Nana Yaa Adusa-Poku 1, Rogerson Anokye 2
1Directorate of Works and Physical Development, Kumasi Technical University, Kumasi, Ghana
2Department of Interior Design and Materials Technology, Kumasi Technical University, Kumasi, Ghana
Correspondence to: Rogerson Anokye , Department of Interior Design and Materials Technology, Kumasi Technical University, Kumasi, Ghana.
Email: |  |
Copyright © 2020 The Author(s). Published by Scientific & Academic Publishing.
This work is licensed under the Creative Commons Attribution International License (CC BY).
http://creativecommons.org/licenses/by/4.0/

Abstract
Competition among Contractors in the Construction Industry has increased as Ghana sustains her middle-income status. To have a sustained competitive edge, successful industries know that quality management is the key to competing successfully. Recognizing that quality is the key to competition, Total Quality Management (TQM) was introduced in the construction industry in developed countries as a philosophy and a culture to improve productivity and quality. However, developing countries such as Ghana are slow in adopting TQM in the Construction Industry. Therefore, the level of quality in local Ghanaian construction firms is low as compared to international construction firms operating in Ghana. In order to know the quality management practices, questionnaires were administered to project managers, supervisors and construction professionals such as architects and engineers in construction Companies in Kumasi to ascertain their perception of quality and its management practices. The research revealed that the TQM critical success factors rated in order of importance were Process Management, Continuous Improvement, Employees’ Satisfaction/Empowerment, Supplier Chain Management, Customer Focus, Management /Leadership commitment and Training. To enable this implementation of TQM, a framework has been proposed to guide management and this call for a radical cultural change that will transform the construction industry in Ghana.
Keywords:
Total Quality Management, Contractors, Construction Industry
Cite this paper: Nana Yaa Adusa-Poku , Rogerson Anokye , Proposed Framework for Applying Total Quality Management in Construction Industry in Ghana, International Journal of Construction Engineering and Management , Vol. 9 No. 3, 2020, pp. 92-98. doi: 10.5923/j.ijcem.20200903.02.
1. Introduction
In this twenty-first century competitive world, construction companies face the challenge of providing quality works to their clients to sustain their competitive advantage. With the country attaining a middle-income status in addition to the oil-production, which started in the year 2010, there is an increased demand for infrastructural works with its accompanying standard quality requirements. There is an increasing global competition in the Construction sector and Ghanaian Contractors who desire to participate on this global scale need to produce quality works to be more effective and to enhance their competitive advantage.Moreover, with an increasing awareness of the construction quality, contractors have no option than to ensure that Clients get value for money. Considering the influx of Foreign Construction Companies in Ghana and the increasing competitiveness in the construction sector, it is important that Ghanaian Contractors deploy appropriate quality management strategies such as TQM to reduce cost and increase value/quality. In an article named ‘ Construction and the Internet” in The Economist [1], it was noted that up to 30% of construction costs is due to inefficiencies, mistakes, delays, and poor communications [2] noted that Construction Quality Management is the key to a successful project. They explained that the selection of a Construction Quality Manager (CQM) early in a project gives the overall project a better chance of delivery on time, to budget, zero defects as well as high availability and reliability. However, CQM effort can be a cultural change and a challenge for Contractors. It requires attention to detail, tracking of issues and accountability [2]. Quality Management has evolved over many decades. It started with Quality Control (QC) where products are sampled and inspected for errors or defects. After QC, a new technique, Quality Assurance (QA) evolved. The principles for QA are ‘Fit for Purpose’ and ‘Right first Time’. Total Quality Management (TQM) is another concept of Quality Management that has been in existence over the past years. The primary purpose of TQM is to achieve excellence in customer satisfaction through continuous improvement of products and processes by the total involvement and dedication of each individual who is part of that product process [3].Nonetheless, in most developing countries such as Ghana, the principles of TQM are not employed in construction leading to low quality works, high construction costs and dissatisfied clients. There is a major problem in obtaining acceptable levels of quality in the Construction Industry. From both Contractor and Consultant point of view, some of the challenges in the Ghanaian Construction Industry include poor workmanship, inadequate workmanship, low productivity and lack of trained workforce [4].In view of this, the construction industry needs proactive management methods such as TQM in order to improve quality of works, reduce re-work and the cost of construction. A TQM approach is essential for long-term survival in all business including the construction industry [5].There is the therefore the need for the principles of TQM in the Ghanaian Construction Industry to improve the quality of works. The first step towards this feat is to adopt a simple systematic framework to guide all stakeholders in the Construction Industry.TQM implementation is a never-ending exercise and a very challenging task that calls for a well-structured pragmatic approach [6]. Although there are dissimilar characteristics between the Manufacturing and Construction Sector, [7] concluded that the basic principles of TQM can be applied in the construction industry to improve on Quality. [6], listed ten (10) elements essential in implementing TQM. These 10 elements are Leadership and Management Commitment, Customer Satisfaction, Training, Communication, Teamwork, Total Quality and measurement, Continuous Improvement, Process Improvement, Employee Focus and Supplier. He noted that facilitative leadership and training were very essential in the implementation of a successful TQM Programme. [8], designed a TQM implementation framework for real estate firms in Ghana. This structure was designed when his study on QMS in real estate firms confirmed that although these firms are aware of the importance of quality, their knowledge about QM is limited. He realised that their perception about quality is of corrective actions (Quality control) rather than preventive actions (Quality assurance, process and continuous improvement approach). Moreover, the survey indicated that the major problems affecting implementation of QM program are lack of expertise/resources in QM, changing the behaviour and attitude, lack of education and training to drive the improvement process, lack of employee commitment/understanding, lack of top-management commitment/understanding.Just as in most developing countries, Pakistan has vulnerabilities posed by economic constraints in the construction industry and these vulnerabilities can be overcome by taking advantage of TQM philosophy [9]. He agreed that although TQM is applicable in the Construction Industry, there is a lack of consensus on the implementation process.After practising quality assurance based on ISO 9000 for the past 15 years, research proved that project quality in the Hong Kong Construction Industry was still lower than standards expected [10]. They stated that QA was a static approach and TQM being a dynamic approach was needed to be the driving force for quality improvement. The study revealed that Hong Kong Contractors had full knowledge of QA principles but considerable knowledge in TQM principles.Some organisations use models as a guide in the implementation of quality management systems. These models are the frameworks on which TQM implementation is based. [11], support that MBNQA and EFQM are relevant operational frameworks suitable for assessing TQM initiatives. The Malcolm Baldrige National Quality Award (MBNQA) founded in 1988 recognises US organisations for excellent performance. There are seven (7) categories named as the main values in quality management. They are (1) leadership, (2) strategic planning, (3) human resources orientation, (4) process management, (5) information and analysis, (6) customer and market focus and (7) business results. This is as shown in Figure 1. 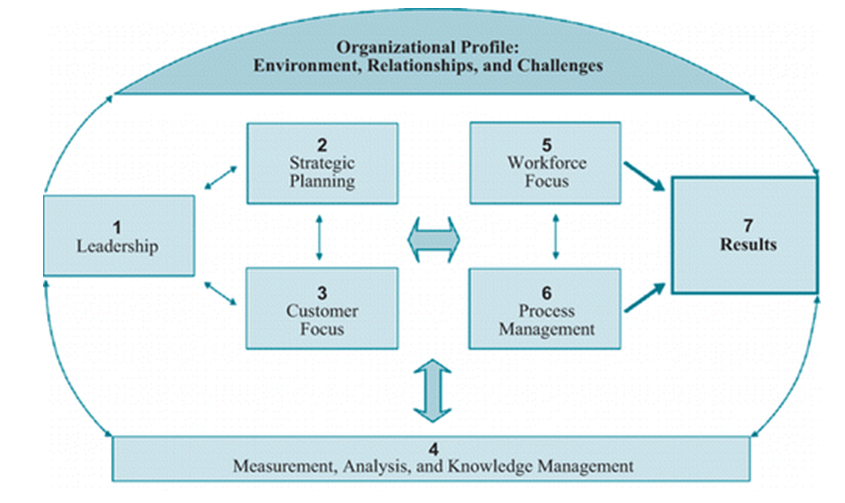 | Figure 1. MBNQA Framework, [12], Baldridge national Quality Program, http://baldridge.nist.gov/ |
The European Foundation created EFQM in 1991 for Quality Management. It is a framework against which applicants of the European Quality Award are judged and recognized for organizational excellence in European companies. There are nine elements made up of five (5) enablers and four (4) results as shown in Figure 2.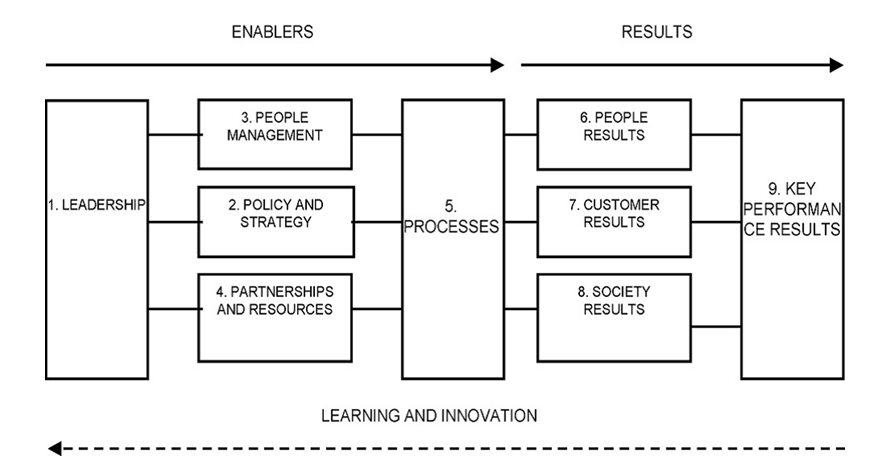 | Figure 2. EFQM Excellence Award [13] http://www.efqm.org |
The EFQM model places much more emphasis on tactical issues relating to the diffusion and implementation of strategy and the monitoring of customer, employee and society results, while the Baldrige model emphasizes the development of strategy and the reporting and analysis of business (financial) results [4]. In comparing MBNQA and EFQM approach towards quality, it was realised that the former was by agility methods and the latter by managing processes. It was concluded that MBNQA is stronger on "Systems Perspective" and EFQM is stronger on "Managing by Processes [15].This paper therefore seeks to propose a framework based on the EFQM model that will guide Construction Companies in the implementation of TQM Principles. The proposed framework is based on the Literature Review and TQM Critical Success Factors.
1.1. Purpose of Framework
Many researchers have given different definitions of framework. According to Merriam-Webster Dictionary, a framework is a set of ideas or facts that provide support for something. Generally, frameworks show the empirical relationships between aspects. In summary, [16] summarises the purpose of frameworks as:i. Illustrating an overview and to communicate a new vision to the organisation; ii. Force management to address a substantial list of key issues which otherwise might not be addressed; iii. Give valuable insights into the organisation's strengths and weaknesses, and its overall strategic position in the market-place; iv. Support implementation and to improve the chance of success because it will provide not only overview but also more detailed information describing the content of each framework element and its relationship to other elements.
1.2. Basic Design of Frameworks
[17] summarised the design requirements for developing a framework that include the following steps. They are:i. Procedures for selecting and implementing measures;ii. Ability to identify whether existing measurement system is up to date and measuring critical issues (i.e. audit capability);iii. Selected measures should be congruent with company strategy and have strong relationship with the six core competitive priorities (i.e. quality, cost, flexibility, time, delivery and future growth); iv. Facilitates rapid selection of measures from a data bank; and workbook approach (i.e. step-by-step methodology).
2. Methodology
The methodology used in this survey was deductive approach being quantitative, in addition with triangulation of data to corroborate and support qualitative findings. The data sources for the triangulation will be by interviews, documents and observation. Structured questionnaires were sent to Contractors based in Kumasi. Since TQM is about all employees including management, questionnaires were sent to all participants in the Kumasi based Companies classified under D1K1 and D2K2 categories for the purpose of collecting primary data. Closed questions were asked to facilitate the data collection and analysis. A few open questions in the form of ‘Others’ were asked to enable other respondents answer in their own words. The five-point Likert scale was employed to explore the respondents’ opinions in relation. The probability technique, random sampling method was used in administering questionnaires to the selected Contractors. 50 questionnaires were sent, out of this number 35 responded which represents 70% response rate.The basic data analysis tool used was the Statistical Package for the Social Sciences (SPSS). For analysing data by ordinal scale, the importance index of the factors was adopted as confirmed by [18]. They were computed using the following equation.
Where: n1 = number of respondent who answered ‘Strongly Disagree’n2 = number of respondent who answered ‘Disagree’n3 = number of respondent who answered ‘Neutral’n4 = number of respondent who answered ‘Agree’n5 = number of respondent who answered ‘Strongly Agree’Results from importance index calculation were ranked 1st, 2nd, 3rd etc. in order to know their cardinality of importance. TQM critical factors are analysed using Importance Index (I. Index) to assess the level of Importance of these factors. The results from respondents indicated their agreement level on the criteria for assessing successful implementation of TQM principles as applied in their companies.
3. Results
Table 1 specifies the results obtained for the critical success factors for TQM implementation.Table 1. Critical Success Factors for TQM Implementation 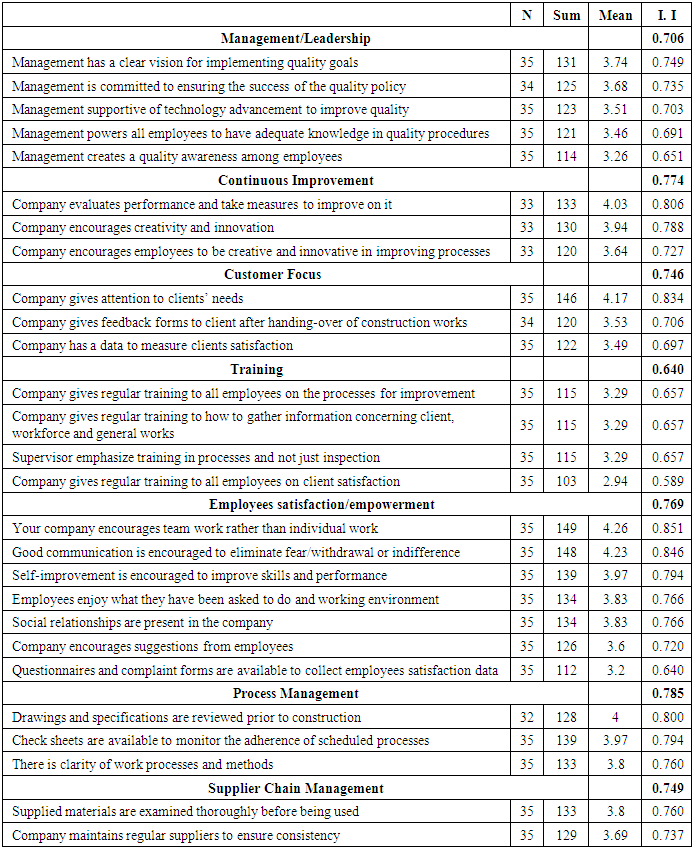 |
| |
|
As observed from the Table 2, the most important factor is Process Management with importance index of 0.785. The indices of the other factors follow the order as listed in table 2. The mean ranking of all the critical success factors are significantly high showing that there is a general agreement that these factors can be applied in assessing successful implementation of total quality management in the construction industry.Table 2. Summary of critical success factors ranking 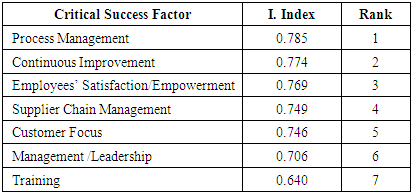 |
| |
|
4. Discussion
Proposed Conceptual FrameworkThe proposed TQM framework is built upon a set of core values and factors that is the foundation for integrating the key performance requirements within the quality framework. The set of basic factors forming the building blocks of the proposed TQM framework in accordance with this study are Process Management, Continuous Improvement, Employees’ Satisfaction/Empowerment, Supplier Chain Management, Customer Focus, Management /Leadership and Training.The proposed framework is based on European Foundation for Quality Management (EFQM). EFQM is a quality model based on nine (9) elements; five (5) enablers and the four (4) elements are Results. EFQM model is more geared towards continuous improvement of systems and customer satisfaction.A simple model depicting the relationship between enablers and results is that when people acquire proper process management skills then performance increases. The simple model is as shown in Figure 3.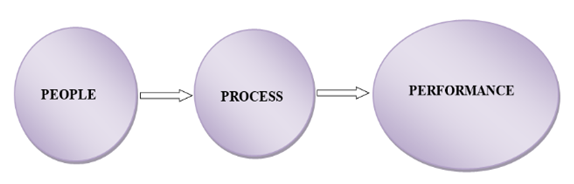 | Figure 3. Simple Model |
As indicated in the results, Process Management is at the most important of all the factors for good performances. Good process management leads to better performance. From this simple model, the researcher proposed a TQM framework based on the above simple model and EFQM and is as shown in Figure 4.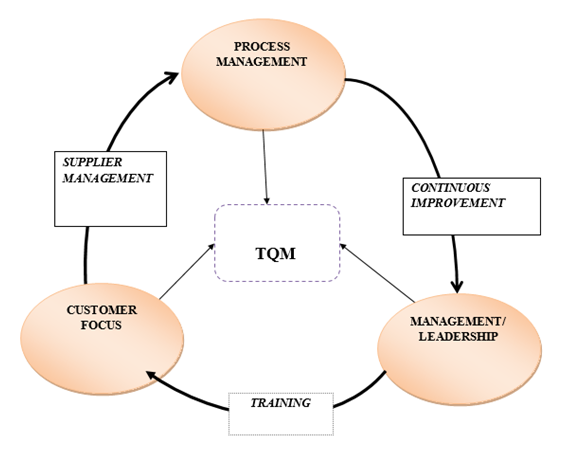 | Figure 4. TQM Framework |
The proposed framework is based on six criteria. Three basic criteria needed for a successful implementation of TQM Framework are Process Management, Leadership Commitment, and Customer Focus. They are the triangular pillars on which TQM derives its support. Process Management is at the top of the triangle indicating that without process management the framework will fail. Customer Focus and Leadership are the Human Resources who play their role effectively in managing all necessary processes.The Customers include the Internal and External Customers. Any one of these criteria that fails leads to a failure of TQM. Continuous Improvement, Training, and Supplier Management are the connectors to the main pillars for an effective and efficient TQM Implementation in the Ghanaian Construction Industry.
4.1. The Three Pillars
4.1.1. Process Management
A typical construction project consists of various activities executed by different skilled personal at differing times within the Project Time Frame. According to triple role concept, within each activity there are three parties; Supplier, Processor and Customer. For an efficient Process Management within the construction industry the Customer must be satisfied before the next activity starts. The Customer of the preceding activity becomes the Supplier of the successive activity. For example in Reinforced Concrete activity, the carpenter who prepared the formwork becomes the supplier for the steel bender handling the reinforcement phase.It is ideal that a Construction Company appoints a Quality Assurance/Control (QA/QC) Manager responsible for construction activities. As in Table 1, respondents rated Process management highest. It is the responsibility of QA/QC to ensure that employees adhere to the procedures and standard operating practices (SOPs). To ensure an efficient process management, he must manage the five M’s namely man, machine, method, measurement, and material. To attain continuous improvement, which is a necessity in TQM, QA manager must measure and control variation of process using statistical tools.
4.1.2. Management/Leadership Commitment
Leadership role in the implementation of TQM is very important. He is the driver directing the affairs of the company and therefore has to understand and be fully committed to the TQM principles. Out of the three main pillars of TQM as proposed in this framework, it is leadership commitment that drives TQM to a successful conclusion.Leadership must first believe in TQM and give support to its implementation. They are responsible for appointing a QA Manager who should liaise between the employees and process management. Leadership communication and involvement in training employees is a motivating factor that builds good environment for employees to thrive.
4.1.3. Customers Focus
The basic aim of TQM system is to produce goods and services consistently for a satisfied customer. These customers can be external (end users) or internal customers (within the company). To achieve this, one would have to know the needs of the customer and then adopt an appropriate framework and environment to achieve the desired needs at the lowest possible cost.The key to improving internal customer satisfaction is by adding value to employees and making them feel significant. Management strategic decisions to motivate, train, reward and recognizing staff improves the value of human resource of a construction company.
4.2. The Three Connectors
4.2.1. Continuous Improvement
One important step that differentiates TQM philosophy from other philosophies is the concept of continuous improvement. A cycle ensures improvement in products and services that ultimately improves the quality of works for a satisfied customer. It may follow Plan Do Check Act (PDCA) cycle [19]. Plan: Through measurement of results and feedback from customers, management defines quality problems identified in the construction activities. This step involves listing the problems and states the specific expected objectives. An analysis of the causes of problems and its influence on the quality based on data collected is essential at this phase. Finally, management devices an action plan that will prevent or improve the activity.Do: This phase involves the implementing the action plan proposed by management. If necessary, it requires training and provision of other material/tools to be able to implement plans. This calls for total management commitment for the TQM process improvement.Check: This is the monitoring and evaluation step to check the effects of measure taken.Act: The last phase of the cycle entails taking note of all effects and measurements. The results are documented and new standard for works is communicated to all stakeholders.
4.2.2. Training and Development
Results from the survey prove that formal training is not a regular exercise done in the Ghanaian Construction Industry. Training of employees is a key issue linking continuous improvement and process management. In Ghana, the low level of education for most of the artisans calls for management commitment to training programs that will improve the skills of artisans and to increase their knowledge in construction works. With new devised plans, it is the responsibility of management to ensure that employees are trained on new concepts. Other regular training sessions include training on customer satisfaction and data collection and analysis.
4.2.3. Supplier Management
The last connector between Customers and Process Management is the role of suppliers. The timely supply of the right quantity and quality inputs determines the final quality of product. As already indicated in the literature review and emphasised by [20], it is better to maintain long-term supplier relationships for loyalty and trust.To improve supplier performance, commitment and involvement of senior management of the Supplier Company and Construction Company is paramount. The synergy between the two knowing and understanding the benefits to be derived from a good product benefits both companies.
5. Conclusions
Research into Quality Management practices in the construction Industry has been increasing to improve on competitiveness, performance, and client satisfaction. Based on the above results on TQM critical success factors in the Construction Industry, a framework was proposed. The proposed framework was based on the EFQM model and supported on three (3) core pillars identified as Process Management, Management Commitment and Customer focus. It is similar to the three-legged stool whereby if one pillar fails the whole framework fails. Three connectors namely Continuous Improvement, Training and Development and Supplier Management links the pillars. These connectors sustain the effective and efficient implementation of the framework. This framework will provide valuable knowledge to Ghanaian Contractors who intends to apply TQM to improve quality of works which ultimately leads to sustainable competitive advantage and customer satisfaction. When adopted by the Construction Industry, this will revolutionise the industry leading to an increase in performance and value creation.
6. Recommendations
Recommendations on improvement of total quality that places value on its products and satisfies the customer in the implementation of TQM in the industry includes:i. Construction companies develop a Quality Culture as an organisational behaviour.ii. Management be committed and dedicated to the application of TQM in order to improve quality.iii. Training, motivation, and recognition are some of the factors that can improve internal customer satisfaction that achieves high productivity. Moreover, the use of accurate collected data should be encouraged to monitor performance of the construction activities.
References
[1] | Economist. (2000, January 15). Construction and the Internet. The Economist. |
[2] | Lad, J. and Beck, B. (2009). Construction Quality: The Key to Successful Capital Projects Delivery. Pharmceutical Engineering, Vol 29, No.6. |
[3] | Ahmed, S. (1993). An Integrated Total Quality Management (TQM) Model for the Construction Process. Ph.D. Dissertation, School of Civil & Environmental Engineering, Georgia Institute of Technology Atlanta, GA, USA. |
[4] | Ofori, G. (2012). Developing the Construction Industry in Ghana: The case for a Central Agency. Retrieved from http://www.buildingcontractorsgh.com. |
[5] | Harris, F., McCaffer, R. and Edum-Fotwe, F. (2006). Modern Construction Management. Blackwell Publishing. |
[6] | Harrington, J.H., & Voehl, F. (2012). Applying TQM to the Construction Industry. The TQM Journal, Vol. 24 No.4, pp 352-362. |
[7] | Arditi, D. and Gunaydin, H. M. (1997). Total quality management in the Construction Process. International Journal of Project Management, Vol 15 No.14, pp 235-243. |
[8] | Imbeah, K. A. (2012). Framework For The Implementation Of Total Quality Management(TQM) In Real Estate Firms In Ghana. MSc Thesis, Facullty Of Architecture And Building Technology, KNUST. |
[9] | Nawaz, T., and Ikram, A.A. (2013). Benefits and Impediments in Implementing Tqm in Pakistani Construction Industry. European Journal of Business and Management, Vol.5, No.4. |
[10] | Lau, A. W. T. and Tang, S. L.. (2009). A survey on the advancement of QA (quality assurance) to TQM (total quality management for construction contractors in Hong Kong. International Journal of Quality & Reliability Management, pp. 410-425. |
[11] | Bou-Llusar, J. C., . Escrig-Tena, A. B. , Roca-Puig, V. and Beltra, I. . (2009). An empirical assessment of the EFQM Excellence Model: Evaluation as a TQM framework relative to the MBNQA Model. Journal of Operations Management Vol. 27, Iss 1, pp 1–22. |
[12] | Brigitte Oger, D. E. (2002, May 3). Value measurement and value creation models in europe and the us: a comparison of the efqm excellence model andthe baldrige award criteria. Association Francophone de Comptabilité, pp. Volume 8, 99 to 115. |
[13] | Lai, L. (2002). Preliminary comparison study among ISO 9001, MBNQA and EFQM. Hong Kong: Hong Kong Society for Quality. |
[14] | Aalbregtse, R.J., Hejka, J.A., McNeley, P.K. (1991). Total quality management (TQM): how do you do it? International Journal of Quality & Reliability Management, Automation, Vol 38 No 8, pp30-32. |
[15] | Medori, D., Steeple, D. (2000). A framework for auditing and enhancing performance measurement systems. International Journal of Operations & Production Management, Vol. 20 No.5, pp.520-533. |
[16] | Enhassi et al. (2007). Factors Affecting Labour Productivity In Building Projects in the Gaza Strip. Journal of Civil Engineering and Management, Vol. XIII, No. 4. |
[17] | Deming, W. E. (2000). Out of the Crisis. MIT Press, Cambridge, MA. |
[18] | Deming, W. E. (1986). Out of the Crisis: Quality, Productivity and Competitive Position. Cambridge University Press, Cambridge. |