Tewodros Getachew1, Miskir Gebrehiwot2
1Department of Construction Technology and Management, Assosa University, Assosa, Ethiopia
2Department of Civil Engineering, Assosa University, Assosa, Ethiopia
Correspondence to: Tewodros Getachew, Department of Construction Technology and Management, Assosa University, Assosa, Ethiopia.
Email: |  |
Copyright © 2020 The Author(s). Published by Scientific & Academic Publishing.
This work is licensed under the Creative Commons Attribution International License (CC BY).
http://creativecommons.org/licenses/by/4.0/

Abstract
Cement production also results in the release of a significant amount of solid waste materials and gaseous emissions. In addition, of the cement production marble quarrying and processing evolves a huge amount of wastage. During marble processing, 30% of the stone (in case of unprocessed stone) goes to scrap because of being in smaller size and/or irregular shape. Produced wastage have dangerous effect on the environment, which includes affecting the fertility of the soil, water pollution and air pollution. Among the potential areas in Ethiopia, the Benishangul Gumuze Region is reach in marble stone. Therefore this problems should be reduced by using marble as cement replacement. The main objective of this research is to investigate the partial replacement of cement with marble dust powder in C-25 concrete production with marble found in Benishangul Gumuz. To check these, marble was collected from Mankusha site and processed for the lab experiment. The physical properties and the chemical composition of the marble dust powder was determined. In addition to this, split Tensile, flexural and compression tests for hardened concrete were conducted for 7, 14 & 28 days by replacing cement with marble dust powder from 5% to 20%. Controlling mix C-25 with 0% marble dust powder was prepared. The 28th compressive strength test result for 0%, 5%, 10%, 15%, 20% are 45.7MPa, 46.2MPa, 46.77MPa, 46.10MPa and 45.05MPa respectively. And the 28th split tensile strength test result for 0%, 5%, 10%, 15%, 20% are 2.91MPa, 3.01MPa, 3.24MPa, 3.15MPa and 2.64MPa respectively. The result for flexural strength test for 0%, 5%, 10%, 15%, 20% are 5.27MPa, 5.38MPa, 5.7MPa, 6.31MPa and 5.78MPa respectively. The results showed maximum compressive and split tensile strength at 10% replacement of 46.77MPa and 3.24MPa respectively. Maximum of 6.31MPa flexural strength at 15% marble dust powder replacement. Therefore, marble in Mankush site has achieved a greater strength than the normal or controlled (C25) in Compressive, split tensile and flexural strength. This will has double benefits. One in protecting the region from marble waste effects and reduces cost by reducing the amount of cement required.
Keywords:
Cement, Compressive strength, Concrete, Marble dust powder, Tensile strength, Flexural strength, Slump
Cite this paper: Tewodros Getachew, Miskir Gebrehiwot, Investigation on Partial Replacement of Cement with Marble Dust Powder on C-25 Concrete Production in Benishangul Gumuz; Ethiopia, International Journal of Construction Engineering and Management , Vol. 9 No. 4, 2020, pp. 126-133. doi: 10.5923/j.ijcem.20200904.03.
1. Introduction
Millions of tons of waste is produced in the world each year and most of it is not recyclable. Furthermore, recycling waste consumes energy and produces pollution. In addition this wastes are dangerous to the environment. Incorporating waste materials in concrete production has two advantages: removing waste and adding good values to concrete properties (Davoud Tavakoli, etal., 2018). Among most widely used industrial wastes that are used to replace cement in concrete productions are Fly ash, blast furnace slag and silica fume, which have a nature called pozzolanic behaviour. For such reason, marble waste powder, which is a by-product of marble processing factory, was studied by many researchers for its use in concrete and mortar production as cement replacing material. Most of the researches showed positive results and benefits (Abrar Awol, 2011).Christian Meyer (2002) stated that, the production of one ton of Portland cement causes the release of one ton of CO2 into the atmosphere. In addition to this the cement industry alone generates worldwide about 7% of it. Marble industry produces large amount of waste during mining and processing stages. This waste is dumped on to open land, which creates many environmental problems (Sudarshan D. and A. K. Vyas, 2015). According to MSME development institute (2006) report, the slurry generated during processing can be estimated at about 10% of the total stone quarried (20% to 25% of the block as received from the quarries), and during polishing as 5% to 7%. The slurry generated during processing can be estimated at about 10% of the total stone quarried (20% to 25% of the block as received from the quarries) and during polishing as 5%.The most interesting deposits of marble are found in the western part of Ethiopia which is found in Benishangul Gumuz regional state, and Mankush is one of the sites found in this region (Haileyesus Walle etal. 2000). Accordingly, during quarrying and processing marbles the waste produced has to be used for the purpose of concrete production in order to save cost by replacing cement and coarse aggregates. Since cost of cement in Ethiopia is high, finding something that replaces it partially is an advantage. If the replacement is a waste for other process, it has double advantages, one in protecting the environment the other in saving cost. The specific objectives of this study are; to determine the physical and chemical properties of marble dust powder used in this study, to investigate the influence of partial replacement of cement with marble dust powder on physical properties of concrete.
2. Marble Dust Powder as a Cement Replacement
Use of marble dust replacement of cement in the production of concrete for the construction industry should be encouraged where there comparative cost advantage, and improved workability as replacement of marble increase, the compressive strength also increased as with increase of marble powder up to 10% replacement (B. Krishna Rao, 2016).Five concrete mixtures containing 0%, 5%, 10%, and 20% marble dust powder as cement replacement by weight basis has been prepared. Water/cement ratio (0.43) was kept constant, in all the concrete mixes. Compressive strength, split tensile strength & flexural strength of the concrete mixtures has been obtained at 7 and 28 days. The results of the laboratory work showed that replacement of cement with MDP increase, up to 10% for compressive strength, & up to 15% for split tensile strength & flexural strength of concrete (Ranjan Kumar, etal., 2015).If percentage of cement replaced with marble dust power is more than 10%, than the compressive strength on concrete will start to decrease. it is showing in the graph that the compressive strength of concrete is increased by replacement of cement with marble dust powder up to 10% (Ruchi C. and Avinash S., 2017).
3. Materials and Methodology
3.1. Materials
For studying the effects of marble waste powder on the properties of concrete, Dangote OPC; with strength grade of 42.5 is used for the preparation of concrete with marble dust powder. For this study, all the coarse aggregate and fine aggregates were from the same source for all tests to be conducted and are tested to comply ASTM C33 standard specification. The marble for this study was collected from Mankush marble site and the marble dust powder was sieved and marbles passing 90 microns sieve was used as a replacement.. And clean potable water was used for washing aggregates, and mixing and curing of concretes.
3.2. Methodology
The research was conducted in western Ethiopia in Benishangul gumuz regional state, particularly in Guba wereda, Mankush Marble site. Which is located 920 km from the capital Addis Ababa.
3.2.1. Sample Preparation and Tests on Sample
For conducting compressive strength, split tensile and flexural strength tests, testing samples were prepared by replacing cement with 0%, 5%, 10%, 15% and 20% marble dust powder. The samples were given designation for each replacement. The designations are presented on Table 1 with cement content and marble dust powder content.Table 1. Sample Designation of Concrete  |
| |
|
For compressive strength test three cube with size of 150mm x 150mm x 150mm are used to determine the 7, 14 and 28th days compressive strength for each percentage replacements according to ASTM. Split tensile strength was conducted on cylindrical sample of 300mm by 150mm according to ASTM. The test was carried out for 7, 14 and 28th days. The other test that was carried out was flexural strength of concrete. This test was carried out on sample of 150mm by 150 mm by 450mm concrete beams.The sample size for compressive, split tensile and flexural strength tests are presented below on Table 2, Table 3 and Table 4 respectively.Table 2. Sample Size for Compressive Strength Test 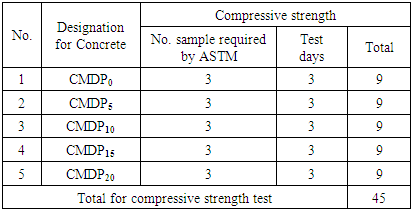 |
| |
|
Table 3. Sample Size for Split Tensile Strength 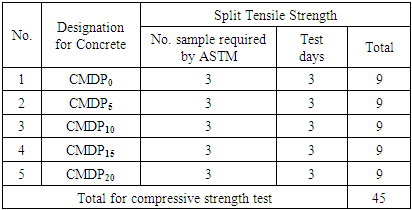 |
| |
|
Table 4. Sample Size for flexural Strength 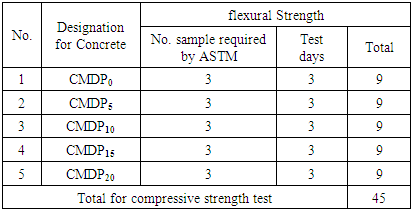 |
| |
|
According to the above tables a total of 135 samples were prepared and tested for compressive, split tensile and flexural strength test. The designation CMDP0 indicated concrete with o% marble replacing cement, CMDP5 concrete with 5% marble replacing cement, CMDP10 concrete with 10% marble replacing cement, CMDP15 concrete with 15% marble replacing cement and CMDP20 concrete with 20% marble replacing cement.The slump of each concrete mix was also measured to see the fresh concrete property. The results for different testes were analysed to address the objectives and discussed in graphs, charts and tables.
3.2.2. Mix Proportion
The mix proportion was calculated by using ACI mix design method. After the quantities of main ingredients are determined, the next step was to replace the cement quantity with marble dust powder without altering the quantities of coarse aggregates and fine aggregate. The water cement ratio used here is 0.49. The summarized mix proportion for each test samples are presented on Table 5 below.Table 5. Summarized Mix Proportion 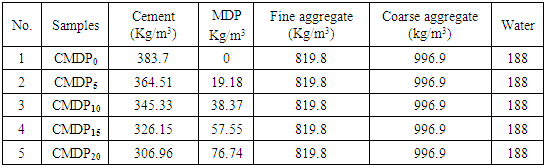 |
| |
|
3.2.3. Testing on Materials
The ingredients were tested for different properties. Prior to mix design. The property test for cement, marble dust powder, sand and coarse aggregates were te56sted. Beside the physical property test, marble dust powder chemical constituents were identified. The physical property tests that were carried out for the marble dust powder, cement, coarse aggregate and fine aggregates are listed on Table 6 below.Table 6. Determined Physical Properties of Concrete Ingredients 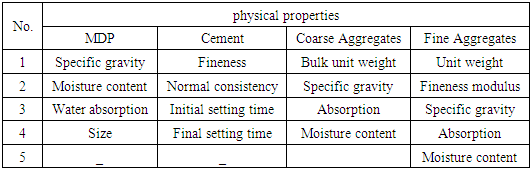 |
| |
|
The results of the above different properties are discussed and compared with standards.
4. Result and Discussion
4.1. Materials Property Test Result
The materials for the production of concrete with marble dust powder were tested for different properties. The physical and chemical property test results of the marble used are presented on Table 7 and Table 8 respectively. Table 7. Physical Properties Test Results of MDP 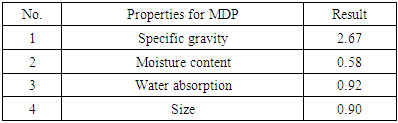 |
| |
|
As shown on Table 7, the marble on this study has a specific gravity of 2.67, moisture content of 0.58% and a water absorption capacity of 0.92 and the marble passed sieve size of 0.90 micron.As shown from Table 8, majority of the compounds are much less than that of ASTM C150/C150M standard specification for Portland cement maximum limit. Whereas silica dioxide (SiO2) composition of the MDP is 0.37 which is much more less than the minimum.Table 8. Chemical Property Test Results of MDP 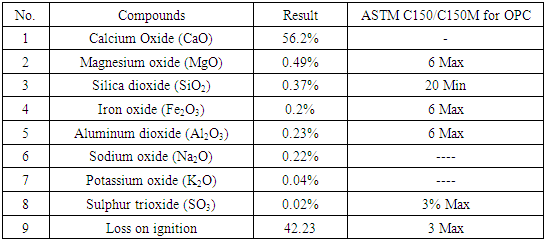 |
| |
|
The other ingredient for concrete production is cement. The cement used for this study has the following physical properties as listed on Table 9 below.Table 9. Cement Property Test Result 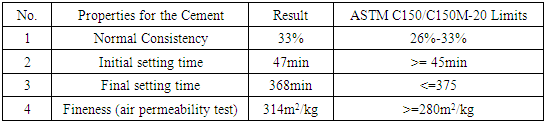 |
| |
|
As shown from Table 9, the normal consistency of the cement used is 33% which is within the limits of ASTM 26%-33. The initial setting time and final setting time of the cement used are 47 minutes and 368 minutes respectively whereas ASTM specifies >45 minutes and <375 minutes respectively. The fineness of the cement by using air permeability method is 314m2/kg which is acceptable according to ASTM. The fine aggregate in this study has the following physical property as shown on Table 10 below.Table 10. Fine Aggregate Physical Property Test Result 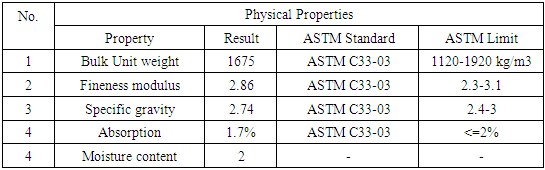 |
| |
|
According to the test result on Table 10, the bulk unit weight of the fine aggregate is within the limit of ASTM C33 (1120 kg/m3-1920 kg/m3) normal weight concrete. Fineness modulus of the sand used here is 2.86, which is within acceptable limit of ASTM C33 (2.3-3.1). The Specific gravity for the sand (2.74) is also within ASTM C33-03 (2.4-3). According to ASTM C33-03, water absorption of sand should be </= 2%. The sample for this study has 1.7% value which is acceptable. Finally the moisture content of sand is 2%. This means the sand has moisture naturally and this moisture was considered during mixing while adding mixing water.The coarse aggregate used has the following properties as listed on Table 11. Table 11. Coarse Aggregate Physical Property Test Result 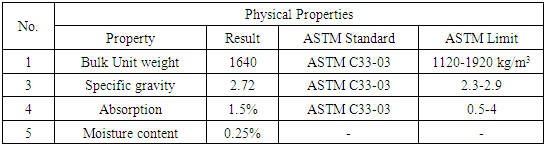 |
| |
|
According to the test result on Table 11, the bulk unit weight of coarse aggregate is within the limit of ASTM C33 (1120 kg/m3-1920 kg/m3) normal weight concrete. The Specific gravity for the coarse aggregate is 2.72, which is according to ASTM C33-03 (2.3-2.9).The water absorption of the sample is 1.5% which is within ASTM C33-03 (0.5-4). Finally the moisture content of sand is 0.25%. This moisture was considered during mixing while adding mixing water.
4.2. Slump Test Result
The fresh concrete property test was conducted for different percentage of marble dust powder replacement. The test result is shown in Figure 1. It’s clearly shown from Figure 1 that, as percentage replacement increases the slump value will also increases from 43mm to 65mm. 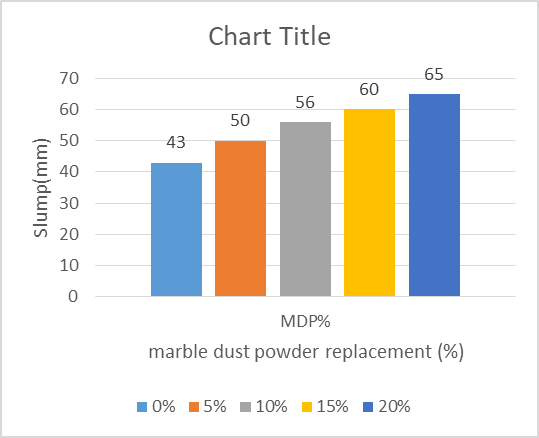 | Figure 1. Slump for different percentage marble dust powder replacements |
As shown from Figure 1, as the percentage replacement increases the slump value also increases. This shows the workability of the concrete increases as the percentage of marble dust powder increases.
4.3. Physical Properties of Concrete
4.3.1. Compressive Strength
The compressive strength of the samples were tested for 7th, 4th and 28th days. The test results for each replacement is presented on the Table 12 below.Table 12. Compressive Strength Test Result  |
| |
|
According to Table 12 and Figure 2, all samples shows an increment in compressive strength with respective to each testing days. 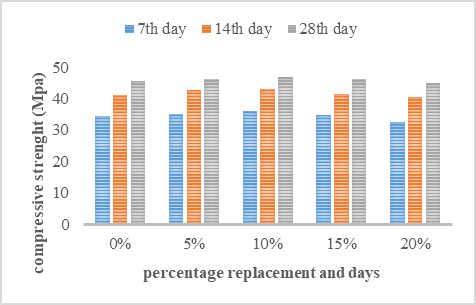 | Figure 2. Compressive strength and percentage replacement |
To see the influence of percentage replacement of cement with marble dust powder on compressive strength, the 28th days compressive strength test results of 0%, 5%, 10%, 15% and 20% were compared to each other. The comparison were made using the graph in Figure 3.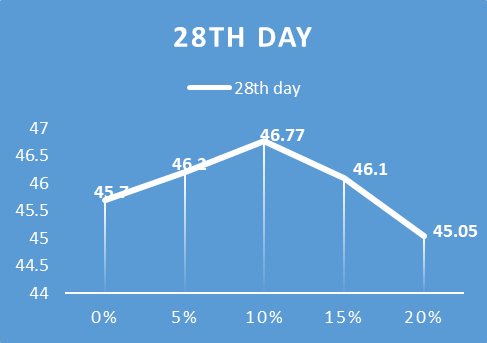 | Figure 3. 28th day Compressive strength and percentage replacement |
As shown in Figure 3, the compressive strength increases up to 10% replacement and decreases afterward. The 10% replacement is with 46.77 MPa compressive strength whereas, the 0% replacement (control concrete) is with 45.7MPa, and this shows the 10% replacement increased with 1.07Mpa from 0% replacement. Here the 15% replacement even has a better compressive strength than the controlled sample (C25).
4.3.2. Split Tensile Strength
Like the compressive strength test, the split tensile strength test was conducted for 7th day, 14th day and 28th days. The split tensile strength was tested on cylindrical sample of 300mm by 150mm. The results of the splitting tensile strength test for 0%, 5%, 10%, 15%, and 20% marble dust powder replacements are listed on Table 13.Table 13. Split Tensile Strength Test Result 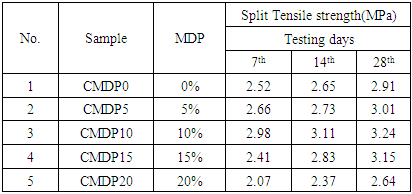 |
| |
|
According to Table 13 and Figure 4, all samples shows an increment in split tensile strength with respective to each testing days. 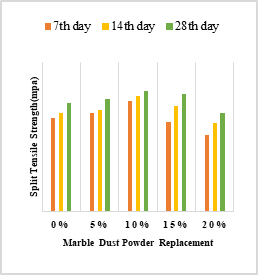 | Figure 4. Split tensile strength and percentage replacement |
To study the influence of marble dust powder replacement on concrete split tensile strength, the 28th days splitting tensile strength of each percentage replacement is presented in Figure 5. As illustrated in Figure 5, the split tensile strength increases as the marble dust powder percentage replacement increases up to 10%. But after wards the split tensile strength decreased. At 0% replacement the splitting tensile strength at 28th day was recorded as 2.91MPa, and increased up to 10% replacement. At 10% replacement, the split tensile strength of the sample is 3.24MPa. Then afterwards, the split tensile strength decreased to 2.64MPa at 20% MDP. However, this strength is still greater than the 0% marble dust powder concrete which is the controlled sample (C25). This implies that, the 20% MDP concrete has a better strength than 0% marble dust powder replacement concrete.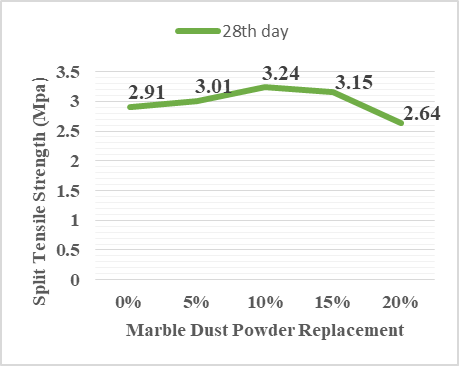 | Figure 5. 28th day Split tensile strength and percentage replacement |
4.3.3. Flexural Strength
Like the compressive strength test and split tensile strength, the flexural strength test was conducted for 7th day, 14th day and 28th days. The flexural strength was tested on a beam sample of 150mm by 150 mm by 450mm. The results of the flexural strength test for 0%, 5%, 10%, 15%, and 20% marble dust powder replacements are listed on Table 14. In order to see the effect of the replacement on each testing days, the chart in Figure 6 is used for better illustration. Table 14. Flexural Strength Test Result 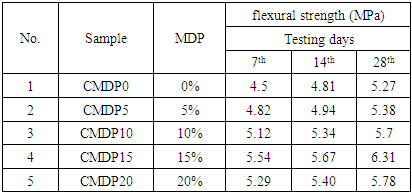 |
| |
|
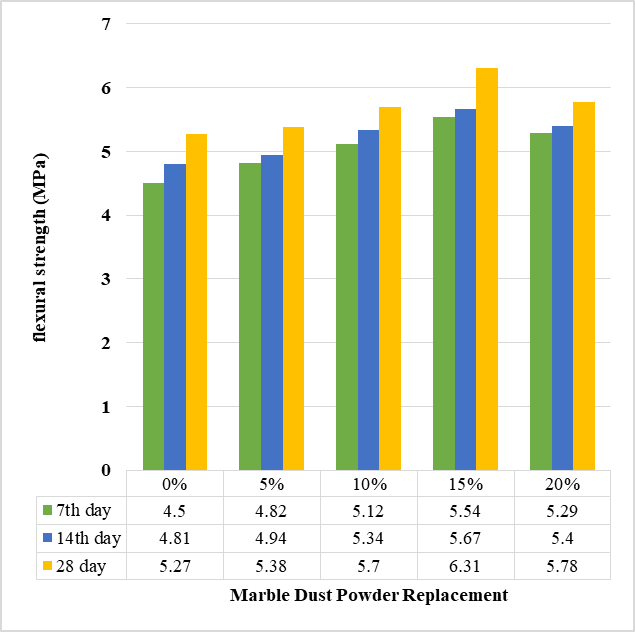 | Figure 6. Flexural strength and percentage replacement |
According to Figure 6 and Table 14, all samples shows an increment in flexural strength with respective to each testing days. To study the effect of marble dust powder replacement on concrete flexural strength, the 28th day’s flexural strength of each percentage replacement are presented in Figure 7. As illustrated in Figure 7, flexural strength increases as the marble dust powder percentage replacement increases up to 15%. But after wards the flexural strength decreased. At 0% replacement the flexural strength at 28th day was recorded as 5.27MPa, and increased up to 15% replacement. 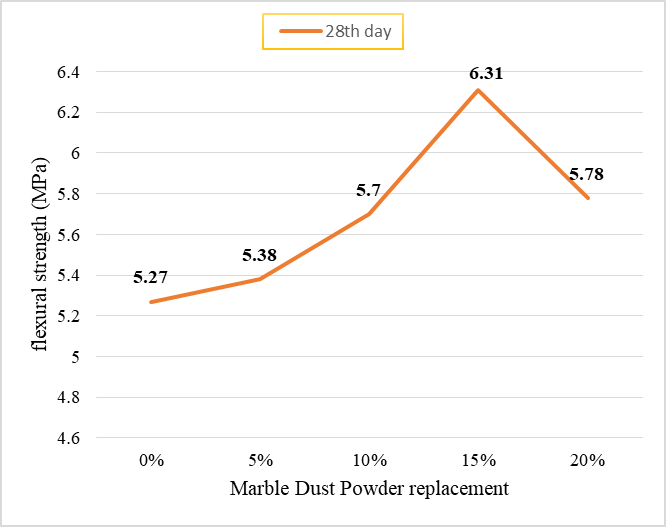 | Figure 7. 28th day Flexural Strength and percentage replacement |
At 15% replacement, the flexural strength of the sample is 6.31MPa. Then afterwards, the flexural strength decreased to 5.78MPa at 20% MDP. However, this strength is still greater than the 0% marble dust powder concrete which is the controlled sample (C25). This implies that, the 20% MDP concrete has a better flexural strength than 0% MDP concrete.
4.4. Comparison of Compressive, Flexural and Split Tensile Strength
The compressive, split tensile and flexural strength test results were considered for comparison. As shown fro Table 15, compressive and split tensile strength of the concrete with 10% replacement shows maximum result. Whereas, flexural strength of the concrete shows maximum result at 15% replacement. Table 15. 28th day compressive, tensile and Flexural Strength 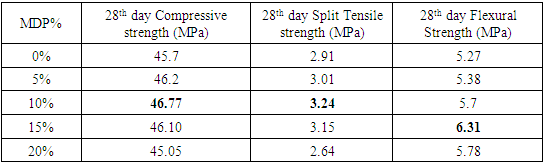 |
| |
|
5. Conclusions
In this study, different tests were conducted to determine the physical and chemical properties of marble dust powder used in this study, to investigate the influence of partial replacement of cement with marble dust powder on physical properties of C-25 concrete.Accordingly, the following conclusions were made from the results:Ø The marble used has a specific gravity of 2.67, moisture content is 0.58, water absorption of 0.92% and size of 0.90 micro.Ø The chemical composition of the marble is 56.25 CaO, 0.49% MgO, 0.37% SiO2, 0.2% Fe2O3, 0.23% Al2O3, 0.22% Na2O, 0.04% K2O, 0.02% S03, and loss on ignition is 42.23%.Ø All the samples showed an increase in compressive, split tensile and flexural strength with respect to each testing days.Ø The slump test result implied, the increase in workability as the percentage of marble dust powder increases. Ø The 28th compressive strength results of the 0%, 5%, 10%, 15% and 20% are 45.7MPa, 46.2MPa, 46.77MPa, 46.10MPa and 45.05MPa respectively.Ø The compressive strength at 10% marble dust powder replacement has the maximum compressive strength of 46.77MPa.Ø The 28th split tensile strength results of the 0%, 5%, 10%, 15% and 20% are 2.91MPa, 3.01MPa, 3.24MPa, 3.15MPa and 2.64MPa respectively.Ø The split tensile strength at 10% marble dust powder replacement has the maximum split tensile strength of 3.24MPa.Ø The 28th flexural strength results of the 0%, 5%, 10%, 15% and 20% are 5.27MPa, 5.38MPa, 5.7MPa, 6.31MPa and 5.78MPa respectively.Ø The flexural strength at 15% marble dust powder replacement has the maximum split tensile strength of 6.31MPa.Ø The concrete with 10% marble dust powder has maximum compressive and split tensile strength. Whereas, 15% marble dust powder concrete has a maximum flexural strength. Generally according to the study, the marble dust powder in Mankush site, has shown appreciable result in compressive, split tensile and flexural strength. Thus in order to protect the environment from the marble dust powder effect and in order to save cost by minimizing cement amount, marble can play an important role.
References
[1] | Abdullah Anwar, Sabih Ahmad, Syed Mohd, Ashraf Husain and Syed Aqeel Ahmad, (2015). Replacement of Cement by Marble Dust and Ceramic Waste in Concrete for Sustainable Development, International Journal of Innovative, Engineering and Technology, 4(6), PP 496-503. |
[2] | Abrar Awol, (2011). Using Marble Waste Powder in Cement and Concrete Production, Addis Ababa University School of Graduate Studies. |
[3] | ASTM C150/C150M-20, Standard specification for Portland Cement, ASTM international, West Conshohocken, PA, 2020. |
[4] | ASTM C33-03, Standard specification for Concrete Aggregates, ASTM international, West Conshohocken, PA, 2003. |
[5] | Christian Meyer, (2002). Sustainable Development and the Concrete Industry. |
[6] | Davoud Tavakoli, Masoumeh Hashempour and Ali Heidari, (2018). Use of waste materials in concrete. Pertanika J. Sci. & Technol. 26 (2): 499 – 522. |
[7] | Esra Tugrul Tune, (2018). Recycling of marble waste: A Review Based on Strength of Concrete Containing Marble waste, Journal of Environmental Management. 231(1), pp 86-97. |
[8] | Gulden Cagin Ulubeyli, Turhan Bilir and Recep Artir, (2016). Durability Properties of Concrete Produced by Marble Waste as Aggregate or Mineral Additives, Procedia Engineering, 161(2016) 543-548. |
[9] | Haileyesus Walle, Sintayehu Zewde & Tom Heldal, (2000). Building stone of central and southern Ethiopia: deposits and resource potential. |
[10] | I. M. Aho and E. E. Ndububa, (2015). Compressive and Flexural Strength of Cement Mortar Stabilized With Raffia Palm Fruit Peel (Rpep). Global Journal of Engineering Research Vol 14. |
[11] | Kaleeswari. G and Dhanalakshim, (2017). Study on Marble Powder as Partial replacement of Cement in Concrete, Global Research and Development Journal For Engineering, 2(2), PP 77-80. |
[12] | MSME-Development institute, (2006). Status report on commercial utilization of marble slurry in Rajasthan. |
[13] | Nitisha Sharma and Swami Dyal, (2015). Use of Marble Powder as Partial Replacement in Cement Sand Mix. International Journal of Engineering Science and Research Technology, vol. 4, Issue 05, PP 501-504. |
[14] | Nutan C. and Jayeshkuma P., (2013). A Technical Study on Quarrying and Processing of Marble and Its Waste Incorporating With Concrete. Global Research Analysis, Volume: 2, Issue: 2 No 2277 – 8160. |
[15] | P. N. Rragunath, K. Suguna, J. Karthick and SarathKumar, (2019). Mechanical and Durability Characteristics of Marble Powder Based High Strength Concrete, Scientia Iranica, Transaction A: Civil Engineering, 26(6), PP 3159-3164. |
[16] | Ranjan Kumar, Shyam k. and Kishor Kumar, (2015). Partial Replacement of Cement with Marble Dust Powder, Journal of Engineering Research and Applications. Vol. 5, Issue 8, (Part - 4), pp.106-114. |
[17] | RochakPandy, Prof. M.C. Paliwal, Jatin Mehta and Jeet N Tiwari, (2016). Optimum Partial Replacement of Cement in Concrete with Waste Marble Dust in Conjunction with Super Plasticizers, 5(8), PP 867-876. |
[18] | Ruchi C. and Avinash S., (2017). Cement Replacement in concrete with Marble Dust Powder, International Research Journal of Engineering and Technology (IRJET), 4 (3). |
[19] | Sudarshan D. and A. K. Vyas, (2015). Impact of Waste Marble Dust on the Sustainability of Cement Sand Mortar, Third Conference on Sustainability in Process Industry. |