Motasem N. Saidan
University of Jordan, Chemical Engineering Department, Amman, Jordan
Correspondence to: Motasem N. Saidan, University of Jordan, Chemical Engineering Department, Amman, Jordan.
Email: |  |
Copyright © 2012 Scientific & Academic Publishing. All Rights Reserved.
Abstract
This paper evaluates the effect of heat treating of linerboard for improvement of its stiffness and compressive strength. The experiments and testing of the physical and strength properties were conducted according to TAPPI test methods. The results revealed that heat treatment of linerboard at 200℃ increases themachine-direction and cross-direction compression strength 10-15%. Moreover, the increase of the linerboard weight decreased the machine-direction and cross-direction, mainly of both of tensile index and compression index, at approximately equal board density. Additionally, the increase in density will add to the increase in properties in the machine-direction and cross-direction.The effect of the dwell times has been investigated in this study and found that an increase in cross-direction short span compression was 2.5% for the 19.05 kg liner and 5.5% for the 11.8 kg liner. However, the benefits of the increased strength have to be balanced against the energy costs.
Keywords:
Linerboard, Heat treatment, Compressive strength, Short-span compressive (STFI), Stiffness
Cite this paper: Motasem N. Saidan, Improvement of Linerboard’s Strength by Heat Treatment, International Journal of Materials Engineering , Vol. 3 No. 5, 2013, pp. 93-96. doi: 10.5923/j.ijme.20130305.01.
1. Introduction
There is currently a significant emphasis on linerboard treatments to improve various qualities of linerboard because of its wide use in the packaging market. The treatments involves heat and pressure, or heat alone, during or after the production process. However, the qualities of the linerboards that should desirably be enhanced depend upon the intended application of the product.A primary determinant of the performance of linerboard is the compressive strength as measured by short-span compressive (STFI) test. In particular, the compressive strength, mainly the cross-direction (CD), is often the weakest point of the board. Various studies have been conducted on the compressive strength of linerboard and reported that the linerboard is a very sensitive material and can lose rigidity depending on environmental conditions [1, 2].According to the literature, several methods have been used to increase the stiffness and compressive strength of the manufactured linerboard and corrugating medium. A method was proposed for heat treatment of corrugated boardthat involved blowing hot air at 190C through stacks of board where it could be heat-treated and then cooled with a cycle time of 100min. Although the process improved the wet compression strength however such a system would not be practical for a large production facility[3, 4].A higher production heat treatment process was proposed where the paper web is subjected to a heat treatment at 350-400C for a few seconds[5]. With this treatment, the wet compression strength was increased from 10% to more than 25% of the dry strength. The main effect of the heat treatment was believed to be an increase in moisture resistant cross-linked bonds in the cellulose[6]. The increase in wet stiffness however has to be balanced against an increase in dry brittleness.Another improvement methods were proposed based on combination of densification and heat treatment process of linerboard or bleached board with press-drying rolls at the dry end of the paper machine[7, 8]. The sheet density is increased to 700-900 kg/m3 and treated at a temperature of at least 216C. In a machine trial, the machine direction (MD) and CD dry compressive strength were increased 8 and 19% respectively while the MD and CD wet tensile were increased 240 and 270% respectively. However, there was a loss in folding endurance of about 26%. Several drying processes were proposed to increase the paper density and strength[9]. For instance, two commercial Condebelt dryers are employed today on board machines [10, 11]. However, more research is needed for better investigation of heat and mass transfer phenomena inside the dried sheet and inside the drying chamber in all of these drying processes sheet and inside the drying chamber[12].The motivation for of this study started by investigating the effects of heat treatment of a portion of a papermaking furnish to improve the paper machine drainage and sheet bulk. Experimentally, it was noticed that when heat treatment is applied to the fines fraction from a linerboard pulp, a tough congealed mass was obtained that could not be easily dispersed to add back to the furnish. Based on this it was decided to pursue heat treating of linerboard for improvement of stiffness and compressive strength.
2. Methods and Materials
The experiments were conducted on three types of commerciallymade linerboards whichwere obtained from the Jordanian Paper and Cardboard factory. The Linerboard was treated in a computer-controlled heated press (5”x5”) at 200℃ and different times.Prior to testing, the treated boards were conditioned under conventional conditions (23C and 50% RH) for more than 24 h. For every measurement, a sample of five specimens was testedfor each type of Linerboard.The symmetry directions of the linerboard are shown in Figure 1 and defined as the following: the machinedirection (MD) corresponds to the winding directionof the spindle, the cross direction (CD) correspondsto direction transversal to MD in the sheet plane, andthe thickness direction (TD) corresponds to the directionalong the thickness out of the sheet plane.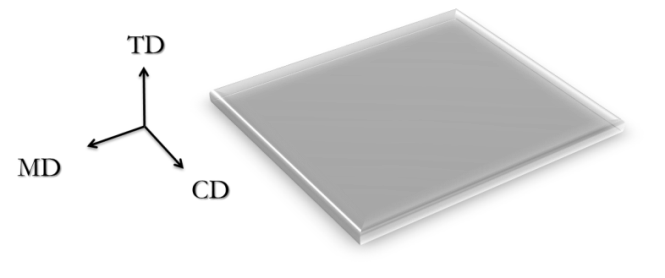 | Figure 1. Linerboard geometry and principal material directions |
The physical and strength properties of dried linerboard were measured using tensile and compression testing instruments according to TAPPI T826, TAPPI T494, and TAPPI T414. However, the results were statistically presented by means of table showing the average value of the property (with 95% confidence level) for each time.
3. Results and Discussion
The results from the laboratory investigation are summarizedin Table 1. The most significant changes were in the CD properties. The pressure of 1 psig was just enough to keep the platens in contact during the heat treatment. Even with a short dwell time, the CD tensile index increased by 23%, the CD TEA increased 55%, and the CD short span compression (SCT) increased by 11%. Moreover, increasing the density by wet pressing at 200C, has relatively shown increase in the mechanical properties, as shown in Table 1.However, a higher pressure of 25 psig resulted in an increase in sheet density but no further improvement in the compression strength.However, for further investigation, additional testing was conductedfor other linerboard weights (11.8 and 19.05kg) by heat treating at 200℃ for 10 minutes and 1 psig. The results are shown in Table 2. It is clear that the significant change is in the compression strength. More importantly, the increases in the CD compressive strength of 11-15% are particularly noteworthy since this is often the limiting factor in performance of the board. The heat treatment conditions to achieve this, however, are not practical.Table 1. Mechanical properties of heat treated15kg linerboard 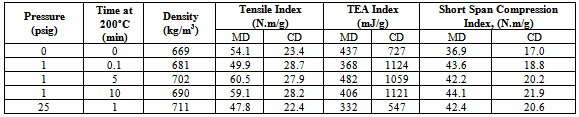 |
| |
|
Table 2. Mechanical properties of heat treated linerboard samples at 200oC, 10 minutes 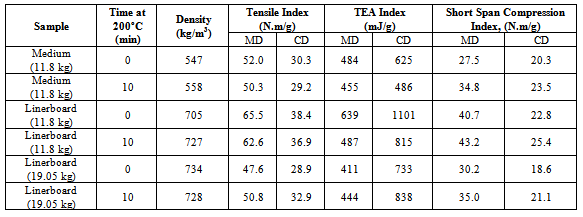 |
| |
|
Generally speaking, the increase of the linerboard weight decreases the MD and CD of both of tensile index and compression index, at more or less equal board density. This is illustrated in both figure 2 and figure 3.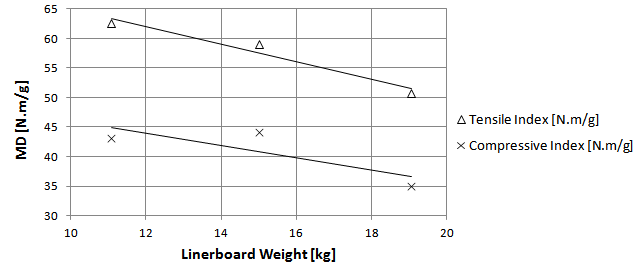 | Figure 2. The effect of linerboard weight on the MD properties |
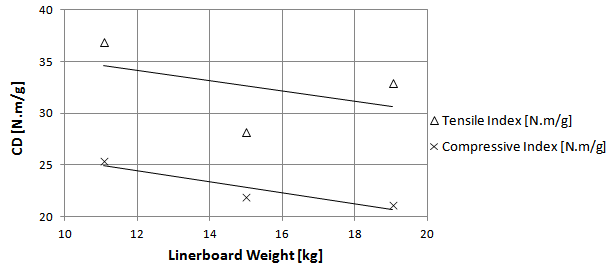 | Figure 3. The effect of linerboard weight on the CD properties |
Table 3. Mechanical properties of heat treated linerboard samples at 200℃, 10 seconds 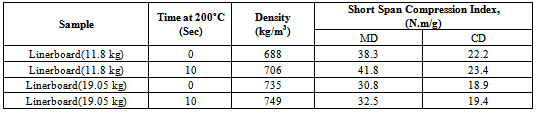 |
| |
|
Much shorter dwell times in the press at 200℃ were tried for the two linerboard samples. The results of the compression strength testing are shown in Table 3. A smaller but statistically significant increase was obtained in the short span compression strength at the shorter dwell time of 10 seconds. The increase in CD short span compression was 2.5% for the 19.05 kg liner and 5.5% for the 11.8 kg liner.Application of the heat treatment would require either heated rolls or a radiant heater section at the dry end of the board machine. The energy requirement to heat the board from 100℃ to 200℃ assuming 50% efficiency would be 126 MBTU/ton or 74 kwh/ton. The energy costs would have to be weighed against the value of the increased compression strength.
4. Conclusions
The benefits of heat treatment in linerboard strength improvement were demonstrated in thelaboratory experiment. It has been found that heat treatment of linerboard at 200℃ increases the MD and CD compression strength 10-15%, mainly due to a reduction in shrinkage and increased density.Moreover, it was noticed that the increase of the linerboard weight decreased the MD and CD, mainly of both of tensile index and compression index, at approximately equal board density.Interestingly, shorter dwell times in the press at 200℃ were tried for the two linerboard samples. A smaller but statistically significant increase was obtained in the short span compression strength at the shorter dwell time of 10 seconds.The improved sheet properties obtained with heat treatment enables the papermaking industries to reduce the basis weight taking into consideration the energy costs.
References
[1] | Allaoui, S., Aboura, Z., and Benzeggagh, M. L. (2009). “Effects of the environmental conditions on the mechanical behaviour of the corrugated cardboard,” Compos. Sci. Technol. 69(1), 104-110. |
[2] | Allaoui, S., Aboura, Z., and Benzeggagh, M. L. (2009). “Phenomena governing uni-axial tensile behaviour of paperboard and corrugated cardboard,” Compos. Struct. 87(1), 80-92. |
[3] | Anderson, R. G., and Back, E. L. (1975). “A method of increasing wet stiffness of corrugated board by means of batchwise hot air treatment—Design and costs of process,” TAPPI J. 58(8), 156-159. |
[4] | Anderson, R. G., and Back, E. L. (1975). “A method of increasing wet stiffness of corrugated board by means of batchwise hot air treatment-board properties,” TAPPI J. 58(6), 88-91. |
[5] | Back, E. L.; Stenberg, L. E. (1976) , “ Wet Stiffness by Heat Treatment of the Running Web. (1). Properties Of Treated Liner And Corrugating Medium,” Pulp and Paper Canada 77(12):T264 |
[6] | Stenberg, E. L. (1978), “Effect of Heat Treatment on the Internal Bonding of Kraft Liner,” SvenskPapperstidning -- Nordisk Cellulosa, 81(2):49 |
[7] | Swenson, R. S.; MacDonald, D. M.; Ring, M.; Field, J. H. (1987), “Kraft Linerboard by Densification and Heat Treatment” U.S. Patent4692212 |
[8] | Swenson, R. S.; MacDonald, D. M.; Ring, M. (1988), “Bleached Kraft Paperboard by Densification and Heat Treatment” U.S. Patent #4718981 |
[9] | Kunnas, L., Lehtinen, J., Paulapuro, H., Kiviranta, A. (1993), The effect of Condebelt drying on the structure of fiber bonds. Tappi Journal, Vol.76, No.4, pp.95-104 |
[10] | Lee, H.(2002), Beyond the theory-The Condebelt in Practice-A case study. Pira International, Helsinki,25-26 March, Paper 13, 14 p. |
[11] | Retulainen, E., Hamalainen, A.(1999), Three years of Condebelt drying at Stora Enso Pankakoski Mill inFinland. Tappi Eng. Conf., Sept.12-16, Anaheim, CA, USA, 12p. |
[12] | Oleg, N.T., Jari, I., and Janne, K. (2004)Effect of Process Parameters in Paper Temperature in Condebelt Drying, Drying 2004 – Proceedings of the 14th International Drying Symposium (IDS 2004), São Paulo, Brazil, 22-25 August 2004, vol. B, pp. 1327-1334 |