Ayegba C. O., Makinde T., Obigwa P., Orijajogun J.
Sheda Science and Technology Complex
Correspondence to: Ayegba C. O., Sheda Science and Technology Complex.
Email: |  |
Copyright © 2015 Scientific & Academic Publishing. All Rights Reserved.
This work is licensed under the Creative Commons Attribution International License (CC BY).
http://creativecommons.org/licenses/by/4.0/

Abstract
The production of silica gel from the natural clay obtained from Kwali area council of Abuja was carried out using alkaline extraction followed by acid precipitation. The alkaline extraction was investigated using 4%, 15%, 25% and 30% (wt) sodium hydroxide solution at various reaction times of 1hr 1½ hr, 2hrs, 2½ hrs, 3hrs, 4hrs, 5hrs,7hrs and 8hrs. The highest yield of 15.25% silica gel for 25g of clay was recorded at 25% (wt) of the sodium hydroxide solution and reaction times of 4hrs. The x ray diffraction analysis and characterization of the clay showed the predominance of quartz and illite. There were also peaks showing the presence of kaolinite, goethite and rutile.
Keywords:
Silica Gel, Quartz, Diffraction, Extraction
Cite this paper: Ayegba C. O., Makinde T., Obigwa P., Orijajogun J., Production of Silica Gel from Clay, International Journal of Materials and Chemistry, Vol. 5 No. 6, 2015, pp. 123-126. doi: 10.5923/j.ijmc.20150506.01.
1. Introduction
Silica is extensively found in nature either as a major mineral in most igneous (e.g granite) or sedimentary (e.g sand and sand stone) or metamorphic rocks (quartzite, gneiss). Silica is most commonly found in nature as quartz, as well as in various living organism. It is produced by a simple method based on alkaline extraction this is followed by acid precipitation, the gelatinous precipitate is washed, then dehydrated to produce silica gel. The gel or colloid consist mainly of hydrated silica (SiO2.nH2O). The term “Gel” merely indicates the condition of the material at one stage of its manufacture. It is highly porous structure, characterized by uniformity of the arrangement of the pores and their sizes. The pore area of silica gel varies with the method of manufacture. Silica gel is widely used as a desiccant. Its role as a catalyst support, as a flatting agent in coatings and as a selective adsorbent in column chromatography is well established. It has the application in modification of viscosities and thixotropy of the liquids. Soluble silicates produced from silica are widely used in the glass, ceramics, and cement as a major component and in pharmaceuticals, cosmetics, and detergents industries as a bonding and adhesive agents (Anon., 1997); (Laxamana, 1982). Silica also has been used as a major precursor for a variety of inorganic and organometallic materials which have applications in synthetic chemistry as catalysts, and in thin films or coatings for electronic and optical materials (Lender and Ruiter, 1990; Brinker and Scherer, 1990). (Mizuki et al., 1993) and (Krishnaro and Godkhindi 1992) investigated the formation of silicon carbide from rice hulls at high temperatures and (Maeda and Komatsu 1996) studied the semiconductor properties of silicon carbide produced from rice hull. Semiconductor industries require pure silica, currently produced by smelting quartz in a high temperature furnace, to produce ultrapure polycrystalline silicon and silicon hydride.Most of the research work carried out for the preparation of different grades and forms of silica gel exist in patent form and no detailed experimental procedures are available (Hafiz et al., 2009). This work is aimed at investigating the effectiveness of: (1) alkali extraction of silica from Kwali clay, and (2) washing silica gel with water, in reducing the mineral content of silica produced by the alkali extraction.
2. Experimental Section
2.1. Materials and Method
The clay used for the production of silica gel was obtained from Kwali in Kwali area council, Abuja Nigeria. The clay was ground into powder and sieved using a 250micron sieve. 25g of the clay powder was then mixed with various concentration of aqueous Sodium hydroxide (4%, 15%, 25% and 30%) at liquid to solid ratio 2:1 in a 250ml circular flask. The flask was placed on a heating mantle at a temperature of 80°C and heated and agitated at various reaction time of 1hour, 1½ hour, 2hours and 2½ hour, 3hours, 4hours, 5hours, 6hours, 7hours and 8hours. The mixture was removed from the heating mantle and centrifuge. The liquid portion of the mixture was separated and the pH adjusted to 4 with hydrochloric acid. The liquid was neutralized with ammonia solution and then centrifuge to separate the precipitate (gel) from the solution. The gel was washed several times with deionized water to remove sodium chloride. Complete removal of the salt was verified by the X-ray diffraction analysis. The sample was then dried in the oven at 105°C and quantified. Figure 1 is a process diagram for the production of soluble sodium silicate.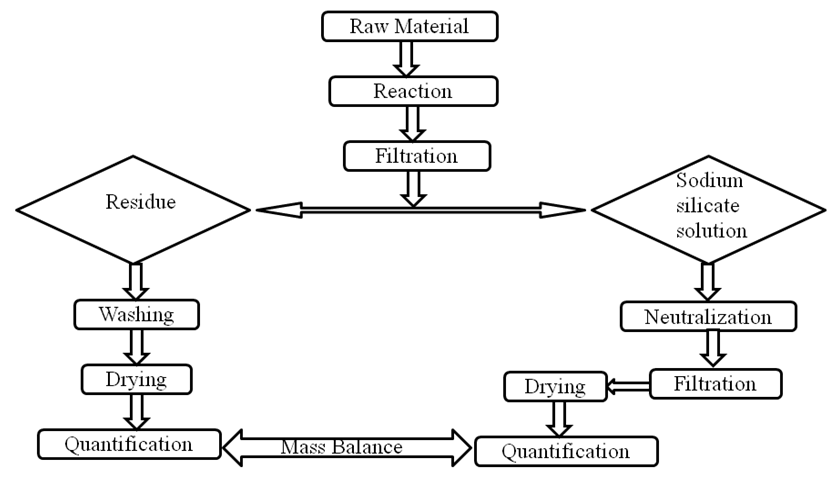 | Figure 1. Flow diagram for the production of soluble sodium silicate |
2.2. Characterizations
The X-ray diffraction analysis of the silica gel produced and the clay (powder) were carried out to determine their the phases present, the x ray diffraction analysis was carried out using multipurpose x-ray Diffractometer (Panalytical). The yield of silica gel produced at various concentration of sodium hydroxide was determined from equation (1):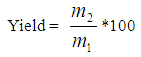 | (1) |
Where m1 = mass of clay (g)m2 = mass of silica gel produced (g)The iodine number of the silica gel was determined using ASTM method. The iodine number was calculated using equation (2)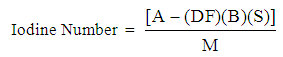 | (2) |
N2 = normality of iodineN1 = normality of sodium thiosulphateDF = dilution factorI = volume of iodine (ml)H = volume of 5% HCl (ml)F = filtrate (ml)
3. Results and Discussion
3.1. Effect of Reaction Time on Yield of Silica Gel
The effect of reaction time on the yield of silica gel from kwali clay was investigated by varying the reaction time one and half hour to 8hours. The highest yield of silica gel was obtained at the reaction time of 4hours. (XU YING-MEI et al., 2010) reported a reaction time of 3hour.
3.2. Effect of NaOH Concentration of on the Yield of Silica Gel
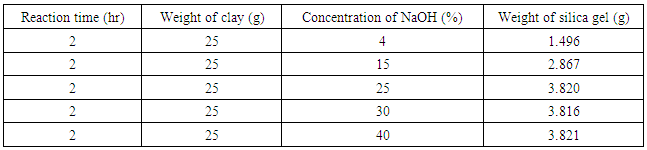
3.3. X-ray Analysis
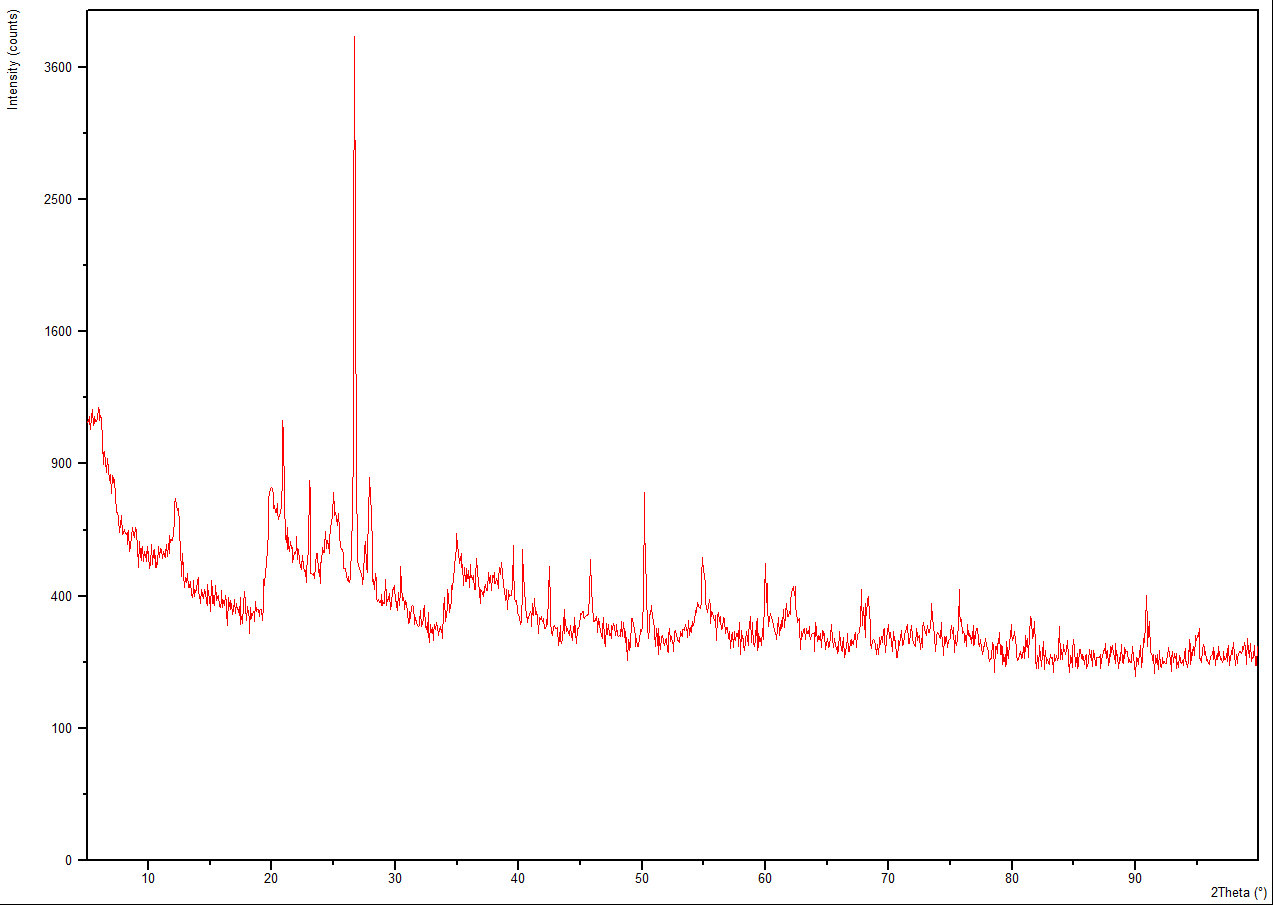 | Figure 2. XRD of Clay |
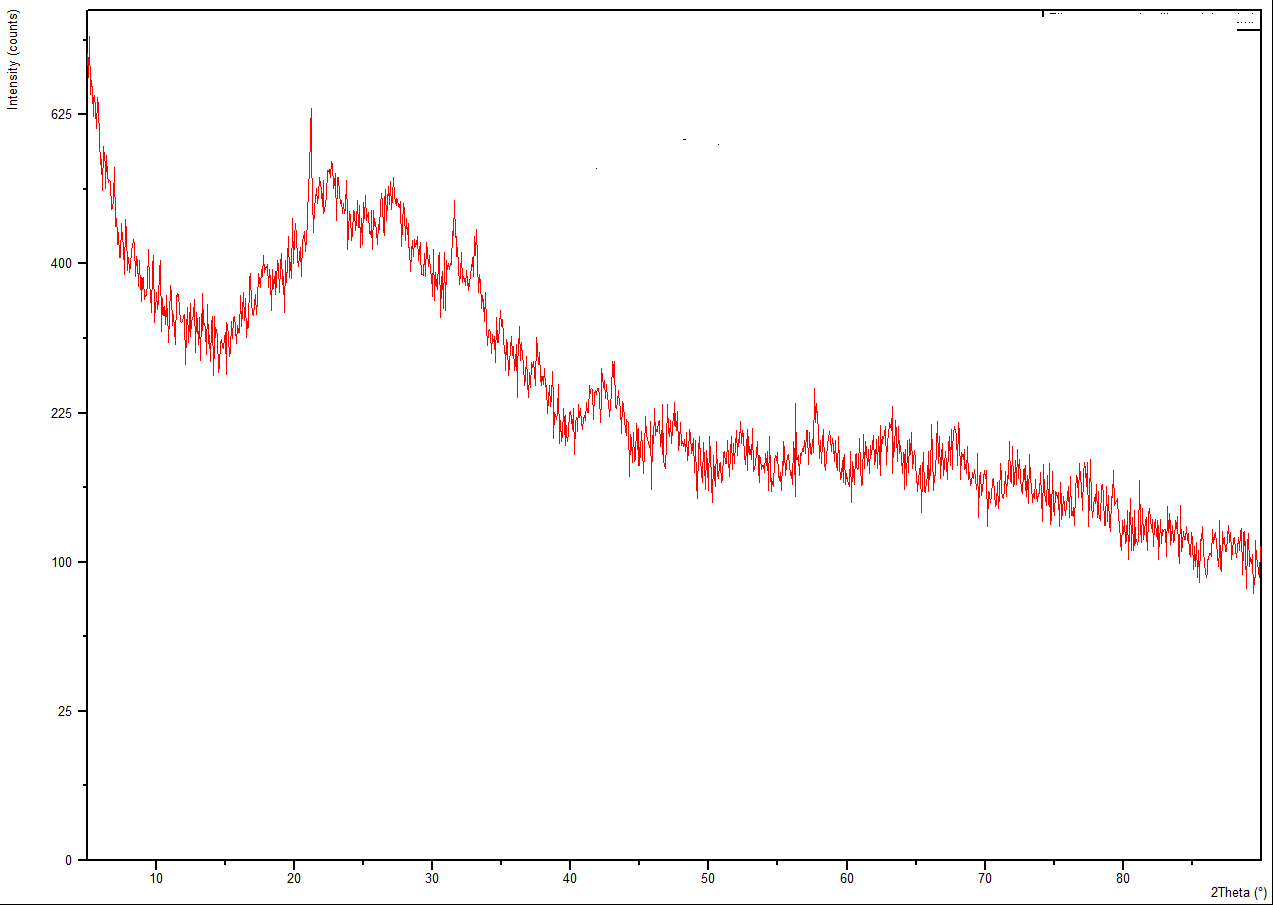 | Figure 3. XRD of Silica Gel |
The interpretation of the diffractogram was done by carrying out search and match on highscore software (panalytical). The highscore compares diffractograms with reference diffractograms by using different colouration to identify different phases in a sample. The result of search and match on the highscore identified quarzt and kaolinite as the predominant phases with scores of 58 and 42 respectively. Peaks at 23.036°, 26.702°, 40.374°, 45.838°, 50.220°, 54.953°, 60.034°, 62.304°, and 76.037° showed the presence of quartz in the clay. And peaks at 12.186°, 19.844°, 25.081°, and 42.478° showed the presence of kaolinite. The x ray diffraction analysis of the clay showed the predominance of quartz and illite. Also the diffractogram was compare to previous work reported by (Souza et al., 2013). Using the technique of peak position (2thetha) and intensity of peaks, kaolinite, goethite and rutile seem to be present.The X-ray diffraction pattern shown in Figure 1 reveals that the X-ray diffaction studies of the silica gel indicated relatively high disordered structure of silica. It also shows that the silica gel is completely free of sodium chloride, proving the effectiveness of the extraction process.
3.4. Iodine Number
Iodine number indicates the extent of surface area existing in the silica gel sample and hence are important parameters for assessing the usefulness of the sample for its industrial applications as a desiccant and catalyst support. The iodine number of 21.95mg/gI2 was obtained for the silica gel produced. This value is close to iodine number of 23.87mg/gI2 for commercial granular silica gel. Also (Hafiz et al., 2009) reported 23.60mg/gI2.
4. Conclusions
Non indicating (white) amorphous silica gel has been prepared successfully. The clay used for this work is widely avalaible in kwali, Abuja, Nigeria. This investigation has indicated that there is a great scope for their exploitation as the raw materials for the production of silica gel on industrial scale in the country.This investigation shows that the quantity of silica gel produced increased with the increase in reaction time with the optimum quantity of 3.82g of silica gel obtained per 25g of clay in 4hrs. also the quantity of silica gel produced increased with the concentration of sodium hydroxide with the optimum quantity obtained at 25% of sodium hydroxide. The silica gel produced shows close resemblance to the properties of a good quality commercially available silica gel
ACKNOWLEDGEMENTS
The authors are grateful to the Sheda Science and Technology Complex, Abuja for facilities and sponsorship of this project.
References
[1] | Anon., (1997). Soluble Silicates and their Applications. Crossfield Publication, Crossfield, Warrington, UK, Issue No. 2. |
[2] | Laxamana, N.B., (1982). Binders from rice hull ash low-cost housing materials. Forbride-Dig. College: Forest Products Research and Industries Development Commission 11, 27-30. |
[3] | Brinker, C.J., Scherer, G.W., (1990). Applications. In: Sol-Gel Science, The Physics and Chemistry of Sol-Gel Processing. Academic Press, San Diego, CA, pp. 839-880. |
[4] | Lender, P.W., Ruiter, R., (1990). Novel inorganic materials and heterogeneous catalysis: Preparation and properties of high surface area silicon carbide and silicon oxynitrides. In: Sheats, J.E., Carraher, C.E., Pittman, C.U., Eldin, M., Currell, B. (Eds.), Inorganic and Metal-Containing Polymeric Materials, Plenum Press, New York, pp. 187-195. |
[5] | Mizuki, E., Okumura, S., Saito, H., Muro, S., (1993). Formation of silicon carbide from rice husks using enzymatic methods for carbon control. Biores. Technol. 44, 47-51.\ |
[6] | Maeda, E., Komatsu, M., (1996). The thermoelectric performance of silicon carbide semiconductor made from rice hull. Mater. Res.Soc. Symp. Proc. 410, 77-82. |
[7] | Krishnaro, R.V., Godkhindi, M.M., (1992). Distribution of silica in rice husk and its effect on formation of silicon carbide. Ceramics Intl. 18, 243-249. |
[8] | Xu Ying-Mei, Qi Ji, He De-Min, Wang Dong-Mei, Chen Hui-Ying, (2010). Guan Jun, Zhang Qiu-Min. Preparation of Amorphous Silica From Oil Shale residue and Surface Modification by Silane Coupling Agent. Oil Shale, Vol. 27, No. 1, pp. 37–46. |
[9] | Souza A. E.; Teixeira S. R.; Santos G. T. A.; Longo E. (2013). Addition of sedimentary rock to kaolinitic clays: influence on sintering process Cerâmica vol.59 no.349. |
[10] | Hafiz Asghar Ali, Arshad Chughtai and Abdul Sattar, (2009). Synthesis of quality silica gel; Optimization of parameters Journal of Faculty of Engineering & Technology, pages xx-xx. |