Ted Kozman , Yucheng Liu , William Simon , Jeff Guidry
Department of Mechanical Engineering, University of Louisiana, Lafayette, LA 70504, USA
Correspondence to: Yucheng Liu , Department of Mechanical Engineering, University of Louisiana, Lafayette, LA 70504, USA.
Email: |  |
Copyright © 2012 Scientific & Academic Publishing. All Rights Reserved.
Abstract
An “old” and “obsolete” boiler system was revitalized and an enhanced Steam Lab was established based on that system. In this project, modifications and improvements were made to the facility to establish the revitalized steam lab, which contains a 150 BHP boiler, condenser, steam turbine and generator, dynamometer, and various other pumps, heat exchangers and fluid lines. The working Steam Lab will provide test-bed capability for local companies, with which the project team and help the industry to meet the energy challenge by developing their energy-management plans and utilizing various energy sources efficiently and smartly. It will also be incorporated into the mechanical engineering curriculum at the UL Lafayette thereby substantially enhancing the mechanical engineering program and impacting the engineering education in UL Lafayette. This project was sponsored by the U.S. Department of Energy (DoE) and the Louisiana Department of Natural Resources (DNR) as a part of the Save Energy Now project.
Keywords:
Steam Energy, Steam Lab, Boiler System, Revitalization, Engineering Education
1. Introduction
In order to reduce annual energy consumption within the state of Louisiana, the Louisiana State Energy Office partners with the University of Louisiana at Lafayette (UL Lafayette) and its Mechanical Engineering Department to start a project, whose overall objective is to collaboratively achieve a 2.5% annual reduction in energy intensity among Louisiana’s industrial facilities. As an important part of this project, an “obsolete” boiler system was revitalized and based on which, an enhanced steam lab was established in Mechanical Engineering Department, UL Lafayette. The renovated steam lab will provide test-bed capability for local industrial companies and also be used as an experimental laboratory for teaching and research in the Engineering College of that university. The revitalization of this lab and its industrial and educational impacts are demonstrated in this paper.
2. Background
It is well known that a world energy crisis has been substantially impacting our economy as well as affecting our social life. Most of major industrial countries in the world are experiencing severe energy shortages due to the conflictbetween an enormous increase in the demand for energy as a result of industrial development and population growth and the limited supply of energy, which is far less than the actual demand. Another aftermath of the increasing demand for energy is environmental pollution, which mainly comes from different energy resources from fossil fuels to nuclear. Thus, in order to meet the needs of the present energy demand without compromising the ability of future generations to meet their needs and better protect our environment, renewable energy and green energy technologies need to be greatly developed and applied. Energy sources that are environmentally friendly and non-polluting include geothermal, wind, solar, and hydro are often considered “green” because they are perceived to lower carbon emissions and create less pollution.Among those “green energy sources”, steam energy is an important green energy and can be used as a renewable energy technology. Currently, over 45% of all the fuel burned by U.S. manufactures is consumed to raise steam. Besides being used to heat raw materials and treat semi-finished products, the steam energy is also a power source for equipment, as well as for building heat and electricity generation. Many manufacturing facilities can recapture energy through the installation of more efficient steam equipment and running steam processes.Important industrial applications of steam system include steam engines and steam turbines, energy storage, electricity generation, and cogeneration. Recently, steam energy technology received more and more interests from both industry and research community. Numbers of new technologies and inventions have been developed on utilization of steam energy and steam systems. The Kansai Electric Power Company and Mitsubishi Heavy Industries developed an energy saving technology for flue gas carbon dioxide recovery and steam system in power plant by the chemical absorption method and presented an optimum steam system on the power station[1,2]. Wang et al.[3] discussed the using of steam in power regeneration by thermochemically converting Biomass to hydrogen via catalytic steam reforming and shift conversion of specific fractions. The hydrogen obtained through that approach yields as high as 85% of the stoichiometric value. A similar project of using steam reforming technique on production of hydrogen was conducted by Hirai et al. in Kansai University[4]. It was also proved that producing hydrogen from ethanol steam reforming would not only be environmentally friendly but also would open new opportunities for utilization of renewable resources, which are globally available[5].Steam systems are a part of almost every major industrial process today. Thirty-seven percent of the fossil fuel burned in US industry is burned to produce steam[6]. Because of the important applications of steam energy technologies and steam systems in modern industry, we decided to establish an enhanced Steam Lab in UL Lafayette and use that facility to perform a detailed analysis of boiler energy thereby establishing baseline energy consumption for steam systems. Based on the analysis results, potential energy and cost saving measures can be presented for the steam system in order to achieve the objective of saving 2.5% annually in energy intensity among Louisiana’s industrial facilities. Another beneficiary of this Steam Lab will be the engineering program in UL Lafayette. From the beginning of engineering education, laboratories have had a central role in the education of engineers because in order to manipulate materials, energy, and information successfully, engineers must have knowledge of nature that goes beyond mere theory – knowledge that is traditionally gained in educational laboratories[7]. On the other side, for engineering students, practical experimental activity in the laboratory is essential to the formation of their knowledge and capabilities[8]. Laboratories with well equipped facilities have been built and used for engineering education program in peer engineering colleges[9,10]. Similarly, the Steam Lab will also be actively incorporated into the Mechanical Engineering program in UL Lafayette and it is expected that our students will substantially benefit from that lab.
3. Steam Lab
A steam power laboratory was originally installed in the Southwestern Louisiana Institute (SLI, now University of Louisiana at Lafayette) College of Engineering shortly after World War II. It was designed specifically for educational use and incorporated the following features:• Two 30 kW 3600 rpm Westinghouse C20 Curtiss-stage steam turbines (Fig. 1)• Two 31.3 kV 3600 rpm 220 VAC 60 Hz 3-phase Westinghouse Type G generators• A 150 ft2 Westinghouse water-cooled surface condenser and condensate pump• A steam-driven noncondensables ejector and 5 ft2 after-condenser for vacuum operation• A 60 hp 1200 rpm 220 VAC 3-phase Westinghouse Type G synchronous motor• A water-cooled Midwest Dynamatic eddy-current dynamometer coupled to the synchronous motor• A 5 hp 200 VDC (maximum) Westinghouse motor-generator set to provide DC field excitation to the AC generators and dynamometer• A 12.5 ft2 closed shell-and-tube feed water heater and 10 ft2 feed water cooler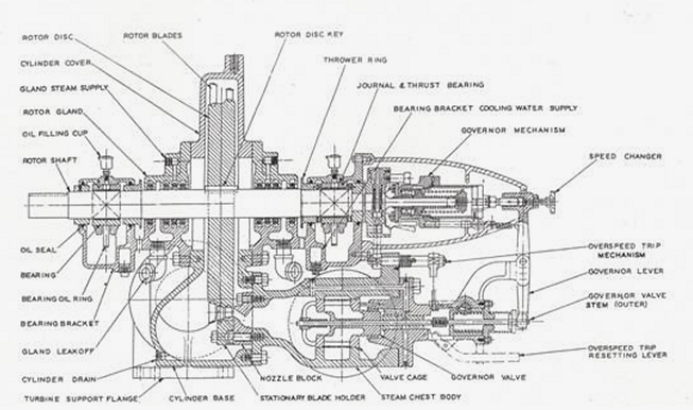 | Figure 1. Westinghouse C-20 Curtis-stage steam turbine |
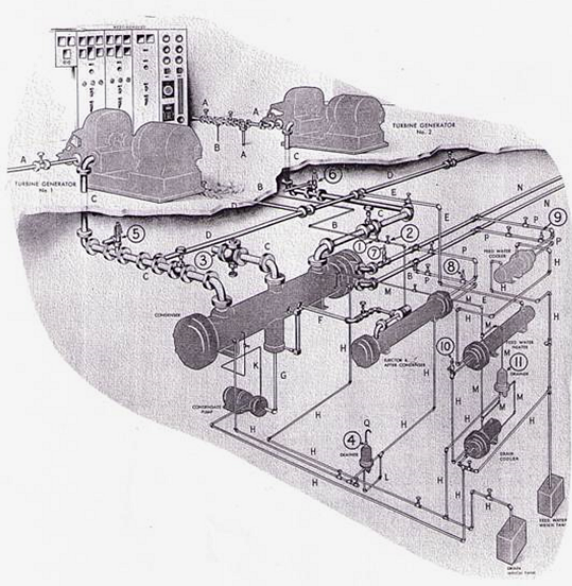 | Figure 2. Original Westinghouse 50 kW laboratory power plant layout |
The turbines were rated for 125 psig saturated steam at the inlet and a range of 25 in. Hg vacuum to 50 psig exhaust. Each turbine-generator set could be operated individually or in parallel with the generators synchronized. In addition, using a steam pressure regulator between the turbines, they could be operated as a “single” turbine with high- and low-pressure stages. Power generated in all operating modes was delivered to the synchronous motor and dissipated via the dynamometer. The surface condenser could be operated at atmospheric pressure or under vacuum using the steam-driven ejector; vacuum as low as 27 in. Hg could be maintained once-through city water; means of independently collecting and weighing the condensate from the main condenser and after-condenser were provided. The feed water heater and cooler were intended for demonstration and independent student testing and were not part of the power system steam circuit. The original layout at SLI is shown in Fig. 2.Since many campuses at the time had utility steam available for heating and other purposes, Westinghouse did not normally provide the boiler. In late 1990’s a 150 BHP circulatic boiler with more modern controls was installed in the laboratory. Fig. 3 shows a typical vapor power “Circulatic” boiler, which is a forced recirculation watertube boiler that uses a drum as a steam separator and a reservoir of water to supply the coils.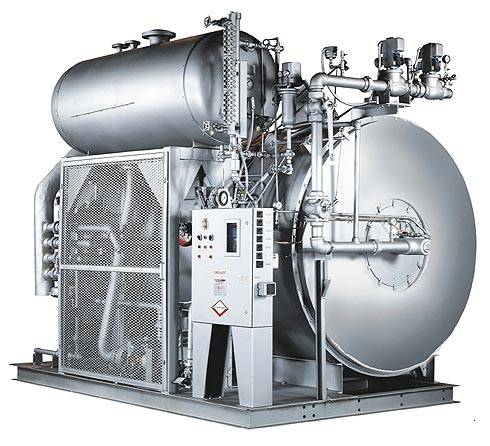 | Figure 3. Vapor power international “circulatic” boiler[11] |
In renovating this lab, a duct which provides outside combustion air to the fan was added to the boiler in order to avoid using indoor (air conditioned) air, which would potentially impact the environmental control of the building. The circulatic boiler itself also underwent refurbishment and is fully operational. Because of funding limitations, only one of the Wesginghouse C-20 turbines along with the surface condenser (with vacuum provisions) was installed. Pipes were arranged so that steam can be directed either to the turbine for power experiments or to the condenser for boiler experiments independent of power production. A second turbine was retained for parts and display, which would be used for respective engineering classes. At present, there is no power generating or power dissipation capacity; a Kahn hydraulic dynamometer is being installed so that turbine performance can be measured. Bearing, gaskets, and packing in the steam pump were replaced and a stainless steel pan was added under the steam pump with drain lines. Several drain lines were also added from the boiler to the floor drains, the steam turbine, and the condenser. Moreover, besides the original condenser, a smaller condenser was newly added with incoming water lines and drain lines. The new condenser allows the main condenser to run under vacuum instead of atmospheric pressure, which is more efficient. Major equipments and facilities in this refurbished lab include a 150 BHP boiler, condenser, steam turbine and generator, dynamometer, and various other pumps, heat exchangers and fluid lines (Figs. 4-6).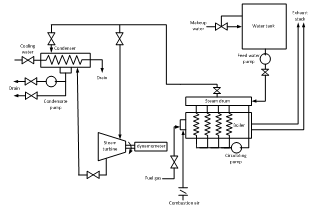 | Figure 4. Flow diagram of the Steam Lab |
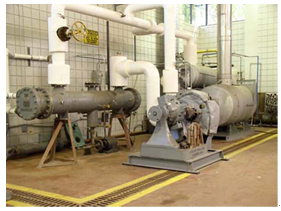 | Figure 5. Condenser, turbine, and boiler |
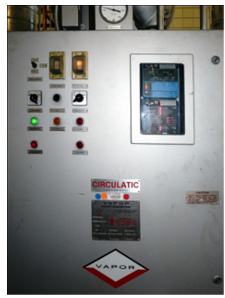 | Figure 6. Control panel |
After finishing the refurbishing work, the enhanced lab was run for testing. A procedural manual for starting, operating and shutting down the system was therefore developed. Key inputs of this lab include boiler feedwater, condensate returned, water treatment chemicals and air input. Key outputs include steam mass flow rate, steam pressure, steam quality, and combustion gas conditions.
4. Impacts on Industry
In this project, the project team established relationships with local and regional industrial companies by organizing a workshop on demonstrating the newly revitalized steam lab. By inviting industrial representatives from steam equipment companies to the workshop, valuable networking has been established, which was one primary goal the project. These relationships are proving advantageous to both industry and the Mechanical Engineering program in UL Lafayette. Through the workshop, the local and regional companies are now familiar with the equipment used in the laboratory classes and thus can make suggestions for further improving and expanding that lab so as to better simulate the real working environment of steam companies, such as purchasing steam ejectors and calorimeters. In the workshop, two companies have extended invitations for a site visit to view a transparent model of a steam power plant, and this should be very beneficial to mechanical engineering students.Future workshops are being planned, and more companies will be invited, through which long-term and stable partnerships between the institution and the steam industry will be established.
5. Impacts on Education
Besides broad impacts on industry, the Steam Lab will also substantially benefit the mechanical engineering program in UL Lafayette. Based on our current curriculum, the Steam Lab can directly benefit five courses and indirectly supplement six other courses. The courses that the lab can directly benefit include Instruments & Measurements, Energy Systems Lab, Energy Systems Analysis, Thermal Systems Design, and Engineering Projects. For the course Instruments & Measurements, the renovated lab can give students hands-on experiences on performing gas analyzer measurements and condensate measurements, using calorimeter, and calculating boiler horsepower and thermal efficiency. The course Energy Systems Lab can even be redesigned as a “premier” course with the using of this facility. From that course students can learn to start, operate and shut down the system; measure all operational parameters (pressure, temperature, condensate flow rate, etc.); calculate system performance (thermal efficiency, fuel/air ratio, condenser performance, steam quality, etc.); envision a full-up steam powerplant in operation, and get a feel for its design and operational aspects. A number of labs can be designed based on the listed activities and those labs as well as the showing of real power cycles can be implemented into a currently lecture-only course, Energy Systems Analysis, so that students can get better understanding of power plants, combustion process, heat exchangers, and system monitoring and simulation. Also, for the course Thermal Systems Design which does require a design project, this Steam Lab can be used to test the device designed and developed by the students. Moreover, the Steam Lab can serve as a base for students to work on their Capstone Senior Design Project, especially the thermal projects. The courses that this Steam Lab will indirectly supplement include the lecture-only courses Thermodynamics, Heat Transfer, Thermal Engineering, Advanced Fluid Mechanics, and the lecture/lab courses Engineering Design and Control Systems. In the course Thermodynamics, with the Steam Lab, students can view components of a real power plant even with a short system operational demo. Homework assignments can be devised based on the boiler system and its components. For the course Heat Transfer, hardware of the lab can be used to illustrate applications of conduction, convection and radiation. In the course Thermal Engineering, the Steam Lab provides a visualized system for combustion process. For the course Engineering Design which requires a design project, such project may involve a kinematic or mechanical design of an add-on component to the Steam Lab. Also, this Steam Lab can be used to demonstrate the performance of nozzles and educators for the course Advanced Fluid Mechanics as well as to synchronize the two turbines and perform other experiments in the course Control Systems.Overall, the addition of the Steam Lab will substantially enhance the mechanical engineering program and it has the potential to be improved and expanded in the future to be of greater benefit in classroom instruction for undergraduate and graduate students. Moreover, this facility is available for use by other departments and entities within the College of Engineering. Plans for incorporating this laboratory into the mechanical engineering curriculum are being developed.
6. Workshop
After finishing the renovation of the Steam Lab, a workshop was hosted for disseminating information on the utility and availability of this resource to the public and the technical community, local and regional steam industry, as well as the College of Engineering faculty at University of Louisiana. This workshop included open discussion by the attendees about company products and equipment which may potentially be added to the lab as the facility is further developed, and ideas for the facilities future use. Grant sponsors, local industry representatives, students, faculty and university personnel attended this workshop. The attendees highly complimented this project and extended their interests in establishing industry/government collaboration based on the renovated Steam Lab.
7. Conclusions
This paper introduces the process of renovating and refurbishing an old Mechanical Engineering Steam Lab and upgrading it to a fully operable condition. The key components of this laboratory as well as its working principle and capacity are presented. It is also shown that this enhanced Steam Lab can provide test-bed capability for local companies to devise measures to achieve the goals of saving energy and cost. Meanwhile, it can be used as an experimental laboratory that can benefit 11 courses in mechanical engineering curriculum. Furthermore, the equipment and facilities in this laboratory can also be shared by other engineering departments for curricular improvements. All objectives of this project are therefore achieved.
ACKNOWLEDGEMENTS
This project was sponsored by the U.S. Department of Energy (DoE) and the Louisiana Department of Natural Resources (DNR) as a part of the Save Energy Now project. The authors are grateful to the personnel in both organizations for their invaluable contributions to this work.
References
[1] | T. Mimura, S. Shimojo, T. Suda, M. Lijima, S. Mitsuoka, “Research and development on energy saving technology for flue gas carbon dioxide recovery and steam system in power plant”, Energy Conversion and Management, 36(6-9), 1995, 397-400. |
[2] | T. Mimura, H. Simayoshi, T. Suda, M. Lijima, S. Mitsuoka, “Development of energy saving technology for flue gas carbon dioxide recovery in power plant by chemical absorption method and steam system”, Energy Conversion and Management, 38(S1), 1997, S57-S62. |
[3] | D. Wang, S. Czernik, E. Chornet, “Production of hydrogen from biomass by catalytic steam reforming of fast pyrolysis oils”, Energy Fuels, 12(1), 1998, 19-24. |
[4] | T. Hirai, N. Ikenaga, T. Miyake, T. Suzuki, “Production of hydrogen by steam reforming of glycerin on ruthenium catalyst”, Energy Fuels, 19(4), 2005, 1761-1762. |
[5] | A. Haryanto, S. Fernando, N. Murali, S. Adhikari, “Current status of hydrogen production techniques by steam reforming of ethanol: a review”, Energy Fuels, 19(5), 2005, 2098-2106. |
[6] | D. Einstein, E. Worrell, M. Khrushch, “Steam systems in industry: energy use and energy efficiency improvement potentials”, Lawrence Berkeley National Laboratory, LBNL Paper LBNL-49081, 2001. |
[7] | L.D. Feisel, A.J. Rosa, “The role of the laboratory in undergraduate engineering education”, Journal of Engineering Education, January 2005, 121-130. |
[8] | N.S. Edward, “The role of laboratory work in engineering education: student and staff perceptions”, International Journal of Electrical Engineering Education, 2002, 39(1), 11-19. |
[9] | T.A. Fjeldly, M.S. Shur, H. Shen, T. Ytterdal, “Automated internet measurement laboratory (AIM-Lab) for engineering education”, 29th ASEE/IEEE Frontiers in Education Conference, 12a2-3, November 10-13, 1999, San Juan, Puerto Rico. |
[10] | J. Hlava, B. Sulc, J. Tamas, “A laboratory scale plant with hybrid dynamics and remote access via internet for control engineering education”, Proceedings of the 16th IFAC World Congress, 2005, Prague, Czech Republic. |
[11] | http://www.vaporpower.com/pages/boilers_cir_image.php |