Arthur B. L. Melo1, Túlio Hallak Panzera1, Márcio Eduardo Silveira1, Luciano Donizeti Varanda2, Decio Gonçalves3, André Luis Christoforo4, Francisco Antonio Rocco Lahr3
1Department of Mechanical Engineering, Federal University of São João del-Rei, São João del-Rei, 36307-352, Brazil
2Department of Science and Engineering Material, Engineering School of São Carlos (EESC/USP), São Carlos, 13566-590, Brazil
3Department of Structural Engineering, Engineering School of São Carlos (EESC/USP), São Carlos, 13566-590, Brazil
4Department of Civil Engineering, Federal University of São Carlos, São Carlos, 13565-905, Brazil
Correspondence to: André Luis Christoforo, Department of Civil Engineering, Federal University of São Carlos, São Carlos, 13565-905, Brazil.
Email: |  |
Copyright © 2012 Scientific & Academic Publishing. All Rights Reserved.
Abstract
This research objective evaluate the main mechanical properties of epoxy resin, used in composite matrices. The tests carried out (according to standards of ASTM - American Society for Testing and Materials) tensile, compression, bending, Charpy and ultra-micro hardness for determining the following properties: modulus of elasticity, tensile strength, compression and bending, toughness (strain energy) and hardness. Preliminary results showed that the modulus of elasticity in compression is significantly greater than in tension, reaching a difference of more than 100%.The values of module in bending were slightly lower than in compression. This difference of stiffness between tensile and compression of the matrix phase cannot be ignored during the development of the composite. Knowledge of this behavior and allow a better orientation distribution of fibers (or particles) during the development of the composite in order to achieve optimal performance of the final product.
Keywords:
Epoxy matrix, Mechanical behavior, Experimental analysis
Cite this paper: Arthur B. L. Melo, Túlio Hallak Panzera, Márcio Eduardo Silveira, Luciano Donizeti Varanda, Decio Gonçalves, André Luis Christoforo, Francisco Antonio Rocco Lahr, Evaluation of Mechanical Properties of a Polymer Matrix Thermosetting (Epoxi), International Journal of Materials Engineering , Vol. 4 No. 2, 2014, pp. 56-60. doi: 10.5923/j.ijme.20140402.02.
1. Introduction
After the 60s, when the composite had its first ascent, began continuous search for new, leading to continuous development of materials lighter and stronger as the number of features, functionalities and geometries [1].In the foreground, the business aviation industries ought this development because the composites assume greater importance in the project scope. Subsequently, the composite materials are now used also in the automotive industries, the possibility of replacement of parts made of steel, leading to the development of new materials and new and valuable scientific research [2].Among the commonly used matrices stages in the preparation of particulate composites and laminates, we highlight the epoxy resin [1, 12]. The use of epoxy resin characterized the search for discovery of new alliances between materials not previously envisioned [6-8], enabling the use of reinforcing phases in the form of slides and particles derived from organic and inorganic materials [9-11].However, epoxy resins exhibit negative traits as undesirable when an interface not worked properly, and the impossibility of recycling because they belong to the group of thermosetting. Nevertheless, this has been used on a large scale for structural applications [2].Thus, knowledge of elastic properties of epoxy resin through different forms of solicitation as well as the possible correlation between the two shows is very important [3].This work aims to evaluate and correlate the elastic modulus from the uniaxial tensile tests, uniaxial compression, bending and ultra-micro hardness bodies in the test piece made of epoxy resin, allowing a greater understanding of their mechanical behavior.
2. Material and Methods
The most widely used polymeric resins and cheaper are polyesters and vinyl esters [11]. Epoxies are more expensive and, in addition to commercial applications, are also widely used for aerospace applications; having improved mechanical properties and better resistance to moisture than polyester and vinyl resins.The epoxy resin used was RENLAM M BR 50 KGB1, AL10019400 batch number, together with HY956 hardener REN 25KG BR, B1 AL10014300 batch number, both manufactured by Huntsman Chemical Industry Brazil Ltda.Manufacture of Positive Role Models and negative MoldsThe models were machined in CNC ® (Figure 1), possessing he bodies of the test piece dimensions and shapes required in the regulatory documents used here [13-16], being fabricated and tested 10 samples of the test piece for each of the four tests carried out in mass fractions of 20% hardener and 80% resin.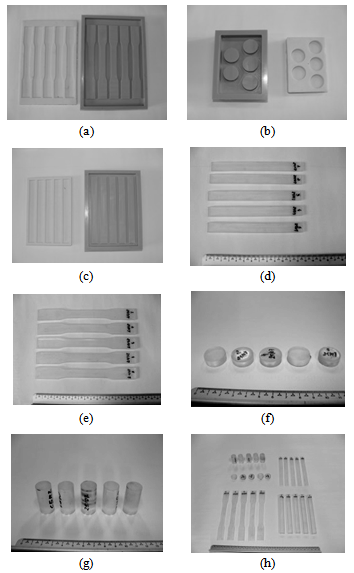 | Figure 1. Models in polymer and silicone molds |
The molds were prepared by using a thermosetting polymer and also with silicone. The sealant used was 940 WHITE, with ratios of 110, 503drops of catalyst per 100g of silica. These proportions were mixed and applied to the models with a cure time of approximately two hours.The molds of the bodies of the test piece for tensile tests, Ultra Micro-hardness tester (UMD) and flexion are presented in Figures 1a, 1b and 1c respectively. The bodies of the test piece for the bending, tensile, hardness and compression tests are illustrated in Figures 1d, 1e, 1f and 1g, both of which are shown in Figure 1h.TestsDensity and PorosityAfter preparation of the specimens, the same were also obtained from the densities and volumetric apparent and apparent porosity, average values respectively equal to 1.152 g/cm³, 1.168 g/cm³ and 1.601%, according to the normative document BSEN 10545 [17].Bending PropertiesThe modulus of elasticity in bending were obtained according to the assumptions for calculating the normative document American ASTM D790-07 [15], which calls the static bending to three points. Figure 2 illustrates the force x displacement curve for one specimen.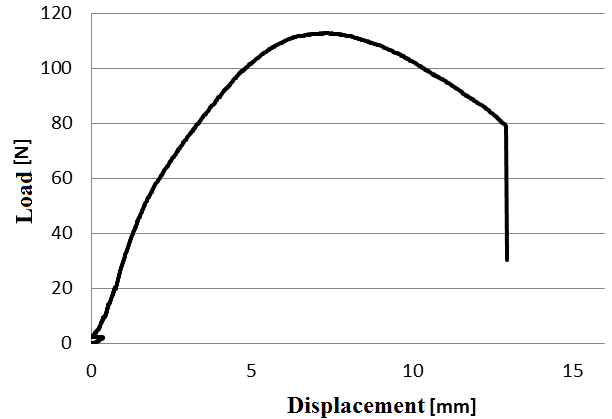 | Figure 2. Force × displacement curve obtained by bending test |
Compressive propertiesThe compression test followed the assumptions for calculating the American standard ASTM D695-02a [14]. Figure 3 illustrates the stress x strain curve for one specimen of the tests.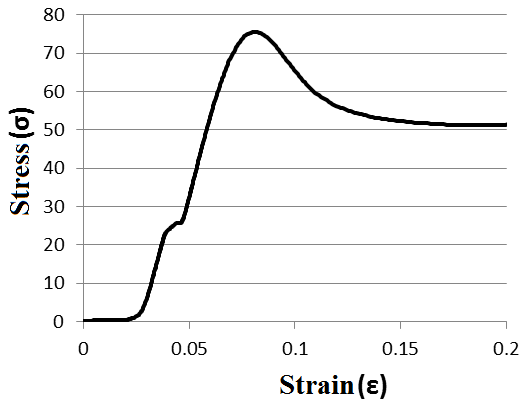 | Figure 3. Stress x strain curve obtained by compressive test |
Tensile PropertiesThe modulus of elasticity in tensile was obtained according to the assumptions of the American Standard ASTM D638-03 [13]. Figure 4 illustrates the stress x strain curve for one tensile test.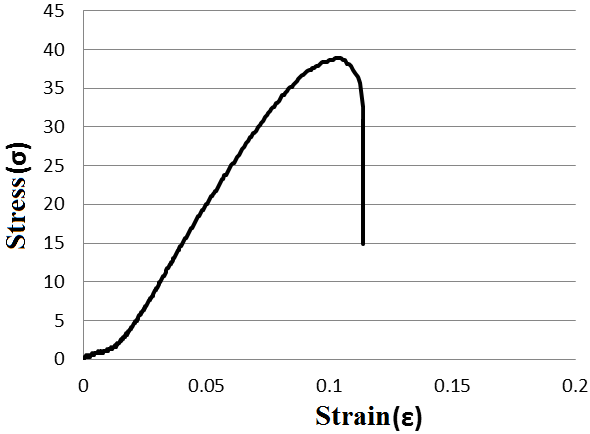 | Figure 4. Tension × deformation curve obtained by tensile test |
Ultra-Micro HardnessThe test may be described by a pressure applied on a polished surface with a penetrator tip. In the case used is evaluated Vickers indenter, tip-shaped diamond pyramid and an applied load of 500 mN, in order to quantify the hardness of the material according to the stated range and modulus of elasticity, with 13.79 HV. Figure 5 illustrates the force × deepness curve of a test bodies of the test piece tested.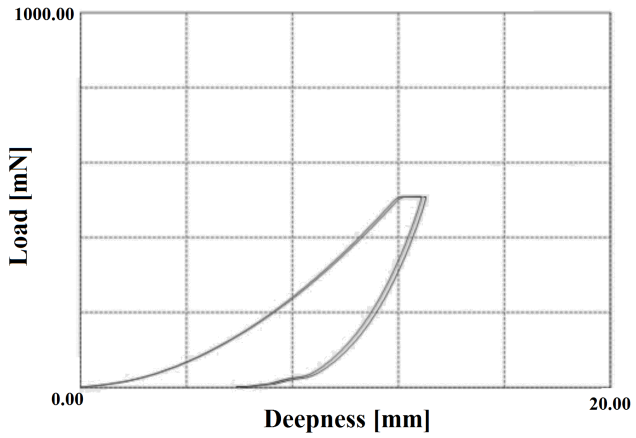 | Figure 5. Load × deepness of hardness test |
Confidence interval between means was used to verify the possible equivalences found between the values of the modulus of elasticity of the resin according to the different test models, as expressed by Equation 1. | (1) |
From equation 1, μ denotes the population mean of the differences, xm the arithmetic mean of the sample differences, n in sample size, Sm the sample standard deviation of the differences and tα/2,n-1 the value tabulated by Student's t distribution with n-1 degrees of freedom and significance level.
3. Results and Discussions
Table 1 shows the mean value (
), standard deviation (Sd) and coefficient of variation (CV) from the values of elastic modulus obtained for 10 samples of the test piece according to compressive trials (Ec), bending (Ef), tensile (Et) and ultra-micro hardness (Ehard).Table 1. Values of the modulus of elasticity of the resin to the tests conducted (MPa) 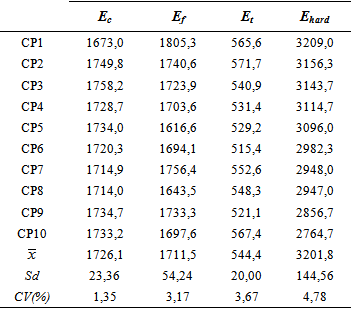 |
| |
|
The Anderson-Darling test was used to confirm normal distribution of modulus of elasticity (or Young's modulus) obtained, showing for both tests P-values greater than 0.05, ensuring normality of the data and validating the use of confidence intervals [4]. Figure 6 illustrates the normal probability plot of modulus of elasticity obtained from compression tests.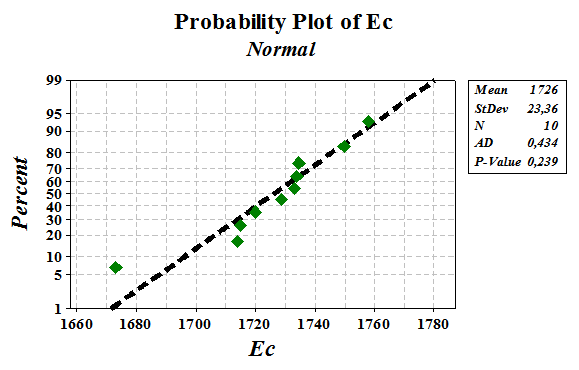 | Figure 6. Normal probability plot for the Ec |
Table 2 shows the confidence intervals found between the values of modulus of elasticity according mechanical tests.Table 2. Values for the confidence intervals 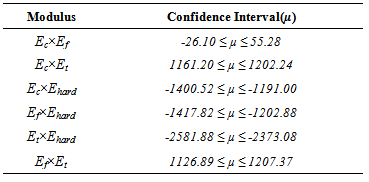 |
| |
|
From the results presented in Table 2 only the modulus of elasticity in compression and bending are considered statistically equivalent to zero for the relevance of the confidence interval [4, 5], this is not happening with the other five relations.Table 3 shows the linear regression equation and coefficient of determination (R2) for the six investigated relationships.Table 3. Coefficients of determination for linear regressions obtained 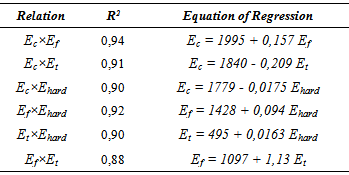 |
| |
|
4. Conclusions
The epoxy resin behaved as expected, with different modulus of elasticity due to the different forms of application.The modulus of elasticity from the four types of test was normally distributed according to the test of normality Anderson-Darling, allowing the use of the confidence interval.The results of statistical analysis showed equivalence only between the moduli of elasticity obtained from compression and bending tests, being different for other relationships. The correlation coefficients obtained from fits of linear regressions between the modulus of elasticity are in average close to 0.90, indicating a good correlation between variables, allowing the knowledge of a particular test, the prediction of elastic modulus to another form of mechanical stress. The improvement of the correlation between the modules can be established in future studies including a larger number of bodies of the test piece, driving the values for determining the coefficient closer to unity.It should be noted that the results presented relate to the resin measured here and may be different for different. However, it is possible to prove the possibility of the correlation between the four modules from the mechanical tests.
References
[1] | Túlio Hallak Panzera (2003). Dissertação de mestrado. Estudo do comportamento mecânico de um compósito particulado de matriz polimérica. Universidade Federal de Minas Gerais. Escola de Engenharia. Programa de pós-graduação em Engenharia Mecânica. 208. |
[2] | Rezende, M. C. et al. Compósitos Estruturais: Tecnologia e prática. Artliber, 2011. |
[3] | Smith A., Wilkinson S. J., Reynolds W. N. The elastic constants of some epoxy resins. Jornal of Materials Science, 9, 1974. |
[4] | Albano, C., Camacho, N., Reys, J., Feliu, J. L., Hernandez, M. Influence of screp rubber addition to Portland I concrete composites: Destructive and non-destructive testing. Composites Structure, 71; 2005. |
[5] | Yang, H., Lin, Y., Hsiao, C., Liu, J. Evaluating residual compressive strength of concrete at elevated temperatures using ultrasonic pulse velocity. Fire Safety Journal, 44, 2009. |
[6] | Nascimento, D. C. O., Ferreira, A. S., Monteiro, S. N., Aquino, R. C. M. P., Kestur, S. G. Studies on the characterization of piassava fivers and their epoxy composites. Composites: Part A, 43, 2012. |
[7] | Crescenzi, F., Marini, F., Nardi, C., Pizzuto, A., Rossi, P., Verdini, L., Rajainmaki, H., Knaster, J., Bettinalli, L. Mechanical characterizacion of glass fibre-epoxy composite material for ITER pre-compression rings. Fusion Engineering and Design, 86, 2011. |
[8] | Mir, A., Zitoune, R., Collombet, F. Bezzazi, B. Study of mechanica and thermomechanical propertis of jute/epoxy composite laminate. Jornal of Reinforced Plastics and Composites, Vol. 29, 2010. |
[9] | Piscitelli, F., Scamardella, A. M., Romeo, V., Lavorgna, M., Barra, G., Amendola, E. Epoxy composites based on amino-silylated MMT: the role of interfaces clay morphology. Journal of Applied Polymer Science, Italy: Institute of Composite and Biomedical Materials, IMAST-Scral, 2011. |
[10] | Singh-Beemat, J., Iroh, J. O. Characterizacion of corrosion resistant clay/epoxy ester composites coatings and thin films. Progress in Organic Coatings, 74, 2012. |
[11] | Ireland, R., Arronche, L., Saponara, V. L. Electrochemical investigation of galvanic corrosion betwwen aluminum 7075 and glass fiber/epoxy composites modified with nanotubes. Composites: Part B, 43, 2012. |
[12] | Liang, H., Yu, D. Mechanical and thermal properties of (Ag/C nanotube) epoxy resin composites. Polymer Science, Ser. B, 2011. |
[13] | ASTM D 638 – 03, Standard Test Method for Tensile Properties of Plastics, 2007. |