Apoorva S., Chaithanya, Rukuma S. Prabhu, Saiswaroop B. Shetty, Denita D’Souza
Department of Electrical & Electronics Engineering, St Joseph Engineering College, Mangaluru, India
Correspondence to: Apoorva S., Department of Electrical & Electronics Engineering, St Joseph Engineering College, Mangaluru, India.
Email: |  |
Copyright © 2017 Scientific & Academic Publishing. All Rights Reserved.
This work is licensed under the Creative Commons Attribution International License (CC BY).
http://creativecommons.org/licenses/by/4.0/

Abstract
The world today faces major garbage crisis- the product of rapid economic growth, overcrowding, poor urban planning, corrosive corruption and political dysfunction. The present tried and tested methods of garbage collection have so far been proven ineffective. And the world today is looking at smarter ways of overcoming the garbage collection problem. This paper presents the Garbage Collector robot for foot path using Arduino microcontroller. The robot is built on a metallic base of size 50x40 cm which is powered by battery of 12V, 7.5Ah. The robot movement is controlled by programming the Arduino. The robot is designed to collect Garbage at foot path, public places (parks, schools and colleges), mostly cemented paths and beach. The robot cannot be used on muddy surfaces. The robot is built in such a way that, when it is started it will move on the path defined in the program. When it encounters the obstacle, depending on the conditions applied in the program the bot proceeds with further motion and then robot picks up the garbage.
Keywords:
Arduino, Swacch Bharat Abhiyaan, MSMWWs
Cite this paper: Apoorva S., Chaithanya, Rukuma S. Prabhu, Saiswaroop B. Shetty, Denita D’Souza, Autonomous Garbage Collector Robot, International Journal of Internet of Things, Vol. 6 No. 2, 2017, pp. 40-42. doi: 10.5923/j.ijit.20170602.06.
1. Introduction
Garbage is the major problem not only in cities but also in rural areas of India. It is a major source of pollution. Indian cities alone generate more than 100 million tons of solid waste a year. In 2000, India's Supreme Court directed all Indian cities to implement a comprehensive waste-management programme that would include household collection of segregated waste, recycling and composting. These directions have simply been ignored. No major city runs a comprehensive programme of the kind envisioned by the Supreme Court. It is not wrong to say that India is on verge of garbage crisis even though 9000crore rupees are allotted for the Swachh Bharath Abhiyan.There are already different type of garbage collection robots [1-3] like Robo-dumpster which mainly aims at collecting garbage from full cans and dispose it designated area and Dust cart which is designed to navigate through urban areas avoiding static and dynamic obstacle and waste door to door. These robots which are in use have various disadvantages like high implementation cost, not user friendly and aims at only collecting filled dustbins but not on collecting mechanism, etc. Also, Municipal solid waste workers (MSWWs) or refuse collectors, universally expose too many work related health hazards and safety risks, notably allergic and other diseases of the respiratory system. Health impacts could also entail musculoskeletal, gastro intestinal and infectious diseases as well as injuries caused by work-related accidents. Hence to overcome this major problem of waste collection Autonomous Garbage Collection robot is developed. It aims at providing automatic control to collect the garbage. It differentiates between static and dynamic obstacle and move accordingly as it programmed. It basically consists of sensors at different levels to detect the dynamic obstacle. It also disposes the garbage to a pre-specified place. If the trash bin is filled, it will be detected and the garbage will be disposed.
2. Methodology
In the present paper, the design of garbage collector robot uses engineering method. In sequence, the method is identification of the needs required. Then these needs are analysed to get specific components. These components are later integrated to get the desired output. The basic methodology is as shown in figure 3.1.The operation of the robot can be classified into three main categories. They are motion control of the robot, garbage collection and disposal of garbage.
2.1. Locomotion of the Robot
The robot can travel in the predetermined path by using a combination of motors, drivers, and sensors connected to the Arduino. This system consists of four geared motors of 30rpm each, motor drivers and three ultrasonic sensors. The ultrasonic sensors act as input to the Arduino. The motors are connected to the output of the Arduino through the drivers. The ultrasonic sensors detect the obstacles and the motors are made to rotate based on the pre-programmed instructions in the Arduino.
2.2. Garbage Collection
The robot Garbage collection system consists of a set of rotating blades mounted on a shaft connected to the motors. The mechanism will not operate for entirety of the vehicle operation and will rotate only for predetermined set of conditions. The rotating blades may be made of galvanised iron or stainless steel to suit outdoor applications as well as durability. The main aim of the mechanism is to collect garbage which is of similar dimensions to that of juice cartons, plastic bottles, crushed papers, and all light items whose height is between 5 to 20cms. Mechanism is mounted on the front side of the base with an appropriate ground clearance. Two motors are mounted on the two sides of the shaft and is connected to Arduino to perform rotating mechanism. The collection mechanism is built is such a way as to suit public places like gardens, bus stands, footpaths. When the sensor detects static obstacle, the mechanism rotates and the garbage is pushed into a bin which is placed right behind the mechanism. The robot keeps collecting the garbage until it reaches certain height in the bin. Once the bin is filled the collected garbage is disposed to a selected place.
2.3. Disposal of Garbage
This action is done using tilting mechanism. The speed of the motor attached to shaft is kept at nominal value to get proper rotating action to move the garbage right into the bin. This is just a prototype and hence the mechanism used can pick only above-mentioned garbage. The mechanism can be changed according to the place where it is being used.
3. Block Diagram
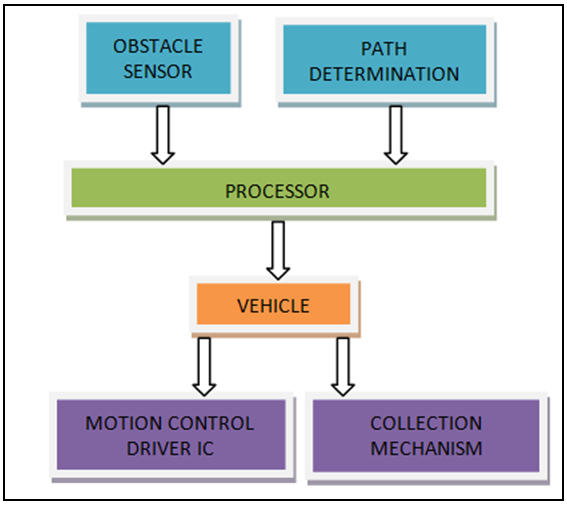 | Figure 3.1. Block diagram of a proposed project |
The above block diagram shows the various blocks involved in the proposed project.
4. Circuitry
Some of the system requirements of the project are listed below:× Motor driver circuit is used for the motion of the robot.× Power supply as to get sufficient power for the motor.× The robot requires a motion controlling unit i.e. Arduino Uno kit with adapter. × Automatic motion of robot is obtained by using sensors in the navigation system.× Metallic structure of the robot.Other auxiliary circuits are added as per the requirements.Arduino Uno is the controller that coordinates the functionalities of the three stages to meet the real-time requirements. Arduino Uno is a microcontroller board based on the ATmega328. It has 14 digital input/output pins (of which 6 can be used as PWM outputs), 6 analog inputs, a 16 MHz ceramic resonator, a USB connection, a power jack, an ICSP header, and a reset button. It contains everything needed to support the microcontroller; simply connect it to a computer with a USB cable or power it with an AC-to-DC adapter or battery to get started.
5. Design of the Robot
A rectangle metal sheet of size 50 X 40 cm is taken as base of the robot. Four wheels are attached with geared motors to the base. The motors are of 30rpm each to move the bot to accurately detect the garbage. The mechanism of the bot has four which of are placed at an angle of 90 degrees from each other. The blades are fixed to a shaft. The blades rotate along with the shaft to collect the garbage. A curved metal sheet is placed below the blades so that the garbage is properly directed to the collecting box placed on the base. The collecting box has a tilting mechanism so that the garbage collected can be disposed to a specified place. There is another level on the base.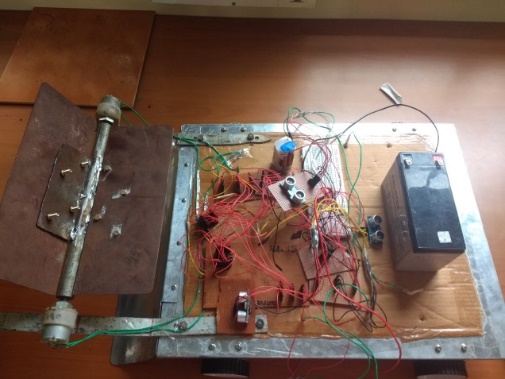 | Figure 5.1. Skeleton of the bot from top view |
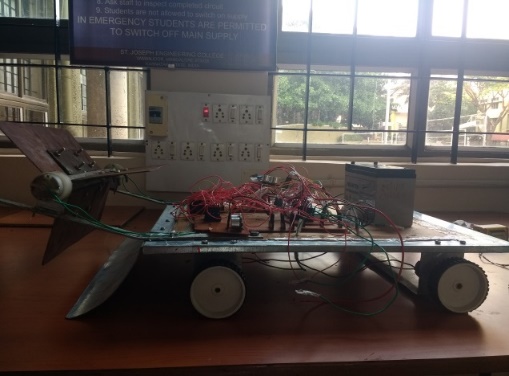 | Figure 5.2. Skeleton of the bot from side view |
6. Flow Chart
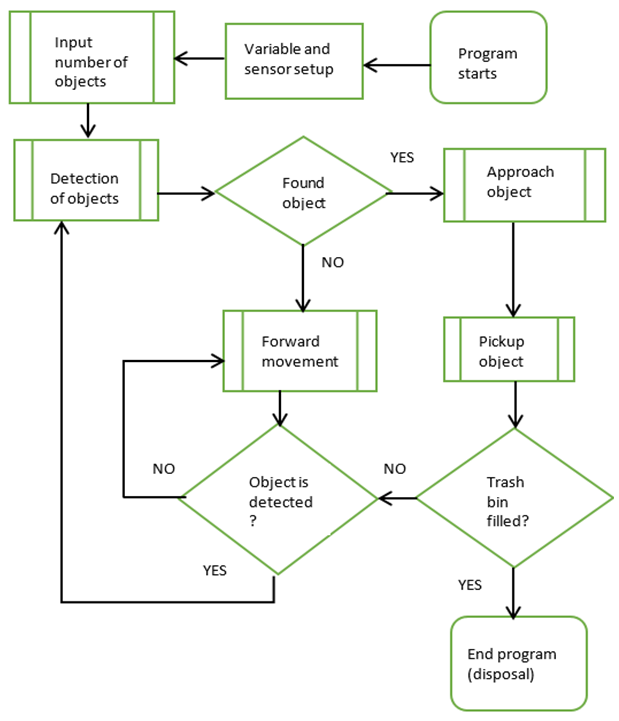 | Figure 6.1. Flow chart of a proposed project |
The working of the proposed project is explained above in form of flow chart.
7. Results
The objective of the project was achieved to some extent. The garbage collected efficiently and effectively. The robot moves in a constant speed. The garbage gets detected when it is at 20cm from the trash. The project is still in progress to achieve the optimised results with few more modifications.
8. Conclusions
The Garbage and recycling pickup work is physically demanding and it exposes workers to many occupational hazards. This project is designed to fulfil the task of collecting garbage from certain places and then dispose it at a single place from where the garbage will then be taken for disposal or process of recycling. To build an automatic trash robot using Arduino microcontroller which detects and collects the paper and plastic items automatically and process it. So, this reduces the requirement of manual clearance of plastic waste.
References
[1] | Saravana Kannan G, Sasi Kumar S, Ragavan R, Balakrishnan M, “Automatic Garbage Separation Robot Using Image Processing Technique”, International Journal of Scientific and Research Publications, Volume 6, Issue 4, April 2016. |
[2] | Hesham Alsahafi, Majed Almaleky, “Design and Implementation of Metallic Waste Collection Robot”, SEE2014 Zone I Conference, April 3-5, 2014, University of Bridgeport, Bridgpeort, CT, USA. |
[3] | Osiany Nurlansa, Dewi Anisa Istiqomah, Mahendra Astu Sanggha Pawitra, Member, IACSIT “AGATOR (Automatic Garbage Collector) as Automatic Garbage Collector Robot Model” International Journal of Future Computer and Communication, Vol. 3, No. 5, October 2014. |