Ezzat S. Elshazly , A. A. M. Abdelrahman , M. A. A. Elmasry
Metallurgy Department, Nuclear Research Center, Atomic Energy Authority, P.O.Box 13759, Cairo, Egypt
Correspondence to: Ezzat S. Elshazly , Metallurgy Department, Nuclear Research Center, Atomic Energy Authority, P.O.Box 13759, Cairo, Egypt.
Email: |  |
Copyright © 2012 Scientific & Academic Publishing. All Rights Reserved.
Abstract
Cr3B4 cermets cemented by cobalt and iron as a metallic binder up to 20 wt% were prepared by hot pressing at 1500 and 1800℃ under a pressure of 14 and 41 MPa for 1hr. The binder addition enhanced the densification of Cr3B4 cermets due to the formation of liquid metal and its flow into the pores. It is also found that the temperature and pressure have a pronounced effect on densification. The densification of Cr3B4 is enhanced by the addition of cobalt and iron due to the liquid phase formation, therefore, the hardness and fracture toughness were improved, to a certain extent. A composite with a both high Vickers hardness of 35.98 GPa and a modest fracture toughness of 2.5 MPa.m1/2 could be obtained by the addition of 8 wt% cobalt at 1500℃ and 14 MPa. There is an overgrowth of the boride grains which surly reduces the hardness but has less impact on the fracture toughness.
Keywords:
Chrome Boride, Metallic Binder, Densification, Mechanical Properties
1. Introduction
Based on their unique physical and mechanical properties, particularly at elevated temperatures, binary borides have a great interest for practical and industrial applications such as thermocouple jackets, crucibles, cutting tools, and jets of airplanes and rockets(1, 2). Chrome Boride is a promising candidate for structural applications especially those requiring high-temperature strength and stability under severe erosion conditions. Because the chrome boride is a brittle material, one of the methods of increasing the toughness is to alloy it with elements which form limited or unlimited substitutional solid solution with chromium(3). By adding a small amount of metal binder, the fracture toughness of the boride will increase and hence improve the mechanical strength of the compact. However, the presence of the metal binder will decrease its hardness and toughness; therefore the amount of the metal binder should be compromised with the hardness and toughness(4-8). On the other hand, the presence of the metal binder can accelerates the compact densification during the hot pressing process through the formation of a liquid phase that flows under pressure and fills the pores. Cobalt, Nickel, and Iron are good candidates as binding materials that can improve the mechanical properties and the thermal resistance of transition metal borides(9, 10). The extent of application of the chrome borides is still quite limited because of the lack ofreliable data on its behavior at high temperatures.The aim of this work is mainly to enhance the densification by adding different amounts of metallic binder to Cr3B4 cermets and, thereby, study the effect of these different process variables on the mechanical properties of it.
2. Experimental
The Cr3B4powder imported from Riedal de Haen having 91 wt% Cr3B4 and 9 wt% Al2O3. The theoretical density of this powder as measured by the null pycnometer was 5.059 g/cm3 and the median particle size was 7 µm as measured by the 3D image analyzer and a surface area of 3.08 m2/g. The iron powder used in this work was imported from Merk with median particle size 0.5 µm, specific surface area 1.2218 m2/g and, a theoretical density 7.73 g/cm3 and, purity 97.745 %. The cobalt powder density 8.22 g/cm3, median particle size 8.5 µm and specific surface area 1.2 m2/g.The Cr3B4 powder was mixed with the required proportion of Fe or Co by tumbling for 6 hrs and mounted equally to a poco graphite die having six cylindrical holes 1 cm diameter each. It was hot pressed for 1 hr at different temperatures and pressures and stagnant Argon atmosphere. The compacts are characterized after that and the micro hardness was measured using a Shiwadzu type M No. 80413 using 50g load. The hardness values represent the medium of 10 measured points. The fracture toughness was evaluated by the Anstis crack length method which is dependent on the elastic modulus of the material, the micro hardness, the crack length and the applied load. Anstis et. al.(11,12) used a simplified two dimensional fracture mechanics analysis and obtained where F is the load in Newtons, c is the crack length from the center of the indent to the crack tip in meters, E is the Young's modulus in GPa estimated by a nondestructive testing, and H is the Vickers hardness in GPa measured experimentally.
3. Results and Discussion
3.1. Hot Pressing
The relative densities of Cr3B4 cermets cemented by cobalt and iron respectively hot pressed, at 1500 and 1800℃ at 14 MPa and 41 MPa for 1hr., as a function of the binder content are shown at figures.1, 2, 3, 4. For these compacts hot pressed at 1500℃ and 14 MPa, it is clear that the relative density increases as the binder content and or the time increases. The increase in the relative density by the addition of binder cobalt and or iron is more pronounced than the increase of time as it may be clear from these figures. With the addition of more than 8 wt% both cobalt and or iron, high relative densities, over 95% were obtained. In particular, the highest value of 98% could be reached for the specimens with 12 wt% of both cobalt and or iron after one hour hot pressing at 1500℃. For the samples containing 20 wt% binder, a relative density more than 0.96 is reached at the beginning of the pressing time. From Figs. 3 and 4 it is clear that the theoretical density is obtained after one hour using 41 MPa at 1800℃ whatever the amount of binder up to 10 wt % binder which indicates that the pressure has a pronounced effect on the densification.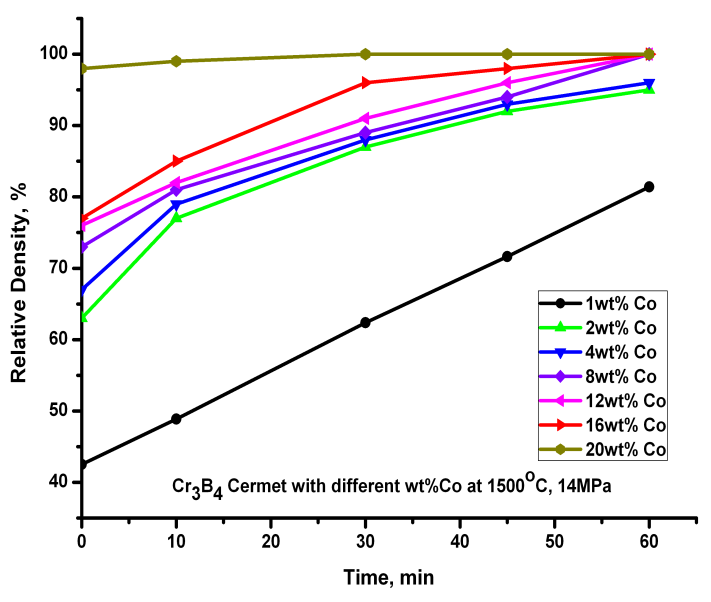 | Figure 1. Effect of time and binder content on the relative density of Cr3B4 - Co cermets at 1500℃ and, 14 MPa |
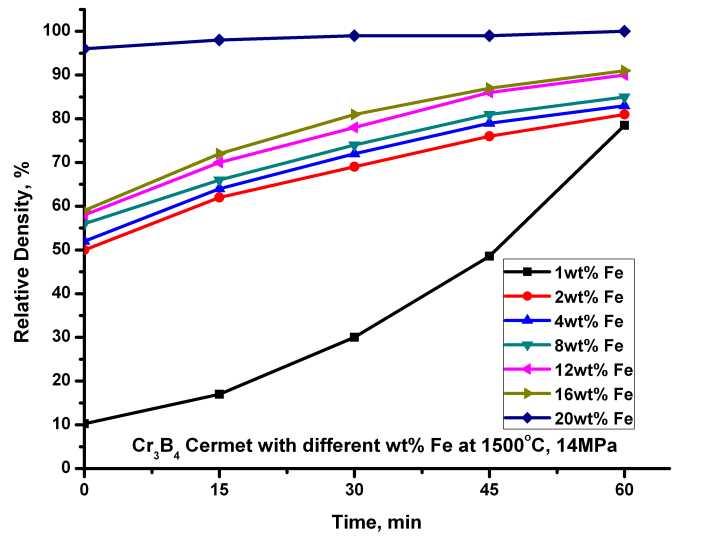 | Figure 2. Effect of time and binder content on the relative density of Cr3B4 - Fe cermets at 1500℃ and, 14 MPa |
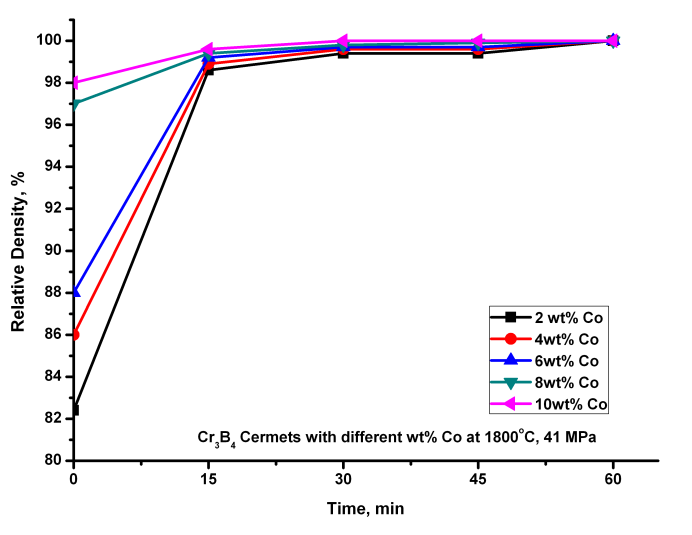 | Figure 3. Effect of time and binder content on the relative density of Cr3B4 - Co cermets at 1800℃ and, 41 MPa |
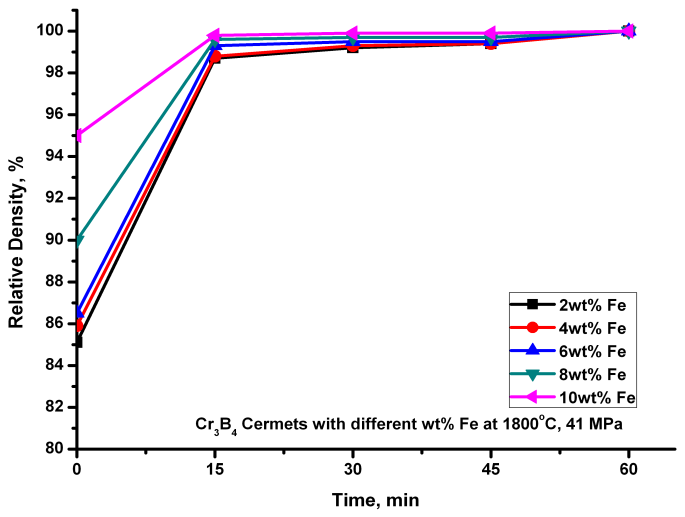 | Figure 4. Effect of time and binder content on the relative density of Cr3B4 - Fe cermets at 1800℃ and, 41 MPa |
3.2. Microstructure
The microstructure of Cr3B4 cermets polished sections, hot pressed at 1500℃, 14 MPa and cemented by 1 , 2 , 12 wt% Co and or 1 , 2 , 12 wt% Fe, is shown in fig. 5 and 6 respectively. The Cr3B4 phase appears as areas of high contrast in the darker cobalt phase. It can be seen that the size and the number of pores decreased with increasing the binder content. The morphology and size of Cr3B4 specimens were quite different from those of Cr3B4 starting powder and seem that the binder in the liquid state penetrates among the Cr3B4 grains. Also from the micrograph, it is clear that with the increasing of metallic binder the composite became denser as it clearly observed from the densification curves Fig. 1 and the same trend is observed also for the Cr3B4 iron cermets but the porosity is a little bit higher.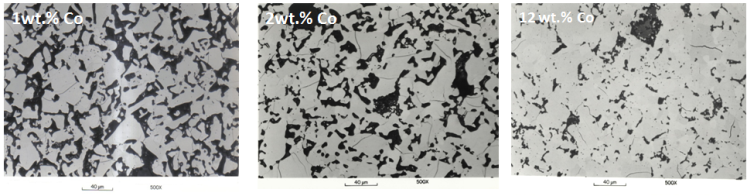 | Figure 5. Microstructures of hot pressed Cr3B4 specimens with 1 wt%, 2 wt% and, 12 wt% cobalt at 1500℃ and 14 MPa |
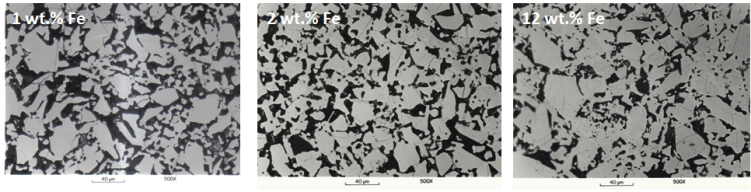 | Figure 6. Microstructures of hot pressed Cr3B4 specimens with 1wt%, 2wt%, and 12wt% iron at 1500℃ and 14 Mpa |
3.3. Hardness and Fracture Toughness
The optical micrograph for an indentation made on the surface of Cr3B4 specimen with the cracks emanating from it is shown in fig. 7 using 1 Kg load. Hardness values were calculated from the dimensions of the impression made on the surface of the specimens and the values shown in Figs. 8 and 9 represent the average of ten values. 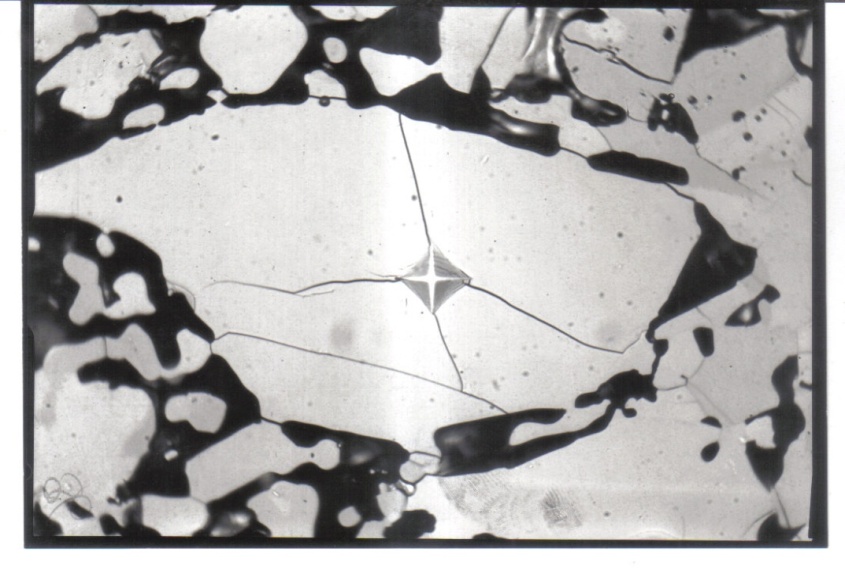 | Figure 7. Optical micrograph for the indentation |
The cracks that appeared at the corners of the indentation are used to calculate the fracture toughness of the material.Increasing of the amount of cobalt added as a cementing material to the Cr3B4 cermets, the hardness increased for both the two pressing temperatures, 1500 and 1800℃ using a pressure of 14 and 41 MPa respectively, up to 8 wt% Co. The Cr3B4 cermets exhibit the highest hardness across cobalt content taking the maximum at 8wt%, 35.98 GPa, at 1500℃ with a pressure of 14 MPa. While the hardness showed a decreasing across the iron content added to the Cr3B4 cermets taking the lowest at 12 wt% of iron at 1500℃ with a pressure of 14 MPa. At 1800℃ with a pressure of 41 MPa, there was no a significant change on the decreasing of the hardness values with the iron content, i.e, the hardness was decreased and reached the lowest value at 12 wt% of iron, nearly the same value for 1500℃ with a pressure of 14 MPa. This can be explained by the insufficient densification which occurred during the hot pressing operation at the two different temperatures or due to the solubility of iron in the boride phase.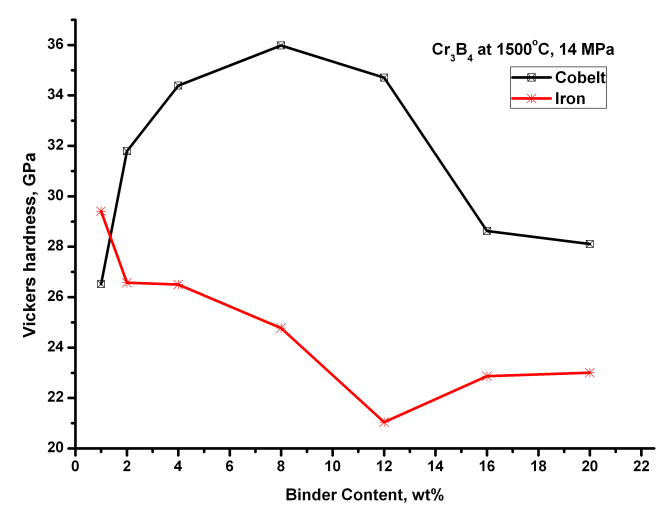 | Figure 8. Vickers hardness of Cr3B4 cermets as a function of binder content at 1500℃ and, 14 MPa |
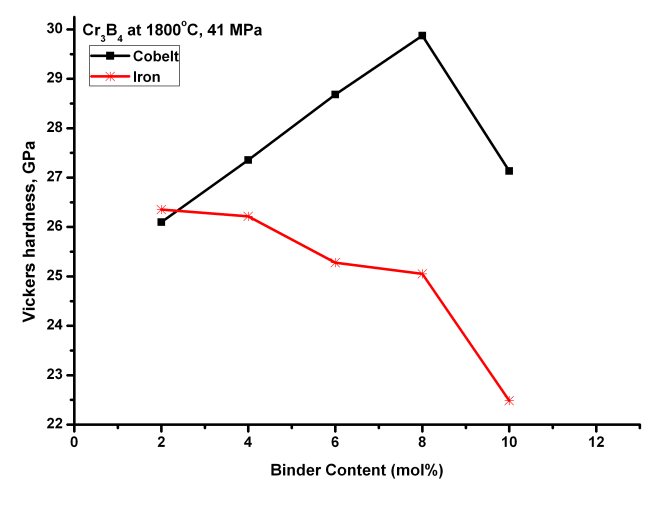 | Figure 9. Vickers hardness of Cr3B4 cermets as a function of binder content at 1800℃ and, 41 MPa |
The fracture toughness values as calculated from equation (1) are shown in figures. 10, and 11, as a function of the binder content, cobalt and or iron, for these specimens that hot pressed at 1500℃ and 1800℃ respectively.The fracture toughness of the specimens that has a cobalt content less than 2 wt% is very low due to insufficient densification. The fracture toughness measurements for the specimens that pressed at 1500℃ with a pressure of 14 MPa increased to 3 MPa.m1/2 with the increasing of cobalt content to 12wt%. On the other hand, the fracture toughness increased to 2.53 MPa.m1/2 with increasing the iron content up to 8 wt% and there after it decreased to 1.51 MPa.m1/2. At the meantime, for the specimens which pressed at 1800℃ with a pressure of 41 MPa, the Cr3B4 cermets exhibit an increase in the fracture toughness measurements taking the highest, 1.92 MPa.m1/2, at 12wt% of cobalt and 1.56 MPa.m1/2 at 8wt% of iron.There was an overgrowth of the boride grains occurred with increasing the cementing content and the pressing temperature and pressure surely reduces the Vickers hardness but in the meantime has less impact on the fracture toughness.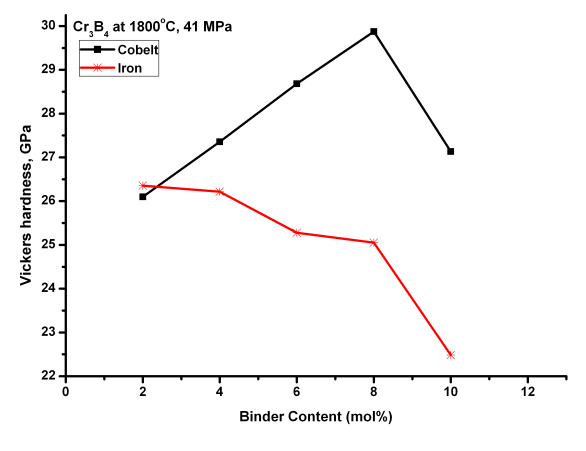 | Figure 10. Fracture toughness of Cr3B4 cermets as a function of binder content at 1500℃ and, 14 MPa |
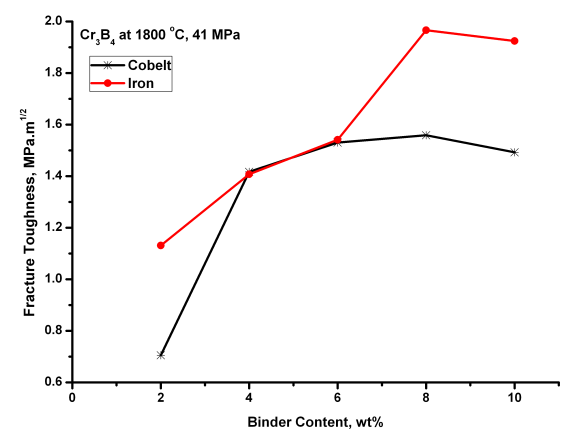 | Figure 11. Fracture toughness of Cr3B4 cermets as a function of binder content at 1800℃ and, 41 MPa |
4. Conclusions
(1) Cr3B4 cermets with different amounts of cobalt and iron as a metallic binder were fabricated by hot pressing of a powder mixture at 1500℃and 1800℃ with an applied pressure of 14 and 41 MPa respectively. (2) The densification of Cr3B4 was enhanced by the addition of Cobalt and or iron due to the liquid phase formation, and therefore, the Vickers hardness and fracture toughness were improved, a change that was ascribed to the densification and residual stress caused by the thermal expansion mismatch of Cr3B4 and the metallic binder. (3) A composite with both high Vickers hardness of 35.98 GPa and a modest fracture toughness of 2.53 MPa.m1/2 could be obtained by the addition of 8wt% cobalt.
References
[1] | YOUNIS S.S., KHATER A.M., ELMASRY M.A., MAHDY A.N., and ABADIR M.F., Thermochim. Acta, 189(1991), 271. |
[2] | CAMPBELL C. E. and KATTNER U. R., Calphad, 26(2002), 477. |
[3] | GUSLIENKO Y. A., LUCHKA M. V., YANENSKII V. N., and KHRIENKO A. F., Poroshkovaya Metallurgiya, 3(1989), 54. |
[4] | SONBER J.K., MURTHY T.S.R., SUBRAMANIAN C., KUMAR S., FOTEDAR R.K. and SURI A.K., Int. Journal of Refractory Metals & Hard Materials, 27(2009), 912. |
[5] | YAMADA S., HIRAO K., YAMAUCHI Y. and KANZAKI S., Ceramics International, 29(2003), 299. |
[6] | OKADA S., KUDOU K., IIZUMI K., KUDAKA K., HIGASHI I., and LUNDSTROM T., J. Cryst. Growth, 166(1996), 429. |
[7] | OKADA S., ATODA T., and HIGASHI I., J. Solid State Chemistry, 68(1987), 61. |
[8] | GUY C. N. and URAZ A. A., Journal of the Less-Common Metals, 48(1976), 199. |
[9] | AUDRONIS M., KELLY P.J., AMELL R.D., LEYLAND A.,and MATTHEWS A., Surface & Coatings Technology, 200(2005), 1366. |
[10] | YAMADA S., HIRAO K., YAMAUCHI Y., and KANZAKI S., J. Eur. Ceram. Soc., 23(2003), 561. |
[11] | WACHTMAN J.B., Mechanical Properties of Ceramics, John Wiley &Sons, Inc., 1996. |
[12] | ANSTIS G.R., CHANTIKLUL P., LAWN B.R. and MARSHALL D.B., J. Am. Ceram. Soc., 64(1981), 533. |