Riyadi, Siska Titik Dwiyati, Ahmad Kholil, Abdi Ilahi
Department of Mechanical Engineering Education, Faculty of Engineering, Universitas Negeri Jakarta, Jalan Rawamangun Muka Jakarta Timur, Indonesia
Correspondence to: Riyadi, Department of Mechanical Engineering Education, Faculty of Engineering, Universitas Negeri Jakarta, Jalan Rawamangun Muka Jakarta Timur, Indonesia.
Email: |  |
Copyright © 2016 Scientific & Academic Publishing. All Rights Reserved.
This work is licensed under the Creative Commons Attribution International License (CC BY).
http://creativecommons.org/licenses/by/4.0/

Abstract
The use of fuel oil and gas by the public society might be replaced by the energy from waste materials. The waste materials such plastic, water hyacinth, coconut shell, and bagasse can be diverted into briquette. This study was aimed to find the most optimum material to be used in producing the briquette. The method in this study was experimental. The plastic materials used in this research was HDPE. This material then was mixed with other environmental wastes such as water hyacinth, coconut shell, and bagasse in charcoal powder mixed with a certain composition and molded into briquettes. The composition is 80-20%, 60-40%, 40-60%, and 20-80% for each mixture of HDPE material with every environmental waste. The parameters used in this study was based on ministerial regulation No. EMR 047 of 2006 on guidelines for the manufacture and utilization of coal and coal-based solid fuel. Several tests were conducted to measure the moisture content, ash content, volatile matter content, bound carbon, calorific value, and total sulfur. The experiment used ASTM-D method. As well as additional testing ignition properties of briquettes such as testing startup, the old flame, and the rate of burning briquettes. The test results show that the whole mixture of briquettes was able to meet the standards that have been set on the main parameters based on regulation of Energy Minister No.047 in 2006 on guidelines for the manufacture and utilization of coal and coal-based solid fuel. The optimum mix briquettes were made of 20% bagasse and 80% plastics (AT20PL80) produced based on the calorific value of 9055 Kcal/Kg and starting flame time for about 71 seconds.
Keywords:
Briquettes, HDPE, Hyacinth, Coconut shell, Bagasse
Cite this paper: Riyadi, Siska Titik Dwiyati, Ahmad Kholil, Abdi Ilahi, Charcoal Briquettes Characteristics of HDPE Mixed with Water Hyacinth, Coconut Shell, and Bagasse, International Journal of Energy Engineering, Vol. 6 No. 3, 2016, pp. 43-48. doi: 10.5923/j.ijee.20160603.01.
1. Introduction
Energy is the crucial component of life. Energy can not be created nor destroyed. It can only be converted into another form to meet the necessities of life, as well as the use of petroleum and natural gas as an energy source.Oil and gas are commonly used in Indonesia even though they are in critical condition. In addition, their availability are dwindling whereas the prices of fuel and gas are also affecting some people with low incomes. Various fuel exploitation is made to obtain alternative fuel that can be used for many people and more affordable with the same quality of the fuel that had been experienced before. This quality includes a high generating heat levels, but not quickly burn out. Briquette is one of several alternative renewable energies and has enormous potential in Indonesia. Moreover, a briquette refers to a block of solid material which is highly flammable and used as fuel. The common types of briquettes are charcoal and biomass briquettes. The conversion of charcoal to a briquette may greatly enhance the efficacy of the charcoal produced from coal, wood or agricultural biomass regarding combustion and handling characteristics [1]. Major biomass includes cashew nutshell, grass, and rice husk were used in the form of raw biomass, hydrolyzed biomass and carbonized biomass [5]. Hence, it is necessary to produce briquettes to replace the use of gas and oil fuel oils. One of the solutions is the briquettes to be made from environmental waste such as garbage, and other industrial wastes that can be used to blend the briquettes [4]. In Semarang, hyacinth was used as briquette for agriculture and domestic purpose with price Rp. 1000 – Rp. 2000 per kilogram. Different from coconut shell briquette, hyacinth briquette produces fire. Coconut shell briquette is applied as energy alternative with total energy 6481 cal/kg.Plastic waste is contributing 2% of the total municipal solid waste. The plastic used as packaging is a type of plastic that is the most abundant in the plastic waste because of the fast consumable. High Density Polyethylene (HDPE) is a type of plastic that most widely used as a packaging. Likewise, organic waste such as water hyacinth, coconut shell, and bagasse. Plastic waste has a high calorific value, and is potentially increasing the calorific value of the organic waste. One type of plastic rubbish is HDPE. The calorific value of this kind of plastic at 11,047 kcal / kg, meets the standard calorific value of bio-coal after carbonized briquettes molded.
2. Materials of Briquettes
The initial step in this research was the preparation of briquette manufacturers such as briquette mold tools, carbonization kiln and pot reactor useful to form briquettes and as a raw material burning tool (Figure 1).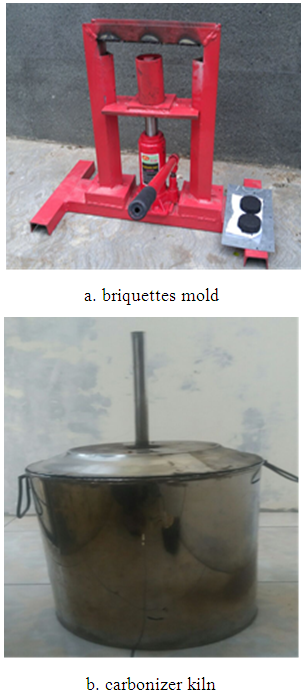 | Figure 1. Briquette maker |
The following is the collection of raw material briquettes, burning, and molded the briquettes (Figure 2).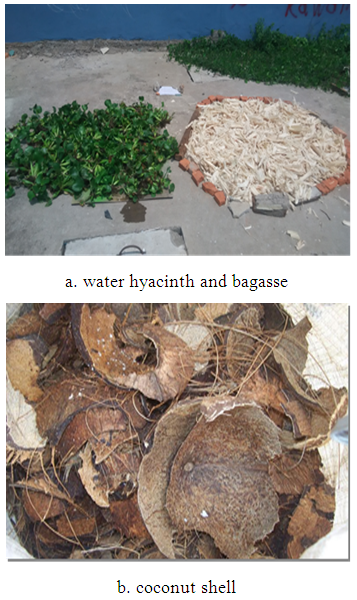 | Figure 2. Materials of briquettes |
After collecting the raw materials, the following process is the making of charcoal powder from the main raw materials by carbonization. The main component in the form of charcoal powder with a certain composition is mixed with an adhesive material such as starch and it is formed using a compaction molding briquettes. Then, the briquettes are dried by sunlight. The selection of the mixing is 80-20%, 60-40%, 40-60%, and 20-80%. The samples of briquettes are as follows:a. EG80PL20, contain 80% charcoal of water hyacinth and 20% charcoal of HDPE.b. EG60PL40, contain 60% charcoal of water hyacinth and 40% charcoal of HDPE.c. EG40PL60, contain 40% charcoal of water hyacinth and 60% charcoal of HDPE.d. EG20PL80, contain 20% charcoal of water hyacinth and 80% charcoal of HDPE.e. TP80PL20, contain 80% charcoal of coconut shell and 20% charcoal of HDPE.f. TP60PL40, contain 60% charcoal of coconut shell and 40% charcoal of HDPE.g. TP40PL60, contain 40% charcoal of coconut shell and 60% charcoal of HDPE.h. TP20PL80, contain 20% charcoal of coconut shell and 80% charcoal of HDPE.i. AT80PL20, contain 80% charcoal of bagasse and 20% charcoal of HDPE.j. AT60PL40, contain 60% charcoal of bagasse and 40% charcoal of HDPE.k. AT40PL60, contain 40% charcoal of bagasse and 60% charcoal of HDPE.l. AT20PL80, contain 20% charcoal of bagasse and 80% charcoal of HDPE.Figure 3 shows the appearance of the samples.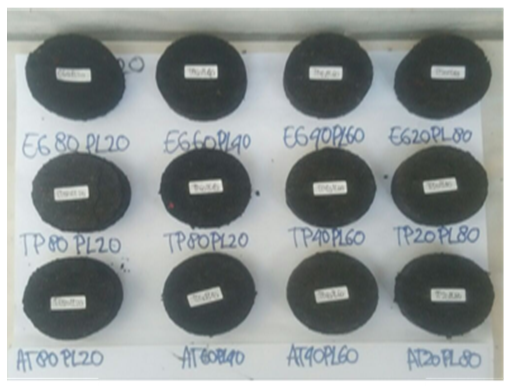 | Figure 3. Samples of briquette |
3. Analysis of Briquettes
The qualities tests of samples are complete moisture test and proximate content tests which include: moisture content, ash content, fixed carbon, and volatile matter tests. In addition, there are also calorific value and ignition properties, flame time and briquette burning rate tests.
3.1. Moisture Content Test (ASTM D.3173-08)
First of all, the weight of the empty cup was measured (B), then the test sample was weighed as much as ± 1 gram. After that, the weigth of the cup together with the sample were measured (A). The difference in the result of the cup weight and sample test (C) was calculated as formula (1). The samples were subsequently incorporated into an oven/the furnace at a temperature of 104-110°C in 1 hour. Once inserted into the oven/furnace, the cup containing the sample is inserted into the desiccator for ± 30 minutes (D). The moisture content, KA, was then calculated using formula (2). | (1) |
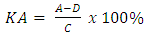 | (2) |
KA : moisture content (%)A : weight of the cup + weight of the test sample (gram)B : weight of empty cup (gram)C : weight of sample (gram)D : weight the cup + sample after heating (gram)
3.2. Ash Content Test (ASTM D.3174-04)
At first, weigh the empty cup, then the test sample was weighed as much as ± 1 gram. Next, weigh the cup plus the weight of the test sample. The ashing step is done by entering the platinum dish containing the test sample into the incineration furnace. The ashing process has three stages, first, insert the tool into the cup platinum furnace and heat to a temperature of 400-450°C for 1 hour. Then the temperature is increased again to 700-750°C for 2 hours. Finally, raise the return temperature ashing furnace to a temperature of 900-950°C and wait for 2 hours. The ash content was calculated using formula (3).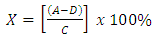 | (3) |
X : ash content (%)A : weight of the cup + weight of the test sample (gram)C : weight of sample (gram)D : weight of the cup + sample after heating (gram)
3.3. Volatile Matter Test (ISO562-2010)
Firstly, weight the empty platinum cup. Then enter the sample ± 1 gram into a platinum cup, fill the cup containing the test sample into the furnace at temperatures ranging from 850-950°C for 7 min. After that, remove the cup from the platinum furnace tool and put into a desiccator for 30 minutes. | (4) |
 | (5) |
A : weight of the cup + weight of the test sample (gram)B : weight of empty cup (gram)C : weight of sample (gram)D : weight the cup + sample after heating (gram)ZT : volatile matter (%)KA : moisture content (%)
3.4. Fixed Carbon Test (ASTM D.3172-07)
Levels of carbon bound can only be known if its value of moisture, ash, and volatile matter are also known. The calculation of the carbon content as ASTM D 3172-07 was using the following equation: | (6) |
FC : fixed carbon (%)KA : moisture content (%)ZT : volatile matter (%)X : ash content (%)
3.5. Gross Calorific Value Test (ASTM D.5865-10a)
The gross calorific value test was applied using bomb calorimeter equipment which well suited to ASTM D5865-10a as follows: | (7) |
Qvad : calorific value (J / gram)Ee : the heat of the bomb tool (J / °C)t : temperature when it is raised (± 10.7 °C)e1 : acid value (J)e2 : Value of mix when the process bomb (J)e3 : Value of sulfur (J)e4 : Value of aid combustion process (J)m : weight of sample (gram)
3.6. Total Sulfur Test (ASTM D.3177-02)
The total sulfur test was conducted to determine the level of total sulfur in a briquette. It should have passed the testing process calorific value using a bomb calorimeter. Determination of sulfur content was obtained based on the equation according to ASTM method D3177-02 as a reference source in the laboratory of Balai Pengujian Mutu Barang Indonesia as follows: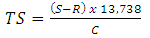 | (8) |
TS : Total Sulfur (%)S : sediment value (gram)R : correction value (gram)C : weight of sample (gram)
3.7. Long Startup Test
The long startup test was applied to find out the most easily ignited on the briquettes. Compares to the others fuel, briquettes rated was quite difficult to be ignited. The long startup test used a cotton ball soaked in kerosene then ignited, and the flame was used to lit the briquettes. The burning time of the briquettes was measured by using a stopwatch.
3.8. Flame Time Test
The flame time test aims to determine which briquettes are the most rapid depleted when they are burnt. The testing process was done when the flame lit briquettes to burn and calculated the time needed to burn out a briquette by using a stopwatch.
3.9. Burning Rate Test
Burning rate is the speed of briquettes discharged to ashes with a certain weight. Burning rate is expressed in the units of grams/minute. | (9) |
4. Result and Discussion
4.1. Moisture Content
The moisture content observed decreases with an increase in HDPE concentration (Figure 4). The EG80PL20 performed the highest moisture content (10.1%), the TP20PL80 performed the lowest moisture content (0.9%).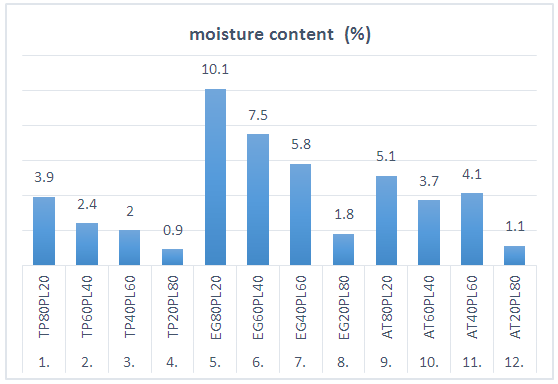 | Figure 4. Moisture content |
Figure 4 shows the higher levels of HDPE in the briquettes, the lower the water content contained therein. The water content of all samples of briquettes in this study meets the standards ESDM N0.047 2006 is lower than 15%.
4.2. Ash Content
Based on the test results within all samples of ash content briquettes, it was attained the highest ash content in briquettes (EG80PL20) of 23.1% and ash content was lowest for the coconut shell (TP80PL20) of 2.6 as shown on figure 5.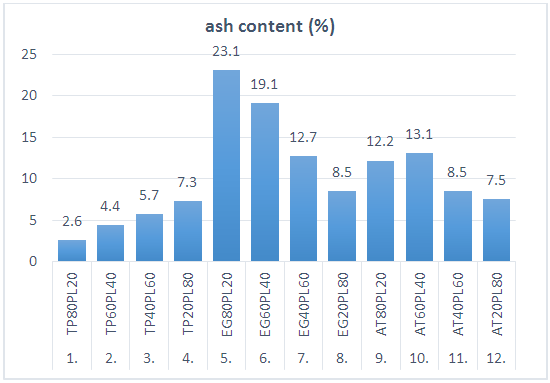 | Figure 5. Ash content |
Compliant ESDM N0.047 In 2006, ash content briquettes are allowed at less than 15%, so there are two samples that do not meet the standards that EG80PL20 which has ash content of 23.1% and EG60PL40 with ash content of 19.1%.
4.3. Volatile Matter
The volatile matter of the briquettes observed increases with an increase in HDPE concentration. Based on the results of the volatile matter test among all samples of the briquettes, the highest levels of the substance contained in the briquette fly EG20PL80. The highest value was 84.7%. Meanwhile, the lowest volatile matter content was the (TP80PL20) as amounted to 35.2%.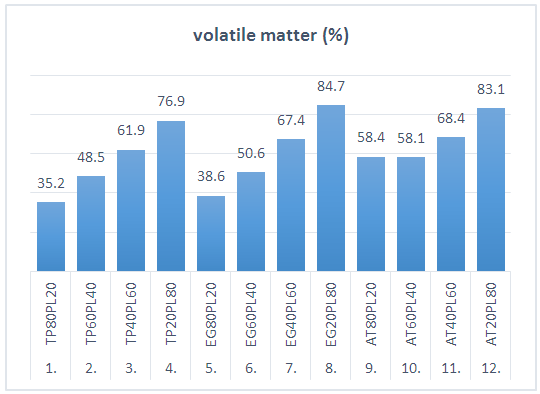 | Figure 6. Volatile matter |
Volatile matter consists of gas-combustible gases such as hydrogen, carbon monoxide (CO), methane (CH4), and gases that do not burn like CO2 and H2O, and it effects on the volatile matter combustion perfection and intensity of the fire. Standard ESDM N0.047 of 2006 states that the value of volatile matter adjusted to the raw material of the briquettes.
4.4. Fixed Carbon
It was observed that fixed carbon content decreases almost monotonically with an increase in HDPE concentration. The highest bound carbon content found in coconut shell briquettes was 80% and 20% HDPE plastic (TP80PL20) of 58.1% and the lowest for the carbon bonded briquettes 20% water hyacinth and plastic HDPE 80% (EG20PL80) of 4.9% as shown on figure 7. Standard ESDM N0.047 not determine thresholds for levels of carbon bound.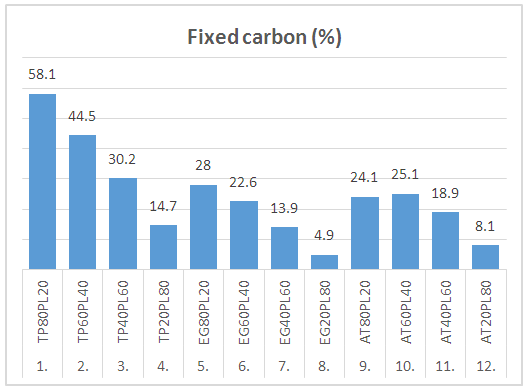 | Figure 7. Fixed carbon |
4.5. Gross Calorific Value
Based on the results of testing the content of the calorific value in all samples of the briquettes, the highest value was performed by the charcoal briquettes (AT20PL80), which is 9055 Kcal/Kg, whereas the lowest was shown by the briquettes (EG80PL20) of 3510 Kcal/Kg.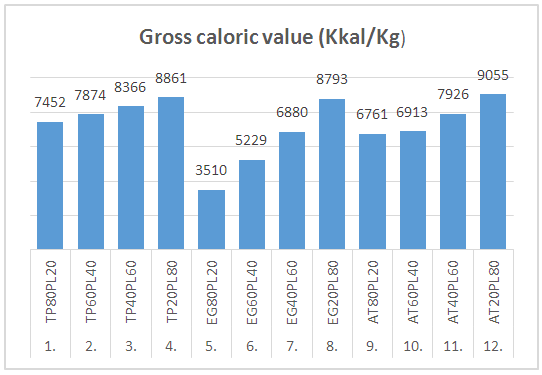 | Figure 8. Gross calorific value |
The calorific value of briquettes is improved by increasing the content of charcoal briquettes plastic. In accordance with Standards ESDM N0.047, calorific value is allowed to be higher than 4400 Kcal / Kg. Amongst all the samples, only sample EG80PL20, which has a calorific value of 3510 Kcal / Kg, did not meet the standards.
4.6. Sulfur Content
Figure 9 shows the value of the lowest sulfur contained in the sample TP40PL60 i.e. 0.06%. The content of the highest calorific value contained in EG40PL60 samples with results of 1.07%. Compliant ESDM 47 permitted sulfur content below 1%, then the sample EG40PL60 did not meet those standards.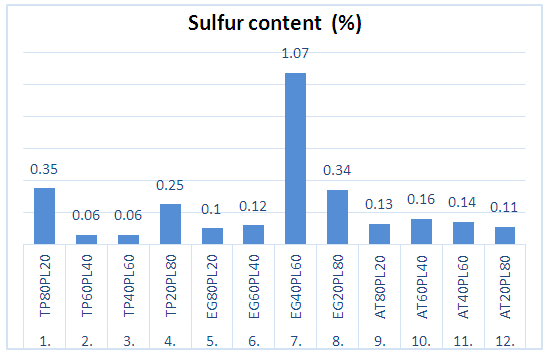 | Gambar 9. Sulfur content |
4.7. Long Start Up
Based on the test results of long startup for all samples briquettes, it is obtained that startup longest time contained in briquettes TP80PL20 was 210 seconds, and the fastest long startup contained in briquettes EG80PL20 for 71 seconds.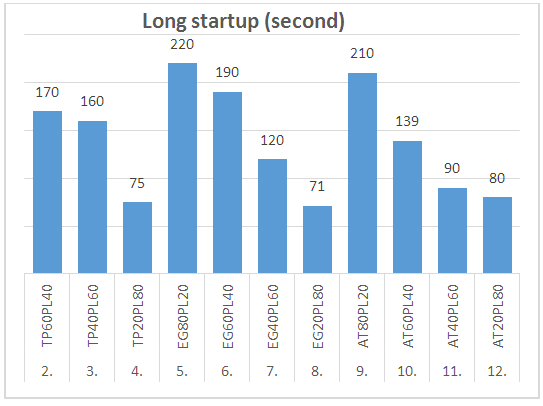 | Figure 9. Long startup. Long startup is not regulated in the standards ESDM N0.047 |
4.8. Flame Time
The longest flame time was the briquettes TP80PL20 with the longest time 35 minutes 11 seconds. Meanwhile, the briquette with a short period of flame was the briquette EG80PL20 for 14 minutes 31 seconds. 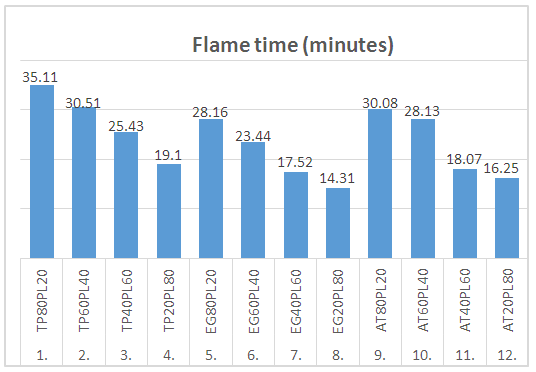 | Figure 10. Flame time |
The flame time was not set in the standard ESDM No. 47. briquettes combustible or flame will quickly run low.
4.9. Rate of Burning
Based on the flame time test results for all samples, the highest burning rate was performed by the composition of EG20PL80. The burning rate is 02.71 g/min. The briquette with the fastest firing rate was obtained by AT80PL20 of 00,99 g / min (figure 11).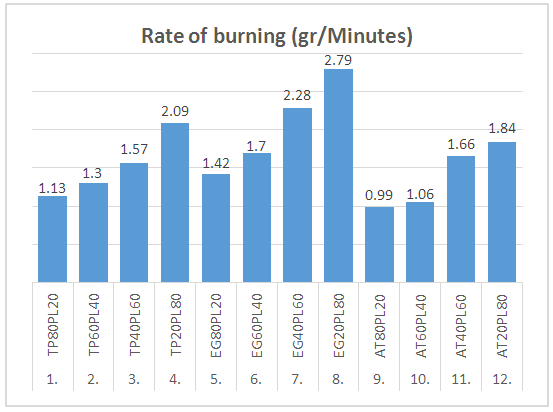 | Figure 11. Rate of burning |
Theoretically, the higher content of volatile compounds, the more combustible briquettes with high combustion speed.
5. Conclusions
HDPE waste with a mixture of coconut shell, water hyacinth, and bagasse can be utilized as fuel in the form of briquettes to be used as an alternative energy.HDPE plastic waste briquettes mixed with coconut shell, water hyacinth, and bagasse are made to meet the standards set in the main parameter based on the Minister of Energy Regulation No. 047/2006 on guidelines for the manufacture and utilization of coal briquettes and coal-based solid fuel.The optimum mixture of materials to be used based on the calorific value of briquette is briquette charcoal material bagasse 20% to 80% HDPE plastic charcoal (AT20PL80).
ACKNOWLEDGEMENTS
The writers are highly thankful to Kementrian Riset Teknologi dan Pendidikan Tinggi Republik Indonesia for funding the research.
References
[1] | Abdu Zubairu, Sadiq Abba Gana, 2014, Production and Characterization of Briquette Charcoal by Carbonization of Agro-Waste, Energy, and Power, 4(2): 41-47. |
[2] | Agus Triono, 2006, Charcoal Briquette Characteristics of Mixed Sawdust Wood Africa and Sengon with Addition of Coconut Shell, Institut Pertanian Bogor. |
[3] | Siti Nurjanah, Dede Rohmat, Agus Hidayatul Rahman, 2010, Utilization of Water Hyacinth Fiber as Composite Materials For Textile, Institut Pertanian Bogor. |
[4] | Sudiro Sigit Suroto, 2014, Effect of Composition and Size of Briquette Powder Made from Coal and Straw for Combustion Characteristics, Surakarta, Politeknik Indonusa. |
[5] | S. H. Sengar, A. G. Mohod, Y. P. Khandetod, S. S. Patil, A. D. Chendake, 2012, Performance of Briquetting Machine for Briquette Fuel, International Journal of Energy Engineering, 2(1): 28-34. |
[6] | Ju Win, 2010, Quality of Composite Board Made from Different Levels of Additives Waste Oil Palm Trunk and High Density Polyethylene, Universitas Sumatra Utara. |
[7] | J. T. Oladeji, C. C. Enweremadu, 2012, The Effects of Some Processing Parameters on Physical and Densification Characteristics of Corncob Briquettes, International Journal of Energy Engineering, 2(1): 22-27. |
[8] | Pallavi, H. B., Srikantaswamy, S., Kiran, M.B., Vyshnavi, D. R. and Ashwin, C. A., 2013, Briquetting agricultural waste as an energy source, J. of Environmental Science, Computer Science and Engineering & Technology. (2) 1 p. 160 – 172. |
[9] | Olorunnisola, A. O., 2007, “Production of Fuel Briquettes from Waste Paper and Coconut Husk Admixture” Agricultural Engineering International: the CIGR E-journal. Manuscript EE 06 006 Vol. IX. |
[10] | Ugwu, K. E. and Agbo, K. E., 2011, Briquetting of palm kernel shell, J. Appl. Sci. Environ. Manage. (15) 3 p. 447 – 450. |