Dok Yen D. M. 1, Nana Tabi K. 2, Adinyira E. 2
1Department of Building Technology, Tamale Technical University, Tamale, Ghana
2Department of Building Technology, Kwame Nkrumah University of Science and Technology, Kumasi, Ghana
Correspondence to: Dok Yen D. M. , Department of Building Technology, Tamale Technical University, Tamale, Ghana.
Email: |  |
Copyright © 2018 The Author(s). Published by Scientific & Academic Publishing.
This work is licensed under the Creative Commons Attribution International License (CC BY).
http://creativecommons.org/licenses/by/4.0/

Abstract
Construction workers need adequate facilities such as toilets, washing facilities, places to eat, and storage place for clothing and so on. However, these basic requirements are often neglected or inadequate even where they are provided. The purpose of this paper was to assess the adequacy of welfare facilities on construction sites in Ghana. The population sample for this study consisted of all active construction sites at the Kotoka International Airport (KIA) vicinity. Eighty (89) copies of the questionnaire were administered to permanent workers (respondents) in five (5) construction sites with on-going construction activities for this study. Structured questionnaire and the census sampling technique were used to collect data. Descriptive statistics was employed to analyse primary data into percentages and frequencies. The study revealed that 70% construction sites in Ghana do not provide adequate welfare facilities for their site workers. Inadequate welfare facilities and poor maintenance turn to have negative effects on workers on site. The study recommends that construction firms should be committed to providing adequate welfare facilities at the sites. Clients through their consultants should ensure compliances with health and safety regulations and rules on site before approval is given to start actual construction. Welfare facilities on sites should be properly maintained, adequate number must be provided and the space should be well ventilated. Facilities should be accessible, properly identified, clean and hygienic to use. This research would go a long way to address the problem of inadequate welfare facilities on construction sites in Ghana.
Keywords:
Construction Sites, Welfare Facilities, Adequacy, Ghana
Cite this paper: Dok Yen D. M. , Nana Tabi K. , Adinyira E. , Assessing the Adequacy of Welfare Facilities on Construction Sites in Ghana, International Journal of Construction Engineering and Management , Vol. 7 No. 4, 2018, pp. 162-167. doi: 10.5923/j.ijcem.20180704.04.
1. Introduction
The provision welfare facilities provisions at construction sites play an essential role in worker’s well-being and health (Health and Safety Executive (HSE), 2010). The Construction (Design and Management) Regulations 2007, and Ghana Labour Act, 2003 (ACT651) defined well the basic legal requirement of welfare facilities. Adequate welfare facilities on construction sites can lead to direct impact on increase productivity of workers and profit. However, it can result in low output as well as lost of profit when workers are dissatisfied in with inadequate facilities. Construction Design and Management Regulations (CDM, 2015) posits that construction site needs to be provided with minimum welfare facilities such as suitable toilet and washing facilities, potable drinking water, facilities for storage and rest. Although the Labour Act 651 of Ghana, Section 118 makes it mandatory for employers to provide welfare facilities for construction site workers, nevertheless the basic requirements for welfare facilities are often inadequate and sometimes neglected in the worst case by contractors (HSE, 2010). Even though, Welfare facilities for workers such as a place to eat food and snacks, wash and clean their hands, visit wash room, a place to relax to recover from fatigue and so on can lead to increase worker output, it can as well turn to have a negative effect on workers if they are not adequately provided and maintained in a good state (Hiba, 1998). Experience and observation shows that there is very little study on construction sites in Ghana in relation to the adequacy of welfare facilities provisions for sites for workers hence the need for this study. This research aims to fill the gaps in literature on the inadequacy of welfare facilities, an aspect of health and safety regulations in the construction industry. The objective of the study was to assess the condition of site welfare facilities in the construction industry in Ghana, which will go a long way to improve the quality and adequacy of welfare facilities provisions by employers to their employees on construction sites in Ghana.
2. Conceptual Framework/Literature Review
Clients through their consultants must ensure that their contractors have arrangements put in place to provide adequate welfare facilities for construction workers. If the work is notifiable (that will last more than 30 days or will involve more than 500 person days of work) then they must ensure that construction work (including demolition) does not start until suitable welfare facilities are in place (CDM, 2007). Also, it is important for contractors to ensure that suitable, adequate welfare facilities are provided from the start and are maintained throughout the construction phase for workers under their control (CDM, 2007).
2.1. Planning Welfare Facilities
The availability of welfare facilities and their location on site and regular maintenance must be considered at the planning and preparation stages of every construction project before construction work (including demolition) starts. When planning welfare provisions for construction sites, it is important to consider for instance; the nature of the work to be carried out as well as the health risk factors that are associated with provision of showers where the project involves hazardous substances or very dirty work (For instance Sewer maintenance, dusty demolition activities, works with contaminated land or concrete pouring); the proximity of welfare facilities to workers; The project duration and number of different locations; The total number of people needed for the project; The cleaning and maintenance of the welfare facilities and so on and so forth (CDM, 2007).
2.2. Types of Welfare Facilities
Welfare facilities can be classified under two types namely; intra-mural and extra-mural. Intramural activities consist of facilities provided within the organisations or sites and this includes sick bay, supply of water, washing and bathing facilities, changing rooms, canteens, provision of safety measures, tasks which assist in improving the conditions of work, and such alike (Suresh and Vijayarani, 2015).
2.3. Main Parts of Welfare Facilities
The minimum welfare facilities required for construction sites have been broken down into five (5) main parts namely: sanitary conveniences, washing facilities, drinking water, changing rooms and lockers, and finally facilities for rest (CDM, 2015).
2.4. Toilets
Toilets must be adequately ventilated, lit and maintained in a clean condition. The frequency of cleaning will depend on the level of usage. The British Standard (BS) 6465 code of practice for the design of sanitary facilities and scales of provision of sanitary and associated appliances recommends that, there should be adequate number of toilet provisions on site for the workers. However, the number of facilities will always depend on the total number of workers on site, the type of facilities provided as well as the frequency of emptying. The BS6465 code (2006) recommends that a ratio of 1 toilet to 7 persons where portable toilets are emptied once a week. Also, it is possible for men and women to use the same toilet facilities where it is in a lockable room with partitioned from any urinals. Otherwise separate toilets should be provided. However, there should be adequate supplies of toilet paper available at all times (HSE, 2010). Proximity of toilet facilities to the workplace should be close as practicable as possible for workers to visit without travelling miles from their workplace. Similarly, the average number of toilets on an active site should be within a ratio of at least one is to ten (ratio 1: 10), that is, a fraction of 1 toilet to every 10 workers on site (Anon, 2010).
2.5. Washing Facilities
The HSE (2010) observes that sites should be provided with washing facilities closer to both changing rooms and toilet areas. However; it is advisable to place them next to rest areas if these are far from changing or toilet areas. Also, it is necessary to include a supply of clean, cold and hot or warm water; detergent/soap or other suitable means of cleaning such as; towels, suitable means of drying; sinks large enough to wash face, hands and forearms; sufficient ventilation and lighting for construction site workers for cases where workers are exposed to infectious substances, skin contamination by poisonous, or filth, oil or grease (ILO, 1992 and HSE, 2010).Again, men and women can share sinks used for washing hands, arms and face. Unisex shower facilities can also be provided where there are in separate, lockable rooms, possibly to be used by one person at a time (HSE, 2010). Furthermore, Basins or wash trough points should be provided with water and hot water where practicable, at the rate of at least one for each 10 people or fraction of 10 people. Water taps over a trough should be at least 500mm apart (Anon, 2010).
2.6. Showers
The Draft Facilities for construction sites recommends that a minimum of one shower for each workplace should be provided at the rate of at least one for each 25 people or a ratio of one bath to 25 people (Anon, 2010). However, a higher fraction should be provided for demolition, tunneling or dirty nature works, since this would mostly lead to frequent usage of shower on site. Notwithstanding, care should be taken to ensure separate adequate shower facilities are provided with privacy for the exclusive use of male or females. Nevertheless, where both males and females are employed, each shower cubicle should have a shower curtain or door, soap holder, and hot and cold water (HSE, 2010).
2.7. Drinking Water
The HSE (2010) argues that wholesome drinking water should be supplied on site and readily made available, stored and protected from possible pollution or contamination. Also, it should be ensured that it changes regularly enough to prevent the water from contamination or becoming stale. Furthermore, it may be necessary to clearly mark drinking water storage facilities on site to prevent it from being confused with other hazardous liquids or water which may not be wholesome for drinking. Cups and other drinking vessels should be provided at the outlet, unless the water is supplied in an upward jet, which can be drunk easily (For instance, a drinking fountain).
2.8. Changing Rooms and Lockers
There should be provisions made on site for secure storage facilities for personal clothing not worn on site and in protective clothing needed for site work. Both men and women should have the convenience and privacy to make their changes separately. Where there is a risk of protective site clothing contaminating provisions should be made for everyday clothing and items to be stored separately. Changing room areas should have a minimum floor area of 0.5 metres squared (m²) for each person changing clothes at any one time, this floor area should include bench seating, whilst excluding floors occupied by furniture, fittings, fixed storage space, or any other permanently fixed items, suitable bench seating in all change rooms should be at least 400 millimetres (mm) wide and 460mm in length for each person using the room at any one time. Also, adequate number of secure hooks should be provided for hanging clothes and be spaced at least 460mm apart (Anon, 2010).
3. Research Methodology
The researchers employed a descriptive survey method for this study. This study investigated the adequacy of worker satisfaction at the construction sites in relation to their welfare as earlier stated in the research objective. Administration of questionnaire was the tool adopted in the investigation in order that the right responses are obtained.
3.1. Population
The study population consisted of only permanent workers at the construction sites of D1K1 Building and Civil engineering contractors at Kotoka International Airport (KIA) vicinity. This area was chosen for the study because it was an area where a lot of development is ongoing in Accra and also the projects are undertaken by different construction firms, the justification is that these are workers who have been at the construction site for long and therefore could give better assessment and satisfaction of welfare facilities on the construction site.
3.2. Sample and Sampling Size
The researchers selected all active construction sites at the Kotoka International Airport (KIA). The numbers of active construction sites were eight (8) at the KIA vicinity, but only five sites gave permission to administer the questionnaire. The total numbers of permanent workers on the five sites were 89 persons and it was used as sample sizes. The respondents consist of Project Managers, Project Engineer, Supervisors, Quantity Surveyors, Foreman, Artisans, Helpers, Land Surveyors, Time Keepers and Store Keepers from the five sites.Table 1. Sampling Size from five Construction site 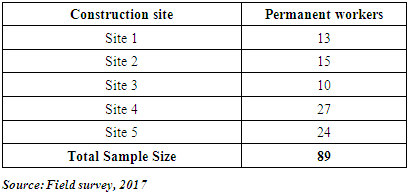 |
| |
|
4. Results and Discussion
This section presents the analysis and discussion of the survey data collected on five active construction sites at the Kotoka International Airport locality on the adequacy of welfare provision on site from eighty seven respondents.
4.1. Designation of Respondents
Table 2 gives an illustration of the designations of the various respondents selected for the data collection for this study. These consisted of project managers with a total frequency of 3 representing 3.4% of the total sample of all the five sites selected, project engineers were also made up to 5 respondents representing 5.7% of all the selected sites, a total number of 5 also representing 5.7% of quantity surveyors responded to the questionnaire. Supervisors, foremen, artisan, safety officers, land surveyors, store keepers and time keepers also from all the sites with their respective frequencies and percentages as follows were part of the respondents for this study; 10 (11.5%), 16 (18.4%), 31 (35.6%), 5 (5.7%), 4 (4.6%), 6 (6.9%) and 2 (2.3%). From the illustration on the table, it can be seen that artisans were the respondents with 31 (35.6%), this is probably due to the fact that artisans are mostly the in majority in most construction sites. However, the table also shows clearly that project managers were the least with only 3 respondents representing 3.4% of the total respondents; this is also due to the fact that mostly few project managers can be found or needed at the site as compared to other workers such as artisans and so on and so forth.Table 2. Designation of Respondents 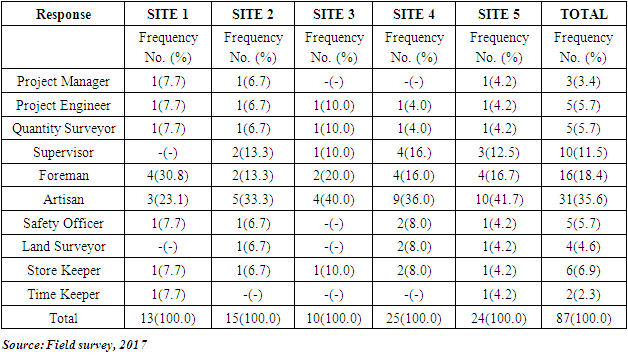 |
| |
|
4.2. Workers on Site
Table 3 shows the number of workers at the various five sites. The number of workers on a site dictates much on the quantity of welfare facilities to be provided for workers on site. Site 1 and 4 had the largest number of workers of over 101 workers at their respective sites, followed by Site 3 and 5 also with workers ranging between 76-100 at their respective sites, whilst Site 2 had the least number of workers with not more than 25 workers. With reference to the Workplace (Health, Safety and Welfare) Regulations 1992 more workers on site mean more facilities needed for adequacy. This implies Site 1 and 4 would need more facilities than Site 3 and 5 to make it adequate, whilst site 2 would also need fewer facilities than Site 3 and 5 to be adequate. Table 3. Workers on site 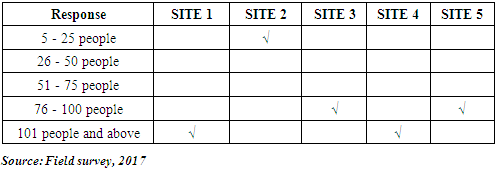 |
| |
|
4.3. Number of Welfare Facilities on Site
Table 4 illustrates the number of welfare facilities available at the five sites sampled for this study. Site 1 had 5 sanitary conveniences (toilets), 4 shower, 4 basins or sink, with no soap and towels, 1 safe drinking water, 1 changing room; 50 Lockers and so on as, can be seen in the table below. Site 2 had1sanitary convenience (toilets), 1 shower, 0 or no basins or sink, 1 soap and towel, 2 safe drinking water, 1 changing room, 4 Lockers and so on. Site 3 also had 3 sanitary conveniences (toilets), 4 shower, 2 basins or sink, 0 or no soap and towels, 1 safe drinking water, 0 or no changing room, 4 Lockers and so on as can be seen in table 4. Site 4 and 5 can be seen respectively in the table below in the order of Site 1, 2 and 3 facilities explained above.DiscussionsThe result of the study from table 4 shows that most of the Ghanaian construction sites do not have adequate welfare facilities on site. Site 1 for instance was supposed to have at least 10 toilets on site because of its large number of workers of ranging over 101 it is unfortunate to discover they had only 5 toilets on site. Site 4 had adequate numbers of toilets facilities on site; however, it failed to provide the adequate number of 1 toilet to 1 wash hand basin ratio since it had only 8 basins. Also, S3 and S4 had inadequate number of sanitary convenience (toilet) with 3 and 4 respectively, and 2 and 3 basins notwithstanding the fact that they both had workers ranging between 76-100. This, therefore, shows that the sites do not have adequate welfare provisions on site, since almost all the sites failed to meet the minimum welfare facilities required. The sites are considered inadequate and therefore the finding corroborate HSE’s (2010) argued that the average number of toilets on an active construction site should be within a ratio of at least one is to ten (ratio 1: 10), that is a fraction of 1 toilet to every 10 workers on site. BS6465 (2006) recommends a ratio of 1 toilet to 7 persons where portable toilets are emptied once a week. In addition the CDM regulations (2015) also recommends that the number of toilets provided should be equal to the number of basins or urinals, every 5 workers per 1 toilet, whilst every 6 to 25 workers on site should have 2 toilets, it means that more than 25 workers need to have an additional toilet for every additional 5-10 workers. The study concludes that at least 1basin or wash trough points should be provided for every 10 workers on site and shower for each workplace should be provided at the rate at least one for each 25 people (Anon, 2010). The results therefore, shows that the Ghanaian construction sites do not have adequate welfare facilities for their workers due to improper conditions of contracts with regards to the provision of adequate welfare facilities, it may also be as a result of lack of strict regulation governing site welfare provision on site. Table 4. Number of Welfare facilities on site 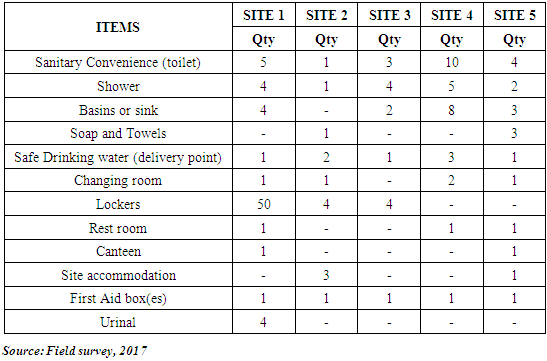 |
| |
|
4.4. Condition of Site Welfare Facilities
Table 5 shows the respondent’s view on the condition of welfare facilities at the various construction sites for this study. From the table, it can be seen that 61.5% of the respondents in site 1 (S1) are of the view that the site sanitary convenience (toilets) is bad, 23.1% of the workers think the toilets condition is very bad. Site 2 (S2), 60% of the respondents are not certain on how to describe the conditions of their toilets whiles 40% of the respondents are of the view that the toilets are in good condition. Site 3 (S3) shows that 60% of the respondents think their site sanitary convenience (toilet) are bad, whilst 30% thinks is in a good condition. However, Site 4 (S4) shows that they have good sanitary convenience (toilet) with 56% of their respondents confirming, even though, 36% of them think is bad. On the other hand, 62.5% of the respondents in Site 5 think their sanitary convenience (toilet) is bad for workers, whiles only 25% thinks is good.Discussion From the analysis, it can be seen that majority of the sites had bad sanitary conveniences (toilets) and this is shown clearly from the respondents from site S1, S3 & S5 recorded the highest percentage that is, 61.5%, 60% and 62.5 respectively as the level of inadequacy of sanitary convenience on the Ghanaian construction sites. However, it is surprising to see that S4 had the highest level of good sanitary conveniences even though, is one of the largest sites visited, one would have expected that they had more sanitary problems, but shows rather better condition. This, therefore, goes to justify the fact that poor on site sanitary condition cannot be blamed on a large number of workers on site because is suppose to be part of the contract condition. Although no site recorded a very good condition, on the contrary S1 recorded a very bad condition of sanitary conveniences implying that the Ghanaian construction site cannot boast of very good sanitary conveniences, but, there are however, very bad sanitary conditions on some construction sites to be worried about. Table 5. State of Sanitary convenience (toilet) 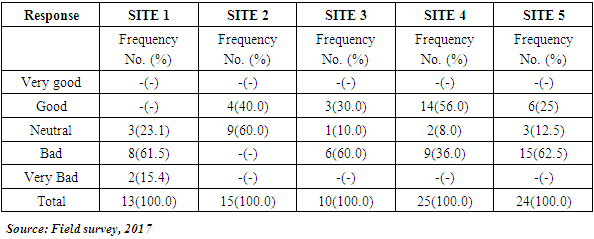 |
| |
|
5. Conclusions
The result from the study shows that most (average of 68%) Ghanaian constructions sites do not have adequate welfare facilities on site. Most sites do not have the average required number of welfare facilities for their workers and also in most cases the limited facilities on site are not in good conditions for workers welfare status. Most sites have less than half of the required number of facilities to be provided. The study reveals that 70% of the construction sites in Ghana do not meet the welfare facilities as required by the Labour Act 651, the Factory, office and Stores Act 1970, the National Labour Commission of Ghana, as well as the workplace health, safety and welfare regulations.
6. Recommendations
This study recommends that construction firms should be dedicated to the provisions of adequate welfare facilities on site to enhance the safety and welfare of their workers. Clients through their consultants should insist on ensuring that adequate minimum welfare facilities are provided on site as part of the preliminary work before approval is given for the commencement of the main construction works. Also, policy makers and construction professional bodies should do regular site checks on welfare facilities needed to be provided to see if they're up to standards for site welfare for workers.
References
[1] | Anon, (2010), Facilities For Construction Sites, Draft code of practice, https://submissions.swa.gov.au/SWAforms/FacilitiesForConstructionSites. [accessed 15th, June, 2017]. |
[2] | British Standard Code 6465-1 (2006), ‘Sanitary installations. Code of practice for the design of sanitary facilities and scales of provision of sanitary and associated appliances’, https://www.thenbs.com/PublicationIndex/documents/details?Pub=BSI&DocID, [accessed 20th June, 2017]. |
[3] | Construction Design and Management Regulations, (2007), ‘Provision of welfare facilities during construction work HSE information’, Available at: http: //www.hse.gov.uk/construction. [accessed 15th June, 2017]. |
[4] | Construction Design and Management Regulations (2015), Managing health and safety in construction. http://www.hse.gov.uk/pubns/books/l153.htm [accessed 16th June, 2017]. |
[5] | Cotton, A. P., Sohail, M., and Scott, R. E. (2005), “Towards improved labour standards for construction of minor works in low income countries. Engineering, Construction and Architectural Management, vol. 12 no.6, pp. 617-632. |
[6] | Government of Ghana. (2003), “Factories, Offices and Shops Act, 1970”, Accra, Ghana. |
[7] | Ghana Labour Act. (2003), “Labour Act 651”, National Labour Commission, Accra, Ghana. |
[8] | Hiba, J. C. (1998), “Improving working conditions and productivity in the garment Industry”, Geneva: International Labour Office Publications. |
[9] | Health and Safety Executive (2013), Workplace (health, safety and welfare) Regulations 1992, 2 nd Edition: 57. |
[10] | Health and Safety Executive (2007), “Welfare at work”, Guidance for employers on welfare Provisions, HTTP: www.hse.gov.uk/pubns/indg293.pdf, [accessed 5th April, 2016]. |
[11] | Health and Safety Executive (2010), Provision of welfare facilities during construction Work, Construction Information Sheet 59, http:www.hse.gov.uk/pubns/cis62.pdf. [accessed 6th April, 2016]. |
[12] | International Labour Office (1992), “Safety and Health in construction; An ILO code of practice”, Geneva: International Labour Office Publications. |
[13] | Laryea, S. and Sarfo M. (2010), “Health and safety on construction sites in Ghana, In: The Construction, Building and Real Estate Research Conference of the Royal Institution of Chartered Surveyors, Dauphine University, Paris, France”, http://centaur.reading.ac.uk/16289/, [accessed 10th May, 2016]. |
[14] | Suresh, G. and Vijayarani, K., (2015),” Intra-mural and extra-mural welfare facilities”, International Journal of World Research, Vol: I Issue XX. |