Tiago Hendrigo de Almeida1, Diego Henrique de Almeida2, Felipe Hideyoshi Icimoto3, Cristiane Inácio de Campos1, Luciano Donizeti Varanda3, André Luis Christoforo4, Francisco Antonio Rocco Lahr2
1Department of Wood Engineering, Paulista State University, Experimental Campus of Itapeva, Itapeva, 18409-010, Brazil
2Department of Structural Engineering, Engineering School of São Carlos (EESC/USP), São Carlos, 13566-590, Brazil
3Department of Science and Engineering Material, Engineering School of São Carlos (EESC/USP), São Carlos, 13566-590, Brazil
4Department of Mechanical Engineering, Federal University of São João del-Rei, São João del-Rei, 36307-352, Brazil
Correspondence to: André Luis Christoforo, Department of Mechanical Engineering, Federal University of São João del-Rei, São João del-Rei, 36307-352, Brazil.
Email: |  |
Copyright © 2012 Scientific & Academic Publishing. All Rights Reserved.
Abstract
This research aimed to investigate, by means of the strength (MOR) and stiffness (MOE) properties in bending, the homogeneity in the manufacture of plywood (Pinus sp wood and phenolic resin) produced by an industry located in the state of Paraná (PR - Brazil). The factors and levels investigated in this study were the choice of panels (A, B, C and D), the extraction position of the specimens (Center; Side) and fiber orientation (Parallel, Perpendicular), providing a full factorial design of 4122 type, with 16 different treatments. On the panel, were extracted 20 specimens (500×75×18mm) for bending tests. ANOVA results showed that the choice of panel and fiber orientation was significant in the properties of strength and stiffness in bending, this is not occurring with the extraction position of the specimens. The MOR and MOE of the specimens obtained in the parallel direction were 87% and 141% higher than the MOR and MOE of the specimens evaluated in the perpendicular direction, respectively, and with respect to non-equivalence found between the mechanical properties by the choice of the panel, for results with greater reliability it is necessary the development of new research with a significantly higher number of plywood.
Keywords:
Plywood, Pinus Wood, Phenolic Resin, Design of Experiments, Analysis of Variance
Cite this paper: Tiago Hendrigo de Almeida, Diego Henrique de Almeida, Felipe Hideyoshi Icimoto, Cristiane Inácio de Campos, Luciano Donizeti Varanda, André Luis Christoforo, Francisco Antonio Rocco Lahr, Quality Assessment in Industrial Production of Plywood by Stiffness and Strength Properties in Bending, International Journal of Materials Engineering , Vol. 3 No. 5, 2013, pp. 108-111. doi: 10.5923/j.ijme.20130305.04.
1. Introduction
The plywood is a panel based on wood veneers bonded with adhesive, pressure and high temperature for cross-lamination technique, that is, the direction of the grain of a veneer is perpendicular to grain veneer adjacent.The arrangement of the wood veneer on panel and the use of adhesive provide to plywood greater dimensional stability and mechanical properties more uniform compared to wood, decreasing the anisotropy of solid wood.Adhesives for plywood most used industrially are urea-formaldehyde, melamine-formaldehyde and phenol- formaldehyde. Determinant for life of plywood is its correct use in accordance with its recommendation for use. Generically, for internal, intermediate and external uses are recommended, respectively, adhesives urea-formaldehyde, melamine-formaldehyde and phenol-formaldehyde[1].Currently there is a scarcity of tropical wood for various purposes, including for use as raw material in industries that produce veneer and plywood. A good alternative to meet the demand of this sector providing good quality woods are the reforestation of Pinus and Eucalyptus[2, 3].The researches about the properties of strength and stiffness of plywood using Pinus wood are important for purposes that may be earmarked, including civil construction and industry[2, 4, and 5].Among the mechanical properties that should be known to characterize a lot of plywood, we have the modulus of elasticity (MOE) and modulus of rupture (MOR). In Brazil, these characteristics are determined from mechanical tests normalized by ABNT NBR 9533[6] "Determination of strength to bending plywood".Research about values of MOE and MOR of plywood produced with Pinus taeda and Pinus oocarpa with three different formulations of adhesive phenol-formaldehyde revealed that the anatomical characteristics of the wood (adult and juvenile wood, width of growth rings and early and late wood) have influenced the mechanical properties of the plywood[7].Others researches has shown that plywoods of Pinus sp. with three different formulations of PVA adhesive and two combinations of temperature and time of pressing, finding lower values of MOE and MOR compared to panels made with urea-formaldehyde and phenol formaldehyde adhesives, which are the most used by the industrial sector[8].Research with plywood made with wood from a hybrid Pinus elliottii var. caribea x Pinus elliottii var. hondurensis analyzing two points removed of the tree trunk, two adhesive grammages (380 and 420 g /cm²) and two times of pressings (8 and 12 minutes). Among the authors' conclusions, the wood of this hybrid presented good results for making plywood for purposes such as civil construction, furniture and packaging[9].The aim of this research consists to analyze the variation of the values of MOE and MOR at different points of same plywood panels produced industrially for evaluation of homogeneity of the industrial manufacturing process of plywood.
2. Material and Methods
For this research we used four panels of plywood collected on the line production of an industry of Paraná (PR - Brazil). The panels were manufactured with wood veneers of Pinus sp. with dimensions of 1.25m×2.50m×18 mm, with 13 veneers in each panel bonded with phenolic resin.Were fabricated and tested 80 specimens for bending tests according to the procedures of the normative document ABNT NBR 9533[6]. With the purpose of determining the influence of the withdrawal position of the specimens in the MOE and MOR, 40 specimens were removed from the center and the others 40 removed from the edge of the panel in parallel and perpendicular directions to the grain of the external veneer (Figure 1).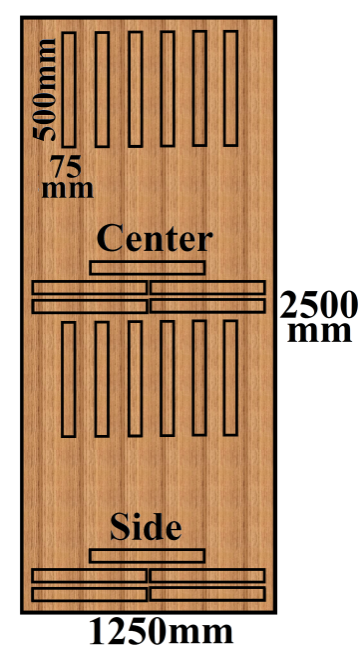 | Figure 1. Scheme of specimens extraction of the plywood |
After extraction of the specimens, they were tested in a universal testing machine DL 30000N according to the guidelines of the normative document ABNT NBR 9533[6]. The testing occurred in the Laboratory of Materials Properties of Experimental Campus Itapeva of Paulista State University (UNESP).The factors and levels investigated in this study were the panels[Bo] (A; B; C; D), the extraction position of the specimens[EP] (Center (C); Side (S)) and fiber orientation [FO] (Parallel (Pa); Perpendicular (Pe)), providing a full factorial design of the 4122 type, with 16 distinct treatments (Tr), explained in Table 1.Table 1. Treatments evaluated 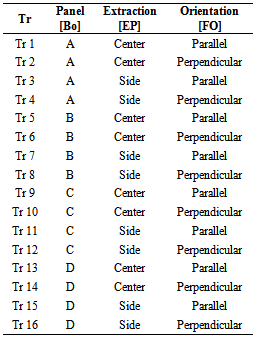 |
| |
|
The factors and interactions of the factorial design were evaluated via analysis of variance (ANOVA) at the 5% level of significance (α), assuming the equivalence between the treatment means as null hypothesis (H0) and the non-equivalence between means as alternative hypothesis (H1). P-value less than the significance level implies rejecting the null hypothesis, accept it otherwise. To validate the ANOVA, Anderson-Darling (normality) and Bartlett and Levene (homogeneity of variances) test were used, both formulated at a significance level of 5%. For the Anderson-Darling test, the null hypothesis assumed was the normality of distributions, and non-normality as the alternative hypothesis. P-value greater than 5% implies accepting H0, rejecting it otherwise. For Bartlett and Levine’s tests, the null hypothesis assumed was the homogeneity of variances between treatments, and the non-equivalence as the alternative hypothesis. P-value greater than 5% implies accepting H0, rejecting it otherwise. Factors considered significant by ANOVA, the sequence was used the Tukey test for multiple comparisons.
3. Results and Discussions
Table 2 presents the average values
and coefficients of variation (CV) of the MOR and MOE of the panels evaluated.Table 2. Results of MOR and MOE of the panels 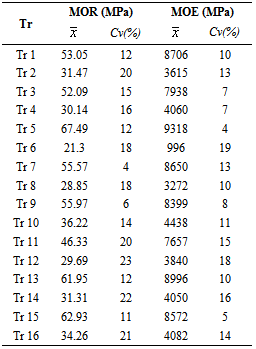 |
| |
|
Figures 2 and 3 show the results of normality and homogeneity of variance, respectively. For P-values found are both greater than 5%, given that the distributions are normal and the variances between treatments are equal, validating the model ANOVA.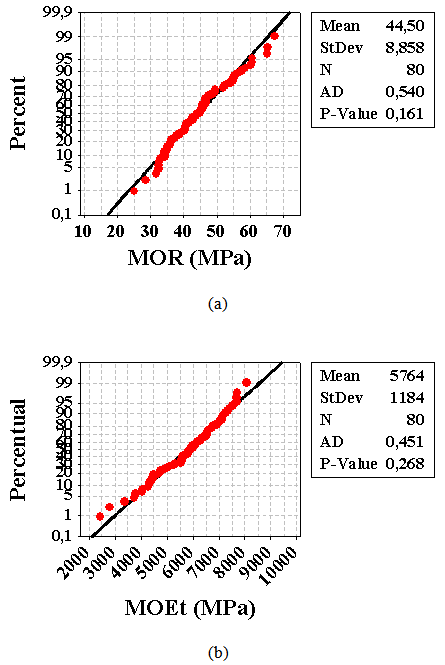 | Figure 2. Results of normality tests: MOR (a) and MOE (b) |
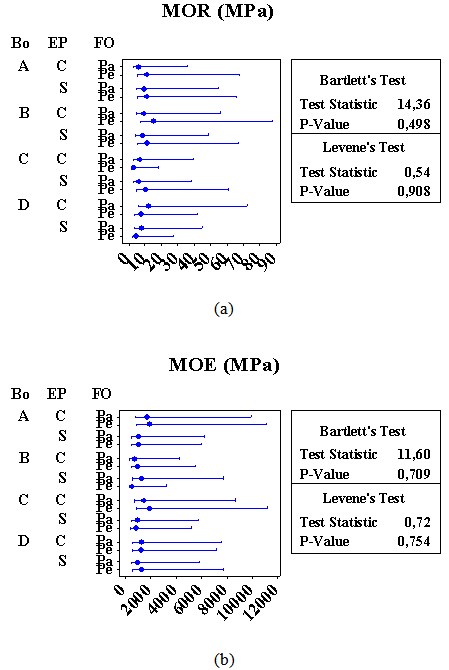 | Figure 3. Results of the homogeneity of variance tests: MOR (a) and EOM (b) |
Table 3 presents the ANOVA results for the MOR and MOE of plywood, with underlined P-values considered significant (P-value <.05).Table 3. Results of ANOVA for the MOR and MOE 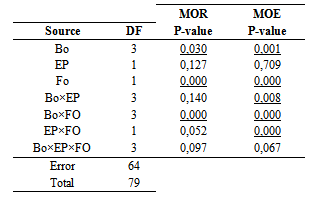 |
| |
|
From Table 3, it appears that the choice of plywood and fiber orientation to obtain the modulus of elasticity and strength in bending were considered significant by ANOVA, which did not occur with the extraction position, which provided equivalent values for both properties, revealing the uniformity achieved in the manufacture of the panel.By fiber orientation was expected that the MOE and MOR in parallel direction were significantly higher than the MOE and MOR in the perpendicular direction. As to the choice of the panels, it was expected that the results of the properties of stiffness and strength were equivalent, which has not occurred, indicated inhomogeneity in the manufacture of the panels. These results may be different for a considerable number of samples, highlighting the need for further studies. Table 4 presents the results of Tukey's test for grouping (Gr) the levels of the factors considered significant by ANOVA. From Table 4, the same letters imply average with equivalent treatments.Table 4. Results of Tukey test 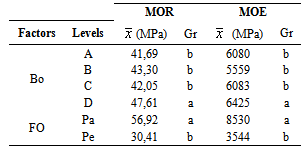 |
| |
|
The MOR and MOE of the specimens obtained in the parallel direction were 87% and 141% higher than the MOR and MOE of the specimens evaluated in the perpendicular direction, respectively.
4. Conclusions
The results showed that the choice of the panels used in the development of this research was significant in the properties of strength and stiffness in bending, this is not occurring with the extraction position of the specimen panel, which provided equivalent results.The values of MOE and MOR for the fiber orientation factor was significant, with those extracted from the fibers in the direction parallel the best results, as expected.Even with a significant choice of panels in obtaining the properties of strength and stiffness in bending, so one cannot conclude on the homogeneity achieved in the manufacture of the panels by the company it is necessary the development of new research with a significantly higher number of panels, thus increasing the reliability of the results.
References
[1] | Iwakiri, S. Painéis de madeira reconstituída. Curitiba: FUPEF, 2005. 254 p. |
[2] | Iwakiri, S.; Nielsen, I. R.; Alberti, R. A. R. Avaliação da influência de diferentes composições de lâminas em compensados estruturais de Pinus elliottii e Eucalyptus saligna, Revista Cerne, v.6, n.2, p. 19-24, 2000. |
[3] | Iwakiri, S.; Matos, J. L. M.; Ferreira, E. S.; Prata, J. G.; Trianoski, R. Produção de painéis compensados estruturais com diferentes composições de lâminas de Eucalyptus saligna e Pinus caribea, Revista Árvore, v.36, n.3, p. 596-576, 2012. |
[4] | Stamato, G. C. Resistência ao embutimento da madeira compensada. Dissertação de Mestrado. Escola de Engenharia de São Carlos, Universidade de São Paulo, São Carlos, 1998. |
[5] | Stamato, G. C.; Calil Junior, C. Resistência ao embutimento da madeira compensada, Cadernos de Engenharia de Estruturas, n.18, p. 49-76, 2002. |
[6] | Associação Brasileira de Normas Técnicas (ABNT). NBR 9533: Determinação da resistência à flexão estática de compensados. Rio de Janeiro, 1986. |
[7] | Iwakiri, S.; Del Menezzi, C. S.; Laroca, C.; Venson, I.; Matoski, S. S. Produção de compensados de Pinus taeda e Pinus oocarpa com resina fenol-formaldeído, Revista Cerne, v. 8, n.2, p. 92-97, 2002. |
[8] | Ferreira, B. S.; Silva, M. S.; Campos, C. I. Análise do desempenho físico-mecânico de compensados produzidos com adesivos a base de PVA, Madeira: Arquitetura e Engenharia, v. 12, n.29, p. 13-22, 2011. |
[9] | Almeida, N. F.; Bortolleto Junior, G.; Mendes, R. F.; Suardi, P. G. Avaliação da madeira de Pinus elliottii var. elliottii x Pinus caribaea var. hondurensis para produção de compensados, Scientia forestalis, v. 40, n.96, p. 435-443, 2012. |