Vo Thanh Tung1, Nguyen Trong Tinh2, Nguyen Hoang Yen1, Dang Anh Tuan1
1Hue University of Sciences, Vietnam, 77 Nguyen Hue Str., Hue city, Vietnam
2Institute of Applied Physics and Scientific Instrument of Vietnamese Academy of Science and Technology, Vietnam
Correspondence to: Vo Thanh Tung, Hue University of Sciences, Vietnam, 77 Nguyen Hue Str., Hue city, Vietnam.
Email: |  |
Copyright © 2012 Scientific & Academic Publishing. All Rights Reserved.
Abstract
This work uses a finite element modeling method to study the electromechanical coupling factor of piezoelectric materials. Two types of piezoelectric materials were chosen, piezoelectric materials (PZT) and Pb-free piezoelectric materials Ba(Zr0.2Ti0.8)O3-50(Ba0.7Ca0.3)TiO3 (BZT-50BCT) that measure the resonance and anti-resonance frequencies for the calculation of the planar and thickness coupling factor values. For PZT5A, in radial vibration mode, these frequencies were 178 and 211 kHz, and in thickness mode, 2.182 MHz, respectively. For the BZT-50BCT, the frequencies were 224 and 250 kHz, and in thickness mode, 2.539MHz, respectively. The coupling factor values were 0.57 (kp) and 0.33 (kt) for PZT5A and 0.50 (kp) and 0.28 (kt) for BZT-50BCT, respectively.
Keywords:
PZT, Electromechanical Coupling Factor, Pb-free Piezoelectric Materials
Cite this paper: Vo Thanh Tung, Nguyen Trong Tinh, Nguyen Hoang Yen, Dang Anh Tuan, Evaluation of Electromechanical Coupling Factor for Piezoelectric Materials Using Finite Element Modeling, International Journal of Materials and Chemistry, Vol. 3 No. 3, 2013, pp. 59-63. doi: 10.5923/j.ijmc.20130303.03.
1. Introduction
Piezoelectric materials are widely used for various applications such as actuators, sensors, sonar transducers, accelerometers,[1-3] etc. Materials like PZT, BaTiO3 and PVDF are popular candidates for use as piezoelectric materials. For half a century, the PZT (lead zirconate titanate) family has been the icon of a large class of technologically important materials piezoelectrics, which dominated almost all piezoelectric applications ranging from cell phone to high-tech scanning-tunneling microscope[4, 5]. Because of Pb toxicity to the environment and to human body, recently many Pb-free ferroelectric systems, such as Ba(Zr0.2Ti0.8)O3-x(Ba0.7Ca0.3)TiO3 (hereafter abbreviated as BZT-xBCT), (K0,436Na0,5Li0,064)Nb0,92Sb0,08O3... have been reported. Especially, the BZT-xBCT material is particularly interested because it exhibits the equally excellent piezoelectricity as in Pb-based systems[6].In the present study, we used a finite element modeling method to measure the electromechanical coupling factor, or k-value of piezoelectric materials (PZT) and Pb-free piezoelectric materials Ba(Zr0.2Ti0.8)O3-50(Ba0.7Ca0.3)TiO3 (BZT-50BCT). The k-value of piezoelectric samples both two types were calculated and demonstrated for applications. In addition, from the received results, we analyze and compare the physic properties of piezoceramics in PZT family and Pb-free piezoceramic (BZT-50BCT) and show the advantage properties of new material BZT-50BCT.
2. Finite Element Modeling Theory
From the theory of piezoelectric material[7-9], the mechanical properties (the relation between stress and strain) are defined in the stress-charge form, in which the user has to specify the elasticity matrix, the coupling matrix, the relative permittivity matrix, the piezoelectric coefficients matrix and the density. These matrices of these parameters are defined as in Table 1. The complete set of constants of the PZT5A material shown in Table 1 is taken out from the data of the libraries of the simulation program. A full set of elastic, piezoelectric, and dielectric parameters of BZT-50BCT are measured and calculated by Dezhen Xue and et.al.[10] when using a resonance method.Investigations using computational finite element methods (FEM method) have successfully analysed the behaviour of piezoceramic discs[11-13]. In our study, we used a simplified 3-D axis-symmetric model in the FEM of simulation program for design the model geometry. The modelling dimensions of piezoceramic discs with radius 5.5mm, thickness 1mm is illustrated in Fig.1 (a). Modelling conducted is meshed of by using the standard meshing tool (the free tetrahedral mode) at 13380 elements, 16 numbers of vertex elements, 208 numbers of edge elements and 4352 numbers of boundary elements in Fig 1.b.Since the analysis involves piezoelectric material, there are two different set of boundary conditions the user has to set. First is the mechanical boundary conditions, second is the electrical boundary conditions. In terms of the mechanical boundary conditions, all surfaces are free. For the electrical boundary condition, the bottom surface of the cantilever beam is set as ground, the top surface set as Terminal/Electrical with the voltage 0.5V. These boundary conditions are illustrated in Fig 1.a.Table 1. Measured and derived piezoelectric, dielectric constants and elastic constants of poled BZT-50BCT ceramic (density 5200 kg/m3) compared to the the PZT-5A ceramic (density 7750 kg/m3) (Ref. 7) 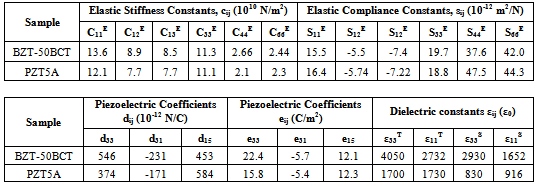 |
| |
|
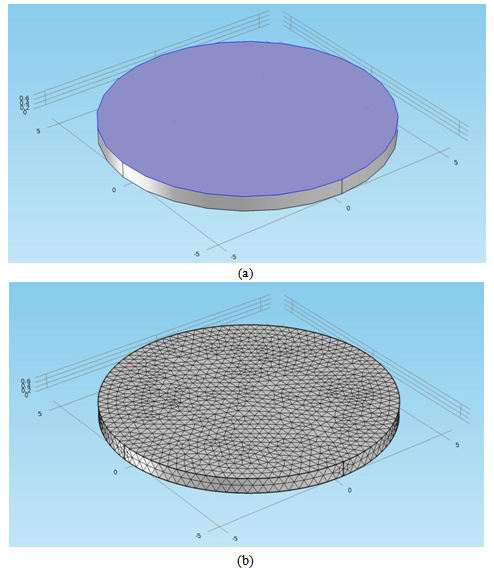 | Figure 1. (a) The fully expanded model of the disk ceramic samples (b) the meshed model of the designed disk ceramic samples |
3. Electromechanical Coupling Factors
The electromechanical coupling factor, k-value, were calculated from equations of the IEEE Standard on Piezoelectricity 1961 and 176-1987[14, 15]. The k-value and its high mechanical quality factor (Qm) defined in terms of by:Coupling factor | (1) |
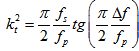 | (2) |
Mechanical quality factor  | (3) |
Where: fp is parallel resonance frequency, fs is serial (motional) resonance frequency, Zm is minimum impedance of sample at fs , Cf is capacitance of sample at frequency of 1 kHz and Δf = fp – fs , : Bessel function of first kind and zero order, j1: Bessel function of first kind and first order, : lowest positive root of
=8.85.10-12 F/m. For IREE Standards on Piezoelectric Crystals 1961:
= 0.31 and
2.05. For IEEE Standard on Piezoelectricity 176-1987:
are defined by using a polynomial to represent the data described by Meitzler et al.[16]:  | (4) |
 | (5) |
where rs =fs1/fs2 is the series resonance ratio, fs1, fs2 is measured for the first and second series resonance frequency. The coefficients of polynomials are shown in the Table[2]: Table 2. Coefficients for the polynomials shown in equation (4) and (5)  |
| |
|
The formulas (1-5) are mathematically accurate for determining k; however, in many cases, appearing the sideband resonance around the fundamental resonance and the impedance curve is disturbed. The disturbance gives the error in determination of fs and fp and hence of k. In this case, the method of Onoe is suggested[17].
4. Simulation Results and Discussions
Figure 2 (a-f) shows the results of the dependence of the impedance on frequency in radial and thickness vibration modes for piezoceramics the PZT family and BZT-50BCT materials respectively. From these results, the resonant and anti-resonant frequencies, the minimum impedance Zmin and other parameters are defined. Using the IEEE Standard on Piezoelectricity 1961 and 176-1987 and the equations (1) to (3) and the method Onoe, the calculated k-values are listed in Table 3.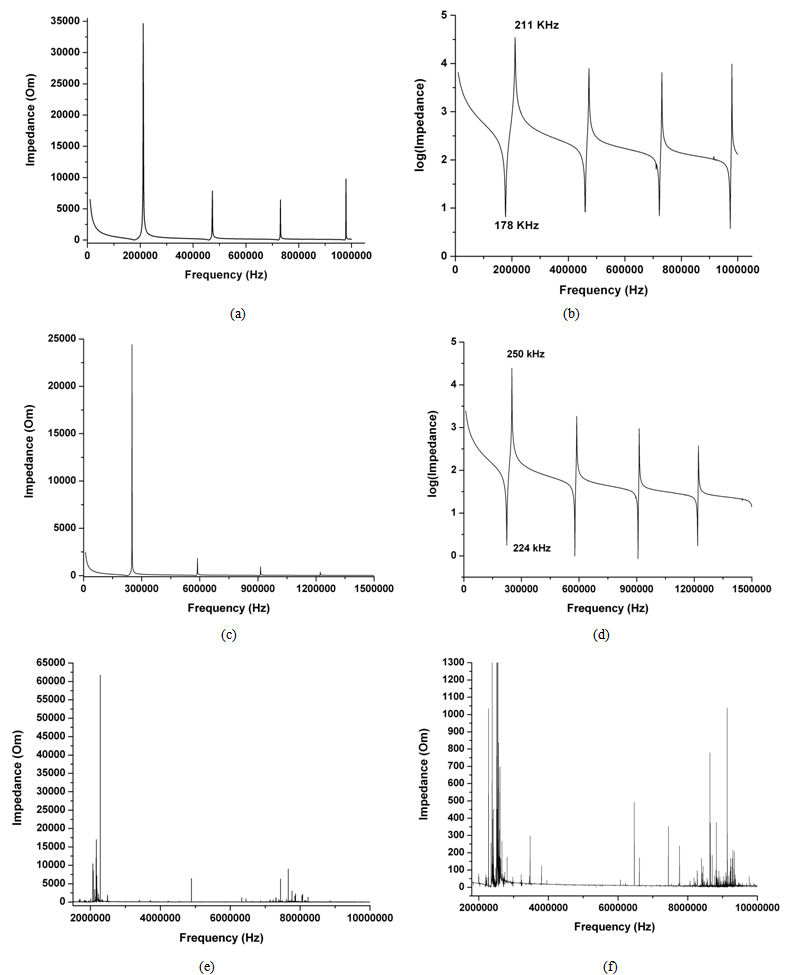 | Figure 2. Variations of impedance and its log as a function of frequency for radial vibration mode (a, b) PZT5A (c, d) BZT-50BCT and thickness vibration mode with 1.00 mm thickness (e) PZT5A (f) BZT-50BCT |
Table 3. Simulation data of the electromechanical coupling factor value for PZT5A and BZT-50BCT 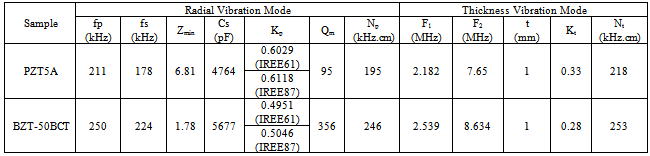 |
| |
|
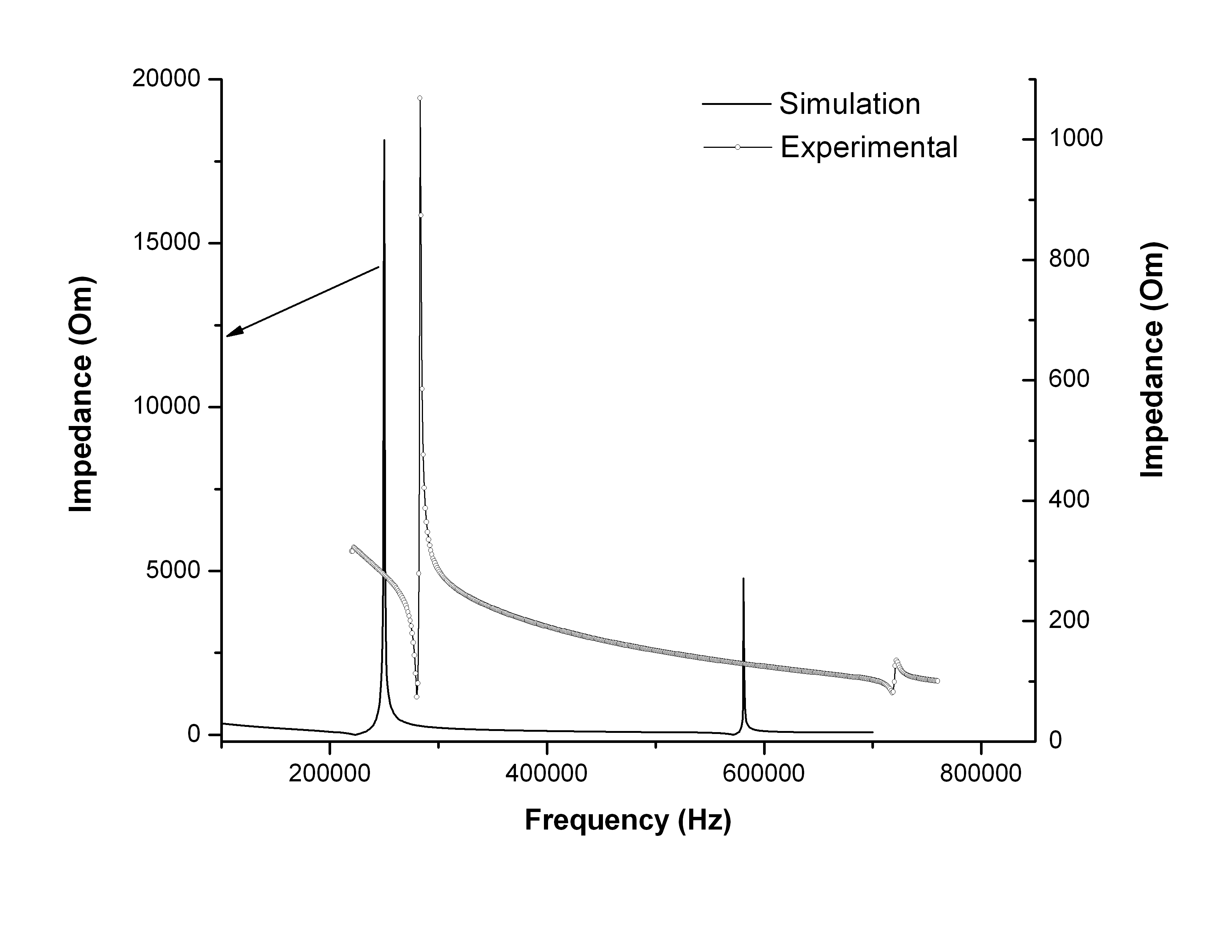 | Figure 3. Comparison between experimental and theoretical normalized frequency spectra of impedance of BZT-50BCT in radial vibration mode |
The k-value of the radial vibration mode for PZT family (PZT5A) are about 0.61 (kp), Np = 195 (kHz.cm) (Radial frequency constant) and 0.33 (kt), Nt = 218(kHz.cm) (Thickness Mode Frequency Constant). These results are similar to the previous research works. They differ from the reported value about 3 percent error for radial vibration mode and about 30 percent error for thickness of 1.0 mm. Therefore, the finite element method is an accurate and easy method for evaluating the electromechanical coupling factor values. For BZT-50BCT materials, the values are about 0.50 (kp) and 0.28 (kt), respectively. Although the electromechanical coupling factors of BZT-50BCT materials is smaller than for PZT5A, however these k-values are rather good. Especially, the mechanical quality factor of BZT-50BCT materials is high (Qm = 356). Such these results reveal that BZT-50BCT ceramic has good piezoelectric properties.The fundamental resonance frequency of PZT5A (radial and thickness vibration modes) are at about 178 kHz and 2.18 MHz, respectively, whereas the resonance frequency for the BZT-50BCT are at 224 kHz and 2.2 MHz. Further, the results show the appearance of the resonant peaks in the simulation curve and the minimum-to-maximum impedance ratio of BZT-50BCT specimen are similar to the specimens of the materials in PZT family. However, it notes that in two vibration modes, the maximum amplitude at the resonant frequencies of BZT-50BCT material is lower than PZT5A. Especially, in thickness modes, the maximum impedance for BZT-50BCT sample is about 1200 Ω, but for PZT5A, is about 60000 Ω.Comparing the normalized frequency spectra of impedance obtained by the experimental and simulated methods for BZT-50BCT material is shown in Fig. 3. It can be observe two similar peaks of the resonance curves. The fundamental resonance frequency of experimental data is about 282 kHz and of simulation data is about 249 kHz. It is possible to see that the simulated resonant frequency match quite well with the experimental ones (up to 10% error). Furthermore, the amplitude of resonant peaks is not similar. Possible reasons for the difference and error could be the lack in manufacture of material and sample, the difference between theoretical and real boundary conditions. As a result, the numerically evaluated FEM do not match exactly the experimental ones.
5. Conclusions
Two types of piezoelectric materials have been studied, PZT5A and BZT-50BCT. The simulation results for PZT5A material are shown to agree well with experimental results. Furthermore, it shows and evaluates the good factor values of BZT-50BCT materials. Consequently, these properties make BZT-50BCT to be used as a piezooelectric transducer. In addition, it is found that the FEM model connected the simulation program has excellent agreement to the experimental data in studying the properties of the new material groups.
ACKNOWLEDGEMENTS
The work was carried out in the frame of the “Basic Project of Hue University 2013-2015”.
References
[1] | B.Sahoo, V.A.Jaleel and Panda, “Development of PZT Powders by Wet Chemical Method and Fabrication of Multilayered Stacks” Actuators. Materials Science and Engineering B 126: 80-85, P.K. 2006. |
[2] | R.E. Newnham, “Functional Composites for Sensors and Actuators:Smart Materials”, Pennsylvania Academy ofScience. In: S.K. Majumdar, R.E. Tressler and E.W. Miller (eds.), pp. 259-275 (Chapter 13). Pennsylvania, U.S, 1998. |
[3] | L. F. Hong Chen, Y. P. Chen, X. J. Wu, Q. L. Huang, Q. J. and X. T Luo, “Preparation and Properties of Polymer Matrix Piezoelectric Composites Containing Aligned BaTiO3”, Whiskers. Journal of Materials Science 39: 2997-3001, 2004. |
[4] | B. Jaffe, R. S. Roth, and S. Marzullo, “Piezoelectric properties of lead zirconate-lead titanate solid-solution ceramics”, J. Appl. Phys. 25, 809 1954. |
[5] | N. Setter, D. Damjanovic, L. Eng, G. Fox, S. Gevorgian, S. Hong, A.Kingon, H. Kohlstedt, N. Y. Park, G. B. Stephenson, I. Stolitchnov, A. K. Taganstev, D. V. Taylor, T. Yamada, and S. Streiffer, “Ferroelectric thin films: Review of materials, properties, and applications”, J. Appl. Phys.100, 051606, 2006. |
[6] | W. Liu and X. Ren, “Large Piezoelectric Effect in Pb-Free Ceramics”, Phys. Rev. Lett.103, 257602 2009. |
[7] | Jaffe B., W. R. Cook Jr., Jaffe H., Piezoelectric Ceramics, (Academic Press, New York) 1971. |
[8] | R. E. Newnham,Properties of Materials: Anisotropy, Symmetry, Structure (Oxford University Press, New York) 2004. |
[9] | C. Z. Rosen, B. V. Hiremath, and R. Newnham, Piezoelectricity, (American Institute of Physics, New York) 1992. |
[10] | Dezhen Xue, Yumei Zhou, Huixin Bao, Chao Zhou, Jinghui Gao and Xiaobing Ren, “Large piezoelectric effect in Pb-free Ba(Ti,Sn)O3-x(Ba,Ca)TiO3 ceramics”, J. Appl. Phys. 109, 054110, 2011. |
[11] | N. Guo, P. Cawley, and D. Hitchings, “The finite element analysis of the vibration characteristics of piezoelectric discs”, Journal of Sound and Vibration, 159, 115–138, 1992. |
[12] | C.H.Huang,Y. C. Lin, and C. C.Ma, “Theoretical analysis and experimental measurement for res-onant vibration of piezoceramic circular plates”, IEEE Transactions on Ultrasonics Ferroelectrics and Frequency Control, 51, 12–24, 2004. |
[13] | D. Kybartas and A. Lukoˇ sevicius, “Analysis of coupled vibration mode in piezoelectric disks”, Ultragarsas, 4, 31–36, 2004. |
[14] | IRE Standard on Piezoelectricity (1961), IEEE Standard 179-1961, Institute of Electrical and Electronic Engineers, New York. |
[15] | IEEE Standard on Piezoelectricity (1987), IEEE Standard 176 -1987, Institute of Electrical and Electronic Engineers, New York. |
[16] | A.H. Meitzler, Jr. O’Bryan HM , H.F. Tiersten, “Definition and measurement of radial mode coupling fac-tors in piezoelectric ceramic materials with large variations in Poisson’s ratio”,IEEE Transactions on Son-ics and Ultrasonics, SU-20, :233-239, 1973. |
[17] | M. Onoe, H. F. Tiersten, and A. H. Meitzler, “Shift in the Location of Resonant Frequencies caused by Large Electro- mechanical Coupling in Thickness-mode Resonators”, J. Acoust. Soc. Am. 35, 36-42, 1963. |