U. G. Kithsiri1, N. S. Senanayake2, Ruchira Abeyweera2
1University of Gavle, Sween
2Department of Mechanical Engineering, The Open University of Sri Lanka, Nugegoda, Sri Lanka
Correspondence to: N. S. Senanayake, Department of Mechanical Engineering, The Open University of Sri Lanka, Nugegoda, Sri Lanka.
Email: |  |
Copyright © 2018 The Author(s). Published by Scientific & Academic Publishing.
This work is licensed under the Creative Commons Attribution International License (CC BY).
http://creativecommons.org/licenses/by/4.0/

Abstract
Load frequency control is very vital to maintain system stability in power network. In Sri Lanka load frequency control is normally done with the support of hydro power generation units. However, during the periods of drought, gas turbines are heavily used to meet the power demand; hence frequency control has to be done with a gas turbine. Only one combined cycle power plant in Sri Lanka is used to frequency control. As CCGT (Combined Cycle Gas Turbine) is coupled with the steam turbine through a Heat Recovery Steam Generator (HRSG), the level of operation of the gas turbine affects the HRSG because of varying gas turbine exhaust gas temperature and the flow rate. In frequency control mode operation naturally the gas turbine has to be operated in a range of power output responding to power demand. This sets a minimum level of gas turbine power that will not affect the HRSG. This study was carried out to investigate the possibility of using combined cycle power plant (CCPP) for load frequency control without affecting the HRSG. The experimental trials were carried out at 60 MW gas turbine output, it was experimentally proved that the selected CCPP can be operated for frequency control at selected load (60MW). Further, the gas turbine when operated at 40 MW output, the exhaust gas temperature and the flow rate derived from the characteristic relationship of gas turbine were used to predict the critical parameters of the steam cycle. The finding showed that the HRSG parameters are not in safe working ranges. This indicates that the minimum gas turbine output should lie between 40 MW and 60 MW.
Keywords:
Frequency Control, HRSG, CCPP
Cite this paper: U. G. Kithsiri, N. S. Senanayake, Ruchira Abeyweera, Frequency Control Operation of a Combined Cycle Power Plant and Impact on Heat Recovery Steam Generator – A Case Study, International Journal of Energy Engineering, Vol. 8 No. 4, 2018, pp. 89-92. doi: 10.5923/j.ijee.20180804.01.
1. Introduction
Maintaining voltage and frequency within designated limits is an essential requirement for the operation of any power network. The system frequency is determined by the speed of rotation of the generators in the system, which in turn is determined by the balance between generator and load power. During the operating period, the deviations between the actual generation and the actual load are taken care of by frequency control schemes which activate frequency control reserves to maintain the balance between generation and consumption. Frequency control reserves are power reserves kept in participating power plants. Load Frequency Control is badly needed for a power system because, if the normal frequency is 50 Hertz and the system frequency falls below 47.5 Hertz or goes up above 52.5 Hertz then the blades of the turbine are likely to get damaged so as to prevent the stalling of the generator [1].Some frequency control reserves are continuously controlled so as to quickly respond to changes in the system known as primary and secondary frequency control schemes. Some others correspond to discrete actions taken by the system operator who can ask power producers to manually increase or decrease the production levels of some of their power plants called tertiary frequency control schemes. In the last couple of decades, there has been a huge trend in installing gas turbine (GT) based industrial power plants, especially with combined cycle with steam turbine (ST) throughout the world. One of the main reasons was the high overall efficiency. All major GT manufacturing companies, including General Electric, ABB-Alstom, Westinghouse Siemens and Mitsubishi offer CCGT plants of power range 680 MW, with very high efficiency claimed up to 62%. [2]. The other major concern is the unfavourable responses of existing coal based steam cycle thermal power plants resulting in unexpected grid behaviour after major disturbances. In many cases simple cycle gas turbine plants have been installed in the world for spinning reserve requirements, rather than base load requirements. The requirement of fast governor response with appropriate spinning reserve was also reason for installing CCGT plants with powerful gas turbines.Many researchers have focused on performance improvement of CCGT power plant utilizing the Brayton Cycle gas turbine and Rankine Cycle steam turbine with air and water as working fluids [3-5]. However, the possibility of using of CCGT for load frequency control has not been tested and reported.
2. The Case Study - CCPP on Frequency Control
In the present study, combined cycle Power Plant in Sri Lanka was studied to explore the possibility of using the GT for frequency control. Figure 1 below shows the layout of the Combine Cycle power Plant. It has been designed for a load from 60% to 100% in 2001 during construction. At present the CCPP operates with the following conditions: 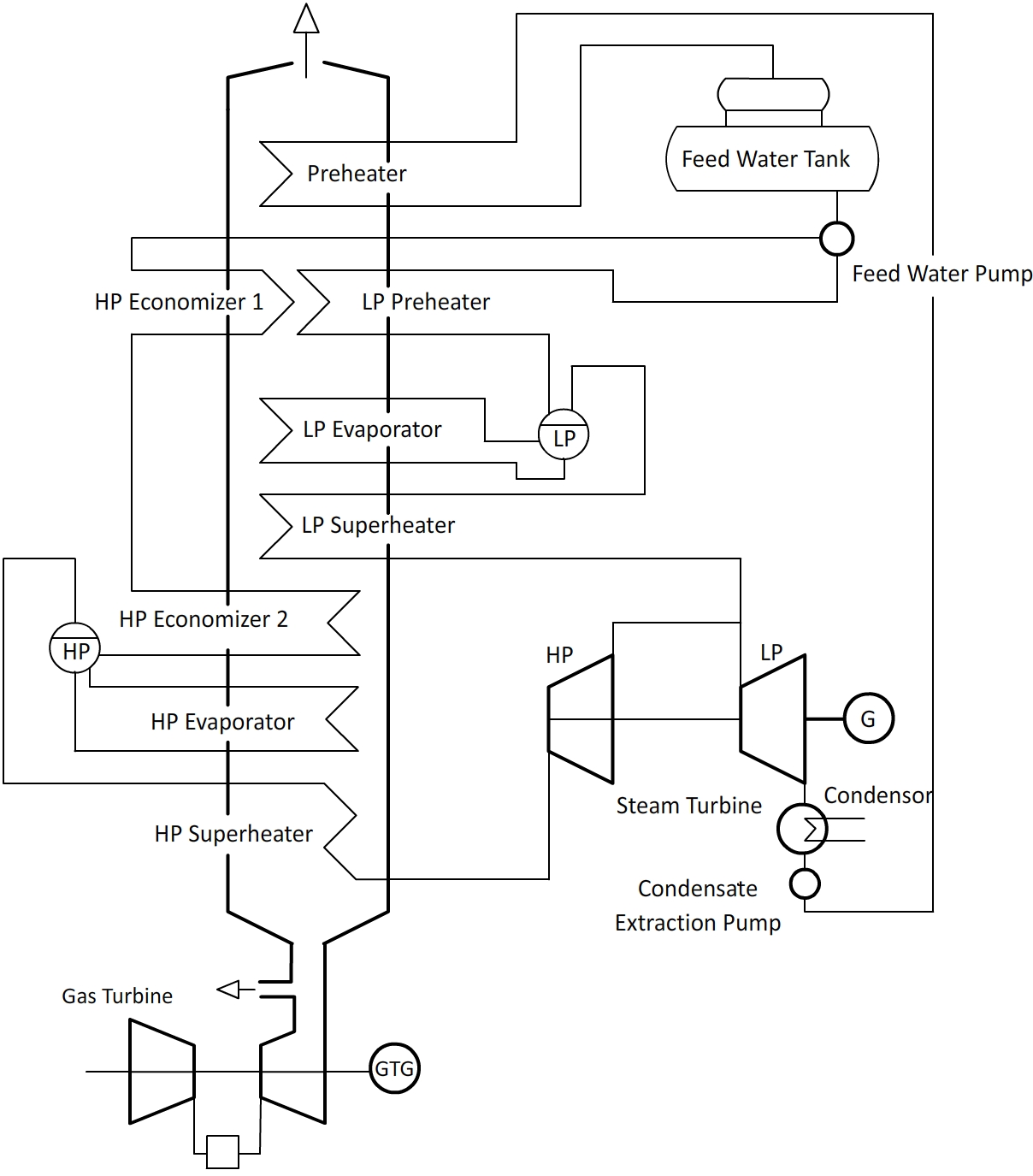 | Figure 1. Layout of Combine Cycle Power Plant |
Simple cycle (GT only) – Min. 40 MW to Based load Combined cycle (GT and ST) – Min. GT 100 MW to Based load Ramp rate - 25MW per MinuteAt present the combined cycle operates in the range 130 – 165 MW. The steam turbine has been decided to operate in the range 40 – 55 MW from the commissioning of the plant. When the combine cycle develops upper limit of 165 MW in which case GT develops 110 MW and ST develops 55 MW. When the GT is put into frequency control to balance the grid frequency, in response to decreasing load, the GT generation is expected to drop from 110 MW to lower values. This will have an impact on the Heat Recovery Steam Generator (HRSG), and then on the steam turbine. So it is necessary to determine the safe level of GT power output that will not seriously impact on the steam power cycle and its critical components. Therefore, it is very important to determine especially the lowest output of the GT when it is put into frequency control, as decreasing GT power output power impacts the HRSG. As such the objective of this study was to determine the safe generation level of the GT with frequency control mode.
3. Methodology
The CCPP was operated with GT power output of 60 MW with total power being 100 MW. Under this operational level, the critical parameters of the HRSG were measured and compared them with recommended values by the manufacturer. The following were the measured parameters for different HRSG components.Economizer: Mass flow rate of waterSuper Heater: Mass flow rate of steam and pressure dropBoiler drum: Wall temperature differenceThe economizer recommended mass flow rates at the design are 128 – 189 ton per hour and 30 – 41 ton per hour for high pressure side and low pressure side respectively. The pressure drop should be in the range 2 – 2.9 bar for high pressure side and more than 0.4 bar for the low pressure side. The maximum differential temperature between inner surface and middle wall of HP (High Pressure) drum is to be 30°C [6].Further, the parameters of HRSG were studied when the GT output is 40 MW. The GT variables (flue gas flow rate and the temperature) were obtained corresponding to the site variables from the GT performance characteristic provided at the design stage. With these input data HRSG variables were determined with the aid of HRSG simulation software.
4. Results
Comparison of measured variables and safe ranges for the economizer, super heater and the maximum wall temperature difference when the GT output was 62 – 64 MW, are presented in Table 1.Table 1. Comparison of measured and design values of variables of the HRSG 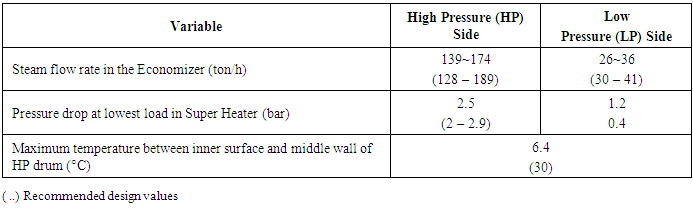 |
| |
|
According to the results for the condition that the Gas Turbine delivers nominal power output of 60 MW, the steam flow rate and the pressure drop at the lowest load were found to be within the safe range recommended by HRSG manufacturer. The maximum temperature difference across the wall of the high pressure drum was also very low, the value being 6.4°C as against maximum permissible value of 30°C.The variation of Gas Turbine exhaust gas temperature and the flow rate with the ambient temperature at 40 MW load is shown in Figure 2 below. According to gas turbine characteristics, the exhaust gas temperature and the mass flow rate at 65 F ambient temperatures are 745 F and 735 lb/s respectively. When these values are fed into the HRSG simulation software, the expected values of the critical parameters for the safe operation of the steam cycle were obtained as given in Table 2. 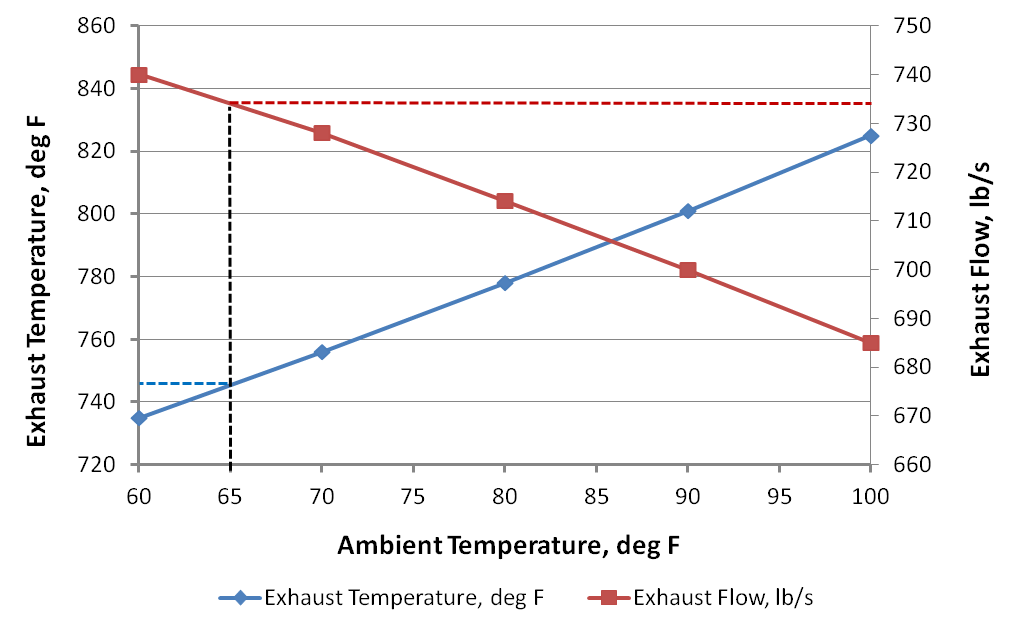 | Figure 2. GT exhaust flow rate and temperature |
Table 2. HRSG variables when GT develops 40 MW 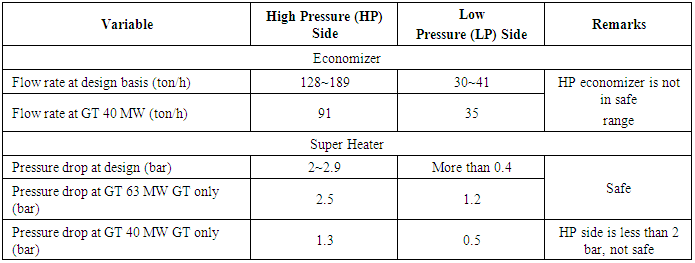 |
| |
|
According to the predicted values by the software, the steam flow rate in the economizer at 40 MW gas turbine power is 91 ton/h, whereas the permissible rang is on high pressure side being 128 – 189 ton/s. As far as the super heater is concerned, the predicted value for pressure drop in the high pressure side at 40 MW output is 1.3 bar, which is less than the safe design range of 2 to 2.9, therefore operating combined cycle with 40 MW gas turbine is not in the safe recommended range.Low pressure side superheater pressure drop at 63 MW is 1.2 bar and 0.5 bar at 40 MW which are higher than required minimum value of 0.4 bar. LP circuit is safe both occasions. However, High pressure side is not safe. Therefore, in overall operating the GT at 40 MW is not safe for the HRSG.
5. Conclusions
The frequency control operation from GT 60 MW to GT base load is acceptable because it is within the initial engineering value. For GT 40MW, that is minimum load for GT it is far expose to potential damage on HP economizer due to flow stagnation and HP super heater due to flow unbalance among tubes.The safe partial load is 100 MW (combined cycle mode) which is 60% of designed output of CCPP. Since operating the GT at 40MW was found to be not safe, the actual lowest point should be in between GT load of 40-60 MW.
ACKNOWLEDGEMENTS
The support extended by the staff of the Power Plant is greatly appreciated.
References
[1] | Md. Al-Amin Sarker and A K M Kamrul Hasan (2016). Load Frequency Control in Power System, SEU Journal of Science and Engineering, Vol. 10, No. 2, December 2016. |
[2] | Nikhil DEV, Rajesh Attri (2015). Performance analysis of combined cycle power plant, Front. Energy 2015, 9(4): 371–386. |
[3] | Al-Hazmy M.M., Najjar Y.S.H. (2004). Augmentation of gas turbine performance using air coolers, Applied Thermal Engineering, Vol 24, No. 2-3, pp 415-429. |
[4] | Nishada, K., Takagi, T., Kinoshita, S. (2005). Regenerative steam injection gas turbine system, Applied Energy, Vol 81, pp 231-246. |
[5] | Rahman, A., Al-Ibrahim, Abdulhadi, V. (2010). A review of inlet air cooling technologies for enhancing its performance of combustion turbines in Saudi Arabia, Applied Thermal Engineering, Vol 30, No. 14-15, pp 1879-1888. |
[6] | HRSG operation and maintenance manual, - HANJUNG- Doosan Heavy Industries Construction Co., Ltd. |