Mwewa Chikonkolo Mwape1, 2, 3, Isaiah Etemo Muchilwa2, 3, 4, Zachary Otara Siagi2, 5, Francis D. Yamba6
1Department of Energy Engineering, Moi University, Eldoret, Kenya
2African Center of Excellence in Phytochemicals, Textile, and Renewable Energy (ACE II PTRE) Eldoret, Kenya
3German Institute for Tropical and Subtropical Agriculture & Transdisciplinary and Social-Ecological Landuse Research and Agricultural and Biosystems Engineering, University of Kassel, SteinstrateBe, Witzenhause, Germany
4Department of Electrical & Communications Engineering, Moi University, Eldoret, Kenya
5Department of Mechanical & Manufacturing Engineering, Moi University, Eldoret, Kenya
6Department of Mechanical Engineering, University of Zambia, Lusaka, Zambia
Correspondence to: Mwewa Chikonkolo Mwape, Department of Energy Engineering, Moi University, Eldoret, Kenya.
Email: |  |
Copyright © 2020 The Author(s). Published by Scientific & Academic Publishing.
This work is licensed under the Creative Commons Attribution International License (CC BY).
http://creativecommons.org/licenses/by/4.0/

Abstract
A static aerated Compost Reactor (CR) was developed in Kitele, Kenya, and used for evaluating the efficacy of generating, extraction, and utilization of compost heat as a source of clean energy. A Compost Heat Exchanger (COHE), hydronically operated, was developed in order to extract and transfer the heat. Energy generated by the compost reactor was calculated, using temperature profiles, captured by the TC-08 data loggers via the K type (PTFE) thermocouples. Heated water to 55°C was obtainable. The total extracted energy from compost was and 174 kWh.
Keywords:
Compost heat exchanger, Thermophilic, Characterization
Cite this paper: Mwewa Chikonkolo Mwape, Isaiah Etemo Muchilwa, Zachary Otara Siagi, Francis D. Yamba, Waste to Energy: Heat Recovery from the Compost Reactor as a Source of Renewable Energy, International Journal of Energy Engineering, Vol. 10 No. 1, 2020, pp. 10-15. doi: 10.5923/j.ijee.20201001.02.
1. Introduction
Composting is the biological decomposition of organic materials in the presence of oxygen (aerobic) [1–3], producing compost, carbon dioxide, heat and water. The aerobic process is exothermic with four major microbiological steps; mesophilic carried out by Mesophilic microorganisms, thermophilic involving thermophilic microorganisms, cooling, and maturation [4]. Stiff policies and regulation recently on the safety of in-vessel waste processing systems, and disposal, underpins the safe and reliable composting systems, with precise moisture and temperature regulation [5]. Current composting methods and technologies highly recommend the utilization of high thermophilic temperatures (˃70°C), high enough to control pathogens [5].Basically, composting processes can be classified into three, pile composting which uses small volumes with less than three meters piles in diameter, in-vessel composting cube or boxes) using small volumes fabricated from wood, masonry metal or other materials and beds composting that uses large trapezoidal volumes rolls usually forced aerated or receive turning frequently to aerate [6].The product of the composting process, compost, is widely used for soil amendment and as a fertilizer. Soil fertility is more important now than before, because of the increased food demand [5]. Hygienisation of both farm and municipal organic wastes to control airborne and soilborn pathogens produced in landfill sites through suppression of harmful micro-organisms by composting, is key to abating greenhouse gas emissions [3,4].High cost of composting process rather than the availability of Biomass Feedstocks deters the commercialization of the bio wastes processing into bioenergy. However, as Energy demand increases rapidly, bioenergy is seen as one of the cheaper renewable energy sources with low climate change effects [8]. The challenge therefore, is the sustainability of heat generation and extraction from the aerobic process, that has been characterized by sporadic efforts with disjointed literature [9].Recently, a focused study on the Compost Heat Recovery Systems (CHRSs) and rates covering 45 CHRSs from 16 different countries, has been presented [9]. The reported average recovery rates are unpredictable and vary greatly. The lab-scale systems reported average rates of 1.9 Mj/hr (1.2 Mj/kg dm), 20 Mj/hr for pilot scale tests and commercially, 205 Mj/hr (7.1 Mj/kg dm) [6,7]. Thus, it is envisaged that heat generated composting can be a great source of renewable energy.The objective of this paper is to present the development and performance evaluation of a pilot-scale compost reactor set up in Kitale. Temperature monitoring was by means of the thermocouples placed within the reactor connected to the PC for real time monitoring via the TC-08 PicoLog Data Loggers with Temperature accuracy of ±0.2% of reading and ±0.5°C. An easy to install and dismantle, Hydronic COHE, mounted on a rectangular frame made out of the 10mm square tubes, was used for extraction of heat from the CR. The COHE was connected to the water tank that provided heating to the inside environment, whose rates of heating have been evaluated.The specific objective of the study were:• Feedstock characterization,• Development of the CHRSs,• Performance Evaluation.
2. Materials and Methods
2.1. Site Geographical and Climatic parameters
This study was carried out in Kitale, Trans-Nzia County in Kenya with geographical location of Latitude 01° 08’ 39N and Longitude of 034° 59’48E. The study area is located at an average of 1907 m elevation, with mean annual temperature: maximum 26.4°C and 12.3°C minimum; average annual mean rainfall of 1259.1 mm with 85.6 sunshine hours per annum.
2.2. Feedstocks Matrix
Successful composting and heat recovery depends on both internal (Feedstocks chemical and physical composition) and external (climatic and weather) variables. Both factors condition the operation of the microorganisms responsible for breaking down the feedstock nutrients [2,5].The characterization of Feedstocks from Kitale at the Kenya Agricultural and Livestock Research Organization (KALRO) helped to optimize the ranges recommended for the process of composting [2,10] as follows:• Total weight of compost reactor matrix-1350 kg,• Moisture content- (779.4 kg) 58%,• C/N ratio- 26:1,• Oxygen content- (122.8 kg) 6-15%,• pH-6.8• Bulk density (free air porosity)- 35 – 50%,• Temperature below 65°C.By composition the feedstock matrix contained; 9.1% (122.8 kg) air, 57.7% (779.4 kg) moisture, Cow manure, 10.5% (180.7 kg), Green weeds (804 kg) 7.2%, Maize cobs 8.6% (134 kg), Maize stovers 5.9% (91 kg) and 1% (17.7 kg) of sawdust. The overall specific heat capacity (Cp) from the feedstocks substrates was 3.03 kJ/kg/°C. The C/N ratio, was calculated using the following equation; | (1) |
Where; X = total weight of ingredient x, z = total weight of ingredient z, %Cx, %Cy, %Cz… = %carbon of ingredients x, y, z… (Dry weight basis) and %Nx, %Ny, %Nz… = %Nitrogen of ingredient x, y z… (Dry weight basis) [12].
2.3. Compost Reactor Development and Parameters
Designed as a standalone rectangular, passively aerated, using the gaps left on the base of the pile as shown in Figure 1, the CR had a steel reinforced frame outside 0.002 m square steel tubes with the length of 1.84m, width of 1.54 m and height of 1 m, resulting in a volume of 2.83 m3. The surface area was 12.43m2 translating into a surface area-to-volume ratio of 4.4[m2/m3]. The steel frame's outer layer, on all sides, rapped with PP woven fabric to ensure that the material is forming the shape and not spilling out. Aeration was by means of the chimney effect and a space of 0.06 m left in between the Compost reactor frame and the Ground to allow air circulation and allow leachate to drain easily.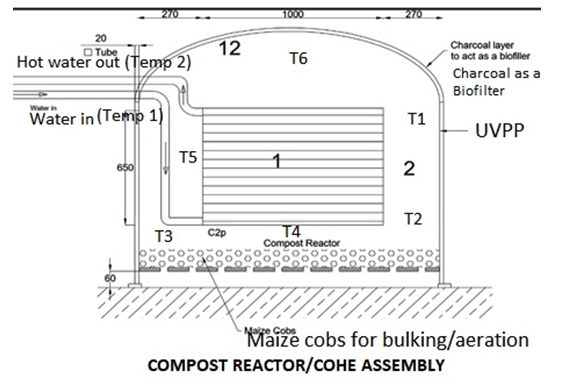 | Figure 1. Compost Reactor/COHE assembly (1=COHE, 2= Compost reactor filled with the Feedstock mixture, T1 to T6= PTFE thermocouples. UVPP=ultra violet treated polypropylene material) |
Figure 1 also shows the Compost reactor design assembly indicating the position of the COHE and the thermocouples (T1 to T6) installed at different levels to monitor temperatures from within the pile. Table 1 gives the summery of the compost reactor parameters used in this experiment,Table 1. Summery of the Compost reactor parameters 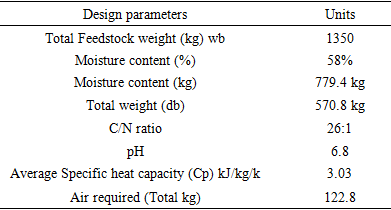 |
| |
|
2.4. Temperature Profiles
Temperature profiles where captured by means of the Polytetrafluoroethylene (PTFE) thermocouples positioned as shown in Figure 1 from T1 to T6, Testo 174H and FreeTec data loggers as shown in Figure 2. The TC-8 Picolog Data loggers with Temperature accuracy of ±0.2% of reading and ±0.5°C, were used to transmit the data to the PC via a 15 m USB cable. The PTFE thermocouples, chosen because of the robustness to with stand harsh conditions within CR due to humidity, pH changes and microorganisms actions resulting into chemical reactions [13,14]. [2], designed a wooden rod that was inserted into the Polypropylene to avoid corrosive environment effects on the sensor. 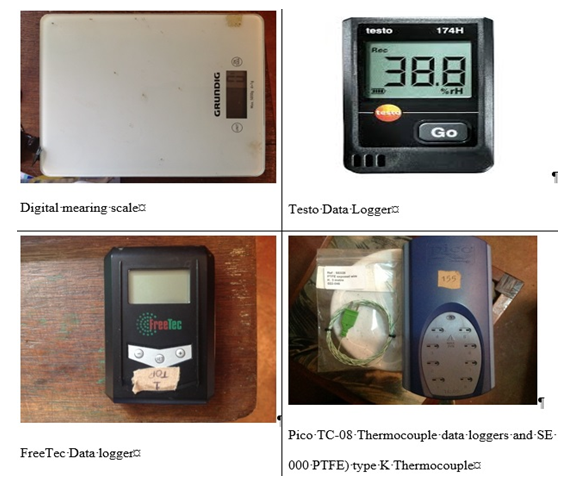 | Figure 2. Data capturing equipment |
2.5. Heat Extraction System
Heat capture was by means of pumping the water through the COHE, within pile Hydronic type, constructed to extract heat from the compost pile with three main parts. COHE was made up of parts namely; rectangular shaped main frame, the 120 meters low density polyethylene (LDPE) pipe with inner diameter 0.0195m, with a wall thickness of 0.003m, 7.4 m2 surface Area (procured from the local market in Katale) winded around the frame. The maximum volume of water in the exchanger tube at any given time was 35.7 liters or 35.7 kg of water. Figure shows the Compost/COHE assembly depicting the partially buried COHE in Feedstocks mixture. 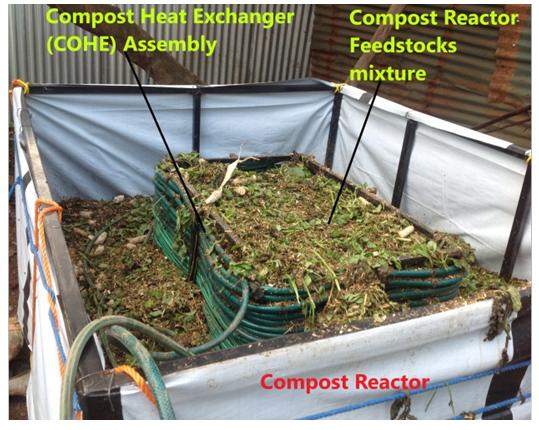 | Figure 3. Compost Reactor/Compost Heat Exchanger Assembly |
Two Mini DC12V 3 M micro-motor submersible brushless water pumps with 5W power consumption, 240l/hr static flow rate, 3 m static lift with 30,000 operating hours, were used to circulate water in a closed loop circuit. The pumps where tested and flow indicated, using a bottle with a known capacity and a stop timer (0.025 l/s). Polyethylene (PE) foam insulation material tightly wrapped around the fittings and connections between the compost reactor and the Water Tank (WT), improved heat insulation. One thermocouple mounted inside the supply pipe from the pile to the WT, monitored the temperature of the water.The temperature results were recorded with a regular time step a minute through-out the 19 days of the experiment time, but averaged for each batch of 30 minutes to derive overall the relationship between time and temperature.
2.6. Energy Values
Energy Generated in the Compost ReactorThe method recommended by [15], used by [5] and [2], of using a standard heat flow into a substance at constant pressure was used, was used to calculate the energy stored in the compost. [16] is one of the researchers who utilized this method too, applying the equation below;  | (2) |
Where; Q is heat energy stored in the compost (kJ/kg), M is compost mass (kg), Cp = overall specific heat of the ingredients in the feedstocks of the compost reactor at a constant pressure (kJ/kg/k) and ∆T is the change in Temperature. Heat energy values, were worked out at each 30 minutes time step using the estimated feedstock material concentration and standard specific heat capacity values. Energy Extracted The energy extracted by the COHE was calculated using the following equation: | (3) |
Where; Q is power in watts,
is mass flow rate in kg/s (density), Cp is the heat capacity of water at constant pressure and
is the temperature differences between the inlet pipe and outlet pipe [2,15,16].
3. Results and Discussions
3.1. Temperature Profiles before Extraction in the Compost Reactor
Figure 4 shows the average temperature profiles between 4 June 2019 and 19 June 2019 (day 1 to 19th day) in the compost reactor and COHE water in and out. The compost reactor temperatures reached 60°C after 1.88 days and highest of 68.9°C recorded, on 6 June 2019 at 13:57 from a starting point of 25.5°C, before decreasing to a mean of 41.1°C on 28 June 2019. The 2-4 days period it took for the temperatures to reach the above 60°C, is in agreement with [19] when composting with an aerated system with one direction of airflow but higher than 0.63 days reported by [17]. Similarly, [5] reported compost reactor temperatures of 60°C after two days from an in-vessel tunnel composting facility in Scotland and [20] reported 65°C while compost Horse based manure, after four days.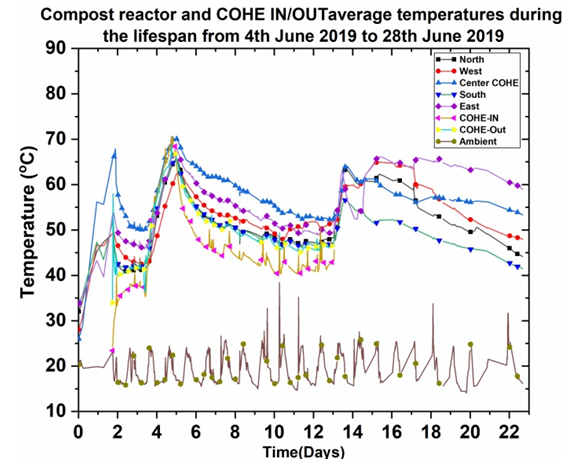 | Figure 4. Temperature profiles in the Compost reactor and IN/OUT COHE water |
A temperature of 60°C was achieved, during winter for a 1.5 to 2 meters compost depth [21]. Furthermore, [2] recorded 65°C in 2 days, while composting using a passively aerated static reactor with enhanced aeration by means of channels arranged vertically. Moist air was evidently push up through the gaps left by the balking materials due to natural convectional system after the temperature started to increase and formed icicles on the top PVC tapeline cover. Covering helped to keep the moisture inside the pile and allow diffusion driven aeration.
3.2. Temperature Profiles in the COHE and Water Tank during Extraction
The results of the COHEIN and COHEOUT pipe outlets for a trial period of 13 days from 6 June 2019 to 19 June 2019 are shown, in Figure 5, indicating the useful energy in terms of water-heated temperatures and energy generated by the COHE. It was observed that a series of peaks and troughs where present during the times the COHE was operational. The COHE, was operationalized when the compost reactor average temperatures were above 65°C on 6 June 2019 at 13:35 (day 1.74). The Initial Temperature of water in the HAC (COHEIN) was 23.4°C as shown in Figure 5 at A1. 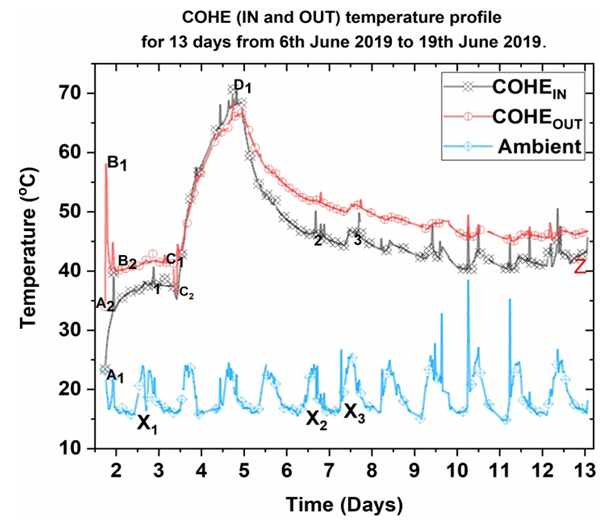 | Figure 5. COHE IN/OUT water Temperature |
Upon turning on the recirculation pump, the COHEOUT, temperature went up to 33.9°C, at an ambient of 21.5°C and Compost Reactor temperature of 65.6°C. At this time set (1.74days), COHEOUT and COHEIN difference was 10.6°C as shown in Figure 6 at A3. Within 30 minutes, the COHEOUT temperature rapidly increased to 58.1°C as denoted by B1 in Figure 5. The Water Tank temperature consequently rose from 21.5°C to 25.5°C.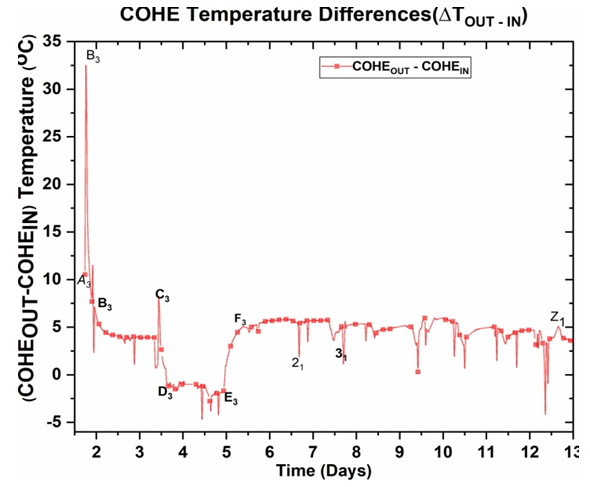 | Figure 6. COHE IN/OUT Temperature summery |
However, the COHEOUT Temperature sharply decreased from 58.1°C to 40.4°C within 5 hours at (1.96days) denoted by B2 (Figure 5) and the Water Tank (COHEIN) temperature had increased to 33.7°C, the compost reactor temperature went down to 61.9°C. The sudden drop was due to the dilution of the COHE water temperature with the cold water from the Water Tank. Between B2 to C1 (16:27 to 19:45pm) on 7 June 2019, the temperature remained constant between 40.1°C to 42°C in the COHEOUT and 30°C to 38°C in the COHEIN the average
been about 10°C. On 7th June 2019 at 17:53, denoted by C1 to C2, the Pumping system was stopped briefly to seal the water leakages hence the trough shown C1 to C2 (Figure 5). The temperatures from the COHE went down from 41°C to 36.2 by 07:28 am on 8th June, 2019. At these time set the COHEIN temperature was at 34.9°C, ambient was 16°C and around average of 51°C from the compost reactor. The quick rise and drop of the temperature was also experienced by [20], where an initial activation of the heat extraction using a compost heat extractor with the fluid mixed with water and Glycol was used to heat the water from 5°C to 48°C, but dropped to 38°C after 5 minutes. [2] The strategy of finding an optimum amount of heat that could be extracted without affecting the composting process dynamics was reported [2], by, staggering the extraction rates and times. At point X1, X2, X3 and 1, 2 and 3 (Figure 5), average temperature peaks of up to 8°C, were witnessed because of the daytime natural solar radiation heating the water in the HAC via the solar Collector and high ambient temperature passing through the compost reactor by the chimney effect. The peak decreases as soon as the solar radiation decreases. Figure 6 highlights the solar radiation induced peaks at C3.On 8 June 2019 at 07:29, the compost reactor average temperatures dropped to around 51°C and it was decided that the Tank water be heated using a 400/750w water heater procured locally. The decision was in (Figure 4 and 7) order to keep the system temperatures above 55°C and activity C2 to D1 in Figure 5 depicted. The water attained 68.4°C and at 20:58 on 9 June 2019 after operating for 37 hrs and 29 minutes, the heater, was turned off. The total energy used by the electrical heater was 28.1 kWh. This resulted in the negative COHEOUT - COHEIN depicted on Figure 5 and 6 at D3 to E3. The compost average temperature rose to 69°C. The pattern of having the positive value for temperature difference resumed after switching off the electrical. The average difference temperature throughout the heat extraction period from 6 June 2019 to 19 June 2019 was 3.5°C. The maximum COHEIN temperature was 70.1°C and 68.7°C for the COHEOUT, minimum of 23.4 and 33.9°C respectively. Ambient Temperature was 14.6 and 38.4 minimum and maximum respectively. Figure 4.18, is a summary of the average temperature profiles (
T) between COHEOUT and the COHEIN. Extracted Energy from the COHE values where then calculated using temperature differences.
3.3. Compost Reactor Generated and COHE Cumulative Extracted Energy
The energy values where calculated using the average temperatures described in Figure 5 and 6 (COHE cumulative extracted energy) and Figure 7 for the Energy generated in the Compost Reactor. The energy within the Compost reactor, with the cumulative heat energy extracted, at each time interval, worked out and presented in Figure 8 together.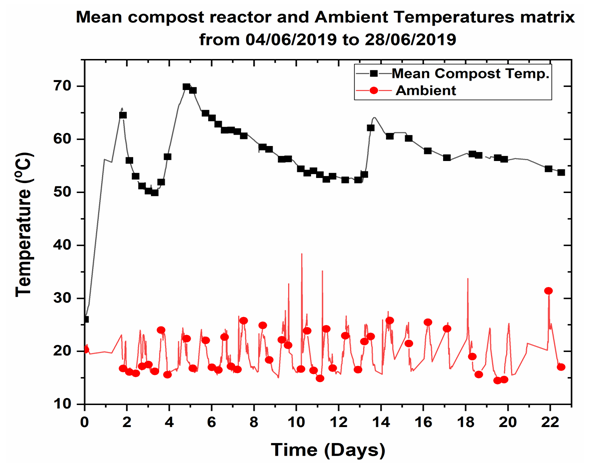 | Figure 7. Mean Compost Reactor Temperature and ambient |
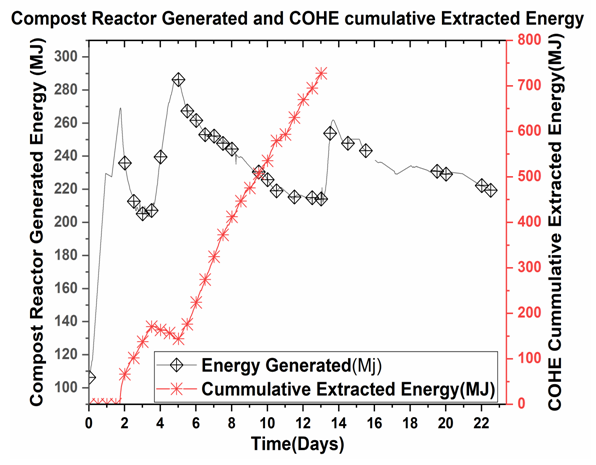 | Figure 8. Compost Generated and COHE cummulative Extracted energy |
The energy stored in the compost reactor increased from 106 MJ to a peak of 286MJ on day5 (9 June 2019) as shown in Figure 8. The results are in the same range as [20], who achieved 279 Mj to 326 MJ on day number 4. During the trial period, the compost energy decreased to 210MJ [20].Cumulative extracted energy increased to727 MJ, from 6 June to 19 June 2019 during the extraction trials. The total energy extracted in kWh was 202 kWh. Now the energy used to heat the water with the electrical heater was 28.1 kWh. Therefore the net energy extracted was 174Kwh, translating into 7.8 kg/kWh or 538kJ/kg per initial mass compost weight matter and 1273kJ/kg on dry matter. This energy values are in the range generated by [20] of 5.7 kg/kWh, but less than those reported by [5] Irvine of 6000 kJ/kg/day and [21] of 2791 kJ/kg/day from straw and poultry manure. However [17], reported 2435 Kj/kg/day when composting paper mill sludge with the boiler litter [17]. The 1273 kJ/kg DM recovered is in the range reported by [9] of 1159 kJ/kg for pilot scale and 4302 kJ/kg DM. For commercial 7084 kJ/kg was reported [9]. A 510 kJ/kg DM heat recovering has been reported recently [1].Discrepancies in cumulative energy values are due to differences in the methods and rates of decomposing subjected to different conditions such as thermal insulation, feedstock types, and methods of extraction. This makes direct comparisons difficult to arrive upon and ultimately ineffectual. However, the values achieved in this research are comparable to other researchers and are reliable.
4. Conclusions
The total energy extracted from the compost in this research was 174 kWh net for 13 days of extraction. This resulted in heating the 340 kg of water to an average of 55.8°C. It is also highlighted the utilization of high carbon density feedstock materials, can prolong the heat recovery time from the compost reactor.The simpler method of extracting the energy from the compost reactor using a COHE made from simple localized materials & easy to assemble and dismantle was highlighted. The COHE delivered water of above 55°C using less energy through two 5 watts pumps hence giving the high COP.Utilization of the energy generated from the compost system is multipurpose. The heat can be used for heating water for domestic uses such as washing, bathing and heating rooms in cold weather conditions. With hybridization with solar energy, the energy could be used for drying food staffs.Further research in sizing, reduction of heat loss, and cost implications of proposed energy generating system, is recommended.
ACKNOWLEDGEMENTS
Authors greatly acknowledge the financial support from the African Center of Excellence in Phytochemicals, Textile & Renewable Energy (PTRE) funded by the World Bank and Moi University. The project “Empowering Jua Kali to Combat Mycotoxins in Kenya’s Maize Supplies: A parcipatory Transdisciplinary Knowledge Integration,” funded by Volkswagen Foundation (VW), through the German Institute for Tropical and Subtropical Agriculture & Transdisciplinary and Social-Ecological Landuse Research and Agricultural and Biosystems Engineering, University of Kassel, Germany, and Zambia Electricity Supply Cooperation Limited.
References
[1] | J. Bajko, J. Fišer, and M. Jícha, “Condenser-Type Heat Exchanger for Compost Heat Recovery Systems,” Energies, vol. 12, no. 1583, pp. 1–16, 2019. |
[2] | J. Bajko, J. Fišer, and M. Jícha, “Temperature Measurement and Performance Assessment of the Experimental Composting Bioreactor,” EPJ Web Conf., vol. 02003, pp. 1–5, 2018. |
[3] | T. Haug R, The Practical Handbook of Compost Engineering - Roger Tim Haug - Google Books. 1993. |
[4] | R. Rynk, aarten van de Kamp, G. Willson, M. E. Singley, T. L. Richard, and J. J. Kolega, On-Farn Composting Handbook. Cooperative Extension, 1992. |
[5] | G. Irvine, E. R. Lamont, and B. Antizar-Ladislao, “Energy from Waste : Reuse of Compost Heat as a Source of Renewable Energy Energy from Waste : Reuse of Compost Heat as a Source of Renewable Energy,” Int. J. Chem. Eng., no. May, p. 12, 2014. |
[6] | T. L. Alves, G. M. De Almeida, A. Michael, and P. Bertino, “Proportions of Organic Waste in the Process of Composting,” Agric. Food Sci. Res., vol. 6, no. 1, pp. 15–21, 2019. |
[7] | W. G. C. Forsyth and D. M. Lvenlet, “Composting ii.--a,” pp. 34–39, 1947. |
[8] | C. A. Wright and S. D. Wright, “The Role of Bioenergy in European Cities,” vol. 36, no. 2, pp. 204–208, 2013. |
[9] | M. M. Smith, J. D. Aber, and R. Rynk, “Heat Recovery from Composting: A Comprehensive Review of System Design, Recovery Rate, and Utilization,” Compost Sci. Util., vol. 25, no. 1, pp. S11–S22, 2017. |
[10] | B. Antizar-Ladislao, G. Irvine, and E. R. Lamont, “Energy from waste: Reuse of compost heat as a source of renewable energy,” Int. J. Chem. Eng., vol. 2010, 2010. |
[11] | E. Epstein, Induatrial composting: Environmental Engineering and Facilities Management. London: Taylor & Francis Group, 2011. |
[12] | B. Columbia and Ministry of Agriculture and Food, BC Agricultural Composting Handbook - BC Ministry of Agriculture, vol. 3100, no. 382. Canada, 1998, p. 70. |
[13] | H. Keener, “Challenges and Opportunities in Composting Organic Waste • Challenge today is reducing fossil fuel use . Why :,” 2008. |
[14] | T. C. Problems, “MONITORING THE COMPOSTING.” |
[15] | R. T. Haug, The Practical Handbook of Compost Engineering. New york: Lewis Publishers, 1993. |
[16] | H. M. Keener, D. L. Elwell, K. Das, and R. C. Hansen, “Remix Scheduling During Composting Based on Moisture Control,” Am. Soc. Agric. Eng., vol. 39, no. 1988, pp. 1839–1845, 1996. |
[17] | H. M. Keener, K. Ekinci, D. L. Elwell, and F. C. Michel, Jr, “Principles of Composting Process Optimization Aeration Design.” p. 15, 1991. |
[18] | Z. Adams, “Understanding Biothrmal Energy,” Univ. Vermont, p. 128, 2005. |
[19] | K. Ekinci, “Theoretical and Experimental studies on the Effects of Aeration Strategies on the Composting Process,” The Ohio State University, 2001. |
[20] | B. Allen and P. D. Chambers, “The Design and Development of Heat Extraction Technologies for the Utilization of Compost Thermal Energy,” Galway Mayo Institute of Technology, 2009. |
[21] | M. S. Finstein, F. C. Miller, and P. F. Strom, “Monitoring and Evaluating Compostin Process Performance,” Water Environ. Fed., vol. 58, no. 4, pp. 272–278, 1986. |