Suresh Sagadevan1, Shanmuga Sundaram Anandan2
1Department of Physics, Sree Sastha Institute of Engineering and Technology, Chennai, 600 123, India
2Department Mechanical Engineering, Sree Sastha Institute of Engineering and Technology, Chennai, 600 123, India
Correspondence to: Suresh Sagadevan, Department of Physics, Sree Sastha Institute of Engineering and Technology, Chennai, 600 123, India.
Email: |  |
Copyright © 2014 Scientific & Academic Publishing. All Rights Reserved.
Abstract
Anilinium D-Tartrate (ADT) was subjected to study the mechanical behaviour of crystal. The microhardness study reveals the mechanical strength of the grown crystal. The Vicker’s and Knoop hardness studies were performed to understand the mechanical behavior of the Anilinium D-Tartrate crystals. The Vicker’s and Knoop microhardness numbers (HV and HK) for the crystal were found for different loads. It is found that these numbers increase with an increase in the load. The Mayer’s index (n) was found to be greater than 1.6 predicting a soft-material category. The fracture toughness value (Kc), was determined from the measurements of the crack length. The brittleness indices (Bi) were found for the grown crystals. Using Wooster’s empirical relation, the elastic stiffness constant (C11) was calculated from the Vicker’s hardness values at different loads. The Young’s modulus was also calculated from Knoop microhardness values.
Keywords:
Microhardness number, Mayer’s index, Fracture toughness, Brittleness indices, Elastic stiffness coefficient, Young’s modulus
Cite this paper: Suresh Sagadevan, Shanmuga Sundaram Anandan, A Study of Mechanical Behaviour of Anilinium D-Tartrate Single Crystal, International Journal of Materials Engineering , Vol. 4 No. 2, 2014, pp. 70-74. doi: 10.5923/j.ijme.20140402.04.
1. Introduction
The structure and composition of the crystalline solids are inviolably related to the mechanical hardness. Microhardness testing is one of the best methods of understanding the mechanical properties of materials such as fracture behavior, yield strength, brittleness index, and temperature of cracking (Lawn et al 1971; Westbrook et al 1958). Superhard materials have attracted great attention because of their important industrial applications. In order to explore new superhard materials, the nature of hardness was extensively investigated, with numerous models proposed to predict the hardness of materials.Hardness is an important factor in the choice of ceramics for abrasives, bearings, tool bits, wear resistance coatings etc. Hardness is a measure of resistance against lattice destruction or the resistance offered to permanent deformation or damage. Measurement of hardness is a destructive testing method to determine the mechanical behaviour of the materials. As pointed out by (Shaw et al 1973), the term hardness is having different meanings to different people depending upon their areas of interest. For example, it is the resistance to penetration to a metallurgist, the resistance to cutting to a machinist, the resistance to wear and tear to a lubrication engineer and a measure of flow of stress to a design engineer. All these actions are related to the plastic stress of the material. For hard and brittle materials, the hardness test has proved to be a valuable technique in the general study of plastic deformation (Westbrook et al 1971). The hardness depends not only on the properties of the materials under test but also largely on the conditions of measurement. Microhardness tests have been applied to fine components of clock and instrument mechanisms, thin metal strip, foils, wires, metallic fibers, thin galvanic coatings, artificial oxide films, etc., as well as the thin surface layers of metals which change their properties as a result of mechanical treatments such as machining, rolling, friction and other effects. The microhardness method is widely used for studying the individual structural constituent elements of metallic alloys, minerals, glasses, enamels and artificial abrasives. The mechanical strength of a material plays a key role in device fabrication. It is a measure of the resistance the lattice offers to local deformation (Mott et al 1956). Hardness is one of the important mechanical properties of the materials (Xingtao Keyan Li et al 2008; Ke Yan Li et al 2009; Ke Yan Li et al 2010). It can be used as a suitable measure of the plastic properties and strength of a material (Desai et al 1983). Stillwel (Stillwel et 1938) defined hardness as resistance against lattice destruction, whereas Ashby (Ashby et al 1951) defined it as the ability of a crystal to resist a structural breakdown under applied stress. This resistance is an intrinsic property of the crystal. The hardness properties are related to the crystal structure of the material and microhardness tests have been carried out to understand the plasticity of the crystals. Also, the hardness of the crystal is dependent on the type of chemical bonding, which may differ along the crystallographic directions. Hardness is generally taken as a ratio of the applied load to the area of indentation. The measurement of hardness is very important, as far as the fabrication of devices is concerned. Organic crystals were intensively investigated due to their high nonlinearities, high mechanical properties, rapid response in electro-optic effect and tailor made flexibility.In the present work the mechanical behaviour of Anilinium D-Tartrate was studied using Vickers microhardness tester. Vickers hardness number Hv, Mayer's index number ‘n’, crack length, elastic stiffness constant, yield strength, fracture toughness and Brittle index were calculated. Hardness measurement is very important for device fabrications. The Young's modulus was calculated from the Knoop hardness test. The results are discussed in detail.
2. Materials and Methods
Anilinium D-Tartrate single crystals were synthesized by dissolving Aniline and D-Tartaric acid were taken in the molar ratio of 1:1 in distilled water. The solution was stirred continuously using a magnetic stirrer. The prepared solution was filtered and kept undisturbed at room temperature. The beaker was closed with a porously sealed cover and the solution in the beaker was allowed to evaporate. A few days later, tiny crystals were seen in the beaker. Among them, a defect free seed crystal was suspended in the mother solution, which was allowed to evaporate at room temperature. Large size single crystals were obtained due to collection of monomers at the seed crystal sites from the mother solution. The mechanical characterization of Anilinium D-Tartrate crystals were made by Vickers microhardness and Knoop microhardness test. The grown crystal with flat and smooth faces and free from any defects was chosen for the static indentation tests. The surface was polished gently with methanol and mounted properly on the base of the microscope. Now the selected face was indented gently by varying the loads for a dwell period of 10 s using Vickers and Knoop indenter attached to an incident ray research microscope (Mututoyo MH112, Japan). From the single crystal X-ray diffraction analysis, it was observed that the Anilinium D-Tartrate crystal belongs to triclinic crystal system having non-centrosymmetry with P1 space group with lattice parameter: a = 6.132 Å, b = 7.425 Å, c = 12.873 Å, α = 84.20°, β = 75.34°, γ = 70.34° and the volume of the unit cell is found to be 543.25Å3.
2.1. Vicker’s Hardness Test
Mechanical strength of the materials plays a key role in the device fabrication. Vickers hardness is one of the important deciding factors in selecting the processing (cutting, grinding and polishing) steps of bulk crystal in fabrication of devices based on crystals. Microhardness measurements were done Anilinium D-Tartrate crystal using Leitz-Wetzlar hardness tester fitted with a Vickers diamond indenter at room temperature.Vicker’s hardness test is said to be a more reliable method of hardness measurement. In order to get a similar geometrical impression under varying loads, Smith et al 1923 have suggested that a pyramid be substituted for a ball. The Vickers hardness test method consists of indenting the test material with a diamond indenter, in the form of a right pyramid with a square base and an angle of 136° between opposite faces and subjected to a load of 1 to 100 kg (Fig .1). The base of the Vickers pyramid is a square and the depth of indentation corresponds to 1/7th of the indentation diagonal. The longitudinal and transverse diagonals will be in the ratio of 7:1. The full load was normally applied for 10 to 15 seconds. The two diagonals of the indentation left in the surface of the material after the removal of the load were measured using a microscope, and their average was calculated. The area of the sloping surface of the indentation was calculated. 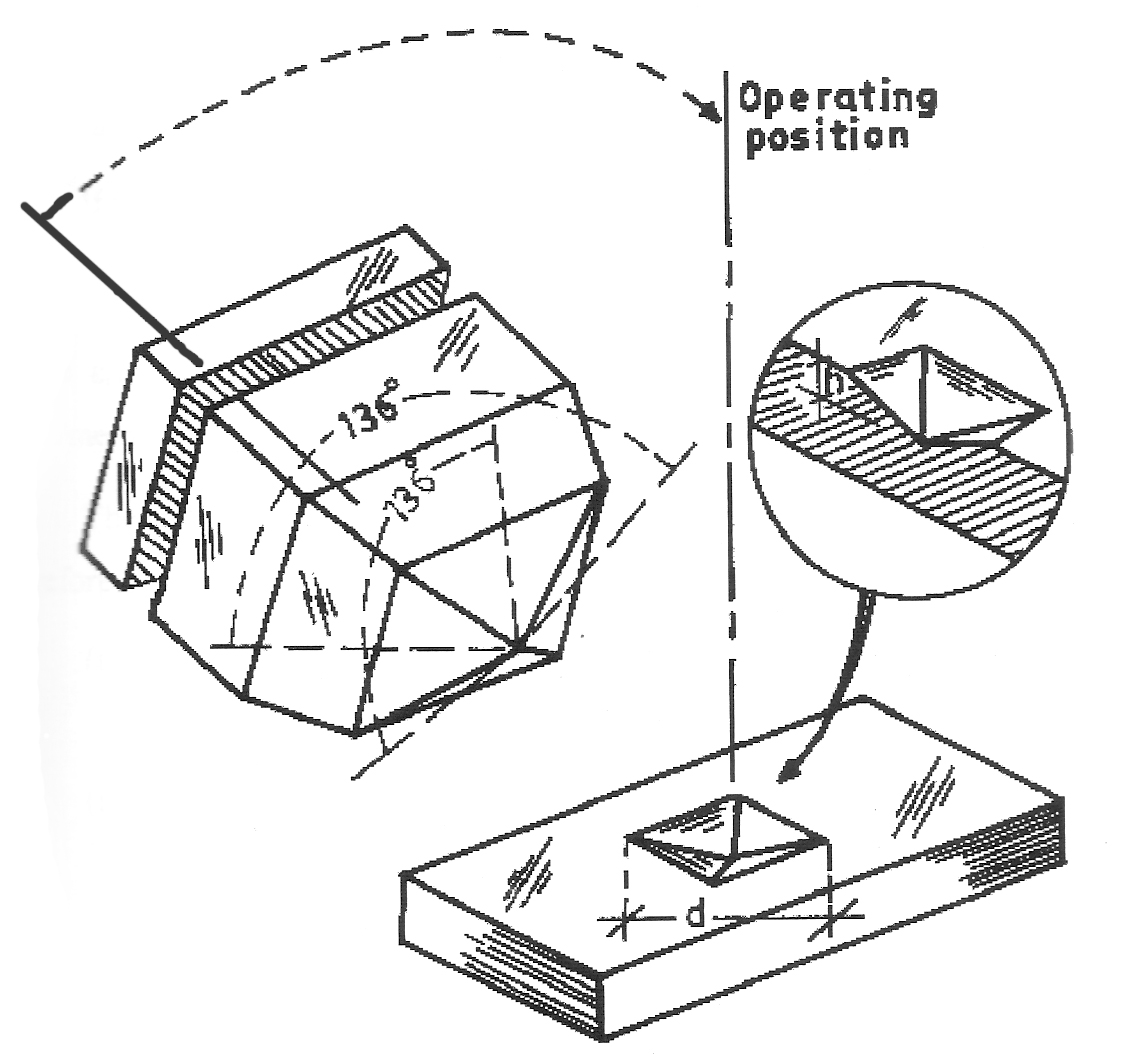 | Figure 1. Vickers hardness test |
The Vicker’s hardness is the quotient obtained by dividing the kg load by the square mm area of indentation.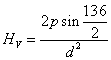
where HV = Vickers hardness number
P = load in kg
d = arithmetic mean of the two diagonals When the mean diagonal of the indentation has been determined, the Vicker’s hardness number can be calculated from the above formula. Several different loading settings give practically identical hardness numbers on uniform material, which is much better than the arbitrary changing of scale with the other hardness testing methods. The advantages of the Vicker’s hardness test are that extremely accurate readings can be taken, and just one type of indenter is used for all types of metals and surface treatments. Hardness values are always measured from the observed size of the impression remaining after a loaded indenter has penetrated and has been removed from the surface. Thus, the observed hardness behaviour is the summation of a number of effects involved in the materials response to the indentation pressure during loading, in the final measurement of the residual impression. The importance of microhardness study lies in the possibilities of making an indirect estimate of mechanical characteristics of materials such as yield strength and toughness having a specific correlation with the hardness.
2.2. Knoop Hardness Test
Knoop hardness can be treated as an alternative to the Vickers test, particularly for very thin layers, Fredrick Knoop developed a low-load test with a rhombohedral- shaped diamond indenter. The long diagonal is seven times (7.114 actually) as long as the short diagonal. With this indenter shape, elastic recovery can be held to a minimum. Knoop tests are mainly done at test forces of 10 g to 1000 g (Fig.2); so, a high powered microscope is necessary to measure the indent size. Because of this, Knoop tests have mainly been known as microhardness tests. The magnifications required to measure Knoop indents dictate a highly polished test surface. To achieve this surface, the samples are normally mounted and metallurgically polished; therefore Knoop is almost always a destructive test.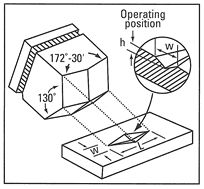 | Figure 2. Knoop hardness test |
The mechanical characterization of the Anilinium D-Tartrate crystals was analyzed by the Vicker’s and Knoop microhardness tests. Crystals with flat and smooth faces were chosen for the static indentation tests and the same crystal was mounted on the base of the microscope. The indentations were made gently by varying the loads from 10 to 100 g for a dwell period of 10 s using both the Vicker’s diamond pyramid indenter and the Knoop indenter attached to an incident ray research microscope (Mitutoyo MH112, Japan). The intended impression of Vicker’s was approximately square in shape. The shape of the impression is dependent on the structure, face and materials used. After unloading, the length of the two diagonals was measured by a calibrated micrometer attached to the eyepiece of the microscope. For each load, at least five well-defined indentations were considered and the average was taken as d. The Vicker’s hardness was calculated using the standard formula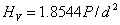 | (1) |
where P is the applied load in Kg, d in µm and HV in Kg/mm2. The Knoop indented impressions were approximately rhombohedral in shape. The average diagonal length (d) was considered for the calculation of the Knoop hardness number (HK) using the relation | (2) |
where P is the applied load in Kg, d in µm and HK is in kg/mm2. Beyond 100 g of the applied load, crack initiation and fragmentation were observed. So the hardness test could not be extended beyond this load. The elastic stiffness constant (C11) was calculated using Wooster’s empirical relation as (Wooster et al 1953) | (3) |
3. Results and Discussion
3.1. Vicker’s Microhardness Test
Fig. 3 shows the variation of HV as a function of applied loads, ranging from 25 to 100 g. It is clear from the Fig.3 shows that HV increases with an increase in the load. It reveals that hardness number increases with increasing applied load. This phenomenon is known as reverse indentation size effect (RISE). When the material is deformed by the indenter, dislocations are generated near the indentation site. The major contribution to the increase in hardness is attributed to the high stress required for homogenous nucleation of dislocations in the small dislocation-free region indented (Kunjomana et al 2005). The RISE can be caused by the relative predominance of nucleation and multiplication of dislocations. The other reason for RISE is that the relative predominance of the activity of either two sets of slips planes of a particular slip system or two slip systems below and above a particular load (Sangwal et al 2000) [39]. The RISE phenomenon essentially takes place in crystals which readily undergo plastic deformation (Li et al 1994).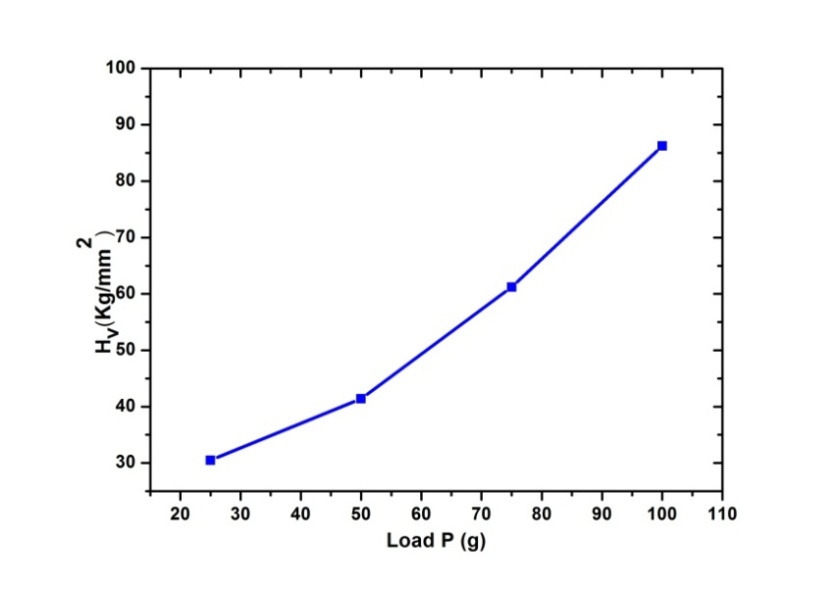 | Figure 3. Variation of the microhardness number HV with load |
The Mayer’s index number was calculated from the Mayer’s law, which relates the load and indentation diagonal length. | (4) |
 | (5) |
where k is the material constant and n is the Mayer’s index (or work-hardening coefficient). The above relation indicates that HV should increase with the increase in P if n > 2 and decrease with P when n < 2. The ‘n’ value was determined from the plot of log P vs log d, as shown in Fig. 4. The slope of the plot of log P versus log d will give the work hardening index (n) which is found to be 3.25. The material Anilinium D-Tartrate is confirmed with large amount of mechanical strength which is better for device fabrications. According to Hanneman (Hanneman et al 1941) the value of ‘n’ is less than 2 for hard materials and more than 2 for soft ones. Thus, Anilinium D-Tartrate crystals belong to the soft-material category. Since, Anilinium D-Tartrate is having moderately higher value of hardness number, the material is found to be suitable for device fabrications. 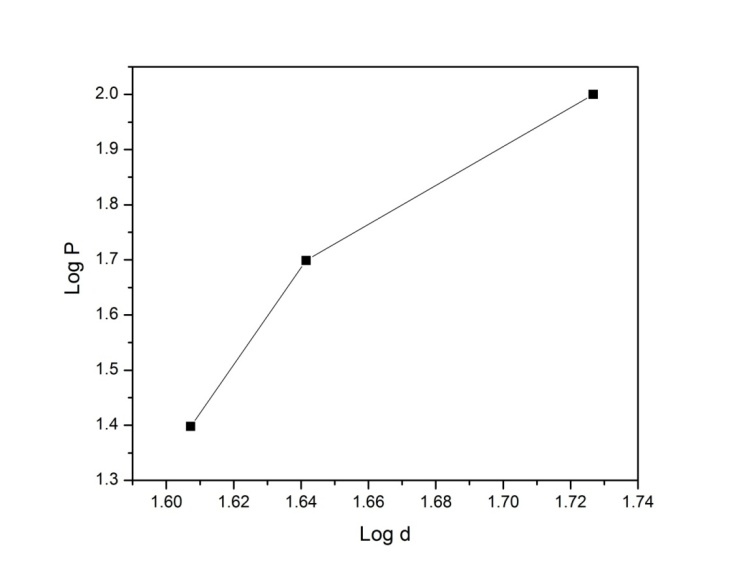 | Figure 4. log P vs. log d |
The elastic stiffness constant (C11) was calculated by Wooster’s empirical relation. The calculated stiffness constant for different loads was tabulated (Table 1). The crack length is measured from the centre of indentation mark to the crack end. Here, the crack length (l) is the average of two crack lengths for each indentation. Resistance to fracture indicates the toughness of material (Jain et al 1994). The fracture mechanics of the indentation process gives an equilibrium relation for a well-developed crack extending under the centre loading condition;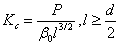 | (6) |
where β0 is the indenter constant, equal to 7 for the Vicker’s diamond pyramid indenter (Lawn et al 1979) and other symbols have their usual meanings. For the Anilinium D-Tartrate, the value of Kc is found to be 2.32 × 104 Kg m-3/2, 3.10 × 104 Kg m-3/2 and 12.10 × 104 Kg m-3/2 and 20.55× 104 Kg m-3/2 at 25, 50 and 100 g respectively.Table 1. Elastic stiffness constant of Anilinium D-Tartrate |
| Load P (g) | HV (Kg/mm2) | C11 x 1014 Pa | 25 | 30.50 | 3.95 | 50 | 41.40 | 6.75 | 75 | 61.20 | 13.39 | 100 | 86.25 | 24.41 |
|
|
Brittleness is another property, which affects the mechanical behaviour of a material, and is expressed in terms of the brittleness index (Bi) as. | (7) |
The calculated values of Bi are found as 12.05 x 104 m-1/2 , 12.60 104 m-1/2, 4.10 x 104 m-1/2 and 3.12 x 104 m-1/2 at 25 g, 50 , 75 and 100 g respectively.
3.2. Knoop Microhardness Test
Knoop hardness (HK) was plotted against loads (P). The plot is shown in Fig.5. From this measurement, it is found that as the load increases the Knoop microhardness number also increases. From the Knoop microhardness measurements, the Young’s modulus (E) of the crystal was calculated using the relation (Pal et al 2005). | (8) |
where HK is the Knoop microhardness value at a particular load, and ‘b’ and ‘a’ are the shorter and longer Knoop indentation diagonals respectively. The calculated Young's Modulus is 1.47 ×1010 Nm−2. 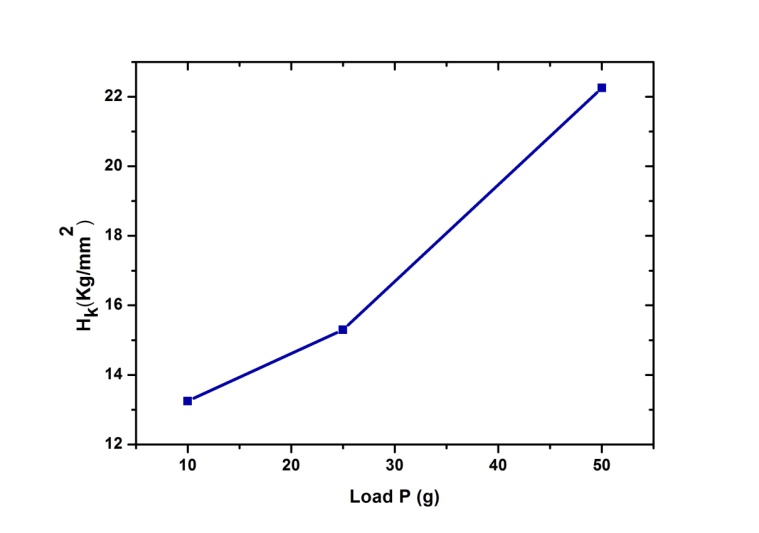 | Figure 5. Variation of the Knoop microhardness with load |
4. Conclusions
The Vicker’s and Knoop microhardness studies were carried out on the grown Anilinium D-Tartrate single crystal. The Vickers and Knoop hardness numbers were calculated for the Anilinium D-Tartrate single crystal, by the application of load and the hardness numbers were found to increase with an increase in the load. The value of the Mayer’s index number is found as 3.25, which proves that Anilinium D-Tartrate falls in the soft-material category. The calculation of the stiffness constant (C11) reveals that the binding force between the ions is quite strong. The Young's modulus was calculated from the diagonal lengths of the Knoop indentation.
ACKNOWLEDGEMENTS
The authors thank the Management of Sree Sastha Institute of Engineering and Technology, Chembarambakkam, Chennai-600123 for their encouragements and constant support throughout this work.
References
[1] | Lawn B R, Marshall D B, (1979), Hardness, Toughness and Brittleness, an Indentation Analysis, J. Am. Ceram. Soc, 62, 347. |
[2] | J. H. Westbrook, Report 58-RL-2033 of the G. E. Research Laboratory, USA, 1958. |
[3] | Shaw M.C. (1973), The Science of Hardness Testing and its Research Application, Ed. By Westbrook J.H. and Condrad. H, ASM. Ohio, pp. 1-11. |
[4] | Westbrook J.H and Conrad H. (1971), The Science of Hardness testing and its Research Applications, American Society for Metals, Ohio. |
[5] | Mott B.W., (1958), Hardness of Butter, Influence of Season and Manufacturing Method Micro indentation hardness testing, J.Dairy Science., Vol. 41, pp. 360-368. |
[6] | Xingtao Keyan Li, Fangfang Wang, Zhang, Dongfeng Xue, (2008), Electronegativity identification of novel superhard materials, Physical Review Letters, 100,235504. |
[7] | Ke Yan Li, Dong Feng Xue, (2009), Hardness of materials: studies at levels from atoms to crystals Chinese Science Bulletin, 54,131-136. |
[8] | Ke Yan Li, Dong Feng Xue, (2010), Hardness of group IVA and IVB nitrides, Physica Scripta, T139, 014073. |
[9] | Desai C C, Rai J L, (1983), Microhardness studies of SnI2 and SnI4 single crystals, Bulletin of Materials Science, 5, 453. |
[10] | Stillwel C W, (1938), Crystal Chemistry, McGraw Hill, New York. |
[11] | Ashyby N A, (1951), Journal of Nuclear Engineering, 6, 33. |
[12] | Smith, R.L., and Sandland, G.E., (1923), “An Accurate Method of Determining the Hardness of Metals with Reference to those of a High Degree of Hardness”, Proc. Inst. Mech. Engrs., 1, pp.623-641. |
[13] | Wooster W A, (1953) Physical properties and atomic arrangements in crystals, Reports on Progress in Physics, Rep. Prog. Phys, 16, 62. |
[14] | Kunjomana A G, Chandrasekharan K A (2005) Microhardness Studies of GaTe Whiskers. Cryst. Res. Technol. 40, 782-785. |
[15] | Sangwal K (2000) On the Reverse Indentation Size Effect and Microhardness Measurement of Solids. Mater. Chem. Phys. 63, 145-152. |
[16] | Li H, Han Y H, Bradt R C (1994) Knoop Microhardness of Single Crystal Sulphur. J. Mater. Sci. 29, 5641-5645. |
[17] | Hanneman M, (1941), Metall. Manchu, 23, 135. |
[18] | Jain A, Razdan A K, Kotru P N, Wanklyn B M, (1994), Load and directional effects on microhardness and estimation of toughness and brittleness for flux-grown LaBO3 crystals, J. Mater. Sci, 29, 3847. |
[19] | Lawn B R, Marshall D B, (1979), Hardness, Toughness and Brittleness, an Indentation Analysis, J. Am. Ceram. Soc, 62, 347. |
[20] | Pal T, Kar T, (2005), Studies of Microhardness anisotropy and Young’s modulus of nonlinear optical crystal L-arginine hydrochlorobromo monohydrate, Mater. Lett, 59,1400. |