Anusha PB, Disha Shetty, Reshma Marina D’Almeida, Shramika, Chaithra Shetty
Department of Electrical and Electronics Engineering, St. Joseph Engineering College, Mangaluru, India
Correspondence to: Anusha PB, Department of Electrical and Electronics Engineering, St. Joseph Engineering College, Mangaluru, India.
Email: |  |
Copyright © 2017 Scientific & Academic Publishing. All Rights Reserved.
This work is licensed under the Creative Commons Attribution International License (CC BY).
http://creativecommons.org/licenses/by/4.0/

Abstract
In this present era, people live a very busy life. People in cities have irregular and long working times. In such a situation a person will always find ways of saving time. Household chores are the ones that are most dreaded upon. And cleaning a home tops the list. It is not only time consuming, but also its very tiring. Especially for working women it becomes difficult to handle both home and office work together. A new service robot designed for cleaning tasks in home environments is introduced. System has three subsystems: electrical, software and mechanical of which sensors (opponent and light) and motors are the electrical and mechanical subsystems respectively and the LabVIEW-myRIO module is the software subsystem which is the brain of the robot. myRIO is programmed to accept inputs from the sensor and thereby control the wheels of the robot by a motor driver to avoid collision. The vacuum cleaner performs the cleaning process.
Keywords:
LabVIEW-myRIO, Motor driver, Vacuum cleaner
Cite this paper: Anusha PB, Disha Shetty, Reshma Marina D’Almeida, Shramika, Chaithra Shetty, LABVIEW Operated Robotic Vacuum Cleaner, International Journal of Internet of Things, Vol. 6 No. 2, 2017, pp. 43-46. doi: 10.5923/j.ijit.20170602.07.
1. Introduction
In recent years, robotic cleaners have taken major attention in robotics research due to their effectiveness in assisting humans in floor cleaning applications at homes, hotels, restaurants, offices, hospitals, workshops, warehouses and universities etc. Basically, robotic cleaners are distinguished on their cleaning expertise like floor mopping, dry vacuum cleaning etc. Some products are based on simple obstacle avoidance using infrared sensors while some utilize laser mapping technique. Each cleaning and operating mechanism of robotic floor cleaners has its own advantages and disadvantages. For example, robots utilizing laser mapping are relatively faster, less time consuming and energy efficient but costly, while obstacle avoidance based robots are relatively time consuming and less energy efficient due to random cleaning but less costly. Countries like Pakistan are way back in manufacturing robotic cleaners. Importing them from abroad increases their costs. The main objective of this work is to provide a substantial solution to the problem of manufacturing robotic cleaner utilizing local resources while keeping it low costs.
2. Block Diagram
2.1. DC Power Unit
This block consists of a 12V rechargeable battery and a voltage regulator. The LM7805 IC connected to the output of the battery, provides a constant output of 5V regardless of the load in the circuit. Thus the power requirements of the system are strictly met without putting the system at risk during high loads. | Figure 1. Basic block diagram |
2.2. my-RIO
myRIO is real time embeded evolution board made by national instruments. It is a real time data acquisition and data interfacing device. It has inbuilt FPGA processor, ADC, DAC, filters, timers and counters. It is WIFI compatible and hence it can be used as a wireless data acquisition device. It is the heart of the system which makes our robot automatic. It reads the signals from three IR sharp sensors. It then processes this data and controls the movement of robot by giving signals to the motor driver.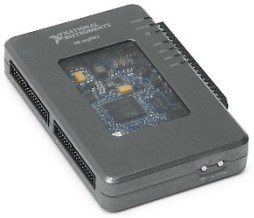 | Figure 2. my RIO image |
2.3. IR Sharp Sensors
The GP2Y0A21 sharp IR sensor used in our project provides great way to add obstacle avoidance and motor control feature to our robot. In this project it operates at 5V and current consumption is about 30mA with a distance of 10cm to 80cm. An analog voltage indicating distance is the output of the sensor which is fed to myRIO.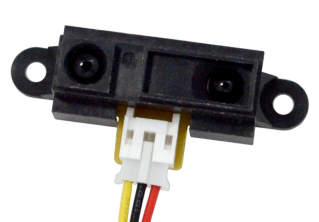 | Figure 3. IR Sharp Sensors |
2.4. Motor Driver Circuit
A motor driver is used to control the two geared DC motors. It can make a motor rotate in either clockwise direction or in anti-clockwise direction according to the control inputs given to it. myRIO provides the control signals to the motor driver IC L293D according to the output of IR sensors. Direction of the rotation of the motor is decided as per the input pins of the L293D.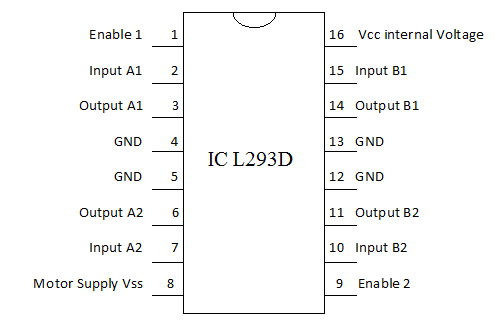 | Figure 4. Pin diagram of ICL293D |
Table 1. Direction of motor rotation according to IC input 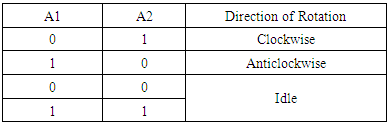 |
| |
|
3. Flowchart
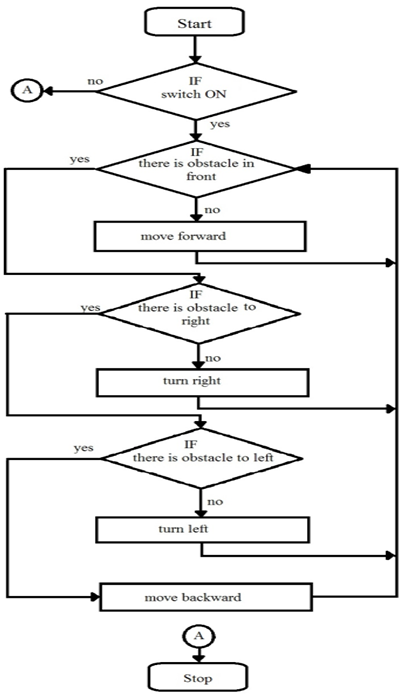
4. Description
Overall designing of the proposed vacuum cleaner revolves around Shape, Sensors, Batteries, Suction, and Motors. Developed vacuum cleaner robot is a square of side 10 inch and height of 4 inch. All robotic vacuum cleaners that are out in the market today are disk shaped. The problem with that is that they cannot clean the corners of rooms very well. Since our main objective was to improve the overall cleaning efficiency, we decided to change the shape from a circle to a square with rounded edges. The rounded edges will allow the vacuum to have the effective mobility to work its way through tight spots and the square shape is for effective cleaning of corner. This robot is robust enough and made to work on normal environment. Base of the vacuum is made of aluminium plank. It is selected such that can carry its required weight. Aluminium is used to make light, rigid and is known for its resistance, toughness and required modification is made to provide electrical insulation.Two dc geared motors are used as the robot base motors which is driven by motor driver IC L293D. The L293D is a quadruple high-current half-H driver. The L293D is designed to provide bidirectional drive current of up to 600mA at voltages from 4.5V to 36V.myRIO is the heart of our project for interfacing the robot. This unit recognises the data from the sensors processes the signal and thereby executes the program depending on the data and guide the motor driver and other unit to perform the intended task and control the complete functioning of the unit. It will send appropriate data to each and every unit requested by the user and will enhance the robot to take the appropriate function. Sensors are mounted at left, right and front of the robot, which detects the obstacle in its way and moves in defined path.Vacuum suction to collect dust is an important part of our project. 12V dc 0.25A exhaust fan is used as sucking unit with conical shaped structure in front. Conical shape is chosen so as to reduce pressure near fan and in rise pressure in pipe fixed to suck debris falling on floor. Two flat brushes are provided concentrating towards opening of pipe for effective cleaning.
5. Operation
The vacuum cleaner can be operated by manually carrying it to the room to be cleaned and pressing the ‘start’ switch. When switch is turned on 12v dc battery provides power to myRIO. myRIO being the controller of the vacuum cleaner receives input from GP2Y0A21 sharp IR sensor. IR sensors are mounted at front, right and left of the robot and input is fed in parallel to myRIO. If the IR sensor senses an obstacle, then it gives a maximum output and a low output otherwise. Hence obtained analog input is converted to binary, then into decimal and the movement of the robot is decided. Truth table of oeration is shown in Table 2.Table 2. Truth tabl 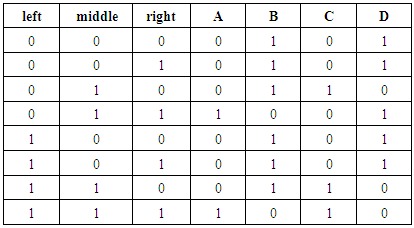 |
| |
|
When dc supply is turned on fan of the vacuum cleaner gets energised. As robot move forward flat brush connected in front of the robot gathers dust lying on the floor vacuum suction unit sucks it up and is collected inside conical structure. Mean while in water dropping unit motor brings water to the water dropping channel and water is spread and mopped using roller bush connected at the back of the robot.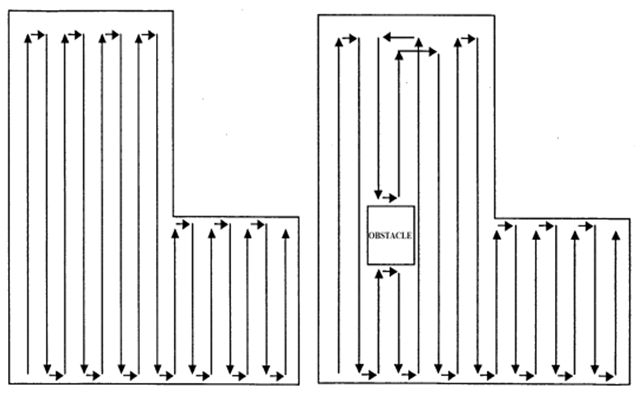 | Figure 5. Movement of Robot |
6. Application
1) Home automation is one domain that has been target of all robotics companies, large and small. Soon a time could come when you clean your home using a robot just like the one we've given life here. These could make the tiresome task of cleaning all those rooms, into a few minutes work. Cleaning your home would no longer be the same. 2) The robotic cleaner enhances the technology of cleaning and can be further used to integrate features of fast and effective cleaner by different other methods. As we can observe that development of comfort systems has found a new market for themselves and if these systems can be remotely operated, i.e. in the click of just one single button we have an entire smart home for us. 3) Gadgets like these prove instrumental in designing homes having all the facilities, and with the inclusion of more and more features like that, a new sound picture of future begins to develop. 4) Places like hospitals, restaurants and retirement homes can take the advantage of these devices where not much dirt is accumulated and can be cleaned easily with these devices.
7. Conclusions
The concept has proven to be an efficient way of saving time and helping physically disabled people. This system is especially beneficial to working women. As specified the user can switch on the device and go for any other work and the robot will automatically clean the floor by detecting and avoiding the obstacles on its way. my rio can be easily used to modify and enhance the various capabilities of any robot evolving its capabilities to explore new pathways of working efficiently. The IR sharp sensors and ir are effective in movement of robot around cliff and boundaries of the room. These sensors, with, greater resolution can give the correctness of movement to degrees which lead to smooth cleaning of the room. Nonetheless, there are still new ideas to improve the developed system and to add new functionality to it. Gsm module can be used to send message that, the robot has done the cleaning task. Camera can also be used for navigation purposes. The advent of these ideas can lead to a breakthrough in modern domestic robot industry.
ACKNOWLEDGEMENTS
We owe our profound gratitude to the people whose kind consent and guidance helped us to complete this work successfully.We would also like to thank those who have always been with us extending their support, precious suggestions, guidance and encouragement throughout this work. Last but not the least we would like to thank Almighty God whose blessings facilitated the completion of our work.
References
[1] | Jordi Palacín, Member, IEEE, José Antonio Salse, Ignasi Valgañón, and Xavi Clua, IEEE transactions on instrumentation and measurement, vol. 53, no. 5, Spain 2004, pp. 1420-1423. |
[2] | www.datasheetcatalog.com |
[3] | Robovac (Autonomous Robotic Vacuum Cleaner) - a survey report. |
[4] | NI my RIO guide from National Instruments. |