H. D. Wickramarathne, N. S. Senanayake, T. S. S. Jatunarachchi
Department of Mechanical Engineering, The Open University of Sri Lanka, Nugegoda, Sri Lanka
Copyright © 2022 The Author(s). Published by Scientific & Academic Publishing.
This work is licensed under the Creative Commons Attribution International License (CC BY).
http://creativecommons.org/licenses/by/4.0/

Abstract
Domestic refrigerators are among the most widely used household appliances. These are the highest energy consuming household appliances due to their widespread use and continuous operation. Many studies have been done to increase the energy efficiency of household refrigerators. Incorporating Phase Change Materials (PCM) is a fairly new approach to improve the performance of refrigerators. The aim of this study was to investigate the effect of PCM on the performance parameters of the refrigerators. A conventional single-door domestic refrigerator was used in this study to carry out the experimental trails incorporating PCM in the evaporator section. A U-shaped PCM container was positioned inside the evaporator compartment so that it is in direct contact with the evaporator inside walls to improve its heat transfer efficiency and to provide a cold storage capacity allowing a few hours of refrigeration without a power supply. The system has been tested with water as the PCM. The experimental results indicate that by integrating PCM in the evaporator, the power consumption is reduced by 10% and the COP is increased by 5.8 - 54.3% compared to the refrigerator without PCM. Also, the PCM incorporated refrigerator indicated a 12.5% reduction in active operating time. When the thermal load was small, water as PCM had a high-power consumption than a conventional refrigerator. With higher thermal loads, water gave better results because of its higher latent heat of fusion.
Keywords:
Domestic refrigerator, COP, Phase Change Material
Cite this paper: H. D. Wickramarathne, N. S. Senanayake, T. S. S. Jatunarachchi, Improvement of Energy Efficiency of Household Refrigerators by the Incorporation of Phase Changing Materials, International Journal of Energy Engineering, Vol. 12 No. 2, 2022, pp. 29-35. doi: 10.5923/j.ijee.20221202.01.
1. Introduction
Household refrigerators are the most widely used appliances in the world and they consume a significant portion of the total domestic energy consumption. In this situation improving the energy efficiency of household refrigerator is an important in terms of energy savings. Studies show that about 1/4th of the energy consumption in a house come from the refrigerator. It also accounts to about 1/6th of the greenhouse gas emissions. Hence improving the efficiency of a refrigerator should be given prime consideration. The efficiency of a refrigerator can be improved by improving efficiency of compressors, heat exchangers and cabinet & door insulation. [1]. Scientists, engineers, and researchers in the field of refrigeration and air conditioning are involved themselves to develop different technical options for improving the energy efficiency of household refrigerators. Followings are the two well-known technical options being considered to increase the energy efficiency.(1) Improving the heat transfer performance in many ways. These include the use of Liquid-suction heat exchangers in condensers, development of loop heat pipe-based evaporators, and using micro fin tubes for both condenser and evaporator, etc.(2) Using Phase Change Materials as a latent heat thermal energy storage system that improves the performance of a household refrigerator by enhancing heat transfer of the evaporator.Latent heat storage using phase change materials (PCMs) is one of the most efficient methods to store thermal energy. Therefore, PCM have been applied to increase thermal energy storage capacity of different systems. The use of PCM provides higher heat storage capacity and more isothermal behaviour during charging and discharging compared to sensible heat storage [2] Using Phase Change Material (PCM) as a latent heat thermal energy storage system is a developing approach to performance improvement of household refrigerators by enhancing heat transfer of the evaporator. Thermal energy storage by Phase Change Material (PCM) has been used for wide applications in the field of air conditioning and refrigeration especially at industrial scale [3].The use of PCMs in the refrigeration system provides various benefits on the system performance and operation. These include temperature stability, increased compressor off- time, higher evaporation temperature, and lower condensation temperature which means a better refrigeration performance [4]. PCMs have high latent heat content and freeze and melt at a specific temperature, accumulating and releasing large quantities of energy during the process of melting and solidification. In the household refrigerator the cooling load stored in the PCM is used to stabilize the temperature in the compartment, for example, by reducing the effects of peak loads and cooling losses during periods when the door is open. Despite the various options are possible to incorporate PCMs to increase the thermal efficiency of refrigerators, no significant progress has been made to make them practically viable due to various reasons. In a study carried out for cold storage it has been found that with the application of a PCM the temperature inside the cold space was 1-4°C lower than without PCM in case of frequent door openings. And, in case of electrical power failures with the use of PCM, temperature maintained was 1-4.5°C lower than without application of PCM [2]. The studies in the use of PCM is continuing to find more reliable methods and gain significant energy savings by the incorporation of PCM in refrigeration systems.The objective of this study is to re-design and fabricate the thermal circuit of domestic refrigerators to enhance the coefficient of performance (COP) by the incorporation of phase changing material.
2. Methodology
The methodology used to study the effect of PCM on the COP of the refrigerator is an experimental approach. In the study a standard single door domestic refrigerator was used to carry out the necessary experiments (Figure 1). The evaporator chamber of the refrigerator was fitted with a container of PCM. The specifications of the refrigerator are given below.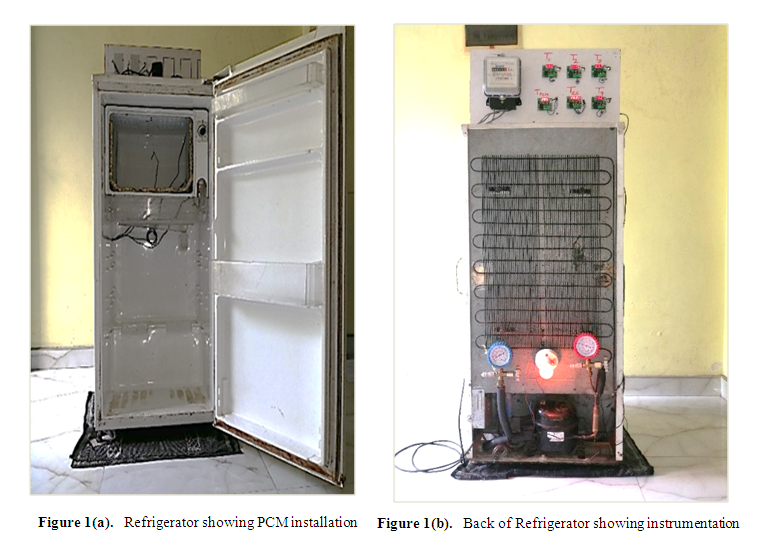 | Figure 1 |
Capacity: 100 Litres single door domestic refrigerator, Evaporator: Aluminium plate type roll bond evaporator, Mode of heat transfer is free convection, Linear length of tube 8.5 m, internal and external diameter of the tube 0.003 m and 0.004 m respectively; Condenser: Mode of heat transfer is free convection; Material of the tube is steel and wire tube; Compressor: Hermetic reciprocating compressor, NS24LHJG, 220V, 50Hz; Expansion device: Capillary tube with internal diameter 1 mm, Refrigerant: R-134a.The experimental setup consisted of a refrigerator, pressure gauges, and thermocouples and energy meter. Five temperature measurement points and two pressure measurement points were selected. Four thermocouple sensors were connected in the refrigeration circuit to measure the temperature of the refrigerator and one thermocouple sensor was placed in the refrigerator compartment. The pressure was measured only at the suction and discharge lines of the compressor.
3. Design of PCM Container
The minimum volume of PCM is calculated to meet the required amount of energy storage by the PCM. If the compartment only contains PCM, the amount of energy (E) stored in PCM neglecting its sensible heat variations is given by the equation (1). | (1) |
Where, ρ = Density of the PCM, V = Volume of PCM, HL = Latent heat of melting of PCM.The following conditions were considered in the refrigerated compartment,• Convective heat transfer at the internal and external surfaces• One-dimensional heat conduction through the refrigerator walls• Heat gain through the gasket of refrigerator door• Radiation heat transfer is neglectedHeat gain through the refrigerator wallsThe amounts of heat transfer rate into the refrigerator from different sides were estimated using equation (2) and the results are given Table 1. The ambient temperature and the refrigerator inside temperature were 30°C and – 10°C respectively. The walls were considered even planes and formed by three layers of steel sheet (outer liner), polyurethane foam (insulation), and a plastic sheet (inner liner).Table 1. Heat transfer through Refrigerator walls 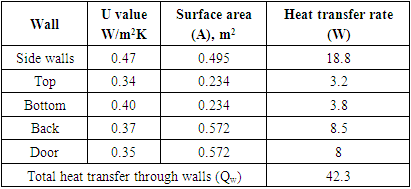 |
| |
|
 | (2) |
Where, U = Overall heat transfer coefficient (W/m2K)
Q = Rate of heat transfer (W) A = Surface area of refrigerator walls (m2) Te - Ti = Temperature difference between environment and cooling chamber (K) L1, L2, L3 = Thickness of walls (m) K1, K2, K3 = Coefficient of thermal conductivity wall layers (W/mK)h1, h2 = Convective heat transfer coefficient of surfaces (W/m2K)Heat gain through gasketsThe heat gain through the gasket was assumed to be steady and the air temperature within the cabinet was uniform. The ambient air temperature was assumed to be constant and uniform. The heat transfer rate through the gasket of the refrigerator door was calculated using the equation 3. | (3) |
Where, Kp = Empirical constant, and Pd = Sealed perimeter of the door.Kp = 0.12 W/mKPd = 3.24 mTherefore,
Therefore, the total thermal power required to maintain the absolute difference between cabinet temperature and the ambient temperature is calculated as below.
To overcome errors, 50% excess power was considered. Therefore.
Total heat gain through the refrigerator walls during compressor off time is therefore,
The average compressor off-time
for no thermal condition is 10 minutes. To marginally meet the required load, the amount of energy stored in the PCM should meet the amount of heat gained through refrigerator walls during compressor off-time. Therefore, the minimum volume for PCM was estimated as given below.
PCM material used is water and heat of fusion is 334 kJ/kg. Therefore, the amount of PCM should be more than 156.33 ml to compensate for the heat gain through the walls during compressor off-time. But PCM should not be thicker than a certain amount to ensure uniform phase change. Otherwise PCM is partially melted/frozen in some areas which reduces its effectiveness.PCM containerA U-shaped box was designed to fit inside the evaporator chamber to contain the phase change material. It was mounted in such a way that the roll bonds are in complete contact with the evaporating surface. For materials for PCM containers, there are many options such as copper, aluminium galvanized iron, and zinc/aluminium coated steel etc. Considering the budget for this project, zinc/aluminium coated steel plate was used to fabricate the PCM container.Details of PCM container are: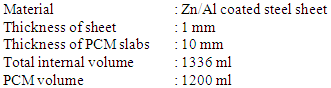
4. Experimental Setup
The experimental set up is shown in Figure 2(a) and 2(b). The procedure used for setting up and conducting trails were according to the methods used by Taib et al (2010) [5].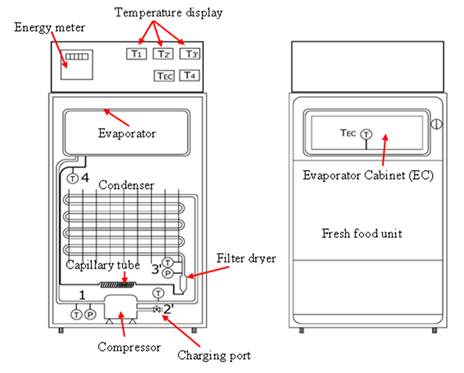 | Figure 2(a). Schematic diagram showing temperature and pressure measuring points |
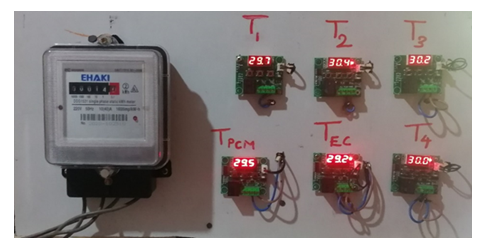 | Figure 2(b). Actual experimental setup |
Experimental conditions and ProcedureIt was assumed that there was no pressure drop across the condenser and evaporator. Experiments were carried out under four different thermal loads at 30°C ambient temperature. The thermal load supply was obtained by using 25W incandescent bulb with a five-step speed regulator as a voltage regulator. The procedure was as follow:1. After switching on the refrigerator, it was left for 3 hours until the system becomes stable.2. The temperature at four locations (after the compressor, after coolant, after evaporation, after expansion, and inside the evaporator cabinet) were measured by W1209 temperature sensors.3. Two pressure gauges were used to measure the evaporation and condensation pressures at the inlet and the outlet (suction and discharge lines) of the compressor.4. At the same time, energy consumption was measured using an energy meter.5. The tests were repeated for 0W, 5W, 10W thermal load conditions inside the evaporator cabinet with and without PCM.
5. Results and Discussion
The compressor on-off mode was triggered by manually using the thermocouple sensor with W1209 temperature controller which is in the evaporator cabinet. The temperature setting point was adjusted so that it starts the compressor at 0°C and stops at -5°C. This adjustment was to keep the evaporator cabinet at a temperature around -5°C. The enthalpies were determined by using P-h diagram for R134a refrigerant. Effect of PCM on Coefficient of Performance (COP)Figure 3 shows the effects of water as PCM on the average COP improvement at different thermal loads. The followings are the significant findings,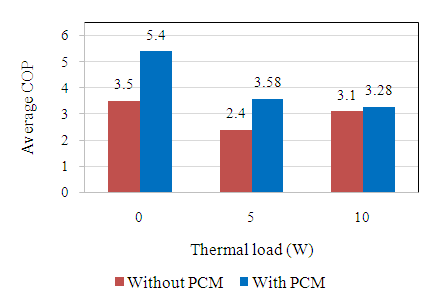 | Figure 3. Average COP with different thermal loads |
It is well established that the performance of the refrigeration system decreases while increasing the thermal load. On the other hand, the application of PCM in a refrigeration system can improve system performance. By raising the thermal load, the system COP decreased even in the presence of a PCM. The reason is that the increase in thermal load results in more partially melted PCM because of lack of sufficient time for phase change that ultimately decreases the system COP.Effect of PCM on evaporation temperature and pressureThe COP increase is due to a higher evaporation temperature and thus a higher evaporation pressure. Figures 4, 5, and 6 show the evaporating temperature variations with time for different thermal loads. They show that the evaporating temperature with PCM for 0 W and 5W is -5°C that is lower than the value without PCM. The evaporating temperature with PCM for 10 W is -3°C that is lower than the value without PCM.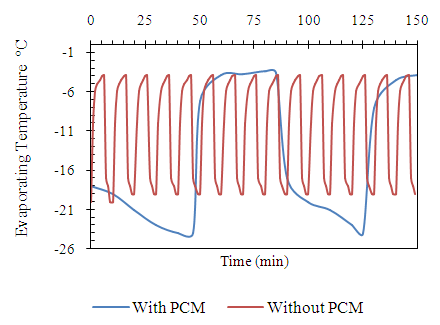 | Figure 4. Evaporating temperature (T4) Vs Time for 0W Thermal load |
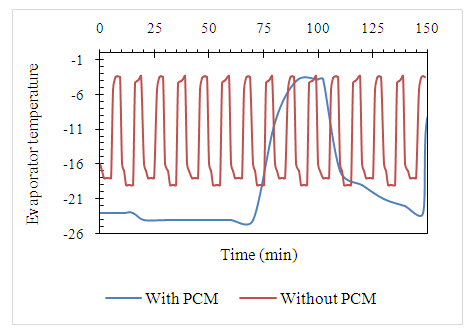 | Figure 5. Evaporating temperature (T4) Vs Time for 5W Thermal load |
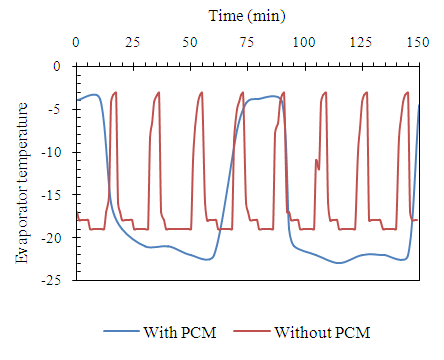 | Figure 6. Evaporating temperature (T4) Vs Time for 10W Thermal load |
Figueres 7, 8, and 9 illustrate how the evaporating pressure is affected by the presence of the PCM for different thermal loads. During the compressor running time, the evaporating pressure is mainly driven by the phase change temperature of the material and this pressure is higher than the value that of without PCM. An average increase of 0.15 bar with the 0 W thermal load and 0.14 bar with 10 W thermal load are observed. But according to the temperature variations with time discussed above, the increase in evaporation pressure does not correspond to the increase in evaporation temperature. This causes a doubt on the accuracy of the evaporating temperature data.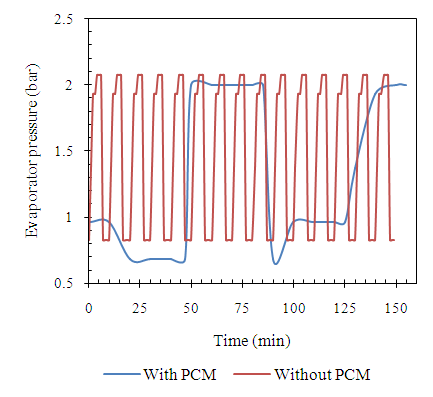 | Figure 7. Evaporating pressure (P1) vs Time for 0W Thermal load |
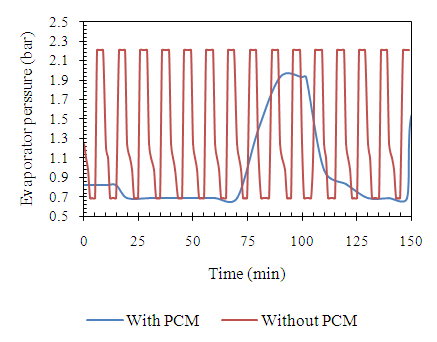 | Figure 8. Evaporating pressure (P1) Vs Time for 5 W thermal load |
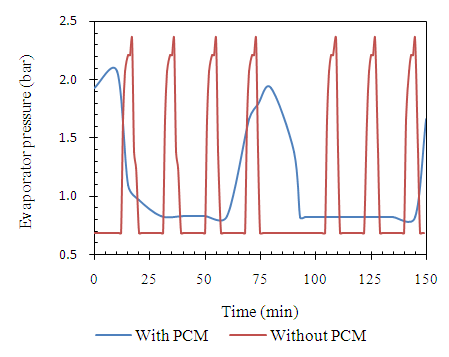 | Figure 9. Evaporating pressure (P1) Vs Time for 10 W Thermal loads |
Effect of PCM on compressor On-Off cycleIn case of without PCM shown in Figure 10, 11, and 12 during compressor off mode the cabinet temperature rises quickly due to the heat inlet by the intake heat from the surroundings due to ambient conditions. As a result, the temperature controller triggers the compressor into on mode quickly. On the other hand, when PCM is used, this excessive heat is absorbed by PCM due to its phase change nature (solid to liquid) which does not allow the compartment temperature to rise quickly. The compressor off-time in the case of without PCM is around 5-6 minutes for different thermal loads. But in the case of with PCM the compressor off-time is 33 - 43 minutes for different thermal loads. As a result, it prolonged the compressor on-cycle and ultimately decreased the compressor on–off cycle to about 4–8 times thus saving about 7.5% of the compressor running time.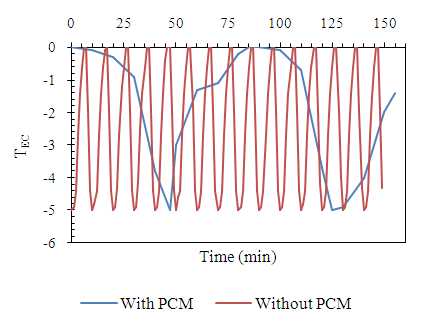 | Figure 10. Evaporator cabinet temperature (TEC) Vs Time for 0W Thermal load |
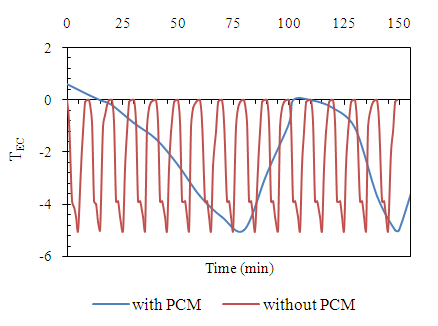 | Figure 11. Evaporator cabinet temperature (TEC) Vs Time for 5W Thermal load |
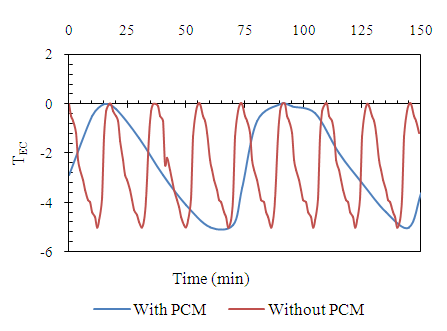 | Figure 12. Evaporator cabinet temperature (TEC) Vs Time for 10W Thermal load |
The effect of PCM on the power consumption of refrigeratorTables 2 and 3 show the measured values of the energy consumption, total cycle time, and cycle operating time under different thermal load conditions with and without PCM at the evaporator section. In both cases the energy consumption of the refrigerator increased with the thermal load and the power consumption without PCM was higher than that of the refrigerator with PCM for 0 W thermal load. In this case, the energy consumption increased by 23%. In the other two cases, the energy consumptions are reduced by 10% and 0% for 5W and 10W thermal loads. From this, we can conclude that when the thermal load was small, water as PCM had a shorter compressor-on-time compared to others and high-power consumption, while for higher loads water was a better candidate because of its higher latent heat of fusion.Table 2. Power consumption for different thermal loads 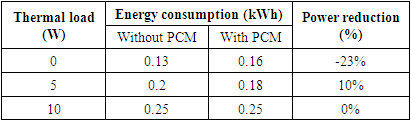 |
| |
|
Table 3. On-Off Cycle ratio for with and without PCM 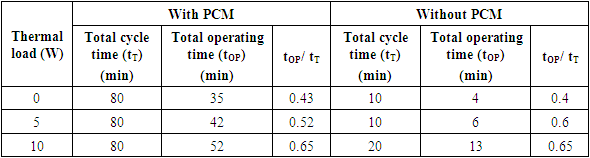 |
| |
|
PCM at the evaporator section also gives slower fluctuation of compartment temperature and more stable conditions against thermal load variations. However, the incorporation of PCM at the evaporator section increases the compressor running time initially and raises the condensation temperature. Therefore, it causes high power consumption initially with the PCM incorporated into refrigerator. Also, from Table 3, the ratios of operating cycle time to the total cycle time for the refrigerator without PCM are 0.4, 0.6, 0.65 for 0 W, 5 W, and 10W thermal loads respectively. However, the corresponding values for refrigerator with PCM are 0.43, 0.52, 0.65 respectively. Further, it can be noticed that the ratio of operating cycle time to the total cycle time for the refrigerator with PCM is less when the thermal load inside refrigerator increases.
6. Conclusions
In this work, the thermal circuit of a domestic refrigerator was re-designed and fabricated to enhance the COP by the incorporation of phase changing material at the evaporator section. Based on this design, an experimental test rig was developed to conduct a series of experimental studies to minimize the energy consumption of the single-door household refrigerator. From the experimental results, the following conclusions were made.• The experimental results show that under the different thermal load conditions, the energy consumption of the household refrigerator with a PCM is reduced by 10% for 5W and the COP is increased by 5.8-54.3% compared to the refrigerator without PCM. • To effectively integrate a PCM in a refrigerator compartment it is necessary to employ PCM emplacements in the evaporator walls of the compartment which helps to rapidly stabilize and homogenize the temperature. This increases the cut-off time of the compressor and thereby minimizes the energy consumption of the refrigerator.• A comparison of the PCM incorporated refrigerator with conventional refrigerator indicated a 12.5% reduction in compressor operating time. • When the thermal load was small, water as PCM had a high-power consumption than a conventional refrigerator, while for higher thermal loads, water was a better candidate because of its higher latent heat of fusion.
References
[1] | Arun Kappen, Titto John George, Vinay V. N. (2016). Performance Improvement of a Household Refrigerator by Use of a Phase Change Material, International Journal of Scientific & Engineering Research, Volume 7, Issue 3, March-2016 58 ISSN 2229-5518. |
[2] | Raj V, Goswami T. K. (2018). Use of phase change material (PCM) for the improvement of thermal performance of cold storage. MOJ Curr Res & Rev. 2018; 1(2): 49-61. DOI: 10.15406/mojcrr.2018.01.00010. |
[3] | Tulapurkar, Chetan. (2010). “Phase change materials for domestic refrigerators to improve food quality and prolong compressor off time.” International refrigeration and air conditioning conference. 2010. |
[4] | James Riffat, Cagri Kutlu, Emmanuel Tapia-Brito, Samuel Tekpetey, Francis B. Agyenim, Yuehong Su & Saffa Riffat (2022). Development and testing of a PCM enhanced domestic refrigerator with use of miniature DC compressor for weak/off grid locations, International Journal of Green Energy, 19:10, 1118-1131, DOI: 10.1080/15435075.2021.1984244. |
[5] | Taib, M. Y., Aziz, A. A. and Alias, A. B. S. (2010). Performance Analysis of a Domestic Refrigerator: In proceedings of National Conference in Mechanical Engineering Research and Postgraduate Students (1st NCMER 2010) 26-27 MAY 2010, Kuantan, Pahang, Malaysia, pp. 582-591. |