Dinara B. Buranova1, Mirjalil Y. Yunusov2, Zabibulla K. Babaev3, Sherzod R. Kurambaev3, Sherzod K. Matchanov4
1Independent Researcher, Urgench State University, Urgench, Uzbekistan
2Doctor of Technical Sciences, Professor, Tashkent Institute of Chemical Technology, Tashkent, Uzbekistan
3Doctor of Technical Sciences, Associate Professor, Urgench State University, Urgench, Uzbekistan
4Candidate of Technical Sciences, Associate Professor, Urgench State University, Urgench, Uzbekistan
Copyright © 2023 The Author(s). Published by Scientific & Academic Publishing.
This work is licensed under the Creative Commons Attribution International License (CC BY).
http://creativecommons.org/licenses/by/4.0/

Abstract
The article provides information on determining the suitability of the Khiva mine for use in glass production by enrichment of feldspar quartz sand. Based on complex physical and chemical analysis, it was found that quartz sand mainly belongs to quartz and feldspar, as well as a small amount of hematite, chlorite and calcite minerals. It was found that the chemical composition of quartz sand consists of 86–87% silicon oxide, but iron oxide, which has a negative effect on glass production, is up to 1.25%. Based on the selected enrichment technology, reduction of iron oxide from 1.25 to 0.05% and other harmful additives from 10.05% to 1.82% was achieved.
Keywords:
Glass production, Quartz sands, Khiva deposit, Minerals, Feldspar, Enrichment, X–ray phase analysis, Iron oxide, Glass, Silicate materials, Silicon oxide
Cite this paper: Dinara B. Buranova, Mirjalil Y. Yunusov, Zabibulla K. Babaev, Sherzod R. Kurambaev, Sherzod K. Matchanov, The Enrichment of Quartz Sands of the Khiva Deposit for Glass Production, International Journal of Materials and Chemistry, Vol. 13 No. 2, 2023, pp. 19-22. doi: 10.5923/j.ijmc.20231302.01.
1. Introduction
In the production of inorganic materials on a global scale, great attention is being paid to the development of technologies for the enrichment of raw and man–made resources and the production of low–cost, high–quality products. The quality indicators of the used raw materials are considered to be the main factor, and it is noted that the reserves of high quality raw materials are decreasing, and the quality indicators of the new mining raw materials do not meet the standard requirements. The glass products produced on the basis of raw materials are becoming one of the most important industries worldwide and determine the development of a number of production sectors. Based on this, it is important to produce glass products based on concentrates obtained from inorganic and man–made raw materials using enrichment technologies [1,2].However the large numbers of siliceous raw materials, which are considered important for the production of silicate materials, there are few mines that use them without enrichment for the production of glass and glass products [3]. The quality of glass and ceramic products depends on the chemical and mineralogical properties of the raw materials used [4]. One of the main problems of processing silicate materials is the high consumption of energy in the processing of raw materials.Currently, a number of researches are being carried out in the world on enrichment of low–quality raw materials and man–made waste, acceleration of technological processes in the production of inorganic materials, and improvement of their properties and characteristics. In this regard, in the production of glass products, special attention is paid to the production of glass with high transparency, the development of new effective compositions, and the introduction of innovative technologies that save energy and resources [5,6].This article describes the research on the enrichment of quartz sands of the “Khiva” deposit which is located in Khorezm province of the Republic of Uzbekistan, as well as their use in the silicate industry.
2. Material and Methods
The quartz sands of the “Khiva” deposit, located in the Khorezm region, were studied as a research object.IR transmission spectra of glass samples were obtained at room temperature in the wavelength ranges of 4000–400 cm–1 and 4000–300 cm–1 using a SPECORD M–80 (Carl Zeiss JENA) spectrophotometer with a spectral resolution of 4 cm–1. The research analysis is based on the principle of two–beam measurement with the determination of the electrical zero point and double interruption [7].To identify the phase composition of the component used and the obtained samples, X–ray phase analysis was used on a LABX XRD–6100 SHIMADZU diffractometer using CuKα radiation (β–filter–Ni, wavelength 1.5418 Å, current mode and tube voltage 30 mA, 30 kW) [8].The granulometric, chemical, chemical–mineralogical composition of raw materials was determined by physical–chemical analysis [9-11].
3. Results and Discussions
“Khiva” mine, in the upper part of the earth’s surface, the depth is from 2.0–3.0 m to 20.7 m, in some places the height of the piles reaches 10–25 m. Mineral deposits in the mine belong to the group of eolian sands and are located in the form of mine plast. The color of the sand grains is light yellow and it belongs to quartz sand according to its composition [12-13] (Figure 1).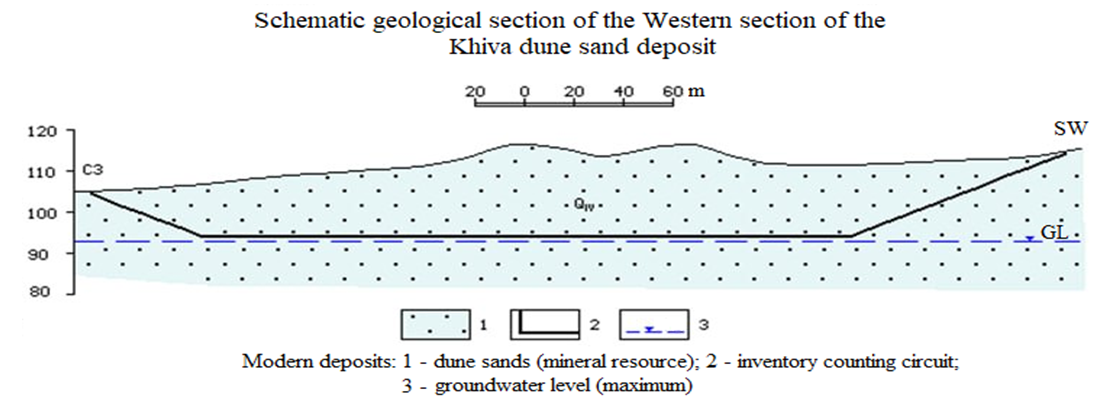 | Figure 1. The scheme of the geological section of the western division of the Khiva deposit |
The chemical and chemical–mineralogical composition of quartz sand of the Khiva mine was studied. It was found that the chemical composition consists mainly of silicon oxide up to 86.54 percent and there are also small amounts of aluminum, calcium, sodium potassium and iron oxides. The chemical composition is given below: SiO2–86.54; Al2O3–2.78; Fe2O3–1.25; CaO–1.50; MgO–0.32; K2O–1.72; Na2O–1.91; TiO2–0.02; SO3–0.50 and LOI 3.11.In order to determine the mineralogical composition of raw samples, X–ray phase analyzes were carried out (Figure 2).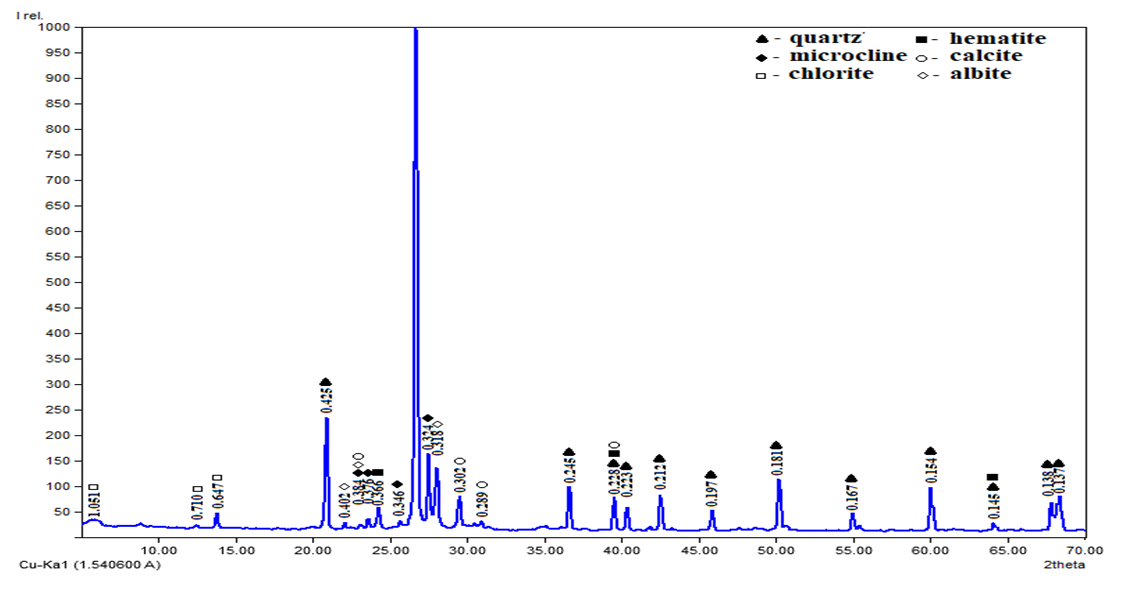 | Figure 2. X–ray of quartz sand sample |
The results of the X–ray phase analysis showed that quartz sand contains mainly quartz mineral diffraction lines (d=0.425; 0.334; 0.245; 0.228; 0.223; 0.212; 0.197; 0.181; 0.167; 0.138; 0.137 nm) and feldspar minerals (d=0.4 02; 0.384; 0.376; 0.346; 0.324; 0.318 nm). It was also determined that there are small amounts of hematite (d=0.366; 0.228; 0.145 nm), chlorite (d=1.051; 0.710; 0.647 nm) and calcite (d=0.302; 0.289; 0.228 nm) minerals with low intensity.According to the results of the analysis, it was found that these sands belong to the group of fine–grained quartz–feldspar sands, and the main mineral in the composition is high–grade oblong–cylindrical α–quartz. The main part of the examined Khiva sand quartz is transparent, its bulk density is 1.42–1.49 g/cm3, its actual density is 2.63 g/cm3, and the amount of grains larger than 5 mm in the sand content is up to 0.15%. It was determined that the amount of clay or dusty mixtures in the sample is equal to 25–26%. In the process of granulometric analysis, the residue on the 0.8 mm sieve was 1.61% and the residue on the 0.1 mm sieve was–0.11%. This indicator partially meets the requirements of GOST 22551–77.Based on preliminary studies, it was determined that enrichment of these sands is required to obtain colorless and transparent glass enamel frits from this raw material.In the process of beneficiation of quartz feldspar sand of the Khiva mine, studies were initially carried out using traditional technologies. Based on the results of the analysis, it was scientifically proven that the existing traditional technologies are not effective for this resource.Due to the specificity of the composition, it was found appropriate to use combinations of methods of enrichment– washing, gravity, classification (by size–0.8+0.1 mm), scrubbing, sorting in the electromagnetic field, flotation.The amount of the main components (SiO2, Al2O3 and Fe2O3) in the samples taken on the account of raw material enrichment was determined based on the established normative documents (Table 1).Table 1. The chemical composition of quartz sand obtained by enrichment of raw samples 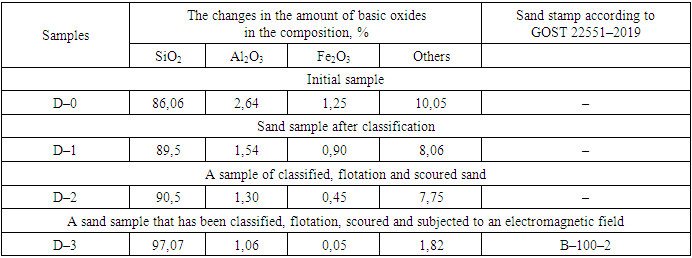 |
| |
|
Electron paramagnetic resonance (EPR) analyzes were conducted in order to determine the valency and coordination state of iron compounds in the sample sands (Figure 3).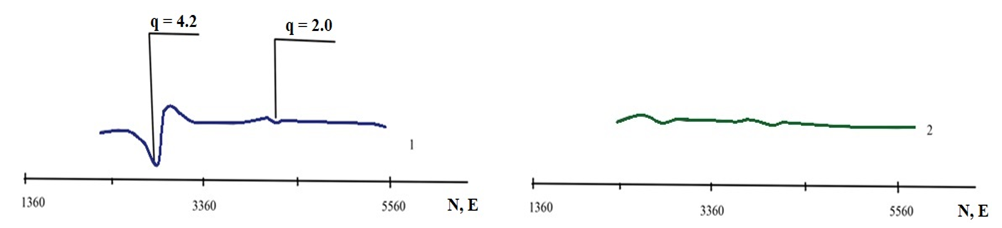 | Figure 3. The image of EPR analysis of Khiva quartz feldspar sands. 1–unenriched sample; 2–sample after enrichment |
It is known [14] that iron ions (Fe2+, Fe3+) in crystalline and vitreous solids are formed when the EPR spectrum lines have values of spectroscopic separation factors equal to q–2.0 and q–4.0. CdO–ZnO–Fe2O3–R2O3–SiO2 system glasses (where R–V, AI, Ga) and SaO–MgO–Fe2O3–SiO2 according to the results of the analysis, the lines in the interval q=4.1 χ÷4.3 are in the coordination state [FeO4] belongs to, and when q=2.0 it corresponds to octahedral groups [FeO6].The results of the analysis based on these given data were also consistent with the data presented in this source for the quartz sand of the Khiva mine under study. It was found that the intensity of the EPR lines was high in non–enriched sands, and decreased in intensity in enriched samples.X–ray phase analyzes of the sample taken as an object in the research work after enrichment of sands were carried out. The results of the analysis show that in these samples before enrichment (Figure 2), the intensity of diffraction peaks of minerals decreased, in particular, chlorite (1.051; 0.710; 0.647 d, nm), calcite (0.385; 0.303; 0.289; 0.228 d, nm), hematite (0.366; 0.228 and 0.145 d, nm) peaks were completely lost (Figure 4).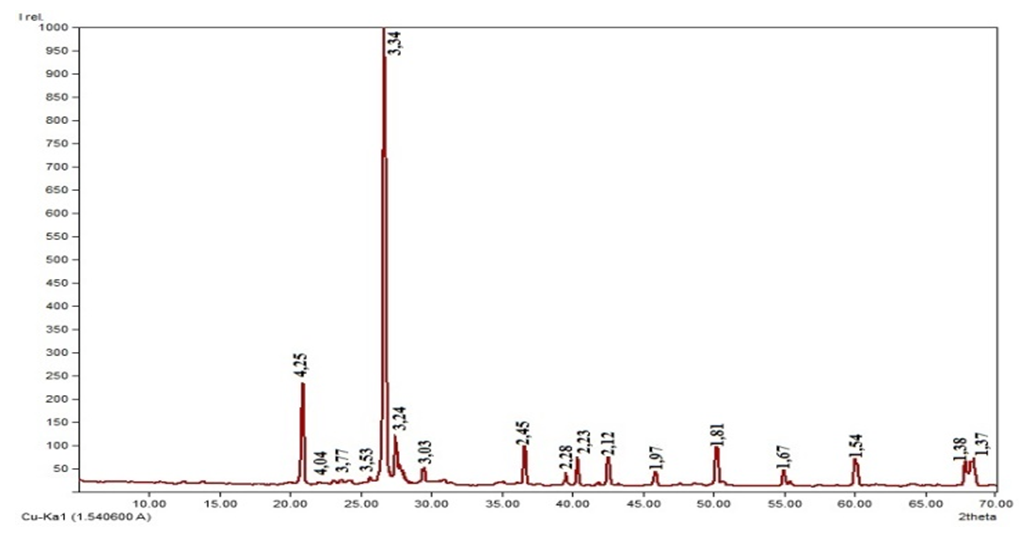 | Figure 4. X–ray image of an enriched sample quartz sand of Khiva deposit |
As a result of a large number of researches, a unique technology of beneficiation of Khiva quartz sand with optimal technological parameters has been developed.
4. Conclusions
The quartz sand of the “Khiva” mine was subjected to a comprehensive physical and chemical analysis. Based on complex physical and chemical analysis, it was found that quartz sand mainly belongs to quartz and feldspar, as well as a small amount of hematite, chlorite and calcite minerals. It was found that the chemical composition of quartz sand consists of 86–87% silicon oxide, but iron oxide, which has a negative effect on glass production, is up to 1.25%. Based on the selected enrichment technology, reduction of iron oxide from 1.25 to 0.05% and other harmful additives from 10.05% to 1.82% was achieved.
References
[1] | Harbek H. Optoelectronic separation in feldspar processing at Maffei Sarda. Aufbereitungs Technik, 2001. Vol. 42, No. 9. – p. 438–444. |
[2] | Shagiev I.I., Dresvyannikov A.F. Comprehensive assessment of the quality of sand for the glass industry. Bulletin of the Technological University, 2016. Vol. 19, No. 10. – p. 86–90. |
[3] | Artikhodzhaeva D.M. Mirkhodzhaev B.I. On the issue of the raw material base of quartz sands of the Republic of Uzbekistan and methods for studying their fraction using the example of the Dzheroy deposit. Journal of Economics, 2022. No. 2. – p. 34–35. |
[4] | Kovacec M., Pilipovic A., Stefanic N. Improving the quality of glass containers production with plunger process control Journal of Manufacturing Science and Technology, 2010. №3. – p. 304–310. |
[5] | Biryulev G.I., Gonyukh V.M., Bobrikov E.V., Kornilov A.V. Reference book “Mineral raw materials”. CJSC Geoinmark. Moscow, 1999. – p. 536. |
[6] | Babaev Z.K., Matchonov Sh.K., Buranova D.B., Iskandarov O.D., Ibodullayev B.O., Pirnafasov A.A. Conditions and Development of the Uzbekistan’s Glass Industry. International Journal of Advanced Research in Science, Engineering and Technology, 2018. Vol. 5, Issue 11. – p. 7270–7273. |
[7] | Pavlushkin N.M., Sentyurin G.G., Khodakovskaya R.Ya. Workshop on glass and ceramic glass technology–2nd ed. reworked and additional. – M.: Publishing house of literature on construction, 1970. – p. 512. |
[8] | Khomidov F.G., Kadyrova, Z.R., Usmanov Kh.L., Niyazova Sh.M., Sabirov B.T. Peculiarities of Sol–Gel Synthesis of Aluminum–Magnesium Spinel // Glass and Ceramics, 2021. Vol.78. – p. 251–254. |
[9] | GOST 22552.7–2019 “Quartz sand, ground sandstone, quartzite and vein quartz for the glass industry. Method for determining the granulometric composition”. – M.: Standardinform, 2019. |
[10] | GOST 13451–77 “Feldspathic and quartz–feldspathic materials for the glass industry”. Specifications (with Amendments No. 1, 2, 3, 4). – p. 24. |
[11] | GOST 22552.2–2019 “Quartz sand, ground sandstone, quartzite and vein quartz for the glass industry. Methods for determining iron oxide”. – M.: Standardinform, 2019. |
[12] | Dehler M. Optical sorting of ceramic raw materials. Tiles and Bricks International, 2003. Vol. 19, No 4. – p. 248–251. |
[13] | Harbek H. Optoelectronic separation in feldspar processing at Maffei Sarda. Aufbereitungs Technik, 2001. Vol. 42, No. 9. – p. 438–444. |
[14] | Brustolon M., Giamello E. Electron Paramagnetic Resonance. Practitioner’s Toolkit. Hoboken: John Wiley & Sons, Inc, 2009. – p. 553. |