Atanda P. O. 1, Olorunniwo O. E 1, Alonge. K 1, Oluwole O. O. 2
1Materials Science and Engineering Dept., Obafemi Awolowo University, Ile-Ife, Nigeria
2Mechanical Engineering Dept., University of Ibadan, Oyo State, Nigeria
Correspondence to: Oluwole O. O. , Mechanical Engineering Dept., University of Ibadan, Oyo State, Nigeria.
Email: |  |
Copyright © 2012 Scientific & Academic Publishing. All Rights Reserved.
Abstract
This work investigated the effects of Bentonite and Cassava starch binders on foundry moulding sand. The two binders were applied separately to silica sand in different proportions and also as a mixture in different proportions as well. The effects of these various additions on foundry moulding sand were investigated by conducting out various tests as permeability, moisture content, green compressive and green shear strength, dry compressive and dry shear strength as well as the AFS of the sand. The results showed that bentonite had better binding characteristics than cassava starch but a mixture of both in equal proportions gave a range of excellent mould properties that could be exploited in making moulds for different weights of castings. Permeability for the two binders decreased as the quantity of binder increased.
Keywords:
Cassava Starch, Bentonite, Moulding Properties, Silica Sand
Cite this paper:
Atanda P. O. , Olorunniwo O. E , Alonge. K , Oluwole O. O. , "Comparison of Bentonite and Cassava Starch on the Moulding Properties of Silica Sand", International Journal of Materials and Chemistry, Vol. 2 No. 4, 2012, pp. 132-136. doi: 10.5923/j.ijmc.20120204.03.
1. Introduction
1.1. Moulding sand
Sand is the principal moulding material used for all types of castings, irrespective of whether the cast metal is ferrous or non-ferrous. This is because it possesses good properties such as refractoriness, mouldability, permeability, collapsibility, chemical resistivity, etc that are vital to foundry applications[1,2].The principal ingredients of moulding sands are: Silica sand grains, Clay (bond) and Moisture. The silica sand grains are of paramount importance in moulding sand because they impart refractoriness, chemical resistivity, and permeability to sand. They are specified according to their average size and shape[3]. The finer the grains, the more intimate will be the contact and the lower the permeability. Clay on the other hand, imparts the necessary bonding strength to the moulding sand so that after ramming, the moulding does not lose its shape. However, as the quantity of the clay is increased, the permeability of the mould is reduced. Clay is defined by the American Foundry Society (AFS) as those particles of sand (under 20 microns in diameter) that fail to settle at a rate of 25mm per minute, when suspended in water. Clay consists of two ingredients: fine slit and true clay. Fine silt is a sort of foreign matter of mineral deposit and has no bonding power. True clay supplies the necessary bond. Under high magnification, true clay is found to be made up of extremely minute aggregates of crystalline particles, called clay minerals. These clay minerals are further composed of fluke –shaped particles, about 2 microns in diameter, which are seen to lie flat on one another[3].Clay acquires its bonding action only in the presence of the requisite amount of moisture. When water is added to clay, it penetrates the mixture and forms a microfilm which coats the surface of each flake. Moulding sand is classified as either natural or synthetic sand. The natural moulding sand is also called green sand. It is taken from river bed or dug out from pits, and it contains the binder which is used in the as-received condition with water added. It contains from 5-20% binder and about 5-8% water may be added.Green sand moulding is the least expensive, fastest, and most common of all the currently available moulding methods. The mixture of sand and binder can be used immediately after the mixing process that coats the sand grains. Although the time taken to shape the mould is of importance in some cases, for the purposes of this article, the forming process can be considered to be almost instantaneous. The synthetic moulding sand on the other hand, is made in the foundry by mixing a relatively clay free sand with selected clay binder like bentonite. Water and other additives may be added as may be required.Bentonite ClayBentonite is a type of clay generated from the alteration of volcanic ash, consisting predominantly of montmorillonite. Bentonite is composed of plate-silicate minerals, and belongs to the group of minerals known as alumino-silicates. It present strong colloidal properties and increases its volume several times when coming into contact with water, creating a gelatinous and viscous substance. The special properties of bentonite are swelling index, water absorption ability, viscosity and thioxiotropy which make it very valuable clay for a wide range of uses and applications. It is used as a binder material in the preparation of moulding sand for production of steel and non-ferrous casting. The adhesive and cohesive forces of the sand-bentonite-water mixtures are evaluated by the resistance of the mixture to compression or shear in the green in dry state showed that the mechanical properties alone cannot predict the performance of adequately bonded aggregate for the production of defect-free castings. Extracted bentonite is distinctly solid, even with a moisture content of approximately 30%. The material is initially crushed and, if necessary, activated with the addition of soda ash (Na2CO3). Bentonite is subsequently dried to reach a moisture content of approximately 15%. According to the final application, bentonite is either sieved (granular form) or milled (into powder and super fine powder form). For special applications, bentonite is purified by removing the associated gangue minerals, or treated with acids to produce acid-activated bentonite (bleaching earths), or treated with organics to produce organo-clays. The unique properties of bentonite yield green sand moulds with good flowability, compatibility and thermal stability for the production of high quality castings[4].
1.2. Starches
Starches are extensively used in steel foundries and to a lesser degree in iron and nonferrous foundries. They are derived from corn and potatoes. Many varieties of cereals and starches are available, but their selection is a matter of their cold water solubility[5]. This chemical property will determine the water-absorbing characteristic at the muller and, ultimately, its effect on high-pressure moulding. The flour produced from the cassava plant, which on account of its low content of noncarbohydrate constituents might well be called a starch, is known in world trade as tapioca flour. It is used directly, made into a group of baked or gelatinized products or manufactured into glucose, dextrins and other products as reported in FAO journal, society of chemical industry[6].Starchy foods have always been one of the staples of the human diet. They are mostly consumed in starch-bearing plants or in foods to which commercial starch or its derivatives have been added. The first starch was probably obtained from wheat by the Egyptians for food and for binding fibres to make papyrus paper as early as 4000-3500 BC[5].Starches are now made in many countries from many different starchy raw materials, such as wheat, barley, maize, rice, white or sweet potatoes, cassava, and sago palm. Although they have similar chemical reactions and are usually interchangeable, starches from different sources have different granular structures which affect their physical properties. Starch and starch products are used in many food and non-food industries and as chemical raw materials for many other purposes, as in plastics and the tanning of leather. Non-food use of starches - such as coating, sizing and adhesives - accounts for about 75 percent of the output of the commercial starch industry[7]In many industrial applications, there is competition not only among starches from various sources but also between starches and many other products. Resin glue has largely replaced starch in plywood industry because of its greater resistance to moisture. Resin finishes are used extensively in the textile industry and natural gums compete with starches in paper making. Nevertheless, the continuous development of new products has enabled the starch industry to continue its expansion. The growth of the starch industry in the future appears to be very promising, providing the quality of products and the development of new products permit them to compete with the various substitutes.The principal user of instant starch or pregelatinized starch are the paper and foundry industries, while smaller quantities of pregelatinized modified starches form the basis of many cold water pastes including wall paper paste powder, in oil-well drilling, and in the production of certain types of instant dessert. Bentonite is commonly used as binder in foundries[8,9,10]. The thermal stability of bentonite in foundry sandf has also been studied[11].The effect of various other clays as binders have been investigated[8-14] including the effect of moisture on moulding sand[15] but there is a dearth of literature on the use of cassava starch as binder or as an additive binder with bentonite. This work seeks to study these.
2. Experimental Procedure
2.1. Materials
The silica sand used for this work was collected from the deposits of processed sand used by a glass manufacturing company in Ondo State of Nigeria, the cassava starch was collected from a cassava starch manufacturer, in Oyo State, Nigeria, while the Na- based bentonite was imported from Baroda, India. The work was carried out at the foundry Laboratory of Nigeria Machine Tools Limited, Osogbo, Osun State, Nigeria.
2.2. Methods Used
2.2.1. Sieve Analysis
The silica sand was taken to a stack of sieves arranged in descending order of magnitude on a shaking table that is responsible for the vibration of the sieves that aids in sieving. The sizes of the sieves in the stack are listed as follows: 1.4mm, 1.0mm, 850μm, 710μm and 600μm respectively and their arrangement was in descending order of magnitude to allow lower sizes of the silica sand percolate through easily. The arranged sieves were then placed on a sieve shaker whose function is to cause vibration of the stack of sieves and aid in allowing respective sizes of the silica sand to percolate through the sieves. The vibration is allowed to go on for between 6-7 minutes, the timing being done with the aid of a stop-watch.
2.2.2. Weighing, Mixing and Mulling of the Samples
Various samples of silica sand, bentonite, cassava starch and water were weighed using an electrical weigh balance as shown in table 1. Seven sets of samples were prepared from each binder mix. For the bentonite and cassava starch their percentages were increased in the steps of 3% from 3 to 21% for every 100% silica sand used, whereas equal volume of water (4%) was used throughout the experiment. Samples of silica sand as shown in the tables 1 were mixed and mulled appropriately in the laboratory sand mixer/muller for about ten minutes in other to allow the samples to mix together properly to avoid segregation of some of the materials in each samples and the specimen were prepared according to ASTM sand specimen specifications. The moisture content, permeability, green compression Strength, green Shear Strength, dry compression and shear, and mould hardness tests were carried out.Table 1. Percentage of bentonite and cassava starch used for every 100% silica sand |
| Binder | Samples (%) | | I | II | III | IV | V | VI | VII | Bentonite (B) | 3 | 6 | 9 | 12 | 15 | 18 | 21 | Cassava (C) | 3 | 6 | 9 | 12 | 15 | 18 | 21 | Bentonite and Cassava | 1.5B+1.5C | 3B+3C | 4.5B+4.5C | 6B+6C | 7.5B+7.5C | 9B+9C | 10.5B +10.5C |
|
|
3. Results and Discussion
3.1. Results
The results of the various sand tests are presented in Figures1to 6. Figure 1 shows the variation of moulding strengths with increasing bentonite content in the sand. There is a general trend of increasing strength with increasing binder content. Dry compressive strength was observed to be greater than green compressive strength. Also, the dry shear strength was also greater than the green shear strength. The compressive strengths were greater than the shear strengths.Figure 2 shows the variation of moisture content in the moulding sand with increasing bentonite binder content. Here, there is a decreasing trend of moisture content with increasing bentonite content. The same decreasing trend was observed in Figure 3 with sand permeability in sand as bentonite content increased in the sand.Figure 4 shows the variation of moulding strength with increasing cassava starch content as binder. The results show a general increasing trend of strengths with increasing starch content with the exception of the green compressive strength where after 9% percentage starch additive, the green compressive strength began to drop and continued dropping. The variations of moisture content and sand permeability with increasing starch additive are presented in Figures 5 and 6 respectively. Permeability showed a Figure Acronyms: gcs- green compaction strength; gss-green shear shear strength; dcs-dry compaction strength; dss-dry shear strength decreasing trend with starch content. However, moisture content showed a decreasing trend up to a starch content of 12 % after which it started rising till 21 % starch content when the experiment was stopped. | Figure 1. Trend of moulding strengths with increasing bentonite in moulding sand |
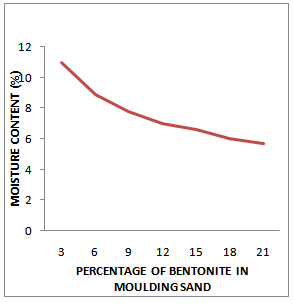 | Figure 2. Trend of moisture content in moulding sand with increasing bentonite content in moulding sand |
Figure 7 shows the variation of moulding strength with increasing cassava starch and bentonite additive. The results show a general increasing trend of strengths with increasing binder content for the green moulding sand. For dry moulding sand, the strengths increased until 6% binder additive after which the strengths began to drop until the end of the test at 21% binder additive. Sand permeability decreased with increasing binder content as presented in Figure 8. However, moisture content ( Fig. 9) decreased up to 2% binder content after which moisture content increased till the end of the experiment at 21% binder content.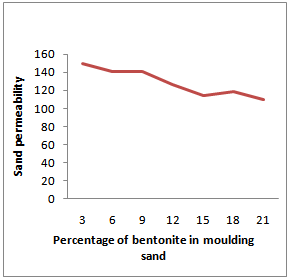 | Figure 3. Trend of moulding sand permeability with increasing bentonite content |
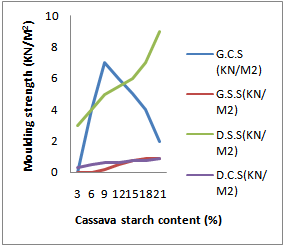 | Figure 4. Trend of sand strengths with increasing cassava starch content in moulding sand |
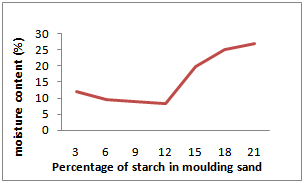 | Figure 5. Trend of moisture content with increasing starch content of moulding sand |
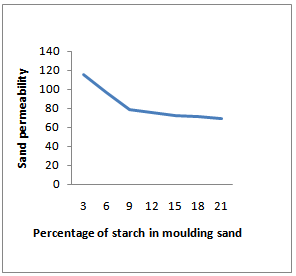 | Figure 6. Trend of sand permeability with increasing cassava starch content of moulding sand |
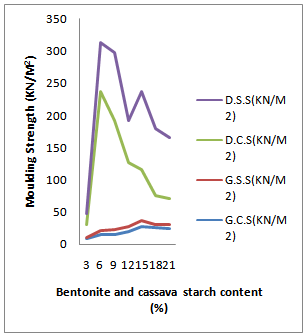 | Figure 7. Trends of moulding strengths with increasing bentonte and starch content of of moulding sand |
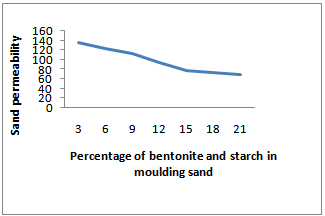 | Figure 8. Trend of sand permeability with increasing bentonte and starch mixture content in moulding sand |
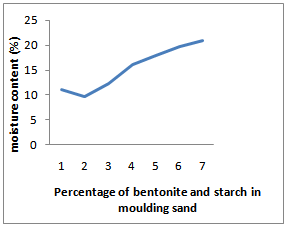 | Figure 9. Trend of moisture content with increasing bentonte and starch mixture content in moulding sand |
3.2. Discussion of results
From figures 1,4 and 7 the values of green compressive strength, green shear strength, dry compressive and dry shear strength showed the binding ability of both the bentonite and cassava starch as binders either as combined binder or as single binder. The combined use of the two binders showed very high green and dry sand strengths. The use of cvassava starch alone showed the least moulding sand strength. Moisture content (figs. 2,5 and 9) for the three classes of binders used were seen to be within range for different percentages of the binders. However, for dry moulding sand, the moisture content would not be a sticking point especially for a mix of bentonite and cassava starch. Permeability (Figs. 3, 6 and 8) for the three classes of binder were observed to be within range. In the case of dry compressive strength, the dry compressive strength increases as the percentage of starch increases when starch alone is used as binder. The dry and green compressive strength increases with a small value as the percentage of starch is increases, this little increment is due to the coarse nature of starch in moulding sand.
4. Conclusions
Bentonite had much better binding characteristics when used alone as a binder than cassava starch. Cassava starch had very poor binding characteristics. However, usage of mixture of bentonite and cassava starch in equal proportions gave a whole variety of good moulding properties which could be beneficial for different weights of castings. Permeability decreased with increase in the percentage of any of the binders used.
References
[1] | Scaffer E. and James, P. (1995), The Science and Design of Engineering Materials, 1st ed., Longman, London. |
[2] | Sarkar, A.D.,(1967), Mould and core material for the steel foundry, pergamon press, London. |
[3] | AFS(1963)Foundry handbook, seventh edition, American foundrymen’s society, Des plaines, III. |
[4] | http://en.wikipedia.org/wiki/bentonite, accessed January 2009. |
[5] | Dufour, L. D. (1994); Cassava in Amazonia: Lessons in Utilizatio and Safety From Native Peoples. In: Cassava Safety; Acta Horticulturae 375; pp175 |
[6] | Higgins R.A. (1970). ‘Elements of Materials and Engineering’. 6th edition, English Univ. Press, London. |
[7] | Ugwu F.M. and Odo M.O. (2008), ‘Effect of Cassava Variety on the Quality and Shelf Stability of Soy-Garri’. Pakistan Journal of Nutrition 7 (2): 381-384 |
[8] | Pearce.J.T.H (2012) Greensand Moulding Technology for High Volume Castings Production’ www.tiche.org /tiche17/file/ |
[9] | Strobl.S(2000) ‘Fundamentals of green sand preparation and control’ www.simpsongroup.com/tech/rpt.sales.Modern Casting Fundi Expo 2000,p.8 |
[10] | A. Abdullah, Shamsuddin Sulaiman, B.T. Hang Tuah Baharudin, Mohd Khairol H. Arifin, T.R. Vijayaram (2011)‘ The Effect of Bentonite Clay on Green Compression Strength for Tailing Sands from Old Tin Mines in Perak State, Malaysia for Making Green Sand Casting Mould’ Key Engineering Materials- Composite Science and Technology;Volumes(471 – 472),p.769-774. www.scientific.net/KEM.471-472.769 |
[11] | myhomefoundry.com (20120Green sand for moulding; Pros & Cons’ www.myhomefoundry.com/casting_info/Green_ sand_06.pdf |
[12] | George J. Vingas And Arthur H. Zrimsekj(2012)Thermal Stability Of Bentonites In Foundry Molding Sand’ 368 Thirteenth National Conference On Clays And Clay Minerals,367-380 |
[13] | Ibitoye, S.A and Afonja, A.A (1997a) “ Adaptation of Ipetumodu potter’s clay to foundry use:1. Moulding properties of as mined and silica mixed potter’s clay.” Ife Journal of Technology,7(1):17-22 |
[14] | Ibitoye, S.A and Afonja, A.A (1997b) “ Adaptation of Ipetumodu potter’s clay to foundry use:2.Development of potter’s clay bound synthetic moulding sand.” Ife Journal of Technology, 7(1):39-45 |
[15] | Atanda.P.O, Oluwole.O.O And Ogale.O.T(2008) “Adaptation Of Ushafa Clay, Abuja, as A Suitable Replacement For Bentonite In The Foundry Industry’Journal of Raw Materials Research, Raw Materials Research and Development Council,ABUJA.5(1&2),53-60 |
[16] | EHOW(2012) ‘Effect of moisture on moulding sand’ http://www.ehow.com/facts_7940958_effect-moisture-content-molding-sand.html |