Sohail Afzal, Zishan Raza Khan
Department of Civil Engineering, Integral University, Lucknow, India
Correspondence to: Sohail Afzal, Department of Civil Engineering, Integral University, Lucknow, India.
Email: |  |
Copyright © 2018 The Author(s). Published by Scientific & Academic Publishing.
This work is licensed under the Creative Commons Attribution International License (CC BY).
http://creativecommons.org/licenses/by/4.0/

Abstract
Ready- mix concrete is the basic construction material used in large quantities for construction purpose all around the world. RMC is only productive when it is delivered in time to the customers. The delivery is usually affected by long hauls, delays due to traffic or queues. This paper reviewed factors on which previous researches were done like travelling distance, traffic conditions, time split, delays, route optimization, late deliveries, pre-owned or rented trucks and others miscellaneous factors and the also the techniques used to overcome these factors. Further going it also focused on untouched factors like issues caused by drivers end.
Keywords:
RMC Delivery, Factors, Time split, Scheduling problems, Route, Distance, Late deliveries
Cite this paper: Sohail Afzal, Zishan Raza Khan, A Review Paper on Factors Affecting Ready- Mix Concrete Delivery Pattern, International Journal of Construction Engineering and Management , Vol. 7 No. 3, 2018, pp. 97-100. doi: 10.5923/j.ijcem.20180703.01.
1. Introduction
Ready-mix concrete is an important construction material used widely all around the world prepared according to a set engineered mix design. Ready-mix concrete or majorly referred as RMC is specifically manufactured for customer's construction projects as per specification provided by the customer. RMC is a mixture of Portland cement, water and aggregates: sand, gravel, or crushed stone. Aggregates used in RMC manufacturing should be properly washed. Ready-mix concrete is bought and sold by volume - usually expressed in cubic meters.The future of RMC in India is very bright and RMC is easily available not only in metro cities of India but also in smaller town as well. It is estimated that in the coming ten to fifteen years, number of mix concrete plants will come up in different parts of the country and nearly ten to fifteen percent of cement consumption will be through ready mix concrete. Government in association with many local bodies is planning to make future prospects for installing new RMC plants all over India. In these prospects it includes allotment of lands at lower rates and giving some relaxation in taxes to RMC owners.Though RMC plant is not a new technology, we have observed that large projects have been using captive batching plants. These captive plants are producing quality concrete for their work. Now even in small projects small users are also using the benefits of the quality and reliability of RMC plants which was once only limited to large projects.
2. RMC Transportation Process
Table 1. Factors and sub-factors that affect schedule (Feng etal, 2006; Srichandum etal, 2010, Pan Hao 2012) 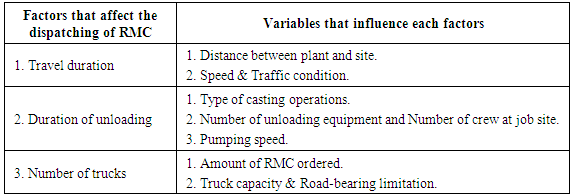 |
| |
|
When concrete is ready in plant, the next step is its transportation. For transportation, concrete mixes are collected in the trucks. To deliver concrete mix on time one has to plan the routing and scheduling for the trucks. Delays and hauls caused by traffic conditions, long distance, time split and other factors results in loss of concrete. As soon as the truck is loaded it should be immediately dispatched to the site. RMC delivery is also affected by skill of the crew especially the driver. To perform a successful delivery of concrete persons involved at each level of production, dispatching and transportation should be in proper sync. Choosing clients and his demand of order for RMC also affects delivery schedule of concrete. Distance between plant and site determines the travel duration of delivery. Increasing numbers of trucks for delivery at plant and site also affects the delivery time as it makes the both plant and site a little congested.MAJOR ISSUES IN RMC DELIVERYWe know that at RMC plant quality concrete is manufactured but this quality concrete has to be transported to the site for its final use but two major issues always arises during RMC delivery:a. Long hauls and delays involved while transporting the concrete mixes which can decrease the workability of concrete that needs to be maintained till pumping.b. Concrete pump has to maintain its pump able consistency so that it can pump the concrete mix at desired rate which not only includes the workability but also the pump ability characteristics.
3. Literature Review
The Ready Mixed Concrete in India on commercial basis started in 1994 and has achieved about 2% conversion from the site-mixed concrete by the year 2001. It is heartening that the acceptability of Ready mixed concrete is increasing though at a slow pace. The entry of foreign firms and major Indian cement producers in this field are likely to provide necessary boost to this industry in the future. The growth prospects of Ready-mixed concrete are enormous, provided requisite support is given by the regulatory authorities, consumers and decision makers. At the present, the cost differential between Ready-mixed concrete and site mixed concrete is proving major constraint in its growth. This problem will be resolved with the increasing awareness about the advantages of RMC by the end consumers [1] A K Jain, (2002).About concrete industry companies and their scheduling problem which they are facing on daily basis. Working on feasible solutions such as hybrid approach and variable neighbored search moreover he concentrated integer multi commodity flow. All these solutions were approached for computational results showing growth in RMC delivery. [2] Verena Schmid etal, (2009). A model for costing production and transportation of ready-mix-concrete (RMC) is prepared based on type of the mix and customer site information. They used the concept of activity based costing (ABC). They mainly focused on a function of traveling distance, traffic factor, and demand. Volume- based discounts, penalty for late delivery, and cost of mix spoilage. Activity based management (ABM) was used to improve the financial performance of the company. They made several activity charts on expense that includes maintenance work, administration work, accounting work, transportation work and preparation of raw material. They used several matrix model and interrelated the activities on different framework models [3] O. Al-Araidaha etal, (2012). Optimization of route in terms of delivery pattern is a major concern for RMC delivery performance. He took five to six owned trucks generally as an example for plant owners and two or three extra trucks for high demands. He also assumed that some owners rent the trucks. He primarily focuses upon the route pattern for these due to increase demand of RMC by infrastructure growth and limited number of trucks by plant owners [4] Jishnu Gohel etal, (2017).Survey on the vehicle routing problem with multiple depots MDVRP was done between 1988 and 2014 which includes studies like time split, delivery, heterogeneous fleet, periodical deliveries. This also classifies Finding an optimal (or at least very good) route for vehicles delivering products to customers is one of the key functions in any logistics systems [5] Jairo R Montaya Torres etal, (2014). Talking about importance of RMC as the primary material for construction, so he targeted on customers demand and delivery pattern. He worked on various constraints and he assess on alternate stratergies for truck allocation and production planning [6] Sławomir Biruk, (2015).RMC delivery and dispatching operations is monitored by integrated navigation system, based on Global Positioning System (GPS)/Dead Reckoning (DR)/Bluetooth Beacon (BB) and Global System for Mobile Communication (GSM) technologies [7] Ming Lu, (2006). For RMC dispatching operations two kinds of techniques have been implemented to deal with this problem: (i) evolutionary techniques and (ii) numerical techniques. Robust Genetic Algorithm (Robust-GA) and Column Generation (CG) were selected and tested with different sizes of RMC problems [8] Vivek Periaraj etal, (2014). Ready-Mixed Concrete Suppliers face operational problems such as the acquisition of raw materials, scheduling of production facilities, and the transportation of concrete. To curb these concrete delivery issues this paper prepares approaches that include a Mixed Integer Programming (MIP) model and a Constraint Programming model [9] J. Kinable etal, (2010). A network flow model was created to minimize the total cost genetic algorithm for integrated scheduling model. Algorithm is better than combinations of priority rules. Affection of fleet size, cost and time windows is reported in three sequences (construction sites, delivery order and vehicle IDs) operators work on the sequences of construction sites [10] Yang Zhang etal, (2014). Dispatching operations in this study includes time windows and demand postponement, as well as the external cost of transport, in a multi-objective programming model. It includes small to medium concrete plants and how to make their operation cost effective and thus making them to achieve better customer service [11] Jenhung Wang etal, (2010).The objective of the study is to determine of the concrete truck fleet size that fits best the project needs. Data collection is done to define activity durations and also alternative scenarios are being examined by the use of sensitivity analysis. Simulation outputs are declared against the actual data and the actual implications of the deployed truck fleet size is examined against utilization and productivity criteria [12] Antonios Panas etal, (2012). Dispatching of RMC is determined by application of production scheduling techniques. Earliest Due Date (EDD) and First-Come, First-Served (FCFS) are two techniques of priority rules used for RMC scheduling in providing more precision and accuracy of related inputs which can be used in order improve efficiency of the entire RMC process. GIS–Geographic Information Systems software (ArcGIS) is used to calculate distances, travel speed and travel times [13] Ladda Tanwanichkul etal, (2016). An urban area was divided into 7 districts that include 4 concrete batch plants that have issues like time split, traffic conditions, and delays. Linear programming and genetic algorithm were applied to solve this problem and compared each other under the same condition which is applied on both the cases. The result depicts linear programming is more efficient for this study because constraints and variables are limited. [14] Ugur Albayrak etal, (2016).
4. Inference
The existing problems in the RMC delivery process are long hauls and delay because of traffic conditions which caused the major hindrance in RMC delivery. The above mentioned researches give us a brief account of how issues such as scheduling problems, fleet size, time split, amount of RMC ordered, type of casting operations, number of unloading equipment, number of crew at job site, pumping speed, truck capacity, road conditions and routing problems are tackled by using various operational technologies.
5. Methodology
With the idea that RMC delivery operations can be extremely profitable if they are efficiently tracked, through several books and journals, it was concluded to solve the problem of poor operational performance, the indicators of RMC supply performance are examined from the suppliers and contractors perspectives. Through personal interviews and questionnaire survey factors are highlighted which affects the delivery of RMC. These factors are fleet size, distance, time of delivery (peak hours, daytime and nighttime), direction, weather conditions, drivers skill and road. Researches based on these factors are monitored and reviewed by authors using techniques like Robust Genetic Algorithm (Robust-GA) and Column Generation (CG), GIS–Geographic Information Systems software (ArcGIS), Mixed Integer Programming (MIP) model and a Constraint Programming model, operations is monitored by integrated navigation system, Global Positioning System (GPS)/Dead Reckoning (DR)/Bluetooth Beacon (BB) and Global System for Mobile Communication (GSM) technologies and others.
6. Conclusions
From this paper, it have been able to clearly conclude that factors which affects the delivery of RMC are:-1. Distance between plant and site2. Fleet size3. Weather conditions4. Route5. Skill of crew6. Road conditionThe support tools used to plan transport routes and schedule production of the mix are rarely utilized by the plants. The quantity of fulfilled orders, betterment in truck utilization rates and clients satisfaction can be increased by implementing systems like these. In the highly demanded market of ready mix production, this would also help in achieving competitive advantage. Changes in transport times during the day related with traffic conditions, allowing for availability of trucks and pumps of various capacity is what the further research will be aimed at. The model divides the cost into on-floor delivery and penalties related cost.
References
[1] | A K Jain, 2002, 29 - 30 August Ready-Mixed Concrete growth prospects in India-, 27th Conference on OUR WORLD IN CONCRETE & STRUCTURES, Singapore Article Online Id: 100027032. Page-1-3. |
[2] | Verena Schmid, etal 2009, A Hybrid Solution Approach for Ready-Mixed Concrete Delivery. <https://pubsonline.informs.org/doi/abs/10.1287/trsc.1080.0249.> |
[3] | O. Al-Araidaha etal 2012, Costing of the Production and Delivery of Ready-Mix-Concrete - Jordan Journal of Mechanical and Industrial Engineering - Volume 164 6, Number 2 (ISSN 1995-6665)2012. |
[4] | Jishnu Gohel etal, 2017, 1st-2nd August. Route Optimization for delivery of (RMC): a literature review - Proceedings of 67th IASTEM International Conference, Dubai, UAE. |
[5] | Jairo R Montaya Torres etal, 2014, A literature review on vehicle routing problem with multiple depot –www.elsevier.com/locate/caie. |
[6] | Sławomir Biruk 2015, Dispatching concrete trucks using simulation method Budow nictwo i Architektura 14(2) (2015) 5-10. |
[7] | Ming Lu etal, 2006, Real-time Monitoring of Ready-Mixed Concrete Delivery with an Integrated Navigation System- Journal of Global Positioning Systems (2006) Vol. 5, No. 1-2:105-109. |
[8] | Vivek Periaraj etal, 2014, Solving Ready Mixed Concrete Delivery Problems: Evolutionary Comparison between Column Generation and Robust Genetic Algorithm -, computing in civil and building engineering ©asce. |
[9] | J Kinable etal 2010, The concrete delivery problem- <https://www.sciencedirect.com/science/article/pii/S0305054814000434?via%3Dihub.> |
[10] | Yang Zhang etal 2014, Integrated scheduling of ready-mixed concrete production and delivery-, <https://www.sciencedirect.com/science/article/pii/S0926580514001836?via%3Dihub.> |
[11] | Jenhung Wang etal 2010, Dispatching ready mixed concrete trucks under demand postponement and weight limit regulation- Automation in Construction, 19(6), 798-807. DOI: 10.1016/j.autcon.2010.05.002. |
[12] | Antonios Panasa etal, 2012, Simulation-Based Concrete Truck-Mixers Fleet Size Determination for On-Site Batch Plant Operation- 26th IPMA World Congress, Crete, Greece. |
[13] | Ladda Tanwanichkul etal, 2016, Application of production scheduling techniques for dispatching ready-mixed concrete- International Journal of Technology (2016) 7: 1163-1170 ISSN 2086-9614. |
[14] | Ugur Albayrak etal, 2016, 10, October Investigation of Ready Mixed Concrete Transportation Problem Using Linear Programming and Genetic Algorithm- Civil Engineering Journal Vol. 2, No. |
[15] | Pan HAO 2012, October Improvement of RMC Delivery Operation Performance through Inventory Control Based on Discrete Event Simulation-, School of Civil and Environmental Engineering The University of New South Wales. Table 1. |