K. G. A. Fernando, N. S. Senanayake, T. S. S. Jathunarachchi
Department of Mechanical Engineering, The Open University of Sri Lanka, Nawala, Nugegoda, Sri Lanka
Correspondence to: N. S. Senanayake, Department of Mechanical Engineering, The Open University of Sri Lanka, Nawala, Nugegoda, Sri Lanka.
Email: |  |
Copyright © 2024 The Author(s). Published by Scientific & Academic Publishing.
This work is licensed under the Creative Commons Attribution International License (CC BY).
http://creativecommons.org/licenses/by/4.0/

Abstract
This research evaluates the effectiveness of harnessing condenser heat from a household refrigerator for hot water needs. A modified refrigerator with a heat extraction system on the condenser's outer surface was utilized in the study. The prototype, featuring aluminium and composite EPE foam insulation, incorporated a temperature sensor, insulated storage tank, and an automatic mechanical water level controller for batch heating. Experimental trials achieved heating of 3 litres of water to a maximum of 44.5°C in an ambient environment of 31°C, with a minimum heating duration of 90 minutes to reach 40°C. Heat flux reached 252.5 W/m². Implementing the system resulted in no significant deviation in power consumption, with daily energy usage decreasing from 2.23 kWh to 2.13 kWh, indicating enhanced energy efficiency by 0.1 kWh per day. The cuboidal prototype effectively extracted condenser heat, heating water beyond 40°C, with the shortest heating time observed at 90 minutes during trials, while shorter durations of approximately 40 minutes were noted in personal domestic use, influenced by factors like refrigerator load and temporal availability.
Keywords:
Domestic refrigerator, Condenser heat, Energy saving
Cite this paper: K. G. A. Fernando, N. S. Senanayake, T. S. S. Jathunarachchi, Harnessing Refrigerator Condenser Waste Heat for Sustainable Heating Solutions, International Journal of Energy Engineering, Vol. 14 No. 1, 2024, pp. 1-6. doi: 10.5923/j.ijee.20241401.01.
1. Introduction
Cooling systems release a considerable amount of heat energy into the environment, which is not harnessed for productive uses. Existing approaches to recovering waste heat primarily target industrial applications, often overlooking opportunities for heat recovery at the household level.In residential buildings, household refrigerators play a role of base load for their continuous operation. They’re responsible for approximately 6% of the electrical energy produced worldwide [1]. Domestic refrigerators account for 14.2% of the household electricity use in Japan, 14% in USA and 21% in South Korea [2]. On a global scale, refrigeration, which includes air conditioning, accounts for approximately 17% of the total electricity consumed worldwide [3]. It is evident that the primary source of high energy consumption within households often involves some form of refrigeration. In the context of published research on domestic waste heat extraction, most studies focus on capturing heat that is rejected from condensers.For the household purpose of heating food, Thangavel et al. conducted a study in which they redirected the condenser coils of a refrigerator into an insulated container. In this setup, heat was exchanged between the coils and the food. The temperature inside the container reached 50 degrees Celsius, a sufficient level to maintain the warmth of the food. The maximum heat recovery achieved was 33.66 kJ/kg. However, this approach has notable drawbacks, primarily involving permanent modifications to the refrigerator's condenser coils to accommodate a secondary condenser. Additionally, within the confined space of the hot chamber, the heat from the secondary condenser must traverse through air before reaching the food placed in the hot chamber [4]. In research conducted by Mills and Perlman in 1986 (cited by Robert et al. in 1996), wastewater was utilized as a heat source to warm a storage tank containing fresh water. A closed-loop piping system connected the submerged evaporator in the wastewater tank to the submerged condenser in the freshwater tank. When the temperature within the wastewater tank exceeded a predefined threshold, a water-water heat pump facilitated the transfer of heat from the wastewater tank to the freshwater tank. This experiment demonstrated energy savings of up to 60% [5].In the study conducted by Robert et al. in 1996, an approach was employed where condenser tubes were routed through a water tank to heat fresh water. This setup successfully raised the water temperature to 45 degrees Celsius. However, this design had notable limitations. Firstly, the condenser tubing needed to be precisely tailored to match the system's requirements, and the modified tubing design turned out to be inadequate for the intended application. Consequently, this design would necessitate a customized system for different refrigerator types, lacking versatility [5]. A rececent study indicates that a hot box temperature of approximately 35°C-40°C can be generated by harnessing the recovered heat from a domestic refrigerator [6]. Ongoing research is focused on extracting waste heat from residential cooling systems for household applications, with various approaches and methods being developed. The primary aim of the current study was to introduce an innovative method for extracting waste heat at the domestic level. Key design principles of this study were to develop a low-cost domestic waste heat extractor without permanent modification of a machine while being safe and simple to implement for the domestic consumer.
2. Methodology
The method employed to recover waste heat from refrigerators involved experimental procedures. These procedures were conducted after performing essential computations concerning the thermodynamic characteristics of the condenser of the refrigerator. The calculations employed were dimensional analysis, Newton's law of cooling, Heat capacity equations, and Stefan Boltzmann's law.
2.1. Design Concept
The novel heat extraction system makes use of a thermally conductive aluminium vessel which is glued to the condenser of the domestic refrigerator by a layer of adhesive as shown in Figure 1. The vessel holds a volume of water which is to be heated by the heat dissipated by the condenser. Insulation was installed covering the vessel to minimize the heat loss.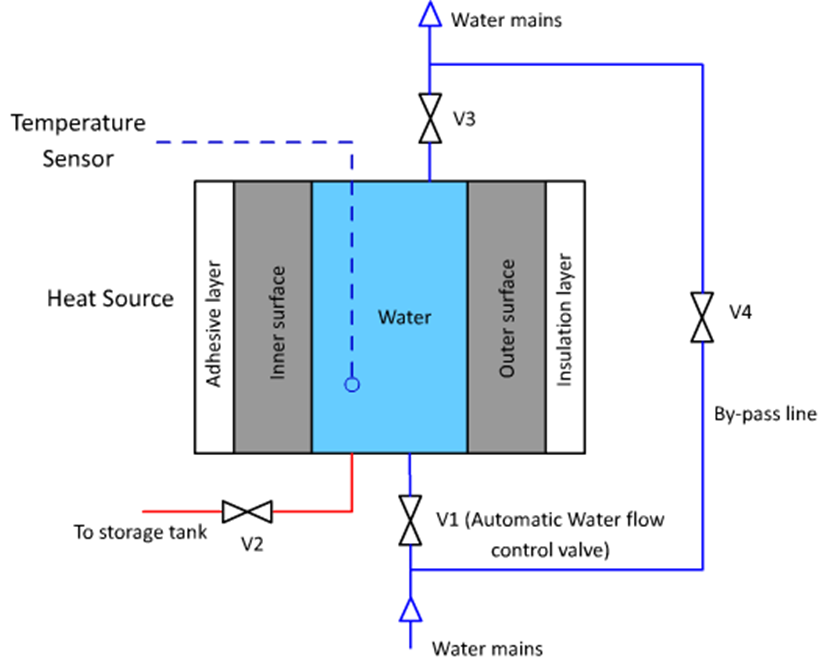 | Figure 1. Concept of Heat Extraction System |
The system was designed with two modes of operation, namely water heating mode and heat source cooling mode. Valves are to be used to direct the flow of mains water depending on the mode of operation. During the water heating mode, the vessel is filled with a volume of water to be heated. The heated water is then transferred to an insulated storage tank. During the heat source cooling mode, water flows through the vessel to provide the additional benefit of increased heat rejection through forced convection. The flow path of water in heating and cooling modes is indicated in red and blue respectively.
2.2. Experimental Setup
Figure 2 illustrates the rear section of the refrigerator, where a water vessel was integrated with the condenser alongside piping and temperature sensors. The vessel, crafted from 32-gauge aluminium sheet, assumed a cuboidal shape measuring 200x400x40 mm (length x height x depth), and was meticulously double-sealed with silicone caulk. Additionally, to shield the vessel's exposed areas from external conditions, aluminium foil-backed EPE foam with a thickness of 12mm was applied as insulation. The thickness of the insulation was determined after assessing the limited range of locally available thicknesses as well as the spatial limitations within the rear compartment of the refrigerator.The interface between the condenser surface and the vessel was secured using synthetic resin Multibond 373 contact adhesive. The principal role of the adhesive is to fully attach the heat extractor on to the surface of the condenser. The choice of synthetic resin adhesive Multibond 373 was based on various factors, including its removability, adhesion compatibility between the two metallic surfaces, ability to bear weight, ease of application, and cost.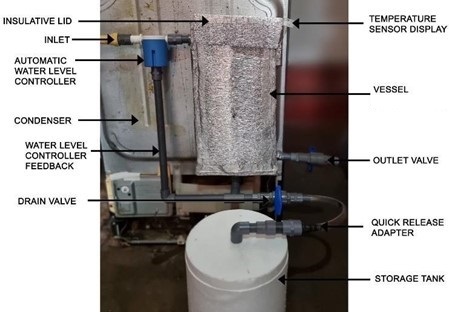 | Figure 2. Rear of the Refrigerator installed with Heat Extraction System |
Standard 20mm sockets were used for the hydraulic circuit. A mechanical automatic water controller prevents water overflow, a digital cylindrical probe temperature sensor with display indicated the temperature of water within the vessel. A 6-liter insulated storage tank accommodated water after heating.The thermal dissipation from the refrigerator condenser was characterized as one-dimensional uniform, steady-state heat transfer along a smooth vertical flat plate, with its magnitude determined employing dimensional analysis, Newton's law of cooling, and Stefan Boltzmann's law. Average temperatures across the surface of the condenser were acquired by utilizing three cylindrical probed thermocouples positioned relative to the compressor discharge as depicted by Figure 3.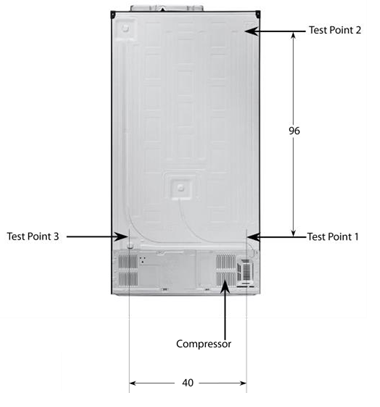 | Figure 3. Test Points on Condenser located vertically furthest from test point 1 and horizontally furthest from test point 1 |
Given that the instruments were generic temperature sensors with displays that lacked automatic data logging capabilities, a manual data capture process was employed at 5 minute intervals.This interval deemed sufficient to capture the thermal changes within the system with adequate resolution. Data collection was ceased at the 260 minute mark as condenser temperatures kept declining post-peak, after yielding insights into the unmodified condenser's thermal behaviour.The adhesive interface was attached to the condenser of the refrigerator LG GLM312RLMC. Data was collected using 3 cylindrical probe thermocouples, one placed on the condenser close to the compressor discharge (TP1), another submerged within the water inside the vessel, and the other placed on the outer surface of the insulation of the vessel. The heat extracted by 3 litres of water to be heated was calculated using the heat capacity equation. The first trial was conducted for a period of 350 minutes but affected by a power cut. The second trial was conducted for a period of 90 minutes.The power consumed by the refrigerator LG GLM312RLMC with and without the adhesive interface attached to the refrigerator was analysed using a 3680W generic digital power meter. With the adhesive interface attached, the vessel was filled and drained with water, whenever heated water was required under domestic working conditions. The experiment was subject to unavoidable daily power cuts at uniform intervals. However, data was gathered over a period of 18 days and averaged to statistically investigate fluctuations in power consumption.
3. Results
Figure 4 depicts the thermal data acquired from the unaltered condenser throughout a duration of 260 minutes. The total heat dissipated from the condenser was computed to be 128.53 watts. Notably, the rate of radiative heat transfer in the condenser substantially exceeds that of convection. Specifically, convective heat transfer amounts to 23.77 watts, while radiative heat transfer constitutes 104.76 watts.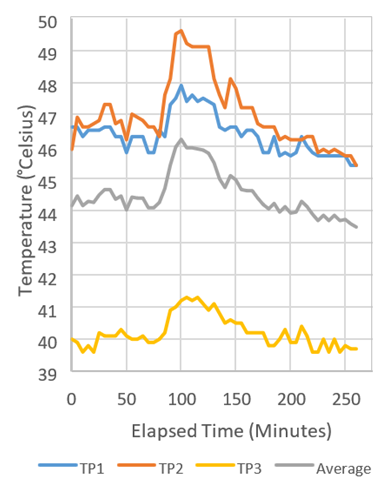 | Figure 4. Temperature measurements of unmodified refrigerator |
Figure 5 presents the thermal data collected over a period of 350 minutes after the application of the adhesive interface onto the condenser. The experiment encountered a disruption due to a power outage.The data does, however, provides insight into the system's response in the absence of power. The indoor environment lacked artificial climate control and any significant heat emitting devices aside from the refrigerator. Therefore, power outages had no discernible impact on the environment.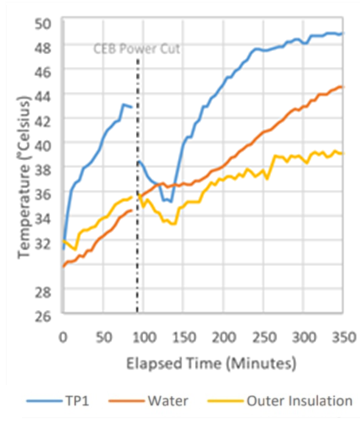 | Figure 5. Temperature measurements of modified refrigerator |
The steady-state heat transfer into the water was determined to be 20.2 Watts, corresponding to 36.4 kJ/kg of water, with a heat flux of 252.5 Watts per square meter across the interface over the 90 minute trial depicted by Figure 6. Notably, within this timeframe, the temperature of 3 litres of water rose from an ambient temperature of 31 degrees Celsius to 40 degrees Celsius.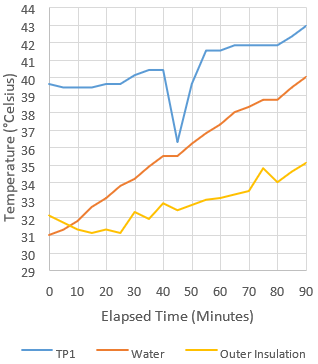 | Figure 6. Temperature measurements of modified refrigerator (Trial 2) |
Figure 7 outlines the daily power consumption patterns of the refrigerator with and without the adhesive interface installed. Observations revealed an average daily power consumption of 2.23 kWh for the unmodified refrigerator under typical domestic operating conditions. Conversely, with the adhesive interface integrated, the refrigerator exhibited an average daily power consumption of 2.13 kWh under similar domestic working conditions.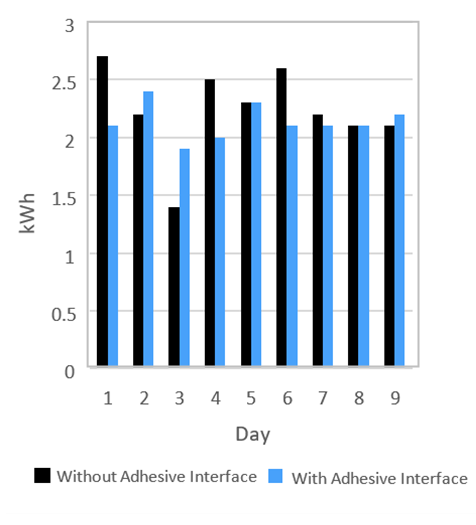 | Figure 7. Power consumption of the unmodified and modified refrigerator |
4. Discussion
Many studies investigated require permanent alterations to the pre-existing system. Some use active systems requiring external energy input to facilitate heat transfer. Research indicates that permanent modifications often entail the risk of adverse effects within the system. A waste heat extractor becomes impractical if the energy or resources expended to extract the waste heat surpass those that could be extracted. Consequently, a sufficient "Return on Investment" is imperative for the successful implementation of such a system.The versatility of the adhesive interface, coupled with its capacity to extract heat without the need for permanent modifications to an existing system, represents a significant advantage. The heat source cooling mode optimizes heat transfer efficiency by employing a water-cooled solution via forced convection. This method of forced convection necessitates no additional local energy input, leveraging the energy head within the water mains.The scalability of this design is a crucial consideration. It can be easily tailored to suit applications ranging from compact to large-scale setups.Aluminium foil-backed Expanded Polyethylene (EPE) foam is a composite insulator comprising a layer of expanded polyethylene with an aluminium foil backing. The EPE foam layer contains numerous air pockets, capitalizing on air's exceptional insulating properties. By isolating air into individual pockets, as in the case of EPE foam, convection is hindered, effectively impeding thermal conduction and convection. The aluminium foil, possessing low radiative emissivity, acts as an efficient barrier against radiative heat loss. Consequently, aluminium backed EPE foam serves as an exceptionally effective insulator across all three mediums of conduction, convection, and radiation.Furthermore, EPE foam offers several additional advantages: it is water and puncture resistant, resistant to termites and fungi, non-hazardous to health, non-crumbling, deters insect nesting, and possesses characteristics of being lightweight, thin, and flexible.The manufacturer of the contact adhesive claims an adhesion strength of 7N/mm2. Theoretical analysis showed that the ratio between the adhesion force and stresses involved was 13494:1. Which is significantly high and well within safety margins. However, over time during operation, the adhesive started to peel at the corners of the interface and slowly detach off in between the condenser an interface due to the stresses involved. The question remains whether the method and style of adhesive application could have influenced the bond, or whether the manufacturer’s claims aren’t up to standard. This detachment would lower the rate of heat transfer considerably, due to the lack of direct contact between the surface of the condenser and interface. The addition of fillers such as Boron Nitride has the potential to enhance the thermal conductivity of adhesives. Boron Nitride boasts exceptionally high thermal conductivity, surpassing that of aluminium by over fivefold. The study by Chung and Lin in 2016 asserts that incorporating Boron Nitride filler elevated the thermal conductivity of composite resins by up to 35.4%. Furthermore, Boron Nitride exhibits chemical inertness and suitability for wet environments. The utilization of fillers appears promising, provided that an augmentation in thermal conductivity can be achieved without compromising adhesive strength or quality [7]. Various forms of waste heat sources are accessible, each presenting distinct characteristics. The surface area and form factor may vary, with surface roughness influencing heat transfer, and temporal availability serving as a decisive factor. The quality of heat emerges as a critical consideration, with high-temperature sources delivering high-quality heat. The rate of heat transfer accelerates with a higher temperature gradient. While high-temperature waste heat sources are infrequent in domestic applications, implementing this system in low-temperature scenarios would significantly alleviate the heating load. For instance, it requires less energy to raise the temperature of water from 40°C to 100°C compared to increasing it from 25°C to 100°C.This design incorporates an automatic water level controller to mitigate the high-pressure head of mains water. During the heat source cooling mode, characterized by a continuous flow of water through the vessel, the pressure at the outlet of the vessel equates to the piezometric head directly above the outlet, representing the height of the liquid to the free surface within the vessel. This head is notably lower than the pressure of mains water, resulting in a considerably reduced flow rate compared to the flow rate of mains water. However, this effect could be counteracted if the vessel and heat source are positioned above the hydraulic circuit. For instance, situating the vessel and refrigerator on the top floor of a residence would supply significant pressure to the floors below during the heat source cooling mode as the water traverses through the vessel.Observations indicate that the targeted heat source, specifically the condenser of the LG refrigerator GLM312RLMC, exhibits non-uniform thermal characteristics. Certain localized regions of the condenser intermittently manifest significantly lower temperatures than the water intended for heating. The temporal availability of heat, as evidenced by compressor run/cut-off cycles, exerts a notable influence on heat extraction dynamics and may lead to a reversal of heat flow back into the condenser via the heated water. Therefore, it is imperative to explore the most optimal location for attaching the interface, considering both temporal and spatial dimensions, to maximize heat transfer efficiency and effectiveness.
5. Conclusions
In conclusion, the thermal analysis of the unmodified condenser revealed an average temperature of 44.5 degrees Celsius across three test points over a 260-minute period, relative to an ambient temperature of 28.7 degrees Celsius. The maximum temperature of 49.6 degrees Celsius was recorded at test point 2, with radiative heat discharge notably surpassing natural convection for the condenser.The discontinuous data points depicted in Figure 5 were attributed to a power outage lasting over an hour, resulting in a decline in condenser temperatures while water temperature continued to rise. This phenomenon can be attributed to the non-homogeneous thermal gradient within the vessel, where cooler water accumulates at the bottom while hotter, less dense water rises to the surface. The maximum water temperature reached during the first trial (Figure 5) was 44.5 degrees Celsius, corresponding to a maximum condenser temperature of 48.9 degrees Celsius.In the second trial (Figure 6), 3 litres of water could be heated to 40 degrees Celsius within 90 minutes. However, heating times and temperatures varied depending on refrigerator load and temporal availability. In personal domestic use, heating times as short as 40 minutes were observed to reach 40 degrees Celsius for 3 litres of water. The trial yielded a heat gain of 36.4 kJ/kg of water and a maximum condenser temperature of 42.9 degrees Celsius at an ambient room temperature of 31 degrees Celsius. The heat flux into the water was measured at 252.5 W/m2.Experimental results indicate no significant deviation in power consumption with the implementation of the system. On average, daily refrigerator power consumption decreased from 2.23 kWh without the system to 2.13 kWh with the adhesive interface installed, suggesting an increase in energy efficiency by 0.1 kWh per day.The cuboidal prototype, measuring 200 x 400 x 40mm and constructed from aluminium and composite EPE foam insulation, effectively extracted condenser heat against an ambient temperature of 31°C, heating water beyond 40°C.Further trials under controlled laboratory conditions are recommended to validate these findings conclusively. Additionally, future research should explore alternative materials and advanced manufacturing methods to optimize the design's performance.
References
[1] | Seyoung Choi, Ukmin Han, Honghyun Cho, Hoseong Lee, Review: Recent advances in household refrigerator cycle technologies, Applied Thermal Engineering, Volume 132, 2018, Pages 560-574, ISSN 1359-4311, https://doi.org/10.1016/j.applthermaleng.2017.12.133. |
[2] | Alessandro Biglia, Andrew J. Gemmell, Helen J. Foster, Judith A. Evans, Energy performance of domestic cold appliances in laboratory and home environments, Energy, Volume 204, 2020, 117932, ISSN 0360-5442. https://doi.org/10.1016/j.energy.2020.117932. |
[3] | Juan M. Belman-Flores, Diana Pardo-Cely, Miguel A. Gómez-Martínez, Iván Hernández-Pérez, David A. Rodríguez-Valderrama, and Yonathan Heredia-Aricapa, Energies 2019, 12, 400; doi:10.3390/en12030400. |
[4] | P Thangavel and S. Mokesh and SA. Reavanth and K. Pragatheeswaran, Performance Evaluation of Domestic Refrigerator with Waste Heat Recovery System, IOP Conference Series: Materials Science and Engineering, Volume 995, No. 1, 2020, doi:10.1088/1757-899X/995/1/012029, https://dx.doi.org/10.1088/1757-899X/995/1/012029. |
[5] | Robert A. Clark, Richard, N. Smith and Michael K. Jensen: An experimental study of waste heat recovery from a residential refrigerator, Energy Conversion Engineering Conference vol 3, Proceedings of the 31st Intersociety, pp 1887-1892. 1996. |
[6] | Vedant Borawake, Tanmay Dixit, Ojas Chitale, Hot and Cold Storage using Waste Heat Recovery System, International Research Journal of Engineering and Technology, Volume: 10, Issue: 05, 2023. |
[7] | Shyan-Lung Chung, and Jeng-Shung Lin, Thermal Conductivity of Epoxy Resin Composites Filled with Combustion Synthesized h-BN Particles, Molecules 2016, 21, 670, https://doi.org/10.3390/molecules21050670. |