MD. Samsul Alam Dipu, Sam Anachh
Department of Civil Engineering, Mymensingh Engineering College, Mymensingh, Bangladesh (Graduate)
Correspondence to: Sam Anachh, Department of Civil Engineering, Mymensingh Engineering College, Mymensingh, Bangladesh (Graduate).
Email: |  |
Copyright © 2024 The Author(s). Published by Scientific & Academic Publishing.
This work is licensed under the Creative Commons Attribution International License (CC BY).
http://creativecommons.org/licenses/by/4.0/

Abstract
The findings and results of an experimental investigation into the impact of salt water on concrete's compressive strength are presented in this work. Both fresh and salt water were used to create the concrete cubes used in this investigation. The concrete mix originated with a water-to-cement ratio of 0.45 and an exact weight ratio of M-30 (1:1.89:2.69). Eight cubes were cast and cured in fresh water for the inquiry, whereas the remaining eight were cast and cured in salt water. In consistent weather conditions, each of these concrete blocks cured for 7, 14, 28, and 90 days, respectively. When concrete is mixed with freshwater, its average compressive strength ranges from 15.63 to 31.11 N/mm2, and when it is mixed with saltwater (35 g/l NaCl content), it ranges from 18.45 to 35.03 N/mm2.
Keywords:
Compressive strength, Concrete blocks, Fresh water, Salt water
Cite this paper: MD. Samsul Alam Dipu, Sam Anachh, Investigating the Impact of Salt Water on Concrete's Compressive Strength, International Journal of Construction Engineering and Management , Vol. 13 No. 1, 2024, pp. 1-4. doi: 10.5923/j.ijcem.20241301.01.
1. Introduction
In construction, concrete is an essential material, and how effectively the water is mixed is paramount. Water contaminants may have a big influence on how concrete sets, hardens, and gains strength. [1] This research examines how saltwater, often used in regions where fresh water is limited, affects the compressive strength of concrete. Water is an important component of concrete since it actively engages in the cement's chemical reaction. [2] When it comes to the preparation and development of concrete's strength, water quality is crucial. [3] Fresh water is pure and free of pollutants. Seawater has a high amount of sodium chloride. [4] Seawater is characterized by a high sodium chloride concentration. Only 2.5% of the world's water bodies are freshwater, with the rest being saltwater. [5]The additional quantities need to be taken into account when determining if the overall amount of impurities that might damage concrete is acceptable. There are several sites where one can find salt water. The primary source of these is the sea. The majority of ions found in salt water are sodium, potassium, magnesium, calcium, and chloride ions. The following salt percentages are given as the main salt components of salt water: 7.8% NaCl, 10.5% MgCl2, 5% MgSO4, 3.9% CaSO4, 2.3% K2SO4, and 0.3% KBr. [6] [7] It is evident from the facts above that sodium chloride predominates in saltwater by a wide margin. Seawater has an approximate salinity of 3.5% overall, with 78% of the dissolved solids being NaCl and 15% being MgCl2 and MgSO4. [6]The main focus of this paper is to explore the effect of water containing large quantities of sodium chlorides (like ocean water or water containing equivalent amount of sodium chloride) on concrete.
2. Materials & Methodology
2.1. Materials
Below are specifics on the different materials that were utilized in the study:Cement: Throughout the study project, all specimens were cast using Portland Pozzolana Cement (PPC) (ASTM Type I).Table 1. Properties of Cement 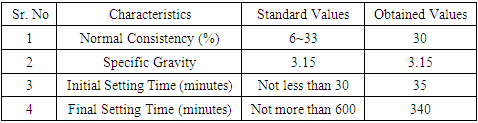 |
| |
|
Sand (fine aggregate): River sand, namely from Sylhet, is utilized; sieve analysis was done to see if it complies with BS criteria. According to the study, the fine aggregate's specific gravity and fineness modulus are both 2.64.Coarse Aggregate: Stone chips that are readily available locally, with a maximum size of 20 mm aggregate, specific gravity of 2.64, and fineness modulus of 7.51, were used.Water: Clean Tape water was used as fresh water for casting and curing.The primary source of salt water is the sea. The research uses marine water from Cox Bazar. The salinity of saltwater in the world's seas is typically 3.5% (35 g/L). [8] That indicates that there are around 35 grams of dissolved salts (mostly sodium (Na+) and chloride (Cl−) ions [9]) in every kilogram (about one liter by volume) of saltwater. A liter of salt water containing 35 grams of salt was used to produce eight of the cubes.
2.2. Methodology
Below are procedures which were followed:Mix design: Mix design followed to made concrete blocks was M30 with and exact weight ratio of (1:1.89:2.69).Material Testing: To ensure that all materials satisfy the BDS standard, properties of each and every one of them was tested in the laboratory. Like some initial testing, sieve analysis, setting time of the cement, absorption capacity test (shown in fig. 1 and 2) was carried out.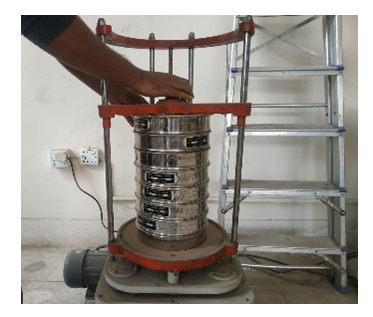 | Figure 1. Sieve Analysis |
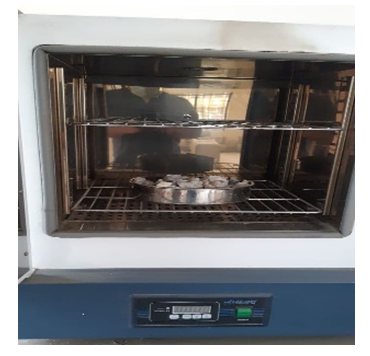 | Figure 2. Absorption Capacity Test |
Mixing of Concrete and Workability: The ingredients were combined according to the mix design in the proper ratio. The concrete was next tested for workability using a slump test on specimens prepared with either fresh or salt water separately. The results showed that the concrete exhibited true slump, indicating that it is appropriate for usage.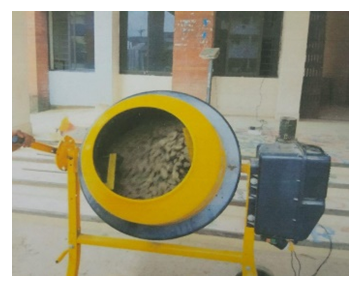 | Figure 3. Mixing |
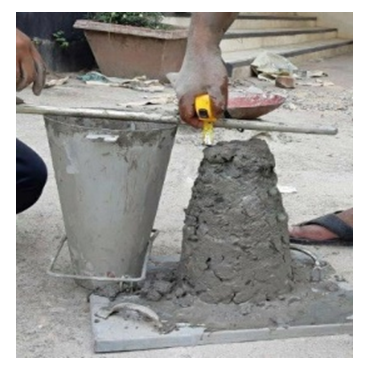 | Figure 4. Slump test |
Preparation of Specimen: To ensure that the concrete would not adhere to the cubes(150mm X 150mm X 150 mm) prior to casting, lubricant was used. This keeps the hardened concrete from adhering to the inside surface of the Mold. Then all specimens were filled with concrete mix and tamping rod-assisted compacted.8 of the cube was cast with fresh water and other 8 was cast with sea water. A smooth finish was achieved by leveling the surface. After then, the specimen was given a full day to set. After 24 hour, the specimens were disassembled using the required equipment.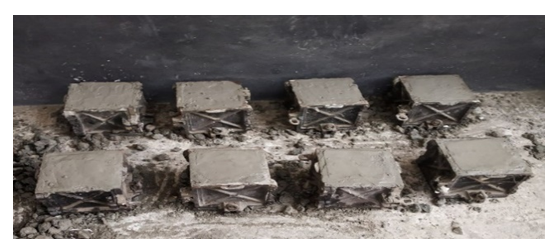 | Figure 5. Casting and molding |
Curing: From all the 8 cubes which were cast in freshwater, 4 of them were cured in fresh water, and the rest of the 4 cubes were cured in saltwater for 7,14,28, and 90 days respectively.The other 8 cubes which were cast in saltwater, 4 of them were cured in fresh water, and the rest of the 4 cubes were cured in saltwater for 7,14,28, and 90 days respectively.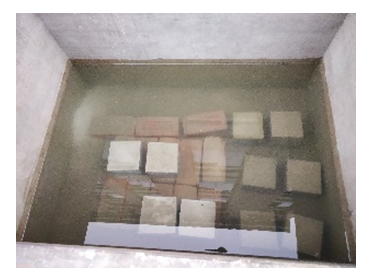 | Figure 6. Curing into Salt Water |
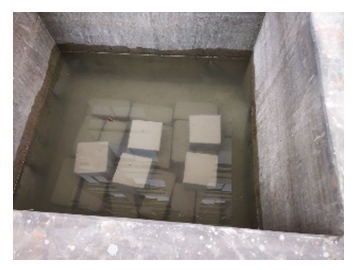 | Figure 7. Curing into Fresh Water |
Compressive Strength Test: In accordance with ASTM C39, the compressive strength was calculated. The specimen was examined after 7, 14, 28, 90, and 14 days of cure. In the compression test, a universal testing machine (UTM) with a loading rate of 2.4 KN/s was employed. The specimen taken from the compression machine was the maximum load, often known as the crushing load. The calculation of the compressive strength f'c involved dividing the crushing load by the test specimen's contact surface area.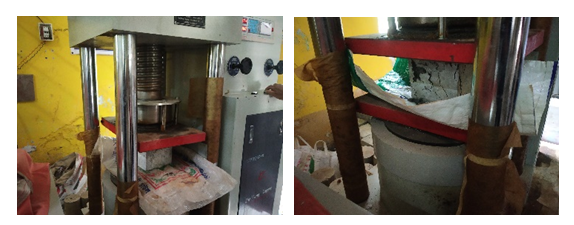 | Figure 8. Compressive Strength Testing |
3. Results
The outcomes of compressive strength test are as follows:In Table 2 the below annotations stand for:-Table 2. Results of Compressive Strength of Concrete using Fresh and Saltwater in both Mixing and Curing Stages 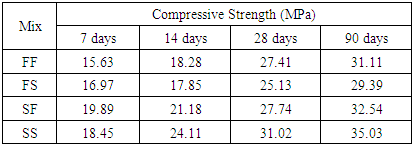 |
| |
|
FF:- concrete cast and cured with fresh water FS:- concrete cast with fresh water & cured with salt water SF:- concrete cast with salt water & cured with fresh water SS:- concrete cast and cured with salt waterThe graph obtain from the table data is given below-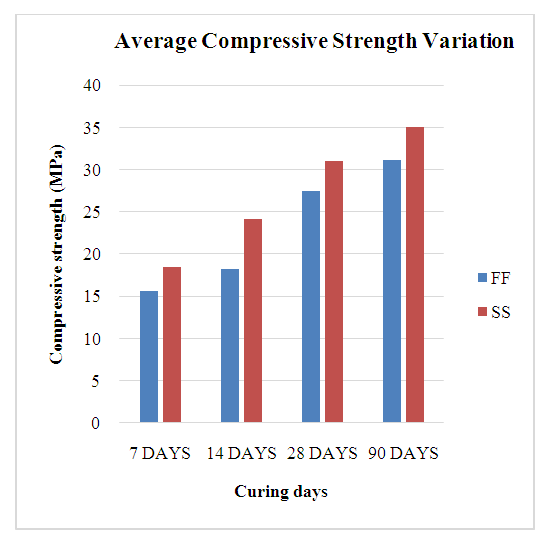 | Figure 9. Average Compressive Strength of Concrete. |
Efflorescence was seen on the surface of the concrete which were cast and cured in salt water: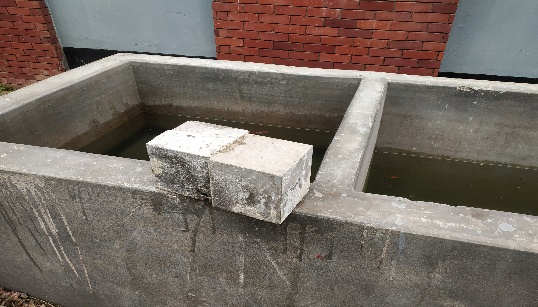 | Figure 10. Efflorescence |
4. Discussion and Conclusions
In this research work, the effect of salt water on the compressive strength of plain mass concrete had been investigated experimentally.The results in Table 2 and Figure 9 above show:The concrete designations SF, FS, and SS, respectively, exhibit a notable improvement in strength after 7 days, when compared to the FF control batches, which exhibit a lower strength at an earlier stage. Additionally, on the 14th day, every batch showed a rise in strength; however, the FF, SS, and SF batches showed an increase at a faster pace than the FS batches. All batches showed an increase in strength growth rate at day 28, however the SS batches' compressive strength was higher at that point than that of the control, or FF batches. Within 90 days, the batches' maximum strength was recorded, however more than 90% of that strength was already attained within 28 days.In long term efflorescence or whitish appearance of deposit salt formed on a specimen. Efflorescence in concrete can be considerable as it hampers the aesthetic appeal and potentially indicate underlying problems. Efflorescence by itself is not dangerous to the structure, but it may indicate that the concrete is too wet. More severe problems include freeze-thaw damage, corrosion of the steel reinforcement, and gradual deterioration of the concrete matrix might result from this moisture.The findings reveal that concrete cubes cast and cured in salt water exhibited a slight increase in strength, when is compared to those treated with fresh water. Compared to the cubes treated with salt water, the strength growth of the fresh water-exposed cubes was slower.
References
[1] | S. Maniyal and A. Patil, “An Experimental Study on Compressive Strength of Various Cement Concrete Under Sea Water,” Int J Sci Eng Res, vol. 6, no. 4, 2015, [Online]. Available: http://www.ijser.org. |
[2] | A. Vishwakarma, A. Rai, and A. Patel, “Effect of Salt Water on Compressive Strength, Flexural Strength and Durability of a Concrete,” International Research Journal of Engineering and Technology, 2020, [Online]. Available: www.irjet.net. |
[3] | O. M. Ojo, “Effect of Water Quality on Compressive Strength of Concrete,” European Scientific Journal ESJ, vol. 15, no. 12, Apr. 2019, doi: 10.19044/esj.2019.v15n12p172. |
[4] | O. S. A and E. E. B, “Effect of Sodium Chloride (NaCl) on Concrete Compressive Strength.” [Online]. Available: www.askthebuilder.com/B251. |
[5] | B. Bolaji and O. Abayomi MEng, “EFFECT OF SALT WATER ON CONCRETE USING BIDA NATURAL STONES AS COARSE AGGREGATE,” 2021. |
[6] | P. Tiwari, R. Chandak, and R. K. Yadav, “‘Effect Of Salt Water On Compressive Strength Of Concrete,’” 2014. [Online]. Available: www.ijera.com. |
[7] | O. A. Qasim, B. H. Maula, H. H. Moula, and S. H. Jassam, “Effect of Salinity on Concrete Properties,” in IOP Conference Series: Materials Science and Engineering, Institute of Physics Publishing, Mar. 2020. doi: 10.1088/1757-899X/745/1/012171. |
[8] | I. Asiwaju-Bello, O. Olalusi, and F. Olutoge, “Effect of Salt Water on the Compressive Strength of Ceramic Powder Concrete,” American Journal of Engineering Research (AJER), no. 6, pp. 158–163, 2017, [Online]. Available: www.ajer.org. |
[9] | A. E. Abalaka and Babalaga, “Effects of Sodium Chloride Solutions on Compressive Strength Development of Concrete Containing Rice Husk Ash,” 2011. |