Vivek Kaundal 1, Rajesh Singh 2, Madhu Sharma 1
1University of Petroleum and Energy Studies, Dehradun, India
2HEAD, Robotics Institute R&D, University of Petroleum and Energy Studies, Dehradun, India
Correspondence to: Vivek Kaundal , University of Petroleum and Energy Studies, Dehradun, India.
Email: |  |
Copyright © 2012 Scientific & Academic Publishing. All Rights Reserved.
Abstract
A Wireless Personal Area Network (WPAN) monitoring system is proposed to measure the voltage and current generated for wind mill farm, it is considered as a target application. It has a Rigid hub structure, economical larger capacity i.e. 5– 7 MW for offshore sitting and variable speed turbines are three major developments characterize in a wind machines. The forth development is the adoption of gearless wind turbine eliminating gearboxes as weakest link in the chain of modern wind turbines. Eliminating the burdens associated with cabling, the proposed wireless network enables sensors to place on the each individual mill to monitor voltage and current so that we can optimize wind farm productivity. The proposed system consist of ZigBee based wireless personal area network i.e. communication through ZigBee transceiver module, coding of microcontroller through AVR Studio4, and interfacing all with wind mill. The data from the wind-power generator will be collected with the help of proposed system and wired RS-232 Interface. The collected data will be displayed with the help of suitable GUI in MATLAB.
Keywords:
WPAN (Wireless Personal Area Network), ZigBee- CC2500, RS-232 interface, MATLAB
Cite this paper:
Vivek Kaundal , Rajesh Singh , Madhu Sharma , "Wireless Parameters Monitoring Simulation and Design in Wireless Personal Area Network Using 2.4 GHz Transceiver Module for Wind Mill", International Journal of Energy Engineering, Vol. 2 No. 6, 2012, pp. 279-284. doi: 10.5923/j.ijee.20120206.02.
1. Introduction
Due to the drawbacks of wired network systems, now a day’s all the wired system is being replaced by wireless systems. In a wired network-• A lot of wiring is required.• Less flexibility.• New devices can’t be accommodated easily.• Costly for networks spread over a large area.In wireless network-• It avoid lot of wiring.• It can add new devices at any time.• Flexibility of physical partitions.• Centralized monitoring can be accessed.To modify the existing design of wind mills engineers must be provided with the information’s like voltage, current, frequency, wind speed and direction, rotor speed, etc. The proper collection of data from the wind power electricity mainly depends on the data collecting and transmission interface and its related system[3].The proposed wireless personal area network system will be designed in the following steps:(1) Remote monitoring and controlling system will be designed as per the requirements of local features.(2) A module for wind-power electricity generator will be designed to transmit real-time parameters during running condition of the wind electricity generator.(2) ZigBee wireless Personal Area Network will be used for the designing a data transmission interface (RS 232) to replace existing design.(3) GUI will be designed to display and store real-time running parameter.
2. Block Diagram
The proposed transmitting system is shown in Figure1. The main components of this proposed structure areFigure 2 shows the receiving section of the proposed system where Zigbee module received the data wirelessly from Transmitting Zigbee module shown in Figure 2 and the data will be the processed through max 232 IC (To Convert RS logic) and then it will fed to PC through USB to serial cable.(1) Voltage and current module that will read the voltage and current data from the wind mill section and will send it to the microcontroller.(2) Microcontroller reads the input data from the voltage and current module and will process it as per the incoming data and will transfer the final signal to the Zigbee module through USART of microcontroller. | Figure 1. Block diagram of Measuring section (Transmitting Section) |
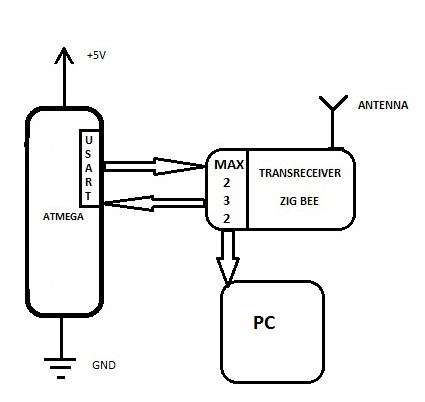 | Figure 2. Block diagram of Data collecting section (Receiving Section) |
3. Hardware Development
Figure 3 and Figure 4 shows the interfacing of transmitting section and receiving section .The brief descriptions of components which is used to design a transmitting and receiving end are given below-a) LCD unit- The lcd jhd162A (16x2) is interfaced with AVR microcontroller to display the dta information. The LCD data pins 11,12,13,14 are connected to port C (PC0 through PC3) of the AVR microcontroller. The control pins of LCD 4,5,6 Register-select (RS), Read/write(R/W) and enable are interfaced with PD6, PD5 and PD7 of the AVR microcontroller, respectively. R/W pin is keep permanently low to put the LCD into writing mode.b) Microcontroller-ATMEGA16 is a microcontroller of AVR series. It is low-power; 8-bit CMOS architecture with AVR enhanced reduced instruction set computer (RISC) architecture. ATMEGA 16 has 16 KB of in-system programmable flash memory, 512 bytes on EEPROM, 1 KB of SRAM, two 8-bit timers, one 16-bit timer, 32 general-purpose I/O lines and 32 general-purpose working registers. It integrates all the subsystems to form a complete unit[12].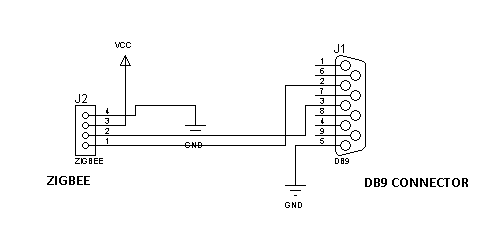 | Figure 3. Schematic of Data collection Section (Receiving Section) |
c) Power Supply- The power supply (220V, 50Hz AC to 12V, 500mA DC) is stepped down by transformer to take a secondary output of 18V at 500 mA. The output of the transformer is rectified by a full-wave bridge rectifier, filtered by capacitor, and regulated by7812. The regulated 12V is used to drive the proposed system.d) Zigbee-It is a low power and low cost 2.4 GHz transceiver designed for wireless applications. The Zigbee is designed for the 2400- 2483.5 MHz ISM (Industrial, Scientific and Medical) and SRD (Short Range Device) frequency band. This provides extensive hardware support for packet handling, data buffering, burst transmissions, clear channel assessment, link quality indication, and wake-on-radio. The main operating parameters and the 64-byte transmit/receive FIFOs of CC2500 can be controlled via an SPI interface. In a typical system, the CC2500 will be used together with a microcontroller and a few additional passive components[9].Key Features of Zigbee module is(1)13.3 mA in receiving mode, 250 kB is baud rate.(2)data rate (Programmable at 1.2 to 500 k Baud)(3)Frequency range is of 2400 – 2483.5 MHz it supported to OOK, 2-FSK, GFSK, and MSK.(4)SLEEP mode current consumption is 400 nA.(5)SLEEP to RX start up time is 240 us or in TX mode measured on EM design.(6)automatic low-power Receiving (RX) polling for Wake-on-radio operation.(7)FIFO buffer of 64-byte for receiving data and 64-byte for Transmitting data by enabling burst mode data transmission.e) DB9- It is 9 pin male/female connector. A D means two or more parallel rows of pins are surrounded by a D-shaped metal shield that provides mechanical support and some screening against electromagnetic interference, and ensures correct orientation. Pin contacts part is called the male connector or plug, and socket contacts part is called the female connector or socket. 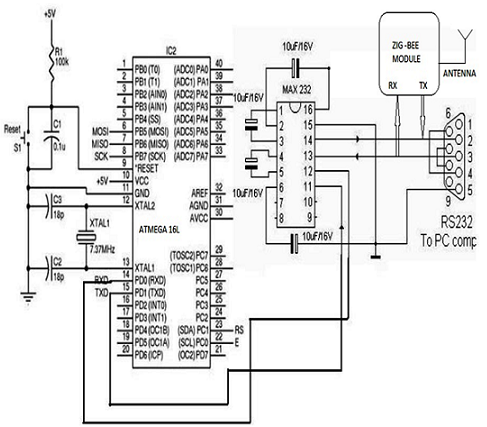 | Figure 4. Schematic of Measuring section (Transmitting Section) |
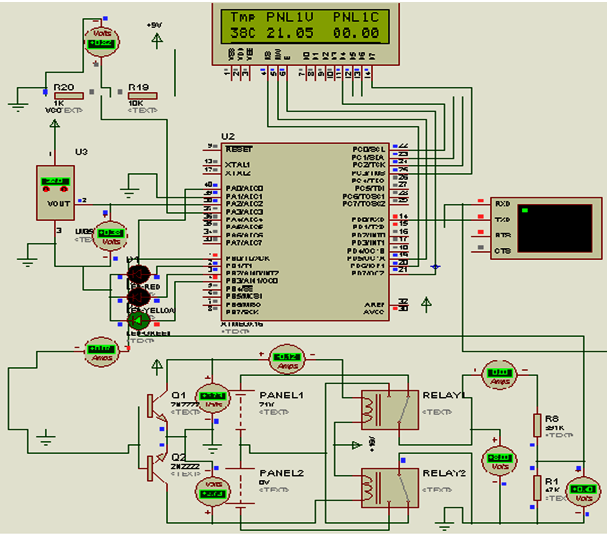 | Figure 5. Simulation model of proposed system using Proteus trial software |
f) In system programmer- MOSI, MISO, SCK, RESET, VCC and GND wires of In-System Programming (ISP) is used to attach the programmer to the 6 pin male connector of the AVR development board. Three wires Serial Clock (SCK), Master In – Slave out (MISO) and Master Out – Slave in (MOSI) are serial peripheral interface (SPI). In programming issue in AVR microcontroller, the programmer (ISP) always operates as the Master, and the AVR development board always operates as the Slave. The Master provides the clock for the communication on the SCK Line. Each pulse on the SCK Line transfers one bit from the Master (ISP Programmer) to the Slave (AVR development board) on the MOSI (Master Out – Slave In) line. Simultaneously, each pulse on the SCK Line transfers one bit from the AVR board (Slave) to the Programmer (Master) on the Master In – Slave out (MISO) line[10].g) MAX232 –It is level converter IC which has two driver/receiver that includes a capacitive voltage generator to supply RS232 voltage levels from a single 5-V supply. Each receiver converts RS 232 inputs to 5V TTL levels.-receivers have a typical threshold and hysteresis 1.3 V and 0.5 V respectively and can accept ±30-V inputs.-driver converts TTL/CMOS input levels into RS 232 levels[11].Finally, the hardware model is simulated using Proteus software (trial). Data which is sensed by the Voltage and current sensor will be processed by the controller and displayed through LCD and corresponding data also send using TX (15) pin of microcontroller. The running data on TX line is displayed using Virtual terminal in Proteus software. Various indicators like Multimeters, LCD data Display, variable data meter and virtual data terminal are shown in figure 5.
4. Software Development
The software development of designed system is used to get integration and functionality. ‘C’ language is used to develop the program to drive the system and AVR studio4 is used as compiler (WINAVR is running in backend). AVR studio4 software is free firmware for Windows and Linux operating systems. AVR functions like UART, timer, ADC, interrupts, etc are handled by AVR studio4 and provide the facility to write the program in embedded ‘C’. The resultant of the program is obtained in hex code file which burn into flash memory of AVR microcontroller using a In system USB programmer. The external generated clock of 14.7456MHz is used to activate the microcontroller; the fuse bytes are as follows:low fuse byte = C9high fuse byte = EF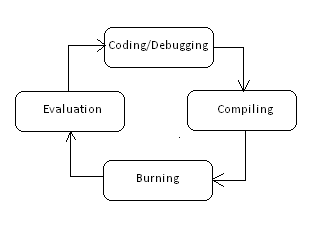 | Figure 6. Steps for software development |
In accordance to the functionality of each sub system the software was written in parts. To get the result of wireless personal area network application, the microcontroller has been programmed, which involved the following stepsIn the programming of the proposed system is used the following .c and .h file(1) lcd_display.c – The functionality of the attached LCD module(jhd162A) is control using c file. This c file contain initLCD( ), LCDclear( ), LCDwritestring( ) and LCDwriteInit ( ).The initLCD( ) code controls the initialization of the LCD, LCDwritestring( ) code control the data(movement, characteristics and location of the cursor) writing on the LCD by string wise or character wise (2) lcd_display.h - The variable, constant values and subroutines are handled by .h header file. This file defines that the use of global variable and subroutines which is used in the software files.(c) adc.c- To control the ADC of AVR microcontroller adc.c file is used . This is contain two major functions initADC( ), uint16_t readADC(uint8_t ch)Initialization of adc:initADC() { ADCMUX=(1< ADCSRA=(1< ADCSRA=(7< }Read data from adc:readADC(data) {//Selection of ADC Channel dataADCMUX&=~(1<<0);ADCMUX&=~(1<<1);ADCMUX&=~(1<<2);ADCMUX&=~(1<<3);ADCMUX&=~(1<<4);data=data &0b00011111;ADCMUX|=data;ADCSRA|=(1<while(!(ADCSRA & (1<ADCSRA|=(1<return(adc); }(d) usart_lib.c – The USART of AVR microcontroller is handled by .c file. This is contain three major functions USARTInit ( ), USARTRead ( ) and USARTWrite ( ).Initialization of usart:This function will initialize the USART.void USARTinit(uint16_t ubrr_value){UBRR= ubrr_value; //Set Baud rateUCSRC=(1<UCSRC=(3<Settle down Frame FormatUCSRB=(1<UCSRB=(1<//to enable The receiver and transmitter}Reading From The usart: This function will read data from the USART. char USARTread( ){while(!(UCSRA & (1< //Wait until a data is received{ //Do nothing}return UDR; // USART has got data from host and is available is usart buffer}Writing to usart:void USARTwrite(char data){while(!(UCSRA & (1< { //Do nothing }UDR=data; // write the data to usart buffer}The USB robokits programmer is used to burn the HEX file (machine language file) into the microcontroller’s program memory, which attached to the USB of Personal computer. Figure 7. shows the snapshot C coding for proposed system using of AVRstudio4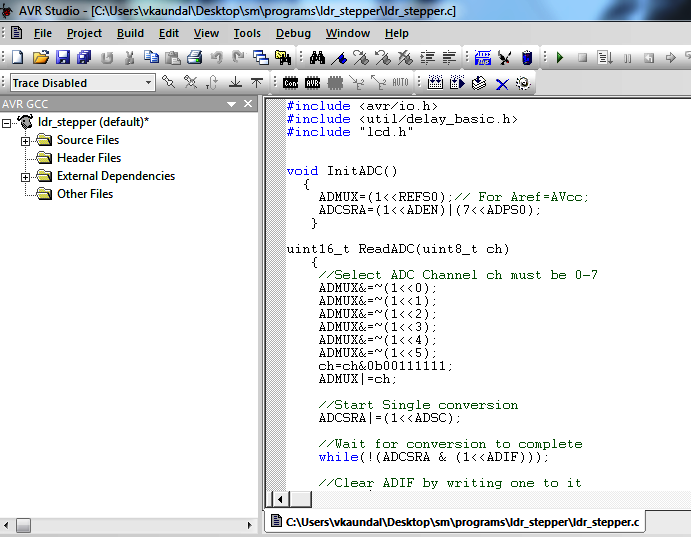 | Figure 7. snapshot C coding for proposed system using of AVRstudio4 |
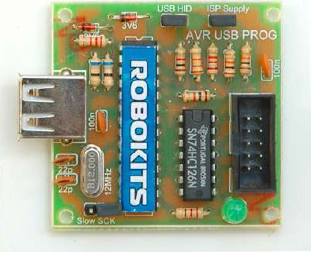 | Figure 8. view of hardware AVR programmer (ISP) by Robokits |
Figure 8 shows the view of hardware AVR programmer (ISP) by Robokits to burn the microcontroller.Figure9 shows the snapshot of robokits AVR programmer window to erase, write and verify .h file generated by AVRstudio4 to target
5. Results
The results of proposed system are shown through the appropriate GUI which is designed using MATLAB. The steps for making any GUI:(1) The first step is to make a Front look for proposed system which is called “GUI” as Graphical User Interface.(2) Settle the properties of each box Like push button, popup menu or box on GUI(3) The GUI is run by pressing run button from editor toolbar or RUN from debug button or simple Function5 (F5).Figure 10 shows the Snapshot of GUI of wireless data capturing using MATLAB.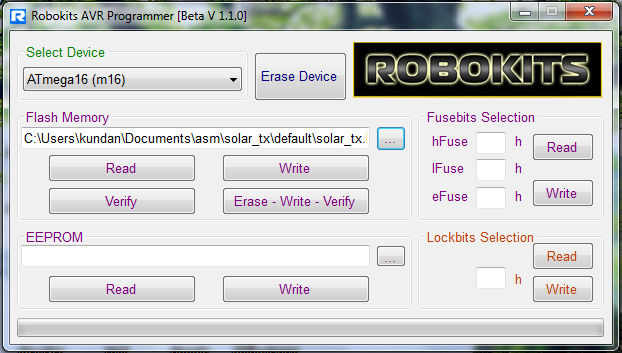 | Figure 9. snapshot of robokits AVR programmer window to erase, write and verify .h file generated by AVRstudio4 to target |
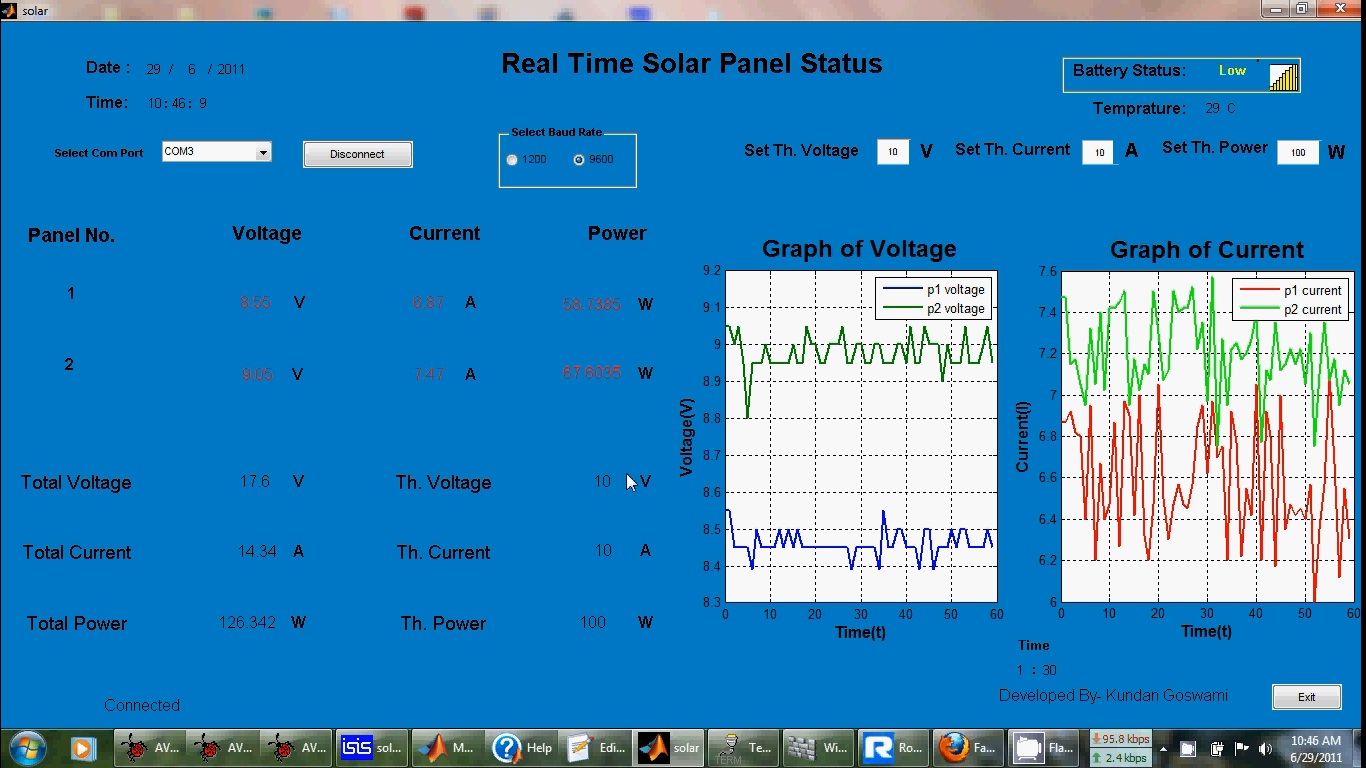 | Figure 10. Snapshot of GUI of wireless data capturing in receiving end using MATLAB |
6. Conclusions and Future Scope
A low-cost solution to enhance the remote monitoring capability of wind mill system is proposed. Portable model of WPAN system for monitoring voltage and current of wind –electricity generator is designed and developed at lab scale and found that(1)It is secure, robust and low-power consuming.(2)It can operate on multiple channels to avoid interference with other wireless devices (5) Continuous monitoring can help fault detection of particular wind mill in wind farm. The proposed system will provide a method to investigating the behavior of each windmill and will reduce the monitoring cost. Again different sensors for the measurement of parameters like wind speed, temperature, and humidity, will be interfaced for correlation and investigation of the effect of environmental loads. This method can also be applied to energy generation like Solar, Fuel cells, Hydroelectric etc. and they can be monitoring by utilizing heterogeneous wireless personal area networks.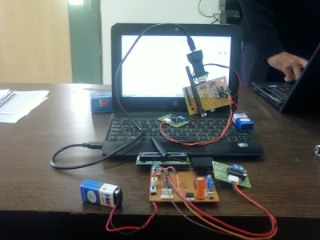 | Figure 11. View of system |
7. View of System
The view of the demonstration model of the system is shown in the figure 11.
References
[1] | Singh, R. Mishra, S. Joshi, P. “Pressure Monitoring in wireless sensor network using Zigbee™ transceiver module” ICCCT – 2011 ISBN: 978-1-4577-1385-9 |
[2] | Singh, R.; Mishra, S. Temperature monitoring in wireless sensor network using Zigbee™ transceiver module” ICPCES – 2010 ISBN:978-1-4244-8543-7 |
[3] | Chun-Liang Hsu and Wei-Bin WU “Practical design of constructing data transistion with zigbee WSN and RS 485 wired interface-example of small scaled wind power electricity generator system” Journal of Software, vol. 3, no. 8, november 2008. |
[4] | Jeong-Ju Kim; Chul-Ho Hong; Dong-Jin Kim; Bbun-Byul Lee; Jeong-Do Kim; Kyung-Nam Ko “The device for generation the distress signal and monitoring system for a Survivor based on WSN” ICEIE – 2010 ISBN: 978-1-4244-7679-4 |
[5] | Weiyun Jiao; Xiaojing Wang; Li Zhao; “Monitoring system of car-guardrail accident based on wireless sensor networks” ITST – 2008 ISBN: 978-1-4244-2858-8 |
[6] | F.L.Lewis “Wireless Sensor Networks”- Chapter 4, Smart environments:Technologies, Protocols, and Applications Journal. |
[7] | Mike Horton and John Suh “A Vision for Wireless Sensor Networks”– IEEE transactions on Industrial Electronics 0-7803-8846-1/05, 2005. |
[8] | A.Flammini, D.Marioli, E.Sisinni, A.Taroni “A real-time wireless sensor Network for temperature monitoring” – IEEE Transactions on Industrial Electronics1-4244-0755-9/07 2007 |
[9] | Rajesh Singh, Vivek Kaundal, Arpit Jain “wireless personal area network design and simulation to locate accidental information using 2.4 GHz transceiver module” international journal of engineering science & advanced technology ISSN: 2250–3676, Volume-2, Issue-2, 297 – 300 |
[10] | Rajesh Singh, Vinod Kumar, Pankaj Joshi “WPAN node design for Gathering Real Time Data through V1.9b terminal using 2.4 GHz Transceiver Module” “International Journal of Electronics and Computer Science Engineering “, ISSN- 2277-1956 |
[11] | J.Y. Chen, X.P. Zhou, “ZigBee Wireless Communication Technology in Industrial Controls,” Radio Engineering of China, Vol. 36, No. 6, pp. 61-64, 2006 |
[12] | Liu Jiangsha, Lei Wei, Yin You, “Designing of a wireless RF unit basingon CC2430,” International Electronic Elements, 2007 |
[13] | JI ZhengZhou, Li Yan, Lu Hu “The Implementation of Wireless Sensor Network node Based on ZigBee” - IEEE Journals 978-1-4244-2108-4/08, 2008 |
[14] | Alan Mainwaring, Joseph Polastre, Robert Szewczyk, David Culler,John Anderson “Wireless sensor networks Habitat monitoring” - WSNA’02, September 28, 2002 |