M. T. Isa1, S. Usman1, A. O. Ameh1, O. A. Ajayi1, O. Omorogbe1, S. U. Ameuru2
1Department of Chemical Engineering, Ahmadu Bello University, Zaria, Nigeria
2Department of Textile Science and Technology, Ahmadu Bello University, Zaria, Nigeria
Correspondence to: S. Usman, Department of Chemical Engineering, Ahmadu Bello University, Zaria, Nigeria.
Email: |  |
Copyright © 2014 Scientific & Academic Publishing. All Rights Reserved.
Abstract
Surface modification of natural reinforcements can enhance their adhesion to polymer matrices. This work reports the effects of varying NaOH concentration (5%, 10%, 15% and 20%) on the properties of the composites at 15wt% fiber loading and 50:50 okra/glass fiber ratio. The result indicated that treatment concentration greatly influence the properties of the resulting composite, showing significant improvement over the untreated fiber composites. The 5 wt % of NaOH treatment concentration gave better MOR (50345.2 kN/m2) and minimal water absorption properties (1.98%). Better tensile strength (24.48MPa), MOE (785.9Mpa) and elongation at break (2.93mm) was observed with composites made with the 10 wt % NaOH concentration treated fiber. The composite have properties which suggest their suitability for application in the building and construction industries as panels for portioning and flooring or wall coverings, architectural landscaping to replace the hardwood currently used hence, preserving the environment.
Keywords:
Okra fiber, Glass fibers, Hybridization, Fiber treatment, Mechanical properties, Water absorption
Cite this paper: M. T. Isa, S. Usman, A. O. Ameh, O. A. Ajayi, O. Omorogbe, S. U. Ameuru, The Effect of Fiber Treatment on the Mechanical and Water Absorption Properties of Short Okra/Glass Fibers Hybridized Epoxy Composites, International Journal of Materials Engineering , Vol. 4 No. 5, 2014, pp. 180-184. doi: 10.5923/j.ijme.20140405.03.
1. Introduction
The final behavior of a composite material depends to a great extent on the adhesion between the reinforcing fiber and the matrix. The adhesion between two different materials is a function of several factors among which are the surface roughness and surface polarity [1, 2]. In order to improve adhesion between cellulosic material and polymeric matrix, several fiber surface modifications such as reaction with acid [3-6], organosilane [8-11] and alkaline treatment (Mercerization) [5, 11-13] have been reported.Mercerization as proposed by ASTM D1965 is the process of subjecting vegetable fiber to an interaction with a fairly concentrated aqeous solution of a strong base, to produce great swelling with resultant changes in the fine structure, dimension, morphology and mechanical properties [14]. When natural fibers are stretched, such arrangement amongst the fibrils would result in a better load shearing by them and hence result in higher stress development in the fiber.Syndenstricker et al., [15] studied the effects of varying NaOH concentration on sisal-polyester composite and observed that NaOH treatment of the sisal fiber decreases fiber density and 10% treatment concentration results in a rougher fiber surface. Girishal et al., [16] concluded in their study that alkali treatment of natural fiber improved the quality of the fiber/matrix interface and hence having significant effect on the mechanical properties of natural fiber reinforced composites. Mishra et al., [17] observed excess delignification of the fiber at 10% NaOH concentration resulting in weaker fibers. NaOH treatment concentration and soaking time were also reported to greatly affect the properties of coir- polyester composite [18].Due to their good mechanical properties and environmental advantages, natural fibers have proved to be a suitable reinforcement material [19] and therefore ways of improving these properties to make them more applicable as structural materials need to be investigated. This study aims to develop natural fiber composite from a relatively new but widely available okra fiber. Investigation of the mechanical and water absorption properties of okra – glass fiber hybrid composite and the effect of varying concentration of NaOH on fiber modification was studied.
2. Experimental
2.1. Materials
The Okra fibers, Glass fibers, the epoxy (Grade 3554A) and the hardener (Grade 3554B) were purchased from Juneng Nigeria ltd, Nssuka, Nigeria and the Sodium hydroxide pellet and acetic acid manufactured by ReAgent Chemicals UK and supplied by Moore Chemicals, Zaria, Nigeria.
2.2. Method
2.2.1. Mould Preparation
A mould with dimensions 210mm x 160mm x 20mm cavity was used in this work. The mold cavity was cleaned to remove particles and then coated with layers of releasing agent (wax) for easy removal (Demolding) of the composite.
2.2.2. Solution Preparation
5% w/v, 10% w/v, 15% w/v and 20% w/v Sodium hydroxide solutions were prepared in 500ml beaker by diluting 20g, 40g, 60g and 80g pellets respectively of sodium hydroxide in 400ml of distilled water. 5% v/v acetic acid solution was prepared in a 500ml beaker by mixing 20ml of acetic acid in 380ml of water.
2.2.3. Fiber Preparation
The okra and glass fibers were chopped to 20mm fiber length. Some quantity of the okra fiber were soaked in the prepared 5% w/v sodium hydroxide (NaOH) solution to remove some of the lignin (delignification) and other materials like wax and pectin. The soaked fibers were kept in the refrigerator (about 5℃) for 20 mins with occasional stirring. On expiration of the time, they were removed, washed with tap water and then soaked in the prepared 5% v/v acetic acid solution for 5 mins to neutralize the excess sodium hydroxide left on the fibers. The fibers were then washed with tap water and finally washed thoroughly with distilled water. They were dried in air for two weeks and finally in an oven at 70℃ until they attain constant weight. The procedure was repeated using the 10% w/v, 15% w/v and 20% w/v sodium hydroxide solutions respectively.
2.2.4. Treated Okra/Glass-Epoxy Composite Specimen Preparation
Preliminary loading of the short okra fiber in the pre-calculated matrix showed that the mean loading capacity was 15 wt %, compared to the 20.4 wt % reported by Srinivasababu et al., [20].The treated okra and glass fibers were hybridized on 50:50 ratio based on the 15 wt% total fiber weight established. The composite samples were made respectively by mixing the pre calculated volume of epoxy and hardener in the ratio of 5:1 by weight in a plastic cup and stirred thoroughly for 10 minutes. A portion of the mixture was poured into the prepared mold and some quantity of the hybridized 50:50 (treated okra [5% w/v conc. NaOH): glass) fibers were loaded in random orientation using hand lay-up method. Brush was used to apply the matrix to ensure the fibers were properly coated with the matrix. The procedure was repeated until the remaining fiber and the matrix was exhausted. The sample was cured at room temperature for 24 hours under load. It was then demolded and further post-cured in an oven at 70℃ for 3 hours. The procedure was repeated using the 10% w/v, 15% w/v and 20% w/v treated okra fibers respectively.
2.3. Characterization
Tensile testing of the composite specimens was carried out using an Instron Machine Model 3369, System Number 3369K1781, Capacity 50kN, Maximum speed 500mm/min, located at Center for Energy Research and Development (CERD) OAU Ile-Ife , Nigeria using ASTM D638. The flexural test was conducted according to ASTM D790 using the Enerpac universal material testing machine, located at the Department of Mechanical Engineering, Ahmadu Bello University Zaria, Nigeria. The flexural modulus (MOR), was calculated using Equation 1  | (1) |
Where, S is the span length of the sample (guage length). P is the load applied; b and tare the width and thickness of the specimen respectively.Water absorption test was conducted using the procedure outlined in accordance with ASTM D570-98. Equation 2 was used to establish the percent water absorbed. Where wi is initial weight of dry sample and wf is final weight of wet sample. | (2) |
All the results were taken as the average of 3 samples for each testing.
3. Results and Discussion
3.1. Tensile Strength
The tensile strength result of the treated okra fiber hybridized composite is presented in Figure 1. A positive treatment effect was observed with fibers treated with the 5 w/v % and 10 w/v % concentrated NaOH solution respectively. They exhibited 46.7% and 98.1% increase in their tensile strength values as compared to the untreated hybrid composite. As the concentration of the NaOH solution was increased to 15% and 20% respectively, a negative effect of treatment was observed.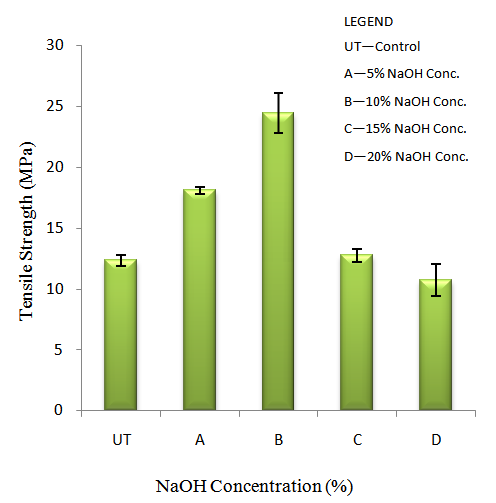 | Figure 1. Effect of Fiber Treatment on the Tensile Strength of the Composite |
The positive treatment effect observed with the composite treated with 5% and 10% concentrated NaOH solution may be attributed to the fact that the alkali treatment resulted in an improvement in the interfacial bonding by giving rise to additional sites of mechanical interlocking, hence promoting more resin-fiber interpenetration at the interface [1]. The alkali treatment improves the surface adhesive characteristics by removing natural and artificial impurities, thereby producing rough surface topography. After certain optimum concentration or higher percentage of alkali treatment, the tensile strength of the composite decreases drastically. At high alkali concentration, excess delignification of okra fiber occurs which makes the fiber weaker [17]. Thus for 15% and 20% alkali treated fiber composites, the lowering of strength was observed.
3.2. Modulus of Elasticity (MOE)
Figure 2 presents the effect of fiber treatment on the MOE of the composite. It was observed that treated fibers improve the tensile modulus of the composite.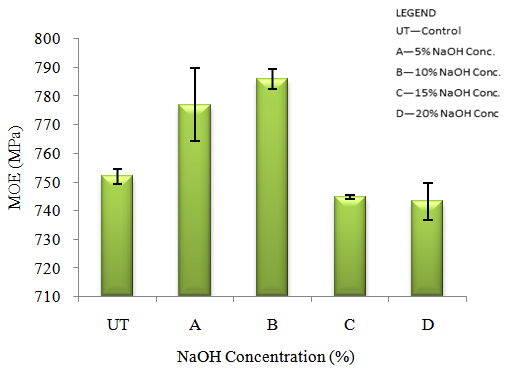 | Figure 2. Effect of Fiber Treatment on the MOE of the Composite |
An improvement of about 1.2% and 4.5% were recorded with the 5% and 10% concentrated NaOH treated fiber composites respectively. It can be observed that the composite made with 10% concentrated NaOH treated fiber exhibited highest average MOE value. Further increase in the concentration of the NaOH resulted in the reduction in the MOE value of the composite. The enhancement in the MOE of the alkali treated composite could be attributed to the improved wetting of the fibers [21]. It could also be attributed to the fact that alkali treatment improves the adhesive characteristics of fiber surface by removing natural and artificial impurities, thereby producing a rough surface topography. It also leads to fibrillation, creating more available surface area on the fiber to interact with the matrix [22]. The increase in tensile modulus for the treated fiber may also be due to the structural transformation of fiber from cellulose-I to cellulose-II. Therefore at 10% NaOH, better compatibility and adhesiveness is achieved [23].The decreasing MOE value observed after the optimal 10% concentration may be attributed to the fibers losing its characteristics [21]. It could also be attributed to damaged fiber surface as a result of the high concentration of alkali [23].
3.3. Elongation at Break
Figure 3 presents the effect of fiber treatment on the elongation at break of the hybridized composite. The composite resulting from the 10% concentrated NaOH solution treated fiber exhibited the highest elongation at break of 2.9mm corresponding to 19% higher than the untreated fiber composite. 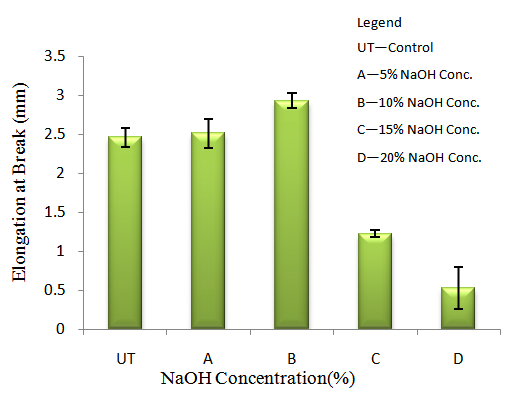 | Figure 3. Effect of Fiber Treatment on the Elongation at Break of the Composite |
The enhanced elongation on treatment is due to the fact more hemicelluloses are removed from fiber as a result of the treatment providing more surface roughness, hence giving rise to better interlocking with the matrix [1]. However, at very high alkali (15% and 20%) treatment concentrations, deterioration in the strength of the composite was observed. This may be due to cellulosic chain scission at high alkali concentration, resulting in loss of strength of the fibers [17, 24].
3.4. Modulus of Rupture (MOR)
The effect of fiber treatment on the flexural modulus of the hybridized composite is presented in Figure 4. The results showed that fiber treatment concentrations strongly affect the flexural modulus of the composite.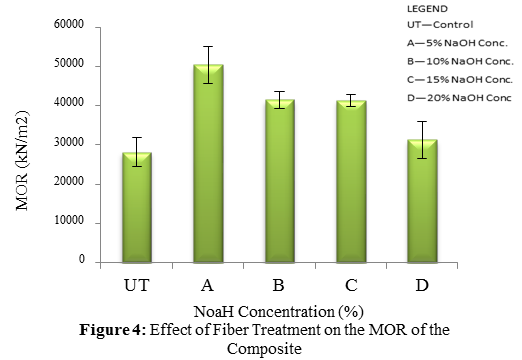 | Figure 4. Effect of Fiber Treatment on the MOR of the Composite |
Positive treatment effect was observed with the 5% alkaline concentrated treated fiber composite as compared to the untreated composite, hence presents the best flexural modulus of 50345.2kN/m2 (50.4MPa), which is 78.8% higher than the untreated fiber composite. With higher concentration of alkaline treatment, a negative effect was observed when compared to the 5% alkaline concentrated treated fiber composite.The increasing flexural modulus with alkaline treatment could be as a result of formation of fibers (fibrillation). Fibrillation is observed in treated fibers and this may be due to the leaching out of the waxy substances. After alkaline treatment, the materials in the inter-fribillar region reduces with increasing concentration of alkaline solution and treatment time, hence the interfacial interaction between the fiber and the matrix are increased. It also increases the surface area available for contact with matrix and possibly increases the possibility of load transfer between the fiber and the matrix [25]. The decreasing trend observed after the optimum 5% alkaline treatment concentration may be as a result excess delignification of the okra fiber with increasing alkaline concentration resulting in a weaker or damaged fiber.
3.5. Water Absorption
The effect of fiber treatment on the water absorption capacity of the composite is presented in Figure 5. It was observed that the water absorption capacity of the untreated fiber hybrid composite dropped from 2.6% to 2.0%, when the fibers were treated with 5% concentrated NaOH solution. Denser NaOH solution treatment further increased the water uptake of the composite as compared to the 5% concentrated NaOH solution treated fiber composite. The reduction in the water absorption could be attributed to the greater adhesion between the fiber and the matrix, which could be possible due to the surface treatment of the fibers [17]. By providing additional sites for mechanical interlocking, alkali treatment leads to improvement of interfacial bonding hence, promoting resin-fiber interpenetration at the interface. This hydrophobic resin pick-up could also account for the reduction in water absorption.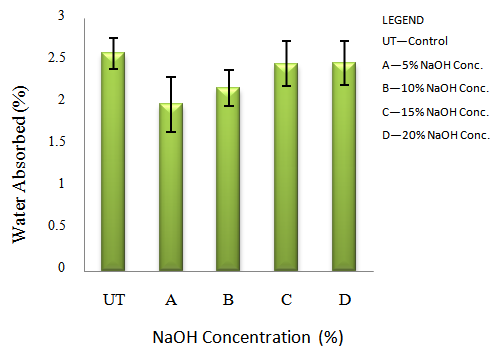 | Figure 5. Effect of Fiber Treatment on the Water Absorption propertiy of the Composite |
4. Conclusions
The effects of fiber treatment on the properties of short okra and glass fiber hybridized composite have been investigated in this paper.Fiber treatment greatly improves the properties of natural fibers by creating a rougher surface for good adhesion between the cellulosic fibers and the polymeric matrices. Better flexural strength and minimal water absorption was obtained at 5 wt % of NaOH treatment concentration. The 10 wt % treatment concentration produced composite with better tensile strength, MOE and elongation at break.The composite have properties which suggest their suitability for application in the building and construction industries as panels for portioning and flooring or wall coverings, architectural landscaping to replace the hardwood currently used hence, preserving the environment.
References
[1] | A.K Bledzki, J. Gassan, “Composites Reinforced with Cellulose Based Fibres” Prog. Polym. Sci. 24; 1999 221–274. |
[2] | Kokta BV, Raj RG, Deneault C, Polym – Plasttechnol Eng. 1989; 28: 247 – 259. |
[3] | Zafeiropoulos N.E, Williams D.R, Baillie C.A, Matthews FL.”Engineering and Characterisation of the Interface in Flax Fibre/Polypropylene Composite Materials. Part I. Development and Investigation of Surface Treatments” Compos Part A 2002; 33:1083–1093. |
[4] | Marcovich N. E, Reboredo M. M, Arangurenmi.”Dependence of the Mechanical Properties of Wood flour-Polymer Composites on the Moisture Content” J Applpolymsci 1998; 68:2069–2076. |
[5] | Mwaikambo L.Y, Martuscelli E, Avella M. “Kapok/Cotton Fabric Polypropylene Composites” Polym Test 2000;19: 905–918. |
[6] | Joseph P.V, Joseph K, Thomas S. “Effect of Processing Variables on The Mechanical Properties of Sisal-Fiber- Reinforced Polypropylene Composite. Compos Sci technol 1999; 59: 1625–40. |
[7] | Karnani R, Krishnan M, Narayan R. “Biofiber-Reinforced Polypropylene Composites”. Polymengsci 1997;37: 476–83. |
[8] | Hornsby P.R, Hinrichsen E, Tarverdi K. “Preparation and Properties of Polypropylene Composites Reinforced with Wheat and Flax Straw Fibres. Part II. Analysis of Composite Microstructure And Mechanical Properties”.J Mater Sci 1997; 32:1009– 1015. |
[9] | Kokta B.V, Raj R.G, Daneault C. Use of Wood Flour as Filler in Polypropylene: Studies on Mechanical Properties. Polym-Plast technol eng1989;28:247–259. |
[10] | Coutinho F.M.B, Costa T.H.S, Carvalho D.L. Polypropylene-Wood Fiber Composites: Effect of Treatment And Mixing Conditions on Mechanical Properties. J Applpolymsci 1997; 65:1227–1235. |
[11] | Joseph K, Thomas S, Pavithran C. Effect Of Chemical Treatment on The Tensile Properties of Short Sisal Fibre Reinforced Polyethylene Composites. Polymer 1996; 37: 5139–49. |
[12] | Sydenstricker T.H.D, Mochnaz S, Amico S.C. Pull-Out and Other Evaluations in Sisal-Reinforced Polyester Biocomposites. Polym Test 2003; 22:375–80. |
[13] | George J, Sreekala MS, Thomas S. A Review On Interface Modification and Characterization Of Natural Fiber Reinforced Plastic Composites. Polym eng sci 2001; 41:1471–85. |
[14] | Aboulfadl A.M, Zeronian S.H, Kamal M.M, Kim M.S, Ellison M.S. Textile Res. Inst. 1985; 55: 461 – 464. |
[15] | T. H. D Sydenstricker Et Al., “Pull Out and Other Evaluations in Sisal Reinforced Polyester Hybrid Composite” Polymer Testing Vol 22: 2003; 375 -380. |
[16] | C. Sanjeevamurthy, Guntirangasrinivas “Effect of Alkali Treatment, Fiber Loading and Hybridization on the Tensile Properties of Sisal Fiber, Banana Empty Fruit Bunch Fiber and Bamboo Fiber Reinforced Thermoset Composites” International Journal Of Engineering Science & Advanced Technology, Vol 2(3); 2012: 707 -711. |
[17] | S.Mishra, A.K Mohanty, L.T Drzal, M. Misra, S. Parija, S.K Nayak, S.S Tripathy “Studies on the Mechanical Performance of Biofiber/Glass Reinforced Polyester Hybrid Composites” Composite Science and Technology 63(2003) 1377-1385. |
[18] | S. Jayabal, S. Sathiyamurthy, K. T Loganathan & S. Kalyanasundaram “Effect of Soaking Time And Concentration of Naoh Solution on Mechanical Properties of Coir – Polyester Composites” Bull. Mater. Sc. Vol 35 (4); 567 – 574. 2012. |
[19] | Guillermo Cantero, Aitorarbelaiz, Rodrigo Llano-Ponte, Inaki Mondragon “Effects Of Fibre Treatment on Wettability and Mechanical Behavior of Flax/Polypropylene Composites” Composites Science and Technology 63 (2003) 1247–1254. |
[20] | N. Srinivasababu, K. Muralimohanraoandj. Suresh Kumar // International Journal Ofengineering (IJE) 3 (2009) 403. |
[21] | J. P. Siregar, S. M. Sapuan , M. Z. A. Rahman And H. M. D. K. Zaman “The Effect of Alkali Treatment on the Mechanical Properties of Short Pineapple Leaf Fibre (PALF) Reinforced High Impact Polystyrene (HIPS) Composites” Journal Of Food, Agriculture & Environment Vol.8 (2): 1103 - 1108 . 2 0 1 0. |
[22] | Mohanty, A.K., Mubarak, A.K. And Hinrichsen, G. 2000. Surface Modification of Jute and Its Influence on Performance of Biodegradable Jute-Fabric/Biopolcomposites. Composites Science And Technology 60:1115-1124. |
[23] | N. Venkateshwaran, A. Elayaperumal And D. Arunsundaranayagam. Fiber Surface Treatment and Its Effect on Mechanical and Visco-Elastic Behaviour of Banana/Epoxy Composite”, Materials and Design 47,(2013), Pp. 151-159. |
[24] | G.M Arifuzzaman Khan, M Abdullah-Al-Mamun1, S. M Ashrafulabedin, M Jonayedchoudhury, M A Gafur and M Shamsulalam.”Renewable Okra Bast Fiber Reinforced Phenol Formaldehyde Resin Composites: Mechanical And Thermal Studies.” Research and Reviews: Journal of Material Sciences Volume 2 Issue 1 January - March, 2014. |
[25] | Mansour Rokbi, Hocineosmani, Abdellatifimad, Noureddinebenseddiq “Effect Of Chemical Treatment on Flexure Properties of Natural Fiber-Reinforced Polyester Composite” Procedia Engineering 10 (2011) 2092–2097. |