K. Ch. Varada Rajulu, Anand Nandanwar, M. C. Kiran
Indian Plywood Industries Resarch and Training Institute IPIRTI, P. B. No 2273, Tumkur road, Bangalore
Correspondence to: K. Ch. Varada Rajulu, Indian Plywood Industries Resarch and Training Institute IPIRTI, P. B. No 2273, Tumkur road, Bangalore.
Email: |  |
Copyright © 2012 Scientific & Academic Publishing. All Rights Reserved.
Abstract
Smoke density of wood based panel materials like General purpose plywood, Marine Plywood(BWP grade), Medium Density Fibre Board (MDF), Bamboo Mat Board (BMB), Pre-laminated Particle Board (PPB) were measured using chamber method (ASTM D 2843-70). The specimens are tested inside closed chamber and readings of light transmission were taken at 5-seconds interval. Measurements were made in terms of loss of light transmittance through an accumulated volume of smoke. It was observed that pre-laminated particle board and general purpose plywood with 22.20% &22.47% of smoke accumulation area respectively resulted lower values as compared to other panel products such as marine plywood (BWP grade), MDF, BMB etc. A uniform rate of smoke build-up was recorded. This study provides the basis for predicting the smoke production rate, time to ignite (TTI), and Toxicity index which can be developed by combustion of the wood product.
Keywords:
Smoke Density, Wood-Based Panels, Smoke Production Rate, Fire Tests
Cite this paper:
K. Ch. Varada Rajulu, Anand Nandanwar, M. C. Kiran, "Evaluation of Smoke Density on Combustion of Wood Based Panel Products", International Journal of Materials and Chemistry, Vol. 2 No. 5, 2012, pp. 225-228. doi: 10.5923/j.ijmc.20120205.07.
1. Introduction
The smoke-limiting requirements in current building codes have been established as an attempt to regulate and to reduce the potential light-obscuration hazard from smoke generated by the interior building finish materials applied to walls, ceiling and floors in case of fire[1]. These requirements are commonly based on the results from tests devised principally for measuring comparative surface flammability. Unfortunately the relationship between the results of such tests and the visual-obscuring qualities of smoke are not well established. The most common method for smoke suspension measurements today employs a light source and a photoelectric cell, so that the electrical output of the cell may be used as a measure of the attenuation of light by smoke[2,3]. In previous study, an attempt was made to relate the smoke density rating for a variety of building materials with visual and photoelectric observations in a chamber which is computer interfaced[4-8].The immediate objectives of the present study is to measure smoke density under prescribed chamber method as per ASTM D 2843[9], ASTM F814[10] and ASTM D 618 [11]in standardized exposure conditions and evaluate the appropriate optical properties of smoke which obstruct human vision in building fires, without regard to the chemical nature of the smoke or fundamental processes of its generation. The effects of the smoke produced by a fire depend on the amount of smoke produced and on the properties of the smoke. With respect to defining the hazard when a person is trapped in a room where smoke is being generated or accumulated, three important aspects should be considered: 1. Maximum smoke accumulated quantity from a given area of material under the prescribed exposure. 2. Maximum smoke accumulation rate represents how quickly the smoke level increased as averaged over a time period (2min). 3. Time to reach a prescribed smoke density represents the time period prior to attaining a critical smoke level. Approaches have been made to predict effects of smoke in fires[12,13].Smoke is generally considered to be the gaseous products of burning organic materials in which small solid and liquid particles are also dispersed. The major cause of the loss of life in a fire involving wood appears to be the generation of carbon monoxide through thermal break-down of cellulose, partial oxidation of carbon, nitrogen oxides, and hydrogen based chemicals. The rate of thermal degradation of wood depends upon the heat transfer through the wood, type of char formed and the rates of diffusion of the gaseous decomposition products and degradation of products during their passage through the char.This research article presents experimental results on smoke emission for a variety of wood based panel materials such as general purpose plywood, marine plywood/BWP grade, MDF(medium density fibre board), BMB (bamboo mat board) and PPB(pre-laminated particle board)of 12mm thickness. Which are most commonly used in applications such as partitions, cupboards, furniture’s, etc.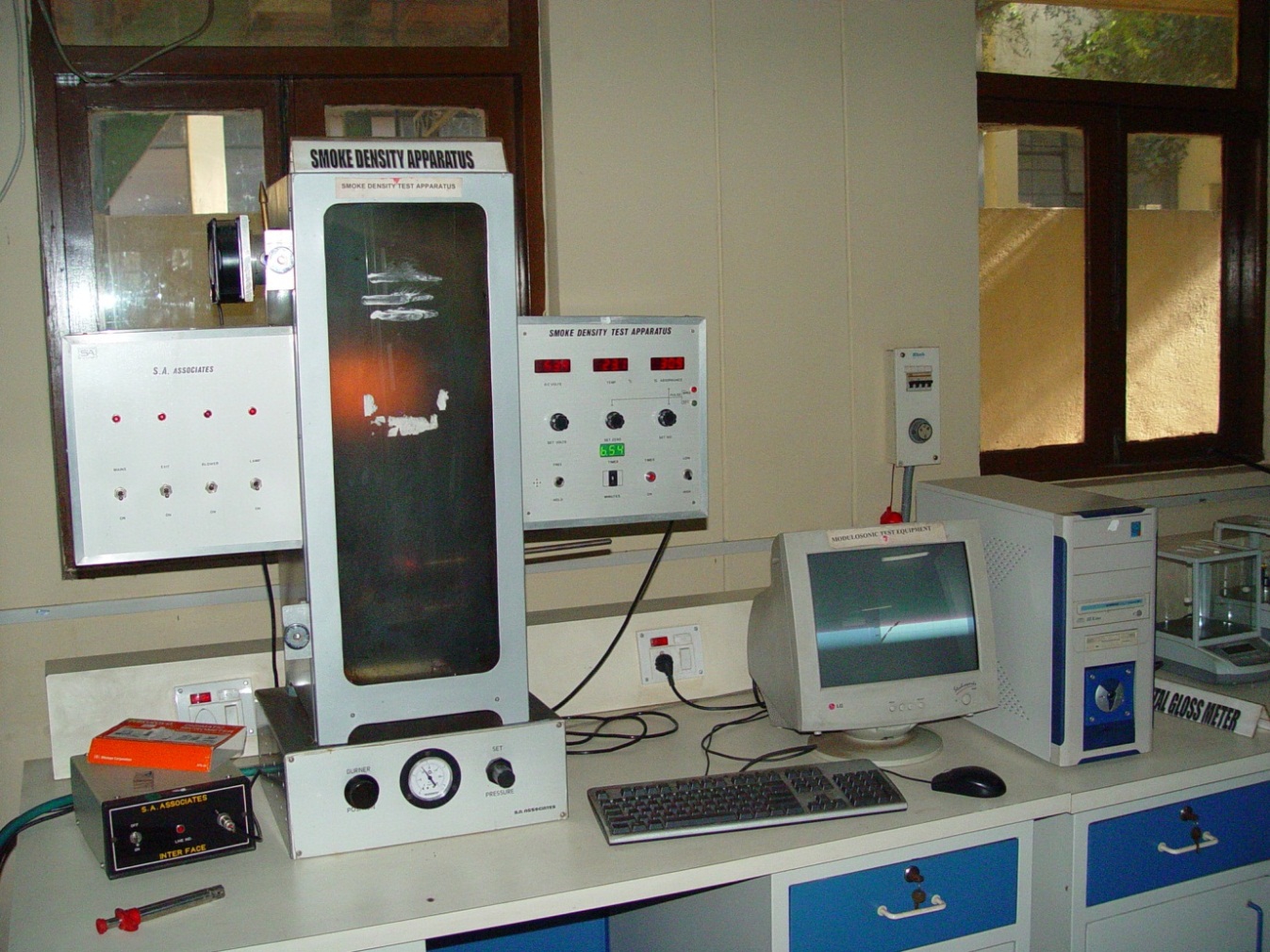 | Figure 1. Computer interfaced Smoke density equipment |
2. Experimental Procedure
The method of measuring smoke density using simple light transmission measurements has been developed by the Rohm and Haas Company. In this method, test apparatus consists of a smoke chamber with a light source located on one side. The light beam traverses the 300mm path through the chamber and strikes a photoelectric cell located on the opposite wall. The specimen was burned inside the closed chamber, and light transmission was recorded at 5-seconds interval. These data were plotted against time, the smoke production rate (slope of the curve) and the total smoke produced (area under the curve) was determined. The maximum smoke density was also read from the curve.Samples of size 25x25x12mm different types of wood based panel materials were conditioned at 27±2OC and 65±5%relative humidity for unless constant mass was obtained. After conditioning the samples were tested at controlled environment of temperature 27± 2OC and 65±5% relative humidity.The specimen were then placed on the supporting metal screen (wire mesh) and burned in test chamber as shown in fig.1.The flame was generated using a propane burner operated at pressure of 276kPa (40psi). The size of 300x300x790 mm test chamber is instrumented with a light source, d.c.voltage at 5mV, a photoelectric cell, 25mm high ventilation openings around the bottom and a meter to measure light absorption horizontally across the 300mm light beam path. The test specimen was exposed to flame for duration of 9min and the smoke generated was trapped in the chamber in which combustion occurs.
3. Results and Discussion
A dedicated calibration was performed using reference samples whose density was previously determined by measuring the volume and mass by a balance with an accuracy of 0.001g. Sample of thickness is about 12 mm were taken for samples viz. MDF, BMB, PPB etc. 4specimenswere taken for determining smoke density. Density and volume of different types of panel products are given in table1.Table 1. Density and volume of wood panel materials |
| Name of the Sample | Density(g/cc) | Volume (cm3) | General purpose plywood | 0.763 | 9.355 | Marine Plywood(BWP grade) | 0.755 | 7.965 | MDF | 0.759 | 8.103 | BMB | 0.849 | 9.556 | PPB | 0.826 | 8.631 |
|
|
The reduction of the light transmittance caused by smoke was converted to specific optical density using the relation:Ds= G log10(100%/T)where,T is the light transmission (%),Ds is maximum smoke density G is geometrical factor for the chamber (=132), the optical path length of the light beam and the exposed specimen surface area.Measurements were made in terms of loss of light transmittance through a collected volume of smoke and effluent of a test specimen produced in a fixed volume chamber under controlled standardised conditions. The burning conditions were simulated by the smoke density chamber: radiant heating in the absence of flaming in the presence of supporting radiations.Generally, wood based panels are hygroscopic in nature at high humidity products absorb moisture and thereby increase in density and vice versa. From table 1 it is observed that density of BMB is more than other wood composite materials. From the results it is observed that the general purpose plywood has low smoke density, in comparison with other materials studied. The results of smoke density of different panel products are given in table2.One can observe from the table 2 that the major wood and BMB which are used for exterior and interior applications of building materials shows uniform rate of smoke build-up in the chamber. This is evidenced by almost similar time taken to achieve maximum density (Ds) in all samples except MDF. This may be the fact that the MDF having fibres, which catches fire easily and start charring at early stage.Almost similar trend of Absorption % versus time curves was observed for all tested panel products as shown in fig.2. A linear increase (Except MDF) in smoke generating process was observed and approach to final reading, representing maximum accumulated smoke. During and after a typical test smoke was disappears due to settling and coagulation, the rate being greater at higher concentrations. No adjustments were made to the measurements for these losses, since it may be supposed that a similar, though generally not identical process of smoke build-up occurs in chamber or room of other size. It may be concluded from the above results that the pre-laminated particle board as well as general plywood resulted lower values of the specific optical density of smoke generated.Table 2. Results of smoke area, maximum Smoke density and time |
| Name of the Sample | Maximum smoke accumulation (area) % | Maximum smoke density(Ds) | Time (T), Min | General purpose plywood | 22.42 | 40.59 | 5:15 | Marine Plywood(BWP Grade) | 36.57 | 62.81 | 5:45 | MDF | 30.36 | 55.03 | 2:45 | BMB | 24.29 | 47.15 | 5:00 | PPB | 22.20 | 47.11 | 5:45 |
|
|
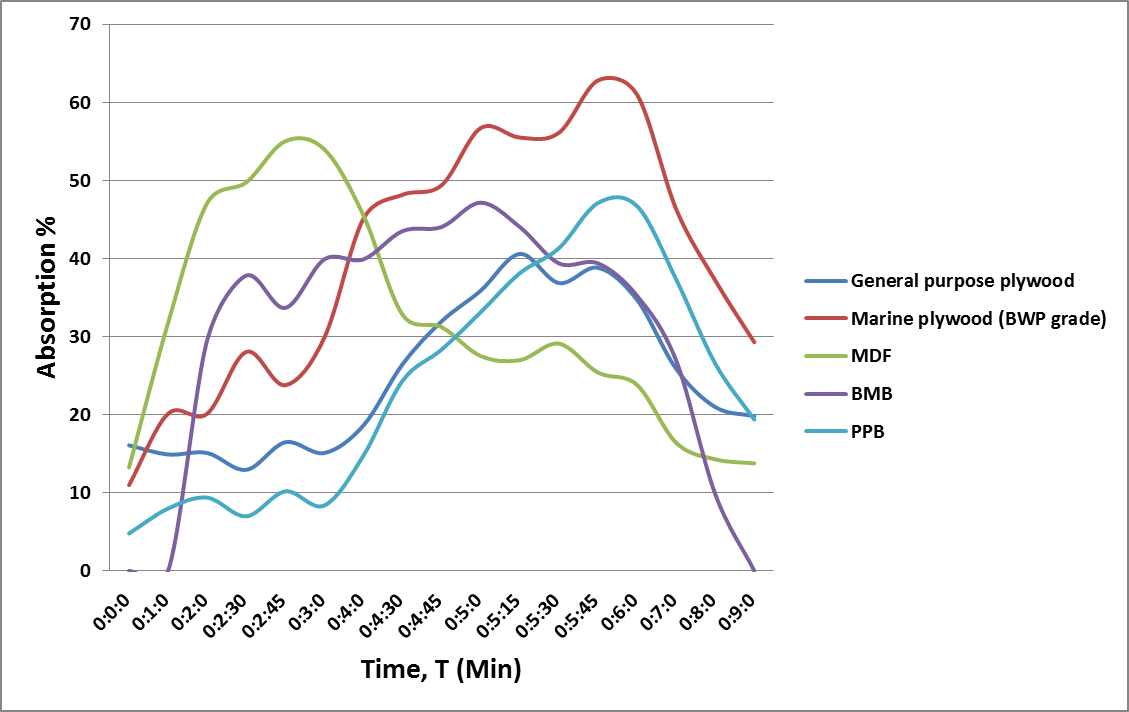 | Figure 2. Light absorption in various samples with time |
4. Conclusions
The results clearly presenting the reaction of smoke optical density properties of wood based products. Specific optical density provides the basis for predicting the smoke production rate, time to ignite (TTI), and Toxicity index which can be developed by the same product in the other fire involved areas in the other enclosure volumes. General purpose plywood has lowest smoke density (40.59) and marine plywood has highest smoke density (62.81) in comparison with other studied materials. Results were presented which illustrate the variation in smoke production between materials. This new knowledge can be used to estimate the smoke toxicity and conventional toxicity index for wood and wood based panel products.
ACKNOWLEDGEMENTS
The authors would like to sincerely thank to Director, IPIRTI, Bangalore for permission and for providing necessary research facilities.
References
[1] | Baker, Dennis S.,” Wood in fire, flame spread and flame retardant treatments”, Chem. Ind. (London), 14, 485-490 (1981). |
[2] | Stoecker, Wilbert F., “Smoke density measurement”, Mech. Eng. 72,793-798,(1950). |
[3] | Dev, “Studies on fire retardant cum preservative composition”. J. Timber Dev. Assoc. India, 28, 30-33, (1982). |
[4] | Lee, Kin chung, “Fire-resistant coating compositions”, U.K. Pat Appl. G.B, 2088400, (1980). |
[5] | Pearson, Geenn A., “Fire retardant composition”, U.S. Pat. 4,427,745, (1984). |
[6] | Wittbecker F.W., “Smoke Detectors and Escape Times”, Fire Europe, 4, 5-8, (1997). |
[7] | Bankston C.P., Cassanova R.A., Powell E.A.,Zinn B.T., “Initial Data on the Physical properties of Smoke Produced by Burning Materials under Different Conditions”, J.F.F., 7,165,(1976). |
[8] | Jin T., “Visibility through fire smoke” journal of fire and flammability, 9,135-155, (1978). |
[9] | “Standard Test Method for Density of Smoke from the Burning or Decomposition of Plastics”, ASTM D2843, (2004). |
[10] | “Test Method for Specific Optical Density of Smoke Generated by Solid Materials for Aerospace Applications”, ASTM F814 - 84B, (1995). |
[11] | “Standard Practice for Conditioning Plastics for Testing”, ASTM D618, (1994). |
[12] | ISO 13344 Determination of the Lethal Toxic Potency of Fire Effluents. |
[13] | SO TR 13387,1-8: The application of fire performance concepts to design objectives; Design fire scenarios and design fires; Assessment and verification of mathematical fire models; Initiation and development of fire and generation of fire effluent; Movement of fire effluent; Structural response and fire spread beyond the enclosure of origin; Detection, activation and suppression; Life safety: Occupant behavior, location and condition. |