Venu Malagavelli , Neelakanteswara Rao Paturu
Department of Civil Engineering BITS, Pilani – Hyderabad Campus, Hyderabad, Andhra Pradesh , 500078, India
Correspondence to: Venu Malagavelli , Department of Civil Engineering BITS, Pilani – Hyderabad Campus, Hyderabad, Andhra Pradesh , 500078, India.
Email: |  |
Copyright © 2012 Scientific & Academic Publishing. All Rights Reserved.
Abstract
Concrete, a composite material made with cement, aggregates, admixtures or super plasticizers and water comprises in quantity the largest of all man-made materials. Although aggregates make up three fourths of the volume of concrete, the active constituent of concrete is cement paste. The properties and performance of concrete are largely determined by the properties of the cement paste. Super plasticizers in concrete confer some beneficial effects such as acceleration, retardation, air entrainment, water reduction, plasticity etc., and these effects are due to their action on cement. The scientists are mainly concentrating to develop the specialized concretes, to enhance the service life of the buildings, and to provide satisfactory performance under aggressive environments. In the present experimental investigation M30 concrete is used as control mixture with four different super plasticizers namely SNP (Sulphonated Naphthalene Polymer) 1, SNP 2, SNP 3 and SNP 4. Strength of modified concrete is compared with the normal concrete i.e. without super plasticizer. The results show that the significant improvement in the strength and workability of modified concrete.
Keywords:
Admixtures/Super Plasticizers, Mix Design, Workability, Compressive Strength, Concrete
Cite this paper:
Venu Malagavelli , Neelakanteswara Rao Paturu , "Strength and Workability Characteristics of Concrete by Using Different Super Plasticizers", International Journal of Materials Engineering , Vol. 2 No. 1, 2012, pp. 7-11. doi: 10.5923/j.ijme.20120201.02.
1. Introduction
Concrete is a building material composed of cement, sand as fine aggregate, crushed rock as coarse aggregate and water. High Performance Concrete (HPC) is defined as a concrete meeting special combination of performance and uniform characteristics that cannot always be achieved routinely using conventional constituents, and normal mixing, placing and curing practices (Mehta, P. K., 1999; Mehta, P. K. and Paulo, J. M. M., 2006). At an early stage of development in the 1980s, the High-Performance Concrete (HPC) was regarded as a concrete that had many advantageous engineering properties such as high strength, high modulus of elasticity, high workability, low permeability, etc. (Mehta, P. K., 1999). The standard mix designs vary according to both the intended use of mix and its projected properties in the hardened state. One area where the focus required is the use of super plasticizers in concrete. The ultimate goals of using super plasticizers are to improve one or more aspects of concrete performance, or to maintain the same level of performance. Many super plasticizers available today are composed of both chemical and/or mineral ingredients. More than 250 test samples were prepared with four different super plasticizers and tested for 7 and 28 days compressive strength.
2. Properties of Materials
Cement: The Ordinary Portland Cement (OPC) 43 grade is used in this investigation. The physical & chemical properties of the cement are as shown in Table- 1.Table 1. Properties of Cement |
| Properties | Test Results | Limits as per IS8112-1989 | Fineness (M2/Kg) (Specific Surface) | 290 | 225 minimum | Setting Time in minutes (Initial) | 50 | 30 | Setting Time (Final) | 280 | 600 | Sound NessBy LechatelierBy Auto Clave | 3.00.06 | 10mm0.8% | Compressive strength3 days7 days28 days | 30.640.253.6 | 23MPa Min33MPa Min43MPa Min |
|
|
Aggregates: The aggregate consists of both fine and coarse components. The fine aggregate, which often referred to sand, is usually not a commercially manufactured product but one that is taken directly from nature. Coarse aggregate is a material commonly produced by crushing larger rock, separating the crushed portion according to size, and recombining in a carefully controlled manner.Fine Aggregate: The Locally available river sand from karimnagar, Andhra Pradesh, India, is used as fine aggregate in the concrete design mix. The specific gravity, water absorption and fineness modulus are 2.62, 0.28% and 2.83 respectively. The grain size distribution curve is given in fig.1.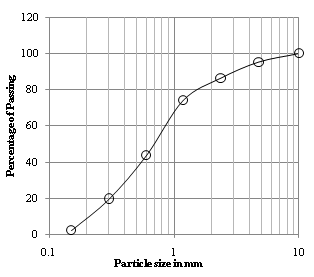 | Figure 1. Grain size distribution of Fine aggregate |
Coarse Aggregate: The coarse aggregate used in the experimental investigation is a mixture of 20mm and 10mm size aggregates. The aggregates are angular in shape and free from dust. The specific gravity, water absorption and fineness modulus are 2.71, 0.32% and 7.18 respectively. The results of sieve analysis of coarse aggregate are shown in Table-2.Table 2. Sieve Analysis of Coarse Aggregate |
| IS Sieve | Weight retained | % weight retained | Cumulative % weight retained | % passing | Limits as per IS 383 – 1970 IS 2386 – 1963 | 80 | 0 | 0 | 0 | 100 | 100 | 40 | 0 | 0 | 0 | 100 | 100 | 20 | 962 | 19.24 | 19.24 | 80.76 | 85– 100 | 10 | 3990 | 79.8 | 99.04 | 0.96 | 0 – 20 | 4.75 | 48 | 0.96 | 100 | 0 | 0 – 5 | 2.36 | 0 | 0 | 100 | 0 | 0 | 1.18 | 0 | 0 | 100 | 0 | 0 | 600 | 0 | 0 | 100 | 0 | 0 | 300 | 0 | 0 | 100 | 0 | 0 | 150 | 0 | 0 | 100 | 0 | 0 | Total cumulative % of weight retained | 718.28 | | |
|
|
Water: Water should be free from sewage, oil, acid, strong alkalies or vegetable matter, clay and loam. The water used in the concrete is potable, and is satisfactory to use. Water sample collected from bore well and its properties are shown in Table-3.Table 3. Properties of Water sample |
| S. No. | Parameter | Results | Limits as per IS 456 – 2000 | 1 | pH | 6.6 | 6.5 – 8.5 | 2 | Chlorides (mg/l) | 49 | 2000 (PCC) 500 (RCC) | 3 | Alkalinity (ml) | 8 | < 25 | 4 | Sulphates (mg/l) | 116 | 400 | 5 | Fluorides (mg/l) | 0.089 | 1.5 | 6 | Organic Solids (mg/l) | 53 | 200 | 7 | Inorganic Solids (mg/l) | 129 | 3000 |
|
|
Super Plasticizers: A super plasticizer is a material other than water, aggregates and cement used as an ingredient of concrete and added to the batch immediately before or during the mixing. Super Plasticizers (IS 9103 – 1999) are used where a high degree of workability and its retention are required, where a delay in transportation or placing is required, or when high ambient temperatures cause rapid slump loss. It facilitates production of high quality concrete. The super plasticizers enable quicker placing and compaction of concrete. They also minimize the risk of segregation and bleeding; thus aids pumping of concrete.Four different types of super plasticizers namely SNP 1 to 4 are considered and a comparative analysis is done in the present study. The properties of super plasticizers are presented in Table-4.SNP 1 is a chloride free, super-plasticising admixture based on selected sulphonated naphthalene polymers. It disperses the fine particles in the concrete mix, enabling the water content of the concrete to perform more effectively. The very high level of water reduction is possible with SNP 1, which increases the strength of the concrete mix. SNP 2 is also a chloride free and highly effective dual action liquid superplasticizer for the production of free flowing concrete or as a substantial water-reducing agent for promoting high early ultimate strengths. This consists of Aqueous solution of anionic formaldehyde - polycondensate, naphthalene sulphonic acid and sodium salt. It decreases the amount of vibration required, normal set without retardation and reduces risk of segregation.SNP 3 has lingosulphonate base. It is chloride free and suitable for high performance concrete to produce pumpable concrete. The workability increases without extra water. It improves cohesion, minimise segregation and give better finish.SNP 4 is based on modified Sulphonated naphthalene formaldehyde. It is chloride free and it promotes dispersing of cement particles and reduces water requirements without affecting the workability, thus resulting increased strength and lower permeability.Table 4. Properties of super plasticizers |
| S. No. | Test Parameter | SNP 1 | SNP 2 | SNP 3 | SNP 4 | 1 | pH | 7.61 | 7.65 | 7.71 | 7.75 | 2 | Specific gravity | 1.24 | 1.21 | 1.19 | 1.184 | 3 | Solid Content (%) | 41.261 | 35.51 | 34.51 | 39.40 | 4 | Appearance | Brown liquid | Dark Brown liquid | Brown liquid | Brown liquid |
|
|
Mix Proportions And Samples PreparationThe concrete mix is designed as per IS 10262 – 1982, IS 456-2000 and SP 23. Target mean strength for M30 grade concrete is 38.25 N/mm2. Table-6 represents the quantities of mix proportion for one cubic meter of concrete and one cement bag. Standard cast iron moulds of size 150x150x150 mm are used in the preparation of cubes. The moulds have been cleaned to remove dust particles and applied with mineral oil on all sides before the concrete is poured into the mould. The super plasticizer is mixed with the constituents of concrete at the time of adding water. Full blending of the super plasticizer and the concrete is ensured by mixing for a period of at least two minutes. Thoroughly mixed concrete is filled into the mould and compacted in three equal layers. Excess concrete is removed with trowel after proper compaction and top surface is smoothened. Overdose may also cause increase in air entrainment, which will tend to reduce the strength of the mix. After casting, the specimens are stored in the laboratory with room temperature for 24 hours from the time of addition of water to the ingredients. After this period, the specimens are removed from the moulds, immediately submerged in the clean and fresh water tank. The specimens are cured for 28 days. Three samples of every super plasticizer were tested for 7 and 28 days compressive strength.
3. Results & Discussions
Slump tests are conducted using slump cone for all samples of concrete without and with super plasticizers (SNP 1 to 4) for water cement ratio 0.45.The maximum, minimum and average slumps (in mm) of 25 samples with or without super plasticizer are listed below.Table 5. Slump test results |
| | Max. Slump | Min. Slump | Avg. Slump | No Admixture | 86 | 40 | 61.42 | SNP 1 | 102 | 48 | 66.12 | SNP 2 | 98 | 52 | 68.81 | SNP 3 | 112 | 90 | 95.10 | SNP 4 | 101 | 58 | 72.11 |
|
|
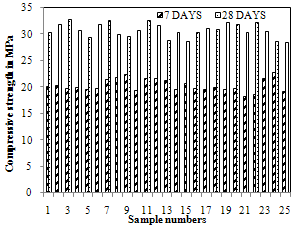 | Figure 2. Compressive strength of normal concrete at the age of 7 and 28 days |
Among the super plasticizers, SNP 3 gave better slump results when compared to other three super plasticizers. This gives better pumpability of concrete. 25 samples have been selected for the present study.The maximum, minimum and average 7 and 28 days compressive strengths without super plasticizers are 22.85, 18.3, 20.37 and 32.88, 28.52, 30.78 N/mm2 respectively. The maximum, minimum and average 7 and 28 days compressive strengths with SNP1 admixture are 36.63, 18.56, 27.04, and 40.25, 29.1, 36.28N/mm2 respectively (Fig. 3). 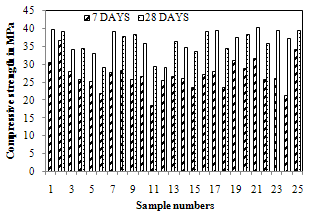 | Figure 3. Compressive strength of concrete at the age of 7 and 28 days with SNP 1 |
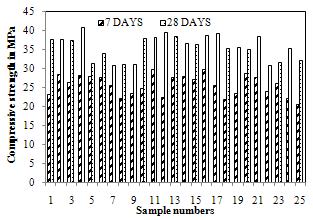 | Figure 4. Compressive strength of concrete at the age of 7 and 28 days with SNP 2 |
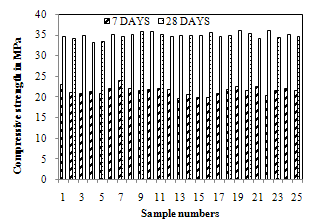 | Figure 5. Compressive strength of concrete at the age of 7 and 28 days with SNP 3 |
Similarly the maximum, minimum and average 7 and 28 days compressive strengths with SNP2 super plasticizer are 29.53, 20.49, 25.58 and 40.68, 30.62, 35.51N/mm2 respectively (Fig. 4). For the SNP 3 super plasticizer the maximum, minimum and average 7 and 28 days compressive strengths are 23.86, 19.58, 21.42 N/mm2 and 36.12, 33.01, 34.81 N/mm2 (Fig. 5).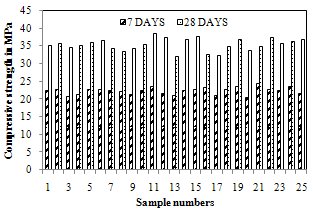 | Figure 6. Compressive strength of concrete at the age of 7 and 28 days with SNP 4 |
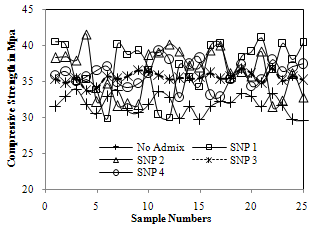 | Figure 7. Compressive strength of concrete at the age of 56 days |
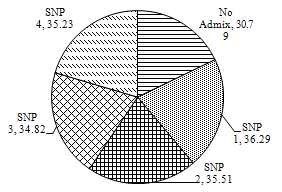 | Figure 8. Average compressive strength of concrete at the age of 28 days |
The maximum, minimum and average 7 and 28 days compressive strengths with SNP4 admixture are 24.22, 20.45, 22.18 and 38.5, 32.00, 35.23N/mm2 respectively (Fig. 6). The following table gives the 56 days strength of different concretes.Table 6. Compressive strength of concrete at the age of 56 days |
| Compressive strength (N/mm2) | Without SP | SNP1 | SNP 2 | SNP 3 | SNP 4 | Maximum | 33.88 | 41 | 41.48 | 36.81 | 39.22 | Minimum | 29.52 | 29.85 | 31.42 | 33.7 | 32.72 | Average | 31.78 | 37.03 | 36.31 | 35.5 | 35.95 |
|
|
From the Fig. 3 to 7, it is observed that 7, 28 and 56 days compressive strengths of the concrete are varying abnormally in case of SNP1, SNP2 and SNP4. The result of SNP3 shows uniformity for all the samples. From the fig. 8, there is much difference in the average compressive strengths of modified concretes.From Fig. 9, the standard deviations of 56 days compressive strength of concrete cubes are 3.41, 3.17, 0.73 and 1.74 by using SNP1, SNP2, SNP3 and SNP4 respectively. The degree of control of these Superplasticizers is excellent for SNP1, SNP2, SNP4 and laboratory precision for SNP3 (Shetty, M. S., 2000).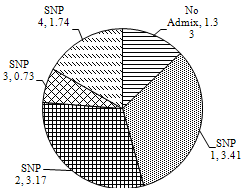 | Figure 9. Standard deviation of compressive strength |
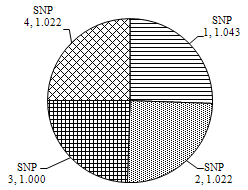 | Figure 10. Cost of Superplasticizers |
The cost analysis was made and reported in Fig. 10 in terms of cost per tonne. It observed that the cost of SNP1, SNP2 and SNP4 Super plasticizers is more when compared to SNP3.
4. Conclusions
Based on the experiments conducted, the following conclusions are drawn.1. Superplasticizers are to test in the laboratory before using in the mass concrete applications.2. The workability and compressive strength of concrete increases with the use of super plasticizers3. The average slump of measuring workability of concrete with SNP3 super plasticizer is near to the designed value of the concrete.4. The average 56 days compressive strength of M30 concrete by using SNP3 admixture is increased by 11.69% compared to concrete without admixture.5. The concrete with admixture SNP3 is consistent and uniform in giving the experimental results. Also it is evident from standard deviation which is of laboratory precision.
References
[1] | Mehta, P. K. and Paulo, J. M. M. (2006), CONCRETE Microstructure, Properties and Materials, 3rd edition, Tata McGraw-Hill Publishing Company Ltd., New Delhi |
[2] | Mehta P. K., (1999), “Advancements in Concrete Technology”, Concrete International, June, pp. 69-76 |
[3] | Shetty, M. S. (2000), Concrete Technology, 4th Edition, Chand, S. & Co Ltd, New Delhi |
[4] | SP – 23: Hand Book on Concrete Mixes |
[5] | IS 10262 – 1982: Recommended Guidelines for Concrete Mix Design |
[6] | IS 2386 – 1963: Methods of Test for Aggregates for Concrete |
[7] | IS 383 – 1970: Specification for Coarse and fine Aggregates from Natural Sources for Concrete (Second revision) |
[8] | IS 456 – 2000: Plain and Reinforced Concrete Code of Practice |
[9] | IS 8112 – 1989: 43 Grade Ordinary Portland cement Specification |
[10] | IS 9103 – 1999: Concrete Admixtures – Specifications |