Sampada Katekar, Namdeo A. Hedaoo
Department of Civil Engineering, COEP, Pune, India
Correspondence to: Namdeo A. Hedaoo, Department of Civil Engineering, COEP, Pune, India.
Email: |  |
Copyright © 2021 The Author(s). Published by Scientific & Academic Publishing.
This work is licensed under the Creative Commons Attribution International License (CC BY).
http://creativecommons.org/licenses/by/4.0/

Abstract
The mixture of aggregate, filler, and binder produces Cold Bituminous Emulsion Mixtures (CBEM). CBEM has many several environmental and cost-effective benefits. However, it offers poor early life properties besides achieving maximum strength it required a long curing period. In this experimental study, waste rice husk ash and ordinary Portland cement are used as substitutes for mineral filler with 0%, 1%, 2%, and 3%. The main objective of this study is to improve performance CBEM by combining Waste Rice Husk Ash (WRHA) and Ordinary Portland Cement (OPC). To evaluate enhancement in performance of CBEM, Retained Stability test, Tensile Strength Test, and Marshall Stability Test were conducted. The experimental results show that the tensile strength and Marshall stability of CBEM increased drastically by replacing mineral filler with waste rice husk ash and ordinary Portland cement. The moisture-induced damages are reduced due to the WRHA and OPC is added in the CBEM. As the tensile strength values and stability values of WRHA modified CBEM are more optimistic than OPC modified CBEM.
Keywords:
Cold bituminous emulsion mixtures (CBEM), Marshall stability test, Ordinary Portland cement (OPC), Waste Rice Husk Ash (WRHA), Tensile strength test
Cite this paper: Sampada Katekar, Namdeo A. Hedaoo, Experimental Study on the Reaction of Cold Bituminous Emulsion Mix with Waste Rice Husk Ash, International Journal of Construction Engineering and Management , Vol. 10 No. 2, 2021, pp. 25-30. doi: 10.5923/j.ijcem.20211002.01.
1. Introduction
This Cold bituminous emulsion mix (CBEM) is produced by mixing the materials known as aggregate, binder and filler. Due to the elimination of heating of binder and aggregate, the environmental, as well as cost-effective characteristics, can be increased by using cold mix technology [6]. There are also other advantages of the cold mix such as it works in humid condition and also it is beneficial for road construction in isolated and remote areas where the manufactured hot mix will be set before reaching on-site. But cold mix has offered some drawbacks such as low strength and high air-void content [4]. Besides, CBEM is not used as a structural layer since it takes an extensive curing time to achieve maximum strength. Previous studies have been shown that several additives were tried to enhance the performance of CBEM. Cement and hydrated lime are most commonly used as additives in the cold mix. This study shows the calculations of the mechanical properties of bituminous emulsion with 0% to 6% Portland cement, their test results are illustrated that there was an increase in mechanical properties and water damage resistance of cold mix by addition of cement [7]. Furthermore, they have suggested as the emulsion mixes modified with cement might be used for the structural pavement layer. However, the use of cement and lime increases the chances of increased production costs and environmental degradation [3]. Waste Rice husk is collected during the milling process. It is an agricultural waste residue obtained from the outer covering of rice grains. Combustion of rice husk in boiler results in Waste Rice Husk Ash (WRHA) which is generally considered as waste material. About 678 million tons of rice paddies are produced worldwide annually, which leads to approximately 150 million tons of waste rice husk per year and because of burning this quantity of rice husks, near about 38 million tons of WRHA produced. Since waste rice husk ash had no other use, it was normally disposed of as waste in landfills or water streams, harming the environment until it was known to be secondary cementitious material for concrete production. When WRHA as a pozzolanic material used in the cement and concrete industry, it gives many advantages such as improved durability properties and strength [5]. Based on the test results, suggested the use of WRHA as mineral filler in Hot Mix Asphalt (HMA) concrete. He found that the Marshall Stability of HMA mixture increased by substituting conventional mineral filler OPC with WRHA [1]. Hence, instead of mineral filler, the use of WRHA in CBEM is becoming active areas of research due to its water absorption ability and economic benefit [2]. This study aims to investigate the workability of using WRHA as a replacement for conventional mineral filler in CBEM to modify their properties. In the present work, WRHA is using as a replacement with different percentages ranging from 0 to 3% with an increment of 1% instead of conventional mineral filler. The enhancement in mechanical properties was accessed using the Marshall Stability test & Indirect tensile strength test. Besides resistance to moisture damage of mixes was determined by performing Retained stability test. In this study, various cold mixes were considered as shown in following Table 1.Table 1. Details of various mixes 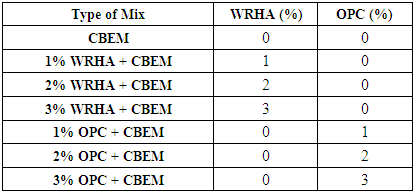 |
| |
|
2. Materials
2.1. Aggregate
In this study basalt type aggregate is used. Gradation of aggregate was adopted according to the specified by MORTH 2013 is as given in following Table 2 [15].Table 2. Aggregate gradation 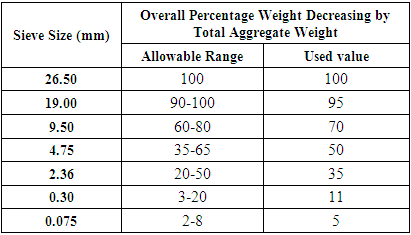 |
| |
|
Table 3 shows the properties of aggregate [11].Table 3. Properties of Aggregate 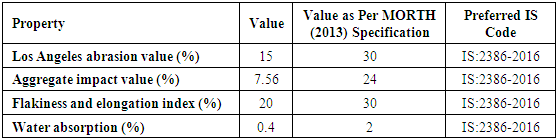 |
| |
|
2.2. Emulsion
Table 4 showing the test results of the emulsion [12,13].Table 4. Test results of emulsion 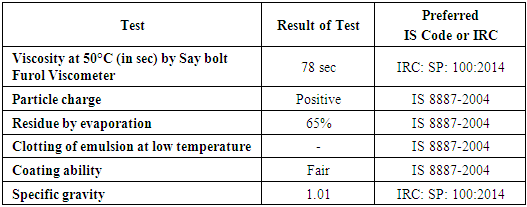 |
| |
|
The cationic emulsion used in this study. It has a positive particle charge test result. The effect of viscosity and residue is verified by an evaporation test, indicating that a medium grade of the emulsion was used in this experiment.
2.3. Additives
In the present study, two types of additives including Rice Husk Ash and Ordinary Portland Cement were used.
2.3.1. Ordinary Portland Cement (OPC)
In this study, OPC of 53 grade was used. The specific gravity of OPC is 3.10. Stone dust of specific gravity 2.62 was replaced with OPC in the range of 1-3% with increments of 1%.
2.3.2. Waste Rice Husk Ash (WRHA)
Waste Rice Husk ash was brought from a local authority situated in Pune, Maharashtra, India which is having a Specific gravity is 1.7. Stone dust was replaced with WRHA in different proportions, 1%, 2% and 3%. The chemical composition of WRHA is shown in following Table 5.Table 5. Chemical composition of WRHA 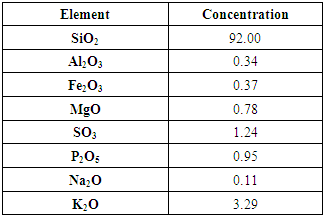 |
| |
|
3. Sample Preparation
The samples were prepared as per guidelines given in IRC: SP: 100-2014. Initially, specimen samples were prepared with an adequate quantity of water and various percentages of emulsion to evaluate the foremost emulsion content. For each emulsion content, mainly three samples were prepared. Optimum Emulsion specimens prepared and tested for Indirect tensile strength tests and Retained stability. An aggregate of different sizes is mixed to get aggregate gradation as specified in MoRTH (2013). To get the proper coating of emulsion on to aggregate, optimal water content was added to the mix. For the present study, the optimal water content was found to be 3%. Then emulsion was added in different proportions ranging from 7.5 to 9 percent with an increment of 0.5%. After mixing, for dehydration, the mixture was set under the fan for approximately 1-2 hr. Afterwards, this mixture was heated in the oven for 2 hrs. at 40°C temperature. After the completion of the heating process, the mixture is removed from the oven and placed into the Marshall mould along with the thin paper on the base plate. In the present study, compaction of the mixture was carried out with the help of a Marshall hammer by providing 50 blows on both faces. Then the prepared samples were extruded after 24 hrs and then for 72 hrs heated in the oven at 40°C temperature. Each emulsion content prepared the three samples.
4. Sample Testing
4.1. Marshall Stability Test
Marshall stability test is used to determine the Optimum Emulsion Material. Only the optimum emulsion material mix with 4% air voids was selected. This test was performed at 25°C as specified in IRC: SP: 100-2014 [13].
4.2. Retained Stability Test
Moisture damage in bituminous mixtures refers to the loss in strength and durability due to the presence of water. This test is used to evaluate resistance to moisture-induced damage of cold bituminous emulsion mixtures. This test performed as per AIMS No.14 (MS-14) -1989 [14].
4.3. Indirect Tensile Strength Test
To achieve the maximum tensile strength of mixtures the ‘Indirect tensile strength’ test is used. The test is performed under 25°C temperature as per the ASTM D 6931 – 2017 [9]. In this test, using two opposite loading strips, with a vertical diametrical plane the compressive load is applied to a specimen. The configured load develops uniform tensile stress ultimately causing failure of the specimen by splitting with the vertical diameter.
5. Results
5.1. Marshall Stability Test
The variation between the stability values of CBEM and emulsion content is shown in Graph 1.From Graph 1, it is observed that the stability value of mixtures including WRHA and OPC is greater than the control mix. WRHA particles react as reinforcing material in the mix which will affect increasing the stiffness.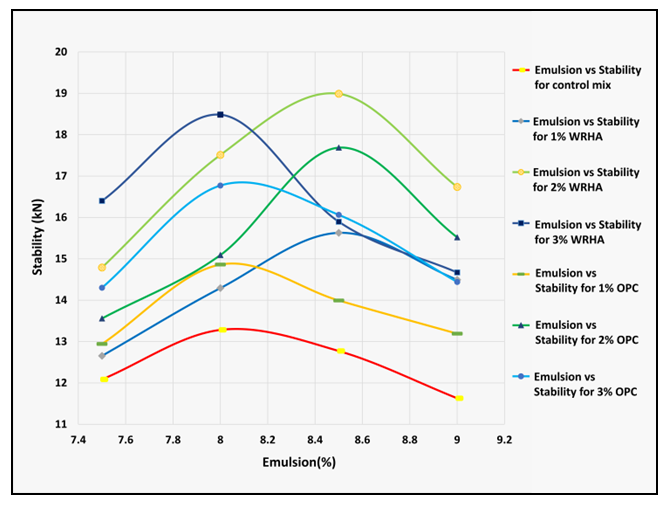 | Graph 1. Emulsion vs Stability for all mixes |
The variation of flow value of cold bituminous emulsion mixes at different emulsion content is shown in Graph 2.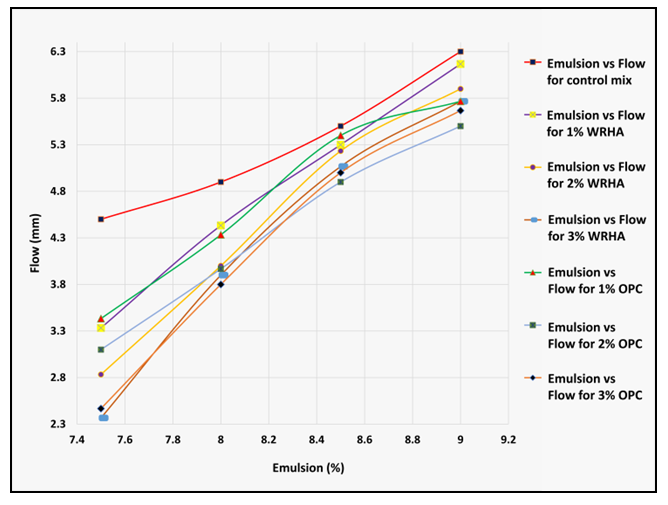 | Graph 2. Emulsion vs Flow for all mixes |
From Graph 2, it is illustrated that flow values of cold bituminous emulsion mix decrease slightly by the addition of WRHA and OPC. The shear strength and stiffness of the mix may increase due to non-spherical particles and as a result resistance to plastic flow increases.The following Table 6 shows the effects of the Optimum Emulsion Content (OEC) and Marshall stability tests.It shows that stability values of mixes with WRHA are greater than mixture with OPC. Both WRHA and OPC modified mixtures give maximum stability at 2% additive content.Table 6. Optimum Emulsion Content (OEC) and Marshall test result 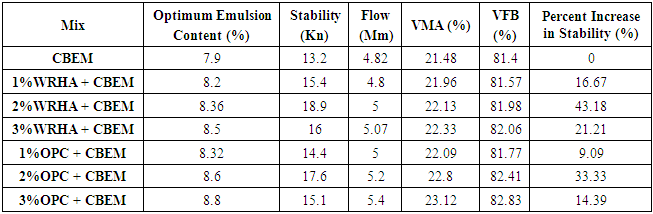 |
| |
|
5.2. Retained Stability Test
Graph 3 shows Marshall stability values of CBEM prepared with WRHA and OPC in both unconditioned stability and conditioned stability.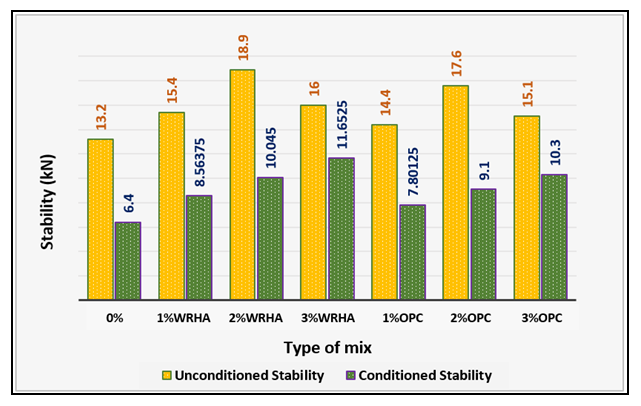 | Graph 3. Marshall stability values for unconditioned and conditioned specimens |
Obtained results of Retained stability ratios for various CBEM are shown in following Graph 4.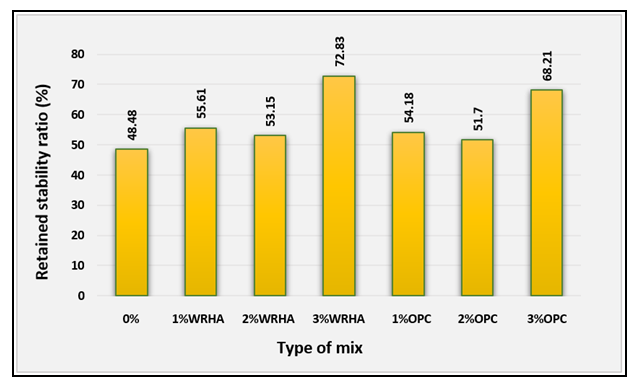 | Graph 4. Retained stability ratio of various CBEM |
As per MoRTH (2013), Retained stability value of more than 50% is recommended as the requirements for CBEM to resist moisture-induced damages. From Graph 4, it is observed that for the control mixture, the value is 48.48% and for both modified mixtures, the value is greater than 50% which support the need for an additive in CBEM to increase resistance to moisture-induced damages. It has also been reported that for all cold bituminous emulsion mixtures the stability value decreases with an irrespective type of additive. Modified CBEM adapt with 3% WRHA and 3% OPC have shown the Retained stability ratio has improved substantially.
5.3. Indirect Tensile Strength (ITS) Test
Graph 5 shows the result of an Indirect tensile strength test of various cold bituminous emulsion mixtures. | Graph 5. Effect of types and concentration of additives on ITS of CBEM |
From Graph 5, irrespective of the form of additive, both modified cold bituminous emulsion mixtures have observed higher tensile strength as compared to control mixtures. The additives present in CBEM strengthens the bond between aggregate and binder, resulting in higher tensile strength in the changed mixtures. The Indirect tensile strength of modified CBEM prepared with 3% WRHA and 3% OPC was significantly increased. However, WRHA modified mixtures have higher tensile strength as compared to the OPC modified mixtures.
5.4. Statistical Analysis
Based on results obtained from the mixture of optimum emulsion content, the analysis of ANOVA was considered. The significance level
= 0.05 was considered while performing ANOVA. The results of ANOVA are shown in Table 7. After several tests performed on CBEM with various WRHA percentages, it is observed that the pre-determined
- value is greater than the probability value (i.e., p-value). Hence, the combination of WRHA and CBEM with various percentage significantly improves the performance of CBEM. Table 7. ANOVA results (Compared with control mix) 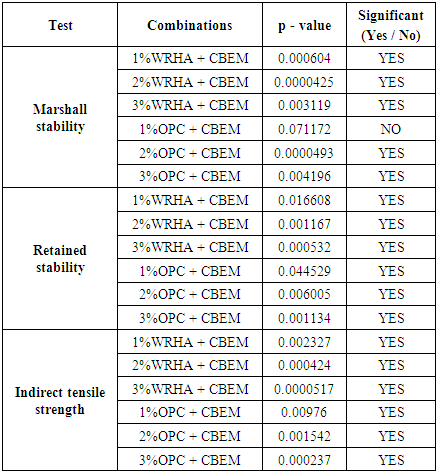 |
| |
|
It is an exception for Marshall stability of 1% OPC mix, similarly the different percentage of OPC of p - value is lower than 0.05 in different tests performed on mixtures. Hence, the incorporation of 1% of OPC to CBEM offered an insignificant effect on the Marshall Stability of CBEM.The results shown in [8] found that the performance of cold-mix bitumen is improved with the addition of cement. The test results show that the addition of 1-2% cement significantly improved the mechanical performance of the mixes and significantly accelerated their strength gain. As per the comparing results of the addition of 2% WRHA, it gives better performance than OPC and conventional mixes, so it the clear that the WRHA added mix improves the performance of CBEM.
5.5. Rate Analysis
• Rate analysis was carried out for pavement which is 1000m in length and 7.5m in width (2 lanes). The thickness of bituminous concrete is considered 50mm.• It is observed that waste rice husk ash modified mix is cost-effective as compared to OPC modified mix. The cost of WRHA modified mix is greater than control mix but the incorporation of WRHA in CBEM results in enhancement in their performance.Table 8. ANOVA results (Compared with control mix) 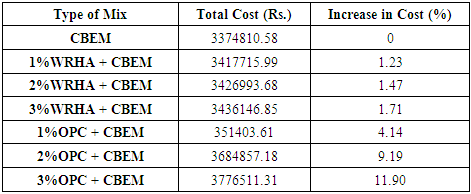 |
| |
|
As shown in Table 8, the percentage increase in the cost of WRHA modified CBEM is in the range of 1.23 to 1.71% and the cost of OPC modified CBEM is increased by 4.14 to 11.90%. Thus, WRHA modified CBEM is cost-effective than OPC modified CBEM.
6. Conclusions
As per comparison between previous research papers, it is found that the use of WRHA in CBEM improves the mechanical properties of mixes, it gives better performance than conventional mixes.As a result of the replacement of traditional mineral filler with WRHA and OPC, the marshal stability of CBEM gets increased. The WRHA modified mix gives maximum stability of 18.9 kN at 2% WRHA content. However, OPC modified mix gives maximum stability of 17.6 kN at 2% OPC content.The addition of WRHA & OPC in CBEM leads to a reduction in moisture-induced damages as per the results obtained from Retained stability test.Both WRHA modified and OPC modified CBEM has shown a significant increase in tensile strength values. The range of WRHA modified mixes is obtained from 14 to 26% and for OPC it is from 3 to 16%. However, the tensile strength of the material is improved by 3 to 16% for OPC modified mixes.The WRHA modified CBEM perform slightly better than OPC modified CBEM when it is compared with the test results of Retained stability test, Indirect tensile strength test and Marshall stability test.The results of ANOVA analysis shows that the effect of additives on tensile strength, Marshall stability and Retained stability values of CBEM are found to be significantly different.As per the rate analysis, WRHA modified CBEM is cost-effective than OPC modified CBEM.According to the findings, it is concluded that WRHA can be used as a substitute for traditional mineral filler in CBEM.
References
[1] | Al-Hdabi A., Nageim H. Al, Seton L., 2014. “Superior cold rolled asphalt mixtures using supplementary cementations materials" Construction and Building Materials 64, 95–102. |
[2] | Al-Hdabi A., 2016. “Laboratory investigation on the properties of asphalt concrete mixture with Rice Husk Ash as filler” Construction and Building Materials 126, 544–551. |
[3] | Choudhary, R., Mondal, A., Kaulgud H. S., 2012. Use of Cold Mixes for Rural Road Construction. International Conference on Emerging Frontiers in Technology for Rural Area (EFITRA), 20-24. |
[4] | Nageim, H. Al, Al-Busaltan, Shakir Falih, William A., George S, 2012. “A comparative study for improving the mechanical properties of cold bituminous emulsion mixtures with cement and waste materials.” Construction and Building Materials 36, 743–748. |
[5] | Nassar A. I., Mohammed M. K., Thom N., Parry T., 2016. “Mechanical, durability and microstructure properties of cold asphalt emulsion mixtures with different types of filler” Construction and Building Materials 114, 352–363. |
[6] | Naya Pouliot N., Marchand J. and Pigeon M., 2003. “Hydration mechanisms, microstructure, and mechanical properties of mortars prepared with mixed binder cement slurry-asphalt emulsion”, Journal of Material in Civil Engineering, Vol. 15(1), 54 – 59. |
[7] | Oruc Seref, Celik Fazil and Akpinar M. Vefa, 2007. “Effect of Cement on Emulsified Asphalt Mixtures”, Journal of Materials Engineering and Performance (ASM International), Vol. 16(5), 578-583. |
[8] | Thanaya N. A., Zoorob S. E., Forth J. P. 2007. “A laboratory study on cold-mix, cold-lay emulsion mixtures”, Institution of Civil Engineers (ICE), 47 – 55. |
[9] | ASTM D 6931, 2017. “Indirect tensile (IDT) Strength of Bituminous Mixtures”, American Society for Testing Materials, Philadelphia, USA. |
[10] | IS 383, 2016. “Specification for coarse and fine aggregate from natural source for concrete”, Bureau of Indian Standards, New Delhi, India. |
[11] | IS 2386, 2016. “Methods of test for aggregate for concrete”, Bureau of Indian Standards, New Delhi, India. |
[12] | IS 8887, 2004. “Bitumen emulsion for roads (cationic type) – Specification” (Second Revision), Bureau of Indian Standards, New Delhi, India. |
[13] | Indian Roads Congress (IRC) (2014) IRC: SP: 100: Use of cold mix technology in construction and maintenance of roads using bitumen emulsion. IRC, New Delhi, India. |
[14] | Asphalt Institute Manual Series No. 14 ((MS-14), 1989. - Asphalt cold mix manual (Third Edition). |
[15] | MORTH, 2013. Specifications for Road and Bridge Works (Fifth Revision), Ministry of Road Transport and Highways, New Delhi, India. |