Hosein Rajaieh 1, Yaser Mandi Sanam 1, M. Hadi Rafiee 2, Seyed Mojtaba Bagha 1
1Department of Civil Engineering, Amirkabir University of Technology, Tehran, Iran
2Department of Civil Engineering, Babol University of Technology, Babol, P. O. Box 484, Iran
Correspondence to: M. Hadi Rafiee , Department of Civil Engineering, Babol University of Technology, Babol, P. O. Box 484, Iran.
Email: |  |
Copyright © 2012 Scientific & Academic Publishing. All Rights Reserved.
Abstract
In order to constant developing principles, use of technologies as an appropriate substitution for materials and traditional methods discussed. Meanwhile non-load bearing walls –as a part of structural main members- dedicated a great share in using of traditional methods. Expenditure and implementation speed, dead load and structural performance, environmental compatibility and pollutions minimizing, construction ease, utilizing native specialties, using national interior resources and easiness in transportation and displacing considered in modern toward traditional method. Precast plaster panels produced in Australia in early 1990's and then utilized by other countries (India & China). In this regard, widespread researches on plaster materials and their applications in construction industry were initiated in Industrial university of Amirkabir since 1999 & polymer precast panels with plaster matrix in 50cm width, 10cm depth, and floor up to roof-integrated height and with a hollow section, as a industrial solution been studied and successfully passed the semi-industrial production. In this paper introducing of production manner of this panels & surveying & comparing with non-loading bearing walls traditional method in industrializing frame been presented.
Keywords:
Construction, Polymer-precast Panels, Non-load Bearing Walls, Plaster Matrix
Cite this paper: Hosein Rajaieh , Yaser Mandi Sanam , M. Hadi Rafiee , Seyed Mojtaba Bagha , Construction and Implementation of Non-Load Bearing Walls by Using Polymer-precast Panels with Plaster Matrix and Comparing Them with Existence Systems, International Journal of Construction Engineering and Management, Vol. 2 No. 1, 2013, pp. 1-7. doi: 10.5923/j.ijcem.20130201.01.
1. Introduction
Increase of demands in part of habitation following by quick growth population, Utilization from traditional methods in construction lead to Lack of the balance of efficiency with demand, according to the last census the country front shortage of 2.3 million residential units, unit age get of statistic from polling population and habitation. Similarly, condition of the secure of citizenry habitation until 1400 will be the following table (1)[1].global experiments have revealed that when is needed significant content from building and secure condition, only suitable made of aggregative with level, programming, assessment and industrial method[2]. Industrial habitation constructing, ingredient produce with over efficiency and repeat produce processing, assemble, possible building jitney and economic habitation; that is at first step, obtain very economical laboursaving, and also, at long-term will be lead to improve present situation with effect in culture construction of country and inter new technical knowledge in designing category and constructing the buildings[1].It can be resulted from table (2) that more than 51% from existed price of infrastructure is cause of autochthonous features and ordinary methods of production habitation, that by changing of production methods it can economies at the extinction price of the infrastructure. Non-load bearing walls as parts of building material are concluded mentioned percentages and with reduction to 51% costs of wall performance, by new utilization and industrial methods and materials. in addition to major recognitions ,one wall includes of components, methods and accomplishment rate, weight unit of surface all over , minimum require thickness and or ever adaptation with environment existence could be selected a suitable method. Many observations done at several countries for industrialization non-load bearing walls that included of them are studied that lead to produce walls (rapid wall) system[3] also studies on several non-load bearing walls and advantages were done those rather than together[4].A comprehensive investigation that included about 120 experimental tests and theoretical studies was completed at the University of Adelaide and the University of South Australia in 2002[5], and structural design theories and guidelines were developed based on this investigation[6-10].Large-scale experimental tests, similar to those conducted in Australia, have also been undertaken in India at the Indian Institute of Technology Madras[11, 12].Table 1. Prediction of production and mortgage needs in country[1]  |
| |
|
Table 2. changeable expenditure in completion cost of infrastructure[1] 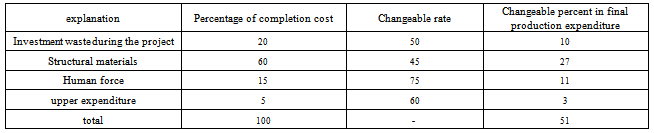 |
| |
|
Requirement to industrialization in construction materials production including non-load bearing walls at our country is apperception. Here about, done activity that Lead to produce, some of the modern material, ( non-load bearing walls, light prefabricate LSF, non-load bearing walls, semi prefabricate with 3D sandwich-ate sheet, cement yarn board system, made wall blocks to the light gaseous concrete, cemented board to wood excelsior’s)[13]. there, done widespread research from 1379 on land plaster component and usage those at construction industry beginning in industrial university of Amirkabir and polymer precast panels to plaster matrix in 50 cm width, 10 cm thickness, floor to roof integrated height and with hollow section, as an industrial solution be studied and successfully passed the semi-industrial production. In this study introduction of production manner of this panels and surveying and comparing with traditional methods of non-loading bearing walls in industrializing frame been presented.
2. Plaster as a Formative Matrix
From point view of energy subject and consistent development, in table (3) rate of consuming energy construction material considered in construction industry for this material presented, such as cement, lime, arabesque, glass and brick, and be severity, that in the plaster production process, it is law rate of energy usage.Because about 80% of primarily component panels are plaster, and with attention to utilization from fossil fuel in production process, noticed at classified utilization on universal panels, actually that is significant, remnant reduction consumption of unacceptable county resources. From of view subject of natural resource plaster, be observation, Iran has been second stratum in production plaster at global after united state (USA) in 2005, and after china in 2009[13]. According to this statistics, Iran is securing a major part of requiring plaster of construction industry in middle orient. There are more than 470 reserved and potential plasters in Iran that at present more than 270 reserved is beneficiating. Many of these mines have been contained stony plaster with best sincerity about 99% present [13].Table 3. Comparison of average consumption energy in materials production in Iran and world[13] 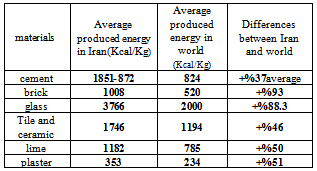 |
| |
|
In range of keeping the environment and wastage management, with attention to tenet ternate 3R (reduce, reuse, recycle)[14] and cases that before be mentioned, the plaster has been needed the lowest rate of energy at the process of production, between other standard material at the construction industry of Iran. With attention to utilization of fossil fuels as major resources of energy that is much few rate of greenhouse gases production especially co2 in process of plaster panels in comparison with other standard materials such as, several kinds of bricks, cement block and or concretive composite panels[3]. On the other hand, the plaster is only case recoverable and restorable among other traditional standard material, including ripe boles, and or cement with 100% to the natural cycle[15].totally by using these panels we can diminish the environmental effects of administration non-loading walls.
3. Experimentations
By choosing plaster as a slightly major formative material of technologic, several parameters for obtaining the design of the commixtures’ sake of replication to the necessity production, performance and attribute of necessity should be considered. These parameters include of check of the attribute of plaster in different rates, water to plaster, increasing material effect and finally utilization of yarn sake in order to improve attribute plaster and suitable instantaneous supersensible, compressive resistance, flexibility resistance, tensional resistance, and timing. Disposability material for examination of structural plaster of Semnan, yarn of polypropylene, additive plaster with trade name of TERA and was to the drink water of Tehran. Done examination includes two steps of test on effect of versatility of additive and resistance of plaster of chalk, that design of the commixture and that results in table (4). Second step examinations cheeked for removing of difficult mealy breakable of yarn effect at the compressive resistance, flexibility resistance, and tensional resistance plaster chalk, that brought its results in the table(5). It is citable that at the second step in addition to versatility of necessity chalk to decrease errors due low plaster versatility at instances production. It is selected be without utilization from increasable material, rather weighable of water to the cement 55% for plaster's production chalk and yarn. Sake surveying of compressive resistance utilized from instances to size 50*50*50 mm, and sake flexibility resistance of chalk from instance to size 40*40*160 mm and from dumbbell able instances sake of surveying of the gravitational resistance chalk yarn that you observe this instances at the figure (1).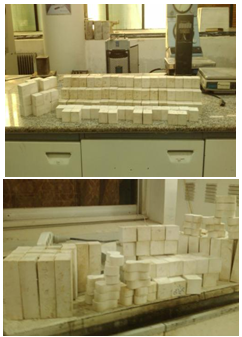 | Figure 1. made samples |
Table 4. porous pattern and first experimental results 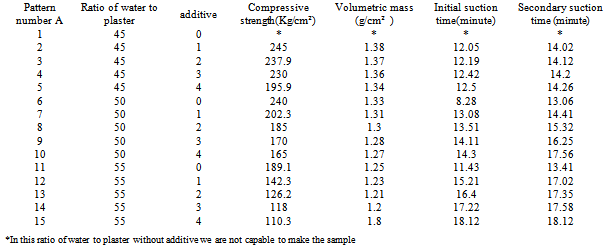 |
| |
|
Table 5. porous pattern and results of secondary experiments[8] 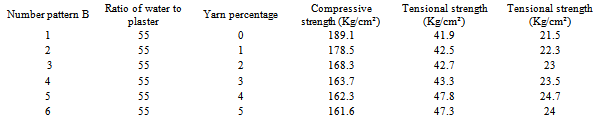 |
| |
|
By studying table(4) gravitational resistance of instances made by utilization from lubricate chalk at the low chalk rates to the water are observed, that obtained to the resistances at about 250 CG per cm. also, with increasing gravitational resistance, representation lesser resistance, relations upper lubricate rather than minimum those percents. Sake reach maximum resistance should be utilized from minimum of water and lubricate to relation scalable. This material is effective on chalk charisma and cause to increase it .Also, reduction of plaster masses of volume increases the instance's porosity that is adapting with result of compressive resistance. It is expressed this lubrication leads to increase porosity at the chalk plaster. It is also can be observed the production of bubble and lather at time of making the instance.It is observed by considering the examination results and utilization from lubricating at the low relation to the chalk lead to reduce plaster resistance between 25% to 50%. In addition to lack of possible plaster chalk production at low relation lesser than 50% due to be short time of charisma, and missing plaster performance, will not be possible to produce without lubricating by mention methods. Then, utilization of lubricating despite of resistance, it is seemed suitable selection, what many results of obtained will be acceptable and significant.( compressive resistance 250 KG on cm). By consideration table(5) and in addition to obtained results from examinations, be observed that, using of polypropylene maximum to 14% lead to increase inflexibility and gravitational resistances, but on the other hand, at the same rate, lead to reduce compressive resistance of plaster. These increasing and reduction rates of resistances are not significant, but utilization of this yarn, is one of the difficulties of chalk production, namely brittle that partly removed. During observation that done in laboratory and represented in figure(2), yarn avoided brittle, as instances at all yarn percent were not separated after break, and likewise kept primary partly own shape.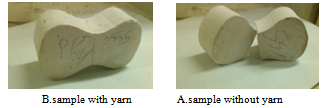 | Figure 2. not separating of tensional sample after fracture by using yarn |
4. Choice of Commixture Pattern
According to previous records, obtained experiences during the experiments revealed the commixture pattern at the traditional methods for chalk production blocks and also, instances made be experimental panels, until could be full fill suitable lubricated sake formerly an aggregate production at factory. Resistance panel against admittance of due translation and utilization period, limited unit weight of panel surface to the maximum 60 KG per m2 where section similar figure (3) , optimized usage in using excessive material and yarn in order to control costs production and suitable ductile by processing of production. According to mentioned cases and obtained results from examinations done, commixture selective patterns are descriptions following: (The relation of weight of water to the chalk: 45%, relation of weight lubricate to the chalk is 2%, relation of weight of polypropylene yarn 19 mm to the chalk: 0.2% percent)According to the above commixture pattern, the weight of unit of obtained content plaster will be circa 1/37 gram /cm3. likewise Compressive resistance , usage of polypropylene yarn will be to the shape of dissipated equals 210 kg/cm2 and bending resistance equals 52 kg/cm2 and time chasm primary of mixture get equal 12 minutes. As it expressed in previous selections, only usage of yarn is reducing nature of ductile chalk, and increasing of acceptable energy of panel.
5. Dimension Selection and Production of Testing Panel
Spot dimension for panels, according to casting and production possibilities, transport and relocation at site, en bloc covering of floor to roof, installation easiness without requiring to the machinery in addition to panels weight and implementation all architectural to the shape of 0/5 m width, 3m height, and 10 cm thickness considered. Thus, panel height according to current residential buildings height; (between 2/7 to 3 m) all floor height is covered. Thickness 10 cm secure in minimum thickness of partitioned walls and 0/5 width is facilitated implementation of architectural plans.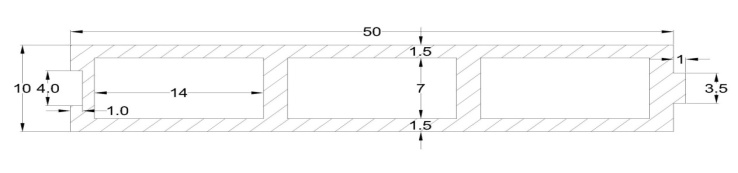 | Figure 3. panel’s section surface |
The thickness of panel walls is according to (3) figure, equal 15 cm. of course, because of increasing the panel’s resistance in its low that is at against of more strokes whether on installation time or on utilization time. This thickness gradually increases to the 25 mm. Dimension of holes are equal to 70*140 mm.
6. Comparison between Made Panels and Existed Systems
Moreover, adoptability to environment and low production process energy, which come in paragraph (2), produced panels can comprised and be considered with the following cases:
6.1. Performance Rate
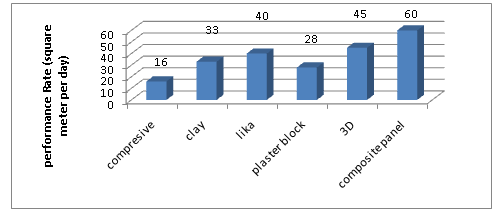 | Figure 4. Comparison of administrative speed of 10 cm current methods of separating bladed[13] |
Moderately, an administrative group can perform about 60 to 70 panels daily. Performance rate of internal walls as represented in figure (4) is about twice as earthen blocks. Figure (4) comparison speed performance of current method of separating knife at 10 cm.[13]
6.2. Increase of Useful Infrastructure
In the common and traditional methods, brick and blocky walls named 10 cm(10 centimeters), have minimum equal 11 to 12/5 applicative to performance quality. Moreover, whereas at the final will be received thickness of joinery include of chalk and soil and whitewash of this thickness to the 15 until 18cm.In comparison with traditional methods. Thickness of made walls with mentioned panels will be at the end of act, equal 10 cm and whereas joinery maximum 12cm. This reduction of thickness at a 90 metric unit that would have a useful 80 meters infrastructure(30 meters length) has internal wall will have about 2.5% increasing in usefulness of infrastructure . Of course, this rate increases with kind of project to 7%.
6.3. Joinery and Performance of Mechanical and Electrical Installations
According to removing the layer of the chalk and soil mixture, or cement sand from required joinery for implemented walls by this panels and also, reducing the thickness of layer whitewash chalky circa 30 to 50 percent, from view of material costs and application, has reduced significantly rather than other current methods that be considered in previous parts.Carve and destruction due function mechanic and electric installation are from cases that our avoidable for current methods at time performance of wall. This job own as far performance, material human energy and time is sumptuary.At the comparison with current methods Can with usage from holes of inter panel for across significant, content of curve and destruction.
6.4. Building Dead Load
Table 6. comparison of final weight per area unit of common walls with polymeric panels (kg/m2)[13] 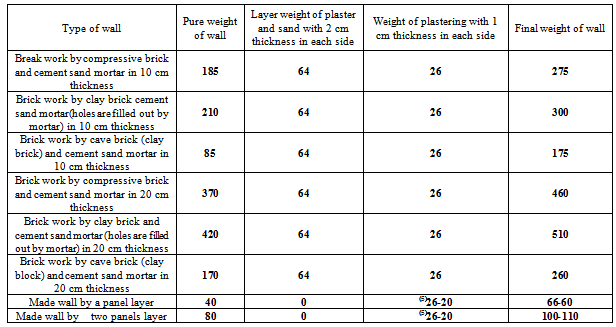 |
| |
|
Final weight per unit area of walls by these panels can be divided to panels weight and the mortar used in into joinery. Due to the flat surface of these panels a thin plaster and sand layer can be removed and it is needed to maximum of 1 cm thickness layer of plaster mortar of whitening. Accordingly weight per unit area with 10 cm thick walls will be restricted to wall surface about 60 to 70 kg per square meter. Final weight (considering joinery) 10 cm leaky walls equal 300 kg and 10 cm bat block equal 175 kg, respectively should be 76 and 60 percent lower. In table 6 is noticed to unbacker walls with different thickness.Walls weight as a part of building dead load has a great effect in designing process and constructing building in different measures. Effects of decreasing weight (dead load) related to building walls can be surveyed in different aspects. (As below).
6.4.1. Effect of Dead Load Wall on Designing Structure
We contemplate primarily a 4-storey building with useful infrastructure of 80 m2, all infrastructure 90 m2 and floor up to roof height of 2/7 m, for consider affection dead load at make-up design. This building will contain about 80 m2 interior walls and 144m2 exterior walls. By comparison with the amount of surface unit weight of different materials and current methods of operating non-load bearing walls by these panels, weight reduction about 60 until 80% is observed. This rate of dead load reduction at equal of this building weight, that using from traditional material was been equal 580 ton, it will be received to 380 ton equal 35% reduction with use of this panels. This dead load reduction lead to decline in structure elements dimension and therefore operation cost. Only in case of earthquake load, the reduction will be about 28% (5) that perform basic rolls at designing structure. At condition that due to limitation of design preferences, strength of structure could not be reduced by proportion of dead-load reduction, this amount of dead-load reduction will be cause to increase in structure safety factor.
6.4.2. Effect of Dead Load on Structural Designing
The installation methods of these panels are such that minimized the transfer of structural elements deformation to the walls, specially, at condition of exerting lateral load such as wind and earthquake on structure, by creating freedom grades relation to the structure.According to the 2-12-1 paragraph of "design building preference against earthquake standard 84-2800 third editions", this behavior does not make limitation in structural movement toward wall plane therefore wall designing for induced-tensions within it due to wind & earthquake is not require. Just should be able to transfer earthquake created-force due to mass of wall to the structure. With regard to operation system & weight of these walls, the transfer of this force will execute completely.
6.4.3. Transportation Cost
As cases that usually hide from view designer, performer, construction and industrial managers about costs and its changes, is costs of material transportation to the project site, due to variation in operating method and material. This cost that accounted weight per distance unit, can allocated much amount to own. For instance, at the same building that considered in previous section, with assumption equal transportation distance, transportation cost from factory to site will be reduced minimum 50 until 60%. Direct affect of this project expenditure not only is tangible but also with the same relation in great scale will reduced by reduction of heavy vehicles transportation, environmental pollution cost due traffic, fuel and depreciation of vehicles and roads.
6.5. Thermal Insulator
In order to respond to the requirement of chapter 19 of Iran national regulations, surrounding walls of building should be construct in double wall with use of middle or external insulator. Therefore, utilize of double walls is necessary in aspect of suitable thermal strength preparation in surrounding walls and adjacent to uncontrolled spaces. Also, at table (7) a comparison panel's thermal strength with other fashion walls is given and observed that designed panels with less width has appropriate thermal strength.Table 7. comparison of polymer thermal strength panels with other current walls[13] 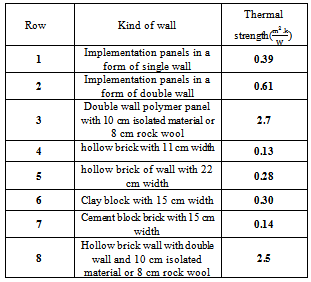 |
| |
|
7. Conclusions
To respond the residual requirement and with regard to population growth trend, economic condition and reaching to consistent development, construction industrializing is one of the effective solutions. Non-load bearing walls are not exempt as part of major building elements, and it require fundamental evolution in operation method and primarily material. Due to the extant and enormous resources of chalk in Iran, this material selected as major material in precast panels. We will be encounter a noticeable reduction in cost of wall operation, building dead load, environmental pollution, energy consumption in produce and building beneficiary and operation speed increment and effective infrastructure and ease of mechanical and electrical implementation by utilizing of these panels in operation of building internal and external partition walls.
References
[1] | Hosein Rajaieh ,Yaser Mandi Sanam , Majid Ipakchi “New methods in the non-load bearing walls using prefabricated panels polymerThe gypsum matrix” 9th International Congress on Civil Engineering, May 8-10, 2012 Isfahan University of Technology, Isfahan, Iran |
[2] | Roger-Bruno Richard, Industrialized building systems: reproduction before automation and robotics, Automation in Construction 14 (2005) 442-451 |
[3] | Y.-F. Wu, The structural behavior and design methodology for a new building system consisting of glass fiber reinforced gypsum panels, Construction and Building Materials, Volume 23, Issue 8, August 2009, Pages 2905-2913 |
[4] | Abdulmohsen Al-Hammad and MohammadA.Hassanian ,VALUE ENGINEERING IN THE ASSESSMENT OF EXTERIOR BUILDING WALL SYSTEMS,Journal of Architectural Engineering ,September 1996,pages 115-119 |
[5] | Wu YF. A 2002 report into the physical testing and the development of design guidelines for the structural application of Rapidwall in building construction. Adelaide (Australia): Dare Sutton Clarke Engineers; 2002. |
[6] | Wu YF, Dare MP. Axial and shear behavior of glass fiber reinforced gypsum wall panels: tests. J Compos Constr ASCE 2004;8(6):569–78. |
[7] | Wu YF. The effect of longitudinal reinforcement on the cyclic shear behavior of glass fiber reinforced gypsum wall panels: tests. Eng Struct 2004;26(11): 1633–46. |
[8] | Wu YF, Dare MP. Flexural and shear strength of composite lintels in glass fiber reinforced gypsum wall constructions. J Mater Civil Eng ASCE 2006;18(3):415–23. |
[9] | Liu K, Wu YF, Jiang X. Shear strength of concrete filled glass fiber reinforced gypsum walls. Mater Struct2008;41(4):649–62. |
[10] | Wu YF. Development of the structural design theory for Rapidwall building system. Constr Des Project 2004;189(1):47–51[in Chinese]. |
[11] | Janardhana M, Prasad AM, Menon D. Studies on the behavior of glass fiber reinforced gypsum wall panels. In: Proceedings of the 8th US national conference on earthquake engineering, San Francisco, California, USA; 18–22 April 2006. Paper no. 1326. |
[12] | Janardhana M, Prasad AM, Menon D. Behavior of glass fiber reinforced gypsum wall panel under cyclic lateral loading. In: Proceedings of the fourth international structural engineering and construction conference (ISEC-4), Melbourne, Australia; 26–28 September 2007. p. 707–11. |
[13] | Majid Ikchi. The effect of cost of construction with using light composite panel with plaster matrix in comparison with normal buildings.faculty of civil engineering and environment-Amirkabir university oftechnology-Tehran-Iran.2010-2011 (thesis) |
[14] | Ashok V. Shekdar, Sustainable solid waste management: An integraاted approach for Asian countries Waste Management, Construction and Building Materials, Volume 29, Issue 4, April 2009, Pages 1438-1448 |
[15] | Omahen R. Ecologically sustainable development: approaches in the construction industry. Master of economics thesis, Faculty of Economics, University of Regensburg: Regensburg, Germany; 2002. |