S. H. Sengar 1, A. G. Mohod 1, Y. P. Khandetod 1, S. S.Patil 2, A. D. Chendake 2
1Deptt. of Electrical and Other Energy Sources, College of Agricultural Engineering and Technology,
2DBSKKV, Dapoli, 415712, Dist: Ratnagiri
Correspondence to: S. H. Sengar , Deptt. of Electrical and Other Energy Sources, College of Agricultural Engineering and Technology,.
Email: |  |
Copyright © 2012 Scientific & Academic Publishing. All Rights Reserved.
Abstract
Cashew nut shell, grass and rice husk were used as major biomass in the form of raw biomass, hydrolyzed biomass and carbonized biomass. Carbonized biomass was found suitable as compared to raw (as such) and hydrolyzed biomass for briquetted fuel. The briquettes were prepared on screw press extruder briquetting machine for different combinations of major biomass. The prepared briquettes after sun drying were subjected to various tests for assessing the quality of fuel. The suitability of briquetted fuel as domestic fuel was studied with standard water boiling test. Cashew shell briquettes burnt with good flame in cook stove and observed 15.5 per cent thermal efficiency. Better results in cashew shell briquettes related to calorific value, shattering indices test, tumbling test, degree of densification, energy density ratio, resistance to water penetration and water boiling test as compared to grass and rice husk briquettes were observed. Calorific value was found more in cashew shell briquetted fuel as 5154.58 kcal/kg. Net Present Value of cashew shell, grass and rice husk briquettes were 1935370.8, 2256434.38 and 631948.8 respectively. Pay back period for cashew shell, grass, rice husk briquettes were 8.1, 7.56 and 29.35 months respectively. Benefit Cost Ratio for cashew shell, grass, and rice husk briquettes were 2.8, 2.93 and 1.51 respectively.
Keywords:
Screw Extruder, Proximate Analysis, Bulk Density, Shattering Indices
Cite this paper:
S. H. Sengar , A. G. Mohod , Y. P. Khandetod , S. S.Patil , A. D. Chendake , "Performance of Briquetting Machine for Briquette Fuel", International Journal of Energy Engineering, Vol. 2 No. 1, 2012, pp. 28-34. doi: 10.5923/j.ijee.20120201.05.
1. Introduction
India produces nearly 350 million tonnes of agricultural waste per year (Naidu, 1999). It has been estimated that 110-150 million tonnes crop residues is surplus to its present utilization as a cattle feed, constructional and industrial raw material and as industrial fuel. Due to their heterogeneous nature, biomass material possesses inherently low bulk densities and thus it is difficult to efficiently handle large quantities of most feedstock. Therefore, large expenses are incurred during material handling, transportation, storage etc. Transportation had the 2nd highest cost by considering all factors, when the biomass power plant was run at full capacity (Kumar et al.2003). It is noted that transportation cost will increase with increasing power plant size. In order to combat the negative handling aspects of bulk biomass, densification is often required. If such crop residues are converted into briquettes they can provide huge and reliable source of feedstock for thermo chemical conversion (Anonymous, 2002). Apart from the problems of transportation, storage, and handling, the direct burning of loose biomass in conventional grates is associated with very low thermal efficiency and widespread air pollution (Grover and Mishra, 1996). In India total area under cashew nut cultiva-tion is 7,20,000 ha of which 76,270 ha are productive producing 4,50,000 MT of cashew. On an average shell makes 50 % of weight of nut while CNSL makes 15 to 30 per cent of shell production of cashew nut shells may be estimated to 2,25,000 MT from available statistics (Raina &Kulkarni, 2005). The CNSL removed, deoiled shells are abundantly available as a biomass waste. The waste biomass generated in cashew processing is utilized as a substitute to wood fuel or thrown as waste. This biomass requires much energy to make it in powder form for briquette. On such typical task, only the solution is to convert this biomass firstly into activated carbon form which is easier to make briquette from carbonization of cashew nut shell, grass, rice husk and hence keeping in view study is undertaken entitled “Characterization of biomass fuel in briquetted form”.
2. Materials and Methods
Material including deoiled cashew shell, rice husk, grass, glyricidia, saw dust and cow dung were collected from university experimental plots, in Dr. Balasaheb Sawant Konkan Krishi Vidyapeeth, Dapoli and their proximate analysis was carried out for raw, hydrolyzed and carbonized biomass. Selected biomasses were hydrolyzed for 2-3 month.The carbonized biomass samples were obtained by burning them in a kiln. A kiln made up of a cylindrical metal drum which accommoded about 100 kg of biomass. A kiln was closed with metal lid after loading with biomass as shown in Fig 12 (1). Little amount of biomass was used in the firing portion to ignite the kiln. Due to absence of air heat spreaded over a biomass and carbonized samples were obtained.Determination of moisture contentThe moisture content of raw biomass was determined by calculating the loss in weight of material using hot air oven dying method at 105℃ to 110℃ for one hour and up to constant weight loss. (Dara S.S.)Moisture content (% wb)
Where, w1 = weight of crucible, gw2 = weight of crucible + sample, gw3 = weight of crucible + sample, after heating, gDetermination of volatile matterThe dried sample left in the crucible was covered with a lid and placed in an electric furnace (muffle furnace), maintained at 925 ± 20℃ for 7 minutes. The crucible was cooled first in air, then inside a desiccator and weighed again. Loss in weight was reported as volatile matter on percentage basis. (Dara S.S.)Volatile matter (%) =
Where, w4 = weight of the empty crucible, gw5 = weight of empty crucible + sample, gw6 = weight of the crucible + sample after heating, gDetermination of ash contentThe residual sample in the crucible was heated without lid in a muffle furnace at 700 ± 50℃ for one half hour. The crucible was then taken out, cooled first in air, then in desiccators and weighed. Heating, cooling and weighing was repeated, till a constant weight obtained. The residue was reported as ash on percentage basis (Dara, 1999).Ash content (%) =
Where, w7 = weight of the empty crucible, gw8 = weight of empty crucible + sample, gw9 = weight of the crucible + ash, gFixed carbon determinationThe fixed carbon percentage was calculated by using following relationship.Percentage of fixed carbon = 100 - % of (moisture content+ volatile matter + ash)Process for briquette preparationThe carbonized cashew shell, rice husk and grass were used as major constituents for briquetting without any binding material. The various combinations of major constituents were tried in order to get briquettes of the desired quality. Different combinations as 50:25:25, 25:50:25 and 25:25:50 for cashew shell, rice husk and grass were made for observing the properties of briquettes. The known quantity of water was added in mixture using thumb rule for that the material should get bind by hand pressing after addition of water. The mixture was fed to briquetting machine and briquetting machine was operated at rated speed and power.Screw press extruder type briquetting machineThe screw press extruder type briquetting machine was used in the present study. It consists of driving motor, screw, die, and hopper and power transmission system. Pulley and belt were used to transmit power from motor to the screw. The raw material was fed to the hoppers, which convey it to screw by gravity. The material was pushed forward due to geometry of screw. As the material was pushed, it got compressed and binded material comes out of die in the form of briquettes. The detail technical specification of screw extruder type briquetting machine is shown in Table 1. The pictorial views of briquetting machine are shown in Fig 12 (4).Table 1. Technical specifications of the screw extruder type briquetting machine |
| Sr. no. | Particular | Specifications | 1 | Screw dimensions | No of turns = 4Screw pitch = 6 cmMaximum diameter of screw = 9 cmMinimum diameter of screw = 6 cm | 2 | Die dimensions | No of exit tubes = 3Diameter of exit tube = 2.5 cmLength of exit tube = 4 cm | 3 | Voltmeter | Analog with range = 0 to 300V | 4 | Ammeter | Analog with range = 0 to 30 A | 5 | Pulley and belt | Diameter of driven pulley = 26 cmDiameter of driving pulley = 9 cmBelt type V-belt | 6 | Motor | Single phase induction motorPower = 1HpSpeed = 1425 rpm | 7 | Overall dimensions | Overall length of machine = 31 cmOverall width of machine = 31 cmOverall height of machine = 62 cm |
|
|
3. Analysis of briquetted fuel
Physical properties of briquettesThe physical properties of briquettes determined as moisture content as produced, overall length, diameter of briquettes, density of briquettes, shatter resistance, tumbling resistance, resistance to water penetration. Bulk DensityWater displacement method was used to measure the volume of individual briquette. The briquettes were coated with wax, in order to prevent any water absorption during merging process. Each briquette was weighed and then coated with wax as shown in Fig12 (7). The wax coated briquettes were weighed and then submerged into water in suspension position and weight of displaced water was measured and recorded as the volume of the wax briquettes as shown in Plate 8. The volume of each briquette was calculated by subtracting the volume of coating wax from the volume of wax briquettes. The volume of coating wax was obtained by dividing its weight of the wax obtained by subtracting original weight of briquette from the weight of wax briquette by its volume. (Tayade, 2009)Shatter indicesShatter indices were used for determining the hardness of briquettes. The briquette with known weight and length was dropped on RCC floor and concrete floor from the height of one meter. The weight of disintegrated briquette and its size was noted down. The percent loss of material was calculated. The shatter resistance of the briquettes was calculated by using following formula (Ghorpade, 2006).Percent weight loss =
% Shatter resistance = 100 - % weight lossWhere,w1 = Weight of briquette before shatteringw2 = Weight of briquette after shatteringTumbling testTumbling test was used for testing the durability of briquetted fuel. The cuboid formed by angle iron frame having dimensions of 30×30×45 cm and fixed over hollow shaft diagonally was used to conduct the tumbling test. The sample of briquettes was put inside and cuboid is rotated for15 minute. After 15 minutes of tumbling action the briquette was taken out weighed and percent loss was calculated by using formula same that of shatter resistance (Ghorpade, 2006).Percent weight loss =
Durability Index = 100 - % weight lossWhere,w1 = Weight of briquette before tumbling, w2 = Weight of briquette after tumblingResistance to water penetrationIt is measured of percentage water absorbed by a briquette when immersed in water. Each briquette was immersed in 25 mm of water at 27°C for 30 seconds. The percent water gain was then calculated and recorded by using following formula. (Tayade, 2009) % Water gained by briquette =
Where,w1 = Initial weight of briquette w2 = Final weight of briquette % Resistance to water penetration = 100 - % water gainDegree of densificationDegree of densification is defined as percent increase in density of biomass due to briquetting. Degree of densification represents ability of material to get bind (Ghorpade, 2006).Energy density ratioThe energy density ratio is the ratio of energy content per unit volume of raw material and the energy content per unit volume of briquetted fuel. The energy density ratio of briquetted fuel was calculated by using following formula (Ghorpade, 2006(unpub.)).Thermal properties of briquettesThe important thermal properties of briquette include their calorific value, volatile matter, ash content, fixed carbon. The determination of volatile matter, ash content, fixed carbon involves same procedure as that of raw biomass material (Dara, 1999).Calorific valueThe calorific value of briquetted fuel was determined by using bomb calorimeter. The calorific value of briquetted fuel was determined by using following formula (Dara, 1999).Calorific value (Kcal/kg) =
Where,W = weight of water in calorimeter (kg),w = water equivalent of apparatus T1 = initial temperature of water (℃),T2 = final temperature of water (℃)X = weight of fuel sample taken (kg)The experimental set up of determination of calorific value using bomb calorimeter is shown in plate 9. The result was obtained for determination of calorific value of briquetted fuel for each treatment is depicted in Appendix G.Water boiling testVolume of the pot was measured and filled it 2/3 by water. Pot was kept on stove and covered with propped lid for minimizing the losses. Thermometer was fixed in central part of pot. Two kg of briquettes were measured and made into four parts for testing. Ambient temperature (T1) and initial temperature of water in a pot were measured. Setting time of fire was recorded after litting the fire. Final temperature of water after boiling was observed. Kept the fire continued by burning briquettes to heat water to vaporize until the given briquettes were used up. Quickly pot lid was removed and evaporation was continued for 20 minutes. Pot from the cook stoves was separated; cool it for 2 hours and volume of water of were measured (Rathore, 2008) thermal efficiency was calculated as follows.Where,Wi = initial volume of water, kg,Cp = specific heat of water, J/kg ℃T2 = final temperature of water, ℃,T1 = initial temperature of water, ℃Wi = initial volume of water taken, kg,Wf = final volume of water, kgL = Latent heat of water = 540 kcal/kg
4. Result and Discussions
Raw material characterizationRaw BiomassProximate analysis of as such raw biomass like moisture content, volatile matter, ash content and fixed carbon were carried out. Calorific value of raw material was determined using standard procedure.It is observed from Fig 1 that maximum fixed carbon percentage was obtained from cashew shell, where as in grass and rice husk was 19.24 per cent and 16.76 per cent respectively. Fig 2 shows that calorific value of raw cashew shell was 4683.59 kcal/kg, where as 3108.52 kcal/kg and 3267.03 kcal/kg was found in grass and rice husk material. Higher calorific value of cashew shell was observed.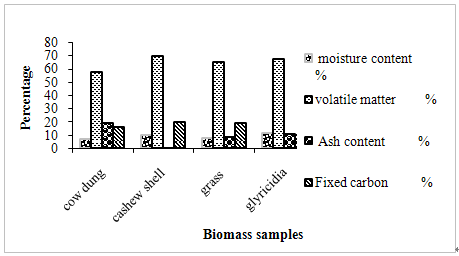 | Figure 1. Proximate analysis of raw biomass samples |
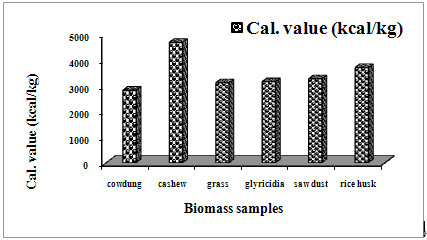 | Figure 2. Determination of calorific value of raw biomass Samples |
Hydrolyzed biomassSelected raw biomasses were hydrolyzed with water for two to three month in open condition. After two to three month properties of hydrolyzed biomass were observed. It is observed that moisture content varies in the range from 33.84 to 45.98 per cent range while fix carbon ranges from 5.37 to 15.32 per cent. Maximum carbon percent was obtained in saw dust. Fig 3 shows proximate analysis of hydrolyzed raw material. Hydrolyzed biomass were used in briquetting machine for briquetted fuel. Rice husk, cashew shell, grass, glyricidia, sawdust were not suitable for briquette preparation in machine because of its not proper hydrolyzed though it kept for three months. Only sawdust and dung cake after hydrolyzed were found suitable for briquette preparation under 0.5 hp briquetting machine.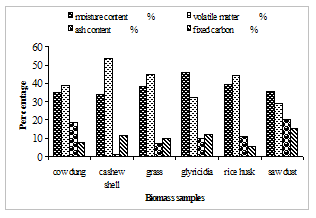 | Figure 3. Proximate analysis of hydrolyzed biomass samples |
Carbonized biomassRaw biomass was carbonized by using kiln and then used for briquetting. It is observed that carbonized material obtained as 26 per cent, 28 per cent and 31 per cent for cashew shell, grass and rice husk respectively. Observed carbonized material crushed and made into powder form. The results of proximate analysis and calorific value of carbonized biomass are depicted in Fig 4 and Fig 5 respectively.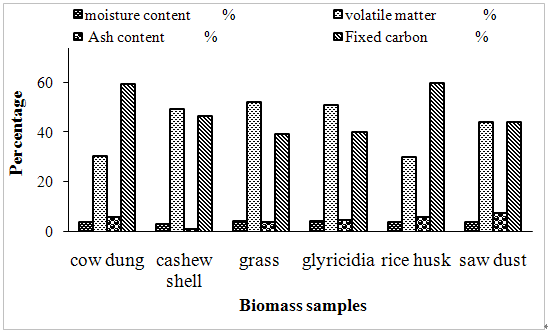 | Figure 4. Proximate analysis of carbonized raw material for briquetting |
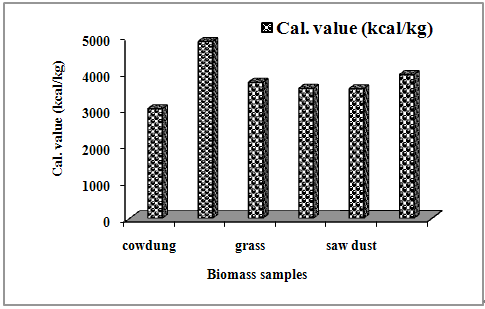 | Figure 5. Determination of calorific value of carbonized biomass Samples |
It is observed that the moisture content of carbonized biomass varied from 3.13 to 4.53 per cent for cow dung, cashew shell, grass, glyricidia, rice husk, saw dust respectively. The volatile matter observed in the range from 29.99 to 52.17 per cent where as fixed carbon content was ranges from 39.7 to 60.08 per cent. The calorific value of carbonized biomass ranges from 3021.10 to 4877.29 kcal/kg. The calorific value of deoiled cashew shell was found to be maximum as 4877.29 kcal/kg. Raw hydrolyzed biomass is suitable after crushing it, but it required large amount of energy to convert it into powder form. Considering an important of energy requirement raw biomass were carbonized and then it is used for briquetted fuel. In case of deoiled cashew shell little amount of energy is required to make into powder form.Performance evaluation of briquetting machinePerformance evaluation of briquetting machine includes operational parameters of raw material and operational parameters of machine. The performance of briquetting machine was carried out using three combinations of raw material as mentioned in previous chapter.Operational parameters of raw materialThe operational parameters of raw material for each combination during briquetting were recorded. The results obtained are depicted in Table 2.It is observed that the fresh briquette obtained was found to be maximum for combination 2 (0.8kg) of briquettes. The material output in the form of fresh briquettes was least in case of combination3 (0.5kg). Amount of unused material was highest for combination.3. (0.75kg) as of compared to least for combination 1(0.55kg). The moisture content of fresh briquettes coming out also ranged between 41.9 to 59.5 per cent, where as moisture content of dried briquettes ranged between 6.81 to 8.43 per cent.Table 2. Operational parameters of raw material |
| Particulars | Combinations C1 C2 C3 | Weight of sample taken (kg) | 0.5 | 0.5 | 0.5 | Water added in raw material (kg) | 0.7 | 1 | 0.75 | Total weight of raw material and water (kg) | 1.2 | 1.5 | 1.25 | Weight of unused material (kg) | 0.55 | 0.7 | 0.75 | Weight of fresh briquettes obtained (kg) | 0.65 | 0.8 | 0.5 | Moisture content of fresh briquettes (%) | 41.9 | 59.5 | 53.57 | Moisture content of dried briquettes (%) | 8.43 | 6.81 | 6.92 |
|
|
Operational parameters of briquetting machineThe operational parameters of briquetting machine were recorded during the productions of briquettes from each combination of raw material. The results obtained are depicted in Table .3.Table 3. Operational parameters of machine |
| Parameters | Combinations C1 C2 C3 | Voltage, V | 220 | 220 | 220 | Current, A | 3 | 3 | 3 | Power consumed, kW | 0.66 | 0.66 | 0.66 | Time required (Sec) | 65 | 70 | 80 | Capacity of machine (Kg/hr) | 36.11 | 41.14 | 22.5 | Energy consumption kcal/kg(kW-h/kg) | 15.72(0.0183) | 13.80(0.0161) | 25.23(0.0293) |
|
|
It was observed that there was a smooth operation of briquetting machine and no operational difficulties were observed during the operation The average capacity of briquetting machine was about 35 kg/hr with average energy consumption of about 18. Kcal/kg of briquetted fuel. The average time required for briquetting were varied from 65 to 80 seconds per 0.5 kg of raw material.Analysis of briquetted fuelThe various properties of briquetted fuel were tested to analyze the briquetted fuel as follows.Physical properties of briquettesThe physical properties of briquetted fuel after eight days of sun drying were recorded. The result obtain was depicted in Table 4.Table 4. Physical properties of briquettes |
| Properties of briquettes | C1 | C2 | C3 | Average length (cm) | 6.05 | 5.3 | 4.98 | Average diameter (cm) | 2.25 | 2.27 | 2.24 | Average weight (g) | 12.92 | 9.68 | 12.45 | Average volume (cm3) | 14.45 | 8.8 | 11.23 | Average density (g/ cc) | 0.895 | 1.105 | 1.109 |
|
|
It is observed that the average length of briquettes varied from 4.98cm to 6.05 cm. The average diameter of briquettes varied from 2.24 cm to 2.27cm. The average density of briquettes was maximum for combination 3 (1.109 g/cc)) as compared to combination 1 briquettes (0.895 g/cc).Calorific valueThe Calorific value of briquetted fuel shows that, the calorific value of combination 1 briquettes was found highest (5154.58 kcal/kg) and briquettes from combination 3 have least calorific value of 4188.64 kcal/kg depected in Fig 6.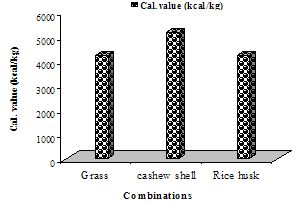 | Figure 6. Calorific value of briquetted fuel |
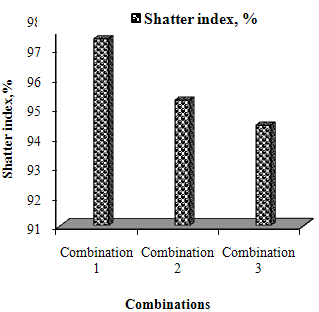 | Figure 7. Shatter indices of briquetted fuel |
Shatter indices of briquetted fuelIt is observed from Fig.7, out of three combinations the briquettes from combination have good shatter indices with retention of 97.33 per cent of its weight on concrete floor. Where as the percent retention of briquettes from combination 3 was about 94.4 per cent of its weight, which was least among all the combinations.Tumbler TestFrom the result of tumbling test it is observed that briquette from combination 2 have least durability (92.12 per cent) compared to highest durability index of 95.83 per cent for briquettes from combination 1 Shown in Fig.8. It may due to oil content in cashew shell raw material, which acts as its own binding properties.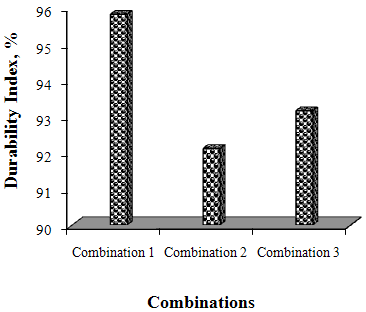 | Figure 8. Durability indices of briquetted fuel |
Degree of densificationThe degree of densification was found least for briquettes for combination 3 (25.17 per cent). The briquettes from combination 1 have highest degree of densification of 32.79 per cent depected in Fig. 9.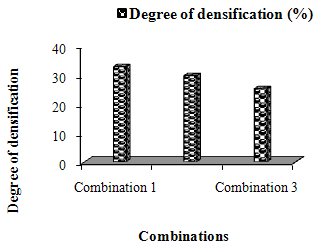 | Figure 9. Degree of densification of briquetted fuel |
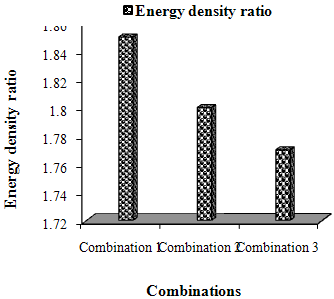 | Figure 10. Energy Density ratio of briquetted fuel |
Energy density ratioEnergy density ratio was observed to be maximum for combination 1 briquettes having energy density ratio of 1.9 followed by combination 2 and combination 3 briquettes having energy density ratio of 1.88 and 1.84 respectively. Least energy density ratio was reported for combination 3 briquettes as 1.84 Shown in Fig.10.Resistance to water penetrationAfter analysis the various properties of briquetted fuel from each combination, it is observed that the briquetted fuel from combination 1 had desirable good properties as compared to the briquetted fuel from other two combinations. The briquetted fuel from combination 1 required minimum energy for production and low water absorption properties shown in Fig.11. Their best shatter and durability indices showed that they have good shock and impact resistance and are good for handling and transportation. They also have good density ratio. Out of three, combination 1 briquettes observed highest calorific value, hence selected for thermal efficiency test on cooking stove.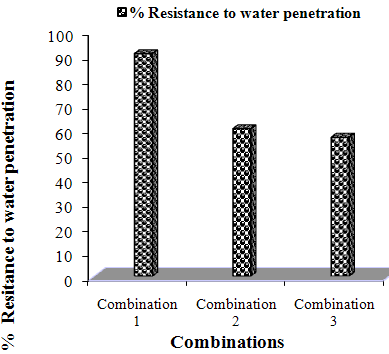 | Figure 11. Resistance to water penetration of briquettes |
Water boiling test of briquetted fuelBriquettes of combination 1 were selected for water boiling test for checking their suitability in domestic use as fuel. It is observed the briquettes were burnt completely in Vikram stove and gave uniform flame. Very little ash was left after burning. The thermal efficiency of Vikram cooking stove [Fig. 12 (8)] using Cashew shell briquetted fuel was found to be 15.5 per cent.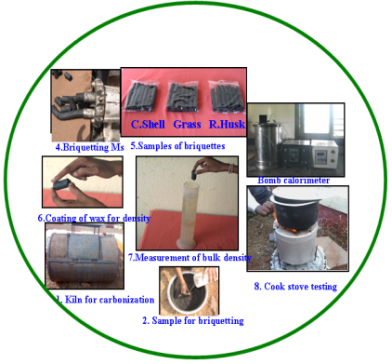 | Figure 12. Complete setup for briquettes preparation and testing |
5. Conclusions
Maximum percentage of fixed carbon (19.53 per cent) was obtained from raw cashew shell where as in grass and rice husk was 19.24 per cent and 16.76 per cent respectively. Carbonized biomass was found suitable as compared to as such and hydrolyzed biomass for briquetted fuel. Cashew shell briquettes gave better results for shattering indices test, tumbling test, water boiling test as compared to grass and rice husk briquettes. Calorific value was found more in cashew shell briquetted fuel as 5154.58 kcal/kg.
ACKNOWLEDGEMENTS
Authors are highly thankful to Department of Electrical and Other Energy Sources for providing all kind of facility to carry out the research work.
References
[1] | Anonymous, 2006. Waste to energy. ENVIS pondchery pollution control comity. Vol 2 (1) 1- 3 |
[2] | Babu, Y. D., 2001. Biomass Briquetting Technology: Past and RecentTechnology, Vol. 8 No. 3 155-156 |
[3] | Borekar, M. U., V.S. Sapkal,R.S. Sapkal, 2005. Manual of Conversion of Furnace Oil Fired Boiler to Briquette Fired External Furnace Boiler, Department of Chemical Technology, Amravati. Chin, O.C., K.M. Siddiqui, 2000. Characteristics of some Biomass Briquettes prepared under modest die pressures. Biomass and Bioenergy Vol. 18:223-228 |
[4] | Claub, B., 2002. Beitrag Zur komapaktigerung von unzerkleinertem halmgut for die energetische Nutzung. Contribution to the compacting of unchopped crop stalks for energetic use, Ph.D. thesis. Dara,S.S.,1999.A textbook on Experiments and Calculations in Engineering Chemistry,S. Chand publication, New Delhi,70-72 |
[5] | Eriksson, S., M. Prior, 1990. The Briquetting of Agricultural Wastes for Fuel, FAO Environment and Energy Paper 11, FAO, Rome |
[6] | Fel Fli, F.F., Uengo, C. A., Beaton, P. A. and Suwez, J.A., 2005. “Wood briquette torrifaction” in kopetz, H., (Ed) biomass for energy and industry, Wurzburg, germany: 1593-1595 |
[7] | FNR, 2000. Fachagentur Nach-wachsende Rohnstoffe E.V. Leitfaden Bioenergy. (Specialized Agency of Raw materials). Manual of bioenergy. Gagandeep, K.S., S.R.Sharma., A.K. Singh and V.K. Sehgal, 2002. Status of agro based briquetting Industry in Panjab. Agricultural Engineering Today.24 (3): 1-6 |
[8] | Grover, 1996. Biomass briquetting technology and practices. Regional Wood Energy Development Programme in Asia GCP/ RAS/154/Net Field Document No.46 |
[9] | Grover, P.D., Mishra S.K., 1996. Biomass Briquetting. Evaluation of technologies Vol. 7 No. 1 37-43 |
[10] | Ghorpade, S.S., A.P. Moule, 2006. Performance Evaluation of Deoiled Cashew Shell Waste for Fuel Properties in Briquetted Form. B.Tech. Thesis (unpub.),Dapoli, 15 |
[11] | Hamelinck, C. N., R.A. Suurs and A.P.Faaij,2003. International bioenergy transport costs and energy balance. ISBN 90-393-3508-7: 5-6 |
[12] | Marathe, S. A., J. P. Machaiah., B.K.Rao., M.D. Pednekar and Sudha V.Rao, 2002. Extension of shelf life of whole-wheat flour by gamma radiation. International journal of food science and technology.37: 163-168 |
[13] | Piyali Das and Anuradha Ganesh.2003. Bio-oil from pyrolysis of cashew nut shell-a near fuel. Biomass and Bioenergy. 25: 113 – 117 |
[14] | Piyali Das, T. Sreelatha and G. Anuradda, 2004.Bio-oil from pyrolysis of cashew nut shell-characterization and releated properties. Biomass and bioenergy. 27: 265 – 275 |
[15] | Raina, A., N. Kulkrni , 2005. Performance valuation of different methods of cashew nut shell liquid extraction. B. Tech.(Agril.engg.) thesis(unpublished), Dr.BSKKV, Dapoli |
[16] | Rathore, N.S.,N.L. Panwar,2008.Renewable Energy Theory and Practice, Himanshu Publication, New delhi,273 |
[17] | Singh, R.N., U. Jena, J.B. Patel and A.M.Sharma, 2006. Feasibility study of cashew nut shell as an open core gasifier feedstock. Renewable energy. 31: 481-487 |
[18] | Singh, A.K., A. D. Sharma, 2006. Farm waste utilization –New Avenue for agribusiness. Tayade ,S.R., 2009. Evaluation of different biomass briquettes making for gasifier. M.Tech. Thesis (unpub.), Akola,34-35 |
[19] | Tsamba, A. J., Yang Weihong and Wlodzimierz Blasiak.2006. pyrolysis characteristics and global kinetics of coconut and cashew nut shells. Fuel processing technology. 87:523-530 |
[20] | Vasudevan, R., 1993. Briquetting of Agricultural Residues. Problems and Imperatives, IREDA News, New Delhi, Vol. 4, No. 2 |
[21] | Wamukonya, L., B. Jenkins, 1995. Durability and relaxation of sawdust and wheat straw briquettes as possible fuels for Kenya; biomass and Bioenergy Vol 8 (3): 175-179 |
[22] | Wilaipan, P., 2006. Physical characteristics of maize cob briquette and moderate die pressure, American J. Appl. Sci. vol4 (12) |