Nur Farhana M. Yunos1, Magdalena Zaharia2, Anis Nadhirah Ismail1, Muhammad Asri Idris1
1University Malaysia Perlis, School of Materials Engineering, Arau, Malaysia
2One Steel, Rooty Hill, Sydney, Australia
Correspondence to: Nur Farhana M. Yunos, University Malaysia Perlis, School of Materials Engineering, Arau, Malaysia.
Email: |  |
Copyright © 2014 Scientific & Academic Publishing. All Rights Reserved.
Abstract
Agricultural wastes and rubber tires have the potential to be used in industries seeking alternative fuel and sustainable raw materials sources. Previous studies focused on recycling these materials as fuel resources, i.e. rubber in cement industry and agricultural materials for power production. The present paper focuses on investigations of carbon/slag reactions, namely slag foaming and FeO reduction by using rubber and palm shell wastes as sustainable carbon sources through quantitative estimation of the slag volume. An improved volume ratio for the rubber blend and palm shells char compared to coke was seen. It was found that rubber showed a higher rate of FeO reduction than that of coke. However, the present study indicated an opposite trend for palm shell char, where the rate of FeO reduction was found to be lower due to low fixed carbon compared to rubber blend. These results indicate that partial replacement of coke with rubber and palm shell is efficient due to improved interactions with EAF slag.
Keywords:
Palm Shells Char, Rubber Tires, Carbon/slag Reactions, FeO Reduction, EAF Steelmaking
Cite this paper: Nur Farhana M. Yunos, Magdalena Zaharia, Anis Nadhirah Ismail, Muhammad Asri Idris, Transforming Waste Materials as Resources for EAF Steelmaking, International Journal of Materials Engineering , Vol. 4 No. 5, 2014, pp. 167-170. doi: 10.5923/j.ijme.20140405.01.
1. Introduction
Iron and steel making are two of the largest energy intensive industries with the highest growth rate in energy consumption of all energy utilization sectors. In order to meet the growing greenhouse challenges, incorporation of renewable energy sources to the existing and emerging metallurgical operations is desirable. In this respect, agricultural waste from palm shells and rubber tires can potentially be applied in EAF steelmaking as renewable materials. As the chemical components available in these waste materials are carbon and hydrogen, these clearly have the potential to be a cheap and readily available auxiliary source of carbon, to partially replace conventional carbon materials (coke/coal) in steelmaking.The use of plastics as a partial fuel substitute for coke or coal in coke ovens and in the blast furnace is being practiced in Japan [1]. Limited studies have reported the use of polymeric materials in EAF steelmaking and they showed improvements in combustion performances and better carbon/slag interactions with the addition of plastics and rubber [2]. Interactions between FeO containing slag with plastics/coke and rubber/coke blends as a carbon source at 1550 ºC using the sessile drop technique were respectively investigated by Sahajwalla and Magdalena et al. [3-6]. Dankwah et al. [7] measured the reduction of FeO in EAF steelmaking slags using blends of coke, high density polyethylene (HDPE) and rubber tires as reductant and found that the hydrogen and fixed carbon contents leading a faster reduction rates and carburisation.Alternative and renewable materials such as agricultural waste have drawn attention in the iron and steelmaking sector since they are carbon neutral. The use of wood char in ironmaking has been extensively reviewed by Gupta [8], Burgess [9] and Dell’Amico et al [10]. Charcoal has been used as a reducing agent in blast furnaces for a number of years [11], Babich et al. [12] found that the combustion efficiency of all the tested charcoals is better or comparable to conventional coals. However, most of the previous studies considered agricultural materials as reducing agent in the blast furnace, while fewer investigations were considered for applications in steelmaking. Thus, agricultural waste materials derived from palm shells are among the main renewable waste source in Malaysia [13]. The palm shell charcoal was seen to possess other advantageous characteristics; e.g. low sulphur and nitrogen con-tent, resulting in low SOx/NOx emission; the alkaline ash present in the palm shell waste is known to capture some of the SO2 produced during combustion. Besides that, the palm shell waste is a true renewable fuel, so it does not contribute to the increase in the global CO2 concentration.The current paper focus on recycling of wastes derived from polymer and agricultural practices as inject carbon resources in EAF steelmaking industry. It involves a quantitative estimation of the changes occurring in slag volume as a function of time and reduction behavior of FeO slag from the gas formations.
2. Results and Discussion
2.1. Materials Characteristics
Metallurgical coke is widely used by steelmakers as the primary carbon resource in EAF steelmaking. The properties of coke, such as fixed carbon content, ash level and composition play an important role in its interactions with molten slag. Rubber is a polymeric material with inherent high volatile content as well as medium amount of carbon (Table 1). Palm shell is a renewable material with high amount of volatiles, low amount of ash which consists mainly of iron oxide and low amounts of sulphur and phosphorus (Table 2). The oxygen in palm shell is available due to its cellulose and hemicellulose content. The presence of oxygen in palm shells may influence CO formation at high temperatures [14].Table 1. Proximate and ultimate analyses of metallurgical coke and palm shell char samples 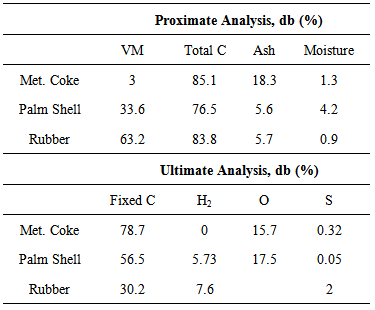 |
| |
|
Table 2. Ash Analysis of the carbonaceous materials used in this study (wt %) 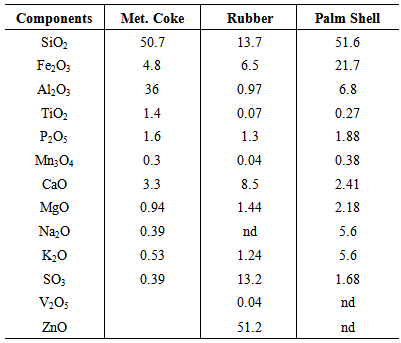 |
| |
|
Rubber was blended with coke in various proportions. MC was chosen as the base material because it is the typical carbon injectant used at OneSteel EAF, Sydney Steel Mill, Australia. Rubber was cryogenically ground to reach a particle size similar to that of coke. Palm shells were collected from Malaysia and volatile matter was removed by heating it in oxygen free atmosphere. The rubber blends were further crushed in a jaw crusher and a vibrating grinder to increase the uniformity in particle size distribution. The carbonaceous substrates were prepared by grinding and sieving the carbon based materials to particle sizes < 60 μm, and further compacting them at ~ 4.0 MPa in a steel die using a hydraulic press. The substrate had a diameter of 20 mm and a thickness of 3 – 4 mm.The slag used was provided by Onesteel and its composition is detailed in Table 3 below. The substrate was placed on an alumina holder of the sessile-drop experimental assembly, and the carbon/slag reactions were recorded by a charge coupled device (CCD) equipped with a video camera [4].Table 3. Onesteel slag composition 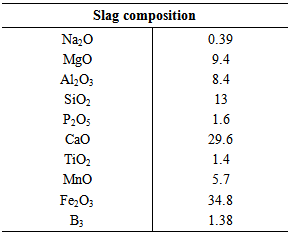 |
| |
|
2.2. Waste Materials (Carbon)/ Slag Interactions
To qualitatively demonstrate the behavior of the slag volume at steelmaking temperatures, a few representative dynamic wetting images of the slag droplet in contact with metallurgical coke and its blends with rubber and palm shell char are shown in Figure 1. When rubber replaced part of the coke an in-creased slag volume was seen with reaction time. Moreover, with increased reaction time, the volume of the slag in contact with rubber/coke blend was improved as opposed to coke alone. The renewable palm shell showed an increased slag volume compared to coke. 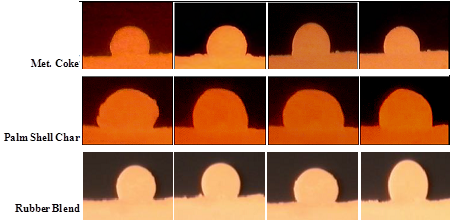 | Figure 1. Snap shots of slag droplets in contact with 100% MC, Rubber Blend, and Palm char at 1550°C as a function of time |
The changes in slag volumes, attributed to formation, entrapment and release of gases, Vt/V0 was calculated and plotted as a function of time. The volume ratio, Vt/V0, of the EAF slag reacting with metallurgical coke records an initial value of 1.0; with time it decreased without any wide fluctuations to 0.5. This indicates a lower extent of gas entrapment by the slag. For the rubber blend, the slag volume ratios showed significantly different trends with much higher levels of droplet volumes in the first 150 seconds of reaction (Figure 2 (a)). The palm char showed fluctuations, with the drop continuously growing and dropping, however maintaining an increased volume. This indicates that the decrease in slag volume took much longer when Rubber and palm shells replaced the metallurgical coke usage suggesting significant levels of gas entrapped and subsequently released during carbon/slag interactions.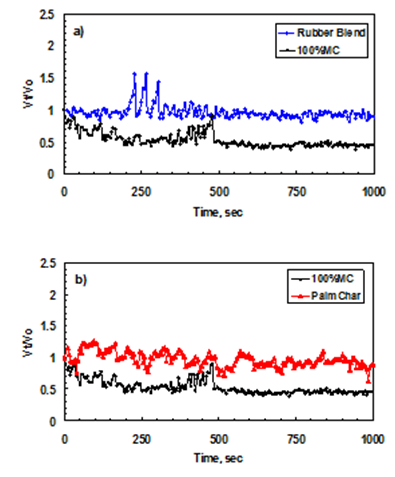 | Figure 2. Vt/V0 plot for coke only and two different rubber/coke ratio blends [15] |
As carbon is continuously injected into the slag bath of the electric arc furnace where the temperature exceeds 1500 ºC, the initial gas phase reactions occur very fast and the gases evolved at these high temperature are expected to participate in the subsequent slag reactions.
2.3. FeO Reduction
The rate of reduction is equivalent to the rate of CO and CO2 gases produced from the system. Iron oxide is the main oxide getting reduced as a result of the interaction of slag with various carbonaceous materials under investigations. For metallurgical coke, a value of 2.16 x 10-5 moles/cm2 s was calculated as the maximum rate, while a lower value of 0.937 x 10-5 moles/cm2 s for palm char. On the other hand, rubber blends was measured approximately 2.5 x 10-5 moles/cm2 s (Table 4).Table 4. Reaction rate constant (moles/cm2 s) for metallurgical coke, palm char and rubber blends 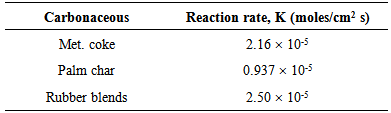 |
| |
|
The blends appeared to have contributed to more gas evolved, which was subsequently entrapped into the slag phase. Previous publications detail on the rates of gas generation when rubber replaced part of the coke [16]. At temperature above 900°C hydrogen was seen to be present which was attributed to the interaction of cellulose and lignin during pyrolysis. Palm shells contain high lignin (53.4 %) and cellulose (29.7 %) and their interaction at high temperature is known to release a considerable amount of gases [17]. Moreover, the inorganic matter could also influence the formation of gas at temperature 800°C. Conversely, a relatively slower rate of gas generation in the case of palm char could cause the gas bubbles to be trapped in the slag sample instead of rapidly escaping from the slag.When rubber was used, it was found by Dankwah et al. [7] that the gases evolved were mostly CO, CO2 with considerable amount of CH4 and H2. Thus, the rubbers/palm shell kinetic advantage might come from its richer hydrogen content, in comparison to metallurgical coke, because the reduction reaction (FeO + H2(g) = Fe + H2O(g)) is much faster than the reduction of FeO with C. This study has shown that blends of rubber with metallurgical coke and palm char could be used to partially replace some of the conventional metallurgical coke used in EAF steelmaking for its injecting carbon requirements.
2.4. Acknowledgments and Legal Responsibility
Financial support was provided by FRGS Grant from Ministry of Education, Malaysia.
References
[1] | Minoru Asanuma, T.A., Development of Waste Plastics Injection Process in Blast Furnace. ISIJ International, 2000. 40(3): pp. 244-251. |
[2] | Sahajwalla, Influence of carbonaceous materials on slag foaming behavior during EAF steelmaking. Iron & steel technology 2006. 3(2): pp. 54 -63 |
[3] | Sahajwalla, V., Recycling Waste Plastics in EAF Steelmaking: Carbon/Slag Interactions of HDPE-Coke Blends. Steel Research Int., 2009. 80(8): pp. 535-543. |
[4] | Sahajwalla, V., et al., Recycling Plastics as a Resource for Electric Arc Furnace (EAF) Steelmaking: Combustion and Structural Transformations of Metallurgical Coke and Plastic Blends. Energy & Fuels, 2009: pp. 379–391. |
[5] | Sahajwalla, Environmentally Sustainable EAF Steelmaking Through Introduction of Recycled Plastics and Tires: Laboratory and Plant Studies. AISTech - Iron and Steel Technology Conference Proceedings, 2009. |
[6] | Zaharia, M., et al., Recycling of Rubber Tires in Electric Arc Furnace Steelmaking: Simultaneous Combustion of Metallurgical Coke and Rubber Tyres Blends. Energy & Fuels, 2009. 23(5): pp. 2467–2474. |
[7] | Dankwah, J.R., et al., Reduction of FeO in EAF Steelmaking Slag by Metallurgical Coke and Waste Plastics Blends. ISIJ International, 2011. 51(3): pp. 498-507. |
[8] | Gupta, S., et al., Minerals and iron-making reactions in blast furnaces. Progress in Energy and Combustion Science, 2008. 34(2): pp. 155-197. |
[9] | Burgess, J. Biomass and Renewables as Alternative Energy Sources and Reductants in the Minerals Industry. in Green Processing Conference, AusIMM. 2004. Melbourne. |
[10] | M. Dell’Amico, R.L. P. Fung, and J.M.a.M. O’Connor. Green Iron Ore Sintering. in Green Processing Conference, AusIMM. 2004. Melbourne. |
[11] | Macedo, C., E.A.O. d'Avila, and J.G. Brosnan. Start Up and Operation of a Closed Calcium Carbide Furnace Using Charcoal as the Reducing Agent in Electric Furnace Proceedings. 1985. Atlanta, USA. |
[12] | Babich, A., D. Senk, and M. Fernandez, Charcoal Behaviour by Its Injection into the Modern Blast Furnace. ISIJ International, 2010. 50(1): pp. 81-88. |
[13] | Basiron, Y., The Oil Palm & Its Sustainability. Journal of Oil Palm Research, 2004. 16(1): pp. 1-10. |
[14] | Mohan, D., Pittman, Charles U., and P.H. Steele, Pyrolysis of Wood/Biomass for Bio-oil: A Critical Review. Energy & Fuels, 2006. 20(3): pp. 848-889. |
[15] | Sahajwalla, V., et al., The power of steelmaking-harnessing high-temperature reactions to transform waste into raw material resources. Iron and Steel Technology, 2013. 10(8): pp. 68-83. |
[16] | Zaharia, M., Carbon/Slag Interactions between Coke/Rubber Blends and EAF Slag at 1550 C. ISIJ International, 2009. 49(10): pp. 1513-1521. |
[17] | Yunos, N.F.M., et al., Recycling Agricultural Waste from Palm Shells during Electric Arc Furnace Steelmaking. Energy & Fuels, 2011. |