Irena Cosic, Alexandra Lazar, Drasko Cosic
R&I, AMALNA Consulting, Black Rock, Australia
Correspondence to: Irena Cosic, R&I, AMALNA Consulting, Black Rock, Australia.
Email: |  |
Copyright © 2024 The Author(s). Published by Scientific & Academic Publishing.
This work is licensed under the Creative Commons Attribution International License (CC BY).
http://creativecommons.org/licenses/by/4.0/

Abstract
To solve problems with charging of electric vehicles including limited driving range, not enough charging places, long charging times, etc, there is growing interest in technologies that allow electric vehicles to recharge while driving. The innovative technology based on induction from power lines is introduced here. Our previous research on induction of voltage in conductive vires from Earth’s magnetic field only, is extended here with measurements within suburban area, where mostly 50Hz radiation is dominant due to power lines, with the aim to investigate the possibility of recharging electric vehicles’s batteries, while vehicle is moving. The experiments have been done with simplified model of wires and due to fact that induced voltage is proportional to number of wires, the model has been extended with calculations of possible induced voltage for bigger models. It has been found here that the model of reasonable size and number of wires could be used for recharging batteries of electric vehicles through electromagnetic induction, while the vehicle is moving in urban areas with dominant 50Hz radiation. Proposed technology is simple, inexpensive and widely applicable, and it is completely different to already proposed inductive recharging technologies, as it would use already existing power lines networks, rather than requiring building of additional road infrastructure.
Keywords:
Electromagnetic induction, Battery recharging, Electric vehicles
Cite this paper: Irena Cosic, Alexandra Lazar, Drasko Cosic, Simple and Inexpensive Technology for Recharging of Electric Vehicle while Vehicle is Moving, International Journal of Electromagnetics and Applications, Vol. 13 No. 1, 2024, pp. 10-13. doi: 10.5923/j.ijea.20241301.02.
1. Introduction
The modern life is fully dependable on transport, but still mostly based on vehicles running on combustion engines, which due to pollution are quickly becoming outdated. Thus, petrol or diesel vehicles are being quickly replaced by fully electric vehicles (EVs), which have zero tailpipe emissions and are much better for the environment. The main benefit of electric vehicles is pollution reduction, but also electric vehicles produce less noise, are easier to drive and much easier to maintain as electric motors have simpler construction without burning elements.One of the concerns is that electricity being used for running electric vehicles is still mainly produced by fossil fuels. However, this is changing now in favour of renewable energy [1]. On the other hand, the main problem with EVs is limited driving range and charging availabilities. Although driving range is increasing with new models of EVs, it is still a question if there are enough and well-placed charging stations within the driving area. It is an advantage that initial charging can be done at home, but very often there is a need to drive a vehicle far from home and into the rural areas. This is even more relevant for countries like Australia, where distances are large and thus is very costly to have enough charging stations to cover such vast areas. A lack or slow introduction of charging stations has hindered broader use of EVs even the auto industry is moving fast toward electrification. Currently, electric vehicles (EVs) need to stop for recharging at specialised charging stations, and charging process can last from half an hour to several hours, depending on the charging speed and battery size. This charging process represents a huge waste of time for drivers, significantly slowing transport and consequently is increasing costs of transportation. To solve this problem, there is a growing interest in technologies that would allow EVs to recharge while driving. Such technologies could eliminate the need for regular stops at charging points and potentially increase the driving range of EVs. One of the possibilities to recharge electric vehicles while on the move is "dynamic wireless charging" or "inductive charging" technologies, which produce electricity to recharge a vehicle’s battery based on magnetic field induction from a charging infrastructure embedded in the road to a receiver installed in the undercarriage of the vehicle [2]. The wireless technology is currently undertaking research due to their reliable, convenient and efficient charging with minimum human interaction. In review paper [3] the comprehensive literature review is presented including “different types of magnetic coupler designs for both static and dynamic methods and compensation networks, power electronic circuits and architecture, shielding techniques, control systems, standards, and communication networks in stationary and dynamic wireless charging”. However, all these designs require huge infrastructure and coils built-in in the vehicle and thus even more promising, dynamic wireless charging is still in the developmental phase, but would be also very costly for longer distances and thus is not yet widely adopted [2].The first wireless electronic road in USA has been installed in Detroit allowing electric vehicles to charge up as they drive along at the cost of two million dollars per mile [4]. The question: is this really the future of transport?In addition, Sweden has pioneered electrified roads through several pilot projects, including the world's first temporary electric road [5]. Another such example has been made in Japan with wireless EVs recharging while driving with technology similar to wireless smartphone charging. The chargers embedded in the road apply an electrical current only after detecting a vehicle [6].Mentioned above technologies are very expensive and limited to a small number of city roads and can be implemented only for short distances. As such these technologies are not applicable for longer drives nor for rural areas and only very wealthy and small in area countries can afford it. Thus, it would be hugely beneficial to have a technology of recharging EV batteries while driving, which would be simple, inexpensive, and applicable in any area with power lines.Here, the novel technology for continuous recharging of electric vehicles while they are driving has been presented. This technology is simple, inexpensive, and widely applicable. It is completely different to already proposed inductive recharging technologies and will take advantage of power lines that already exist in all urban areas.
2. Methods
This paper is a continuation of our previous research [7], where induction of voltage, due to the Earth’s magnetic field only, in conductive wires mounted on the roof of the car while vehicle is moving, has been investigated. Within this previous research the following has been shown:1. Electromagnetic field is indeed induced in conductive wires when they are cutting lines of the Earth’s magnetic field. 2. Voltage of this induced electromagnetic field is proportional to the speed of the vehicle.3. This electromagnetic field is proportional to the number of wires used.However, with the Earth’s magnetic field present only, the induced voltage is extremely low, and it would require a large number of wires to produce voltage that can be sufficient for recharging batteries. In addition, it is extremely unusual to drive electric vehicle in areas with only the Earth’s magnetic field present. The most usual situation is to drive electric vehicle within urban areas, where there is a variety of electromagnetic radiation present, mostly from 50Hz power supply, but also from microwave communications, TV, radio, etc. Such radiation is anyway induced in metal elements of electric vehicle, usually producing Eddy’s currents and as such this energy is wasted [7]. It has been proposed here that voltage induction in the wires could be enough for charging batteries in electric vehicles, while the vehicle is moving through area with electromagnetic radiation present. To prove this idea, the measurements within a suburban area, where mostly 50Hz radiation is present due to power lines, has been done. In such an urban setting, much higher voltage induction is expected and thus the experiments with simpler and smaller model of wires are possible. Results from these measurements could be applicable even for electric bicycles that are becoming more prevalent in urban areas. With the previously obtained knowledge [7], that induced voltage is proportional to the number of wires and speed of the vehicle, it would be easy to then extend these measurement results for bigger models and faster driving. For this experiment a simplified model of parallel wires mounted on an electric tricycle has been designed in form of the panel with 120 wires, 40cm long, mounted on the frame of 40x30cm, as presented in Figure 1.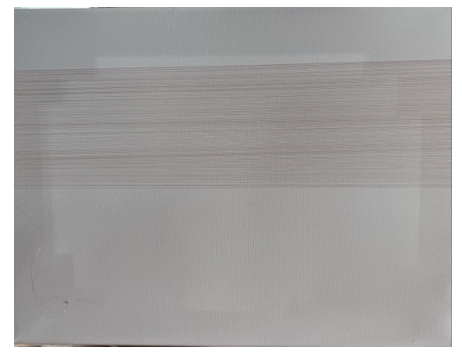 | Figure 1. Panel with 120 wires, 40cm long, mounted on the frame of 40x30cm |
This panel was mounted on the tricycle with 40cm long wires perpendicular to the movement of the tricycle and connected to DS213 oscilloscope, as presented in Figures 2a/b.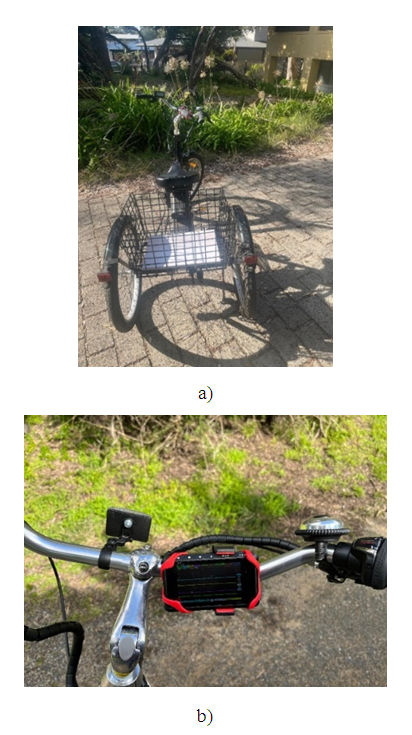 | Figure 2. (a) Simplified model of wires mounted on the tricycle with 40cm long wires perpendicular to the movement of the tricycle. (b) DS213 oscilloscope mounted on the handle of the tricycle |
The measurements have been done while the tricycle was moving along the suburban street with overhead power lines. The velocity of the tricycle was about 15km/h. The induction voltage has been measured by standard DS213 oscilloscope with voltage range of 0.5V per square on the oscilloscope screen. The oscilloscope was set to record for 200mS per screen and to present 50Hz frequency, as it is the most prevalent radiation causing induction in the wires within the model. These DS213 oscilloscope settings are presented in Figure 3. | Figure 3. Detailed settings on the screen of DS213 oscilloscope |
3. Results and Discussion
In the experiment explained above the measured induced voltage recorded on the screen of DS213 oscilloscope is presented in Figure 4. The blue line A is the voltage recorded on the one terminal of the model with wires, while the yellow line B is the voltage recorded on the other terminal of the same model. The purple line is the sum of voltage A and inverted voltage B, and as such is the basis for further rectification. 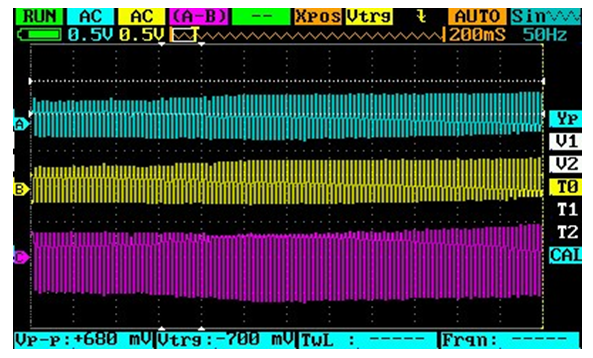 | Figure 4. Induced voltage recorded on the screen of DS213 oscilloscope. The oscilloscope was set to record 200mS per screen and to present 50Hz frequency. The blue line A is the voltage recorded on the one terminal of the model with wires, while the yellow line B is the voltage recorded on the other terminal of the same model. The purple line is the sum of voltage A and inverted voltage B, and as such is the basis for further rectification |
From Figure 4 and highlighted detail of pick-to-pick value presented in Figure 5, it can be observed that induced pick-to-pick voltage is 680mV (0.68V). This voltage is too small to recharge batteries for any electric vehicle including cars, bicycles, etc. However, due to the previously obtained knowledge [7], that induced voltage is proportional to number of wires, length of the panel on which the wires are mounted and speed of the vehicle, it would be easy to extend these measurement results for bigger model and faster driving. As the induced voltage is directly proportional to number of wires, as well as directly proportional to the length of panel with wires [7], the required voltage for recharging batteries can be achieved by increasing the number of wires and increasing the length of panel with wires.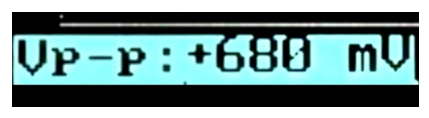 | Figure 5. Detailed pick-to-pick value |
In the experiment presented here, the panel with 120 copper wires, 40cm long mounted on the frame of 40x30cm has been used, as presented in Figure 1. As the induced voltage is directly proportional to the length and directly proportional to the number of mounted wires, for example the length of the wires can be increased three times to the length of 120cm (like in experiment in reference [7]) and the number of wires can be increased four times to 480 wires. In this case the expected pick-to-pick induced voltage could be twelve times higher to the value of around 8V. This induced voltage would be 50Hz AC voltage due mostly to induction from power lines. For charging batteries, we need DC voltage, so for that conversion we can use formula:
.Using this conversion, our example voltage of 8Vac pick-to-pick would become voltage of 5.7Vdc. This induced voltage, after resistance adjustments, would be enough for recharging one cell of different lithium batteries, which would generally need about 3.65Vdc to be recharged. For recharging more cells, more panels are required. This technology could be easily built in within the frame of vehicle, so the number of wires and panels should not be an issue. Have in mind that this example has been calculated for vehicle velocity of 15km/h (as per experimental measurements) and with increased speed the induced voltage would be proportionally higher.
4. Conclusions
Even with the huge benefit in pollution reduction, the revolution of electric vehicles is still mostly hindered by problems with their battery charging, which includes limited driving range, not enough charging places and long charging times. To solve these problems there is growing interest in technologies that would allow EVs to recharge while driving. The novel, simple, inexpensive, and widely applicable technology based on induction from power lines into wires mounted on vehicle has been presented here. This technology could possibly enable continuous recharging of electric vehicles while they are driving. The concept has been experimentally tested here with the simplified model and results have been projected through calculations to bigger model, which could induce feasible voltage for recharging electric vehicle batteries while vehicle is moving. The proposal here is completely different to already proposed inductive recharging technologies [3-6] and will take advantage of power lines that already exist in all urban areas. This wires-based technology is simple, inexpensive, and widely applicable. It is completely different to already proposed inductive recharging technologies, as it would use already existing power lines networks, rather than requiring building of additional road infrastructure.The final adjustment of this technology needs to be done by electric vehicle industry for different requirements for recharging different electric vehicle batteries.
ACKNOWLEDGEMENTS
The authors would like to thank Miss Amy Cosic for proofreading this manuscript.
References
[1] | Holland SP, Mansur ET, Muller NZ, Yates AJ: Are There Environmental Benefits from Driving Electric Vehicles? The Importance of Local Factors. American Economic Review, 2016, 106(12), 3700-3729, doi: 10.1257/aer.20150897. |
[2] | Gray F: Are EVs Capable of Charging While on the Move? nationwidevehiclecontracts.co.uk, 08/02/2024. |
[3] | Mahesh A, Bhatiraja C, Mihet-Popa L: Review on Inductive Wireless Power Transfer Charging for Electric Vehicles – A Review. IEEE Access, 2021, 99, doi: 10.1109/ACCESS.2021.3116678. |
[4] | Paris M. Wireless Charging: The Roads where Electric Vehicles Never Need to Plug-in. BBC, 31 January 2024. |
[5] | Carbonaro G: Stelantis has run successful trial for an EV that can charge itself without having to stop. euronews.com, 24/06/2022. |
[6] | Sakurai Y: Wireless EV charging while driving enters first Japan road test. JST Technology, asia.nikkei.com, 17/10/2023. |
[7] | I. Cosic, A. Kamber, D. Cosic, “Is It Possible to Harvest Energy through Earth’s Magnetic Field Induction”, International Journal of Electromagnetics and Applications, 2023, vol. 12(1), pp. 1-4, doi: 10.5923/j.ijea.20231201.01. |