Juneseok Lee
Department of Civil and Environmental Engineering, San José State University, San Jose, California, USA
Correspondence to: Juneseok Lee , Department of Civil and Environmental Engineering, San José State University, San Jose, California, USA.
Email: |  |
Copyright © 2015 Scientific & Academic Publishing. All Rights Reserved.
Abstract
The major objectives of this research were to: (i) observe pressure variations at the T-junctions in service lines, (ii) compare the hydraulic transients’ characteristics with and without a leak. To accomplish objectives (i) and (ii), an instrumented PVC piping network was built to represent real service lines and used to demonstrate that leaks attenuate the transient pressure peak values compared to no leak situations. At the T-junction there was no marked difference in steady state pressure values for different locations, but for unsteady states some differences were observed that appeared to depend on the geometry. In addition, numerical methods were applied and compared with experimental outcomes. The results of this study shed new light on the precise relationships between hydraulic transients and water leaks.
Keywords:
Service lines, WAter hammer and water leaks
Cite this paper: Juneseok Lee , Hydraulic Transients in Service Lines, International Journal of Hydraulic Engineering, Vol. 4 No. 2, 2015, pp. 31-36. doi: 10.5923/j.ijhe.20150402.02.
1. Introduction
Executive Order 13010, signed by President Bill Clinton on 15 July 1996, designated water distribution systems as one of 8 critical national infrastructures, signifying that their incapacity or destruction would have a major adverse impact on the security of the nation and its citizens. This highlights the importance of our drinking water distribution systems, which bear serious operational and managerial responsibilities for public health [1]. Recently, however, American Society of Civil Engineers (ASCE) assigned a grade of D to the United States’ water infrastructure [2] and the American Water Works Association (AWWA) has estimated that approximately $325 billion needs to be spent on upgrading water systems in the United States over the next 20 years [3]. Leakage rates, where water is lost while being transported from treatment plants to premise plumbing, in drinking water systems can be as high as 32% in some utilities [4]. AWWA estimated that 6 billion gallons of treated water are disappearing while being transported [3]. Pumping stations devote up to 90% of the total energy expended in water supply and treatment systems to providing appropriate pressure for delivering treated drinking water through pipelines. Consequently, water leakages also waste significant amounts of energy and associated carbon footprints. Service lines connect municipal water pipes to the plumbing systems within residential units. Generally, the water service line, which is the property owner’s responsibility, begins at the curb stop and only the systems running from the main to the curb stop are maintained by the utility company. Lee [1] compiled detailed information on the characteristics of these service lines. Research into major leak sources has revealed that large water losses can occur on the customer service lines branching from the water main, and these can originate in the service lines, fittings, and connections to households [3, 5]. Leaky service lines are expensive in terms of both lost water and the associated energy consumption. Colombo and Karney [6] presented an analysis of leakage vs. energy consumption and concluded that the energy consumption increases the further downstream the leak is located, which emphasizes the importance of service line managements. A water system with its myriad of appurtenances (including pumps, valves, and tanks) is known to be susceptible to hydraulic transients, resulting in a succession of high and low pressure waves passing through the network [7]. The most common causes of this phenomenon are i) rapid closing of valves and ii) pump on/off events. Lee et al. [7] concluded that poor physical condition of the service lines and lowered hydraulic integrity at the water mains can both result in serious public health risks due to possible contamination intrusion through leaking sections. More importantly, homeowners are seldom aware of issues such as health effects and the taste and odor of water that are related to defects in the piping systems within their property lines [8]. It is clear that developing a better understanding of the need for good management of service lines will improve the quality of operational and managerial processes and thus, ultimately, benefit public welfare. The major questions that drove this research are: Why are service lines showing an increase in the number of leaks reported? Can hydraulic transients be responsible for the frequent failures in service lines? To help answer these questions, an experimental piping system was designed, built and tested in the lab to simulate real-world systems. The specific objectives of this paper are to: (i) observe pressure variations at T-junctions in the service line (in particular where the water main and service line meet) for both steady and transient flow as a function of valve positions and sudden valve closing/ opening; and (ii) compare the hydraulic transient characteristics with and without a leak in the service lines. In addition, the experimental hydraulic transients results reported by Lee et al. [7] were compared using various numerical schemes. The results of this study will help to identify the physical parameters that may be responsible for service line failures and characterize the relationship between transients and water leaks. The information gained regarding the impact of transients on water line integrity will provide major support for those seeking to develop best practice and maintenance strategies for the future.
2. Methods
2.1. Experiments
To accomplish objectives (i) and (ii), an instrumented PVC piping network was built to represent real service lines. The layout is shown in Figure 1. The equipment was selected based on its similarity to actual drinking water systems in terms of layout, generated pressures, and velocities. Highly sensitive sensors were installed to observe the spatial and temporal variation of the flow patterns. The basic design of the system reproduces the 7.62 cm (3”) water main, service lines, and plumbing systems typically found in a house in the U.S. (Figure 1). To accomplish this, a 3.81 cm (1½”) line is tied into the water main, which then branches off into 1.91 cm (¾”) and finally 1.27 cm (½”) pipes for distribution to various fixtures within the house. The water in the system is then re-circulated through a storage tank in the basement. 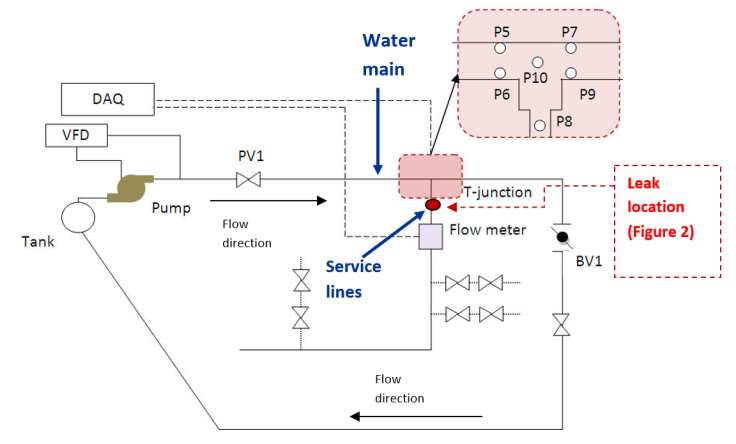 | Figure 1. Layout of the experimental test system |
Hydraulic transients occur if a valve is suddenly closed (PV1 or BV1; Figure 1) in a pipe system, causing an abrupt change in the velocity and pressure. As the pressure wave passes along the pipe, pressure measurements of the order of a hundred readings per second were needed to adequately capture the maximum and minimum and thus visualize the flow patterns in the service lines [7]. The pressure continues to fluctuate until the transient energies are fully dissipated, so the measurements continued for some time after the event. Flow rates in the system were measured simultaneously using a flow meter. A data acquisition system (DAQ, Data Acquisition Systems, National Instruments), a bi-directional flowmeter, pressure transducers, a centrifugal pump, and various pipe fittings were adopted for the experiment. The pipe and pipe fittings were obtained from a local hardware store. Below is a summary of the rationale behind the choice of the various components. ● Pipe: The pipe diameter and material choice were based on the working pressure of the system and the pipe’s pressure rating. 40-clear-PVC was chosen for all of the sections of pipe that required visual inspection (T-junction). For the ancillary sections of pipe from the pump to the test section, the return from the test section to the storage tank, and the pipe from the tank to the pump, regular schedule 40-PVC was chosen to reduce costs.● Pump: The relevant specifications here were the rated head, rated discharge, rated pump speed, rated torque, and rotational inertia; the rated characteristics are the characteristics at the point of maximum efficiency. The pump was selected based on the requirements of the system, namely 303 LPM at 414-552 kPa. ● Pressure Transducer: The OMEGA pressure transducer was chosen based on its ability to measure pressures ranging from -96 kPa to 1700 kPa and its output range of 4-20mA, which is compatible with the DAQ system. The data was acquired at a rate of 100 Hz. As it is possible for the large pressure fluctuations caused by the hydraulic transients to damage the sensors, snubbers (OMEGA) were used to protect the pressure transducers. A hole was drilled in the pipe close to the point at which the change in direction occurred and leads threaded through for a pressure transducer. This allowed some flexibility as to the precise mounting location of the pressure transducer to enable points of interest such as the pressure variations at the T-junction sections between the water mains and the service lines to be examined in more detail. For example, a total of six pressure transducers were attached at the T-junction (Figures 1 and 2).● Flowmeter Selection: The flowmeter needed to be 3.81 cm in diameter at the service lines, and able to measure directional flows ranging between 19 and 4,088 LPM with at least an accuracy of 0.5%. Its output of 4-20 mA was again compatible with the DAQ system. In this experiment, the characteristics of the hydraulic transients at the T-junctions focused on a comparison of the leak vs. no leak scenarios in the service lines. Simulated leaks are shown in Figure 2. The size and location of the leaks will dictate the water loss and associated energy burden on the utility systems. Here, the leak consisted of a circular hole with a diameter of 0.476 cm; the corresponding leakage rate was about 20.8 LPM. Hydraulically, the magnitudes of the transients’ highest and lowest peaks (at the T-junction) are expected to be attenuated when service lines have a leak. This experiment will verify the effect of leaks on the hydraulic transients. A clear understanding of these variables will help utilities prioritize leak repairs, leak detection, and related services.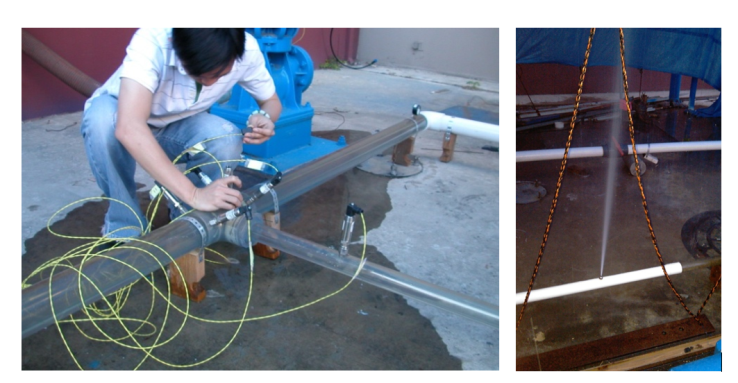 | Figure 2. Pressure Transducers at the T-junction and the Experimental Water Leak |
2.2. Numerical Models
The gas in a liquid can take two forms: dissolved and free. The dissolved gas is effectively invisible in the liquid and does not noticeably increase either its volume or its compressibility, but free gas (or entrained gas) is dispersed throughout the liquid as bubbles, which can make the liquid appear turbid. Liquid that has not been completely degassed will usually contain some entrained air in the form of microscopic or sub-microscopic bubbles, either in the bulk of the liquid, around a solid contaminant (or nucleation site), or close to the container wall. According to Wallis [9], free gas in liquids is most commonly modelled using homogeneous, separated, or drift flux models. For a two phase or two component mixture/one dimensional flow model, six equations are required to represent the conservation of mass, momentum, and energy of each phase. To describe the interactions between each phase, additional formulations are required. One or more conservation equations must also be formulated for the mixture as a whole in addition to those for the individual phases, so simplified governing equations must be established. Drift flux considers only the velocity difference between the two phases, while separated models include all of the equations mentioned above. If there is no significant difference in the velocities of the two phases, homogeneous models can safely be applied to bubbly mixture models; in homogeneous models, the two components are treated as a single pseudo-fluid with averaged fluid properties. In the preliminary phase of this study, continuity and momentum equations were proposed for a two phase mixture having a low void fraction and insignificant slip. Several assumptions were made when using Equations (1) and (2) below: 1) the fluid mixture is homogenous, bubbly, and two-component in nature; 2) the difference in pressure across a bubble surface can be neglected; and 3) there is no momentum exchange between each phase and hence no slip between phases.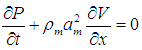 | (1) |
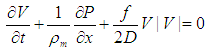 | (2) |
Here, P is the pressure, V the velocity, x the spatial dimension, t the time, f the friction factor, ρm the mixture density and ɑm the wave speed of the mixture. The additional gas release volume when the pressure drops below saturation pressure was also considered, requiring the fractional volume of the free bubbles to be adjusted. As the gas release rate is proportional to the degree of under-pressurization: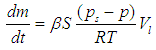 | (3) |
where, β is the gas transfer coefficient, which includes the diffusion coefficient and the interfacial area for gas transfer per unit volume of liquid; S is Henry’s constant; R is the gas constant; T is the absolute temperature; and Vl is the unit volume of liquid.Observations of the real phenomenon through clear plastic pipes [7] revealed that the liquid was present as a single phase rather than a homogeneous mixture, thus allowing classical water hammer equations to be employed. For completeness, the water hammer equations are included here: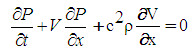 | (4) |
 | (5) |
where P is the pressure, V the velocity, c the wave speed, ρ the density, g the acceleration due to gravity, α the angle of inclination of the pipe, f the friction factor, D the diameter, x the spatial dimension, and t the time. These equations can be solved for a pipe network that incorporates suitable interior boundary conditions for appurtenances such as valves and junctions of several pipes, as well as external boundary conditions such as service lines, tanks, and faucets. The solution of these equations yields the pressure, P(x, t) and velocity, V(x, t) as functions of x and t with x being the dimension along the length of the pipe. The pressure can be highly positive or negative and the velocity can also be negative, indicating flow reversal. In this study WHAMO [10] and Hammer [11] are utilized to solve pressure and flow patterns in small diameter pipe networks involving valves, faucets, and T-junctions. It is noted that WHAMO uses the implicit finite difference method, where the unknown dependent variables in a section at the end of each time step are expressed in terms of the unknown values of the dependent variables at the near nodes. The implicit method replaces the partial derivatives with finite differences and provides a set of equations that can then be solved simultaneously. Hammer takes a different approach, applying Method of Characteristics (MOC) to solve the governing equations. MOC is known to be an accurate and informative way to solve water hammer problems that takes into account both the friction and gravity within the pipe as well as the minor losses. In order to conduct a comprehensive comparison, the explicit scheme was selected for this study and the second-order explicit model utilized for the analysis of single liquid transient flows, as higher order schemes are known to reproduce sharper shocks compared to the relatively simple first order methods [12]. Three numerical schemes are adopted and solved for a selected case (Figure 5 in [7]).
3. Results and Discussion
3.1. Experimental Results
As mentioned in the Methods, 6 pressure transducers were installed at the T-junction to study the pressure variations across different locations in and around the junction (Figures 3 (a)). Under steady state conditions, minimal differences in the pressures measured by the transducers were observed (Figures 3(b)-3(e)). However, during a transient event there was some variation depending on the location of the pressure transducers (Figures 3(b)-3(e)). When there was no leak present (corresponding to a flow of 303 LPM and 414 kPa in the main), a sudden valve closure of PV1 (Figure 3: upstream of the T-junction; time of closure tc = near to zero) caused the pressure to drop below 0 kPa (Figure 3(b)). Note that the effect of the hydraulic transients tends to diminish with lengthening valve closure time (tc) and subsequent cycles will have steadily smaller amplitudes. When there is a leak (a 20.6 LPM discharge through the leak), the sudden closure of valve PV1 and the corresponding pressure variations at the T-junction are shown in Figure 3(c). It is noticeable that there is no negative pressure experienced here and the pressure variations are relatively smoother. A sudden valve closure downstream of the T-junction (BV1 in Figure 1) caused a pressure increase followed by lower pressure right across the T-junction until all the energy had been dissipated (Figure 3(d)). The amplitudes of the peak pressures decreased with increasing closing time (tc). The corresponding pressure variations at the T-junction for a leak of 20.6 LPM are shown in Figure 3(e). Here, there is around a 138 kPa pressure difference due to the leak and once again, the pressure at the T-junction peaked at a lower level.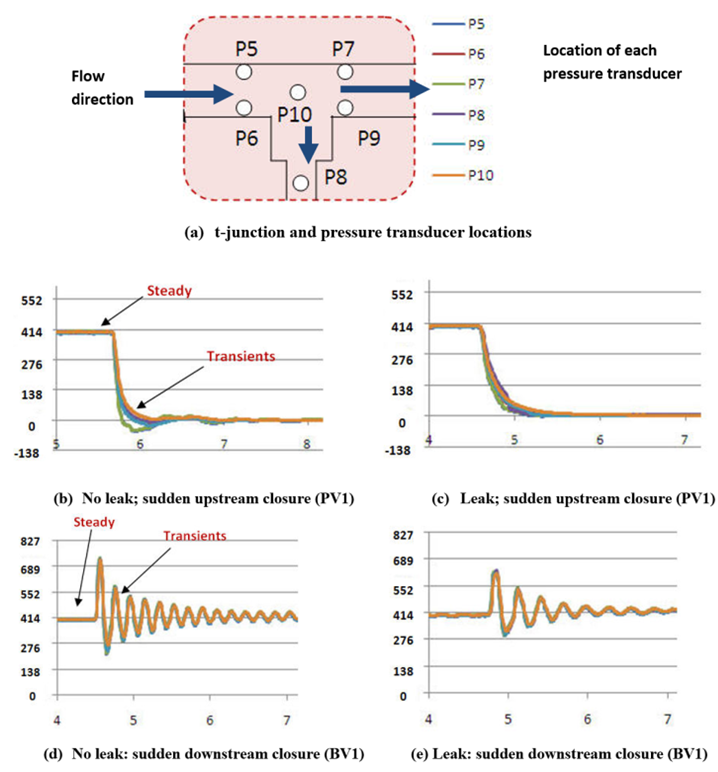 | Figure 3. Results (leak vs. no leak) - (y-axis: pressure in kPa; x-axis: time in seconds) |
3.2. Numerical Results
When the valve was suddenly closed to simulate closing an upstream water mains valve, the lowest observed pressure in the service line is -69 kPa [7]. Only the first peak is guaranteed to be truly dynamic in nature; the second and all subsequent peaks are residual wave actions that the sensor tracks as the system settles back into a steady state [13]. Time step is 0.001 sec and wave speed is measured to be 61 m/sec. Major section of the pipes are made of clear plastic pipe (for visualization purposes) [7], which has significant impacts on the wave speed values. Darcy-Weisbach friction factor is calibrated to be 0.1. The numerical results of the simulation are presented in Figure 4. All three methods predicted similar behaviour, including the lowest pressure values, and were in good agreement with the observed values reported by Lee et al. [7].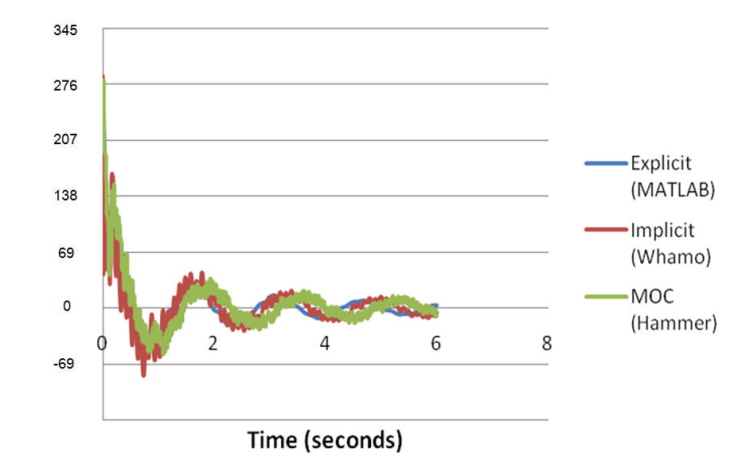 | Figure 4. Numerical Results (y-axis: Pressure in kPa) |
4. Conclusions
The pressure variations experienced in service lines corresponding to typical street level pressures encountered in a real-world water supply system are addressed in this paper. Major findings of this research are as follows: 1. Steady and unsteady conditions in service lines were investigated with and without a leak. Water leaks demonstrably attenuated peak transient pressure values compared to those measured with no leak present. 2. Across the T-junction, there was no marked difference in steady state pressure values for different locations, but in the unsteady state there was some degree of variation observed due to geometries, which will bear further in-depth examination. In addition, single liquid water hammer equations were solved using MOC, implicit and explicit finite difference approaches. The results obtained showed a reasonably good agreement with previous experimental measurements [7]. This study provides a foundation for future work to derive the specific relationships between water leaks and transient peaks, precisely how energy losses depend on the leak shape and location, and the effect of different pipe materials. A better fundamental knowledge of the various physical parameters (including the pressures, velocities, and hydraulic transients associated with leaks) will improve the efficiency and best practice management of drinking water distribution applications.
ACKNOWLEDGEMENTS
This study was conducted with the help of generous funding from the Charles Davidson College of Engineering within San José State University. The author also appreciates the assistance rendered by Mr. Phong Doan, Mr. Abdullah Fayyaz and Mr. Carl Crizer in setting up and running the hydraulic transients experiment.
References
[1] | Lee, J. 2008 Two Issues in Premise Plumbing; Contamination Intrusion at Service Lines and Choosing Alternative Plumbing Material, Ph.D. Dissertation, Virginia Polytechnic Institute & State University. |
[2] | ASCE 2013 Report Cardhttp://www.infrastructurereportcard.org/ (accessed on November 1, 2014). |
[3] | AWWA 2007 Installation, Condition Assessment, and Reliability of Service Lines. AWWA Research Foundation, Denver, CO. |
[4] | Kirmeyer G., Friedman M., Martel, K. Howie D., LeChevallier M., Abbaszadegan M., Karim, M. Funk, J. & Harbour, J. 2001 Pathogen Intrusion into the Distribution System. American Water Works Association Research Foundation: Denver, CO. |
[5] | Thorton J., Sturm R. & Kunkel G. 2008 Water Loss Control. McGraw-Hill, New York. |
[6] | Colombo A.F. & Karney B.W. 2002 Energy and costs of leaky pipes: toward comprehensive picture. J Water Res Pl-ASCE, 128(6), 441-450. |
[7] | Lee J., Lohani V., Dietrich A. & Loganathan G. V. 2012. Hydraulic transients in plumbing systems. Wa. Sci. Technol. 12(5), 619–629. |
[8] | Lee J., Kleczyk E., Bosch D., Dietrich A., Lohani V. & Loganathan G. V. 2013 Homeowners' decision-making in a premise plumbing failure-prone area. J. Am. Water Works Assoc. 105(5), E236-E241. |
[9] | Wallis G. 1969 One dimensional two phase flow. McGraw Hill, New York. |
[10] | Fitzgerald R. & Van Blaricum V. L. 1998 Water Hammer and Mass Oscillation (WHAMO) 3.0 User’s Manual. U.S. Army Corp of Engineers Construction Engineering Research Laboratories ADP Report 98/129, September 1998. |
[11] | Bentley, Hammer Software,http://www.bentley.com/en-US/Products/HAMMER/ accessed on July 28, 2015. |
[12] | Anderson J. D. 1995 Computational Fluid Dynamics. Mechanical Engineering Series. McGraw-Hill, New York. |
[13] | Glynn, T. 2007 PCB, Personal Communication. |