Baba Akaribo, Benjamin Afotey
Department of Chemical Engineering, Kwame Nkrumah University of Science and Technology, Kumasi, Ghana
Correspondence to: Benjamin Afotey, Department of Chemical Engineering, Kwame Nkrumah University of Science and Technology, Kumasi, Ghana.
Email: |  |
Copyright © 2017 Scientific & Academic Publishing. All Rights Reserved.
This work is licensed under the Creative Commons Attribution International License (CC BY).
http://creativecommons.org/licenses/by/4.0/

Abstract
The goal of this research was to identify a more efficient and environmentally friendlier octane-enhancing fuel additive as a substitute to Methylcyclopentadienyl Manganese Tricarbonyl (MMT). The current amount (18 mg/L) of MMT required to ensure that the final gasoline product meets acceptable octane rating poses health threats on combustion of the fuel. Different blends of selected aromatic octane-enhancing fuel additives (aniline, 2,4-dimethylaniline and N-methylaniline) with base gasoline were prepared. The prepared blends were subjected to Ghana Standards (GS)/American Society for Testing and Materials (ASTM) test methods that required the determination of Reid vapor pressure (RVP), distillation, aromatic content, benzene content, copper corrosion, washed gum content, oxidation stability, density and octane number using the Cooperative Fuel Research engine. The response values of the octane-enhancing fuel additives used were then compared with Methylcyclopentadienyl Manganese Tricarbonyl. Results from the tests showed that N-methylaniline produced the highest octane numbers of 90, 93.4, 96 compared with 89.5, 92.7, 95.3 for 2,4-dimethylaniline and 88.5, 91, 93.5 for aniline when 1%, 2%, and 3% volumes respectively of each booster were added to the base fuel, with all other parameters meeting the required standard. For the same base fuel, the octane rating for the final gasoline product when 18 mg/L MMT was added was 86.6, which is much lower than what N-methylaniline as gasoline additive produced.
Keywords:
Research Octane Number (RON), Octane-enhancing fuel additive, Methylcyclopentadienyl Manganese Tricarbonyl, Cooperative Fuel Research Engine, N-methylaniline
Cite this paper: Baba Akaribo, Benjamin Afotey, Comparative Analysis of Selected Octane Enhancing Fuel Additives as Substitute to Methylcyclopentadienyl Manganese Tricarbonyl (MMT), International Journal of Energy Engineering, Vol. 7 No. 3, 2017, pp. 65-73. doi: 10.5923/j.ijee.20170703.01.
1. Introduction
Octane enhancing fuel additives (octane boosters) are organic or organometallic compounds or mixtures that are added to gasoline with the sole objective of raising its octane number in order to improve upon the combustion characteristics of the fuel and engine performance of the automobile. The use of fuel additives to increase the octane number of gasoline is cost effective compared to improving octane number by changing gasoline chemistry through refinery operations. A typical blended gasoline contains over 200 distinct components [1]. A range of standard parameters are used to determine gasoline quality. The characteristics of gasoline as a fuel may be classified into three categories: 1) the operating characteristics, such as the octane number of the gasoline; 2) the robustness and chemical stability of the gasoline and 3) the chemical constituents of the gasoline. The performance features of gasoline are considerably influenced by the octane number, Reid vapor pressure, lead content, sulfur content, existent washed gum and stability [2-4].
1.1. Goal and Objectives
The overall goal of this research was to identify a more efficient and environmentally friendlier octane-enhancing fuel additive as a substitute to Methylcyclopentadienyl Manganese Tricarbonyl (MMT). The specific objectives were:(1) To measure properties of blends of three aromatic octane-enhancing fuel additives (aniline, 2,4-dimethylaniline and N-methylaniline) with base gasoline, using Ghana Standards (GS)/American Society for Testing and Materials (ASTM) test methods and the Cooperative Fuel Research engine.(2) To compare the properties of the aromatic/gasoline blends with those of MMT/gasoline blends.The work presented here represents the first testing of aniline, 2,4-dimethyleaniline and N-methylaniline as additives to Ghana base fuel, and first comparison using Ghana standards.
1.2. Methylcyclopentadienyl Manganese Tricarbonyl (MMT)
MMT is one of the least costly but appreciably effective octane-improving additives after lead. The acceptable amount of MMT normally used in gasoline in Ghana is 18 mg/l. This amount produces between a 1.0 – 2.0 increase in octane number of gasoline [5]. MMT, a liquid in concentrated form, is freely soluble in gasoline but insoluble in water. MMT is extremely poisonous and harmful if inhaled, ingested, or contacted with the skin. Manganese, a silver-colored metal, constitutes approximately 25% of the molecular weight of MMT. Though prolonged exposure to manganese over a lifetime could lead to irreparable neurotoxic impairment, neurobehavioral effects can also be experienced even at relatively low doses. Manganese can enhance motor dysfunction in adults suffering from pre-Parkinson’s syndrome. People with iron deficiency disorders have shown higher levels of manganese in their blood, which may be an indication of how manganese and iron ions move across the blood-brain barrier. [6, 7]. Manganese is part of a balanced diet in food. However, inhalation is potentially a more dangerous route of exposure than ingestion. When taken orally, manganese passes through the digestive system, where the liver is able to regulate the concentration entering the bloodstream. When manganese is inhaled into the lungs, however, it bypasses the liver and can enter the bloodstream directly, where it travels unfiltered to the brain and can potentially accumulate to toxic levels. The progressive neurological damage manganese produces in workers is called “Manganism”. As symptoms of Manganism progress, the chance of recovery diminishes. Given the state of the science, there is as yet no known successful treatment or cure for “Manganism” [7-9]. Occupational studies have also shown impacts of manganese in the pulmonary and reproductive systems. An increasing number of voluntary and regulatory bans on MMT have restricted its use in the developed world and many countries in the developing world. A ban has been in place in the U.S. State of California since 1976. A separate regulatory limit restricts manganese to no greater than 8.3mg/l in the remainder of the nation’s fuel. Countries where a ban of MMT is in place are Brazil, the Czech Republic and Germany. The European Parliament is moving to place limits on manganese as strict as New Zealand’s standard of 2 mg/L. As of 2007, a voluntary boycott by fuel suppliers restricted MMT to less than 1 percent of the supply in the United States. Similar boycotts are in place in other countries and regions including Canada, the European Union, and India. MMT is being used in China, but strict government controls came into force in Beijing in January 2008 that limits the concentration to 6 mg/l. In South Africa the majority of fuel sold does not contain MMT. This trend shows that actions to restrict MMT use are increasing in number, not only in developed nations but also in developing nations [7].
1.3. Aromatic Compounds as Octane Enhancing Additives
Aromatics, in general, are source of fuels with high energy density and have high octane ratings; hence, they are able to achieve targeted values of octane quality. Because aromatic compounds have octane ratings greater than 100, water and carbon (IV) oxide are produced after complete combustion. As a result, the emissions control systems, including the catalyst and oxygen sensors, of the vehicle are not affected. Yet, the formation of engine deposits with respect to the combustion chamber has been characterized by heavy aromatic compounds. However, reduced levels of such compounds generally lead to minimal amounts of carcinogenic benzene found in exhaust emissions from spark ignition engines [10].Aromatic amines in particular have been noted in several applications as compounds with the ability of enhancing the octane number of gasoline. Remarkably, hydrocarbon mixtures containing even low volumes of 2,4-dimethylaniline and/or N-Nitrosodiphenylamine have octane numbers higher than the corresponding base gasoline. Consequently, addition of a large quantity of aromatic amines resulted in a large increase in the Research Octane Number (RON) value according to Alessandra Berra et al, 2014. Moreover, 2,4-dialkyl aniline and N-Nitrosodiphenylamine have been reported not to cause any damage to the anti-emission devices of recent internal combustion engines. [11].
1.4. Comparism of Health, Engine and Emissions Impact of the Aromatic Amines and MMT
The aromatic amines have been reported to result in an increase in nitrogen oxide emissions while MMT lowers the nitrogen oxides emissions. [14]. Also the aromatic amines may cause engine corrosion at higher percentages while MMT cause plug valve fouling and catalyst plugging even at lower concentrations and raise the cost of vehicle maintenance. [8].Further, aniline is known to be carcinogenic, while 2, 4 dimethylaniline and N-methylaniline are not but MMT is known to cause brain damage upon inhalation. [12, 13, 15].Tables 1 & 2 compare the health, engine and emissions impact of alternative octane boosters.Table 1. Health Effects of Selected Aromatic Fuel Additives Compared to MMT 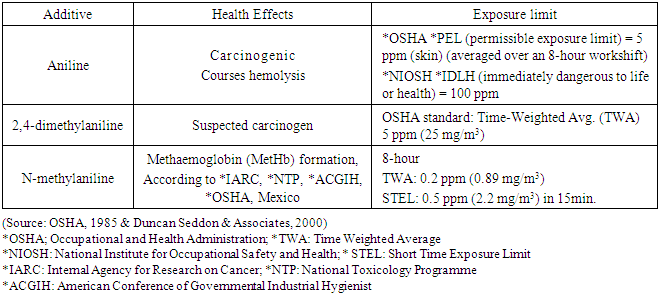 |
| |
|
Table 2. Engine and Emissions Impact of Aromatic Fuel Additives Compared to MMT 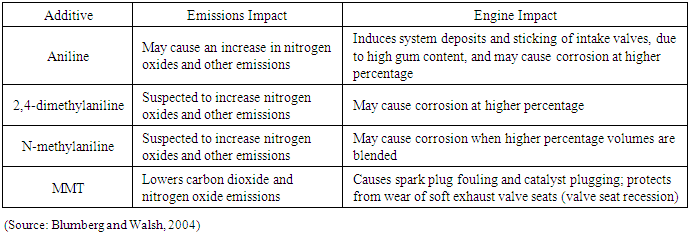 |
| |
|
2. Methodology
2.1. Introduction
The quality of gasoline is generally well-defined by government regulators and state organizations with specific minimum standards and appropriate test methods are used to analyze gasoline properties. The minimum standards are occasionally modified to suit the demand as well as environmental and health concerns. In the U.S, the American Society for Testing and Materials (ASTM) specifies minimum quality standards of gasoline, whereas in Ghana, the Ghana Standard Authority, a member of African Organization for Standardization (ARSO), International Organization for standardization (ISO) and an affiliate member of International electrochemical commission (IEC), is the constitutional organization mandated for development and declaration of Ghana Standards (GS). The organization responsible for reviewing Ghana Standards is the Committee on Petroleum and Petroleum Products. The Ghana Standard Authority specifies the minimum quality requirement, sampling and test method for gasoline.
2.2. Cooperative Fuel Research Engine
The Cooperative Fuel Research engine (CFR) was used as the main study equipment for octane number determination. The equipment is shown in Figure 1. Its test method, ASTM D2699, is designed for laboratory controlled experimental determination of research octane number of automotive engine fuel, including fuel that contains up to 25% v/v of ethanol. The equipment consists of a research octane number determination unit, a box-type crankcase with flywheel connected by V-belts to power electrical motor, an adjustable compression ratio of 4:1 to 18:1, a valve mechanism to provide constant valve clearance as compression ratio changes, a piston, a fuel system consisting of a carburetor of single vertical jet and fuel flow control to permit adjustment of air-fuel ratio, and an ignition which electronically triggers condenser discharge through coil to spark plug [16].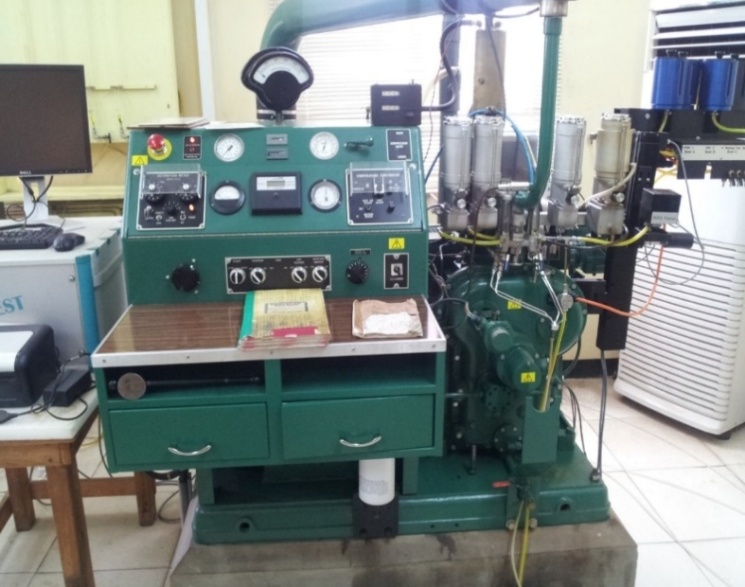 | Figure 1. Cooperative Fuel Research (CFR) Engine |
Other equipment such as the distillation unit, automated vapor pressure tester, seta copper/ silver corrosion bath unit, seta auto-oxidation control unit, air & steam jet tester, gas chromatography unit, hydrometer with a thermometer were used to determine distillation, Reid vapor pressure, corrosion, oxidative stability, washed gum content, aromatic & benzene content and density respectively. Calibration of all equipment was conducted before data collection as required by protocol.
2.3. Sample Preparation
2-liter samples were prepared containing an aromatic fuel additive, with the balance base fuel RON 85.6: 3 with aniline, 3 with 2,4 dimethylaniline, and 3 with N-methylaniline (in percent of 1%, 2%, and 3% by volume).The samples were kept in a refrigerator for about 15 minutes prior to the analysis, to prevent loss of lighter hydrocarbons during the analysis. A sample of base fuel of RON 85.6 containing about 18 mg/L of MMT was also prepared in a brown glass bottle, labeled and kept in a refrigerator for about 15 minutes prior to the analysis.
2.4. Product Analysis
2.4.1. Research Octane Number Determination
The research octane number of the blended fuel was determined with the CFR engine operating under standard conditions and comparing the detonation characteristics of the blended fuel to those of primary reference fuel blend of a known octane number. The CFR engine was calibrated using a reference guide table before being used. The sample was run by adjusting the compression ratio and air-fuel ratio in order to establish a midway reading on the knock meter to produce standard knock intensity. The fuel to air ratio for maximum knock intensity could be achieved either by 1) creating incremental step modifications within the mixture strength and checking the equilibrium knock intensity guide table value for every step, until the maximum knock intensity is achieved or 2) selecting the extreme knock intensity as the strength of the mixture is altered from either fuel rich-to-fuel lean or fuel lean-to-fuel rich at a constant rate.By using the reference guide table, the appropriate reference fuel(s) was determined such that either the same pressure was read on the knock meter as the sample or a bracketing pressure was produced. If the same pressure was read on the knock meter, then the octane number of the primary reference fuel blend that matched the knock intensity of the sample fuel established the research octane number of the fuel under determination. If the bracketing pressure was obtained, the sample fuel pressure value was interpolated within the bracketing reference fuels and equation (1) was used to obtain the research octane number of the sample under determination [2]. | (1) |
Where:ONS = octane number of the sample fuelON.LRF = octane number of the low PRFONHRF = octane number of the high PRFKIS = knock intensity of the sample fuelKILRF = knock intensity of the low PRF, andKIHRF = knock intensity of the high PRFLRF = Lower reference FuelHRF = Higher reference fuelPRF = Primary reference fuel
2.4.2. Reid Vapor Pressure of Petroleum Products Determination
3 ml of the refrigerated, air-saturated test specimen was injected into a thermostatically controlled, evacuated test chamber (Stanhope-Seta of model number 81000-2U). The test chamber has a moveable piston that expands the volume after sample introduction. The total volume of test sample injected was about five times less than the internal chamber volume. The test specimen attained thermal equilibrium at the test temperature, 37.8°C (100°F) in the chamber. The pressure transducer sensor and indicator measured the increase in pressure brought by the test specimen within the chamber. The technique measured only the total pressure, which is the sum of the partial pressure of the sample and the partial pressure of the dissolved air.The measured total vapor pressure was converted to a dry vapor pressure equivalent (DVPE) [16].
2.4.3. Distillation of Petroleum Products Determination
Depending on the composition of the fuel, the vapor pressure of the anticipated initial boiling point or anticipated end boiling point, or a combination of both, was used to categorize the sample into one of four groups. The arrangement of the instrument, the temperature of the condenser, and the remaining operating variables were defined in accordance with the group into which the test specimen is placed as shown in Table 3.Table 3. Group Characterization of Test Sample 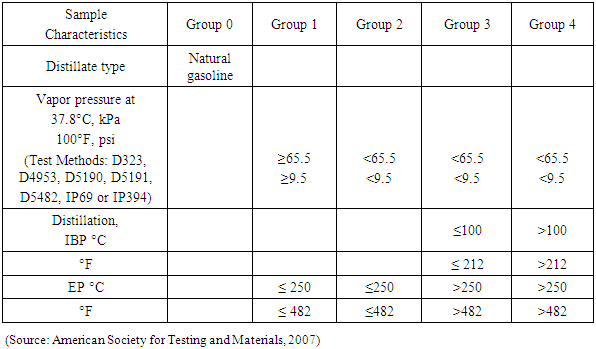 |
| |
|
100 ml of each sample was distilled within the recommended conditions. Distillations were executed using laboratory distillation equipment (Stanhope-Seta, model number 11860-3 U) at ambient pressure and under conditions that are considered to deliver in the region of one theoretical plate fractionation. Temperature readings and condensation volumes during the distillation process were systematically observed and recorded. The amount of residue and loss were also determined. Test results were then reported as percent evaporated or recovered against corresponding temperature in a table [16, 17].
2.4.4. Aromatics and Benzene of Petroleum Product Determination by Capillary Gas Chromatography
A test specimen from each sample (1 microliter) was injected into a gas chromatograph (Agilent 6890 N) equipped with a flame ionization detector and methyl silicone joined segment bonded silica capillary column. The initial and final temperatures of the column was 35oC and 200oC respectively. Eluting peaks were identified by relating their retention index to a table of retention indices and by visual matching with a standard chromatogram to identify each component. However, this method does not provide absolute identification. The table of retention indices was established by running reference compounds under identical conditions. The mass concentration of each component was determined by area normalization with response factors [16].
2.4.5. Copper Corrosion of Petroleum Product Determination
The copper corrosion test was used to determine the effect of the gasoline product on copper metal. Initially a copper strip was prepared by placing 00 grade silicon carbide paper on a flat surface and moistened with wash solvent (isooctane). The copper strip was rubbed against the silicon carbide paper in a circular motion.In the final step, a moistened cotton wool with 105 mm (150 meshes) silicon carbide grains was used to polish the strip. All metal dust was cleaned from the strip by rubbing vigorously against a clean pad of absorbent cotton until a fresh pad remains unsoiled.The prepared polished copper strip was immediately immersed in 30 ml of the test specimen and heated at 40°C for 3 hours. The copper strip was removed, washed, and compared with the ASTM Copper Strip Corrosion Standards of 1a, 1b 2a, 2b, 3c with 1a showing the least corrosion effect and 3c the maximum corrosion effect [16].
2.4.6. Determination of Washed Gum Content
Four beakers and a tare (control) were thoroughly washed with equal volumes of toluene-acetone mixture (gum solvent), rinsed with water and immersed in a mildly alkaline detergent cleaning solution for 6 hours. The glassware was removed by means of stainless steel forceps, dried in an oven at stable temperature of 150°C for an hour and transferred into a cooling vessel for about 2 hours to attain room temperature. The four beakers and the tare were weighed to the nearest 0.1 mg. Each of the first three beakers was then filled with 50 ml of the blended samples containing 0%, 1%, 2%, and 3% by volume of N-methylaniline and the remaining beaker with base fuel. The beakers and tare were then transferred into the evaporation bath and each conical jet was placed in each beaker. The samples were heated and allowed to evaporate under controlled conditions for 30 minutes. The beakers were transferred to a cooling vessel for about 2 hours to cool to room temperature. The unwashed gum was extracted with 25 ml of heptane. The extraction process was repeated to obtain the washed gum.The beakers were dried in the evaporating bath at 163°C for 5 min and cooled in the cooling vessel for 2 hours. The beakers and the tare were weighed and recorded. The tests were repeated and the average results reported in mg/100 ml as the washed gum content.The solvent washed gum content of the blended fuels were calculated using the following equation: | (2) |
WhereS = solvent washed gum content, mg/100 mL, C = mass recorded for the sample beaker plus residue in grams (g),D = mass recorded for the empty sample beaker, g, X = mass recorded for the tare beaker before analysis, g, Z = mass recorded for the tare beaker after analysis [2] Similar tests were run for aniline and 2,4-dimethylaniline fuel additives.
2.4.7. Oxidation Stability (Induction Period) of Petroleum Products Determination
The test specimen was oxidized in a pressure vessel which was first filled to 15 at 25°C with oxygen at a pressure between 690 to 705 KPa and heated to a temperature of 98 to 102°C. The pressure was recorded at specified intervals until the breakpoint was attained. The breakpoint being the point in the pressure-time curve that is preceded by a pressure drop of exactly 14kPa within 15 minutes and succeeded by a drop of not less than 14kPa in 15 minutes. The period used for the test specimen to attain the breakpoint was the observed induction period at the temperature of the test, from which the induction period at 100°C can be calculated [16].
2.4.8. Density of Petroleum Product Determination Using Hydrometer
A test portion of the sample was transferred into a hydrometer cylinder at room temperature. The appropriate hydrometer at room temperature was lowered into the test portion, displaced and allowed to stabilize. The meniscus of the test sample on hydrometer scale and the temperature were read simultaneously as the observed density and temperature.The test was repeated and the average observed hydrometer reading was reduced to the reference temperature by means of petroleum measurement tables [16].
3. Results and Discussion
Tables 4, 5 & 6 show test results of aniline, 2,4-dimethylaniline, N-methylaniline additives and methylcyclopentadienyl manganese tricarbonyl (MMT) along with acceptable gasoline standards established by the Ghana Standard Authority. 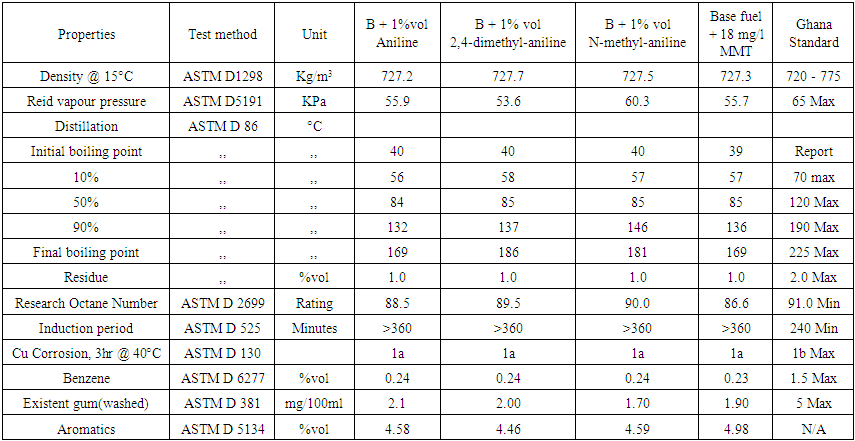 | Table 4. Results of 1% volumes each of aniline, 2,4-dimethylaniline, N-methylaniline with 99% volume of RON 85.6 base fuel and 18 mg/l of MMT with base fuel |
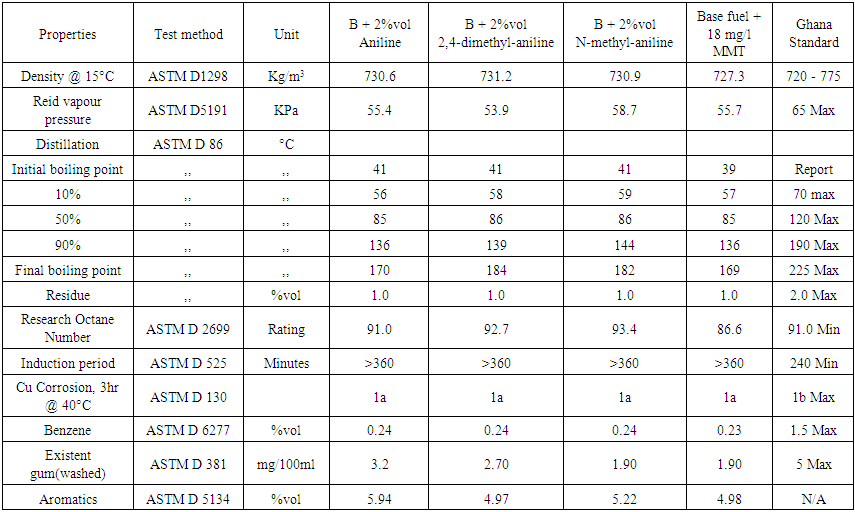 | Table 5. Results of 2% volumes each of aniline, 2,4-dimethylaniline, N-methylaniline with 98% volume of RON 85.6 base fuel and 18 mg/l of MMT with base fuel |
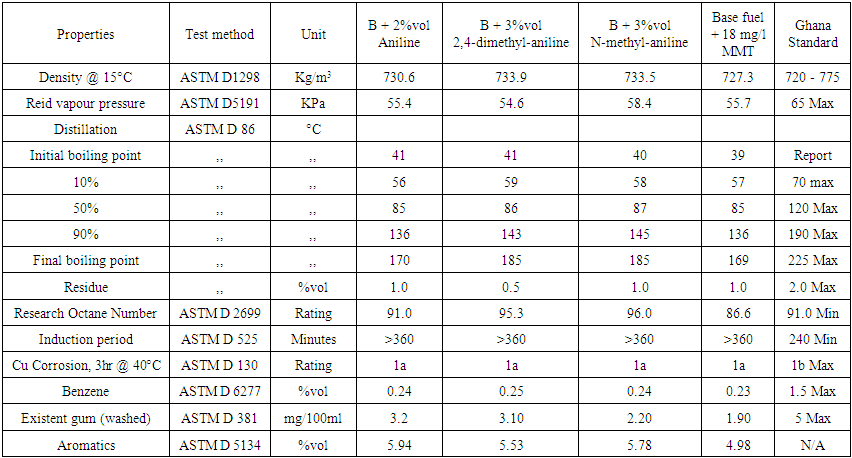 | Table 6. Results of 3% volumes each of aniline, 2,4-dimethylaniline, N-methylaniline with 97% volume of RON 85.6 base petrol and 18mg/l of MMT with base fuel |
Based on the results from the laboratory experiments and Figure 2, a 3% volume of N-mehtylaniline added to the base fuel of 85.6 research octane number yielded a research octane number of 96.0, while 95.3 and 93.5 were obtained from 2,4 –dimethylaniline and aniline, respectively. This shows that a research octane number gain of 10.4 was obtained by adding 3% volume of N-methylaniline, which is higher than the 9.7 and 7.9 gain by adding the same 3% volume of 2,4-methylaniline and aniline, respectively, to the base fuel.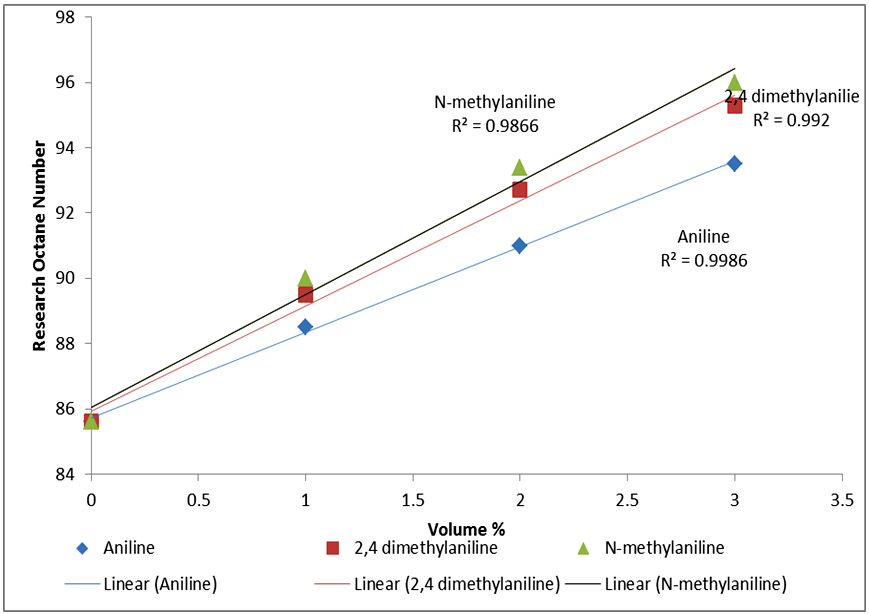 | Figure 2. Comparison of RON responses of blended base fuel with selected aromatic amines in different volume% |
Similarly, 2% volume of each of the additives added to the base fuel of 85.6 research octane number produced gasoline with research octane numbers of 91.0, 92.7 and 93.4 for aniline, 2,4 dimethylaniline and N-methylaniline, respectively, which satisfied the minimum Ghana standard requirement of 91.0 research octane number of gasoline sold as super grade. Finally, a 1% volume addition each of aniline, 2,4-dimethylaniline and N-methylaniline resulted in 88.5, 89.5, 90.0 research octane number of the final gasoline products, respectively, which do not meet the standard.These results showed that N-methylaniline in RON 85.6 base fuel produced the highest research octane number for all the percent volumes of additives used, with all other parameters meeting the required standards. For N-methylaniline, the 3% volume sample produced the highest research octane number of 96.0, exceeding the minimum Ghana standard requirement for V- Power or Effimax of grade 95.0 research octane number. Further, cost analysis conducted showed that it cost 144GH¢ to produce 7.9 research octane number gain over and above the base fuel octane number when 3% of aniline is used as octane booster. Similarly, it cost 174GH¢ to produce 10.4 research octane number gain over and above the base fuel octane number when 3% of N- methylaniline is used as octane booster and 9.7 for 178.5GH¢ when 2,4 methylaniline is used for the same volume percent. The cost in Ghana cedi per unit gain in octane number, however, was evaluated as 18.6 for aniline additive, 16.7 for N-methylaniline and 18.4 for 2,4 methylaniline. This makes N-methylaniline more cost effective compared with the other fuel additives. Also, considering the fact that N-methylaniline could cause headaches and dizziness upon exposure, compared with the other aromatic fuel additives which are carcinogenic and MMT which causes neurological brain damage, makes it a better choice as fuel additive.Finally, figure 3 shows that, addition of 3% volume of aniline to the base fuel produced a significant increase in washed gum content of base fuel from 1.4 to 4.6 mg/100ml, which is so close to the Ghana standard limit of 5mg/100ml. While addition of 3% volume of N- methylaniline and 2, 4 dimethylaniline to the base fuel increased the washed gum content from 1.4 to 2.20mg/100ml and 1.4 to 3.10mg/100ml respectively. Hence, the amount of washed gum produced when N-methylaniline is used is 0.8mg/100ml compared to 3.2mg/100ml and 1.7mg/100ml for aniline and 2,4 dimethylaniline respectively. This, therefore, makes N-methylaniline a better fuel additive since the amount of solids produced that could impact engine efficiency is lower compared to the case with aniline and 2,4 dimethylaniline. 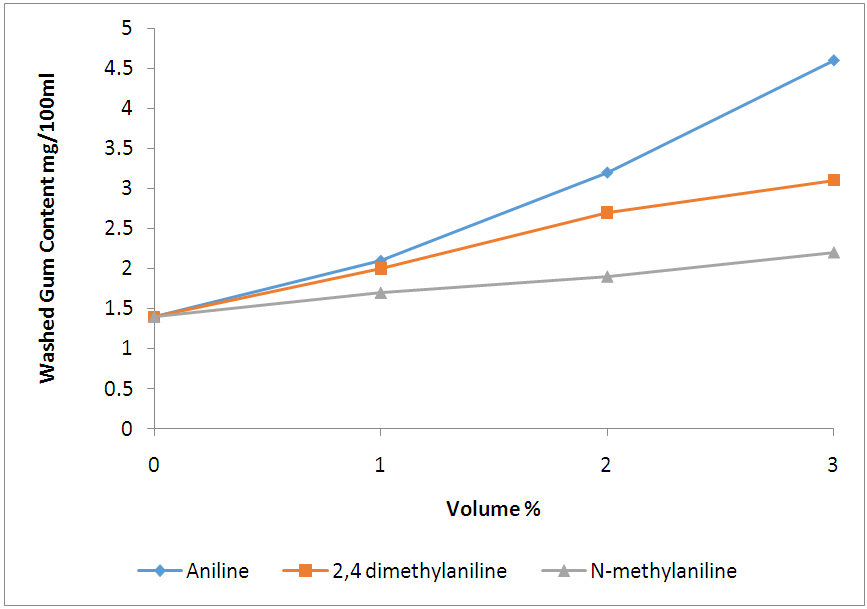 | Figure 3. Comparison of washed gum content of blended base fuel with selected aromatic amines in different volume% |
4. Conclusions and Recommendations
Research octane numbers for gasoline products with four different fuel additives were determined using a Cooperative Research Fuel engine. The final values obtained using the additives indicate that the 3% vol of N-methylaniline is the best additive since it provided the highest octane number at the lowest cost. It is recommended that future work should include detailed economic analysis that can highlight additional advantages of one additive over the others. Further, future work on N-methylaniline should provide a more detailed health impact assessment. Finally, alternative ways to boost octane number of gasoline should be examined in future work. For instance, investments to improve upon refinery operations can boost the octane number of fuel without the need for metallic additives and high octane blending components. Pre-blended fuels that do not contain MMT or other metallic additives can be considered if technological changes in refinery operations are too costly.
ACKNOWLEDGMENTS
The authors will like to acknowledge Emmanuel Darko for information support, Godwin Niikoi Amon for his assistance with data collection, and Augustus Wiredu for assistance with equipment maintenance for data collection.
References
[1] | Domask W.G (1984). Introduction to petroleum hydrocarbons: Chemistry and composition in relation to petroleum-derived fuels and solvent. a.d.v.nod.environ.tox.8; pp 1-26. |
[2] | Reese E. and Renate D. Kimbrough, (1993). Acute Toxicity of Gasoline and Some Additives Environmental Health Perspectives Supplements 101: 115-13. |
[3] | Rigby, B., Lasdon, L. S., & Waren, (1995). The evolution of Texaco’s blending systems: from OMEGA to StarBlend. Interfaces 25:5: 64–83. |
[4] | Matijošius J. and Sokolovskij E., (2009). Research into the Quality of Fuels and their Biocomponents Transport 24:.3: 212–217. |
[5] | Hammerle, R. H., et al. (1992). Effect of mileage accumulation on particulate emissions from vehicles using gasoline with methylcyclopentadienyl manganese tricarbonyl. SAE Technical Paper Series 920731. HDSB. (2007). |
[6] | Duncan Seddon & Associates, (2000). Octane Enhancing Petrol Additives/Products: Literature Review and Analysis pp 54-58. |
[7] | Ray J. Minjares and Michael Walsh, (2009) Methylcyclopentadienyl Manganese Tricarbonyl (MMT): A Science and Policy Review, pp12-17. |
[8] | Blumberg, Katherine and Walsh, P. Michael (2004) Status Report Concerning the Use of MMT in Gasoline- International Council on Clean Transportation, pp 2-12. |
[9] | Ardeleanu, A., Loranger, S., Kennedy, G., L'Espérance, G., & Zayed, J. (1999). Emission rates and physico-chemical characteristics of Mn particles emitted by vehicles using Methylcyclopentadienyl Manganese Tricarbonyl (MMT) as an octane improver. Water, Air, & Soil Pollution, Vol. 115(1), pp411-427. |
[10] | Carlos R. Kaiser, Joana L. Borges, Anderson R. dos Santos, Débora A. Azevedo, and Luiz A. D’avila, (2010), Quality control of gasoline by 1H NMR: Aromatics, olefins, paraffinic, oxygenated and benzene content Fuel, 89: 99–104. |
[11] | IARC (1989). IARC Monographs on the Evaluation of Carcinogenic Risks to Humans: Diesel and Gasoline Engine Exhausts and Some Nitroarenes, Volume 46, pp 424. |
[12] | SCOEL, the Scientific Committee of Occupational Exposure Limits (2010) Recommendation from the Scientific Committee on Occupational Exposure Limits for aniline. SCOEL/SUM/153. The European Commission, Employment Social Affairs and Inclusion. Pp 12-16. |
[13] | SCOEL, the Scientific Committee of Occupational Exposure Limits (2012) Recommendation from the Scientific Committee on Occupational Exposure Limits for N-mehtylaniline. SCOEL/SUM/178. The European Commission, Employment Social Affairs and Inclusion. Pp 3-9. |
[14] | Tjälve H., Henriksson J., Tallkvist J., Larsson B. S., and Lindquist N. G., (1996) Uptake of manganese and cadmium from the nasal mucosa into the central nervous system via the olfactory pathways in rats. Pharmacology & Toxicology 79:347-356. |
[15] | Yokel, R. A., and J. S. Crossgrove. (2004) Manganese toxicokinetics at the blood-brain barrier. Health Effects Institute Research Report Number 119. pp 7-8. |
[16] | Annual book of ASTM Standards, 1989 American Society for Testing and Materials, Petroleum products, lubricants, and fossil fuels. Vol 1-14. |
[17] | American Society for Testing and Materials (ASTM). 2007. "Standard Test Method for Distillation of Petroleum Products at Atmospheric Pressure," ASTM Standard D 86 - 07b, pp.6. |