Pedro Gutemberg de Alcântara Segundinho1, Carlito Calil Neto2, Antonio Alves Dias2, Carlito Calil Junior2, André Luis Christoforo3
1Department of Forestry and Wood Sciences, Center of Agricultural Sciences, Federal University of Espírito Santo, Espírito Santo, Brazil
2Department of Structural Engineering, Engineering School of São Carlos (EESC/USP), São Carlos, Brazil
3Centre for Innovation and Technology in Composites (CITeC), Department of Civil Engineering, Federal University of São Carlos, São Carlos, Brazil
Correspondence to: André Luis Christoforo, Centre for Innovation and Technology in Composites (CITeC), Department of Civil Engineering, Federal University of São Carlos, São Carlos, Brazil.
Email: |  |
Copyright © 2014 Scientific & Academic Publishing. All Rights Reserved.
Abstract
Although the glulam is a product of the nineteenth century, there are few industries in Brazil. The high cost of the structural elements of glulam is committed at the time, its competitiveness with full tropical sawn timber and reforestation. Being a tropical country, we recommend the use of wood treated to prevent termites attack. This study aims to evaluate the resistance of glulam beams before and after being subjected to chemical treatments with pressure using CCA (Copper Chrome Arsenic) and CCB (Copper Chrome Boron). To that end, we tested 54 glulam beams with nominal dimensions of 9cm×9cm×200 cm, with wood harvested from forest plantations. These beams were subjected to static bending tests, according to Brazilian standard NBR 8458:1984. After analyzing the experimental data it was concluded that the glulam beams produced from wood of Pinus oocarpa had the best results, taking into account the combination wood-adhesive-treatment, because the physical properties remained the same before and after chemical treatment in fullcell method.
Keywords:
Glued laminated timber (glulam), Wood reforestation, Chemical treatment
Cite this paper: Pedro Gutemberg de Alcântara Segundinho, Carlito Calil Neto, Antonio Alves Dias, Carlito Calil Junior, André Luis Christoforo, Evaluation of Brazilian Reforestation Species in Glulam Beams before and after Preservative Chemical Treatments, International Journal of Materials Engineering , Vol. 4 No. 6, 2014, pp. 192-195. doi: 10.5923/j.ijme.20140406.02.
1. Introduction
The glulam is an engineered wood product that requires precision manufacturing in all its stages. The finished product can only be tested in laboratory conditions, so you need quality control in production to ensure that the physical properties of the glulam are appropriate to those specified in current standards, according to [1].The glulam is a structural component consisting of a combination of selected wood laminate, bonded with waterproof adhesive, pressure variable from 0.7 to 1.5 MPa. The blades, attached by glue, are arranged so that its fibers are parallel to each other [2-7].The advantage of glulam is the use of small parts for laminating structural beams. Pieces of several classes of resistance can be used in beams with high strength the parties to composing the outer. One can also vary in the kind of wood structure, according to the application of resistance laminations in each region of the beam [8].The advantage of glulam is the use of small parts for laminating structural beams. Parts of various classes of strength can be used in beams with high strength parts composing the outer. One can also vary in the kind of wood structure, according to the application of resistance laminations in each region of the beam.The objective of this work was to evaluate the resistance of the glulam beams produced from reforested wood planted in Brazil. This evaluation was done by means of standard static test in the Brazilian standard [9]. This paper deals with the method of construction, testcrosses of glulam and their specimens taken from them.
2. Material and Methods
For the production of glulam beams were used species of wood Teak (Tectona grandis), Pinus oocarpa (Pinus oocarpa shied) and Lyptus® (registered trademark of Aracruz Produtos de Madeira (APM)). All these woods have been extracted from renewable forests of trees planted in Brazil, so without running the risk of damaging the environment. For each species produced 18 glulam beams, 9 glued with resorcinol adhesive phenol formaldehyde (RFF) and 9 with adhesive polyurethane (PUR), totaling 54 glulam beams for the three species of wood. After the production the glulam beams was treatment with basis of chemical preservative CCA (Copper Chrome Arsenic) and CCB (Copper Chrome Boron) in fullcell method, to protect against the attack of insects.The production process of 54 glulam beams follows the following steps: storage timber; visual rating; rating mechanics, grouping of wood, processing of the laminate; manufacturing crosspieces; drilling and rounding of the upper surface; preservative treatment against insects; storage of glulam beams. Such glulam beams were placed with an intensity of pressure of 1.0MPa, non-random distribution of weight for both laminate and the adhesives was applied with two spreading rate of 300 to 350 g/m2. The glulam beams had length of 200 cm and cross section of 9cm×9cm and were made with three pieces of wood, each laminate with 30 mm thick. Figure 1 shows the manufacturing planning glulam beams. Figure 2 shows the fabrication of glulam beams and Figure 3 shows glulam beams for static bending test.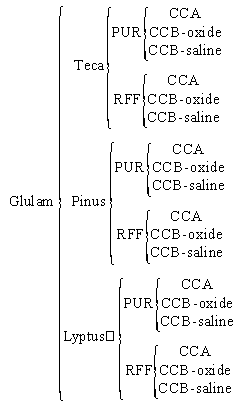 | Figure 1. Manufacturing planning of the glulam beams |
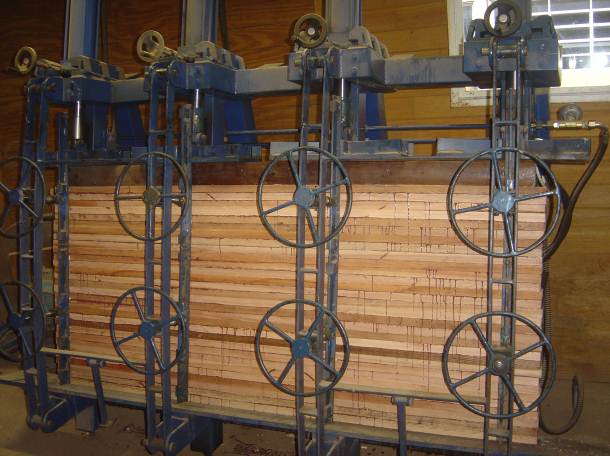 | Figure 2. Wood pressing glulam beams Lyptus® RFF with adhesive on hydraulic press "A" |
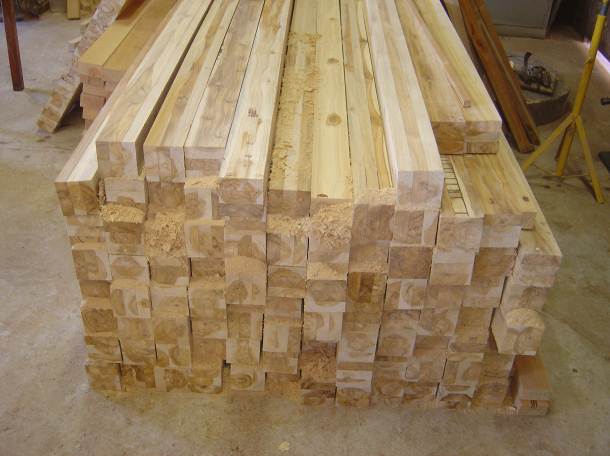 | Figure 3. Glulam beams |
Tests for resistance to bending of glulam beams were performed to evaluate the mechanical properties requirements, according to Brazilian standard [9]. Figure 4 shows the test of resistance to bending of glulam beams.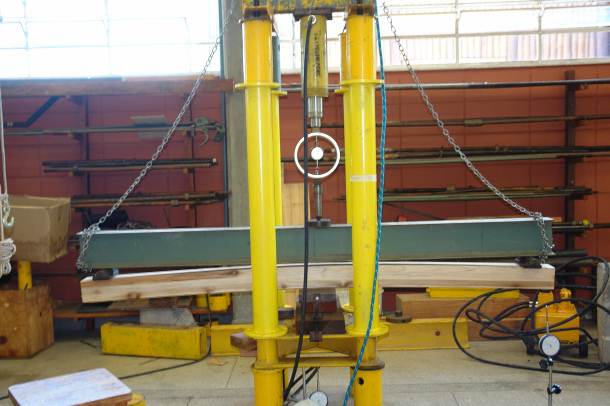 | Figure 4. Static bending test of glulam beams, untreated Teak wood |
The glulam beams be tested and compared with the assessment parameters set out in Table 1, according to Brazilian standard [9].Table 1. Comparison parameters 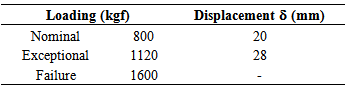 |
| |
|
3. Results and Discussions
Average results of displacements of glulam beams without preservative treatment. The results presented in Tables 2-5 relate to the beams without glulam treatment and preservative treatment made from the three species of wood and forestry work with two structural adhesives. Table 2 presents the mean values of arrows, for glulam beams tested on all four sides without preservative treatment.Table 2. Average results of displacements of glulam beams without preservative treatment 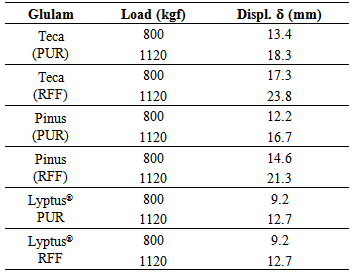 |
| |
|
Table 3. Average results of mass and tensile strength of the glulam beams without preservative treatment 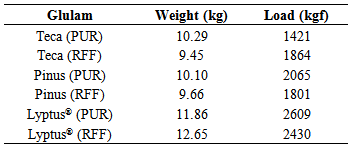 |
| |
|
Table 4. Average results of displacements of glulam beams with preservative treatment 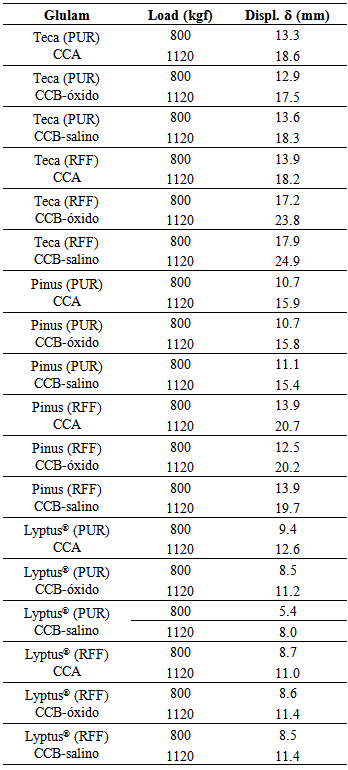 |
| |
|
Table 5. Average results of mass and tensile strength of the glulam beams with preservative treatment 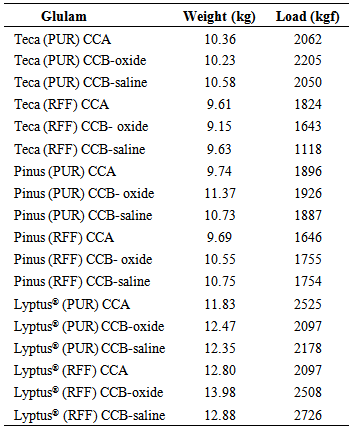 |
| |
|
Table 3 shows the average values of weight and tensile strength for the various types of glulam beams without treatment. Table 4 presents the mean values of the glulam with preservative treatment. Table 5 shows the mean values of the mass and tensile strength for the various types of glulam beams with preservative treatment.
4. Conclusions
It can be concluded that all glulam beams with and without chemical treatment in fullcell method passed the criteria of the Brazilian standard [9] taken when the values of arrows corresponding to the nominal loads of 800 kgf (7845.32 N) and 1120 kgf (11767.98 N) most exceptional. Only minimal disruption in loading, corresponding to 1600 kgf (15690.64 N), Teak beams (RFF) has not exceeded this criterion.Was also observed that the glulam beams made from Teak woods and Lyptus®, did not change its mass, showing that the chemical treatment in fullcell method did not penetrate them. However, the glulam beams from Pinus oocarpa changed its mass.The preservative treatment in Pinus oocarpa not interfere with the strength of the glulam beams, but in Teak and Lyptus® the treatment interferes in strength occurs because delamination.During the endurance tests after chemical treatment showed that the rupture occurred at the glue line delamination in various glulam beams made from Lyptus® wood.Overall the manufacture of glulam beams from reforested wood is certainly a big draw, because besides having an excellent strength/weight does not cause environmental damage and contributes to carbon sequestration from the atmosphere.
ACKNOWLEDGEMENTS
The Foundation for Research Support of the Espirito Santo (FAPES) by support.The authors thanks all the employees from LaMEM/SET/ EESC/USP and CPFL Energy that, directly or indirectly, in partnership contributed to this work was done.Companies LTD Agrotec Agricultural Enterprises and Aracruz Wood Products for the supply of Teak wood and Lyptus®, respectively.
References
[1] | CAN/CSA 077. Qualification Code for Manufactures of Structural Glued – Laminated Timber, Canadian Standards Association, 2006. 16p. |
[2] | Bodig, J.; Jayne, B.A. Mechanics of wood composites. New York: Van Nostrand Reinhold Co. Inc., 1982. 712p. |
[3] | Calil Neto, C.; Christoforo, A. L.; Rocco, F. A. L.; Calil Junior, C. Analysis of Specie - Treatment - Adhesive Combinations for Glulam Purpose. International Journal of Composite Materials (Online), v. 4, p. 41-47, 2014. |
[4] | Christoforo, A. L. ; Rocco, F. A. L. ; Chahud, E. ; Branco, L. A. M. N.; Battistelle, R. A. G.; Valarelli, I. D. Influence of Storage Period of Pieces in Stiffness of Pinus elliottii Glulam Beams. Advanced Materials Research (Online), v. 1025-1026, p. 64-67, 2014. |
[5] | Almeida, D. H.; Cavalheiro, R. S.; Macedo, L. B.; Calil Neto, C.; Christoforo, A. L.; Calil Junior, C.; Rocco, F. A. L. Evaluation of Quality in the Adhesion of Glued Laminated Timber (Glulam) of Paricá and Lyptus Wood Species. International Journal of Materials Engineering, v. 4, p. 114-118, 2014. |
[6] | Segundinho, P. G. A.; Carreira, M. R.; Calil Neto, C.; Regazzi, A. J.; Dias, A. A.; Calil Junior, C. Avaliação do módulo de elasticidade de peças de madeira laminada colada (MLC) obtido por meio do ensaio de vibração transversal. Ambiente Construído (Online), v. 13, p. 7-14, 2013. |
[7] | Fiorelli, J.; Dias, A. A. Glulam beams reinforced with FRP externally-bonded: theoretical and experimental evaluation. Materials and Structures, v. 44, p. 1431-1440, 2011. |
[8] | Forest Products Laboratory. Wood Handbook: Wood as an Engineering Material. Madison: U.S. Department of Agriculture, 1999. 463p. |
[9] | Associação Brasileira de Normas Técnicas. NBR 8458. Cruzetas de Madeira para Redes de Distribuição de Energia Elétrica. Rio de Janeiro, 2010. 11p. |