Traoré S.1, Traoré D. L.2, Kourouma S. Y.3, Magassouba S.4
1Polytechnic Institute, Department of Chemical Engineering, University of Conakry, UGANC, Conakry, Guinea
2Polytechnic Institute, Department of Civil Engineering, University of Conakry, UGANC, Conakry, Guinea
3Polytechnic Institute, Department of Mechanical Engineering, University of Conakry, UGANC, Conakry, Guinea
4Herbier National de Guinee, UGANC, Conakry, Guinea
Correspondence to: Traoré S., Polytechnic Institute, Department of Chemical Engineering, University of Conakry, UGANC, Conakry, Guinea.
Email: |  |
This work is licensed under the Creative Commons Attribution International License (CC BY).
http://creativecommons.org/licenses/by/4.0/

Abstract
Worldwide concerns over energy related climate change combined with spiraling cost of fossil fuels have increased interests in renewable energy alternatives. The unsustainable nature of petroleum, from the point of view of future availability and environmental impact, has spurred an interest in diversification of energy sources, with particular interest in renewable energy. Energy from biomass becomes target of immense interest in the world driven first of all to its renewability. Silicon (Si) is the dominant semiconductor material used in the fabrication of solar cells or modules. Due to its high Si content, rice husk (RH) has become a source for preparation of elementary Si. A low energy and cost effective production of Si is desirable and welcome by many industrial application. This research aims to produce silicon from RH by the use of microwave ashing and acid digestion. The goal is to contribute to a better understanding of the appropriate conditions to produce a cost effective and sustainable Si. RH samples were subjected to thermal treatment at 600°C to produce and investigate rice husk ash (RHA). Si from as received RH was extracted by following procedures: 1) microwaves ashing coupled with HNO3 treatment; 2) microwaves ashing coupled with HNO3+HF treatment; 3) melting digestion. Melting digestion was the most efficient method followed by Microwafe+HNO3+HF and Microwafe+HNO3.
Keywords:
Renewable energy, Rice husk, Silicon, Microwave, Acid
Cite this paper: Traoré S., Traoré D. L., Kourouma S. Y., Magassouba S., Preparation of Silicon from Rice Husk as Renewable Energy Resource by the Use of Microwave Ashing and Acid Digestion, International Journal of Energy Engineering, Vol. 8 No. 2, 2018, pp. 25-29. doi: 10.5923/j.ijee.20180802.01.
1. Introduction
1.1. Sustainability of Energy Requires Its Renewability
Demand for energy and associated services, to meet social and economic development and improve human welfare and health, is increasing. All societies require energy services to meet basic human needs and to serve productive processes. Since centuries, global use of fossil fuels (coal, oil and gas) has increased to dominate energy supply, leading to a rapid growth in carbon dioxide (CO2) emissions. The unmaintainable nature of fossil fuels as an energy source, from the point of view of future availability and environmental impact, has spurred an interest in diversification of energy sources, with particular interest in renewable energy. To be environmentally benign, energy services must be provided with low environmental impacts and low greenhouse gas emissions.Renewable energy sources reduce the threat of climate change but are not able to meet the energy consumption. A possible approach to this problem is the employment of so-called renewable energy [1]. Renewable energy is any form of energy from solar, geophysical or biological sources that is replenished by natural processes at a rate that equals or exceeds its rate of use. Renewable energy is obtained from the continuing or repetitive flows of energy occurring in the natural environment and includes resources such as biomass, solar energy, geothermal heat, hydropower, tide and waves, ocean thermal energy and wind energy. However, it is possible to utilize biomass at a greater rate than it can grow or to draw heat from a geothermal field at a faster rate than heat flows can replenish it. On the other hand, the rate of utilization of direct solar energy has no bearing on the rate at which it reaches the Earth. Fossil fuels (coal, oil, natural gas) do not fall under this definition, as they are not replenished within a time frame that is short relative to their rate of utilization. The solar energy industry is a player in the renewable energy segment, and the electricity generation from solar cells is considered to be one of the key technologies of the future. Although solar photovoltaic power generation is a proven technology, especially in the space industry, development of this technology to meet terrestrial energy demands has been limited. One of the issues that have limited the widespread use of solar photovoltaic power has been the high cost associated with the materials used in fabricating the solar cells.
1.2. Rice Husk a Biomass Providing Energy
The rice plant has high amorphous silica content because it naturally absorbs from the soil and transports silicon in the form of silicic acid to its outer surfaces. The silicic acid on reaching the outer surfaces of the rice plant becomes concentrated due to evaporation and is subsequently polymerized into silica cellulose membrane [2]. Because of this natural selectivity, the rice plant limits the uptake of heavy metallic elements that are found in large concentration in other cheap sources of silica such as quartz, bentonite and diatomaceous earth.As biomass, rice husk is agricultural by-products with 13 to 29wt% inorganic components and 71 to 87wt% organic components such as cellulose depending on the species, climate and geographic location of growth. The rice husk has no commercial value due to its hardness, fibrousness and abrasive nature, being an underused biomass resource. However, it is normally used because of its high caloric content (about 16 720 kJ/kg), as an alternative source of heat to generate hot gases for the drying of the cereal itself. This corresponds to 50% of the thermal capacity of a good quality bituminous coal and about 33% of the thermal capacity of the oil [3]. The inorganic components contain 87 to 97% SiO2 in hydrated amorphous form with small amounts of alkali and other trace elements. The main components in RH are lignin, cellulose, and hemicellulose, which are generally named lignocellulose [2]. There has been considerable interest in exploring readily available alternative starting materials for preparing semiconductor-grade silicon. Rice-husk appeared to be an attractive source material as it contains a huge SiO2 content and has low metal impurity one. The high content of silica in RH presents opportunities for the preparation of value-added silicon based materials. Since the 1970s, various silicon based materials, including silica, silicon carbide, silicon nitride, silicon tetrachloride, zeolite, and silicates, have been successfully synthesized using RH as the silicon source [4].
1.3. Silicon Availability and Reactivity
Approximately 75% of the accessible earth’s crust comprises silicon dioxide, SiO2 (Si: 26.3%; O2: 48.9%) [5]. It is the most abundant element in the earth’s crust after oxygen. Silicon is also by far the most important and popular semiconductor material since the emergence of solid-state electronics.Three major applications have since greatly stimulated the production and purification of silicon, that is, as an alloy in aluminium, silicones and solid-state electronics. Silicon carbide has also found a broad range of applications taking advantage of its hardness and chemical noble character. Bulk Silicon is usually produced for industrial applications by the carbothermic reduction of silicon dioxide in submerged-arc electric furnace. The process is energy intensive requiring temperatures greater than 2000°C, which are well above the melting point of silicon (1410°C) [6].Silicon of various grades, depending on its purity, can be prepared by several methods. Metallurgical grade silicon of ca. 98% purity has generally been prepared by carbothermal reduction of quartz (SiO2) in electric arc furnace at a high temperature of 1900°C [7] and thermal decomposition of leached rice hulls using metals such as Mg, Ca, Ba, and Al etc. as reducing agents [8].High purity polycrystalline silicon for solar cell and semiconductor device can be produced by further purification of Metallurgical grade silicon using Siemens process. The process involves carbothermic reduction of SiO2 (T > 2000°C) followed by chlorination, fractional distillation and pyrolysis of trichlorosilane SiHCl3. Today, quartz sand (SiO2) is converted into crystalline silicon on a megaton scale by reduction with carbon using an electric arc process (T ~2000°C). The process has considerable energy requirements (12,000 kWh/t silicon; technically realized energy efficiency: 84%) and significant volumes of CO2 are released. Since the major sustainability and security challenges we face arise primarily from energy use, biomass processing is taking a significant impact on energy production and utilization. As this process is energy-intensive, efforts have been made to develop alternative lower energy processes.In recent years the use of microwave technology in the field of analytical chemistry has grown in popularity. This growth has stemmed from the ability of microwave instrumentation to fulfill the needs of the analytical chemist. Recent advances in microwave technology have supplied the chemist with more simplistic methods of analysis and the ability to perform these analyses in a time frame which is conducive to plant operations. In short, microwave equipment has provided the chemist an efficient alternative to many standard analytical methods. Areas where microwave instrumentation has had the greatest impact include drying, acid digestions, and most recently dry ashing. The goal of this method is total sample decomposition and with judicious choice of acid combinations.The microwave heating method has been developed to synthesize silica and silicon compounds. This method is provided as a rapid multi-element, microwave assisted acid digestion prior to analysis protocol so that decisions can be made about the site or material. Digests and alternative procedures produced by the method are suitable for analysis by flame atomic absorption spectrometry (FLAA), cold vapor atomic absorption spectrometry (CVAA), graphite furnace atomic absorption spectrometry (GFAA), inductively coupled plasma atomic emission spectrometry (ICPAES), inductively coupled plasma mass spectrometry (ICP-MS) and other analytical elemental analysis techniques where applicable.The method has several additional alternative acid and reagent combinations; it has provisions for scaling up the sample size to a maximum of 1.0 g. The sample and acid are placed in suitably inert polymeric microwave vessels. Most samples will be totally dissolved by this method with judicious choice of the acid combinations. Hydrofluoric acid, which is capable of dissolving silicates, may require the removal of excess hydrofluoric acid or the use of specialized non-glass components during instrumental analysis. In microwave heating, energy is delivered to the materials via molecular-level interactions with the electromagnetic field. Microwave heating offers many advantages such as rapid, selective and volumetric heating, high reaction rates and dramatically reduced reaction times.Electricity generated from silicon can be considered as renewable only if the power utilized in silicon production is derived from renewable sources, with the silicon production process itself also needing to be carbon-neutral. It is left a subject to ascertain which carbon-neutral silicon technology might be best suited to large scale fuel silicon production. Auner and Holl [1] suggest a process based on reacting silica with hydrofluoric acid.
2. Material and Methods
RH was collected from several locations; an average sample was burned out at 600°C in a muffle furnace for 6 h to produce and investigate RHA SiO2 with SEM, XRD. The obtained RHA was characterized in terms microstructure by XRD (PHILIPS with Cu Kα radiation) and SEM (JEOL, JSM-5800 LV). Si from RHA was extracted by following ways and means: 1) Microwaves ashing coupled with HNO3 leaching: RH is weight into silica glass vessels and HNO3 (Merck, Germany) is added. The samples were put into a microwave-heated pressure digestion system (Ultra Clave II; MLS GmbH, Germany). They were digested and left to cool down to room temperature. Then the digests were transferred to 10-ml volumetric flasks and filled up to the mark with ultra-pure water [9].2) Microwaves ashing coupled with HNO3+HF leaching: RH is weight into silica glass vessels and HNO3 (Merck, Germany) is added. The samples were put into a microwave-heated pressure digestion system (Ultra Clave II; MLS GmbH, Germany). They were digested, after digestion 0,5 ml hydrofluoric acid was added and left to cool down to room temperature. Then the digests were transferred to 10-ml volumetric flasks and filled up to the mark with ultra-pure water.3) Melting digestion: RH was glowed for 3 hours at 450°C in platinum crucibles. A mixture of 0.2 g Di-Lithiumtetraborat and 0.8 g Lithiummetaborat is added. The blend were mixed with a plastic spatula and melted at 1100°C for about 30 minutes. The Melts were transferred in a beaker with HNO3 and heated up to the melt is completely solved. Then the sample is filled up to a volume of 250 ml with ultra-pure water. Si content was measured ICP-OES against an external calibration by means of Vista Pro, Varian, Australia equipped with a Scott type spray chamber, a Meinhard type nebulizer and operated at a plasma power of 1.1 kW.
3. Results and Discussion
The RHA sample after burning out at 700°C for 4 h presented a high amount of silica (Fig. 1). The relative contents of other elements increased in general with increase in temperature and time. The crystalline, amorphous or both silica forms depend on the burning temperature or the method used for ash production [10]. 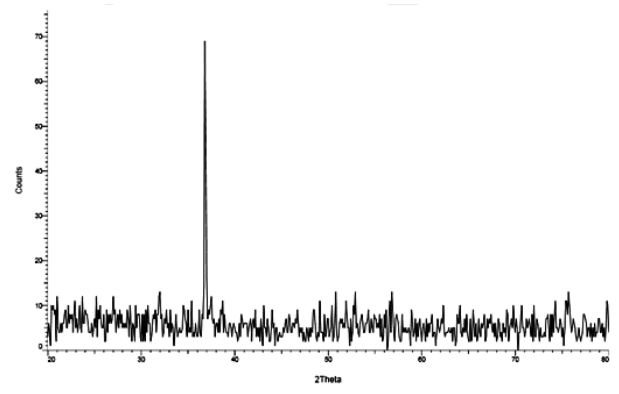 | Figure 1. X-ray diffraction pattern of silica produced from RHA |
When the burning temperature of RH is high, the silica contained in the ash is predominantly crystalline.Inorganic content of RHA has a high amount of silica (95.33%). The silica presented is not completely in the amorphous form since its diffractogram showed a sharp 2θ angle diffraction peak centered at 22, which indicates a crystalline structure. The major reflections or peaks of crystalline quartz occur at 2θ angles of 36.541°. It can be seen that no defined peaks corresponding to these 2θ angles are found in Figure. A rather broad peak spanning 2θ which is characteristic of amorphous structures is observed.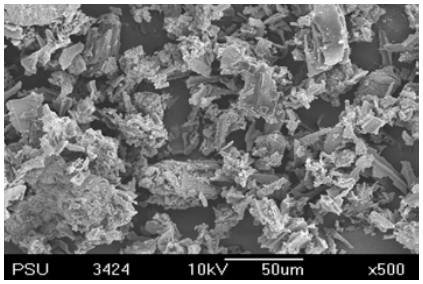 | Figure 2. SEM pattern of silica produced from RHA |
SEM shows a porous and multifaceted particle shape and size. The micrograph shows a porous and multifaceted particle shape and size. The amorphous hump after the thermal treatment shows that the RHA is composed mostly of amorphous silica, but still contains quartz as crystalline form of SiO2. The foremost constituents of rice husk comprise hydrated silica, cellulose and hemi cellulose component totaling a 55-60% and lignin component of approximately 22%. The porous and honeycomb morphology seen can be credited to the burning out of the organic component in the rice husk during combustion. The hydrated silica afterward polymerizes to form a skeletal silica network which may explain the flaky and honey comb-like structure. Table 1 shows the experimental results of Si extraction. They indicate that the most efficient method represents the melting digestion followed by microwave ashing with HNO3+HF leaching.Table 1. Silicon extracted from RH from different localities (mg/kg) 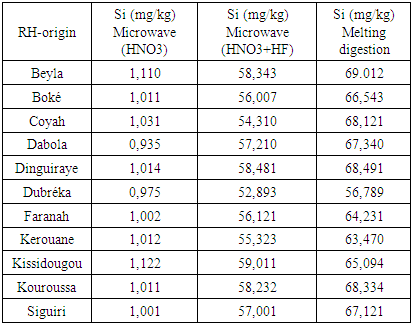 |
| |
|
The microwave ashing combined with HNO3 treatment seems to be the less efficient; the amount of Si extracted by this method does not exceed 1,2 mg/kg Si, independently of RH-origin. Nitric acid is a strong oxidant and tends to provide oxygen to Si extracted by the microwave heat treatment. In average the Si quantity obtained by microwave combined with HNO3 represents 1,80% and 0,532% of the same generated by the microwave ashing combined with HNO3+HF mixture and the melting digestion respectively. Melting digestion produces more silicon than the other two methods; but it requires much more energy.The HF contributes much in the extraction. It is well known that Si is thermodynamically unstable in air or water; it reacts spontaneously to form an oxide film. The oxide can be nonstoichiometric and hydrated to various degrees, though the simple empirical formula is silicon dioxide, SiO2. Silica is a key thermodynamic sink in the silicon system. SiO2 is an electrical insulator that forms passivating films on crystalline silicon; preparation of porous silicon thus requires an additive in the solution to dissolve the oxide and allow electrochemical oxidation to continue [11].The Si–F bond is the only bond stronger than Si–O, and it is the Si–F bond enthalpy that drives the main chemical dissolution reaction used to make porous silicon. In the presence of aqueous HF, SiO2 spontaneously dissolves as SiF62− as shows the equation:SiO2 + 6 HF → SiF2+6 + 2H+ + 2H2OThe reaction of SiO2 with HF is a habitual industrial reaction. It is used to make frosted glass from plate glass and to remove SiO2 masking layers in the processing of silicon wafers in microelectronics. The silicon hexafluoride ion (SiF2+6) is a stable dianion that is highly soluble in water. Thus fluoride is the most important additive used in the preparation of silicon, dissolving the insulating oxide that would otherwise shut down the electrochemical corrosion reaction.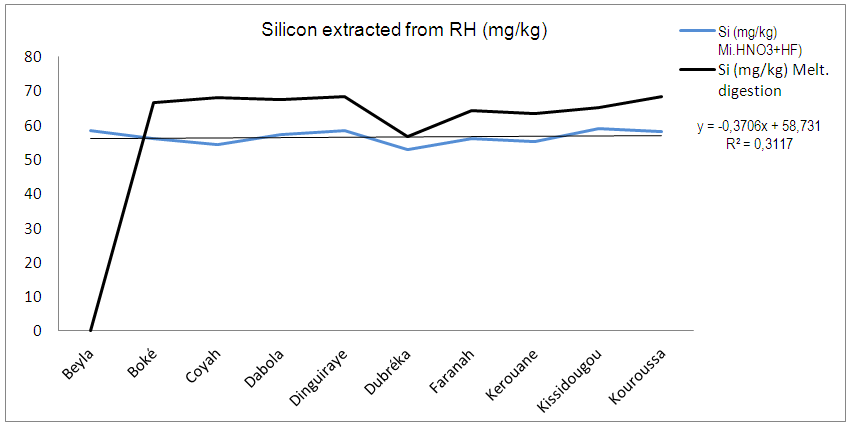 | Figure 3. Shows that the amount of Si extracted by microwave ashing coupled with HNO3+HF leaching and that obtained by the melting digestion are closed. The origin of RH has no influence on the Si extraction rate |
4. Conclusions
As carbon-based primary energy carriers become increasingly exhausted, the search for and development of alternative energy sources are of eminent importance. A possible approach to this problem is the employment of so-called renewable energy. Silicon compounds have found prospective application in a number of industrial fields but sustainable, cost-effective, and scalable synthesis of them from sustainable sources still remained challenging. Highly pure silicon and silicon compounds are required in high technology products such as semiconductors and solar cells. Si metal can be produced by several processes. Silicon extracting from RH becomes a crucial technology for its comprehensive utilization of waste. The microwave ashing assisted with mineral acid digestion is energy effective, it is a useful technique for rice husk valorization. Microwave ashing techniques significantly reduced the time required to ash a variety of sample types. Long and tedious preparation and handling steps used in standard practices can be eliminate.
References
[1] | Auner, N.; Holl, S. (2006): Silicon as energy carrier – facts and perspectives. Energy, v.31, p.1395-1402. |
[2] | Singh, R. and Dhindaw, B. K. (1978): "Production of High Purity Silicon for use in Solar Cells," in Sun, Mankind's Future Source of Energy: Proceedings of the International Solar Energy Congresspp. 776-781. |
[3] | Anwar, M., Miyagawa, T., Gaweesh, M. (2000): Using rice husk ash as a cement replacement material in concrete. Waste Management Series 1, 671-684. |
[4] | Sun, L. Y.; Gong, K. C. (2001): Silicon-based materials from rice husks and their applications. Industrial & Engineering Chemistry Research, 40 (25), 5861-5877. |
[5] | A.F. Hollemann, N. Wiberg (1995): Lehrbuch derAnorganischen Chemie, 101. Aufl., Berlin/New York: de Gruyter Verlag. |
[6] | Nagamori, M., Malinsky, I. & Claveau, A. (1986): Thermodynamics of the silicon-carbonoxygen system for the production of silicon carbide and metallic silicon. Metall. bTrans. B 17, 503-514. |
[7] | O’ Mara, C., Herring, B. and Hont, P. (1990): Handbook of semiconductor silicon technology. New Jersey: Publications Park Ridge. |
[8] | Banerjee, H.D., Sen, S. and Acharya, H.N. (1982): Investigation on the production of silicon from rice husks by the magnesium method. Mater. Sci. Eng. 52: 173-179. |
[9] | VDLUFA (2011): Handbuch der Landwirtschaftl. Versuchs-und Untersuchungsmethodik (Methodenbuch), Band VII Umweltanalytik. |
[10] | Shinohara, Y. and N. Kohyama, (2004): Quantitative analysis of tridymite and cristobalite crystallized in rice husk ash by heating, Industrial Health, 42, 277-285. |
[11] | Michael J. S. (2012): Porous Silicon in Practice: Preparation, Characterization and Applications, First Edition; Wiley-VCH Verlag GmbH & Co. KGaA. |