhD thesis, University of Technology, Bhagdad, Bhagdad, Iraq |
[12] | Bineli A.R.R, Barbosa M.I.R, Jardini A.L and Filho R.M (2010), Simulation to Analyze Two Models of Agitation System in Quench Process. 20th European Symposium on Computer Aided Process Engineering – ESCAPE20 |
[13] | Canale E and Totten G.E (2005), Quenching Technology: A Selected Overview of the Current State-of-the-art. Journal of Materials Research, Vol. 8, No. 4, 461-467. |
[14] | Yekinni A.A, Agunsoye J.O, Bello S.A, Awe I.O and Talabi S.I (2014), Fabrication of End Quenched Machine: Hardenability Evaluation. Journal of Minerals and Materials Characterization and Engineering, 107-113. |
[15] | UCON Quenchants. User’s Manual http://msdssearch.dow.com/PublishedLiteratureDOWCOM/dh_0064/0901b803800641b1.pdf?filepath=ucon/pdfs/noreg/118-01567.pdf&fromPage=GetDoc |
[16] | Totten G.E and Lally K.S (1992) Proper Agitation Dictates Quench Success. Part 1 Heat Treating Magazine. http//www.heat-treat-doctor.com/.. |
[17] | Khurmi R.S and Gupta J.K (2004) A Textbook of Machine Design. Eurasia Publishing House (Pvt) Ltd. Ram Nagar, New Delhi. |
[18] | Blackwood R.R, Webster G.M, Totten G.E, Narumi T and Jarvis L.M (1996) Reducing aluminum distortion with Type I quenchants. Metal Heat treating 28-31. http://www.books.google.com.ng/books?isbn=0203912594. |