Tanjin Amin, Shohanur Rahman Shohug
Department of Mechanical Engineering, Bangladesh University of Engineering & Technology (BUET), Dhaka, Bangladesh
Correspondence to: Tanjin Amin, Department of Mechanical Engineering, Bangladesh University of Engineering & Technology (BUET), Dhaka, Bangladesh.
Email: |  |
Copyright © 2015 Scientific & Academic Publishing. All Rights Reserved.
Abstract
In this paper, an effort is made to show the common steam engineering practices in Textile Sector. It has been observed that malpractices are causing a lot of wastage of energy and making the process inefficient. Various sources of loses are investigated and represented by using some simple calculations. The investigation shows the most alarming is the draining of condensate which saves not only heat energy but also electrical energy. Condensate also reduces the heavy load on ground water. We have concentrated on distribution system and blowdown systems also. After going through this paper, it is expected that, other industries outside Bangladesh will have an idea about efficient steam engineering practices. If proper steam engineering practices have been applied in textile industries, it will obviously increase the GDP of Bangladesh.
Keywords:
Feed Water Temperature, Blowdown, CRS, PRS, PPPU, Flash Steam, Condensate
Cite this paper: Tanjin Amin, Shohanur Rahman Shohug, A Study on Steam Engineering Practices in Textile Industries of Bangladesh, International Journal of Energy Engineering, Vol. 5 No. 1, 2015, pp. 5-8. doi: 10.5923/j.ijee.20150501.02.
1. Introduction
Bangladesh has emerged as a giant in textile industries within just three decades. The Generalized System of Preferences (GSP) of the European Union and USA, which conferred certain quota, has benefitted the textile sector enormously [2]. Almost 80% of total foreign earnings comes from this sector and near about 50% of total work force of the country is involved in textile sector [1]. The availability of cheap labour along with work quality has made it convenient the world famous brands to choose Bangladesh as a utopia in this sector. But lower fuel cost is often ignored, when an effort is made to find out the main reason of emergence of textile sector. Steam is used in all types of textile industries; sometimes to ensure the product quality parameters, sometimes to assist the utility machineries, such as chillers. It is a matter of pity that, steam is often considered free and its use is not done in an efficient way. Most probably, the availability and relatively low cost of natural gas are behind such ideas. Condensate, process water & dyeing water are drained, which can be reused [3, 5]. In this paper, an effort is made to show the usual alarming misuse of steam energy. We have also tried to suggest solutions using some conventional instruments. For this purpose, we have visited twenty textile industries in Bangladesh and observed the steam generation and distribution system very carefully. Steam engineering practice is often ignored and there is very little amount of research work on this field for Bangladesh. It is expected that this article will raise awareness regarding steam system designing not only in Bangladesh but also in other developing countries. This article will motivate others to undertake extensive research work to find out the optimum solution for textile industries in Bangladesh.
2. Efficiency Scenario
Boiler is used as the steam generator. It has been observed that, the boilers are running at much lower than the design pressure, which results in lower efficiency. To cope up with space available, scenario in eight industries is shown below in two tables.Here, Ind stands for industry and design pressure for all the boilers is 10.54 barg. But, all the boilers run in maximum efficiency at 9 barg & 90ºC FWT.Table 1. Boilers with Higher FWT 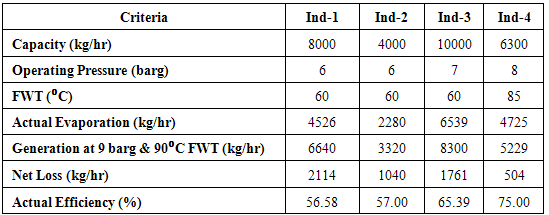 |
| |
|
Table 2. Boilers with Lower FWT 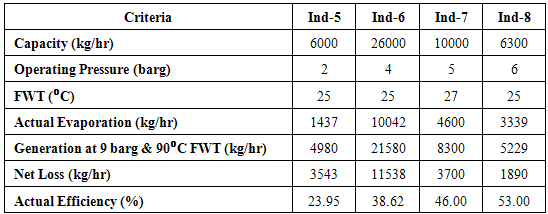 |
| |
|
Observing these two charts, it has been clearly understood that, efficiency is independent of boiler capacity. Efficiency mainly depends on feed water temperature & working pressure. Boilers with higher feed water temperature run more efficiently. Lower operating pressure results in lower efficiency. More closer to design pressure, gives better efficiency. The cumulative effect of feed water temperature and operating pressure can be easily found from Industry 4 & 8. Nearly 8-9% efficiency is reduced due to reduction in 1 barg operating pressure. Operating in lower boiler pressure is the effect of lower gas pressure in many cases. But, lack of consciousness is the main reason in maximum industries in Bangladesh. Feed water temperature can be easily raised by following steps.1. Using Economizer2. Utilizing flue gas 3. Feeding condensate in boiler feed waterIndustry 5 to 8 is not applying any of the stated measures. Economizer is only available in Industry-4. Economizer can increase the efficiency up to 5%. Condensate recovery is rarely done in Bangladesh. Interestingly, flash steam is bypassed to environment. In condensate, there are 90% water and 10% flash steam approximately. But, this 10% flash steam contains near about 40% of total energy due higher latent heat of vaporization. A simple Pressure Powered Package Unit (PPPU) can help to recover condensate from steam consuming machines. Flash steam pressure produces the driving force of condensate to the boiler feed tank. No electrical power is required. For an efficient condensate recovery system, it is highly recommended to keep the steam consuming machines closer to the boiler feed tank while planning the layout of the factory. To find out the wastage of energy due to absence of condensate recovery system, loses in terms of m3 of natural gas is shown in table 3.Sample Calculation:Industry-7 is considered for sample calculation.Actual evaporation = 4600 kg/hrAmount of recoverable condensate = (4600 X 0.80) kg/hr = 3680 kg/hrAmount of flash steam = (3680 X 0.10) kg/hr = 368 kg/hrAmount of condensed water = (3680 X 0.90) kg/hr = 3312 kg/hrEnthalpy of flash steam at 8 barg = 2269 KJ/kgEnthalpy of condensed water at 95ºC = 395 KJ/kgHeating value of natural gas = 34694 KJ/m3Total enthalpy of flash steam = (368 X 2269) KJ/hr = 834992 KJ/hrTotal enthalpy of condensed water = (3312 X 395) KJ/hr = 1308240 KJ/hrTotal recoverable energy = 2143232 KJ/hrAmount of natural gas required to produce this energy = (2143232/34694) m3/hr = 61.78 m3/hr Table 3. Wastage of Natural Gas due to Absence of CRS 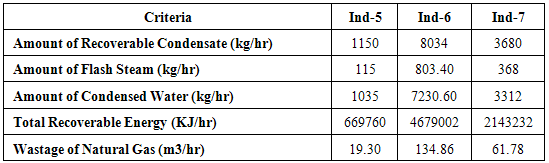 |
| |
|
In a project of USD 45 million in Bangladesh, it is found that to have an effective condensate recovery system, which is capable of recovering 80% of total actual evaporation, only 0.30% of total project value is required and the pay-back period is nearly one year. In countries where fuel cost is higher, pay-back period will be surely reduced. Effective condensate recovery system will not only increase efficiency of the system but also reduce the heavy demand on ground water. Another interesting fact about condensate recovery is that, it lessens the heavy load on ground water as it runs like a closed loop. As a result, saves a significant amount of electrical energy too. Now there is near about 15-18% more water used than required [4]. If condensate is recovered, this amount will significantly be reduced.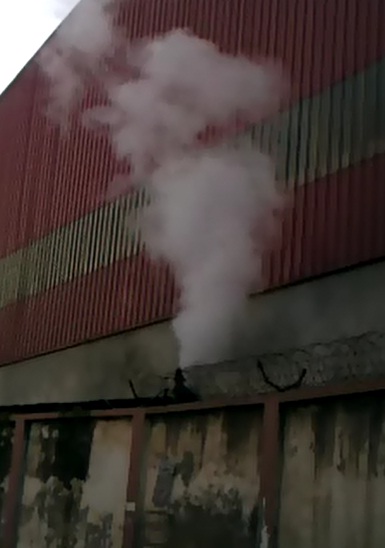 | Figure 1. Flash Steam is Vented to Atmosphere |
3. Blowdown Scenario
All the industries are running with manual blow down system. It is causing significant loss of natural gas. To have an idea about how much waste of natural gas is done by manual blow down, frequency and amount of blow down are observed and actual blowdown requirement is also calculated. The results are shown in table 4. Table 4. Wastage of Natural Gas due to Manual Blowdown 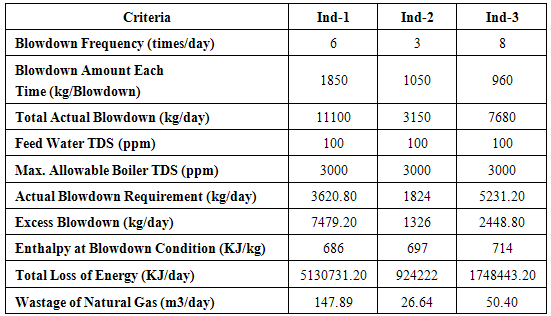 |
| |
|
Sample Calculation:For Industry-3,Actual blowdown requirement = (Feed Water TDS / Max. Allowable Boiler TDS) X Actual Evaporation X 24 = (100/3000) X 6539 X 24 kg/day = 5231.20 kg/dayIt has been found that, all the factories are contributing to significant amount of wastage of natural gas by conventional manual blowdown process. More the amount of actual evaporation more will be the amount of loss. Automatic blowdown control can minimize the loss to a significant extent.
4. Distribution Scenario
Improper pipeline sizing & distribution practice cause significant loses. Steam should be produced & distributed at High pressure (i.e. 9-10 barg) and utilized at low pressure (i.e. 3-4 barg). Due to high pressure, specific volume of steam would be low; which results in reduced pipe diameter as well as reduced radiation loss. Again, utilizing steam at low pressure ensure greater latent heat of condensation. So, maximum amount of heat can be extracted for utilizing in the heat exchangers. This can be simply done by a Pressure Reducing Station (PRS), which reduces pressure of steam without hampering the flow. It also increases the dryness fraction & supplies better quality dry steam. Some simple calculations are given below to show how a PRS can save energy.Let us take Ind-5 from Table. 2 as an example, which produces 1437 kg/hr steam at 2 barg operating pressure. When it reaches the process the pressure becomes 1.5 barg due to distribution losses. This factory is generating steam at lower pressure as the appliances demand lower pressure. But doing this, they are certainly wasting a lot of heat.Sample Calculation:Enthalpy of steam at 6.5 barg = 2760 KJ/kgLatent heat of steam at 1.5 barg = 2613 KJ/kgIf PRS is used, the amount of energy saved = (2760-2613) KJ/kg = 147 KJ/kgWastage of Natural Gas = (147 X 1437 / 34694) m3/hr = 6.08 m3/hr Actually, the loss is more as the factory is generating reduced amount of steam than the capacity.
5. Conclusions
The following conclusions can be made from the observations.1. In most of the boilers are operated at lower pressure, which cause huge reduction in overall efficiency of boiler.2. Condensate is not recovered properly, which causes 70-80% of total loss.3. 10-15% of total loss happens due to improper blowdown process.4. 8-12 % loss occurs because of using steam at high pressure in appliance side.5. Condensate recovery not only increases the heat energy, but also saves the amount pumping power.
ACKNOWLEDGEMENTS
The authors deeply acknowledge technical & financial support of Surma Dyeing Ltd, Natural Denim Ltd, Anlima Yarn Dyeing Ltd, Maxcom International Dyeing Ltd, Zaara Composite Dyeing Ltd, Pakiza Dyeing & Printing Ltd, CPM Composite Dyeing Ltd, Nightingale Composite Dyeing Ltd, Ama Syntex Dyeing Ltd, Islam Dyeing Ltd, Uttara Dyeing & Knitting Ltd, Arkay Hometex Ltd, Spark Composite, Angels Composite, Mahmud Denims Ltd, Mozart Composite, Hypid Textile Ltd, Matsouka Apparels Ltd & Square Denims Ltd.
References
[1] | CPD Dialogue Report 18, “The Textile and Clothing Industry of Bangladesh,” Aug. 1999. |
[2] | M. M. Islam, K. Mahmud, O. Faruk, and M. S. Billah, “Textile Dyeing Industries in Bangladesh for Sustainable Development,” International Journal of Environmental Science and Development, Vol. 2, No. 6, December 2011. |
[3] | A. Kar. (2012) Clean by Design homepage on NRDC. [Online]. Available: http://www.nrdc.org/international/cleanbydesign/files/cbd-textile-mills-best-practices-bangladesh.pdf |
[4] | BTT Desk (2011) Greening the Supply Chain of the Textile Industry in Bangladesh. [Online]. Available: http://www.textiletoday.com.bd/magazine/222 |
[5] | M. M. Islam, “Assessment of environmental impacts for textile dyeing industries in Bangladesh,” International Conference on Green Technology and Environmental Conservation (GTEC), December 2011. |