Nobumitsu Shohoji1, Fernando Almeida Costa Oliveira1, José Galindo2, Jorge Cruz Fernandes3, José Rodríguez2, Inmaculada Cañadas2, Luís Guerra Rosa3
1LEN - Laboratório de Energia, LNEG - Laboratório Nacional de Energia e Geologia I.P., Lisboa, Portugal
2PSA - Plataforma Solar de Almería, CIEMAT - Centro de Investigaciones Energéticas, Medioambientales y Tecnológicas, Tabernas, Spain
3IDMEC- Instituto de Engenharia Mecânica, DEM - Departamento de Engenharia Mecânica, IST - Instituto Superior Técnico, UL - Universidade de Lisboa, Lisboa, Portugal
Correspondence to: Nobumitsu Shohoji, LEN - Laboratório de Energia, LNEG - Laboratório Nacional de Energia e Geologia I.P., Lisboa, Portugal.
Email: |  |
Copyright © 2019 The Author(s). Published by Scientific & Academic Publishing.
This work is licensed under the Creative Commons Attribution International License (CC BY).
http://creativecommons.org/licenses/by/4.0/

Abstract
Nitriding experiments for powder specimens of Mo and Fe were carried out using a solar furnace SF40 at PSA (Plataforma Solar de Almería) in Tabernas (Spain) in uncracked ammonia NH3 gas (NH3 gas with suppressed extent of dissociation by flowing) aiming at determining the range of linear velocity v of NH3 gas flow to yield higher nitride phases, δ-MoN for Mo and ε-Fe2N for Fe. Standard solar exposure duration at a specified reaction temperature T was set to be 60 min over range of v between 1.14 mm·s-1 and 11.4 mm·s-1. By X-ray diffraction (XRD) analysis, presence of δ-MoN was detected besides γ-Mo2N and metallic Mo for Mo powder specimen heated to 900 ºC in NH3 gas flow at v = 1.14 mm·s-1 but XRD peaks identifiable as δ-MoN became indiscernible when v was increased to 11.4 mm·s-1. On the other hand, for Fe powder specimen exposed to NH3 gas flow at v = 1.14 mm·s-1 at T = 500 ºC, remnant metallic α-Fe was detectable by XRD at the down-stream side of the specimen holder but no metallic α-Fe was detected at the up-stream side of the specimen holder suggesting that chemical activity a(N) of N atom in uncracked NH3 gas tended to decrease along the NH3 gas flow path on going from the up-stream side to the down-stream side.
Keywords:
Uncracked ammonia (NH3) gas, Concentrated solar energy, Temperature homogenizer, δ-MoN, ε-Fe2N
Cite this paper: Nobumitsu Shohoji, Fernando Almeida Costa Oliveira, José Galindo, Jorge Cruz Fernandes, José Rodríguez, Inmaculada Cañadas, Luís Guerra Rosa, Influence of Linear Flow Velocity of Uncracked Ammonia (NH3) Gas on Formation of Higher Nitrides, 𝛅-MoN and 𝛆-Fe2N, under Concentrated Solar Irradiation in the SF40 Solar Furnace at PSA, International Journal of Materials and Chemistry, Vol. 9 No. 1, 2019, pp. 1-12. doi: 10.5923/j.ijmc.20190901.01.
1. Introduction
On account of unique properties of nitrides of transition metals, intensive research efforts have been invested for nitride synthesis. Besides high hardness of metal nitride MN, some MN's are claimed to possess special functional properties. For example, Inumaru et al. [1] investigated aspects of high-pressure synthesis of δ-MoN in view of δ-MoN being a superconducting material. On the other hand, ε-Fe2N appears to be considered as a promising candidate material for anode in lithium ion battery [2, 3].Generally, synthesis of nitride MN through reaction of metal M in N2 gas atmosphere requires high temperature due to high chemical stability of N2 gas molecules. Synthesis of "higher" nitride such as δ-MoN of Mo cannot be realized in N2 gas environment even at very high N2 gas partial pressure p(N2) of order of several hundreds of atm for prolonged reaction duration of several tens of hours [1, 4-16].One of optional routes for synthesizing higher nitride of metal M by reaction at normal pressure is the use of uncracked NH3 gas as a powerful nitriding medium [4, 5, 7, 8, 10-22]. Uncracked NH3 is a stream of NH3 gas whose degree α of dissociation is suppressed from the degree of dissociation αeq under equilibrium state in a closed reaction chamber | (1) |
Inherently unstable nature of uncracked NH3 gas leads to the following two characteristic features on its usage as a nitriding medium;<1> at a specified spot in the reactor set at temperature T, extent α of dissociation of uncracked NH3 is determined as a function of its linear flow velocity v, <2> along the NH3 gas flow path at any given T, α would increase steadily on going from up-stream side to down-stream side.That is, nitriding power of uncracked NH3 gas determined by the chemical activity a(N) of uncracked NH3 gas molecule tends to decrease with decreasing v at a given T and, even at given v and T, a(N) of uncracked NH3 gas tends to decrease along the flow path on going from up-stream side to down-stream side on account of increasing α (i.e. decreasing partial pressure p(NH3) of NH3 gas). In other words, even at given experimental conditions of T and v, a(N) of uncracked NH3 gas would decrease steadily along the flow path on going from inlet side to outlet side of the reaction tube. This trend was experimentally demonstrated by Nishimaki et al. [14] as decreasing N content in hypo-stoichiometric ε-Fe2N phase synthesized in NH3 gas stream at 550 ºC along the flow path over about 4 cm length. In the preceding works using uncracked NH3 gas as a nitriding medium under irradiation of concentrated solar beam, synthesis of nitride MN was detected for transition metals including Ti, Zr, V, Nb, Ta, Cr, Mo and W and also for Fe [7, 8, 21, 23]. However, these results were obtained using a spherical reactor made of Pyrex glass in which NH3 gas flow pattern was unknown. In these preliminary works of nitriding group of transition metals in stream of NH3 gas, metal specimens were in form of compacted pellet in order to carry out the test runs with minimized risk of cross-contamination among specimen materials within the limit of designated solar beam time for users. In the recent experimental campaign carried out in September/October 2017 at PSA using SF40 for nitriding Mo and Fe powder specimens, specially designed tubular silica glass furnace and steel specimen holder were used to look into influences of v of NH3 gas stream and of specimen position along the NH3 gas flow path on phases synthesized. Range of linear NH3 gas flow velocity v tested was between 1.14 and 11.4 mm·s-1 that corresponded to volumetric flow rate of 0.08 and 0.83 L·min-1, respectively, in the used experimental setup. Steel specimen holder was drilled with 4 holes of diameter 8 mm and depth 5 mm to hold powder specimens of Mo or Fe and these 4 holes were designated with P1 at up-stream side of NH3 gas stream to P4 at down-stream side. The distance between the central spot of P1 and the central spot of P4 was 45 mm.Test results acquired for nitride synthesis for Mo and Fe in stream of NH3 gas under irradiation of concentrated solar beam are summarized in this report.
2. Experimental
2.1. Sample Materials
The molybdenum (Mo) powders of nominal purity 99.9% and median particle size 2 μm were supplied from Goodfellow (UK) and the Fe powders of nominal purity 99.9% were supplied from Alfa Aesar, now part of Thermo Fisher Scientific Inc. (USA), defined as “sponge” product with a density of 7.86 g·cm-3 and a particle size < 100 mesh (150 μm). Ammonia (NH3) gas used was with purity 99.8% (H2O < 0.1 ppb) and N2 gas with purity 99.998% (H2O < 3 ppm; O2 < 5 ppm), both supplied from Carburos Metalicos (Air Products) S.A. (Spain).
2.2. Experimental Setup and Procedure
The nitriding experiments were carried out using SF40 solar furnace, with nominal power output 40 kW, at PSA (Fig. 1) whose detailed performance characteristics might be referred to elsewhere [24]. At the focal spot of the concentrated solar beam, the radiative flux reaches 7000 Suns (1 Sun = 1 kW∙m-2).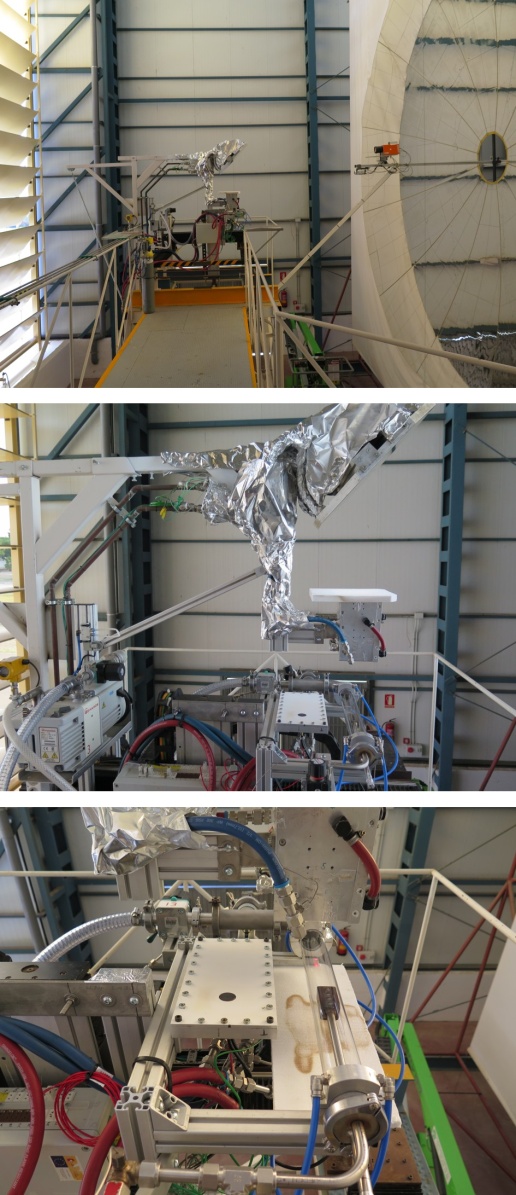 | Figure 1. Experimental setup used for nitriding Mo and Fe powders in uncracked NH3 gas under heating with concentrated solar beam in SF40. <top> Overall view with the solar beam concentrator at the right hand side, the test table at the middle and louvered shutter on the left hand side. <middle> Detail of test table showing the tilted mirror (top center) together with homogenizer (below mirror) and reaction tube (bottom). <bottom> Close-up view of the reaction tube showing sample holder below secondary concentrator |
Constitution of the gas feed line was basically the same as the one integrated in the SF5 furnace [25] used for the earlier nitriding experiments in uncracked NH3 gas [7, 8, 21, 23].The amount of sunlight incident on the concentrator (shown at right hand side edge of top picture of Fig. 1) and therefore the radiative flux was controlled by the angular motion of the louvered shutter salts (shown at left hand side edge of top picture of Fig. 1). Moreover, a tilt mirror (45º; shown at the middle of upper edge of middle picture of Fig. 1) was used to perform these tests in a horizontal plane, which turned 90° the focal beam and projected the concentrated solar beam onto the specimen holder.The reactor consisted of a standard 2.5 mm thick silica glass tube with inner diameter 45 mm and length about 1000 mm. Both ends of the silica tube were sealed with water-jacketed vacuum flanges to guaranty gas-tightness to avoid undesirable NH3 leaks to and O2 impurity penetration from external atmospheric environment. The sample holder was specially designed and manufactured using a refractory steel. As shown in Fig. 2, four cylindrical holes (diameter 8 mm and depth 5 mm) were drilled to contain the powders of Mo or Fe to be nitrided. For exact temperature control, eight K-type thermocouples inserted through SUS316 stainless steel tube of diameter 1 cm from down-stream side of silica glass reactor tube (cf. bottom picture of Fig. 1) were set at both the top and bottom planes of the powder samples (T1 ~ T8), as illustrated schematically at the bottom of Fig. 2. For allocation of the thermocouples, 2 mm holes were drilled to about 1 mm depth from the bottom of the 4 holes for holding powder specimens (T1 ~ T4) and to about 1 mm depth from the top surface (T5 ~ T8) of the sample holder top surface. A 2 mm thick plate of the SUS316 steel was welded to the bottom of the sample holder to inhibit contact of the thermocouples with the NH3 gas. 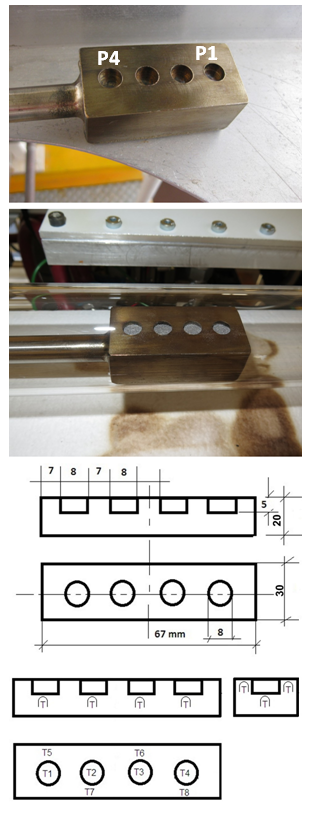 | Figure 2. Powder specimen holder made of refractory steel. <top> Sample holder prior to preliminary nitriding in NH3 gas. P1 at up-stream side and P4 at down-stream side of the NH3 gas flow. <middle> Appearance with the specimen powder after nitriding test run; <bottom> Schematic of the holder showing its dimensions and positions of 8 thermocouples, T1 ~ T8, allocated in the specimen holder; Distance between the center of P1 and the center of P4 was 45 mm |
In addition, heat flux measurements were carried out using a Gardon type radiometer ThermoGage TG1000-1, supplied from Vatell Corporation, with 0 ~ 6469 kW·m-2 range. Typically, at 900°C, radiometer reading fell around 300 kW·m-2, whereas at 600°C, the values obtained were around 115 kW·m-2.Temperature homogeneity covering the entire specimen holder area was achieved by the integration of a newly developed temperature homogenizer in the path of the concentrated solar beam (Fig. 3). Temperature difference among the 8 K-type thermocouples fell in the range of ±5°C (at 500°C) or ±10°C (at 900°C) throughout test runs, E01 ~ E10 (Table 1) as seen in Fig. 4. This is a remarkable achievement in view of the fact that, in a previous study on temperature homogeneity in solar furnace [26], it was observed that the temperature profile around the focal spot of the concentrated beam was Gaussian yielding radial temperature difference between the focal spot centre and the focal spot periphery (e.g., 80°C at 1073 K measured using an AISI 310 plate receiver). Even through indirect heating using a primitive design of temperature homogenizer, results demonstrated temperature drop of around 50°C along the height beneath the top graphite disc (serving as receiver of concentrated solar beam) and the bottom sample holder [27]. Therefore, in order to achieve a more uniform temperature distribution throughout the test samples being exposed to the solar beam, a secondary concentrator consisting of a tronco-conical mirror kaleidoscope of square shape (around 127 mm top aperture and 105 mm in the bottom side, respectively) with height 250 mm, hereafter called simply as temperature homogenizer, was placed over the tubular reactor (Fig. 3).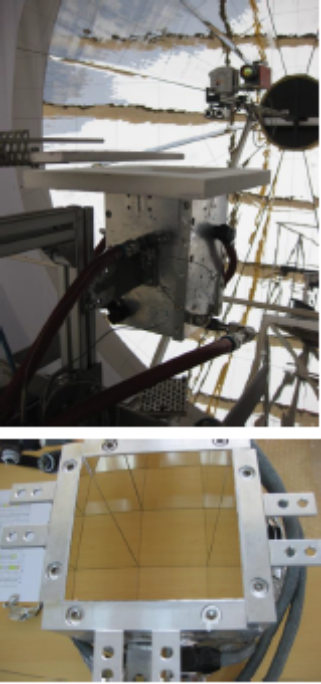 | Figure 3. Appearance of temperature homogenizer. <top> General view from the side against the background solar beam concentrator. <bottom> Bird's eye view looking down the interior mirror surface. Dimension of the temperature homogenizer is height 250 mm, top opening edge length 127 mm and bottom opening edge length 105 mm |
Table 1. List of test conditions carried out at PSA in September/October 2017 for Mo and Fe powder specimens in stream of NH3 gas (uncracked NH3) under irradiation of concentration solar beam. Test runs for Fe powder specimens were shaded 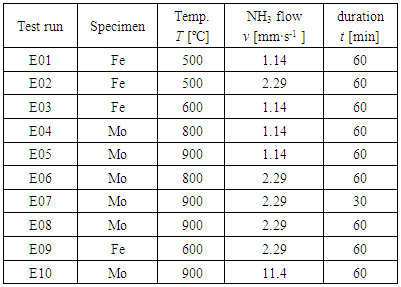 |
| |
|
By insertion of the temperature homogenizer, not only improvement of the planar homogeneity of the temperature of the focal spot but also minimization of the time fluctuation of the arbitrary spot in the focal area was achieved as evident from the comparison between T profiles reproduced in Fig. 4 in this work with temperature homogenizer and the ones detected under similar solar irradiation experiments using SF5 solar furnace at PSA without temperature homogenizer reported earlier (Fig. 3 in [7]; Fig. 1A in [21]). Careful readers might notice in the T vs. t profiles of Fig. 4 that, during heating period, heating was arrested for about 5 min at T = 200°C. This was to ensure removal of surface oxide layer over metal powders making use of high hydriding power of uncracked NH3 gas at relatively low T [13, 20, 22, 28]. 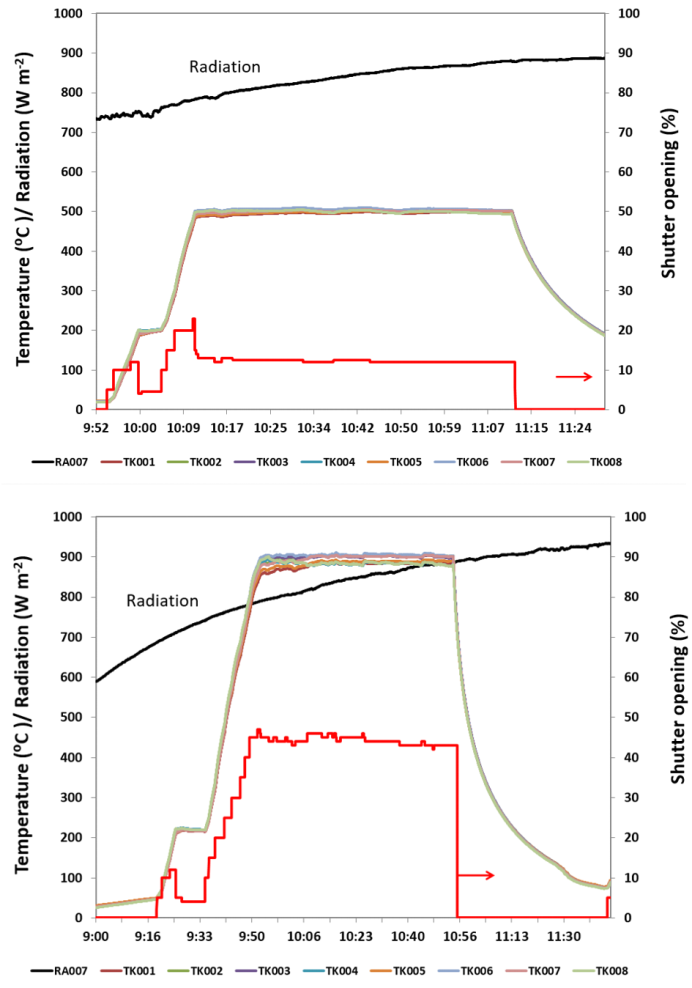 | Figure 4. Typical thermal cycles used for nitriding Fe at 500°C and Mo at 900°C under uncracked NH3 gas together with shutter opening required to control temperatures in each case. In the legend, RA007 refers to solar radiation whereas TK001~TK008 refer to K-type thermocouples |
High degree of homogeneity of temperature over the specimen holder along the NH3 gas flow path is seen in infra-red (IR) video image reproduced in Fig. 5. 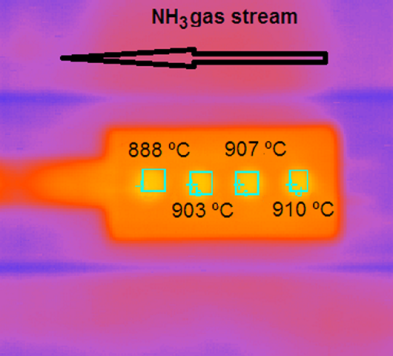 | Figure 5. Snapshot IR video image of the sample holder together with the registered temperatures by K-thermocouples at the indicated locations |
Eleven test runs were carried out during the 10-working day campaign (from 25th September to 6th October, 2017; one preliminary nitriding run for sample holder was not registered in Table 1). Nitriding of Fe powders were performed at 500 and 600°C for 60 min under flowing NH3 controlled by a variable-area flow meter (VAF-M1-01M-1-0) supplied from Swagelok (USA). Similar conditions were used for nitriding Mo powders at temperatures, 800 and 900°C. Prior to the test run E01, the refractory steel sample holder was subjected to preliminary nitriding at 500°C for 30 min in NH3 gas stream at v = 1.14 mm·s-1 to minimize influence of fresh steel surface on extent α of dissociation of NH3 gas in the E01 test run and thereafter. In fact, it is well established that exposure of Fe parts to NH3 results in the formation of a surface nitride layer which protects the steel material from further nitriding (e.g. [13]). After setting the powders to the refractory steel sample holder, the reactor was evacuated to 0.18 mbar by rotary vacuum pump at ambient temperature and then filled with pure nitrogen (N2) gas for flushing. This operation was repeated three times before introducing flowing ammonia (NH3) gas to the reaction chamber at ambient temperature. Powders were then heated under flow of NH3 gas to a specified reaction temperature T for specified duration t. After completion of the reaction of duration t at temperature, gas was changed from NH3 to N2 (flowing at 5 L·min-1 maintaining the temperature at T for 5 min). This was to ensure full substitution of the reaction chamber environment to N2 gas from NH3 before starting to cool down. This precaution to substitute gas from NH3 to N2 at the onset of cooling immediately after the end of the nitriding reaction was taken to minimize loss of N from the nitrided specimen surface during cooling. X-ray diffraction (XRD) analysis was performed using a Panalytical XPert Pro MPD diffractometer in the Bragg -Brentano configuration. The data were collected with a step size of 0.02° using an X’Celerator 1D detector with CuKα radiation. 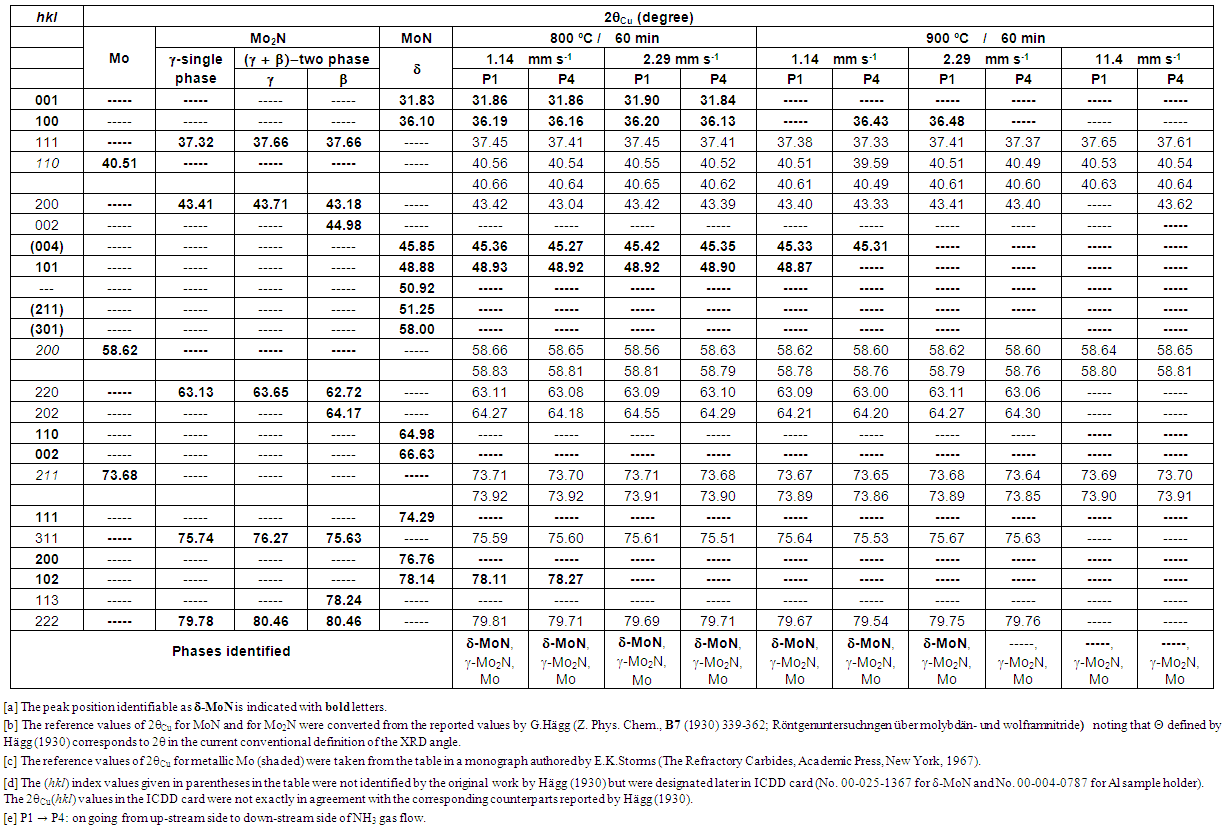 | Table 2. XRD (X-ray diffraction) peak positions (CuKα) detected for Mo specimens exposed to stream of NH3 gas flow under irradiation of concentrated solar beam for 60 min with identification of phases being compared with reference peak positions for Mo, Mo2N (β and γ) and δ-MoN phases |
3. Results and Discussion
3.1. Mo
XRD peak positions obtained for Mo specimens in uncracked NH3 gas at different linear flow velocity v through the reaction tube at T = 800 and 900 ºC for duration t = 60 min are listed in Table 2 being compared with standard peak positions for δ-MoN, two types of Mo2N (β and γ) and metallic Mo. XRD patterns for Mo specimens placed at P1 position after 60 min exposure to uncracked NH3 gas at T = 900°C are compared in Fig. 6 between the condition with v = 11.4 mm·s-1 (top) and the condition with v = 1.14 mm·s-1 (bottom).As seen in Table 2, at T = 800°C at either v = 1.14 or 2.29 mm·s-1 at both P1 and P4 positions, reaction products were consisted of 3 phases composed of δ-MoN, γ-Mo2N and metallic Mo. This result is consistent with the earlier result obtained in uncracked NH3 gas with unknown v under heating with concentrated solar beam to T = 800°C [7, 8]. In these two early works using concentrated solar beam as the reaction heat source, linear flow velocity v was not specified because the reaction chamber was spherical. Anyway, in conventional electric furnace (that is, under absence of light wave components), δ-MoN became undetected when T exceeded 725°C (XRD pattern shown as Fig. 3 in [5]). The work reported by Yoshizawa et al. [5] was carried out in conventional laboratory electric furnace in stream of NH3 gas at v = 4.3 mm·s-1 for reaction duration t = 20 h. Thence, it was felt quite amazing that δ-MoN was detected in the reaction product of Mo with uncracked NH3 gas at T = 800°C in the preceding work carried out under solar irradiation heating although with unspecified v [7, 8]. In this work, validity of presence of δ-MoN was confirmed at T = 800°C at both v = 1.14 and 2.29 mm·s-1 under solar irradiation heating condition implying that solar irradiation was favourable for raising upper threshold temperature T for formation of δ-MoN. 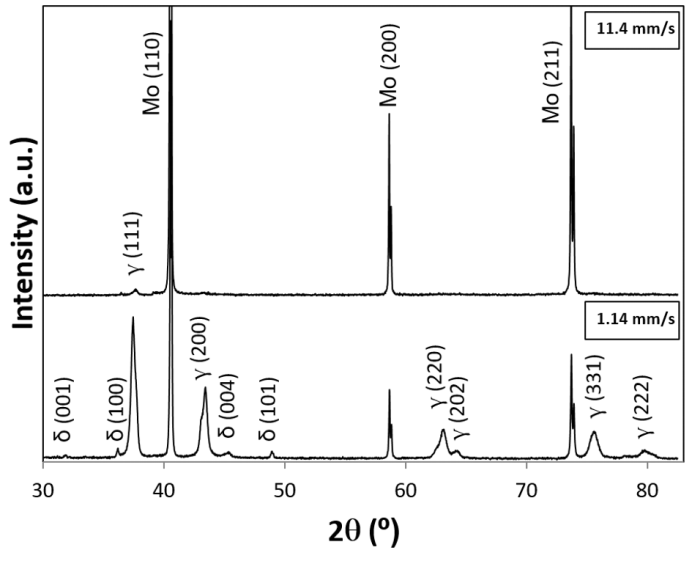 | Figure 6. XRD patterns for Mo specimens after exposure to uncracked NH3 gas at 900 ºC for 60 min at different NH3 gas flow velocity v. <top> at v = 11.4 mm·s-1 (Run E10 at P1). <bottom> at v = 1.14 mm·s-1 (Run E04 at P1). Note that, at v = 11.4 mm·s-1, nitriding to δ-MoN failed to proceed while, at v = 1.14 mm s-1 at both P1 and P4 positions, XRD peaks identifiable as δ-MoN were detectable, although very weak, besides those identifiable as γ-Mo2N and metallic Mo |
As such, although the mechanism of pushing up the upper threshold T for δ-MoN formation remains unknown, experimental evidence points out clearly that presence of concentrated solar beam wave components besides infra-red (IR) heating effect contributed somehow towards synthesis of higher nitride δ-MoN. When v was increased to 11.4 mm·s-1 at T = 900 ºC with the intention of raising a(N) by suppression of dissociation of NH3 gas to promote formation of δ-MoN, effect was adversary to cease yield of δ-MoN in the reaction product (Table 2 and Fig. 6). This was somewhat surprising in view of v-dependence of a(N) but might be understood rationally in view of stability of adsorption of NH3 molecules onto Mo particles surface. For nitriding reaction of Mo to be initiated by adsorbed NH3 molecules, NH3 molecules must reside sufficiently long duration over Mo surface. It is suspected that, at v = 11.4 mm·s-1, the residence time of NH3 molecules onto Mo surface was cut short and penetration of N atoms to Mo matrix failed to take place. Thus, certain upper threshold v for realization of nitriding reaction must be defined. Judging from the results of this work, it must be no faster than 10 mm·s-1.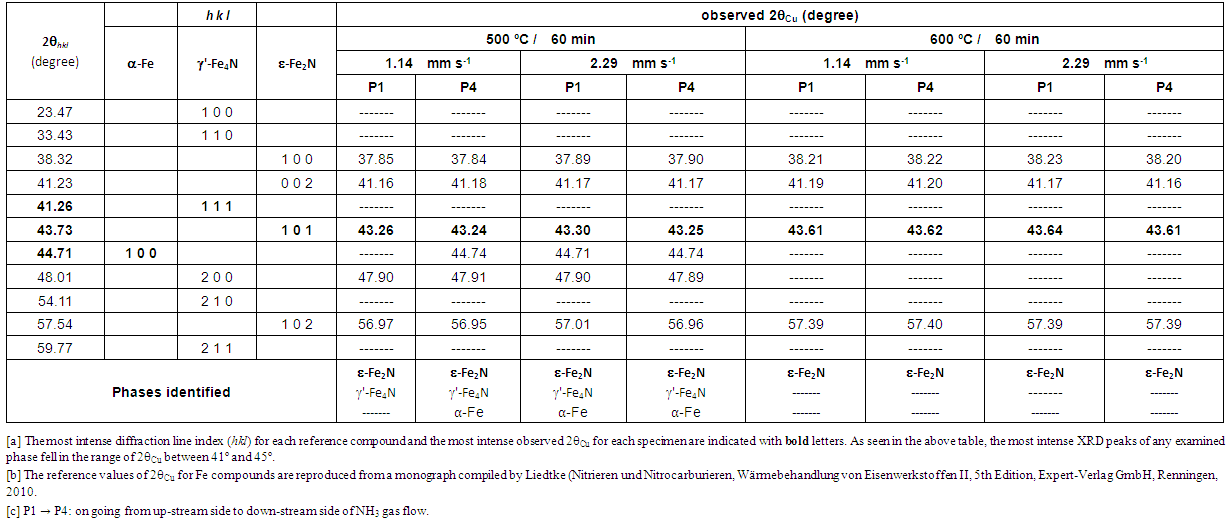 | Table 3. XRD (X-ray diffraction) peak positions (CuKα) detected for Fe specimens exposed to stream of NH3 gas flow under irradiation of concentrated solar beam for 60 min with identification of phases being compared with reference peak positions for α-Fe, γ´-Fe4N and ε-Fe2N phases |
In the nitriding experiment using uncracked NH3 gas at v = 4.3 mm·s-1 (corresponding to volumetric flow rate 200 mL·min-1), nitriding process for Mo proceed all right in a conventional electric furnace with silica reaction tube [5].Thus, the upper threshold level of v for realization of nitriding in NH3 gas stream must be somewhere between 5 and 10 mm·s-1.Looking at results for Mo specimen nitrided using NH3 stream at v = 2.29 mm·s-1 at 900°C (Table 2), small XRD peak referring to δ-MoN (100) remained detectable at P1 position (up-stream side) but, at P4 position (down-stream side), no XRD peak identifiable as δ-MoN was detectable. Thus, at v = 2.29 mm·s-1 at 900°C, nitriding power of uncracked NH3 gas became insufficient to yield δ-MoN in the down-stream side provided that surface coverage rate of Mo powders with uncracked NH3 gas was determined as a function of v along the gas flow path. Thus, judging from the results summarized in Table 2, optimum T for nitriding with uncracked NH3 gas must be 800°C which is by about 100°C higher than the upper threshold T for δ-MoN synthesis in conventional electric furnace under absence of light wave components. Accordingly, use of concentrated solar beam as the reaction heat source for higher nitride formation for Mo in uncracked NH3 gas environment was concluded beneficial in view of acceleration of the reaction rate through increasing T without causing dissociation of δ-MoN like in the experiment in a conventional laboratory electric furnace at T ≥ 725°C [4,5].In this experiment, lower threshold v was not determined due to limitation of minimum NH3 gas flow rate reading of the used variable-area flow meter. It is guessed that the lower threshold v for higher nitride formation for Mo might fall in a range between 0.1 and 1 mm·s-1. In view of realization of nitriding with minimized resource consumption (in this case, amount of NH3 gas spent for the nitriding reaction), determination of lower threshold v is of pragmatic industrial importance than determination of higher threshold v. Anyway, it must be kept in mind that such threshold v values determined experimentally is valid only to a specific experimental setup and not as universally acceptable experimental parameter values. For example, the present experimental setup was made with transparent silicate glass tube furnace with steel specimen holder while that used by Yoshizawa et al. [5] was made with quartz tube furnace with alumina specimen holder. Depending on these reactor components, extent of dissociation of NH3 gas might be affected.
3.2. Fe
Literature information [7, 10-15] demonstrated that synthesis of ε-Fe2N through reaction at normal pressure can be realized only by use of uncracked NH3 but not in N2 gas environment. According to XRD results for Fe specimen summarized in Table 3, optimum reaction T for synthesis of ε-Fe2N in uncracked NH3 gas must be 600°C under irradiation with concentrated solar beam in the present experimental setup. In the preceding report [7], reaction product from Fe pellet specimen was consisted of ε-Fe2N co-existed with γ'-Fe4N by nitriding in uncracked NH3 gas at 600°C under solar irradiation heating in spherical quartz glass reactor. This would mean that a(N) of uncracked NH3 gas at the spot of Fe pellet must have been dropped to a level insufficient to yield single-phase ε-Fe2N in the earlier work [7]. In the preceding experiment [7], 11 compacted disc specimens were exposed to uncracked NH3 gas in a spherical Pyrex glass reactor chamber in which flow pattern of NH3 gas was unknown. Disc specimens were used in that work to carry out maximum number of nitriding experiments in uncracked NH3 gas without risking cross contamination among specimens of unlike metals. Increased number of specimens might have resulted in promoted dissociation of NH3 to lead to drop of p(NH3) and resultant decrease of a(N) to a level insufficient to yield single-phase ε-Fe2N. 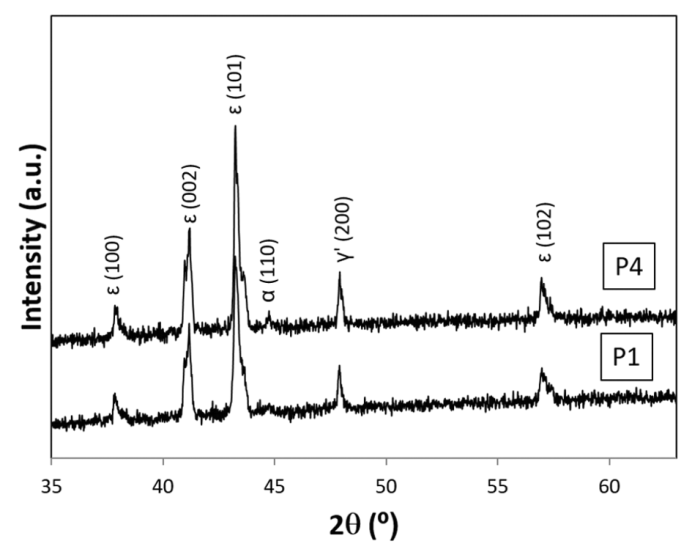 | Figure 7. XRD patterns for Fe specimens after exposure to uncracked NH3 gas at 500 ºC for 60 min at NH3 gas flow velocity v = 1.14 mm·s-1 (Run E01) at P1 (bottom) and at P4 (top). Note that, at down-stream side (P4), weak XRD peak identifiable as α-Fe (110) was detectable while this peak was not detectable at up-stream side (P1) |
It is intriguing to note in Table 3 and in Fig. 7 that, under nitriding with uncracked NH3 gas at v = 1.14 mm·s-1 at 500°C under irradiation of concentrated solar beam, remnant of metallic α-Fe was detected at P4 (down-stream side) but not at P1 (up-stream side) implying gradual decrease of a(N) of uncracked NH3 along the NH3 gas flow path. This trend was clearly demonstrated experimentally by Nishimaki et al. [14] for hypo-stoichiometric ε-Fe2N. At v = 2.29 mm·s-1 in which a(N) at the corresponding spot along the NH3 gas flow path was anticipated to be higher than that at v = 1.14 mm·s-1, remnant of α-Fe was detected at P1 as well as at P4. This seemed a bit queer with reference to a(N) alone but, as pointed out earlier in the text referring to Table 2 and Fig. 6 for the nitriding reaction for Mo specimen, the first step of nitriding process is the adsorption of NH3 gas molecules onto the metal surface. The faster the NH3 gas flow rate, the higher the likelihood of removal of once adsorbed NH3 gas molecules from the metal surface. Thus, it was speculated that rate of coverage of Fe surface by adsorbed NH3 molecules might become lower with v = 2.29 mm·s-1 than with v = 1.14 mm·s-1. Thus, on undertaking experiment using inherently unstable uncracked NH3 gas molecules as a nitriding medium, it must be remembered that nitriding efficiency is dependent on density of surface coverage with adsorbed NH3 molecules (this would tend to decrease with increasing v) as well as on a(N) (this tends to increase with increasing v) and thence the optimum v might be determined for specific configuration of the experimental setup. For example, when adequate catalytic substance is discovered for promoting re-combination of N2 and H2 to yield NH3, high a(N) of uncracked NH3 gas might be held at a level satisfactorily high to yield higher nitride phase in the reaction product even at slow v.
3.3. Merits and Limitations of Using Uncracked NH3 Gas as a Nitriding Agent
In this work, merits of using uncracked NH3 gas as a nitriding medium for metals, that are difficult to be converted to higher nitride, δ-MoN and ε-Fe2N, through reaction with N2 gas, were demonstrated under condition of heating with concentrated solar irradiation (see also [7, 8]). Compared with VIa-group metals (Cr, Mo and W), IVa-group metals (Ti, Zr and Hf) and Va-group metals (V, Nb and Ta) are relatively easily nitrided to yield mono-nitride MN straight away from M in N2 gas under normal pressure at T higher than 1200°C and thence it is not a common habit to use uncracked NH3 gas as a nitriding medium for IVa- and Va-group metals. However, in recent works using solar furnace as a source of reaction heat, low temperature nitriding of IVa- and Va-group metals in uncracked NH3 gas was attempted [21, 23]. These works were done noting the empirical knowledge that presence of partially nitrided metal MNx (x < 1) being mixed with M in the starting material is favourable for minimizing dimensional distortion of final consolidated nitride ceramic component on production from compacted powder by self-propagating combustion synthesis (cf. for example, Gromov and Chukhlomina [9]). Results of the work of low temperature nitriding of IVa- and Va-group metals in uncracked NH3 gas under solar irradiation heating showed that, in spite of relatively low reaction temperature (< 1000°C), evidence of progress of partial nitriding was detected [21, 23]. Such partially nitrided powders might be accepted as a starting material for near-net shape production process by self-propagating combustion synthesis. In the following, merits and problematic aspects of nitriding using uncracked NH3 gas as a nitriding agent are reviewed.Uncracked NH3 gas is inherently an unstable substance and accordingly its extent α of dissociation (cf. Eq. (1)) is determined basically as functions of temperature T and linear flow velocity v of NH3 gas. However, even in a given experimental setup, α would not hold constant along the NH3 gas flow path showing steady rise of α along the flow path and resultant steady decrease of a(N) of uncracked NH3 gas on going from up-stream side to down-stream side. This characteristic of flowing NH3 gas was experimentally demonstrated by Nishimaki et al. [14] as steady decrease of N content in synthesized hypo-stoichiometric ε-Fe2N evidenced by lattice parameter change along the NH3 gas flow path determined by XRD analysis (Fig. 3 in [14]). Accepting isothermal expression for a(N) of uncracked NH3 gas drawn by Katsura [28] on the basis of thermodynamic consideration given as functions of p(NH3), p(H2) and Kp, the expression for a(N) is eventually represented as functions of extent α of dissociation of NH3 gas and Kp at arbitrary T | (2) |
where Kp refers to equilibrium constant for formation of 1 mole of NH3 gas from 1/2 mole of N2 gas and 3/2 mole of H2 gas.On the other hand, isothermal expression for a(H) of uncracked NH3 gas at arbitrary T as functions of α and Kp is drawn likewise 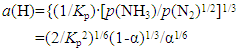 | (3) |
Isothermal a(N) vs. α relationships and isothermal a(H) vs. α relationships are exhibited graphically in [20, 22, 28-31] demonstrating very high extent of a(N) enhancement and modest extent of a(H) enhancement through retardation of dissociation of NH3 gas. Indirect evidence of high power of hydriding of uncracked NH3 gas was demonstrated experimentally by Shohoji et al. [13] on surface nitriding of steel ingot block specimen in which surface nitriding layer of homogeneous thickness was detected for the test pieces heated in NH3 gas flow from the beginning of heating from ambient temperature till the end of t hour reaction at 500°C and then cooled down in N2 gas flow (AN-t specimens in the designation in [13] whereas surface nitriding failed to proceed for the steel ingot specimen heated in flow of N2 gas from ambient temperature to the reaction temperature and NH3 was introduced only when the reaction temperature 500°C was reached (NA-t specimens). This difference between AN-t and NN-t specimens appeared to indicate that surface oxide layer was not removed from the steel block specimen during heating in N2 gas environment (NA-t specimen) whereas surface oxide layer was removed during heating in NH3 gas (AN-t specimen) to allow nitridation at the reaction temperature 500°C. On the other hand, the steel ingot specimen heated from ambient temperature to 500°C in NH3 gas stream, held at this reaction temperature for t hours and cooled down in NH3 stream (AA-t specimens) showed certain extent of N loss from the surface compared with that in the AN-t specimen at the comparable t suggesting that N removal from the specimen surface took place during cooling in NH3 gas stream down to ambient temperature. Thickness of surface nitrided layer in the AA-t specimen became irregular while that in the AN-t specimen was homogeneous (cf. Table 2 and Fig. 3 in [13]).As such, uncracked NH3 gas at relatively low temperature (probably < 300°C) would act as a hydriding agent rather than a nitriding agent. Therefore, on undertaking nitriding of metal in uncracked NH3 gas, it is of essential importance to start NH3 gas flow from the beginning of heating from ambient temperature to ensure removal of surface oxide layer from the specimen to be nitrided during the heating process to the reaction temperature. On the other hand, when the reaction in uncracked NH3 gas at specified temperature is finished, nitrided specimen must be cooled down in N2 gas as fast as possible. When NH3 gas is continued to be flown during the period of cooling down to ambient temperature, undesired loss of N from the nitrided specimen would proceed on account of high hydriding power of uncracked NH3 gas at relatively low T. Likewise, it was demonstrated by Katsura and co-workers [17-19] that N-enriched hyper-stoichiometric sesqui-nitride α-U2N3+x of uranium (U) possessing x value that could not be formed in N2 gas environment was synthesized in uncracked NH3 gas environment at normal pressure. On nitriding of metal powders using uncracked NH3 gas as a nitriding medium, excessive refinement of powder particles size does not seem to be favourable. Indeed, Nishimaki et al. [15] reported that, at comparable flow rate ~20 mL·min-1 at T = 550°C, ε-Fe2N was synthesized from coarse Fe particles with mean diameter 150 μm (estimated α = 0.01 to yield a(N) = 4 × 104) but γ'-Fe4N formed from fine 10 nm Fe particles (estimated α = 0.30 to yield a(N) = 3.6 × 102). Drop of a(N) by 2 orders of magnitude with fine 10 nm Fe particles from that with coarse 150 μm Fe (Table 1 in [15]) was interpreted to be caused by extensiveness of effective surface area of 10 nm Fe particles compared with that of 150 μm Fe particles. As such, even starting material's surface condition might modify α and resultantly a(N) of uncracked NH3 gas. In fact, in the preceding work of nitriding of Fe particles at 550°C in uncracked NH3 gas under concentrated solar irradiation heating [7], some results were a bit puzzling; after reaction duration t = 30 min, the reaction product was single-phase ε-Fe2N but, when t was prolonged to 90 min, the reaction product was reduced down to single phase γ'-Fe4N (Table 3 in [7]). This might be interpreted as follows; a(N) in uncracked NH3 gas at early stage of the reaction (t ≤ 30 min) was high enough to convert Fe powders to single-phase ε-Fe2N but the formed ε-Fe2N promoted dissociation of NH3 gas to lead to decrease of a(N) of the uncracked NH3 gas to turn the reaction product to single-phase γ'-Fe4N at t = 90 min. This aspect requires further experimental verification to validate reproducibility. Anyway, such somewhat queer t-dependence of reaction product constitution formed in uncracked NH3 gas environment appeared to warn of interactive nature of uncracked NH3 gas with reaction product itself as well as with reactor tube surface and sample holder. Keeping this aspect in mind, preliminary nitriding of the refractory steel sample holder was done in NH3 gas stream without the sample powders prior to E01 test run (Table 1) as a precaution to avoid uncontrolled influence of NH3 dissociation mode affected by nitriding process of sample holder on the target reaction of Fe nitriding in the E01 test run. Sample holder with bronze surface colour shown in the picture second from the top in Fig. 2 was the one after being subjected to preliminary surface nitriding in NH3 flow 1.14 mm·s-1 at 500 ºC for 30 min. The surface colour of the initial state of the refractory steel sample holder was whitish silver. Noting these realities with regard to use of inherently unstable uncracked NH3 gas as a nitriding medium, it must be kept in mind that α and thence a(N) cannot be considered as a universal experimental parameter dependent largely on T and v alone for different experimental setup and sample material. The lower and upper v levels set for a given T and for a specified sample material in a given reactor system are quite likely to change in another reactor setup. On nitriding process using uncracked NH3 gas as a nitriding medium, there is no risk of introduction of impurity H atoms into the synthesized metal nitride. Temperature window for stability of metal hydride lays is incomparably lower range than that for stability of metal nitride. Anyway, on account of modestly enhanced a(H) of uncracked NH3 gas molecules at relatively low T (< 300°C), reduction of surface scale layer existing over the metal powders used as the starting material would proceed during heating in NH3 gas flow [13, 28, 31]. To ensure reduction removal of surface oxide layer by action of H in uncracked NH3 gas, deliberate T arrest at 200°C for about 5 min was arranged during heating (cf. Fig. 4). It is also speculated that, for nitriding of metal using uncracked NH3 gas, modest grade of NH3 gas containing certain H2O impurity might be used as a nitriding medium because undesired oxidation reaction by impurity H2O might be preceded by reduction reaction by H with high a(H) in the uncracked NH3 gas [28, 31]. This aspect must be considered as one of pragmatic merits of using uncracked NH3 gas as a nitriding medium in industrial metal nitride production.
4. Conclusions
Linear reaction tube made of silica glass and sample holder made of refractory steel were newly designed and composed to carry out nitriding experiments for powder specimens of Mo and Fe in uncracked NH3 gas at specified linear flow rate v under irradiation of concentrated solar beam in SF40 solar furnace at PSA and following conclusions were drawn.(1) Higher nitrides of Mo (δ-MoN) and Fe (ε-Fe2N) were successfully synthesized using the newly developed experimental setup in stream of NH3 gas with controlled flow rate under irradiation of concentrated solar beam.(2) At a fixed spot of reactor tube, chemical activity a(N) of uncracked NH3 gas varied as functions of NH3 gas flow velocity v and temperature T and constitution of the synthesized nitride phases varied accordingly.(3) At specified v and T, a(N) tended to decrease on going from up-stream side to down-stream side on account of inevitable progress of dissociation of NH3 gas along the gas flow path to weaken nitriding power of uncracked NH3 gas on going from up-stream side to down-stream side. (4) Generally, increasing flow velocity v was found to be beneficial to raise nitriding power of uncracked NH3 gas but, when v exceeded certain threshold value, nitriding power of uncracked NH3 was not gained due to insufficiency of contact between NH3 gas and metal surface. (5) Optimized nitriding condition using uncracked NH3 gas must be determined for specified experimental setup because extent α of dissociation of NH3 gas must be affected by reaction components materials and their surface conditions as well as by the reactant material.
ACKNOWLEDGEMENTS
The authors gratefully acknowledge the EU through the seventh framework program for the financial support of this work under the STAGE-STE project with contract number 609837, the INSHIP project with contract number 731287, and the SFERA II project (Grant Agreement number 312643). This work has also received funding from the Fundação para a Ciência e a Tecnologia (FCT), Portugal, through IDMEC - Instituto de Engenharia Mecânica (Pólo IST), under LAETA - Associated Laboratory for Energy, Transports and Aeronautics (project grant UID/EMS/ 50022/2019). The technical assistance of Fabian Sola and the administrative support of Mrs. Carmen Montesinos are greatly appreciated.
References
[1] | K. Inumaru, T. Nishikawa, K. Nakamura and S. Yamanaka. High-pressure synthesis of superconducting molybdenum nitride δ-MoN by in situ nitridation. Chem. Mater. 20 (2008) 4756-4761. |
[2] | M.-S. Balogun, M. H. Yu, Y. C. Huang, C. Li, P. P. Fang, Y. Liu, X. H. Lu and Y. X. Tong. Binder-free Fe2N nanoparticles on carbon textile with high power density as novel anode for high-performance flexible lithium ion batteries. Nano Energy 11 (2015) 348-355. http://dx.doi.org/10.1016/j.nanoen.2014. 11.019. |
[3] | Y. F. Dong, B. L.Wang, K. N. Zhao, Y. H. Yu, X. D. Wang, L. Q. Mai and S. Jin. Air-stable porous Fe2N encapsulated in carbon microboxes with high volumetric lithium storage capacity and a long cycle life. Nano Lett. 17 (2017) 5740-5746. http://dx.doi.org/10.1021/acs.nanolett.7b02698. |
[4] | G. Hägg. Röntgenuntersuchungen über molybdän- und wolframnitride. Z. Phys. Chem. B7 (1930) 339-362. |
[5] | H. Yoshizawa, N. Shohoji, M. Katsura, T. Sano and T. Yato. Nitrierung des metalls bzw. metallcarbides unter ammoniakstrom. Technol. Rep. Osaka Univ. 27 (1977) 363-370. |
[6] | H. Jehn and P. Ettmayer. The molybdenum-nitrogen phase diagram. J. Less-Common Met. 58 (1978) 85-98. |
[7] | N. Shohoji, F. Almeida Costa Oliveira, J. Cruz Fernandes, L. Guerra Rosa, J. Rodríguez, I. Cañadas, C. Ramos, T. Magalhães and F. Cestari. Synthesizing higher nitride of molybdenum (Mo) and iron (Fe) in ammonia (NH3) gas stream under irradiation of concentrated solar beam in a solar furnace. Mat.-wiss. u. Werkstoffech. 44 (2013) 959-971. http:// dx.doi.org/10.1002/mawe.201300163. |
[8] | F. Almeida Costa Oliveira, L. Guerra Rosa, J. Cruz Fernandes, J. Rodríguez, I. Cañadas, T. Magalhães and N. Shohoji. Nitriding VI-group metals (Cr, Mo and W) in stream of NH3 gas under concentrated solar irradiation heating in a solar furnace at PSA (Plataforma Solar de Almería). Solar Energy 114 (2015) 51-60. http://dx.doi.org/10.1016/j.solener.2015.01. 028. |
[9] | A. A. Gromov and L. N. Chukhlomina (Ed.), Nitride Ceramics -Combustion Synthesis, Properties and Applications. Wiley-VCH-Verlag GmbH, Weinheim, 2015. |
[10] | E. Lehrer. Über das eisen-wasserstoff-ammoniak-gleich- gewicht. Z. Elektrochem. 36 (1930) 383-392. |
[11] | K. H. Jack. Binary and ternary interstitial alloys; I. The iron-nitrogen system: the structure of Fe4N and Fe2N. Proc. Roy. Soc. A195 (1948) 34-40. http://dx.doi.org/10.1098/rspa. 1948.0.0100. |
[12] | Y. Inokuti, N. Nishida and N. Ohashi. Formation of Fe3N, Fe4N and Fe16N2 on the surface of iron. Metall. Trans. A6 (1975) 773-784. |
[13] | N. Shohoji, T. Marcelo and M. Katsura. Influence of metastable species (non-graphitic carbon and ammonia gas) in the reactants on the composition of the reaction product (carbide, carbo-nitride and nitride). Solid State Ionics 38 (1990) 187-194. |
[14] | K. Nishimaki, T. Nakagawa, T. A. Yamamoto and M. Katsura. Equilibrium between flowing NH3 and synthesized FeNx at various positions along flow of reaction gas. Technol. Rep. Osaka Univ. 48 (1998), 153-156. |
[15] | K. Nishimaki, S. Ohmae, T. Nakagawa, T. A. Yamamoto and M. Katsura. Selective formation of iron nitrides by ammonia flow method. Technol. Rep. Osaka Univ. 48 (1998), 333-336. |
[16] | D. Liedtke, Nitrieren und Nitrocarburieren, Wärmbehandlung von Eisenwerkstoffen II, 5th Edition, Expert-Verlag GmbH, Renningen, 2010. |
[17] | M. Katsura. A thermodynamic analysis of nitrogen-rich uranium sesquinitride formation by the reaction of uranium with ammonia. Solid State Ionics 49 (1991) 225-231. |
[18] | M. Katsura and H. Serizawa. Formation of a nitrogen-rich α-U2N3+x phase by the reaction of uranium with a stream of ammonia. J. Alloys Compds. 187 (1992) 389-399. |
[19] | K. Nishimaki, M. Hirota, T. Nakagawa, T. A. Yamamoto, M. Miyake and M. Katsura. Thermodynamics of nitrogen-rich uranium sesquinitride formation by reaction of uranium monocarbide with ammonia. J. Alloys Compds. 271-273 (1998) 654-657. |
[20] | N. Shohoji. Roles of unstable chemical species and non-equilibrium reaction routes on properties of reaction product - A review-. J. Surf. Interfaces Mater. 2 (2014) 182-205. http://dx.doi.org/10.1166/jsim.2014.1052. |
[21] | F. Almeida Costa Oliveira, I. Figueira, J. Cruz Fernandes, I. Cañadas, J. Rodríguez, L. Guerra Rosa and N. Shohoji. Reactions of IVa-group metals, Ti and Zr, with uncracked NH3 gas at a temperature in the range between 600 and 800 ºC under heating with concentrated solar beam at PSA. Solar Energy 138 (2016) 119-127. http://dx.doi.org/10.1016/j.solener.2016.09.012. |
[22] | N. Shohoji. Uncracked Gaseous Ammonia NH3 as a Powerful Nitriding Medium -A Monograph-. Lambert Academic Publishing, OmniScriptum GmbH & Co. KG, Saarbrücken, 2017. ISBN: 978-3-330-04449-4. |
[23] | J. Cruz Fernandes, F. Almeida Costa Oliveira, L. Guerra Rosa, J. Rodríguez, I. Cañadas, T. Magalhães and N. Shohoji. Low temperature short-time nitriding of Va-group metals, V, Nb and Ta, in uncracked NH3 gas under heating with concentrated solar power (CSP). Ciência & Tecnologia dos Materiais 28 (2016) 112-116. DOI: 10.1016/j.ctmat.2017.02.001. (Special Issue on New Challenges in Energy Materials). |
[24] | J. Rodríguez, I. Cañadas and E. Zarza, New PSA high concentration solar furnace SF40. AIP Conf. Proc. 1734, 070028, pp. 1-11, 2016. |
[25] | J. Rodríguez, I. Cañadas and E. Zarza. PSA vertical axis solar furnace SF5. Energy Procedia 49 (2014) 1511-1522. http://dx.doi.org/10.1016/j.egypro.2014.03.16. |
[26] | B. Li, F. Almeida Costa Oliveira, J. Rodríguez, J. Cruz Fernandes and L. Guerra. Numerical and experimental study on improving temperature uniformity of solar furnaces for materials processing. Solar Energy 115 (2015) 95-108. |
[27] | F. Almeida Costa Oliveira, J. Cruz Fernandes, J. Rodríguez, I. Cañadas, J. Galindo and L. Guerra Rosa. Temperature uniformity improvement in a solar furnace by indirect heating. Solar Energy 140 (2016) 141-150. |
[28] | M. Katsura. Thermodynamics of nitride and hydride formation by the reaction of metals with flowing NH3. J. Alloys Compds. 182 (1992) 91-102. |
[29] | L. S. Darken and R. W. Gurry. Physical Chemistry of Metals. McGraw-Hill, New York, Toronto, London, 1953. |
[30] | N. Shohoji. Role of unstable chemical species (non-graphitic carbon and flowing NH3 gas) on the equilibrium point of the reaction product (carbide, carbo-nitride or nitride). Mater. Sci. Forum 449-452 (2004) 221-224. |
[31] | N. Shohoji. Chemical activities, a(H) and a(X), of constituents in H2X type gas molecules (X = O or S) at arbitrary degree of dissociation. Internat. J. Mater. Chem. 2 (2012) 10-15. http://dx.doi.org/10.5923/j.ijmc.20120201.02. |