Shant A. Dajadian1, Daphene C. Koch2
1Bechtel Corp, Gladstone, Queensland, Australia
2Building Construction Management, Purdue University, West Lafayette, USA
Correspondence to: Shant A. Dajadian, Bechtel Corp, Gladstone, Queensland, Australia.
Email: |  |
Copyright © 2014 Scientific & Academic Publishing. All Rights Reserved.
Abstract
Waste has been considered a major problem in the construction industry for its financial and environmental impacts. The attention to Construction and Demolition (C&D) waste has been increasing in the past 20 years from both researchers and specialists around the world. Large numbers of articles have been published in journals related to waste management (WM) discussing sources of waste, cost of waste, and how to minimize waste. A survey of current models used to minimize waste and increase their competition in the global market was reviewed. It is found that many countries have developed regulations to minimize C&D waste. The purpose of this study is to understand the general view of construction waste, cost of waste, sources of waste, and models of waste management. A web based survey design with 20 questions that was distributed to 400 construction professionals from supervisors, field engineer, safety professional, and site managers. The completed survey results were processed; graphs and charts were prepared and finally conclusion was developed and two WM models were recommended, the first is the use of WM subcontractor and the second is to have a WM department within the company.
Keywords:
Construction waste, C&D waste, Waste management, Environment
Cite this paper: Shant A. Dajadian, Daphene C. Koch, Waste Management Models and Their Applications on Construction Sites, International Journal of Construction Engineering and Management , Vol. 3 No. 3, 2014, pp. 91-98. doi: 10.5923/j.ijcem.20140303.02.
1. Introduction
The construction industry is a valuable part of the world economy. Projects can create new public facilities and renovate existing ones to increase the overall living standards. However, each project creates construction waste which can increase project cost and add to environmental pollution. Construction waste issues have become more a part of the focus on a project due to cost and environmental awareness. In addition to its negative impact on the environment by generating waste, consuming landfills, and natural unrecoverable resources, construction project costs increase significantly due to the amount of waste. Environmental agencies have been assessing the waste produced from the construction industry. A report from the United States Environmental Protection Agency reports that 136 million tons of waste was generated in 2002 [1]. In an attempt to protect the environment and to improve sustainability of the construction industry, regulations have been developed in many countries to minimize construction waste. One example is the United Nations Framework Convention on Climate Change (UNFCCC) which has been gradually begun to have enforcing laws and regulations relevant to waste [2]. Lean construction techniques also outline procedures relate to elimination of waste. This project will investigate the amount of waste generated in several countries around the world, will explain types and cost of waste, and will list the causes of construction waste.
2. Problem Statement
Due to the increasing number of construction project throughout the world, it is logical that there was an increase in the construction waste, which is mainly disposed in landfills. This grow would enhance the need for having an effective waste management plan and drive towards that as a requirement by all the contractors and construction firms. The completion of projects within budget and schedule are the goal of construction companies. Any additional efficiencies result in profit.Over production, poor handling, incorrect storage, incorrect ordering, design change, manufacturing defects and rework are factors that contribute in material waste. It has been recorded that 1-1.2 million dollars per project can be lost on waste [2]. Other factors that contribute in a way or another in the generating of construction waste are lack of training and poor craftsmanship. Due to the fact that raw materials wastage, ineffective management of waste is common on construction sites, waste minimization became an important area of concern in the construction industry. Waste Management on project sites had become a major focus due to construction waste’s negative effect on land depletion and deterioration, energy consumption and noise pollution, and it has been considered to be a major source of environmental pollution for its solid waste generation and dust and gas emission. All of these issues highlight the needs of waste management programs for construction companies and this paper analyses few of the WM models that are being implemented on construction sites.
3. Literature Review
Construction waste issues have become more a part of the focus on a project due to cost and environmental awareness. Types of construction waste, cost of waste, causes of C&D waste, models of WM are the topics that will be covered in this literature review, as well as the benefits of having better WM.
3.1. Construction Waste
Many researchers have concentrated on the amount of waste and debris generated from construction project to show the importance of managing the waste generated by construction projects. Construction industry generates waste that has been calculated to include● Australia generates about 14 million tons of waste [3]. ● United States generates approximately 136 million tons of construction waste [1]. ● United Kingdom generates about 70 million tons of construction waste every year [1]. ● Holland generates around 4.25 thousand million tons of waste each year [4].
3.2. Types of Construction Waste
It is very well recognized that the construction industry is not environmentally friendly. A part from consuming large amount of natural resources, it has been criticized to generate high level of solid waste.Construction Sector consumes 25% of virgin wood and 40% of raw stone, gravel and sand globally every year [5]. Other than solid waste; poor quality that causes re-work, material double handling, schedule delays, commuting within the job, waiting for decision and poor constructability are considered other types of construction waste. Construction waste can be grouped into two principle components [6];1) Time wastes which includes waiting periods, stoppages, clarifications, variation in information, rework, ineffective work, delays in plan activities, and abnormal wear of equipment.2) Material wastes comprising over ordering, overproduction, wrong handling, wrong storage, and manufacturing defects.The waste produced by the burning trash furnaces includes more than 200 different dioxin compounds and generates large amount of CO2 emission.Demolition wreckage and package waste may be categorized in three groups in the construction process. Due to the variety of activities on construction sites, construction waste may include plywood, platform, brick, paint, metal, copper, aluminium, concrete, electrical cable, rebar, paper, plastic, electrical device, steel, and much more.
3.3. Cost of Waste
Due to the different types of activities on construction projects, different types of waste are generate that cause the projects millions of dollars every year, which if it was managed properly or minimized, construction contractors could have been saving a tremendous amounts of money and be more profitable companies.The percentage of total purchased materials that ends up as waste is about 9% and from 1% to 10% of every single purchased construction material leaves the site as solid waste (by weight) in the Dutch construction industry [7]. At the end of every project, there will be at least 20% of the purchased material that is unused; this material ends up as waste in most cases and since material accounts for more than 50% of a construction project cost. According to a report by Hong Kong’s Environmental Protection Department, about 2900 tons of construction waste was received at landfills per day in 2007 [1]. Minimizing the over ordering will reduce the amount of waste significantly and thus reduces the use of landfills. Each year construction companies in the United Kingdom pay about £200 million in landfill taxes.In addition to its impact on the economic damages, construction waste has a significant impact on environmental damages. Construction industry consumes annually about 40% of the natural resources around the world. Due to grow in the construction industry, construction waste is also increasing rapidly, half of this waste is excluded from the initial treatment and are disposed directly in landfills.
3.4. Causes of C&D Waste
Literatures that covered C&D waste generation indicated a number of construction waste generation sources that continues throughout a project from start to completion. The main six causes of waste are design, procurement, materials handling, operation, residual, and other [7].Late design change is considered to be a major cause of waste on construction sites, but there are other factors that are considered to be C&D waste source, incomplete or late information, poor material management, incompetent labour, and damage during transportation are examples of C&D waste sources. Recently, several studies have indicated the importance of the design stage. It has been estimated that 33% of on-site waste is due to architects’ failure to implement waste reduction measures during design stage [8]. A list of origins and causes of construction waste is shown in table 1 [9].Table 1. Origins and causes of construction waste 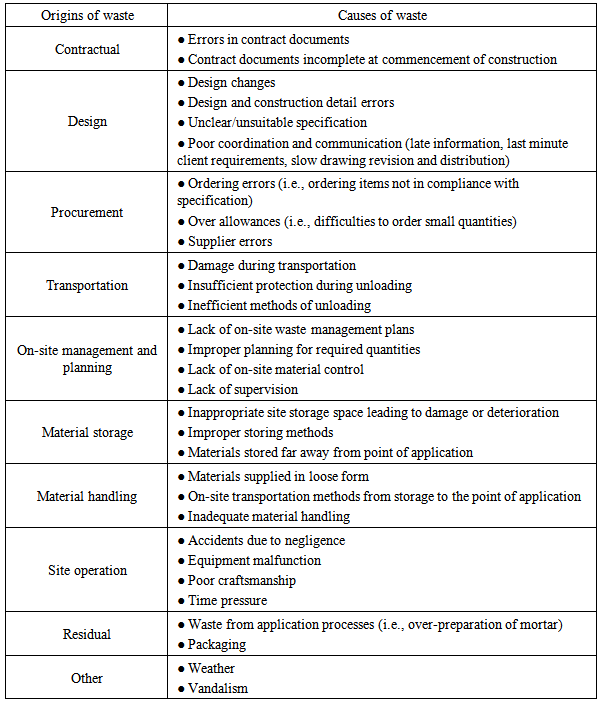 |
| |
|
4. Models of Waste Management
In this section we will show briefly some of the waste management models and the ability to use them on construction sites. The first 3 models are the average cost estimation model, equivalent method of cost estimation, and activity-based costing model [10].1. Average cost estimation modelThe average cost estimation model can be used when considering a company producing one product only. It involves simply dividing the total cost for the period in question by the total production during that period, resulting in the cost per ton, or litre etc.This study proposes that when applying the average cost estimation method, the cost of a given waste fraction is determined by multiplying equation 1, by the actual or budgeted average cost for the period in question. | (1) |
A = quantity of a certain waste producedB = quantity of normal product output, andC = the sum of the quantities of all the different waste produced2. Equivalent method of cost estimationThis model can be applied to companies producing a limited number of different products, all based on mainly the same raw material and having similar manufacturing process.ER = (normal cost per unit for a given product) / (normal cost per unit for the product with the lowest cost per unit). Where ER = equivalent rate.3. Activity-based costing modelThe activity-based costing (ABC) model is based on the fact that if many of the costs arise from factors that are non-volume based, the ABC model is clearly applicable. The goal is to trace costs to products or services instead of arbitrarily allocating them.The models shown above are all based on several mathematical equations and steps that should be followed, number to be input, and calculations to be performed in order to get results which are not very applicable on construction sites, they are applicable for industrial management but not necessarily applicable for waste management purposes.4. This model was proposed for evaluating the environmental, economic and social sustainability of demolition waste [1]. By inputting data obtained from a practical case into the established model, social impacts of demolition waste were studies. The reason of scant use of this model is because of the low priority of the social influence of performing construction waste management on construction sites, and because of social impact is not always amenable to empirical measurement.The following waste management models are applicable to construction sites and projects.5. Investment in C&D waste managementInvestment in C&D waste management can help promote waste management practices in many ways by assigning workers responsible for on-site waste collection, sorting and handling, purchasing equipment and machines for waste management, developing and implementing waste management plans, motivating practitioners to minimize C&D waste and improving operatives’ skills of waste handling through vocational training. The financial reward of this model was perceived as a key incentive driving waste reduction during a construction project [9]. 6. Site space for performing waste managementSite space refers to the space used for on-site waste collection, sorting and handling. Since C&D waste is often the mixture of inert and organic materials, and mixed and contaminated waste is not suitable for reuse or recycling but generally disposed of at landfills directly [11], on-site sorting is effective in achieving a higher rate of waste reuse and recycling. According to Yuan (2013) site space was found to be one of the most important factors when selecting on-site sorting schemes. Without a space layout pre-planned for waste collection and sorting, the temporary placement of sorting facilities and implementation of waste collection and sorting activities might disarrange other construction activities [12].The pollution resulted from the huge amount of C&D waste to the surroundings would be greatly lessened through effective on-site sorting [11], therefore sufficient on-site space for waste sorting is important to maximizing C&D waste reuse and recycling.7. The waste contractorThe use of a waste contractor or waste transportation firm with a primary responsibility to provision of waste collection bins and labelling of the bins to suit the waste stream identified in the contractor’s waste management plan is highly recommended [4]. The waste material can become the property of the waste removal contractor and any rebates paid on recyclable products should be made to the account of the waste removal contractor. 8. Eliminating Waste This model is also known as designing out waste, which is the technique of minimizing waste by avoiding, eliminating, and reducing waste at its source. Designing out waste at the earliest stages of the construction process offers the greatest opportunities for waste minimization [13].Some waste generated in the process of construction can be eliminated by using durable modular metal form systems for use in concrete construction may be selected on the basis of being readily demountable and reusable on other projects. Eliminating wood waste associated with formwork fabricated of plywood and dimensional lumber can be beneficial to reduce impacts on human health and the environment [14]. Reducing waste means more efficient use of materials by adopting efficient practices, less product will be purchased which will lead to less generation of waste and thus cost savings on material and waste disposal.9. Three Rs’ (3Rs)This model refers to the 3Rs’ of Reduce, Reuse, and Recycle. The 3Rs’ is meant to their desirability [15]. Reduction is considered as the most effective and efficient method for managing C&D waste. By reducing waste generation the cost of waste transportation and disposal will be reduced as well. The reuse of material that is considered waste is another effective method of reducing waste that is disposed on landfills and thus a major cost savings for construction projects. The third part of this model encourages the use of recycled material. Using recycle material will protect the environment and reduces the use of unrecovered natural resources.10. PrefabricationThis model uses prefabrication and Industrialized Building Systems (IBS) to reduce waste generation and management problems [16]. Advantages of applying prefabrication in the building and construction activities include enhance integrity on the building design and construction, reduction unskilled workers; reduce construction cost, fixed design at early stage of design, better supervision, promote safer and more organized construction site and improve environmental performance through waste minimization.Having a better WM, a construction company can reduce its cost of waste disposal as well as onsite risks and environmental pollution. The company that has better construction waste record will have better chance to meet the government regulations and contractual obligations. To support the idea of the WM and to reach to the best conclusion and give the best recommendation a survey questionnaire was prepared as explained next.
5. Data Methodology
Survey was designed to collect information to understand the level of support related to WM on a construction site. Through research of survey development, a survey of 20 questions was prepared and submitted to Purdue University’s Institutional Review Board (IRB). The IRB approved the questions and the survey was distributed to 400 construction professionals. The survey was distributed to employees with the titles of field engineer, superintendent, supervisor, general foreman, project control, safety professional, site manager, construction business owner, designer, and project manager. The list was developed by selecting 40 personnel from 10 titles randomly, the total number of selected personnel to whom the survey was sent equaled to 400. The survey was available for over 2 months to allow sufficient time for everybody to participate; the goal was to reach at least 100 responses. The total number of completed surveys included 96 construction professionals; this is 24% of total surveys sent out. Once the survey was closed data collection process started, conclusion and recommendation was developed accordingly. Appendix 2 lists the survey questions and their answers.The survey included demographic data and pointed questions to determine the general knowledge of the people working in the field related to waste management. Demographic information included participant’s personal experience, the size of the company, and the business type that the respondent’s company performs, then the survey tried to explore the construction projects through a number of questions to discover the types of waste containers, the discipline that generates the most waste on construction sites, and the advantage to use recycled material on construction sites. The third part of questions concentrated on the reasons of supporting WM, the availability of sufficient training, and the company’s WM plan. The last group of questions addressed the penalties and the clause that relates to waste management. Appendix 1 illustrates the survey questions.
6. Results
Demographics show that 52% of the participants have worked in the industry for more than 10 years and that 79% of them work for large companies of 5000 employees or more, these companies vary from construction as the highest percentage 96%, procurement 79%, design 71%, and transportation and recruiting with lower percentages44% and 38% respectively. Fig1 shows the distribution of experience of the responses.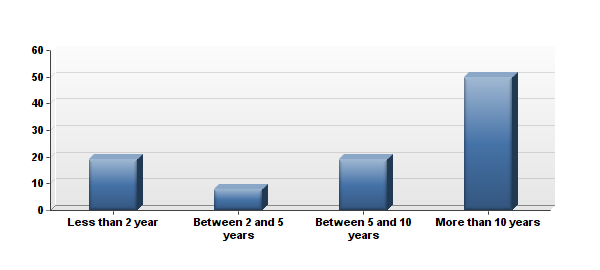 | Figure 1. Distribution of experience of the respondents |
Majority of these companies have WM procedure 92% and that 99% of the participants support WM, however only 86% of the participants support WM because it protects the environment while 7% support WM because it’s a cost savings. Respondents work on projects which 96% amongst use separate container for different waste from metal bin 91%, oil drum 64% to cable and concrete bin 40% and 38% respectively. Nearly half of the respondents 49% agree that the waste is disposed daily on project sites while 33% indicated that the waste is disposed on weekly basis, bi-weekly and monthly got lower results with 5% and 1% respectively, The percentage of people who didn’t know the schedule of waste disposal was 12%. Fig 2 shows the time interval waste disposal on construction sites.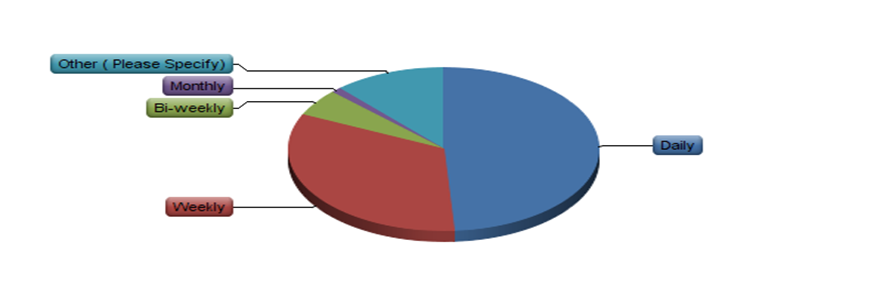 | Figure 2. Time interval of the waste disposal on construction sites |
The company’s encouragement to the practice of WM is very important factor in our study. The third group of questions was about the support to WM, 73% of respondents think that their companies support the practice of WM and 92% think that WM will help reducing construction waste. The ultimate goal of construction WM is zero waste, however 69% of the respondents think that their projects produce significant amount of waste which opposes the notion of having low waste construction sites. Large percent of our respondents 89% think that there should be more support to apply WM on construction sites.Respondents who didn’t receive WM training equalled to 60 which represent 64% of total participants and 82% think that there should be more training on WM. In regards to the discipline with most waste, civil got the highest percentage amongst the disciplines that generate the most waste with 40%, mechanical discipline with 32%, and then structural steel with 11%. Electrical and piping disciplines came with the lowest percentage amongst the disciplines that generates the most waste with 9% and 8% respectively. Fig 3 shows the distribution of the most waste generating discipline on construction sites.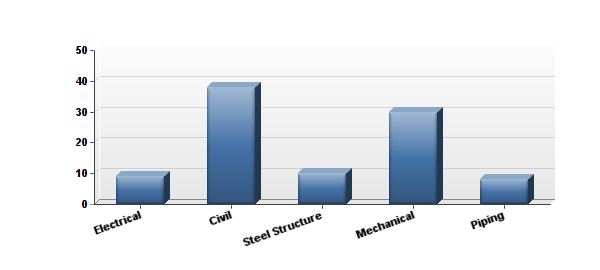 | Figure 3. The discipline that generates the most waste on construction site |
Going through the survey, the last three questions showed that 68% of the respondents think that penalties should be charged on contractors who don’t have WM plan and 81% think that contracts should include a clause that requires the contractor to use recycled material because 81% think that will reduce the amount of waste.
7. Conclusions
The construction industry has been assessed on the amount of waste produced each year. Most construction companies concentrate on reducing cost by improving productivity and compressing schedule without realizing that managing construction waste is another huge cost saving factor that they need to take in consideration.For many years as one of the main reasons for occupying the landfills with millions of tons of waste every year causing millions of dollars to the companies trying to control waste and follow the proper disposal procedures. In an attempt to protect the environment, many countries have developed various regulations to minimize C&D waste, but only few large size companies have established waste management guidance and procedures to reduce construction wastes and maximize their reuse.This project identified that not only projects costs are increased due to the increased amount of waste, but also significant amount of valuable land is being occupied with the waste generated on construction projects which is negatively impacting our environment. It appears that construction waste is a global phenomenon that involves Europe, Asia, Australia, and America. Although all the concentration is on construction phase at construction sites, but one major factor that affects the amount of construction phase is the design. Engineering firms must establish new design standards to help reduce the amount of construction waste by designing to dimensions available in the market that will eliminate cutting and shaping steel frame, plywood, and drywall.The survey that was designed for this study confirmed some of the information that was available before we start this research. Most projects generate significant amount of waste that can be eliminated by using smart engineering, standard dimensions, recycled material, metal form work instead of wooden form work for concrete works. The lack of training is another significant factor that construction companies should re-visit. Most of these projects use separate waste containers or bins for each kind of waste without most of them knowing the reason behind it because of lack of training. Although most of our surveyors have long years of experience but the majority of them indicated that they didn’t have any kind of training on WM. Providing the proper training to the individuals that are performing work on site is definitely additional cost to the project but it will save huge amount of money at the end. Having a WM contractor is the recommended model to be used on construction projects. Having a separate subcontractor for WM will eliminate or at least reduce company’s responsibility regarding the disposal of C&D waste. The WM contractor will estimate the quantity of total construction waste and its main components, will be specialized for managing waste on the project site, and shall have sufficient staff that is professionally trained and have extensive knowledge on construction waste and shall be fully engaged in the process. Providing different containers and smaller bins for all possible kinds of waste marked clearly and properly to indicate the type of waste that will contain, scheduled waste disposal and replacement of waste containers will be part of the subcontractor’s responsibility. There should be weekly meetings to discuss the amount of waste disposed for each discipline to track, assess, evaluate, and act accordingly to reduce it.Another recommended model is to have a department of WM that will hire specialty staff. The WM staff responsibility shall be managing waste and dispose it properly. Post signs of wastes and waste management on different location on the project; develop training sessions to the craft and improve their knowledge regarding C&D waste types and disposal process, Locate waste containers around the project in multiple areas to make it as easy as possible on the craft encourage them to dispose their waste properly, estimate the quantity and the types of waste in the design phase so that smart engineering can be applied and a significant cost will be saved during the construction phase.This study is a foundation for future studies about construction waste; it can be used as a reference for construction companies to establish their WM plans and procedures. This study can be a material for WM training sessions on construction sites and help construction companies to find the best way to control waste.
Appendix 1. Survey Questions
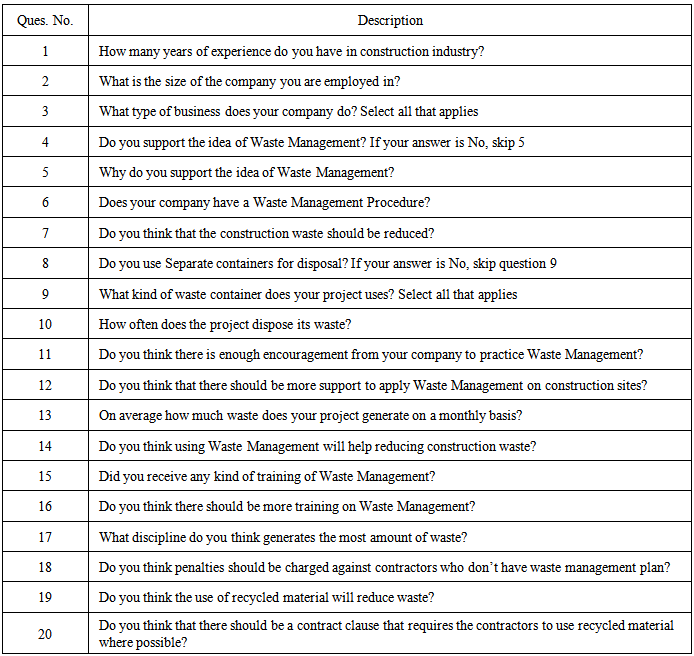
ACKNOWLEDGEMENTS
Acknowledgments to the Author’s wife Sonia Tatian for her outstanding support and encouragement.
References
[1] | Yuan, H. (2012). A Model for Evaluating the Social Performance of Construction Waste Management. Waste Management,32, 1218-1228. doi: 10.1016/j.wasman.2012.01.028. |
[2] | Dong-Woo, S., Hee-Sung, C., Jae-Moon, K., & Jee-Hye, K. (2006). Development of the Construction Waste Management Performance Evaluation Tool (WMPET). Retrieved from http://www.iaarc.org/publications/fulltext/isarc2006-00143_200606201320.pdf. |
[3] | Site Waste Management Plans in Construction Industry. (2013). Retrieved from http://www.ukessays.com/dissertations/construction/site-waste-management-plans-in-construction-industry.php?cref=1. |
[4] | Seydel, A., Skitmore, R. M., & Wilson, O. D. (1998). Waste Management in the Construction Industry. Construction and the Environment,2, 879-886. Retrieved from http://eprints.qut.edu.au/archive/00004540. |
[5] | Amaratunga, D., Haigh, R., Kulatunga, U., & Rameezdeen, R. (2006). Management of Environmental Quality: An International Journal. Retrieved from http://www.emeraldinsight.com/journals.htm?articleid=1537410&show=html. |
[6] | Anis, A. R., Garas, G. L., & El-Gammal, A. (2001). Materials Waste in The Egyptian Construction Industry. Retrieved from http://cic.vtt.fi/lean/singapore/Garasetal.pdf. |
[7] | Bossink, B., & Brouwers, H. (1996). Construction Waste: Quantification and Source Evaluation. Journal of Construction Engineering and Management. Retrieved from http://www.tue.nl/en/publication/ep/p/d/ep-uid/231803/. |
[8] | Danai, G. I., & Panos, K. (2012). Survey Regarding Control and Reduction of Construction Waste. Retrieved from http://www.plea2012.pe/pdfs/T05-20120130-0006.pdf. |
[9] | Glass, J., Osmani, M., & Price, A. (2008). Architect’s Perspective on Construction Waste Reduction by Design. Retrieved from www.lib.purdue.edu/. |
[10] | Stenis, J. (2004). Construction Waste Management Based on Industrial Management Models: A Swedish Case Study. doi: 10.1177/0734242X05050184. |
[11] | Drew, D., Shen, L. Y., Tam, C. M., & Tam, V. W. (2004). Mapping Approach for Examining Waste Management on Construction Sites. Retrieved from http://prof.incheon.ac.kr:8082/~uicem/pdf/seminar/100518b.pdf. |
[12] | Kang, X., Lu, W., Wang, J., Yuan, H. (2010). Critical success factors for on-site sorting of construction waste: A china study. doi: 10.1016/j.resconrec.2010.01.012. |
[13] | Austin, S., Baldwin, A., & Keys, A. (2000). Designing to Encourage Waste Minimization in The Construction Industry. Retrieved from https://dspace.lboro.ac.uk/2134/4945. |
[14] | Napier, T. (2012). Construction Waste Management. Retrieved from http://www.wbdg.org/resources/cwmgmt.php. |
[15] | Chini, A. R., Lu, Y., Shen, L., & Yuan, H. (2011). A Dynamic Model for Assessing the Effects of Management Strategies on the Reduction of Construction and Demolition Waste. 32, 521-531. doi: 10.1016/j.wasman.2011.11.006. |
[16] | Abu-Lebdeh, T., Bolden, J., &Fini, E. (2013). Utilization of Recycled and Waste Materials in Various Construction Applications. doi: 10.3844/ajessp.2013.14.24. |