Rifkatu D. Kambel1, Buba A. Aliyu2, Jeffery T. Barminas2, Ayodele Akinterinwa2
1Department of Chemistry Gombe State University, Nigeria
2Department of Chemistry, Moddibo Adama University of Technology Yola, Nigeria
Correspondence to: Ayodele Akinterinwa, Department of Chemistry, Moddibo Adama University of Technology Yola, Nigeria.
Email: |  |
Copyright © 2017 Scientific & Academic Publishing. All Rights Reserved.
This work is licensed under the Creative Commons Attribution International License (CC BY).
http://creativecommons.org/licenses/by/4.0/

Abstract
Polyurethane foam is flammable. Incorporating flame retardants in the material minimize this property and hence combustion susceptibility. Here, we developed a flame retardant as we synthesis a nanocomposite from polylactic acid (PLA) and kaolin. This was incorporate into flexible polyurethane foam. FTIR of incorporated foam shows peaks at 1099.26 cm-1 and 1267.51 cm-1 attributable to oxysilicane (Si-O-) and organosilicone (Si-C) respectively, suggesting an interaction between the foam and the nanocomposite. SEM was used to present the morphology of the foam formed, while the effect of the nanocomposite on the flame characteristics of polyurethane was studied at varying amount for optimum effect. The results showed that the flame propagation rate, flame duration, and after glow of foams formed decrease while ignition time and char formation increases with increase in the amount of PLA/kaolin nanocomposite incorporated. These results potentially presents PLA/kaolin nanocomposite as a good flame retardant for flexible polyurethane foam.
Keywords:
Polylactic acid (PLA), Kaolin, Nanocomposite, Flame retardant, Polyurethane foam
Cite this paper: Rifkatu D. Kambel, Buba A. Aliyu, Jeffery T. Barminas, Ayodele Akinterinwa, Synthesis and Application of Polylactic Acid/Kaolin Nanocomposite as a Flame Retardant in Flexible Polyurethane Foam, International Journal of Materials and Chemistry, Vol. 7 No. 1, 2017, pp. 14-19. doi: 10.5923/j.ijmc.20170701.03.
1. Introduction
Loss of materials due to fire disaster may be efficiently checked if the combustion affinity of the materials can be suppressed to the barest minimum. Prior to burning, the surface of a material must receive a significant amount of heat (Onuegbu and Ejimofor, 2011). Polymers on exposure to heat undergo thermal degradation to yield volatile combustible products which interact with atmospheric oxygen, initiating and propagating flame (Camino et al., 1993). The easiest and cheapest way to control or reduce the flammability of polymer is by incorporating flame-resistant additives (Eboatu et al., 1996). Polyurethanes are versatile polymeric material with various functional properties such as; excellent abrasion resistance, high toughness, chemical resistance, and low film-forming temperatures. They have also been used in coating, foam-making, adhesives, composites etc. (Chaoqun, 2014). In recent years, flame retardants containing melamine and halophosphate have been developed to retard the flammability of polyurethane (Dennis et al., 2013). During thermal decomposition, halophosphate breaks down to releases chlorine molecules which combine with the highly reactive radicals released by the foam to form non-volatile inactive molecules that inhibit the fire (Dennis et al, 2013). Ahmadreza and Zahed, (2012) reported that expandable graphite has been used in an effort to create an environmentally-friendly flame retardant system for rigid polyurethane foams. Expandable graphite is an intercalated graphite compound in which some oxidants like sulfuric acid and potassium permanganate are inserted between the carbon layers of graphite. Phosphonamides additives have drawn much attention in the last decade as a result of their excellent flame retardant properties (Ahmadreza and Zahed, 2012). These compounds predominantly act through a gas phase-inhibition mechanism during combustion. They decompose and release low molecular weight phosphorus containing fragments that are able to recombine with H+ and OH- radicals and thus interrupt the combustion process (Ahmadreza and Zahed, 2012). Polymer-layered silicate nanocomposites have also been recently reported to offer great potentials, providing superior properties, when compared to pure polymers and conventional filled composites (Brehme et al., 2011). These properties include high dimensional stability, high heat deflection temperature, reduced gas permeability, improved flame retardancy, and enhanced mechanical properties (Brehme et al., 2011; Xia et al., 2005). Effects of various organoclays of nano sizes on the thermo mechanical properties and morphology of polyurethane foam have been investigated (Ganiyu et al., 2010). This has shown that most clay layers were dispersed homogeneously into the matrix polymer. Another study has also reported that the addition of only a small amount of organoclay is enough to improve the thermal stabilities and mechanical properties of polyurethane foam (Dalen et al., 2014).In this study, we synthesize an organoclay nanocomposite from polylactic acid and kaolin using reported standard methods. The product formed was then incorporated into polyurethane form. The foam produced was characterized for flame properties in a quest to investigate and report the flame retardant effects of the PLA/kaolin nanocomposite in polyurethane foam.
2. Materials and Methods
2.1. Materials
H2SO4, HCl, polylactic acid, Isopropyl alcohol, hydrogen peroxide (30%), aceticacid, polyethylene glycol, Sodium aminolauric acid, chloroform, Methylamine, methylchloride and sodium hexametaphosphate are analytical grade products of the British Drug House. Toluene diisocynate (TDI), silicone oil and stannnous octoate were supply by Vita Foam Jos, Plateau State, Nigeria, yellow oleander seeds were picked from Federal Teaching Hospital staff quarters Gombe, Gombe State Nigeria, and the koalin was purchased in Jimeta market, Adamawa State, Nigeria. All materials except for the seed were used as obtained.
2.2. Methods
Preparation of modified activated kaolinThis was prepared using the method described by Meitaig et al. (2012). A 5 wt. % aqueous suspension of kaolin was prepared by adding 3 g of raw kaolin to 50 ml distilled water in a beaker and stirred for 1 h. The suspension was dispersed using a vortex mixer for 30 min, during which sodium hexametaphosphate solution (as a dispersant) was added. After 1h of sedimentation, the suspension was collected by centrifugation. Collected kaolin was the purified and activated in concentrated HCl for 30 min, washed and dried at 105°C under vacuum for 24 h. The activated kaolin was further modified for organic affinity, by dispersing 2 g of it in 48 ml of distil water and this is aided by votex mixer for 30 mins. Stock solution of sodium aminolauric acid (1ml) was then added drop-wisely, and vigorous stirring was maintained for 3 h at 75°C. The product was filtered and washed with distilled water twice to ensure complete removal of chloride ions, dried at 80°C for 12 h in an oven and pulverized to powder. Synthesis of polylactic acid/kaolin nanocompositesStill adopting Meitaig et al. (2012), solution casting method was utilized to fabricate PLA/Kaolin nanocomposites. In this, 1.0 g PLA and 0.15 g polyethylene glycol (plasticizer) were dissolved in 20 ml chloroform to give a 21% solution. Modified activated kaolin was also dispersed in the chloroform and stirred for 1 h. The final mixture was further stirred 24 h, emptied onto petri dishes and kept in the fume hood for 2 days at room temperature until all chloroform had evaporated. The prepared film was subsequently dried in an Oven 80°C for another 24 h and pulverized to powder.Synthesis of flexible polyurethane with nanocomposite flame retardantThe method described by Onuegbu et al. (2012) was adopted to synthesis the PU foam, and then varying amounts (1 g, 2 g, 3 g, 4 g and 5 g) of the flame retardant (PLA/kaolin nanocomposite) as follows; flame retardant was added to 50 ml polyester polyol inside mixing bowls and stirred vigorously. This was followed by sequential addition of silicone oil (stabilizer), stannous octoate (catalyst), methylamine (catalyst for the gaseous reaction), methylene chloride (auxiliary blowing agent) and distilled water (primary blowing agent). The mixture was stirred; TDI was added and stirring continues until the mixture started rising. It was then immediately poured in a mold (20 by 2 by 3 cm), allowed to solidify for about 10 mins in the mould before being removed and left open for 24 h to completely cure.FTIR analysisSamples were analyzed on KBr pellet using Nicole FT-IR spectrophotometer (model 100FTIR Theroscientific) from 4000 to 500 cm-1.Scanning electron microscopeThe surface morphology was examined with a Hitachi S-4700 scanning electron microscope (SEM) at acceleration voltage of 15 kV after gold coating. Samples analysed are of equal sizes.Determination of flame propagation Each sample was clamped vertically on a retort stand in a room where there is low air current. The sample was ignited at the base with the lighter. The distance traveled by the flame and the time taken for the flame to traverse that distance was measured. The flame propagation rate which is the ratio of distance traveled by the flame to the time taken was obtained thus;
Average of triple determinations was recorded for each analysis.Determination of flame durationSample was clamped vertically in a room with low air current and ignited at the base. The flaming time i.e. the duration between ignition and self-extinguishment was recorded. Average of triple determinations was recorded for each analysis (Eboatu et al., 1990).Determination of after – glow timeThe time between flame extinction and the last visually perceptible glow was taken as the after-glow time. Average of triple determinations was recorded for each analysis (Eboatu et al., 1990).Determination of ignition timeIgnition time was recorded as the time taken for the foam to ignite after coming in contact with flame. Average of triple determinations was recorded for each analysis (Eboatu et al., 1990).Determination of char formationChar formation was calculated from the percentage difference in the mass of the burnt and un-burnt piece of the foam. Average of triple determinations was recorded for each analysis (Eboatu et al., 1990).
3. Results and Discussion
3.1. FTIR Analysis
Figure 1 comparatively presents the FTIR spectra of untreated (0.0g PLA/Kaolin flame retardant) and treated (5.0g PLA/Kaolin flame retardant) polyurethane foam. For the untreated, the broad band observed at 1113.47 cm-1 could be attributed to O-H deformation present in primary alcohol while the noisy peaks between 3900 – 3700 cm-1 OH the stretching bands (Mistry, 2009). The peaks at 1373.98 cm-1, 1522.29 cm-1 and 2926.29 cm1 could be attributed to N-O present in aliphatic nitrites, N=O stretch present in nitrate and C-H stretching bands respectively (Mistry, 2009). While the peaks at 1268.83 cm-1, 1724.77 cm-1 and 2370.87 cm-1 can be due to C-H symmetric stretching present in esters, C=O stretch present in esters and C=N stretch present in isocynate (John, 2000). For the treated, the broad band at 3287.75 cm-1 could be attributed to N-H stretching vibration. The treated foam generally shows higher spectra intensity, hence higher functionality and possibly higher interactions that may hinder ignition. Compared to the untreated, the appearance of the peak at 1099.26 cm-1 assumes a fall into the range attributable to oxysilicate (Si-O-), at 1267.51 cm-1 is attributable to organosilicone (Si-C) stretch, implying a new chemical interaction between flame retardant and the polyurethane foam base materials. In some peaks common in the two spectra, the shifts observed in the treated can be attributed to the effects of the PLA/Kaolin nanocomposite on the structure of the foam (John, 2000).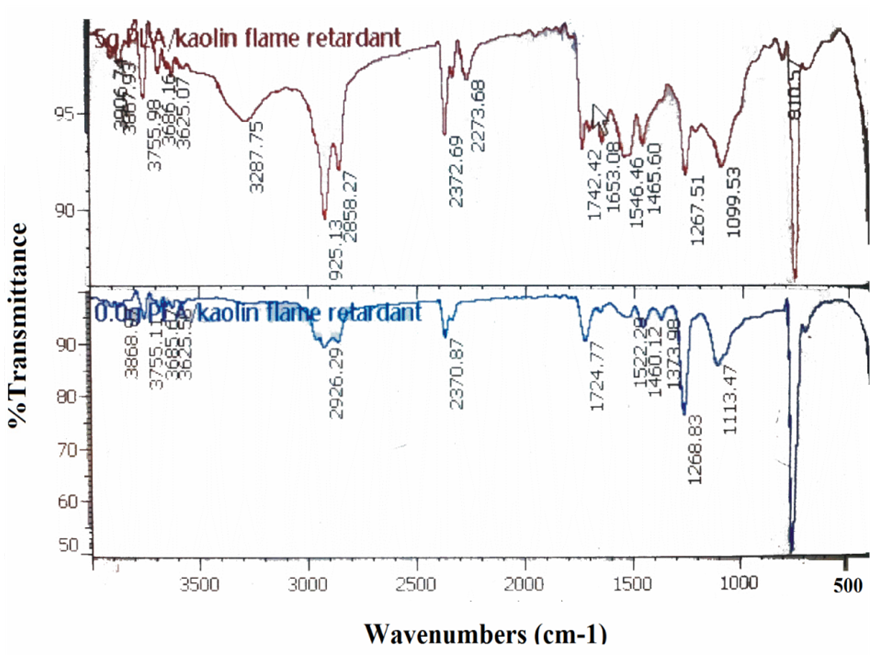 | Figure 1. IR spectra of PLA/Kaolin nanocomposite treated and untreated polyurethane foam |
3.2. Morphological Analysis
Figure 2 is a micrograph showing the dispersity nature of the PLA/Kaolin nanocomposite on polyurethane foam. This reveals an image of different size distribution of particle from the nanoparticle size to micrometer size. The particles were well dispersed in the nanometer region, and this is observed from 613.03 nm to 5.13 µm and extended to 14.46 µm at this region the particle size are visible to the naked eye. Figure 3 shows the arrangement of the particle on the polyurethane foam. The particles appeared to be clustered at outer regions while along the edges they were dispersed evenly forming a surface coating like pattern. The arrangements of particles were observed as intercalated nanoparticle structure in which particle were inserted between the layers of polymer matrix. Figure 4 presents the images (low magnification i.e. 1000x to 1500x on a scale of 80 µm to 50 µm) of the cell structure of the treated foam. The cellular structures are non-uniform and this can be said to results from competitive pressure during foaming (Ema et al., 2006). The images in Figure 4 also show that has a very tiny pore which prevent the release of the carbon dioxide during the foam formulation. Still in Figure 4, the surface of the bubble shown is broken, therefore the foam can be said to show some open-cell features. 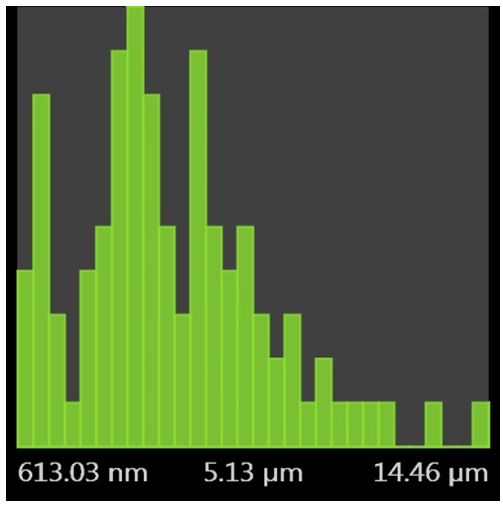 | Figure 2. SEM histogram of polyurethane foam treated with 5 g PLA/Kaolin nanocomposite |
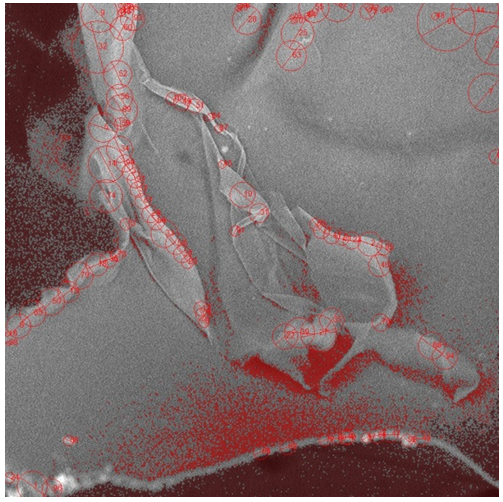 | Figure 3. SEM image of polyurethane foam treated with 5 g PLA/kaolin nanocomposite showing the nano particles arrangement |
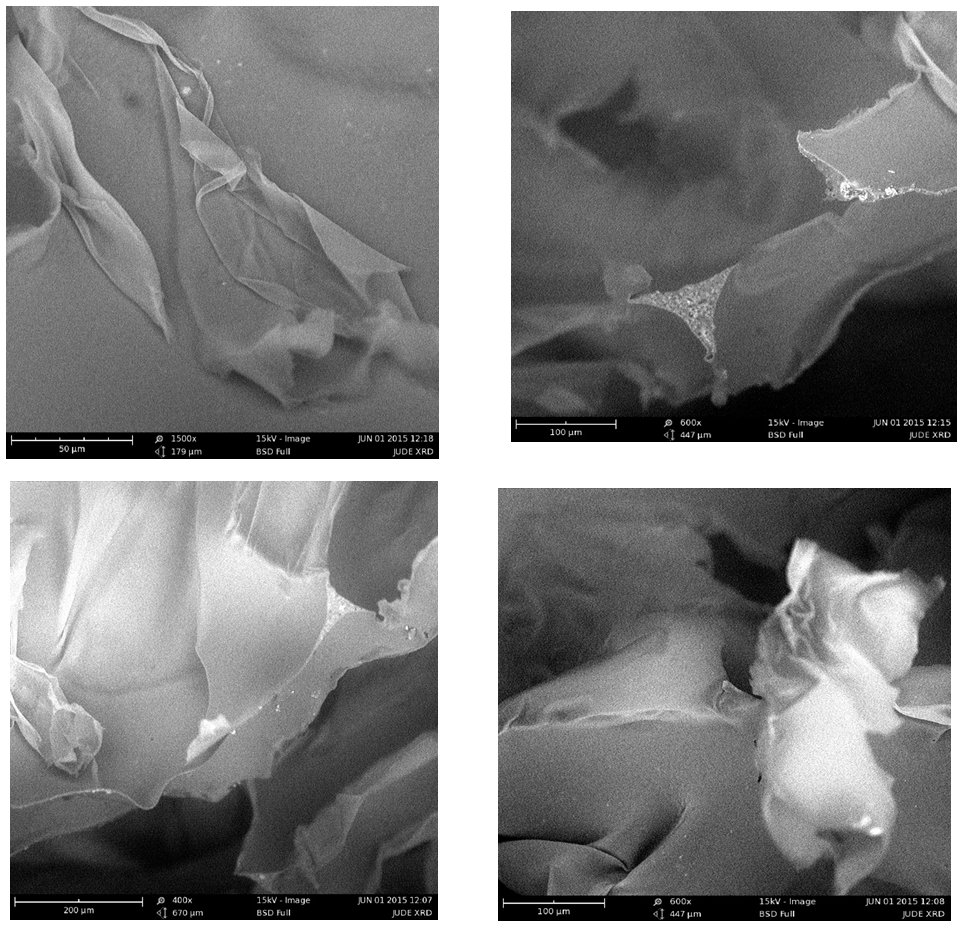 | Figure 4. SEM image showing the cellular structure of polyurethane foam having 5 g concentration of PLA/kaolin nanocomposite |
Effect of Amount of PLA/Kaolin Nanocomposite on Flame Propagation Rate of Polyurethane FoamFigure 5 presents the effect of PLA/Kaolin nanocomposite on flame propagation rate of polyurethane foam. The result shows that the flame propagation rate decreases with increase in amount of PLA/Kaolin nanocomposite incorporated. This effect is also comparable with the report by Okeke (2010), in which tri-ammonium phosphate was used as a flame retardant substance on polyurethane foam. 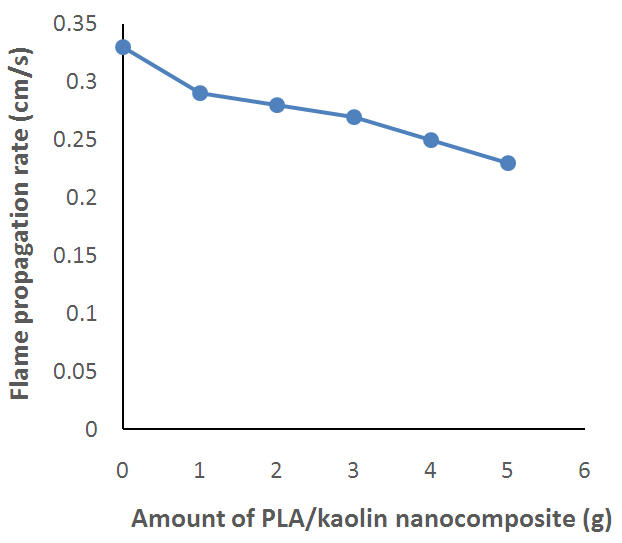 | Figure 5. Effect of Amount of PLA/Kaolin Nanocomposite on Flame Propagation Rate of Polyurethane Foam |
Effect of Amount of PLA/Kaolin Nanocomposite on After-glow Time of Polyurethane FoamFigure 6 presents the result of the After-glow time of polyurethane foam treated with PLA/Kaolin nanocomposite. The increasing incorporation of PLA/Kaolin nanocomposite reduces the after-glow time of the polyurethane foam. This effect is better compared to that of alum and fertilizer reported by Onuegbu et al., (2013). After-glow time is a function of carbonaceous char produced, and it’s responsible for fire re-kindling (Garba and Eboatu, 1990). 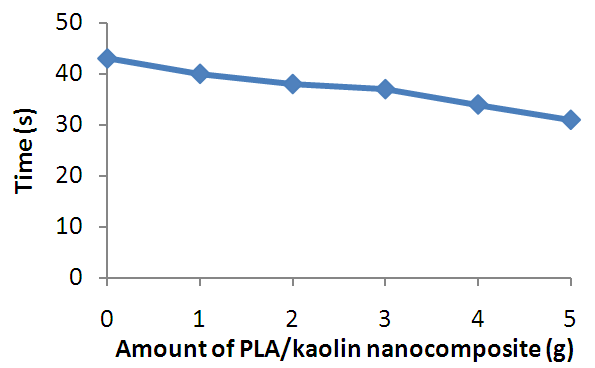 | Figure 6. Effect of Amount of PLA/Kaolin Nanocomposite on After-glow Time of Polyurethane Foam |
Effect of Amount of PLA/Kaolin Nanocomposite on Ignition Time of Polyurethane FoamFigure 7 presents the effect of the PLA/kaolin nanocomposite on the ignition time of the polyurethane foam. The incorporation of the PLA/Kaolin nanocomposite progressively increases the ignition time of the polyurethane foam. Compared to diammonium hydrogen orthophosphate reported by Polycarp (2011), PLA/Kaolin nanocomposite is a better flame retardant for polyurethane foam. At 5g of PLA/Kaolin nanocomposite ignition time is 35s while for diammonium hydrogen orthophosphate at 12g, ignition time is 11s. Ignition time is an important characteristic of any combustible material as its ignition is the onset of thermal degradation that results combustion (Okeke, 2010).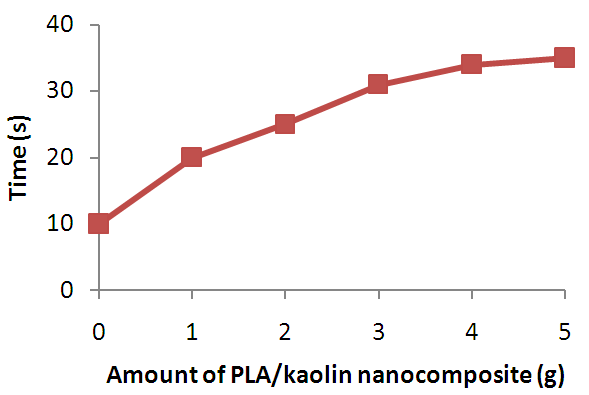 | Figure 7. Effect of Amount of PLA/Kaolin Nanocomposite on Ignition Time of Polyurethane Foam |
Effect of Amount of PLA/Kaolin Nanocomposite on Flame Duration of Polyurethane FoamFigure 8 presents the effect of PLA/Kaolin nanocomposite on flame duration of polyurethane foam. The flame duration of the foam decreases with increase in the amount of PLA/kaolin nanaocomposite incorporated. This effect is comparable to those reported for triammonium orthorphosphate and melamine as flame retardant (Okeke, 2010). Flame duration is the period of the exothermic reaction between the pyrolysis/thermal degradation product of the foam and atmospheric oxygen resulting combustion (Okeke, 2010; Eboatu and Altine, 1991). 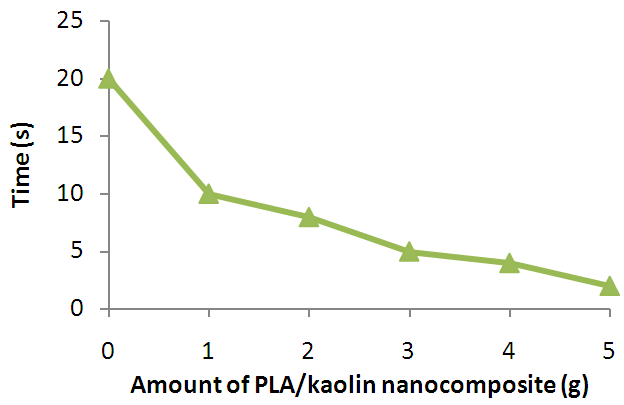 | Figure 8. Effect of Amount of PLA/Kaolin Nanocomposite on Flame Duration of Polyurethane Foam |
Effect of Amount of PLA/Kaolin Nanocomposite on Percentage Char Formation of Polyurethane FoamFigure 9 presents the effect of PLA/Kaolin nanocomposite on the percentage char-formation of polyurethane foam. The incorporation of PLA/Kaolin nanocomposite increases the percentage char formation of polyurethane foam and the effect increase with increase in the amount of PLA/Kaolin nanocomposite. This is comparable to effects reported while using melamine and triammonium orthorphosphate as flame retardant (Okeke, 2010). Char insulates the flame from the rest of polymeric material preventing penetration of burning (Okeke, 2010).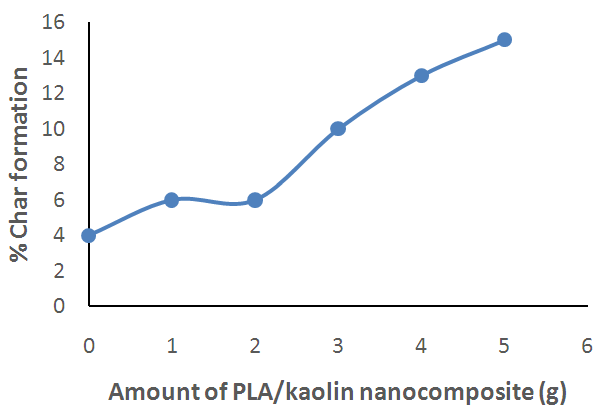 | Figure 9. Effect of Amount of PLA/Kaolin Nanocomposite on Percentage Char Formation of Polyurethane Foam |
4. Conclusions
The PLA/Kaolin nanocomposite synthesized in this work has shown functionalization and morphological modifications resulting into effects that improve the flame characteristics of polyurethane foam. Such effects as; increase in the ignition time, char formation and decrease in flame propagation rate, flame duration, and after glow with increase in amount of the PLA/Kaolin nanocomposites are promising and have presented the potentials of the PLA/Kaolin nanocomposites as an alternative flame retardant for flexible polyurethane foam, hence maximizing the efficiency of the product for more versatile utility.
References
[1] | Ahmadreza, G and Zahed A. (2012). Polyurethane Flexible Foam Fire Behavior journal of intech., 4: 102-120. |
[2] | Brehme, S. Schartel B, Goebbels J, Fischer O, Pospiech D, Bykov Y, and Döring M. (2011). Phosphorus polyesterversus aluminium phosphinate in poly (butylene terephthalate) (PBT): Flame Retardancy performance and mechanisms, J. Polymer Degradation and Stability, 9:875-84. |
[3] | Chaoqun Zhang (2014). Films Foams and Nanocomposite prepared from vegetable oil Graduate thesis and Dissertation Lower State University paper. 13742. |
[4] | Dalen, M.B., Ibrahim A.Q. and H. M. Adamu H.M. (2014). Effects of Low Castor Oil on Mechanical Properties of Polyurethane Foams. British Journal of Applied Science & Technology. 4 (18):2661 – 2683. |
[5] | Dalen, M.B., Ibrahim A.Q., Adamu H.M., and Ikeuba A.I. (2014). Preparation and Characterization of Dehydrated Castor Oil by infrared spectroscopy and titrimetric. Journal of Chemical Society of Nigeria. 39(1):3. |
[6] | Dennis S.W., Pau C. M., Fleischmann M. J., Spearpoint and Kai Y. Li. (2013). Determination of kinetic properties of polyurethane foam decomposition for pyrolysis modeling. Journal of Fire Sciences.13:31 – 356. |
[7] | Eboatu, A.N. and Altine A.M. (1991). Studies on the thermal characteristics of some tropical wood. Nigerian Journal of Renewable Energy, 2 (1): 49-53. |
[8] | Eboatu, A.N., Amanfor I, Akpabio I.O.J. (1996). Flame retardant treatment of some tropical timbers J. Fire and Material Sci., 4:17-40. |
[9] | Ema Yu, Ikeya Ma, and Okamoto Ma (2006). Foam processing and cellular structure of polylactide-based nanocomposites, Journal of science direct 47: 5350-5359. |
[10] | Ganiyu KL., David S A., Alfred A S., and Semiu A K. (2010). Effects of Different Filler Treatments on the Morphology and Mechanical Properties of Flexible Polyurethane Foam Composites Journal Nature and Science 8(6): 23-26. |
[11] | Garba, B. and Eboatu, A.N. (1990). Effect of flame retardant treatment on the thermal behaviour of some tropical timbers, J. Appl. Polym. Sci.39: 109-118. |
[12] | John C. (2000). Interpretation of Infrared Spectra, a Practical Approach, John wiley & sons L.t.d (R.A Mayers Edittion) 10815-10837. |
[13] | Meitang L, Minfeng P. and Hougwan M. (2012). Preparation Structure and Thermal Properties of Polylactide/Sepiolite Nonocomposites with and without organic Modifiers. Composite Science and Technology. 72:1508-1514. |
[14] | Mistry B.D. (2009). Hand Book of Spectroscopic Data Chemistry. (Edition 2009) Oxford L.t.d 1-24. |
[15] | Okeke A. O. (2010). Investigation of effects of two flame retardants on fire characteristics of flexible polyester foam. Master thesis. Nnamdi Azikiwe University Awka.1-156. |
[16] | Onuegbu T.U. and Ejimofor V.N. (2011). Flame retardant effect of potassium alluminium sulphornate on kraft sheet. International Journal of Basic and Applied Chemical Sciences, 1 (1):94-98. |
[17] | Onuegbu T.U., Umoh E.T, and Iwuchukwu I.E. (2012). Flame Retardant Effects on Flexible Polyurethane Foam Treated with Potassium Aluminum Sulphate, Journal of Science and Technology, 2:25-72. |
[18] | Onuegbu T.U. And Ekpunobi U.E. (2013). Flame Retardant Effects On Flexible Polyurethane Foam Treated With Halogenated Paraffin, International Journal of Chemistry, 2:56. |
[19] | Polycarp O.I. (2011). Comparative analysis of flame characteristics of castor oil and some other inorganic flame retardants used in polyurethane foam systems. Journal of Basic and Applied Science.19 (1):55- 63. |
[20] | Xia Cao, James L, Changchun Z, Xiangming J (2005) Polymer nanocomposite Foams Journal Science direct 60: 2344-2363. |