Jones Orumwense
Professor of Management College of Applied of Higher Degrees and Research, Kampala International University Kampala, Uganda
Correspondence to: Jones Orumwense, Professor of Management College of Applied of Higher Degrees and Research, Kampala International University Kampala, Uganda.
Email: |  |
Copyright © 2012 Scientific & Academic Publishing. All Rights Reserved.
Abstract
initiating a total quality management program in organizations involves everyone in the origination gaining a basic understanding of Total Quality Management principles and then indentifying the key issue from top level, strategic interests to everyday operational concerns. The study shows that the current position of Total Quality Management implementation in Nigerians companies is encouraging considering the fact that management philosophy is relating new in the country.
Keywords:
Total Quality Management and Implementation in Organizations
Cite this paper: Jones Orumwense, Total Quality Management Implementation in Nigerian Organizations, International Journal of Finance and Accounting , Vol. 3 No. 1, 2014, pp. 1-5. doi: 10.5923/j.ijfa.20140301.01.
1. Introduction
The need to develop effective business performance improvement strategies has never been greater than it is in Nigeria today. The economy is growing slowly, and is characterized by high cost of funds, materials and services, overcapacity and market stagnation. Organizations in all sectors of the economy are therefore seeking ways to improve their financial performance, market share, customer loyalty and the contribution of employees to the business. Total Quality Management (TQM) is a management philosophy which provides the framework for tying together in a comprehensive way these important business goals. It seeks continuous improvement in the quality of performance of all processes, products and services of a company, with the primary objective of achieving customer satisfaction and loyalty. Ever since the Japanese industries used the TQM principles to achieve competitive advantage in the global market, many companies in Europe and America have also adopted the new management philosophy with resounding successes. However, reports of studies carried out in the United States and Britain indicate that some organizations experience difficulties with their TQM implementation programmes[1,2]. These organizations usually start well and after one to three years of implementation, they run out of steam. Reasons found for this failure include: lack of top management commitment and leadership, lack of strategic focus and goals, lack of supporting infrastructure/culture change and employee involvement programmes, over-emphasis on internal matters and lack of measurement of the performance of the programme. The results of the studies have enabled some of these companies to change their implementation strategies in order to overcome the barriers identified. The implementation of TQM is relatively recent in Nigeria. For example, the first open seminar on TQM was organized by the Lagos Business School in April 1992. Before this time, only local subsidiaries of multinational organizations had begun to implement TQM following directives from their head offices. However, since 1992 more than thirty companies from both the manufacturing and service industries have attended in-house TQM awareness seminars organized by the School as a preparation for implementing the programme. This paper describes the findings of a survey carried out in 1995 to find out the current status of TQM implementation in Nigerian companies. The study also aims at examining the factors contributing to success or failure of TQM programmes in Nigerian companies and to determine those peculiar to the local business environment. Based on the results of the survey and experiences gained while assisting some companies with their TQM implementation, an action plan that will enable organizations to achieve success with their programmes will be proposed.
2. Method of Investigation
The study was carried out by use of questionnaires and, where necessary, through interviews to clarify some key issues. Thirty companies drawn from both manufacturing and service sectors were approached. The questionnaires were structured to obtain in-depth information about five factors which are considered critical to the successful implementation of quality management initiatives[8,3]:• Top management commitment and leadership, • Strategic orientation, • People management, • Continuous improvement orientation, • Organization for TQM. Among the thirty companies surveyed, twenty-two of them returned the questionnaires, thus providing an effective return rate of 73.3%. These included thirteen multinationals and nine indigenous organizations from manufacturing, oil, financial services and commodity trading.
3. Summary of Findings
1. Table 1 shows the stages of TQM implementation reached by each company (see section 4 for explanation of the stages). Two companies were at the planning stages while nine had progressed to the second stage. The remaining ten companies have reached the third stage of implementation. One of the companies, ICL Nigeria Limited was following a different implementation approach. It embarked first on the upgrading of its quality management system with the implementation of the ISO 9001 Certification, and decided to use this as the path to TQM. It has already adopted the European Foundation For Quality Management (EFQM) model and claimed to have obtained an EFQM score of 450 with plans to improve the rating to 750 by the end of 1996. 2. Of the twenty-two respondents, ten companies have each had up to three years’ experience of TQM implementation. One of these companies reported having started the programme in 1985. 3. Eleven of the companies surveyed made use of consultants during their TQM implementation.
4. Results and Discussion
COMPANIES WITH MORE THAN THREE YEARS IMPLEMEfA11ON EXPERIENCE The ten companies that have had TQM implementation experience of three yearn above were assessed against the five c factors for successful TQM implementation The aim was not to assess the companies terms of success or failure because according Oakland et al.[4], the time to expect TQM to deliver benefits is over a of five years. However, these companies considered to have had sufficient experience assess the impact of these factors on programmes, and to show whether they have the essential ingredients for success: The commitment of top management is an essential requirement with which TQM implementation can succeed.
4.1. Top Management Commitment and Leadership
Although all the companies recognized the for top management commitment leadership as a critical factor for successful TQM implementation, three of them re lack of commitment and resistance by senior managers. To worsen their situation these companies lost the chief executive officers who initiated the programmes full integration in the organizations. These I companies reported having difficulties their implementation and that the had stalled. One of these companies re that the quality improvement teams responsible for managing the programme instead of the Quality Council or St Committee, confirming lack of top management participation. The remaining seven rated their senior managers as very corn and reported measurable achievements iii’ programmes. The commitment of top management essential requirement without which I implementation cannot succeed. This has demonstrated through actively support programme: by acting as “role models” I change process, encouraging subordinates participate in quality improvement activities and constantly monitoring the progress of the implementation. Perhaps, the experience of the ISO 9000 can be used for the assessment and upgrading of the quality system of any organization before starting TQM three companies that lost their chief executives during the course of implementation brings to the fore the importance of stability at the top management and the need for general ownership of the programme in the implementation process. In fact, two of these companies embarked upon downsizing exercises which led to uncertainties and lack of support for the programme. This factor is worth noting because it has been a common feature in Nigerian industries over the last few years. The instability observed in the various industrial sectors since the Structural Adjustment programme of 1986 would certainly create barriers for successful TQM implementation.
4.2. Strategic Orientation of the Programme
The strategic focus of the programmes varied from company to company and all the ten companies agreed that the goals of their TQM were in line with their companies current business strategies. The goals included the use of TQM as a competitive strategy, to achieve cost advantages and profitability, to improve quality, to improve operational efficiency, to change corporate culture, to improve customer satisfaction and to build team-work. All the companies, except the three that reported having problems with their implementation, made above average achievement on their selected goals. However, one of the three companies reported that the goals were set without a clearly defined time-frame, while another set short-term goals. All the remaining companies reported following medium to long-term goals. There is always the need to define clearly the goals the TQM programme is intended to achieve for the organization and to use them to support the business strategies. Performance measurement mechanisms are then established to monitor progress. The goals should ideally be medium to long-term, and must have realistic time-frames for achieving them. However, the turbulent Nigerian economic environment with frequent policy changes may force companies to abandon long-term TQM goals for day today operational issues, which should be avoided.
4.3. People Management
To questions about how their companies ensured full participation of their employees, the responses were varied and there were no clear distinction between companies. Training, employee buy-in, empowerment and rewarding participation in quality improvement teams were some of the measures used. Only four companies offered monetary rewards for suggestions leading to quality improvement. One company reported, however, that it discovered as the programme progressed that buy-in success appeared to be superficial and that there was a general feeling that quality was the responsibility of the TQM Coordinator. TQM is about changing the mind-set in an organization and it is the responsibility of the top management to ensure that everyone is committed to the programme. To achieve this requires a deliberate and time-consuming effort to woo the employees. How well a company achieves this will be dependent on a number of factors such as the existing culture, the type of leadership it has, the level of employee satisfaction and how the programme is communicated to organization. Each organization is different and the responsibility of the top management is to find through employee surveys how they feel about the organization and how organization would react to change.
4.4. Organization for TQM
The survey showed that most of the companies followed a similar approach in organizing their implementation. They had a management structure for the programme, at the head of which was a Quality Council or a Steering Committee, they appointed Coordinators or Facilitators and set up Quality improvement Teams. They had clearly defined participatory roles for everyone in the programme. All the companies gave quality training to all employees and introduced the programme company-wide. However, there were differences on how they identified improvement opportunities from the employees, ranging from formal and informal meetings, written reports and suggestion systems. Other preparations carried out by some companies before the commencerment of implementation were customer and employee surveys.
4.5. Continuous Improvement Orientation
There was a marked difference between the companies in their orientation to continuous improvement. Seven companies carried out regular measurements of the quality improvements to show evidence of change, and adopted a preventive approach to managing errors. One of these companies from the service sector, however) reported having difficulty in keeping up with the measurements. The three companies that reported having problems with their implementation (see subsection 3.1.) reported that they were not measuring the performance of the quality improvement programme. To the question about the impact p1 TQM on bottom- line results, only four companies were certain that the programme resulted in considerable change in their performances. This is an area of interest on which further study is planned using the appropriate performance indicators.TQM is about changing the mind-set an organization. To achieve this requires a deliberate and time-consuming effort to woo the employees.It is pertinent here to stress that one of the fundamental principles on which TQM is based is continuous improvement, which itself depends on constant measurement of performance. One cannot improve what has not been measured. It is through regular measurements that one can ensure that the programme goals are being achieved.COMPANIES WITH LESS THAN THREE YEARS OF IMPLEMENTATION EXPERIENCEThere were eleven companies whose experience of TQM implementation was less before than three years at the time of the survey. Three of these were already at the third stage of the quality improvement process with teams working on identified projects and measuring performance.The case of seven of the companies is particularly interesting. These companies had in-house R2M awareness training one year before the survey was carried out but have not managed to get off the ground. None engaged the services of consultants. These companies reflect the confused situation some organizations find themselves in with respect to TQM implementation. The confusion is inherent in the way TQM is implemented. To start with, people jump on the TQM bandwagon, inspired primarily by the “success stories”. Most of them are not clear where to start, what to focus on, what to expect, what to evaluate and how to organize the programme. With the delay in starting the implementation, enthusiasm wanes, everybody gets bugged down by operational issues, people get back to old habits and the company finds it more difficult to start all over again. TQM implementation requires thorough planning before starting, and once you start you cannot stop.MOVING FROM ISO 9000 TOWARDS TQMThe survey found that one company, ICL Nigeria Limited, was following the ISO 9000 path towards total quality. This is a new approach to TQM implementation that some companies in Europe and America have recently been adopting and it is worth commenting on. Although ISO 9000 and TQM supplement and support each other, they do have different objectives, evaluation and improvement processes, and management and success goals. For instance, 150 9000 is. designed to ensure the adequacy of a given quality management system and to use regular internal and external audits to ensure i1 adherence to it. TQM, on the other hand requires and assumes that an effective quality assurance system similar to ISO 9000 exists and is followed. Therefore, an organization that ha successfully put TQM into the fabrics of the business should need only minor changes - meet ISO 9000 registration requirements.Total quality implementation in Nigerian CompaniesISO 9000 as the path to TQM is incomplete. ISO standards do not have sufficient customer focus, do not address how good a product or service is and do not focus on continuous improvement. However, ISO 9000 can be used for the assessment and upgrading of the quality system of any organization before starting TQM. An alternative approach is to integrate the ISO 9000 standard into TQM from the start instead of treating them as separate progrnmmes. The advantage of this integrated approach is that it accelerates the TQM process by giving the management steering committee immediate strategic plans.
5. Proposed Action Plan for Successful TQM Implementation
Initiating a Total Quality programme involves everyone in the organization gaining a basic understanding of the quality management principles, then identifying the key issues from top level strategic interests to everyday operational concerns. The key issues are then prioritized for improvement activities to be planned in accordance with the objectives of the organization and the resources available. The status of the key issues provides the base level against which to measure the success of improvement activities.Improvement Teams and Facilitators at the introduction and during the development stages of the implementation process, but this requirement will change as the quality improvement activities mature, lie structure becomes less important and can be revised when people in all functions take responsibility for their own personal improvement, but it may take some time for this to happen. However, care must be taken to review and re-assess the effectiveness of the revised structure to ensure that the momentum of the improvement process is being maintained.Table 1. TQM Implementation in Nigeria (Companies Surveyed) 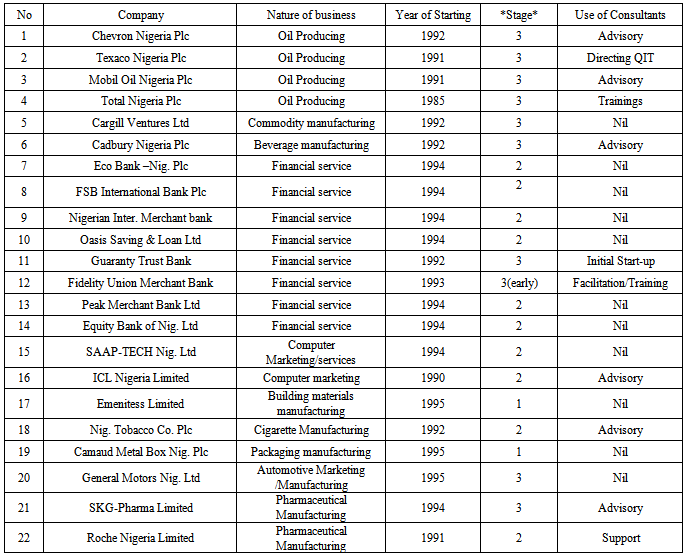 |
| |
|
6. Conclusions
The study has shown that the current position of TQM implementation in Nigeria is encouraging considering the fact that management philosophy is relatively new in the country. Japanese companies have had nearly thirty-five years’ experience with TQM and the Americans and Europeans about twenty years. What has been proved by the early practitioners is that TQM is an effective business tool which has been shown to impact on bottom-line results[4]. However, successful organizations using TQM have learned that it is hard work, takes a long time, needs to be driven by the strategy through the whole business, requires constant measurement of performance and relies a lot on top and middle management commitment and leadership. It will therefore take Nigerian companies some more years of practice in order to enjoy the benefits of TQM and this will be the appropriate time to assess how successful the programme has been.
References
[1] | Cottrell, J. “Favorable Recipe.” TQM Journal, February 17-20. (1992). |
[2] | Dyason, M. and M. Kaye. “Is there life after 1QM?” Quality World, August, 524-529. (1994). |
[3] | Kaye, M. and M. Dyason. “The Fifth Era.” The TQM Magazine, Vol.7 No.1,33-37. (1995). |
[4] | Oakland, 35., M. Zairi and S. Letza. (1994). |
[5] | ‘TQM and Bottom Line Results.” Quality World, September, 600-604. |
[6] | Okolie, E.E. “Implementing TQM.” LBS Technical Papers No. 15, June. (1993). |
[7] | Pike, J. and R. Barnes. “Approaches to the Implementation of TQM.” TQM In Action, 51-84. London: Chapman and Hall. (1994). |
[8] | Saraph, J.V., P.O. Benson and R.G. Schroeder “An Instrument forMeasuring the Critical Factors of Quality Management.”Decision Sciences, Vol.2 No.4, 8 10-829. (1989). |